Аналитическое исследование температурного поля поверхностного слоя валков горячей прокатки алюминиевых сплавов
Автор: Гречников Ф.В., Уваров В.В.
Журнал: Известия Самарского научного центра Российской академии наук @izvestiya-ssc
Рубрика: Механика и машиностроение
Статья в выпуске: 2 т.5, 2003 года.
Бесплатный доступ
Получено аналитическое решение уравнения теплопроводности для вращающегося цилиндра, подверженного циклическому нагреву в контакте с горячим металлом и последующему охлаждению поверхности эмульсией. Данное решение доведено до рабочей методики расчета температур в зависимости от числа оборотов валка и режимов прокатки для рабочих циклов и пауз между пропусками полос. Рекомендации по стабилизации тепловой выпуклости и доотпуску штатных валков в первой клети для повышения их эксплуатационной стойкости могут быть использованы в практике прокатного производства.
Короткий адрес: https://sciup.org/148197769
IDR: 148197769
Текст научной статьи Аналитическое исследование температурного поля поверхностного слоя валков горячей прокатки алюминиевых сплавов
-
1 Самарский государственный аэрокосмический университет,
-
2 Волжский филиал Института металлургии и материаловедения им. А.А. Байкова РАН, г. Самара
Получено аналитическое решение уравнения теплопроводности для вращающегося цилиндра, подверженного циклическому нагреву в контакте с горячим металлом и последующему охлаждению поверхности эмульсией. Данное решение доведено до рабочей методики расчета температур в зависимости от числа оборотов валка и режимов прокатки для рабочих циклов и пауз между пропусками полос. Рекомендации по стабилизации тепловой выпуклости и доотпуску штатных валков в первой клети для повышения их эксплуатационной стойкости могут быть использованы в практике прокатного производства.
Температурный режим поверхностного слоя валков горячей прокатки алюминиевых сплавов определяет как качество горячекатаных полуфабрикатов (плит, полос и рулонов), так и срок службы валков и зависит от целого ряда технологических параметров процесса прокатки и условий охлаждения валков.
В процессе прокатки поверхностный слой рабочих валков прокатного стана подвергается циклическому нагреву в контактной зоне и последующему эмульсионному охлаждению при выходе из контакта на каждом обороте валка. Амплитуда колебаний температуры в течение оборота с удалением от поверхности валка интенсивно уменьшается, и на некоторой глубине становится равной нулю. В более глубоких слоях она при длительной прокатке монотонно возрастает. В паузах между пропусками полос охлаждение эмульсией приводит к снижению температуры как в поверхностном слое, так и в более глубоких слоях валка.
Детальное систематическое исследование температурного поля активного поверхностного слоя, а так же глубинных слоев валка экспериментальными методами трудно осуществимо. Поэтому в данной работе, используя общие подходы к решению подобных задач [1, 2], приводятся расчетные методы и их результаты применительно к реальным режимам эксплуатации валков горячей прокатки алюминиевых сплавов многоклетьево-го стана 2800 [7].
Используя аддитивные свойства интегралов уравнения теплопроводности, температурное поле в валке рассматривается как сумма температурных полей от отдельных тепловых потоков. Результирующую температуру в момент контакта валка с горячим металлом обозначим через t’, а при отсутствии контакта через t= t» -t’», где t»- температура, обусловленная потоком тепла в массу валка, накопленного тонким его поверхностным слоем в очаге деформации, t’»- температура, обусловленная потоком тепла с поверхности валка при его эмульсионном охлаждении. В расчетах температурных полей используются следующие общепринятые обозначения:
-
X - коэффициент теплопроводности,
а - коэффициент температуропроводности, р - плотность тела, с - удельная теплоемкость, к - коэффициент теплопередачи
(вт/м2град), х - расстояние от поверхности (м), тс - время контакта (сек),
-
V- скорость прокатки (м/сек).
Составляющая tпдля поверхности валка рассчитывается через коэффициент тепло-усвоения идеально контактирующих тел т и функцию передачи тепла от полосы к валку через тонкую пленку эмульсии G по формуле [1]
/ m t П = t 0 + Г G(t пол - t 0 ) , m +1
2т t " = 1 -------- п V т + Ат
- t п ) exP
V
---x----
4 а (т + А т ) у
а величина Ат находится из условия tП = tП при т = 0. Выразив время через число оборотов т = т об ■ n = nD в / V m =
( ^ G p ) пол \ ( Х с Р ) вал
для случая однократного контакта валка с металлом на первом обороте, получим температуру от потока тепла на глубине х
G = 1
-
f к exp -
V
2 a т пол с
X
пол
А f erfc / V
kja т пол с
Х пол
A
/
индекс “ пол ” - относится к прокатываемой полосе, а “ вал ” - к телу валка.
Усреднив теплофизические свойства алюминиевых сплавов и валковых сталей и
// (tП,(р tП,(0)) f Р А tx = A I------Т expl л 2
V n+A2 V n+A J где в = x2 = x2 V
4 a т об 4 a n D в ’
приняв время контакта т с= 0,08 - 0,01 с; к = 50^10 4 вт/м 2 град при 8 = 1 - 2 мкм [1], получим т =2,077, т/(т+ 1) = 0,675, G=0,96, h =Gm/m+1=0,65. Применительно к непрерывному процессу прокатки под т 0 будем понимать температуру поверхности валка перед входом в очаг деформации. Тогда для любого числа оборотов валка n получим
A = - b- = 0,302 4 ^ h п^ об Dd6
тоб - продолжительность одного оборота валка;
A h - абсолютное обжатие в данном проходе.
Для поверхности валка при x=0
t П( n ) = ht 0 + (1 - h ) t П ( n - 1) . (1)
//
// _ ( tП ,(1) t П ,(0) )
tП = А I -----7Г ,. (3)
V n + A
При вычислении составляющей t» момент окончания нагрева поверхности от контакта с полосой т = т с рассматривается как начальный момент распространения тепла вглубь валка от мгновенного плоского источника, интенсивность которого согласно [2,3] равна:
Отрицательный тепловой поток q эм , обусловленный охлаждением эмульсией, имеющей температуру 1эм, будем считать постоянным и равным значениям [3]:
q ЭМ = a [ t П ( t ЭМ t H ) ] (4)
Температурное поле, обусловленно е этим потоком, описывается формулой [2]
„ Xcp , , q = 2J (t П у п
- t п ) \к . (2)
Процесс распространения тепла от такого однократно действующего источника при нулевой начальной температуре в теории теплопроводности описывается формулой [3]
где
Л" _ 2 qЭМ т Д x пх р F V 2 40т )
' x 2 '
= exp--
+ А т ) V 4 а( т + А т ) ,
Тогда
t " = q
J пХ с р ( т

А
/ x 2 ) = exp
4a т
V У
- п
xx ъЕI' erfгЕу
x erf 2 Дит - табулируемая функция
интеграла вероятности,
tП - средне интегральная результирующая температура поверхности валка t n = k1 (tn - t П ) ’ k1 - коэффициент осреднения, равный k1= 1,05-1,10.
Совместное решение уравнений (4) и (5)
при х = 0 дает выражение:
tП ,( n )
где
/// tП
2 ак 4т ^
I—. —f1 2 ак 4т ^ V1 + ж J
t n
V
-
tЭМ
-
t H
k
сти
Результирующая температура поверхно-(без начальной температуры tН) от еди-
ничного теплового источника q и охлаждения эмульсией qЭМ будет равна:
t "_t"'= ___1___P/+ ^k1
t n t n t n ptn + I ----7---------x
2^ оккT
/^ п/c/ 1 1
t 3M t H
.
V
к
Выразив время т через число оборотов n и обозначив
= A^t n .. . )
k = 1
D ( n - k + 1)
tn ,( k - 1)
D ( n - k + 1) ]+ t 3 - Н
Нn
-----;= + I h 1 + н4п
4n - k + 1 + A 2 (1 + H4n - k + 1)"
После аналогичных преобразований температура на глубине х перед входом в очаг деформации выразится формулой:
tx ,( n )
= а ^К 'П. k )
k = 1
- tn ,( k - 1)
) D x ,( n - k + 1) ]+ t 3-Н
Hn ■ F (n ) 1 + H4n
+ tH
(9) здесь
D x ,( n - k + 1) = lexp( - У 2 + V^ H (1 - erfy )J D ( n - k + 1 ;
F ( n - k + 1) = exp( - У 2) - V ^ y (1 - erfy );
2 ак 'jП Db _ „
—I — = Н '
4 лА ср 4V

2 4 а л О в
W = 0,6218 4V при x=5 мм,
t ЭМ t H _ t
= t Э - Н
к с учетом уравнения (3), получим
_ . V n,(l) - tn,(0) ) _nn_ n = ,n +a (1+Hn) 1+Hn -Н.(6)
В реальном процессе прокатки источник q действует многократно, т.е. при каждом обороте валка. Поэтому первый член в формуле (6) должен быть представлен многочленом, в котором каждое слагаемое k пропорцио- нально температурным напорам
/
Vt n,(k) 1 n,(k-1)/> длительность действия которых последовательно уменьшается за время одного оборота. Полная (с учетом начальной) результирующая температура поверхности валка перед входом в очаг деформации применительно к любому полному числу оборотов п = 1,2,3... выразится формулой:
= 2 ak 44D H = 0,00155 a
" 4nA c pv ’ W при D B =
=650мм; (12)
W y=vn^iTT (13)
Процесс прокатки каждой полосы N=1,2,3,… состоит из рабочих циклов длительностью n p и пауз длительностью n пз . В паузах тепловые источники q не действуют, поэтому при
(nр + nпз ) N - n пз + 1 ^ n < (n р + nпз ) N принимается tn(n) = tn(n-1) " (14)
Тогда слагаемые сумм в формулах (7) и (9), соответствующие номерам оборотов в паузах, будут выпадать, так как для них
( t n ( n ) - t n ( n - 1) ) = 0 "
Для любого угла поворота валка отно- сительно точки выхода из контакта с металлом (щ) в приведенных формулах вместо n
следует принимать n 1 + 360 O .
Формулы (7) и (9) справедливы для среднего сечения валка при прокатке широких полос или листов, когда тепловым потоком вдоль оси валка можно пренебречь. В сечениях близких к кромке проката с учетом продольного теплового потока в часть валка, не контактирующую с металлом, но охлаждаемую эмульсией, величина tП в каждом проходе составит:
tП ,( n )
= A £ [ ( ' П« )
k = 1
^^^^^^^»
t П ,( k - 1) ) D ( n - k + 1) R ( n - k + 1) ] +
t x ,( n )
где
+ t Э - Н
R ( n ) + t H ,
^ [(t П,(k) t П,(k-1) )D,(n -k+1)R (n -k+1) ] + k=1
+ t Э - Н
F(,n ) R ( n ) + t H ,
0,2 zW
R ( n - k + 1) = 0,5 + 0,5 erf I , 1
V n - k +1
так как остальные вычисляются ранее при последовательном расчете температур для меньших значений n. С учетом этого положения разработана программа расчета температурного поля в поверхностном слое валка на ПЭВМ. Расчеты выполнялись применительно к пятой и седьмой клетям непрерывной группы листопрокатного стана 2800. В расчетах принималось D в = 640мм, t пол = 400°С, tЭМ = б7°С, tН= 60°С .
Вследствие циклического нагрева от контакта с прокатываемой полосой на дуге захвата и последующего эмульсионного охлаждения поверхности, а также наличия пауз между пропусками полос, изменение температуры в точках поверхностного слоя рабочего валка носит сложный характер. Немонотонное изменение температуры в течение одного оборота с быстро затухающей амплитудой колебания при удалении от поверхности валка приведено на рис.1 . Расчеты значений температур в зависимости от угла поворота валка показали, что такой характер изменения температуры при прокатке по различным режимам распространяется примерно до глубины х = 5 мм (активный слой). На этой глубине и в более отдаленных точках (тепловое ядро) в рабочих циклах прокатки температура монотонно возрастает с каждым
z - расстояние от кромки листа до данного сечения, мм.
Для расчета температур по выведенным формулам для заданного числа оборотов n в силу их рекурентности необходим предварительный последовательный расчет температур для всех предыдущих значений п . В развертке сумм формул (7) и (9) комплекс (n-ck+ 1) меняется от п для первого члена суммы (k =1) до 1 для последнего члена (k=n). На первый взгляд кажется, что расчет по этим формулам требует значительного объема вычислений, связанных с определением всех (от k = 1 до k=n) значений коэффициентов D, D x и F при каждом новом обороте n.
Фактически, при данном n из всех значений D (n - k+1) , D х , (п - к+1) и F (п - к+1) вновь требуется рассчитать только D (n) , D x(n) и F (n) ,
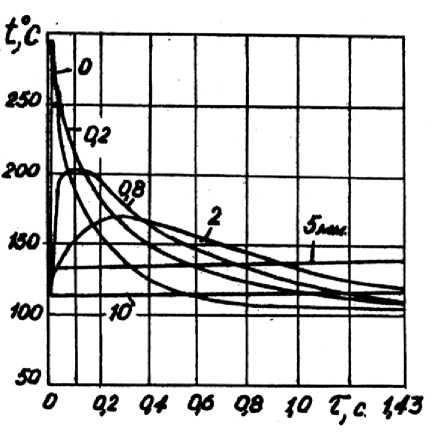
Рис.1 . Изменение температуры в поверхностном слое валка 0 640 мм в течение одного (шестого) оборота при прокатке второй полосы по режиму:
A h = 17 мм, V=1,4 м/с, а =9,700 Вт/(м 2 О С), n р =85, n пз =15.
оборотом валка. Рассчитанная по этой методике температура t x на данной глубине может быть использована в качестве граничного условия для расчета температурного поля в тепловом ядре более простыми известными методами.
Дальнейшие расчеты производились для целочисленных значений n с определением температур поверхности на входе в очаг деформации (tП), при выходе из него (t’П) и температуры на глубине 5 мм (tх). Они показали, что с увеличением числа оборотов n значения указанных температур в рабочих циклах прокатки непрерывно возрастают, но с затухающей скоростью. Во время пауз значения tП и tх снижаются также с замедляющейся скоростью постепенно приближаясь к tЭМ, но из-за их кратковременности далеко не достигая ее (рис. 2). При этом следует иметь в виду, что температура поверхности на каждом обороте циклирует между двумя соответствующими пунктирными линиями, что на рис. 2 не показано.
В процессе непрерывной прокатки полос N = 1,2,3,... со сравнительно короткими паузами между их пропусками через валки, как видно из рис.2, кривые изменения температур tП, tх ,t’П от числа оборотов n распо-
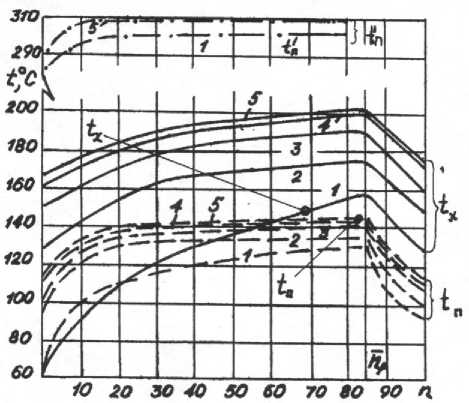
Рис.2 Зависимость температур поверхности валка ∅ 640 мм на выходе (t’ П ), входе (t П ) в очаг деформации и на глубине 5 мм (tx) от числа оборотов (n) при прокатке полос N=1,2….5 gjрежиму: ∆ h = 17 мм, V=1,4 м/с, α =9,700 Вт/(м 2 ОС), n р =85, n пз =15.
лагаются одна над другой с нарастанием N, постепенно сближаясь, но не сливаясь полностью. Однако, учитывая погрешность в выборе значений исходных параметров для расчета и требуемую в практике точность в определении температур порядка 5-10°С, можно считать, что после прокатки 4...5 полос в активной зоне рабочего валка устанавливается квазистационарный температурный режим. К аналогичным выводам пришли авторы работы [2], экспериментально изучавшие тепловой режим работы валков. Установившийся температурный режим в тепловом ядре устанавливается значительно позднее.
Наибольший практический интерес представляют значения температур поверхности и на глубине 5мм для начала прокатки (конца пауз) (tП, n пз , tх, n пз ) и конца прокатки полос (tП, n р , tх, n р ) в квазиустановившемся режиме, наступление которого в дальнейших расчетах принято при прокатке пятой полосы. Для исследования влияния режимов прокатки и охлаждения на значения этих температур проведен расчет 24 вариантов температурного поля поверхностного активного слоя.
Расчеты показали, что на тепловой режим активного слоя оказывает влияние большое число параметров: абсолютное обжатие ∆ h, скорость прокатки V, интенсивность эмульсионного охлаждения, характеризуемая коэффициентом теплоотдачи α , длина прокатанной полосы выраженная числом рабочих оборотов валка n р , длительность пауз τ пз , представленная в расчетах числом оборотов валка в паузах n пз = V τ пз / π Dв .Влияние других параметров режима (tпол, tЭМ, tН) не исследовалось, так как диапазон их изменения незначителен, и они принимались постоянными.
Наибольшее влияние на значения указанных температур оказывает абсолютное обжатие и скорость прокатки. Эта зависимость представлена графически на рис.3, который построен по данным расчета температур по разработанной методике при постоянных базовых значениях других параметров режима : nр =85, τпз ,=20с, α=7500 Вm/
(м 2 град). Зависимость tj,n где j=П,x , n = n р ,
∆h nпз , от A = 0,3024 D при V=const в ис- в следованном диапазоне изменения ∆h - практически линейная, а от скорости V - имеет более сложный характер.
Раздельное влияние каждого из трех ос- тальных параметров i=nр , τпз , α на температуры tj,n(i) оценивалось коэффициентами Kj,n(i), рассчитываемыми по формуле:

Рис.3. Зависимость установившихся температур поверхности (----) и на глубине
5 мм (-----) валка диаметром 640 мм в конце прокатки
K i , n ( i ) =
t j , n ( i ) - tЭМ tj , n ( i *) - tЭМ
в которой значения tj,n(i) определялись из температурного поля, рассчитанного для двух других, отличных от базового, значений параметров i. При этом для каждого нового значения i расчет температур tj,n(i) производился для двух - трех вариантов режима (сочетаниях основных параметров ∆h и V), для которых величина tj,n(i*) известна для базового значения i* и выбирается по графику (рис.3). Рассчитанные таким образом два-три Kj,n(i) для каждого конкретного значения i практически (с точностью до 3 %) совпадали. Рассчитано также не сколько вариантов режима одновременно с двумя новыми значениями i, отличными от базовых i*. Оказалось, что эффект попарного влияния параметров ( на Kjn(() незначителен (2-3 %) и им можно пренебречь, а совместное их влияние определять произведением значений коэффициентов K. п(г) для соответствующих i, каждо е из которых является однопараметрическим. Следует также отметить, что длительность рабочих циклов n р практически не влияет на температуры tП, nпз , и tх, nпз в конце пауз, а длительность пауз τпз (в диапазоне от 15 до 50 с) - на температуры tП, nр , tх, nр в конце рабочих циклов прокатки полос. В то же время интенсивность эмульсионного охлаждения а влияет на температуры как в конце прокатки, так и в конце пауз, причем более значительно полос при nр = 85 (а) и в конце пауз длительностью
Т пз = 20 с (б) от коэффициента обжатия
A = 0,302 4 ∆ h
в
и скорость прокатки V (цифры у
кривых) для tnan =400° С, tH =60°С , tЭМ =67°СО и а = 7500 Вт/(м 2 град).
на температуры поверхности валка.
Графики зависимости коэффициентов Kj,n от параметров i представлены на рис.4. Используя их совместно с графиками на рис. 3, можно, не прибегая к расчету по формулам (1), (5), (7), определять значения искомых температур из формулы (16) при квази-установившемся режиме прокатки с достаточной для практики точностью.
При проведении технических расчетов необходимо знать коэффициент теплоотдачи
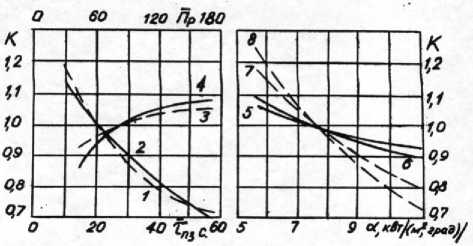
Рис. 4. Зависимость коэффициентов в формуле (18) от параметров режима прокатки и охлаждения :
1 К n ( Т пз ), 2- К , П з ( Т пз ), 3- К п , n р ( n р ),
4- Kx , n р ( n р ), 5- K x П пз ( а ), 6- K x n р ( а ),
7- КпПр (а), 8 - Кп, Ппз (а), а при охлаждении поверхности валка эмульсией, подаваемой из спрейерного устройства (коллектора) под давлением через систему форсунок. Теплофизика и гидродинамика такого процесса весьма сложны; на величину а влияет большое число факторов: удельный расход охладителя, конструкция форсунок и их расположение по углу поворота и длине валка, расстояние от форсунок до поверхности, скорость вращения валка и пр. Расчет α по критериальным зависимостям, полученным в опытах по моделированию процесса спрейерного охлаждения различных объектов [4, 5 ], из-за сложности воспроизведения всех параметров процесса дает резко различные значения - от 2000 до 20000 Вт/{м2 град). Авторы работ [1, 6] рекомендуют α от 12000 до 16000 Вт/(м2 -град). В работе [8] приводятся обобщенные по станам холодной прокатки зависимости а от удельного расхода охладителя q при подаче его через форсунки круглой и щелевой формы различных размеров, при q до 5 л/м.с. Экстраполируя эти данные до значений 10-17 л/м.с, принятых на стане горячей прокатки 2800, получим соответственно α= 6000 + 11000 Вт/{м2.град). Температуры поверхности в конце прокатки полос, рассчитанные при принятых значениях aa, близки к выборочно замеренным на рабочих валках клети № 5 стана 2800 (125 - 145°С) при прокатке по различным режимам [7].
Рассмотрим некоторые практические приложения полученных результатов расчета. Важной характеристикой режима работы стана является устойчивость теплового профиля рабочих валков при прокатке полос по различным режимам и прокатке одной полосы, которая непосредственно связана с величиной изменения температуры tx на поверхности теплового ядра (на глубине 5 мм). Анализ заводских данных по сочетанию параметров ∆ h, V, L( n р ) технологических режимов прокатки разных сплавов показывает, что значение указанной температуры в конце прокатки полос ( tx, n р ) может изменяться от 170 до 215°С в клети № 5 и от 150 до 195 °С в клети №7 при α =7500 Вт/(м 2 . град)=const.
Подчеркнем, что такие колебания температуры (следовательно, и теплового профиля) при переходе от одного режима прокатки к другому могут быть предотвращены (исключая крайние: самый легкий и самый тяжелый) соответствующим изменением интенсивности эмульсионного охлаждения. Однако в практике этот прием используется недостаточно в связи с отсутствием информации о зависимости теплового режима от режимов прокатки и охлаждения. Изменение температуры tx , при прокатке одной полосы от начальной tx, n пз ( в конце пауз ) до конечной tx, n р (в конце прокатки полосы) также связано со стабильностью тепловой выпуклости и проявляется в продольной разнотолщинности листа. Анализ результатов расчета показывает, что увеличение темпа прокатки за счет сокращения длительности пауз и интенсификация охлаждения валков уменьшают разность температур ( tx, n пз - tx, n р ), повышают устойчивость теплового профиля и уменьшают разнотолщинность листа. Напротив, длительные паузы и простои, связанные с нарушением ритма прокатки, дестабилизируют тепловой режим и снижают качество листа по разнотолщинности.
Полученные данные о значениях температуры поверхности валка в контакте с полосой tʼП позволяют судить о соответствии материала валков и температуры их отпуска после закалки условиям эксплуатации. В клети № 5 при температуре полосы 400°С ее значение, соответствующее наиболее тяжелым тепловым режимам прокатки, составляет 320 - 325°С. Отпуск штатных валков при 340°С обеспечивает их структурную стабильность в этих условиях. Рабочие валки реверсивных клетей №1 и №2 имеют более высокую нагрузку, так как температура слитков ряда марок алюминия и сплавов на его основе составляет 450°С, а абсолютные обжатия принимаются 30 - 40 мм в клети №1 и 45 - 50 мм в клети №2. Кроме того, при первых проходах в клети №1 эмульсионное охлаждение валков отсутствует. Дополнительные расчеты, проведенные для ∆h=40мм, V=1м/с, nр= 3 и α = 0 дают tʼП =360°С при tʼпол=450°C. При увеличении температуры слитка до 500°С температура поверхности валка возрастает до 385°С. С ростом температуры разогрева поверхности растет и амплитуда ее колебания в течение оборота валка и пропуска слитка. Поверхность отпущенных после закалки валков при 340°С в этих условиях теряет структурную стабильность в процессе доотпуска при разогреве ее до указанных температур и быстро выходит из строя по трещинам. Температуру отпуска рабочих валков реверсивных клетей рекомендовано повысить до 380 - 400 °С.