Анализ сборочно-резьбообразующего процесса с использованием мехатронной завинчивающей головки
Автор: Леонов В.Н., Охрименко М.И.
Журнал: Известия Самарского научного центра Российской академии наук @izvestiya-ssc
Рубрика: Машиностроение
Статья в выпуске: 1-2 т.12, 2010 года.
Бесплатный доступ
В статье предлагается новый подход к формированию структуры управляющего процесса, основанный на детальном представлении об его параметрах и ходе протекания. Представлена математическая модель, описывающая ход завинчивающего процесса. Обоснована актуальность использования мехатронных систем для решения задач сборки.
Сборочный процесс, мехатронная головка
Короткий адрес: https://sciup.org/148198958
IDR: 148198958
Текст научной статьи Анализ сборочно-резьбообразующего процесса с использованием мехатронной завинчивающей головки
Технологическая система автоматической завинчивающей машины должна обеспечить все необходимые условия гарантированного сопряжения собираемых деталей в ее координатной системе. При этом реализуются следующие действия:
– точное позиционирование рабочего стола для совмещения осей собираемых деталей;
– автоматическая подача крепежной детали в завинчивающую головку;
– осевое перемещение детали до совмещения с кромкой отверстия;
– совокупность движений для совмещения ниток резьбы гнезда и крепежной детали в случае посадки в резьбовое гнездо;
– в случае посадки в гладкое отверстие или в отверстие листового материала необходимо обеспечить надежное удержание крепежной детали для начального этапа резьбовыдавлива-ния;
– выполнение перехода окончательного завинчивания с необходимой затяжкой в конце;
– освобождение крепежной детали и возврат завинчивающих устройств в исходное положение [1].
Для выполнения сборочно- резьбообразу-ющих операций важно также и качественно выполнить завинчивание. При этом необходимо принимать во внимание силы и моменты, действующие на крепежные детали, в процессе наживления и затяжки. Решение задачи сборки соединений с заданными свойствами может взять на себя мехатронная завинчивающая головка, снабженная адаптивной системой управления и силомоментными датчиками. Рассмотрим вариант завинчивающего устройства с управляемой осевой подачей. Кинематическая схема головки приведена на рис. 1.
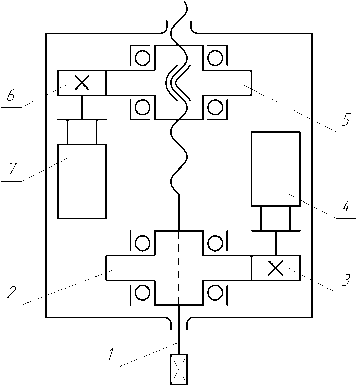
Рис. 1. Кинематическая схема завинчивающейся головки
Главное движение и движение подачи отрабатывается шпинделем головки. Шпиндель 1 посредством шлицевого соединения связан со ступицей зубчатого колеса 2 таким образом, что крутящий момент с этого колеса передается на вал, а в осевом направлении вал может свободно перемещаться. Двигатели 4, 7 представляют собой шаговые двигатели с понижающими редукторами. Редуктор шагового двигателя позволяет получить на выходном валу очень мелкий шаг (доли градуса в полношаговом режиме), что позволяет завинчивающей головке более точно отрабатывать сигналы системы управления и получить довольно большой крутящий момент, что положительно влияет на массо-габаритные характеристики устройства. Осевую подачу в процессе работы устройства обеспечивает пара винт-гайка. Ходовой винт пары винт-гайка является продолжением шпинделя и выполнен с ним «заодно». Ходовая гайка представляет собой ступицу зубчатого колеса 5 с резьбой в осевом отверстии. Таким образом благодаря винтовой части шпиндель головки совершает поступательные движения вдоль оси посредством вращения ходовой гайки, а благодаря шлицевой части шпиндель совершает вращательное движение посредством вращения зубчатого колеса 2.
Работа таких устройств требует определенной логики управления, обоснованной структуры информационной системы и выполнения ряда условий, вытекающих из установления функциональных взаимосвязей между управляющими и управляемыми параметрами.
При любом сборочном процессе можно выделить 4 основных перехода, включая на-живление, завинчивание, затяжку и освобождение головной части крепежного элемента. Каждый из переходов имеет определенные характер изменения угловой скорости to и крутящего момента М . При такой сложной картине изменения указанных параметров встает задача управления ходом завинчивающего процесса.
Для анализа хода сборочного процесса установим координатные оси технологической системы: z – центральная ось машины (ось шпинделя); y – поперечная или радиальная ось. Ход завинчивающего процесса, поведение крепежной детали и ведущего наконечника можно описать следующей системой дифференциальных уравнений [2]:
f Jto = M.- KP®;
ä ì
W = Q , - jY ; (1)
^ mZ = (H - Z) c - kQ • Z.
где J – суммарный момент инерции приводных элементов шпиндельной части; ω – угловая скорость вращения шпинделя; Mä– крутящий момент на валу двигателя главного движения; KM – коэффициент пропорциональности; P – шаг резьбы; m – масса винта и приводных частей завинчивающей головки; Y, Z – поперечная и продольная координаты соответственно; Qè – изгибающее усилие, возникающее в начальный момент наживления; jn – жесткость центральной части завинчивающей головки в радиальном направлении; H – величина сжатия пружины наживления в завинчивающей головке; C – жесткость пружины на-живления; kQ – обобщенная сила сопротивления осевому перемещению винта; k – коэффициент пропорциональности.
Приводной момент главного электродвигателя связан со следующими параметрами
JP • f • I
M a = K . , (2)
p 1
где K n – коэффициент пропорциональности рад/А.с; J p – момент инерции ротора Нмс2/рад; f – частота импульсов тока; I – амплитудное значение импульса [A]; p 1 – число полюсов двигателя.
Приняв частоту вращения ротора пропорциональной частоте следования импульсов ω p = K K f , получим
M
K n a K k
J p • to l p 1
где K K – размерный коэффициент [рад].
Перепишем первое уравнение системы (1) в виде
Jto + KMPto = —• to
M ,
K 1
и приведем его к следующей форме
dto
— = a to , (3)
dt
_ a = Ka. J_pL_
д Kk p1( J + K.P )■
Решение уравнения (3) будет представ лено в виде t„ = — In W\ + c a где ti – время, необходимое для внедрения заходного витка; C – постоянная, связанная с начальными условиями t^ = 0; in [^ = 1. Тогда C=-1/a, и, следовательно,
t^= 11П to —1 =1 (ln to — 1)' aaa
Расчетное время внедрения заходного витка равно t = (d - d0) • 2000 pH 2tgф- tg^ • to- d
где d , d 0 – наружный диаметр резьбы винта и диаметр отверстия, соответственно; φ – угол фаски на торце стержня винта; ψ – угол подъема резьбы.
Воспользовавшись коэффициентом KK, определим необходимую частоту следования импульсов, а на основании зависимости (4) получим значение амплитуды тока в импульсе f = — eatH+1; KK
I = (In ю -1) - KK - P1(J + KmP) tPðíP
Реализация работы завинчивающей головки возможна только на основе разработки подробной схемы идентификации параметров управления. Так, например, работа шагового электропривода главного движения основана на информации о ходе процесса завинчивания, которая поступает из трех источников: – от параметрических датчиков;
– от отдельного блока ввода и хранения расчетных данных;
– от компьютерной модели процесса, представляющего картину формирования параметров сборки по ее этапам.
Шпиндель агрегата и соответственно вал двигателя связан с датчиком крутящего момента и датчиком угла поворота. В блок ввода данных заносятся константы электродвигателя и параметры механических цепей привода. В модели процесса заложены различные варианты таблично-графических представлений о распределении частоты вра- щения по длине завинчивания. Информация с датчиков перерабатывается в соответствии с ходом расчетов по формулам. Данные о поднастройке частоты ±Δf и амплитуды импульсов ±ΔI=F(±ΔM) поступают в устройство управления. Таким образом учитывается реакция системы на внешние возмущения (по M) и по электрическим параметрам [3].
Выводы: представленный подход к формированию структуры управляющего процесса, основанный на детальном представлении об его параметрах и ходе протекания, дает возможность не только создавать системы, основанные на традиционных принципах теории автоматического регулирования, но и позволяет разрабатывать более совершенные и быстродействующие системы, например, на основе нейрорегуляторов.
Список литературы Анализ сборочно-резьбообразующего процесса с использованием мехатронной завинчивающей головки
- Березин, С.Я. Структурный анализ технологических систем сборочных машин-автоматов/С.Я. Березин, Р.Е. Чумаков//Автоматизация и современные технологии. -2003. -№ 5. -С. 25-29.
- Березин, С.Я. Научные основы технологии сборочно-резьбообразующих процессов/С.Я. Березин, Р.Е. Чумаков, В.Н. Леонов. -Чита: ЗабГПУ, 2005. -214 с.
- Охрименко, М.И. Технические средства роботизации сборочно-резьбообразующих операций//Механики XXI веку. VIII Всероссийская научно-техническая конференция с международным участием: сборник докладов. -Братск: ГОУ ВПО «БрГУ», 2009. -С. 114-116