Аглопорит, полученный из отходов углеобогащения, как заполнитель для легких бетонов
Автор: Абрамов Анатолий Кузьмич, Ефимов Виктор Иванович, Никулин Иван Борисович
Журнал: Горные науки и технологии @gornye-nauki-tekhnologii
Статья в выпуске: 11, 2013 года.
Бесплатный доступ
Разработана новая технология переработки мелкодисперсных отходов углеобогащения в аглопорит, применяемый как заполнитель в конструкционных легких бетонах, дорожном строительстве. В сравнении с широко используемым керамзитом, аглопорит имеет значительные преимущества: выше прочность, ниже себестоимость, возможность производства из промышленных отходов.
Отходы углеобогащения, аглопорит, легкий бетон, аглопоритобетон
Короткий адрес: https://sciup.org/140215638
IDR: 140215638
Текст научной статьи Аглопорит, полученный из отходов углеобогащения, как заполнитель для легких бетонов
В России накоплено свыше 85 млрд т твердых угольных отходов и в соответствии с энергетической стратегией развития объем ежегодно образующихся отходов в ближайшие годы может превысить 3 млрд т. При этом основная часть отходов, 85%, приходится на Кузбасс. Из всех угольных отходов только 3% используется в создании товарной продукции [1].
Крупнотоннажные отходы производства, содержащие минеральные материалы могут служить сырьём для производства строительных материалов. В современном строительстве резко возрастает потребность в высокопрочных, энергосберегающих строительных материалах, которые обладают развитой сырьевой базой и изготавливаются с использованием малозатратных технологий.
Разработана новая технология переработки мелкодисперсных отходов углеобогащения на обогатительных фабриках в аглопорит, применяемый как пористый заполнитель в конструкционных легких бетонах и в дорожном строительстве. В сравнении с широко используемым керамзитом, аглопорит по данной технологии имеет значительные преимущества: при равной плотности выше прочность, ниже себестоимость, возможность производства из промышленных отходов.
Начало интенсивного развития производства пористых заполнителей (к которым относится и аглопорит) приходится на 60-е гг. прошлого века и наибольший выпуск был достигнут в 1989г. Но экономический кризис 1990-х г.г, выросшие требования к энерго -экологической безопасности обусловили резкое снижение спроса на пористые заполнители и явились основными причинами уменьшения их выпуска, закрытия многих предприятий. В настоящее время в России пористых заполнителей выпускают чуть более 20% от объема 1989г[2].
Отметим факторы и условия, которые могут определять развитие производства пористых заполнителей. Их можно разделить на объективные, которые не зависят от организаторов строительства, и субъективные, зависимые от участников строительного производства и топливно-энергетического комплекса.
Объективные факторы:
-
1. Мощная сырьевая база, включая крупнотоннажные отходы промышленности, в первую очередь топливосодержащие. Многочисленные работы показали, что замена природного глинистого сырья на топливосодержащие отходы (углеотходы, золошлаковые материалы ТЭС) может снизить расход топлива на изготовление заполнителей несколько раз.
-
2. Пористые заполнители, как и все керамические материалы, обладают высокой стойкостью к воздействию агрессивных сред и относятся к долговечным материалам. Мировая практика имеет многочисленные примеры применения легких бетонов на пористых заполнителях в строительстве уникальных сооружений, в том числе гидротехнических. Некоторые из них построены около 2 тыс. лет назад. Это, например, гидротехнические сооружения в Анконе (Италия), построенные в начале нашей эры и которые эксплуатируются и в настоящее время [2].
-
3. Технология получения пористых заполнителей проста, отличается высокой механизацией, ее легко автоматизировать.
-
4. Основная часть территории России представляет собой равнину, 85% площади которой покрыто осадочными образованиями и 25% горными породами, из которых производится крупный заполнитель щебень. Перевозка щебня в наших условиях составляет 300-500 км, что определяет высокую, постоянно растущую их стоимость.
-
5. Пористые заполнители экологически чистые материалы.
Субъективные факторы:
-
1. Пористые заполнители имеют широкую сферу применения в строительстве и в других отраслях народного хозяйства.
-
2. Для получения качественного бетона важным условием является надежное обеспечение постоянства зернового состава заполнителей. Обследование 86 предприятий ЖБК показало, что в дозаторы от замеса к замесу поступают крайне неоднородные по зерновому составу заполнители. Так, в гранитном щебне 5-20 мм содержание фракций мельче 5 мм (каменной крошки и пыли) колеблется от 0.5 до 37%, что почти в 3 раза превышает пределы, установленные ГОСТ 8267-93, колебания в
-
3. В строительной индустрии России наблюдается нехватка щебня и песка. В 2006 году было поставлено около 170 млн. м3 различных заполнителей, а нужно было в 2-а раза больше. Недостающий щебень в Европейской части России приходится завозить с Украины и Белоруссии. Доля затрат на транспортировку составляет почти 70% от суммы затрат на горные работы [4]. Компенсировать нехватку сырья для производства заполнителей нужно использованием промышленных отходов, в том числе производством пористых заполнителей. В развитых странах их доля составляет 60% от общего объема заполнителей.
соотношении фракций 5-10 и 10-20 мм превышает пределы ГОСТ в 4 раза. А анализ состояния технологии производства природных заполнителей в карьерах показывает, что гарантированное сохранение постоянства зернового состава заполнителей нереально и неосуществимо в обозримом будущем [3]. В производстве пористых заполнителей таких проблем нет.
Разработанная технология позволяет производить аглопорит разных форм и размеров. На рис. 1 представлены образцы формованного, обожженного аглопорита в виде кубиков, колец и цилиндров.
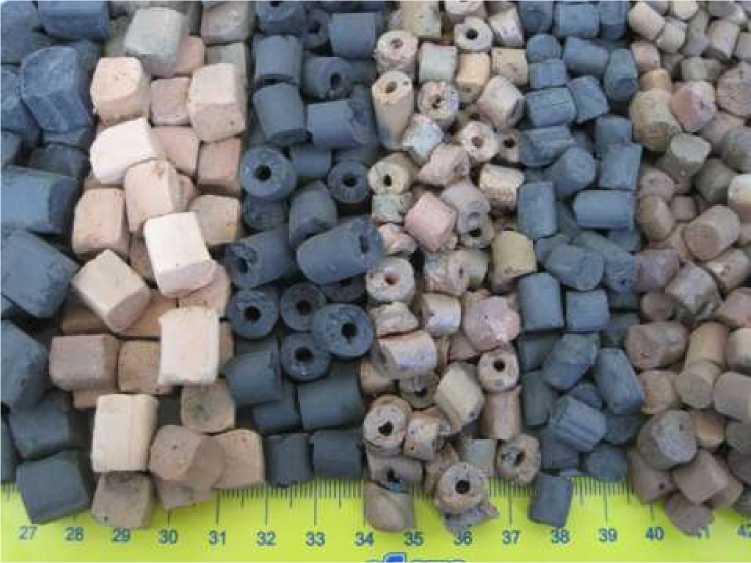
Рис. 1. Образцы формованного, обожженного аглопорита в виде кубиков, колец и цилиндров.
В табл.1 приведены геометрические характеристики керамзита шарообразной формы, аглопорита в виде цилиндров и кубиков.
Характеристики форм заполнителей.
Вид формы |
Разме р |
Формула определе ния поверхно сти |
Размер поверхнос ти, см2 |
Коэффици ент поверхнос ти |
Прочность на сжатие |
Примеча ние |
Шар |
Диаме тр – 1см |
S =л d2 |
3.14 |
примем коэффици ент S шара за 1 |
Минимальн ая. Сила разрушения прилагается в точке |
Форма керамзит а |
Цилин др |
Диаме тр – 1см, высот а – 1см |
S =л dh +лd2/2 |
4.71 |
1.5 |
Средняя. Сила разрушения прилагается по линии |
Форма аглопори та |
Куб |
Ребро – 1см |
S = 6a2 |
6.0 |
1.9 |
Максималь ная. Сила разрушения прилагается по поверхност и |
Форма аглопори та |
Самая привлекательная форма заполнителя та, у которой более высокая поверхность и прочность. Данные характеристики обеспечивают повышенную прочность бетона. Следовательно, наиболее оптимальной формой заполнителя является куб. Применяя аглопорит в виде колец можно снижать плотность и теплопроводность бетона.
В табл. 2 приведены технические характеристики аглопорита.
Технические характеристики (Испытания проведены по ГОСТ 975886 Методы испытаний)
№, п/п |
Наименование показателя |
Единица измерения |
Требования по ГОСТ 9757-90 |
Фактически полученные результаты |
1 |
Внешний вид |
- |
Гранулы |
Гранулы: цилиндры, кубики |
2 |
Фракционный состав |
мм |
5 - 20 |
5 - 10 10 – 15 15 - 20 |
3 |
Насыпная плотность |
кг/м3 |
250-900 |
770 |
4 |
Марка по насыпной плотности |
- |
250-900 |
800 |
5 |
Прочность при сжатии (в зависимости от плотности) |
МПа |
Не менее 1.0 |
Более 10 |
6 |
Марка по прочности (в зависимости от плотности) |
- |
Не менее П150 |
нет аналога |
Как известно, основой строительства является сборный железобетон и в последние годы он претерпевает качественные изменения в направлении уменьшения массы, теплопроводности. Это реализуется путем внедрения легких бетонов на пористых искусственных заполнителях. Модифицированные конструкционные легкие бетоны изготавливают, так же как и тяжелые бетоны аналогичных конструкций, но при этом экономия массы составляет 20-50%. Также снижается теплоотдача зданий, повышается их уровень теплозащиты, паропроницаемости, что ведет к повышению комфортности проживания. В табл. 3 приведены основные преимущества конструкционных легких бетонов в сравнении с равнопрочными тяжелыми бетонами[5].
Основные преимущества конструкционных легких бетонов классов по прочности на сжатие В15-В50 в сравнении с равнопрочными тяжелыми бетонами.
Свойства |
Преимущества |
Эффект |
Плотность |
Меньше на 20-50% |
Снижение массы конструкций, зданий, сооружений на 20-50% – сокращение расходов бетона, арматуры, уменьшение осадки здания |
Уровень нижней и верхней границы области микротрещинообразования |
Больше на 16-25% |
Выше граница перехода линейной ползучести в нелинейную, отсюда больше эффективность преднапряжения арматуры в конструкциях. Выше на 20-30% предел выносливости бетона при действии многократно повторных нагрузок сжатия. Меньше на 16-23% виброползучесть. Выше предел длительной прочности бетона |
Коэффициент динамического упрочнения Предельная деформативность в режиме ударного нагружения |
Больше на 17-25%. Больше на 15-26% |
Выше ударная вязкость - меньше относительное количество разрушающихся оголовков забиваемых свай. Выше долговечность свайных ростверков зданий |
Морозостойкость Водонепроницаемость |
Больше на 2-5 марок Больше на 1-3 марки |
Увеличение долговечности конструкций и надежности зданий и сооружений в эксплуатации |
Коэффициент теплопроводности |
Меньше в 2.5-3.5 раза |
Сокращение до 25% теплопотерь через наружные стены зданий в местах сопряжений с несущими конструкциями, снижение теплоотдачи здания. |
Стойкость к огневому воздействию |
Больше на 0.3-0.5 ч |
Увеличение предела огнестойкости конструкций по несущей способности, повышение пожаробезопасности здания |
Также легкие бетоны дают значительную технико-экономическую эффективность и в дорожном строительстве.
Аглопорит может применяться в различных слоях дорожной конструкции:
-
- в составе асфальтобетонной смеси для верхнего слоя дорожной одежды;
-
- в качестве минеральной составляющей в битумоминеральной смеси;
-
- в составе цементобетона;
-
- в составе слоя основания (укрепленного малыми дозами цемента, металлургическими шлаками).
Особенно целесообразно применять аглопорит в асфальтобетонах в районах с резким континентальным климатом, что обусловлено их высокой теплоизолирующей способностью и низкой трещиностойкостью, а также в районах, где нет природных заполнителей[6].
Из аглопорита были приготовлены легкие бетоны. В табл. 4 приведены технические характеристики легкого бетона.
Таблица 4.
Технические характеристики легкого бетона из аглопорита
№, п/п |
Наименование показателя |
Единица измерения |
Требования по ГОСТ 258202000 |
Фактически полученные результаты |
1 |
Плотность |
кг/м3 |
не выше 2000 |
1680 |
2 |
Марка по плотности |
- |
не выше Д2000 |
Д1700 |
3 |
Прочность на сжатие |
МПа |
не ниже 15 |
62 |
4 |
Марка по прочности |
- |
не ниже М150 |
М600 |
5 |
Класс бетона |
- |
не ниже В 15 |
В45 |
6 |
Назначение |
- |
конструкционный |
конструкционный |
Согласно современным требованиям [7, 8] , легкие бетоны могут быть отнесены к высокопрочным в том случае, если выполняется условие уравнения
Рсж / ρб ≥ 25, где Рсж – прочность бетона при сжатии в МПа, ρб – плотность бетона в сухом состоянии в кг/дм3.
В нашем случае, Рсж / ρб = 62/1.7 = 36.5
Для сравнения характеристик по теплопроводности между аглопоритобетоном и керамзитобетоном приведены данные их коэффициентов теплопроводности при различных плотностях.
Сравнение значений коэффициентов теплопроводности аглопоритобетона и керамзитобетона при различных плотностях.
Плотность, кг/м3 |
1600 |
1800 |
Примечание |
Аглопоритобетон, л, Вт/м К |
0.62 |
0.74 |
Замеренные данные |
Керамзитобетон, л, Вт/м К |
0.6 |
0.7 |
Табличные данные. ТКП 45-2.0443-2006 (02250) «Строительная теплотехника» |
Превышение значений л, % |
3.3 |
2.8 |
Превышение теплопроводности аглопоритобетона над керамзитобетоном незначительное. |
Таким образом, из выше изложенного видно, что полученный из отходов углеобогащения аглопорит и легкие бетоны на его основе имеет высокие технические характеристики, востребованы на рынке строительных материалов. Так как аглопорит изготавливается из углесодержащих отходов, то его себестоимость значительно ниже, чем у керамзита. Угля, содержащего в сырье, достаточно для процессов сушки, обжига аглопорита и имеется возможность часть тепла передавать на технологические нужды обогатительной фабрики.
Список литературы Аглопорит, полученный из отходов углеобогащения, как заполнитель для легких бетонов
- Ефимов В.И. Приоритетные инновационные направления ОАО ХК «СДС-Уголь». «ТехГорМет 21-век»./Национальный минерально-сырьевой университет «Горный»: сб. тезисов докл. III Международной научно-практ. Конф. -СПб., 2012. -С. 48-49
- Казаков В.Б., Попов С.М., Стоянова И.А., Харченко В.В. Методологические основы оценки ценности углепромышленных отходов для расширения масштабов их использования в хозяйственной деятельности//Уголь, 2012. -№4. -С.50-52.
- Петров В.П., Токарева С.А. Пористые заполнители из отходов промышленности//Строительные материалы, 2011. -№12. -С. 46-50.
- Ночной А.В., президент Союза производителей бетона. Заполнители -основа качества бетона//Технология бетона, 2006. -№1. -С. 60-61.
- Орентлихер Л.П. XXI век -век легких бетонов//Технология бетонов, 2010. -№1/2. -С. 31-33.
- Ярмаковский В.Н., Семенюк П.Н. и др. Полифункциональные легкие бетоны для ресурсоэнергосберегющего индустриального домостроения//Строительные материалы,2012. -№4. -С. 4-10.
- Прокопец В.С., Галдина В.Д., Подрез Г.А. Асфальтобетоны на основе пористых заполнителей Западной и Восточной Сибири.//Строительные материалы, 2009. -№11. -С. 26-28.
- Фаликман В.Р., Сорокин Ю.В., Горячев О.М. Высокопрочный легкий бетон: технология и свойства//Бетон и железобетон, 2005. -№2. -С. 8-11.
- Held M. Hochfester Konstruktions-Leichtbeton, Beton, Juli 1996, S.411-415.