Методика определения границ переходных процессов при размерной настройке инструментов для программирования сверления отверстий на станках с ЧПУ
Автор: Н.В. Беляков, С.К. Селезнёв
Журнал: Материалы и технологии @mat-tech
Рубрика: Машиностроение и машиноведение
Статья в выпуске: 1 (11), 2023 года.
Бесплатный доступ
Предложена методика моделирования границ переходных процессов при сверлении, минимальных величин врезаний и выходов, длин рабочих ходов, координат начальных и конечных положений сверл в зависимости от условий врезания, выхода и геометрических параметров их режущих частей для программирования обработки отверстий на металлорежущих станках с ЧПУ. Использование системы на машиностроительных предприятиях дает возможность: снизить затраты на обработку отверстий из-за сокращения основного времени; повысить срок службы и период стойкости инструмента за счет назначения щадящих режимов резания на участках динамических изменений сил резания при врезании и выходе сверл. Результаты работы также могут быть полезны в организациях, специализирующихся на разработке CAM-систем и учебном процессе.
Режущий инструмент, сверло, переходный процесс, длина врезания и выхода, CAM-система
Короткий адрес: https://sciup.org/142239173
IDR: 142239173 | DOI: 10.24412/2617-149X-2023-1-23-33
Текст статьи Методика определения границ переходных процессов при размерной настройке инструментов для программирования сверления отверстий на станках с ЧПУ
УДК 658.512
В работах [1, 2] приводится метод решения задачи определения положения систем координат заготовки и инструмента в начальной и конечной точках траекторий резания, а также величин врезания и выхода концевых и торцевых фрез для размерной настройки при обработке плоских поверхностей на станках с
ЧПУ. Аналогично при программировании обработки внутренних открытых и полуоткрытых цилиндрических поверхностей вращения сверлами на станках с ЧПУ от оптимального расположения системы координат инструмента и заготовки зависит основное (машинное) время и, как следствие, затраты на об- работку. При этом важнейшее значение приобретает учет границ переходных процессов (врезания и выхода сверла). Во время переходных процессов динамически меняются составляющие силы резания, наблюдается нестабильность упругих деформаций технологической системы, что может приводить к затуплению, перегреву и поломке инструмента. Поэтому производители сверл в каталогах инструментов и онлайн-калькуляторах режимов резания рекомендуют их различные значения для переходных процессов и устойчивого резания [3‒4].
Для снижения негативных последствий переходных процессов при сверлении предлагаются способы регистрации начала такого процесса при выходе сверла из отверстия по снижению осевой силы; увеличению крутящего момента; перемещению в направлении оси сверла слоя металла, расположенного под режущей кромкой и др. [5]. Предлагаемые решения требуют использования специальных конструктивных решений повышающих стоимость изготовления деталей.
В современном машиностроении широкое распространение получили станки с ЧПУ. При их про- граммировании возможно предусмотреть изменение режимов резания в любой момент времени и траектории движения инструмента и заготовки. Для подготовки управляющих программ широкое распространение получили CAM-системы: Компас ЧПУ, T-Flex ЧПУ, SiemensNX, MasterCAM, EdgeCAM, SolidCAM, Прамень ЧПУ, Creo, CATIA, PowerMill, Esprite и др. [6‒9].
Однако, современные CAM-сиcтемы, а также онлайн-калькуляторы не позволяют учесть все разнообразие форм режущих частей современных сверл, в автоматическом режиме определять и (или) задавать длины врезаний, устойчивого резания и выходов инструментов для задания различных щадящих режимов резания, и, как следствие, оптимально расположить системы координат инструмента и заготовки в начальных и конечных точках траекторий резания (рис. 1). В справочной и учебной литературе лишь приводятся рекомендации по определению основного времени для некоторых вариантов врезания некоторых сверл без учета различия их режущих частей [10‒11].
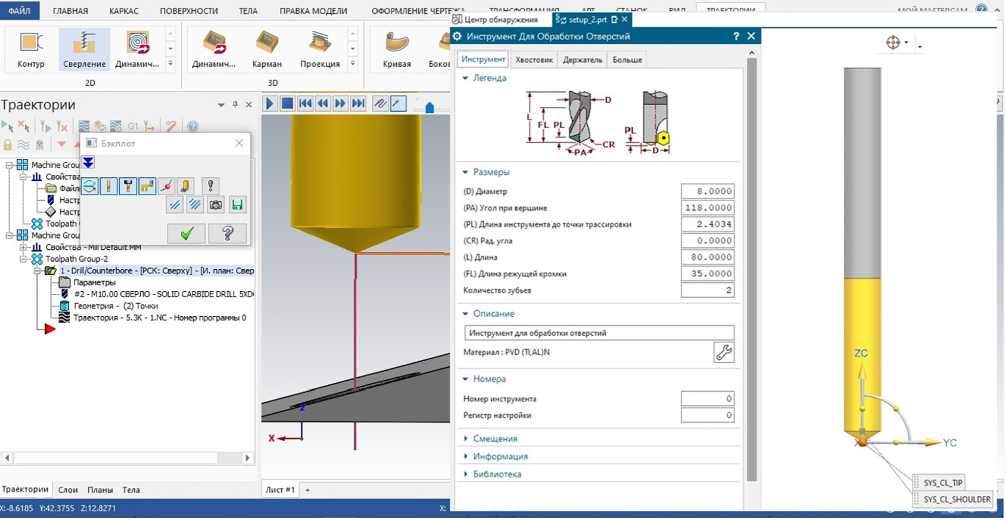
Рисунок 1 – Некоторые интерфейсы задания параметров размерной настройки в MasterCAM и SiemensNX
Поэтому целью работы является разработка методики и программного обеспечения для определения минимальных величин врезания и выходов сверл, координат их начальных и конечных положений, а также основного времени для программирования сверления отверстий на станках с ЧПУ.
Для достижения указанной цели были поставлены и решены следующие задачи:
-
1. Составлены принципиальные расчетные схе-
- мы и математические модели для определения минимальных величин врезаний и выходов, длин рабочих ходов, координат начальных и конечных положений сверл в зависимости от условий врезания, выхода и геометрических параметров их режущих частей;
-
2. Разработаны общие модели для определения затрат основного (машинного) времени;
-
3. Разработан алгоритм функционирования и общая структура программного обеспечения по опре-
- делению длин рабочих ходов, минимальных величин врезаний и выходов, координат начальных и конечных положений сверл;
-
4. Разработано программное обеспечение реализации моделей, проведена его комплексная отладка и предварительные испытания, а также разработаны программные документы.
Для исследования и решения, поставленных в работе задач использовались методы теории автоматизации проектирования, аналитической геометрии, системно-структурного анализа и моделирования. Проводился анализ литературных источников, электронных изданий, опыта использования систем автоматизированного проектирования на предприятиях, а также анализ конструкторской и технологической документации в соответствующих бюро машиностроительных заводов.
РЕЗУЛЬТАТЫ ИССЛЕДОВАНИЙ
При формировании общих моделей для определения затрат основного (машинного) времени установлено, что в практике использования наиболее широкое применение находят варианты врезания и выхода сверл относительно плоскости (перпендикулярной или наклонной) или цилиндрической поверхности (наружной и внутренней симметрично или со смещением). Прочие варианты могут быть к ним приведены.
Различные сочетания поверхностей врезания и выхода инструментов задают различные положения системы координат инструмента относительно системы координат заготовки 42 различными способами. Эти способы определяют общие принципиальные расчётные схемы для определения длины рабочего хода инструмента Lpx , величины врезания Lвp , величины выхода Lвых , а также координат начального и конечного положения инструмента (Е и Е ) в системе координат заготовки (Wh и Wk ) .
Так на рисунке 2 показаны некоторые примеры принципиальных расчетных схем. На схемах тройной штриховой линией обозначены в общем виде формы режущих частей инструментов.
На основе принятых обозначений длина рабочего хода в общем виде может определяться по формуле:
px вp уст вых под нвр квых вых , где Lуст – длина устойчивого резания; Lпод – длина подвода инструмента (принимается 2…3 мм); Lнвр – расстояние между системой координат заготовки и точкой начала врезания инструмента; L – расстояние между системами координат заготовки (определяется заданным на чертеже размером); Lквых – расстояние между системой координат заготовки и точкой начала выхода инструмента.
Включение перечисленных составляющих в формулу длинны рабочего хода и знаки перед Lнвр , L и Lквых зависят от геометрических условий вреза-
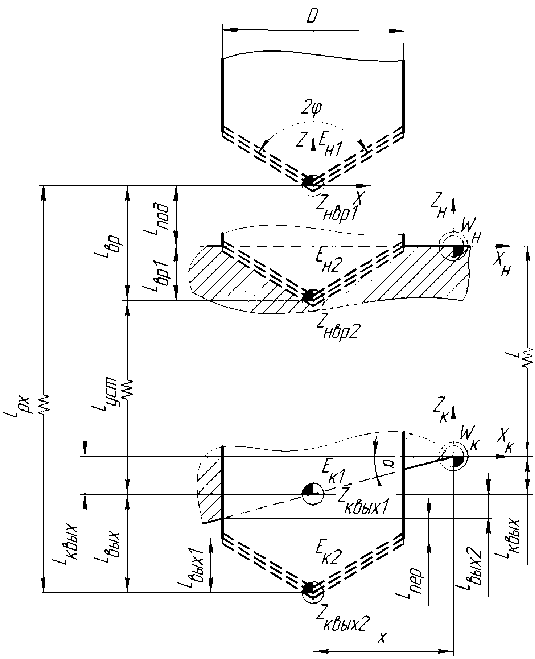
Рисунок 2 – Пример общей принципиальной расчетной схемы для врезания сверла по плоскости перпендикулярной инструменту и с выходом по наклонной плоскости ния и выхода инструментов, а также расположения систем координат Wh и Wk.
Так для схемы, показанной на рисунке 2:
px вp уст вых под квых вы х ,
Таким образом, затраты основного (машинного) времени Tо на переход в общем виде могут определяться по формуле:
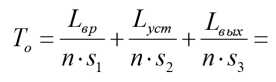

где s 1 - подача на оборот при врезании; s2 - подача на оборот при устойчивом резании; S 3 - подача на оборот при выходе инструмента.
Величины врезания и выхода инструмента:
вp под вр1 вр2 , вых вых1 пер вых2 , где Lвр1 – длина врезания инструмента, обусловленная геометрией его режущей части инструмента; Lвр2 – длина врезания, обусловленная геометрией заготовки; Lвых1 = Lвр1 – длина выхода инструмента, обусловленная геометрией его режущей части;
Lпер – длина перебега (принимается 2...3 мм); Lвых2 – длина выхода инструмента, обусловленная геометрией заготовки.
В результате анализа каталогов фирм производителей осевых инструментов проведена классификация их режущих частей. Так установлено, что все многообразие режущих частей сверл можно свести к 8 вариантам (рис. 3).
Для расчета величин врезания инструментов Lвр1 , обусловленных геометрией его режущих частей, составлены соответствующие расчетные схемы, позволяющие сформировать математические модели для их определения (рис. 4).
Согласно рисунку 4 а из ∆АВС
Lвp1 = АВ = ВС / tgφ = D / 2tgφ.
Согласно рисунку 4 б из треугольников ∆АВС и ∆СDE
Lвp1 = АF = АВ + СD =
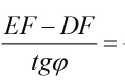
D .
--0,2---sin г»
tgT
+ 0,2D-cos^
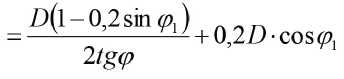
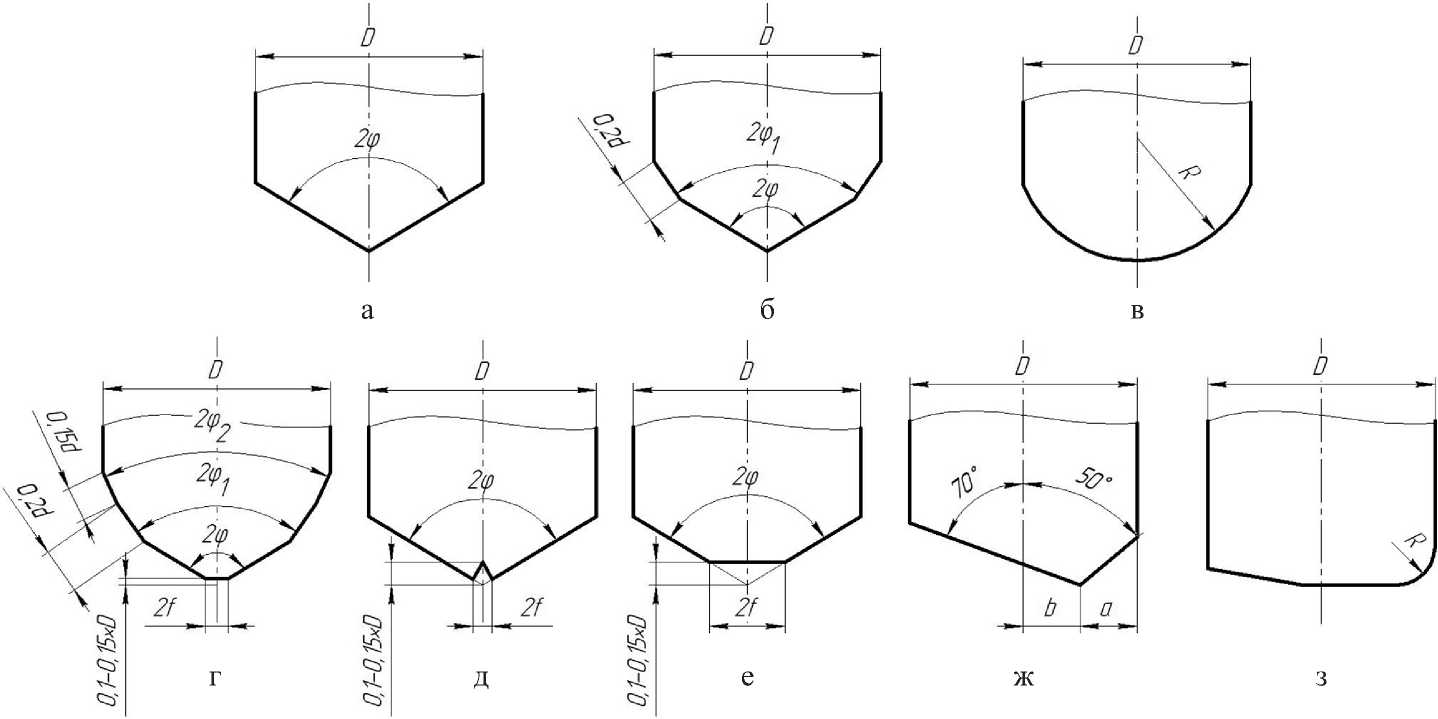
Рисунок 3 – Варианты режущих частей свёрл:
а – спиральное, шнековое, эжекторное с одноплоскостной заточкой;
б – спиральное с двухплоскостной заточкой; в – спиральное с закруглёнными режущими кромками; г – спиральное конструкции В.И. Жирова;
д – спиральное с прорезной перемычкой; е – спиральное со стачиванием перемычки;
ж – ружейное; з – кольцевое, со сменными пластинками
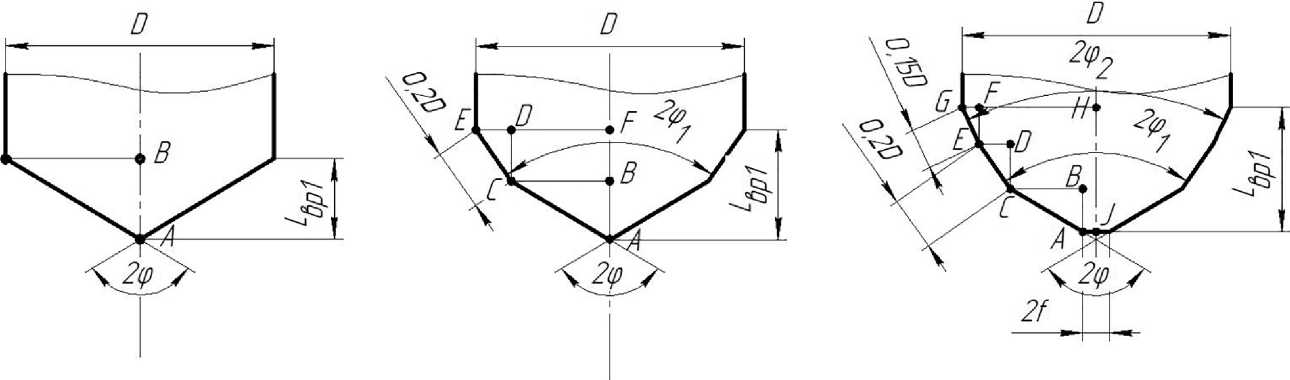
аб в
Рисунок 4 – Примеры расчетных схем для определения L вр1 некоторых видов сверл: а – спиральное, шнековое, эжекторное с одноплоскостной заточкой;
б – спиральное с двухплоскостной заточкой; в – спиральное конструкции В.И. Жирова
Согласно рисунку 4 в из треугольников ∆АВС , ∆СDE и ∆EFG:
= JH = AB + CD + EF = HG F° DE
Lgpi
tg(p
+ EG • со$ф7 + EC-созф? =
= (GH - AJ -0,2-GH -2-81пфу -0,15-GH ■2-sгnф2)■ctgф-v + 0,2GH-2• sin фу • ctgфy +
+ 0,15-GH-2-81пф2 •ctgф7 =
= \—-/—0,2В-81пфу -0,15В-81пф2 I-
• ctgф + 0,2D • sin фу • ctgфу + 0,15D • 81пф2 ■ ctgф2
траектории при врезании Zнвр1 , в конечной точке траектории при врезании Zнвр2 , начальной точки траектории при выходе Zквых1 и конечной точке траектории при выходе Zквых2 ) были составлены соответствующие расчетные схемы. Некоторые схемы для определения этих параметров при сверлении приведены на рисунках 5 и 6. При этом установлено, что принципиальное отличие для сверления при расчетах имеют варианты с наличием горизонтальной режущей кромки перемычки и без неё.
Согласно рисунку 5 а из ∆СED , ∆АВO и ∆АВC :
L нвр
= CD = ED / ctgα = x / ctgα, Lвр2

В таблице 1 приведены математические модели для определения Lвр1 для различных режущих частей сверл.
Для определения таких параметров размерной настройки, как расстояния между системой координат заготовки и точкой начала врезания инструмента Lнвр , расстояния между системой координат заготовки и точкой начала выхода инструмента Lквых , длины входа инструмента, обусловленной геометрией его режущей части Lвр1 , длины входа (выхода), обусловленной геометрией заготовки Lвр2 , а также координат начального и конечного положений сверла в системе координат заготовки (в начальной точке
Тогда
Lвp = Lпод + Lвр1 + Lвр2 = Lпод + Lвр1 +^Iga
Z нвp2
Z нвp1
-
L
нвp
+ L под
X ctga
+ L
под,
- Lнвp -
вр2 вр1
x D t t
- -tga - Lвр1 .
Согласно рисунку 5 б из ∆AСD и ∆АВC :
Lнвр = DB = RS, Lвр2 = AB = BD - AD =
=
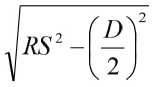
Таблица 1 – Сводная таблица для определения величин врезания сверл L вр1 , обусловленных геометрией их режущих частей
Сверло |
вр1 вых1 |
||
Спиральное с одноплоскостной заточкой |
D / 2tgφ |
||
Спиральное с двойной заточкой |
D - 0,2D • sin фх . _ -------------— + 0,2D • cos ф, 21§ф |
||
Спиральное для сверления чугуна (по В.Г. Жирову) |
| — - 0,2D • sin
ф -
0,15D • sin
ф | • ctgф +
+ 0,2D • sin ^ •
ctgф^
+ 0,1
5D
• sin ^ '
cfg |
||
Сверло |
вр1 вых1 |
Сверло |
вр1 вых1 |
Спиральное с закругленными режущими кромками |
R 1R2 Л — л A-- V 4 |
Пушечное |
D + / 2 tga |
Спиральное со стачиваемыми перемычками |
--/ -COS Ф (2 ) |
Ружейное |
D , --v b-ctga 2 |
Спиральное с прорезной перемычкой |
(D Л --/ -COS Ф (2 ) |
Шнековое |
D / 2tgφ |
Кольцевое (или со сменными пластинками) |
0 |
Эжекторное |
D / 2tgφ |
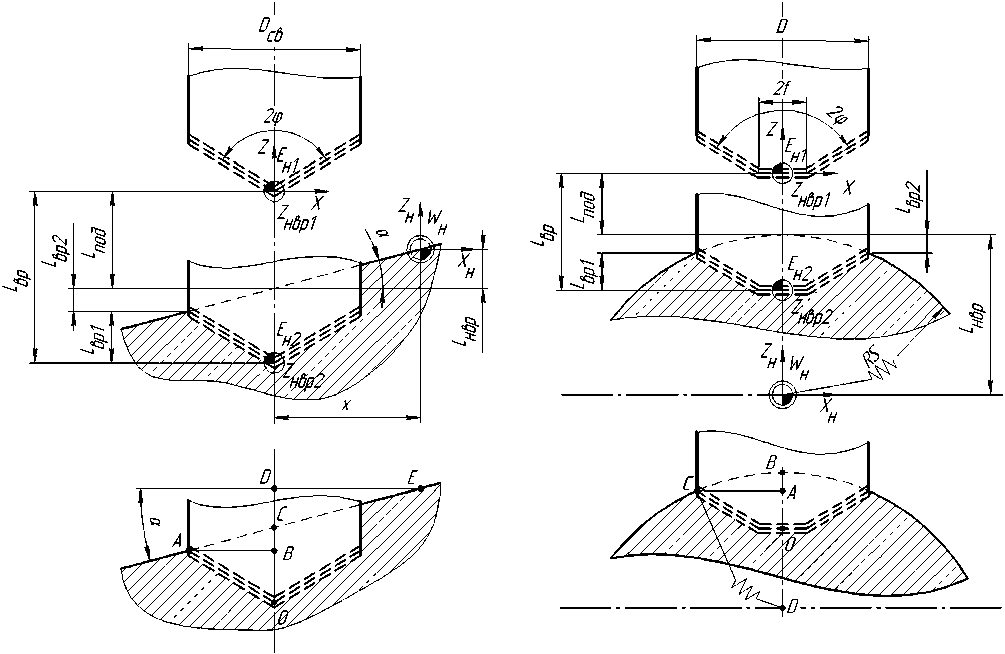
б
а
Рисунок 5 – Примеры расчетных схем для определения параметров размерной настройки при врезании сверл: а – врезание под углом, б – врезание по цилиндру симметрично
'кбых
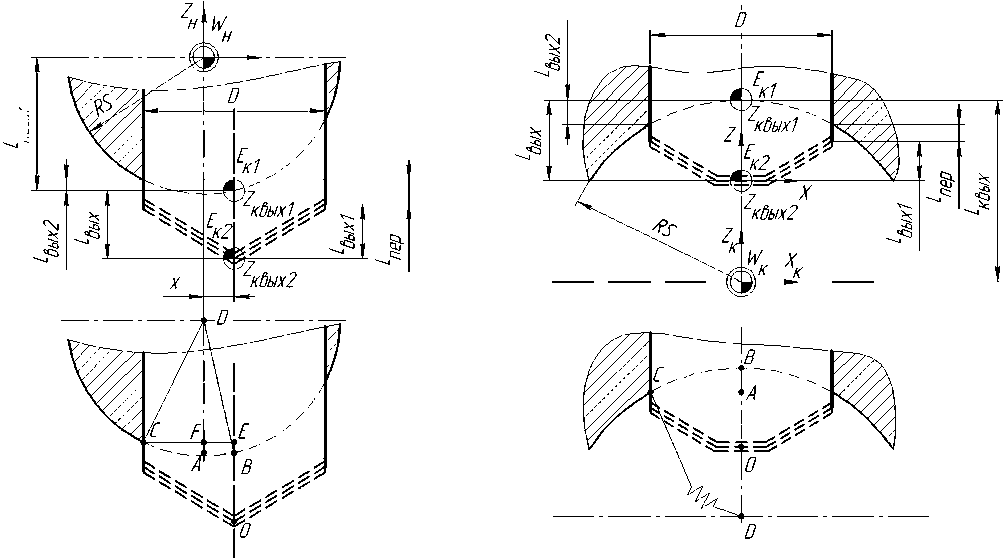
аб
Рисунок 6 – Примеры расчетных схем для определения параметров размерной настройки при выходе сверл: а – выход по наружному цилиндру со смещением, б – выход по внутреннему цилиндру симметрично
Таблица 2 – Сводная таблица для определения нвр1 и нвр2
L, нвр квых
Вход (выход) |
L вр2 |
нвр квых |
Z нвр1 |
Z нвр2 |
Плоскость прямая |
0 |
0 |
L под |
- Lвр1 |
Плоскость наклонная α < 0 |
D 4 tga |
x/ctgα |
X - + L под |
D - - tg α - L ctga 2 вр 1 |
Плоскость наклонная α > 0 |
D 4 tga |
x/ctgα |
X + L под |
D - tg α - L ctga 2 вр 1 |
Цилиндр наружный симметрично |
RS - \ I 2 J |
RS |
RS + L под |
- L вр1 |
Цилиндр наружный со смещением |
- - V (2 J |
^Irs'-x1 |
+ Lпо |
^RS^x1-^- - a/rS2-x2-Jrs2-[ — + X I V (2 J |
Цилиндр внутренний симметрично |
1 i D2 rs-Ars-— \ 4 |
RS |
- RS + L под |
” Л5 ” L epl + + rs-Jrr2- - V v 2 J |
Цилиндр внутренний со смещением |
- V (2 J Al IVA — X |
^Irs'-x1 |
- + L под |
- Jrs2- -aIrS2-x2 |
Таблица 3 – Сводная таблица для определения параметров размерной настройки L вых2 , Z квых1 и Z квых2
Вход (выход) |
L вых2 |
Z квых1 |
Z нвр2 |
Плоскость прямая |
0 |
0 |
вых1 пер |
Плоскость наклонная α < 0 |
D 4 tga |
X ctga |
D - - tg α - L - L ctga 2 вых 1 пер |
Плоскость наклонная α > 0 |
D ч tga |
X ctga |
D ctga 2 ga вых 1 пер |
Цилиндр наружный симметрично |
RS - N <2 J |
- RS |
-RS-L8bKY-Lnep + 1 2 r dV +rs-jrs2-\ — V I 2 ) |
Цилиндр наружный со смещением |
lnc2 (D ) V (2 J - |
- |
-л1н82-х2 -a1rS2-\—-x\ - V 12 ) -^RS'-x^-L^-L,^ |
Цилиндр внутренний симметрично |
RS - V 12) |
RS |
- rs+ rs- Jrs2 - 1 I - l , вых1 |
Цилиндр внутренний со смещением |
- -Jrs2 -Г- + х) V 12 J |
4rS2-x2 |
^RS^-x1 -L.„X-L„T- - a1rS2-x2-ArS2-\—^x\ V < 2 J |
Тогда
Z квых2
-
L
квых
L вых1
L=
пер
ArS2-x2
L вых1
L.
пер
Z нвp1
L вp = L под + L вр1 + L вр2 = L под + L вр1 +
Согласно рисунку 6 б из ∆ACD :
= L
нвp
+ L под
= RS + L под , Z нвp
= L
-
нвp
L вр2
-
L вр1
Lквых = BD = RS,
=
-
L . вр1
Lвых2 = BA = BD -
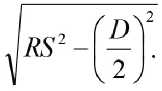
Согласно рисунку 6 а из ∆ABD , ∆DCF :
Тогда вых пер вых1 вых2
Lквых = АD =
Lвых2 = EB = АD - DF =
= L пер + L вых1 + RS -
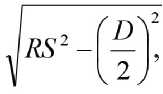
Тогда
=
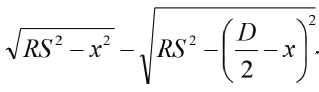
Zквых1 = Lквых = RS,
Z квых2
= L
-
L вых2
-
L пер
-
L вых1
вых пер вых1 вых2
= Lпер + Lвых1 - ,
квых
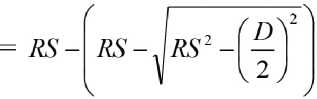
пер
-
L
-
L. вых1
Z квых1
- L квых
aIrS^-x2
Результаты моделирования параметров размерной настройки для сверления сведены в таблицы 2 и 3.
параметров размерной настройки L вр2
L
Предложенные методики, модели и алгоритмы позволили создать систему автоматизированного расчета параметров размерной настройки сверл и доказать их работоспособность (рис. 7).
При работе с системой пользователь последовательно вводит информацию о геометрии заготовки на входе и выходе инструмента, геометрии режущей части сверла и режимах резания, а результатом работы являются координаты начального и конечного положения инструмента, величины врезания и выхода, рабочих ходов и основное (машинное) время обработки на участках врезания, выхода и устойчивого резания инструмента.
ЗАКЛЮЧЕНИЕ
Предложена методика моделирования границ переходных процессов при сверлении, минимальных величин врезаний и выходов, длин рабочих ходов, координат начальных и конечных положений сверл в зависимости от условий врезания, выхода и геометрических параметров их режущих частей.
Представление разработанных моделей на языке теории автоматизации проектирования, алгебры логики и теории алгоритмов позволило создать про- граммное обеспечение для автоматизированного определения указанных параметров размерной настройки сверл для программировании обработки отверстий на металлорежущих станках с ЧПУ и доказать их работоспособность.
Методика и программное обеспечение прошли опытную эксплуатацию в учебном процессе кафедры технологии машиностроения УО «Витебский государственный технологический университет».
Использование системы дает возможность:
‒ снизить затраты на обработку отверстий сверлами из-за сокращения основного (машинного) времени за счет минимизации величин рабочих ходов сверл;
‒ повысить срок службы и период стойкости сверл за счет назначения щадящих режимов резания на участках переходных процессов;
‒ улучшить показатели качества поверхности на участке врезания и выхода инструмента.
Разработки могут использоваться:
‒ в проектных бюро машиностроительных предприятий при размерной настройке металлорежущих станков и проектировании их наладок;
‒ при разработке управляющих программ для станков с ЧПУ;
‒ в организациях, специализирующихся на разработке систем автоматизированного проек- тирования для разработки и совершенствовании CAM-систем;
‒ в учебном процессе для подготовки специалистов в области технологии машиностроения.
Параметры инструмента
Выберите вариант врезания инструмента
Выберите вариант выхода инструмента ф Автоматизированная система расчета параметров размерной настройки Файл Справка Выход
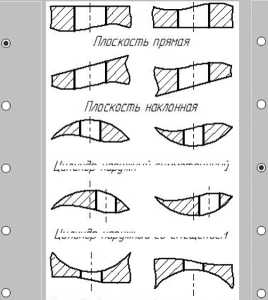
Цилиндр Внутренний симметричный
О
Цилиндр наружный симметричный
Цилиндр наружный со смещением
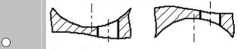
Цилиндр Внутренний со смещением
Метод обработки
•) Сверление О Центровование ОЗенкерование О Зенкование О Развёртывание
Сверло
О Спиральное одноплоскостная заточка
@ Спиральное с двойной заточкой
О Спиральное для сверления чугуна (В.Г. Жирова)
О Спиральное с закруглёнными режущими кромками
О Спиральное со стачиванием перемычки
О Спиральное с прорезной перемычкой
О Кольцевое (или со сменными пластинками)
О Пушечное
О Ружейное
О Шнековые
О Эжекторное
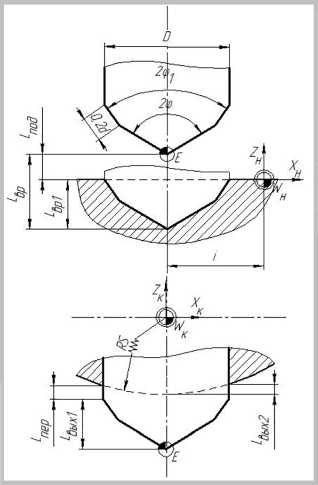
Диаметр инструмента, D, мм
Угол заточки, 2ф, 0
Дополнительный угол, 2ф1, 0
Режимы разания и условия
Скорость резания, м/мин
Подача на оборот при устойчивом реазнии, Подача на оборот при вреазнии, мм/об
Подача на оборот при выходе, мм/об
Длина между системами координат, мм
Длина подвода инструмента, 1лод, мм
Длина перебега инструмента, Lnep, мм Радиус цилиндра, RS, мм
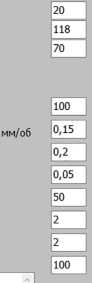
Расчёт
Очистить
= ==Параметры инструмента===
D = 20,000 мм 2ф = 118,000° 2ф1 = 70,000° ====Параметры врезания==== LBpl = 7,907 мм 1под = 2,000 мм 1вр2 = 0 мм
Lep = 9,907 мм 2нвр1 = 2,000 2нвр2 = -7,907 ====Параметры выхода==== 1вых1 = 7,907 мм
Lnep = 2,000 мм 1вых2 = 0,501 мм в частном случае=к 2нвых1=-150,000 2нвых2=-159,405 2квых1=-100,000 2квых2=-109,405 ===Время обработки= = = =
Время врезания = 1,485 с
Время устойчивого резания = 26,784 с
Время выхода = 7,091 с
Время обработки = 35,360 с
Рисунок 7 – Интерфейс программного обеспечения