Анализ опыта подготовки руд к подземному выщелачиванию
Автор: Голик В.И., Разоренов Ю.И., Чжун Чан
Журнал: Горные науки и технологии @gornye-nauki-tekhnologii
Рубрика: Обогащение и переработка минерального и техногенного сырья
Статья в выпуске: 4, 2017 года.
Бесплатный доступ
Актуальность. Метод подземного выщелачивания металлов позволяет доработать потерянные для традиционной технологии запасы. Однако процессы выщелачивания производятся без комплексного учета природных и техногенных факторов, в связи с чем результаты использования технологий не всегда оправдывают возлагаемые на них надежды, и это препятствует расширению границ их применения. Поэтому разработка научных основ и совершенствование технологии выщелачивания металлов из вскрываемых руд являются весьма актуальной задачей горного производства. Методы исследования проблемы включают в себя анализ теории и практики промышленного выщелачивания металлов, обоснование эффективности модернизации существующего положения и разработку рекомендаций по увеличению области применения этой прогрессивной технологии. Результаты. Дан анализ основных процессов подземного выщелачивания металлов. Описан опыт промышленного подземного выщелачивания на примере металлических рудников России и Казахстана. Обозначена необходимость комбинирования подземного выщелачивания бедных и забалансовых руд с традиционной отработкой богатых и балансовых руд на современной стадии горного производства. Описан способ контроля полноты выщелачивания путем вскрытия горными выработками. Обозначен опыт применения электровакуумных установок для дренажа продукционных растворов. Детализированы методы формирования компенсационного пространства и интенсификация выщелачивания взрывом и другими способами. Описана роль гидравлического разрыва пород, инъектирования разрушенных пород твердеющими составами и мелкозернистых инертных материалов в процессе орошения руд. Выводы. Комбинирование технологий выщелачивания бедных и забалансовых руд с традиционной отработкой богатых и балансовых руд на стадиях горного производства комплексно повышает их эколого-экономическую эффективность при использовании оптимальных для комбинируемых способов подготовки и технологических параметров, что позволит подземному выщелачиванию занять приоритетные позиции при добыче вскрываемых руд.
Металл, подземное выщелачивание, традиционная отработка, подготовка руд, горная выработка, скважина, технология
Короткий адрес: https://sciup.org/140230112
IDR: 140230112 | DOI: 10.17073/2500-0632-2017-4-13-19
Текст научной статьи Анализ опыта подготовки руд к подземному выщелачиванию
В России много действующих и отработанных месторождений цветных и редкоземельных металлов, вовлечение которых в повторное производство технологией подземного выщелачивания может способствовать решению региональных проблем [1]. Метод подземного выщелачивания металлов позволяет доработать потерянные для традиционной технологии запасы в охранных целиках, зонах обрушения, отвалах хвостов обогащения и металлургии и т.п.
В настоящее время выщелачиванием добываются уран, медь, золото, причем на ряде предприятий это является основной деятельностью. Дальнейшее расширение области применения прогрессивной технологии ограничивается превалирующей тенденцией получения быстрой прибыли при выборочном использовании минеральных ресурсов. Но истощение запасов минерального сырья в комфортных условиях способствует расширению диапазона технологий с выщелачиванием, пока еще в комбинации с традиционными технологиями.
Небогатый набор публикаций о промышленном использовании подземного выщелачивания свидетельствует о том, что процессы выщелачивания пока еще производятся без комплексного учета природных и техногенных факторов, результаты использования технологий не
всегда оправдывают возлагаемые на них надежды, поэтому разработка научных основ и совершенствование технологии являются весьма актуальной задачей для горного производства [2-4].
Целью настоящего исследования является ознакомление с опытом оптимизации параметров технологии разработки с подземным выщелачиванием скальных, преимущественно урановых месторождений для развития этого перспективного направления горного производства.
Методы исследования
Методология исследования включает в себя анализ теории и практики производственных процессов выщелачивания металлов на предприятиях государств СНГ, разработку рекомендаций и обоснование эффективности модернизации существующих технологий для их использования при добыче вскрываемых металлов.
Показатели составляющих технологию производственных процессов принимаются по результатам их использования на месторождениях с аналогичными условиями.
Рекомендации по совершенствованию технологии базируются на данных промышленного применения технологии.
Результаты
Практика использования технологий в продвинутых отраслях хозяйства показывает, что в настоящее время во избежание рисков потери сырья в процессе освоения инновационной технологии целесообразно комбинировать подземное выщелачивание бедных и забалансовых руд с традиционной отработкой богатых и балансовых руд (рис. 1) [5-7].

Рис. 1. Комбинирование геотехнологий разработки рудных месторождений
Существенным различием подготовки руд при комбинируемых технологиях является крупность рудных кусков. Если при традиционных способах габаритные куски могут иметь размеры 1000 мм и более, то для выщелачивания пригодны рудные куски класса +0-50 мм. При послойной отбойке руды компенсационное пространство для отбойки очередного слоя создается частичным выпуском руды из ранее отбитого слоя. Ру- да разрыхляется только в пределах определенного объема эллипсоида, а в остальном пространстве остается неподвижной. Эти два фактора определяют успех подземного выщелачивания.
Для выщелачивания чаще применяется инфильтрационная схема, основанная на движении потока реагента от оросителей к дренажным устройствам под действием сил гравитации (рис. 2) [8-10].
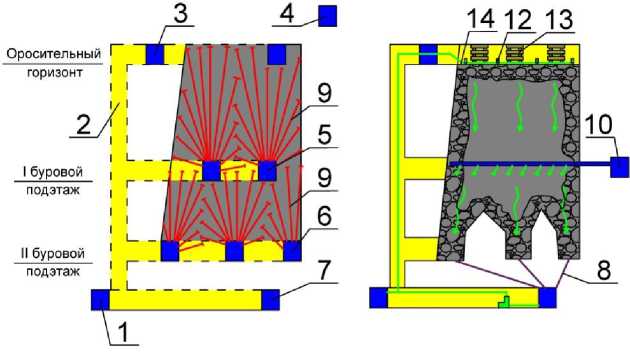
Рис. 2. Схема инфильтрационного выщелачивания металлов: 1 – штрек; 2 – восстающий; 3 – штрек для орошения; 4 – штрек; 5 – буровые штреки; 6 – дренажно-буровые штреки; 7 – дренажный штрек; 8 – дренажные скважины; 9 – промежуточный горизонт орошения; 11 – штрек для орошения;
12 – верхняя подсечка; 13 – костровая крепь; 14 – оросительная система
В процессе извлечения полезного компонента из руд через определенное время возникает необходимость в его интенсификации путем дополнительного воздействия на руду. Наибольшее применение для целей интенсификации нашел метод воздействия с помощью взрывных работ.
Технология подземного выщелачивания металлов наиболее полно освоена на предприятиях Минсредмаша СССР в последней четверти прошлого века и становится основной в наше время на месторождении Стрельцовское (Забайкалье).
Месторождение Восток (Северный Казахстан) представляет собой линзовидное рудное тело неправильной формы в интенсивно рассланцованных осадочных породах крепостью 4-6 по шкале проф. М.М. Протодьяконова. Верхняя часть месторождения отработана системами с обрушением [11–13].
Нарезные работы в блоке подземного выщелачивания длиной 25 м, шириной 5 м и высотой 28 м включали в себя оборудование монтажного и подсечного слоев, выпускной дучки, отрезного восстающего и отрезной щели.
Монтажный слой представлял собой верхнюю подсечку шириной 6 м, высотой 2-3 м и был предназначен для бурения скважин и размещения оросительной системы.
Подсечной слой был проведен с уклоном 5° к центру блока. Гидроизоляция осуществлена укладкой поливинилхлоридной пленки, защищенной деревянным настилом и рудной подушкой.
Отрезная щель шириной 2 м и длиной 5 м образована расширением отрезного восстающего сечением 2×2 м.
Руду отбивали скважинами диаметром 65 мм, которые бурили станком НКР-100М с монтажного слоя параллельно друг другу с оставлением до кровли нижней подсечки 1,5 м.
Заряжание скважин осуществлялось гранулитом АС-0 без забойки. Короткозамедленное с интервалом замедления между рядами 25 мс взрывание осуществлено электрическим способом с дублированием детонирующим шнуром. Общий вес заряда составил 4200 кг, полученный коэффициент разрыхления - 1,12.
Магазинированная руда выщелачивалась в течение 6,5 мес, после чего концентрация металлов в продукционных растворах снизилась ниже допустимого уровня. Для контроля процесса блок выщелачивания был вскрыт выработками сечением 6-8 м2 с креплением дверными окладами.
Обследованием выработок установлено, что дробление массива на мелкие фракции происходило в зоне действия взрыва скважин, равной 2-3 диаметрам заряда, в зоне отрезной щели произошло переуплотнение руды, а растворы двига-
лись по трещинам и переизмельченной руде зоны действия взрыва, где массив был разрушен с преобладанием фракций до 0,4 м.
На повторное дробление магазини-рованной руды затрачено более 5 т ВВ. При удельном расходе ВВ на вторичное дробление 1,55 кг/м3 был получен коэффициент разрыхления 1,43. После интенсификации процесса выщелачивание продолжалось 4,5 мес с получением объема продукции в 1,2 раза больше полученного за первый период выщелачивания.
На месторождении Звездное (Северный Казахстан) опытнопромышленный блок имел длину 60 м, ширину 10–26 м и высоту камеры 36 м. Горизонт улавливания продукционных растворов представлял собой дренажный штрек с дренажными скважинами.
Дробление руды осуществлено восходящими скважинами с опережением отбойки верхнего подэтажа по отношению к нижнему подэтажу.
Взрывание осуществлялось с внут-ривеерным замедлением с использованием ступеней 25, 30, 75 и 100 м после частичного выпуска отбитой горной массы для формирования объема компенсации.
Обрушение руды осуществлялось вначале на отрезную щель, а затем в «зажиме» от центра блока к флангам. Величина заряда на одну ступень 200-600 кг, а количество одновременно взрываемого ВВ - 2,5 т.
Выщелачивание блока продолжалось в течение года и положительного результата не дало. Для выявления причин по магазинированной руде была пройдена контрольная выработка длиной 28 м. Установлено, что выход негабаритного класса в три раза превысил расчетные данные, в массиве образовались зоны переуплотненной руды с переотложениями солей и каналы повышенной фильтрации.
Процесс выщелачивания интенсифицируется нагнетанием сжатого воздуха в пробуренные по замагазинированной руде скважины.
Продолжительность и полнота извлечения полезных компонентов из руд зависят от крупности и плотности укладки раздробленной руды без образования неорошаемых зон [14–16].
Руду дробят на куски крупностью, уменьшающейся пропорционально снижению градиента концентраций извлекаемого полезного ископаемого между поровым раствором и объемом растворителя за счет расположения скважин. Расстояние между концами скважин при отбойке верхней части массива постепенно уменьшается книзу и достигает минимального значения для скважин в нижней части массива. ВВ в скважинах размещается с максимальным для получения нужной крупности расходом ВВ в нижней части и минимальным в верхней части.
Возможность управления крупностью рудных кусков подтверждена горной практикой.
На Салаирском руднике при базовом варианте отбойки скважинами выход негабарита составлял 34-38 %. Размещение вееров во встречно-параллельном направлении за счет перераспределения ВВ по элементам отбиваемого слоя позволило снизить выход негабарита до 8-15 %.
На Тырныаузском месторождении при отбойке в ромбоидальных панелях веерам взрывных скважин придавали форму эллипсоида выпуска на вертикальную плоскость (соотношение полуосей эллипсоида 3:1, высота ромбоидальной панели 33 м, ширина 11 м). При отработке опытной панели потери руды снижены с 15 до 8 %, извлечение чистой неразубоженной руды составило 90 % против 50 %, а объем подготовительнонарезных работ снижен на $28,6.
Для формирования проницаемых для растворов зон используются поин-тервальные гидравлические разрывы из участковых скважин. Трещины гидроразрыва заполняются мелкозернистым материалом.
При комбинировании традиционных технологий и подземного выщелачивания целесообразна подготовка руды
с селективной выемкой богатой части полезного ископаемого.
При совершенствовании систем орошения наиболее перспективны использование пробуренных по разрушенному массиву и обсаженных перфорированными трубами скважин и применение мелкозернистых инертных материалов. В тонких трубках смачивающие жидкости обладают способностью подниматься над общим уровнем. На границе разделения сред с различной пористостью жидкость задерживается в слое с более мелкими порами. Вначале жидкость растекается по тонкозернистому слою, а затем проникает в другой слой.
Дренажная система блока подземного выщелачивания обеспечивает сбор продукционных растворов и охрану внешней среды от загрязнения растворами ими. Улавливание продукционных растворов электровакуумными установками на Быкогорском месторождении позволило ликвидировать трудоемкие работы по гидроизоляции.
Опасность боковых утечек технологических растворов предупреждается использованием экранов из веществ, способных к активной полимеризации под воздействием ударных волн (эфиры акриловой или метакриловой кислот).
Дополнительное воздействие на выщелачиваемую руду осуществляется с помощью взрывных работ и специальных способов типа электромагнитного, ультразвукового и т.п.
Интенсификация выщелачивания взрывом основана на подвижке кусков руды при отбойке на него новых слоев на высоту до 20 м, в результате чего куски смещаются друг относительно друга, разрушают кольматированные зоны и открывают новые поверхности для выщелачивания.
В основу невзрывной интенсификации положено воздействие на руду в блоке импульсами сжатого воздуха высокого давления, импульсно подаваемого одновременно с подачей реагента. Часть энергии сжатого воздуха затрачивается на пе- ремещение трещинных заполнителей, а другая - передается реагенту, который, перемещаясь под давлением, способствует вымыванию заполнителей и разрушению пленок.
Применение ультразвуковых колебаний основано на повышении скорости движения жидкости в капиллярах под действием ультразвука. Под блоком подземного выщелачивания формируется полость, заполняемая материалом, размер частиц которого на порядок меньше размера кусков выщелачиваемой руды. В нижней части полости помещается источник ультразвуковых колебаний, который генерирует импульсы ультразвука, в результате чего скорость перемещения продукционного раствора по капиллярам рабочего тела увеличивается в десятки раз.
В основе электромагнитного выщелачивания руд лежат активизирующая электромагнитная обработка растворов в поле электрического тока и пропускание их сквозь выщелачиваемую рудную массу с подачей пульсирующего низкочастотными импульсами в диапазонах 18–213 или 50–150 кГц электрического тока.
Результаты типизации процессов подземного выщелачивания сведены в таблицу.
Обладая технологическими и экологическими преимуществами, подземное выщелачивание способно занять в недалеком будущем главные позиции при добыче многих полезных ископаемых. Практика промышленного применения новой технологии подтверждает непригодность традиционных методов подготовки руд для этих целей.
Исследование горных аспектов выщелачивания и разработка научных основ и способов его осуществления представляются важнейшими из задач горнодобывающего производства, от решения которых зависит создание высокопроизводительных технологий извлечения полезных ископаемых из недр [17-25].
МИСиС
Таблица
Типизация процессов подземного блокового выщелачивания руд
Процессы |
Параметры процессов |
Требования к процессам |
Дробление руды |
Обеспечение крупности +20 мм… –50 мм |
Равномерная плотность руды. Возможность создания компенсационного пространства для взрыва |
Орошение руды |
Скважины в нетронутом массиве Разбрызгивание с поверхности руды Скважины в разрушенной руде с обсадкой Использование мелкозернистых материалов Гидравлический разрыв пород |
Отсутствие непроницаемых зон и каналов в отбитой руде |
Сбор продукционных растворов |
Противофильтрационные завесы Гидроизоляция участков выщелачивания Электровакуумный дренаж растворов Использование синтетических полимерных материалов |
Исключение попадания продуктов выщелачивания в окружающую среду |
Интенсификация процесса |
Физические методы: нагнетание сжатого воздуха, взрыванием руд, уменьшение крупности пропорционально градиенту концентрации, отбойка слоями с переменной линией наименьшего сопротивления, придание формы эллипсоида выпуска, ультразвуковые колебания, электромагнитная обработка растворов Химические методы: промывка водой с активизирующими добавками, введение химических составов Биологические методы: использование штаммов бактерий |
Получение заданного разрыхления Увеличение содержания в растворе до приемлемого значения |
Контроль полноты выщелачивания |
Скважинные методы: бурение по породе для введения контролирующих устройств, бурение по отбитой руде с отбором проб Проходка выработок с отбором проб |
Представительности проб и измерений для всего блока |
Выводы
-
1. Опыт промышленного подземного выщелачивания металлов свидетельствует о целесообразности комбинирования технологий выщелачивания бедных и забалансовых руд с традиционной отработкой богатых и балансовых руд на стадиях горного производства.
-
2. Способы подготовки руд к выщелачиванию должны отличаться от способов подготовки по традиционной технологии приоритетной ролью циркуляции выщелачивающих растворов в рамках единой системы.
-
3. Полнота выщелачивания металлов обеспечивается процессом выщелачивания с применением электровакуумных установок для дренажа продукционных растворов, формированием компенсационного пространства, интенсификации выщелачивания взрывом и другими способами, а также использованием гидравлического разрыва пород и других технологических приемов.
-
4. При условии рационализации методов подготовки и выщелачивания руд подземное выщелачивание способно занять приоритетные позиции при добыче вскрываемых руд.
Engineering, Hydrometallurgy. 2012. Vol. 111– 112. P. 129–1355.
Processing Wastes // Resources Policy. – Vol. 36. No. 2. Р. 114-122.
Список литературы Анализ опыта подготовки руд к подземному выщелачиванию
- Голик В.И., Комащенко В.И., Качурин Н.М. К проблеме подземной разработки рудных месторождений центрального федерального округа/Известия Тульского государственного университета. Науки о Земле. 2016. № 4. С. 127-139.
- Khasheva Z.M., Golik V.I. The ways of recovery in economy of the depressed mining enterprises of the Russian Caucasus//International Business Management. 2015. Т. 9. № 6. С. 1210-1216.
- Голик В.И. Специальные способы разработки месторождений. М.: ИНФРА-М. 2014. 132 с.
- Mwase J.M., Petersen J., Eksteen, J.J. A conceptual flowsheet for heap leaching of platinum group metals (PGMs) from a low-grade ore concentrate//Mining Engineering & Metallurgical Engineering, Hydrometallurgy. 2012. Vol. 111-112. P. 129-1355.
- Бубнов В.К., Спирин Э.К., Голик В.И., и др. Теория и практика добычи полезных ископаемых для комбинированных способов выщелачивания. Целинград: Жана-Арка. 1992. 545 с.
- Волков Ю.В., Соколов И.В. Подземная геотехнология при комбинированной разработке рудных месторождений//Горный информационно-аналитический бюллетень. 2013. № 1. С. 34-40.
- De Oliveira D.M., Sobral L.G.S., Olson G.J., Olson S.B. Acid leaching of a copper ore by sulphur-oxidizing microorganisms//Hydrometallurgy. 2014. Vol. 147-148. P. 223-227.
- Sinclair L., Thompson J. In situ leaching of copper: Challenges and future pro spects//Hydrometallurgy. 2015. Т. 157. Р. 306-324.
- Дмитрак Ю.В., Камнев Е.Н. АО «Ведущий проектно-изыскательский и научно-исследовательский институт промышленной технологии» -Путь длиной в 65 лет//Горный журнал. 2016. № 3. С. 6-12.
- Karimi N.S., Atashpanjeh A., Mollaei F.M.R. Design considerations of heap leaching at the sarcheshmeh copper open pit mine//International Mining Congress of Turkey -IMCET. 2001. P. 513-516.
- Голик В.И., Брюховецкий О.С., Габара-ев О.З. Технологии освоения месторождений урановых руд. Учебное пособие для ВУЗов. Москва: Издательство РГГУ. 2007. 131 c.
- Ляшенко В.И., Голик В.И. Природо-охранные технологии подземной разработки урановых месторождений//Горный журнал. 2006. № 2. С. 89-92.
- Рыльникова М.В., Радченко Д.Н., Милкин Д.А., Звягинцев А.Г., Пешков А.М. Обоснование параметров и режима выщелачивания сырья техногенных образований, сопутствующих разработке медно-колчеданных месторождений//Москва. Горный информационно-аналитический бюллетень. 2010. № 3. С. 340-350.
- Jordens Adam, Cheng Ying Ping, Waters Kristian E. A review of the beneficiation of rare earth element bearing minerals//Minerals Engineering. 2013. Vol. 41. P. 97-114.
- Franks D.M., Boger D.V., Côte C.M., Mulligan D.R. 2011. Sustainable Development Principles for the Disposal of Mining and Mineral Processing Wastes//Resources Policy. -Vol. 36. No. 2. Р. 114-122.
- Голик В.И. Активация отходов горного производства при выщелачивании металлов//Горные науки и технологии. 2016. № 4. С. 3-9.
- Голик В.И., Заалишвили В.Б. Оптимизация схем подготовки месторождений наклонными съездами//Известия Тул ГУ. Науки о Земле. Вып. 1. 2017. С. 52 -68.
- Разоренов Ю.И., Голик В.И., Куликов М.М. Экономика и менеджмент горной промышленности//Учебное пособие для ВУЗов. Издательство ЮРГТУ. Новочеркасск. 2010. 251 с.
- Голик В.И., Хашева З.М., Шульгатый Л.П. Экономический механизм конверсии горнодобывающей отрасли депрессивных регионов Юга России//Научный вестник Южного института менеджмента. 2016. № 3 (15). С. 27-32.
- Голик В.И. Извлечение металлов из хвостов обогащения комбинированными методами активации//Обогащение руд. 2010. № 5. С. 38-40.
- Golik V.I., Stradanchenko S.G., Maslennikov S.A. Еxperimental study of non-waste recycling tailings ferruginous quartzite//International Journal of Applied Engineering Research. 2015. Т. 10. № 15. С. 35410-35416.
- Голик В.И., Полухин О.Н., Петин А.Н., Комащенко В.И. Экологические проблемы разработки рудных месторождений КМА//Горный журнал. 2013. № 4. С. 91-94.
- Golik V., Komashchenko V., Morkun V., Zaalishvili V. Enhancement of lost ore production efficiency by usage of canopies//Metallurgical and Mining Industry. 2015. Т. 7. № 4. С. 325-329.
- Голик В.И., Комащенко В.И., Качурин Н.М. Концепция комбинирования технологий разработки рудных месторождений//Известия Тульского государственного университета. Науки о Земле. 2015. № 4. С. 76-88.
- Golik V., Komashchenko V., Morkun V., Irina G. Improving the effectiveness of explosive breaking on the bade of new methods of borehole charges initiation in quarries//Metallurgical and Mining Industry. 2015. Т. 7. № 7. С. 383-387.