Adaptation of method combined rolling-extruding for production of semi-finished products from graded waste chip of aluminum alloys
Автор: Zagirov Nikolai N., Sidelnikov Sergey B., Bespalov Vadim M., Burmistrov Konstantin V.
Журнал: Журнал Сибирского федерального университета. Серия: Техника и технологии @technologies-sfu
Статья в выпуске: 2 т.8, 2015 года.
Бесплатный доступ
Was proposed a device for obtaining deformed semi-finished products from chip of aluminum alloys with use combined methods of treatment. Carried experiments to obtain rods and receipted data about their mechanical properties.
Chip, aluminum alloys, combined rolling-extruding, mechanical properties, rods, density
Короткий адрес: https://sciup.org/146114940
IDR: 146114940
Текст научной статьи Adaptation of method combined rolling-extruding for production of semi-finished products from graded waste chip of aluminum alloys
One of promising area of development continuous extruding technology based on installations of combined rolling-extruding is the use them for obtaining rods and wire from non-compact metallic materials of which occupies a special place graded granular chips of
Known a device for force feeding of non-compact material (powder) into the rolls of rolling mill and rolling it in horizontal direction as a metal strip [1], consisting of a bunker a container and auger with a drive and setpoint block. Due to the pressure generated by auger in the container, the device sequentially seals, and moves metal material and through setpoint block send it to the rolls located in a horizontal plane. However, this device allows obtaining only rolled sheet in the form of tapes, which significantly limits the range of products.
Partial solution to this problem other version of the device [2] used specifically to obtain the wire and profiles. The device includes two rolls one of which is made with a creek, the other – with a ledge, which together covered caliber at the output of which is set matrix with the ability to clamp it to the rolls, and roll to capture the non-compact material and its supply to the caliber. This device allows realizing process of combined rolling-extruding and obtaining press-articles of various forms from non-compact metallic materials (powders, chip, granules, etc.). However, the degree of compaction, which is created with an additional roll not always sufficient to obtain a relatively compact billet. In this regard it is difficult in consequence to capture and compress metal by rolls, which significantly affects the quality of study material and the formation of the required press-articles structure. Therefore, there is no way to get the wire and profiles of the non-compact materials with controlled structure and improved mechanical properties.
Improve efficient of the process obtaining wire and profiles from non-compact materials allows the design of the device, protected by a patent for an invention [3]. Device circuit is shown in Figure 1, includes a heated container 1, prechamber 2, drive auger 3 placed in a container 1, roll with a creek 4 and roll with a ledge 5 forming a closed box pass 6 at the output of which is set matrix 7 with hydraulic clamp 8. The matrix is equipped with heaters 9.
Non-compact metallic material (chip) continuously supplied to the container 1 and using rotating auger 3 moves to the tapered portion of prechamber 2. In process of creation the necessary pressure using rotating auger 3 material is compacted and the formation of a more or less compact billet in a rectangular plot of prechamber 2. And shape of the inner cavity and dimensions of prechamber 2 chosen so that compaction of billet takes place gradually with the transition from round section diameter D to rectangular with maximum dimensions h max x b.
Next driven to rotate rolls 4, 5 and billet enters in formed by these rolls closed caliber 6, filling it, crimped by rolls, moving to a matrix 7 pursed to the rolls by hydro clamp 8, extruded and pressed in the form of press-articles with given shape, for example, profiles circular section diameter d П through the matrix 7.
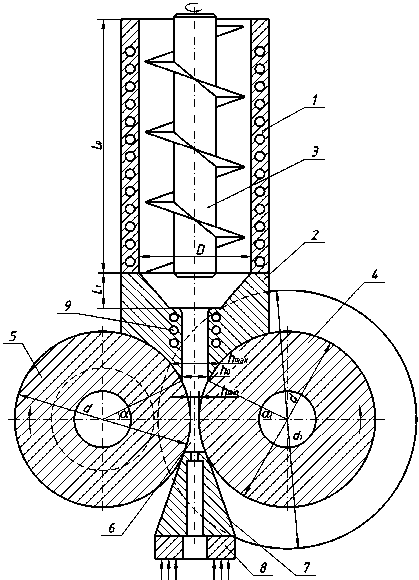
Fig. 1 Scheme of the device to obtain wire and profiles from non-compact materials
The presence of an intermediate prechamber allows before rolling stage make preliminary briquetting of non-compact material and form in the prechamber rectangular billet with the necessary degree of compaction sufficient for subsequent deformation by extruding metal by rolls through the hole of matrix. In this case, to reduce resistance to deformation of the material and therefore efforts extrusion prechamber can be equipped with additional heaters provide a stable temperature conditions in the deformation center.
For sustainable process of compaction in the prechamber necessary that coefficient of material compaction k у ranges between 3 to 5 [1], that is the ratio of the cross sectional area F 1 working cavity of prechamber diameter D by logging in to the granular material and cross sectional area F 0 compacted rectangular billet output from it equal
F- = k« = 3...5, 2 F0
where F = ,_ ; F = b . h0.
Having expressed the value F through the height of caliber in the smallest section h which implements the maximum compression ε during rolling, get
F =b-h
0 = min
1 1-ε.
Substituting formula (2) into equality (1) and taking into account that to ensure relizability of process combined rolling-extruding [4] compression in rolling should be at least 50 % (ε = 0,5), obtain as a result that diameter of the prechamber on the border of the container, where begins forming billet, must be chosen from the ratio
D = ( 2,8...3,6 ) b ⋅ h min , (3) where b – width of closed caliber; h min – height of closed caliber at the lowest section.
Checking of the proposed design of the device was carried out in laboratory conditions of department of metal forming Siberian federal university. Given the deduced formula were designed and manufactured rolls with diameter 200 mm, that after mounting them on one cage rolling mill DUO used to produce rods diameter of 7 and 9 mm. Caliber size in the smallest cross section was h min x b = 7 x 15 mm, and the size of compacted billet output from prechamber were 14 x 14,5 mm. As the test material used granular chips of aluminum alloy АД31. When the diameter of prechamber on the border with the container D = 30 mm compaction of material at the outlet of the prechamber was about 50–60 %. Compression in a closed cavity between rolls on the stage of rolling provided further compaction to a relative density of 85–90 %, and a subsequent extrusion through the matrix rod density reached values 97–99 %.
To estimate the level of mechanical properties obtained press-articles from each of the rods were taken a few fragments from which were grind out the samples with a standard aspect ratio for tensile testing. Tests themselves were carried out on a universal testing machine LFM400 with fixation of the entire course of the deformation in a separate protocol. Processing of received data which was carried out for five samples for each size with the use of well-known formulas showed that: range of values the ultimate tensile strength nB for rod 0 7 mm ranges from 190 to 200 MPa, for rod 0 9 mm - from 175 to 185 MPa; range of values relative elongation 5 for rod 0 7 mm is from 14 to 18 %, and for rod 0 9 mm — 16—20 %
Set out the specific application area of rods and obtained from them by drawing wire from chips alloy АДЗ1 quite difficult. However, it can be assumed that, because of the relatively low cost of production and taking into account achieved mechanical properties they can be used, for example, consumer goods products, in particular, the strapping wire irresponsible use. For these products mechanical properties are not strictly regulated, but it is believed that in the solid (unannealed) state tensile strength for them to be at least 140–160 MPa, and elongation – at least 5–10 %.