Анализ факторов, определяющих работоспособность системы кондиционирования транспортно-технологических машин
Автор: Ионов П.А., Пьянзов С.В., Шунихин Р.Ф.
Журнал: Огарёв-online @ogarev-online
Статья в выпуске: 5 т.11, 2023 года.
Бесплатный доступ
В статье проведен анализ факторов, оказывающих влияние на работоспособность системы кондиционирования транспортно-технологических машин. Проанализированы и рассчитаны величины возможных утечек хладагента в системе кондиционирования. Определены соединения, вносящие наибольший вклад в утечку хладагента.
Компрессор, коэффициент полезного действия, редукционный клапан, система кондиционирования, утечка, хладагент
Короткий адрес: https://sciup.org/147250397
IDR: 147250397
Текст научной статьи Анализ факторов, определяющих работоспособность системы кондиционирования транспортно-технологических машин
Современные транспортно-технологические машины стали комфортными благодаря созданию комфортного микроклимата в салоне системой кондиционирования. Система кондиционирования – это совокупность устройств, которые позволяют охлаждать воздух в салоне транспортно-технологической машины и очищать его от влаги и посторонних запахов. Поэтому в условиях реальной эксплуатации важно обеспечивать работоспособность системы кондиционирования транспортно-технологической машины.
Одной из основных причин потери работоспособности системы кондиционирования является утечка хладагента. Проанализируем возможные пути утечек хладагента в системе кондиционирования и установим их величины. В качестве объекта исследований выбрана система кондиционирования автомобиля ГАЗель Next . На данный автомобиль устанавливаются агрегаты системы кондиционирования компании « Delphi ». Выбор данной системы обусловлен наличием полного комплекта конструкторской документации завода-изготовителя необходимой для расчета [1].
На рисунке 1 представлены возможные пути утечек хладагента в системе кондиционирования автомобиля не связанные с потерей герметичности.
Рис. 1. Возможные утечки хладагента в системе кондиционирования:
1 - утечки в соединениях компрессора; 2 - утечки в редукционном клапане.
Анализируя рис. 1 можно предположить, что фактическая подача, КПД компрессора и всей системы кондиционирования в целом в бóльшей степени зависят от внутренних утечек хладагента внутри компрессора и утечек через редукционный клапан. В компрессоре объемная внутренняя утечка хладагента оказывает более сложное влияние на фактическую объемную подачу. В процессе эксплуатации компрессора хладагент протекая через зазоры распределительной и поршневых соединений снижает фактическую подачу компрессора. При этом утечка в поршневых соединениях, не позволяет отклонить качающий узел компрессора на необходимый угол, что приводит к существенному снижению подачи и падению величины КПД всей системы кондиционирования в целом. В свою очередь утечки через редукционный клапан также снижают КПД всей системы кондиционирования.
По данным производителей компрессоров - Denso (Южная Корея), Delphi (Великобритания), Nissens (Дания), Luzar (Украина), Valeo (Франция) и др. наиболее важными техническими характеристиками являются подача Q , крутящий момент M , мощность N , коэффициент полезного действия (КПД). Справедливы следующие зависимости [1-5]:
Q = V g ⋅ n ⋅ η v , M = 1,56 ⋅ V g Δ p , N = Q ⋅Δ p . 1000 100 ⋅ η mh 612 η t
где Q - фактическая подача, л/мин; V g - рабочий объем, см3; n - частота вращения, мин-1;
Лр - разность давлений на входе и выходе, МПа; n v - коэффициент подачи хладагента (0,95);
η h – механический КПД; η t – полный КПД; М – приводной крутящий момент, Н∙м; N – мощность.
Наиболее точную и достоверную оценку технического состояния компрессора дает его КПД. Выразим из выражений (1) КПД:
ηt = ηvηh =
15,6 ⋅ Q ⋅ Δp М ⋅n
Механический КПД зависит от потерь энергии на трение в самом компрессоре. КПД компрессора определяется исходя из следующего выражения:
1000 ⋅ Q к Q к
.
gт
Анализ выражения (3) показывает, что КПД зависит от отношений теоретической подачи Q т и фактической подачи компрессора Q к . Значения фактической подачи компрессора можно определить из уравнения баланса подачи хладагента:
Q к = Q т – ∑q ут , тогда η v
Q т -Σ q ут
Q
где ∑q ут – суммарная внутренняя утечка хладагента в компрессоре при номинальных режимах работы.
На рисунке 2 представлены возможные пути утечек хладагента в компрессоре.
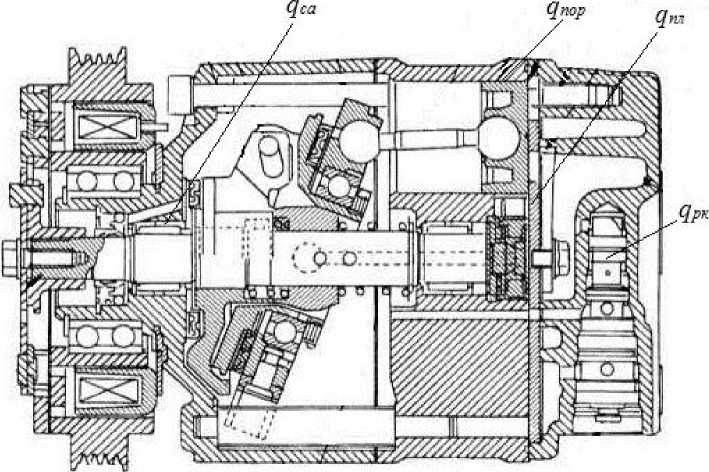
Рис. 2. Пути утечек хладагента в компрессоре:
q ca – утечка в соединении «сальник – вал компрессора»; q пор – утечка в соединении «поршень – отверстие блока цилиндров»; q пл – утечка в соединении «прижимная пластина – крышка компрессора»; q рк – утечка в соединении «клапан – отверстие крышки компрессора».
На рисунке 3 представлены возможные утечки хладагента в редукционном клапане.
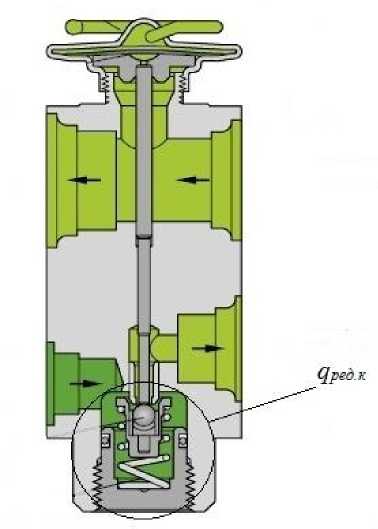
Рис. 3. Пути утечек хладагента в редукционном клапане:
q ped.k — утечка в соединении «редукционный клапан - отверстие корпуса».
Уравнение баланса основных источников суммарной утечки хладагента в системе кондиционирования можно представить в следующем виде:
^С Уут ~ К' q nop + q ca + q пл + q pK + q ped.K + "• + q x .
где К - количество поршней компрессора, находящихся в зоне рабочего давления, шт.; q x -расход потерь сжатия (заполнение «мёртвых» объемов), при прочихравных условиях допускается принимать его за константу ( q x = const ).
Анализ работы компрессора показал, что в зоне высокого давления, когда происходит утечка рабочей жидкости, находятся 3 поршня из 5. Остальные 2 поршня в этот момент находятся в зоне низкого давления, поэтому в нашем случае коэффициент К для выражения (5) будет равен 3.
Тогда принимая во внимание все обозначенные допущения, общее уравнение баланса основных источников суммарной утечки хладагента ∑q ут для системы кондиционирования транспортно-технологических машин примет следующий вид:
^qvm 3^ q nop + q
са
+ q nл + q pK + q ped.K +
Согласно закону Пуазейля, утечку хладагента через эксцентричный кольцевой зазор можно представить в виде [1-5]:
nd^Pz
qут
12 Lu
1 + 3 s2
I 2
]7
, м3/с
где z – кольцевой зазор в соединении, м; d – средний диаметр кольцевой щели, м; L – длина поршня, м; μ – динамическая вязкость, Па·с; ε – эксцентриситет уплотнения, м; ΔP – перепад давления, Па.
Утечка хладагента через капиллярную щель (торцовый зазор) между неподвижными плоскими стенками определяется по выражению:
ΔPbz3 qут=12Lµ⋅103 , м/с
где b – ширина щели, м; z – зазор между плоскими стенками щели, м; L – длина щели в направлении тока жидкости, м.
Для поиска наиболее значимых соединений выражения 6, оказывающих наибольшее влияние на величину суммарной утечки определим величину утечки хладагента в соединениях нового компрессора и редукционного клапана экспериментальным путем и сравним с значениями, полученными по аналитическим выражениям (7) – (8).
Рассчитаем утечки хладагента в системе кондиционирования транспортнотехнологических машин. Для соединений «поршень – отверстие блока цилиндров», «клапан – отверстие крышки компрессора» и «редукционный клапан – отверстие корпуса» расчеты производим по выражению (7). Для соединений «сальник – вал компрессора» и «прижимная пластина – крышка компрессора» расчеты производим по выражению (8).
Расчеты утечек хладагента выполним при следующих условиях. Разобьем обозначенные соединения на две зоны действия давления – зона высокого давления ΔP = 1,76 ∙106 Па и зона низкого давления ΔP = 0,22 ∙106 Па. В зоне высокого давления находятся следующие соединения: «поршень – отверстие блока цилиндров»; «клапан – отверстие крышки компрессора»; «редукционный клапан – отверстие корпуса» и «прижимная пластина – крышка компрессора», а в зоне действия низкого давления находится только соединение «сальник – вал компрессора». Расчеты утечек для всех обозначенных соединений производим при максимальных значениях технологических зазоров для новых соединений.
При расчетах были приняты следующие значения, так для соединения «поршень – отверстие блока цилиндров» максимальный технологический зазор равен z = 46 ∙10-6 м, средний диаметр кольцевой щели равен d = 0,023 м, длина поршня равна L = 74,5 ∙ 10-3 м. В зоне высокого рабочего давления находятся 3 поршня.
Для соединения «клапан – отверстие крышки компрессора» максимальный технологический зазор равен z = 16 ∙10-6 м, средний диаметр кольцевой щели равен d = 0,016 м, длина запирающего пояска клапана равна L = 16,76 ∙ 10-3 м.
Для соединения «редукционный клапан – отверстие корпуса» максимальный технологический зазор равен z = 16 ∙10-6 м, средний диаметр кольцевой щели равен d = 0,013
м, длина запирающего пояска клапана равна L = 4,85 ∙ 10-3 м.
Для соединения «прижимная пластина – крышка компрессора» в качестве максимального технологического зазора между плоскими стенками принимается суммарная шероховатость зоны уплотнения распределителя, которая равна Ra 0,2 мкм, в качестве ширины щели принимается расстояния между окошками пластины в зоне действия давления b = 4 мм, в качестве длины щели взят участок с 3 поршнями в зоне действия высокого давления L = 17,4 мм.
Для соединения «сальник – вал компрессора» в качестве максимального технологического зазора принимается суммарная шероховатость зоны уплотнения, которая равна Ra 0,2 мкм, в качестве ширины щели принимаем ширину зоны уплотнения b = 3 мм, в качестве длины щели длина окружность зоны уплотнения L = 81,64 мм. Результаты расчетов утечки хладагента в обозначенных и проанализированных соединениях системы кондиционирования сведены в таблицу 1.
Таблица 1
Максимальные утечки хладагента в системе кондиционирования
Наименование соединения |
Максимальный технологический зазор, мкм |
Величина давления в соединении, МПа |
Максимальная утечка хладагента, м3/с |
«Поршень – отверстие блока цилиндров» |
46 |
1,76 |
8,6816∙10-4 |
«Клапан – отверстие крышки компрессора» |
16 |
1,76 |
3,1124∙10-4 |
«Редукционный клапан – отверстие корпуса» |
16 |
1,76 |
8,7385∙10-5 |
«Прижимная пластина – крышка компрессора» |
0,2 |
1,76 |
1,2216∙10-20 |
«Сальник – вал компрессора» |
0,2 |
0,22 |
2,3743∙10-22 |
Анализ таблицы 1 показал, что наибольший вклад в утечку хладагента вносят соединения, находящиеся в зоне высокого давления: «поршень – отверстие блока цилиндров»; «клапан – отверстие крышки компрессора»; «редукционный клапан – отверстие корпуса». Наименьший вклад в утечку вносят «прижимная пластина – крышка компрессора» и «сальник – вал компрессора».
Таким образом, проведенные исследований позволили установить соединения, которые вносят значительный вклад в утечку хладагента – это «поршень – отверстие блока цилиндров»; «клапан – отверстие крышки компрессора»; «редукционный клапан – отверстие корпуса». Остальные соединения из дальнейших исследований исключены, так как их влияние на величину утечки хладагента в системе кондиционирования незначительное.
Тогда уравнение баланса основных источников суммарной утечки хладагента в системе кондиционирования примет следующий вид:
∑q ут = 3∙ q пор + q рк + q ред.к
Подставив выражения (7) – (8) в выражение (9) и проведя некоторые преобразования и упрощения, получим качественную оценку суммарной утечки хладагента в системе кондиционирования автомобиля:
р 3 3 3
q ут 1 пор 2 рк 3 ред . к .
V где k1-k3 – постоянные коэффициенты, определяющие характеристики истечения хладагента, зависящие от формы зазора; zпор. – кольцевой зазор в соединении «поршень – отверстие втулки блока цилиндров» компрессора, мм; zрк – кольцевой зазор в соединении «регулировочный клапан – отверстие крышки компрессора», мм; zред.к – кольцевой зазор в соединении «редукционный клапан – отверстие корпуса», мм.
Анализируя функциональную зависимость (10) можно сделать вывод, что величину КПД (ηс) системы кондиционирования транспортно-технологических машин можно представить как функцию зависящую от разности давлений ∆р,вязкости хладагента μ и от зазоров в соединениях:
η с = f ( ∆р , μ , z пор , z рк , z ред.к ). (11)
Таким образом, в выражении (11) представлена группа факторов, оказывающих влияние на работоспособность системы кондиционирования транспортно-технологических машин (на величину КПД). Для детального изучения степени влияния факторов на параметр оптимизации необходимо провести многофакторный эксперимент, который позволит установить связь КПД с величинами зазоров в ответственных соединениях элементов системы кондиционирования.
Список литературы Анализ факторов, определяющих работоспособность системы кондиционирования транспортно-технологических машин
- Пьянзов С. В., Ионов П. А., Фиклинов А. А., Шунихин Р. Ф. Анализ средств диагностирования компрессора системы кондиционирования автомобиля // Современные материалы, техника и технологии. - 2022. - № 5(44). - С. 48-54. EDN: QGVSSY
- Киселев Д. Н. Системы кондиционирования автомобилей // XLV Огарёвские чтения. Материалы научной конференции. - Саранск, 2017. - С. 740-745. EDN: YRCYCP
- Манойлина С. З., Ворохобин А. В. Причины и рекомендации по устранению неисправностей автомобильных кондиционеров // Проблемы ресурсообеспеченности и перспективы развития агропромышленного комплекса. Материалы национальной научно-практической конференции. - Воронеж, 2021. - С. 301-308. EDN: OAEERY
- Галка Г. А. Иванов Р. А., Думлер М. Г., Принцип работы и устройство автомобильного кондиционера // Молодой ученый. - 2017. - № 20. - С. 16-20. EDN: YPECGN
- Манойлина С. З., Ворохобин А. В. Использование р-н диаграммы при выборе автомобильного кондиционера // Проблемы ресурсообеспеченности и перспективы развития агропромышленного комплекса. Материалы национальной научно-практической конференции. - Воронеж, 2021. - С. 294-300. EDN: UWJWPF