Антикоррозионная композиция для защиты арматуры и закладных деталей железобетона
Автор: Матвейко Николай Петрович, Зарапин Виталий Георгиевич, Бусел Екатерина Александровна
Журнал: Вестник Витебского государственного технологического университета @vestnik-vstu
Рубрика: Химическая технология и экология
Статья в выпуске: 2 (23), 2012 года.
Бесплатный доступ
Разработаны и оптимизированы три состава преобразователей ржавчины для защиты арматуры и закладных деталей железобетона, включающие следующие ингредиенты: ортофосфорная кислота, ортофосфат цинка, вода; ортофосфорная кислота, желтая кровяная соль, вода; ортофосфорная кислота, ортофосфат цинка, лигносульфанаты, порошок графита. Изучена микроструктура поверхности образцов стали Ст3 и стали Ст3 с ржавчиной после их обработки разработанными антикоррозионными составами.
Преобразователи ржавчины, антикоррозионная композиция, стальная арматура, сталь, железобетон, детали железобетона, закладные детали, коррозия арматуры, ржавчина, продукты коррозии, антикоррозионные композиции, составы композиций, ортофосфорная кислота, ортофосфат цинка, вода, лигносульфанаты, порошок графита
Короткий адрес: https://sciup.org/142184769
IDR: 142184769
Текст научной статьи Антикоррозионная композиция для защиты арматуры и закладных деталей железобетона
Стальная арматура и закладные детали железобетона, как правило, применяются с уже имеющейся на их поверхности ржавчиной (продуктами коррозии). Это обусловливает дальнейшую коррозию арматуры и закладных деталей в процессе эксплуатации железобетона, существенно снижает прочность конструкций, их безопасность и срок службы [1]. Механическое удаление ржавчины с последующим газопламенным нанесением цинкового защитного покрытия - весьма трудоемкий, экологически небезопасный и дорогостоящий способ подготовки поверхности стальной арматуры и закладных деталей перед изготовлением железобетонных конструкций. Для этих целей перспективными, на наш взгляд, могут быть преобразователи или модификаторы ржавчины. Применение преобразователей ржавчины позволит подготовить поверхность стальных изделий без предварительного тщательного удаления продуктов коррозии. В литературе предлагается значительный перечень преобразователей и модификаторов ржавчины, которые, как правило, содержат три и более ингредиента. При этом часть ингредиентов малодоступна, дефицитна и имеет высокую стоимость [2]. Что касается антикоррозионных композиций для защиты стальной арматуры и закладных деталей железобетона, то они должны преобразовывать ржавчину при комнатной температуре, иметь низкую стоимость и состоять из минимального числа доступных компонентов. Кроме того, такие композиции должны образовывать защитную пленку не только на поверхности стальных изделий, уже имеющих ржавчину, но и на поверхности, свободной от ржавчины.
Цель работы - разработка состава антикоррозионной композиции, обладающей двойным комплексным действием преобразования ржавчины и пассивации поверхности стальных закладных деталей и арматуры железобетона.
Антикоррозионные композиции готовили, используя воду, ортофосфорную кислоту, оксид цинка, желтую кровяную соль K4[Fe(CN)6] , лигносульфанаты и графит. Приготовлено и изучено десять составов композиций, содержащих ортофосфорную кислоту, оксид цинка и воду, восемь составов композиций, содержащих ортофосфорную кислоту; желтую кровяную соль и воду, а также композиции, содержащие ортофосфорную кислоту, оксид цинка, лигносульфанаты и графит с различным соотношением ингредиентов. Для всех антикоррозионных композиций определяли следующие характеристики: время полного высыхания слоя композиции, нанесенной на поверхность стальной пластины, содержащей ржавчину, и без ржавчины; возможность образования защитного пассивного слоя на стали, не имеющей ржавчины; время появления на поверхности первых следов ржавчины, обработанных антикоррозионной композицией стальных образцов, не содержавших ржавчину (для сравнения во всех коррозионных средах определено время появления ржавчины на образцах стали Ст3 без следов коррозии и не имеющих защитного антикоррозионного покрытия); время разрушения защитного слоя, сформированного с помощью антикоррозионной композиции на поверхности образцов, содержавших ржавчину.
Испытания защитных свойств антикоррозионных композиций проводили при полном и частичном погружении образцов стали в следующие коррозионные среды: водопроводную воду, 3 %-ный раствор хлорида натрия и водный раствор цементной штукатурной смеси, близкий по составу к среде, воздействующей на арматуру и закладные детали железобетона в процессе его эксплуатации. Водный раствор цементной штукатурной смеси готовили на основе защитно-отделочной штукатурки НПМ цементной 1 СС 1.25 «Люкс» (СТБ 1263-2001). Этот раствор имел щелочную среду (рН 11,9).
Для определения свойств антикоррозионных композиций использовали образцы стали марки Ст3 в виде пластин размером (мм) 50х50х1 с очищенной поверхностью и с поверхностью, подвергнутой предварительному ржавлению. Для получения на поверхности исследуемых образцов ржавчины их подвергали коррозии следующим образом. Образцы стали Ст3 промывали водой, высушивали на воздухе, затем обезжиривали органическим растворителем путем протирания смоченной в ацетоне ветошью. После этого выдерживали в течение 1 часа в сушильном шкафу при температуре 60 0С и охлаждали до комнатной температуры. Охлажденные образцы помещали в эксикатор в вертикальном положении на расстоянии не менее 20 мм друг от друга. В эксикатор добавляли 3 %–ный водный раствор хлорида натрия таким образом, чтобы расстояние от верхнего края образцов до поверхности раствора составляло не менее 20 мм. Образцы находились в эксикаторе с приоткрытой крышкой (для доступа кислорода воздуха) при температуре 20±2 0С до образования ржавчины на всей поверхности. Испаряющуюся в процессе коррозии образцов воду постоянно пополняли. После образования на поверхности стальных образцов ржавчины их высушивали на воздухе, затем механически с помощью ветоши удаляли рыхлые продукты коррозии и кистью наносили антикоррозионную композицию в двух взаимно перпендикулярных направлениях в два слоя на обе стороны образцов с полной сушкой каждого слоя.
В результате выполненных исследований установлено, что время высыхания слоя антикоррозионной композиции, содержащей ортофосфорную кислоту и оксид цинка, для всех изученных составов меньше, чем время высыхания антикоррозионной композиции, содержащей ортофосфорную кислоту и желтую кровяную соль. С увеличением содержания компонентов антикоррозионной композиции время высыхания слоя увеличивается. Максимальное время высыхания из всех изученных композиций, содержащих ортофосфорную кислоту и оксид цинка, составило при температуре 20 0С 70 минут. Для композиций, содержащих ортофосфорную кислоту и желтую кровяную соль, максимальное время высыхания нанесенного слоя при той же температуре составило 130 минут.
При полном погружении образцов стали без защитного антикоррозионного покрытия в 3 % водный раствор NaCl и водный раствор штукатурки ржавчина при температуре 20 0С появляется уже через 1,5 часа, в то время как в водопроводной воде в тех же условиях ржавчина появляется через 5 часов. Обработка образцов стали Ст3, не имеющей на поверхности продуктов коррозии, композиционным составом, содержащим оксид цинка и ортофосфорную кислоту, увеличивает время появления ржавчины в 3 % водном растворе NaCl и водном растворе штукатурки до 4 – 7 суток, а в питьевой воде – до 15 – 25 суток. Образцы стали Ст3, содержащие на поверхности ржавчину (продукты коррозии), после обработки композицией оксид цинка ортофосфорная кислота при полном погружении в 3 % водный раствор NaCl и водный раствор штукатурки при температуре 20 0С устойчивы к коррозионному воздействию в течение 4 – 7 и 5 – 8 суток соответственно. Аналогичные образцы стали, обработанные композицией желтая кровяная соль ортофосфорная кислота, в тех же условиях не подвергаются коррозии в течение 3 – 5 и 3 – 6 суток. В водопроводной воде образцы стали Ст3 после обработки композицией, содержащей оксид цинка и ортофосфорную кислоту, не подвергаются коррозионному разрушению в течение 14 – 20 суток, а после обработки композицией желтая кровяная соль ортофосфорная кислота – в течение 12 – 14 суток.
В случае антикоррозионной композиции, содержащей ортофосфорную кислоту, оксид цинка, лигносульфанаты и графит, время преобразования ржавчины мало зависит от состава композиции и не превышает 40 минут (при температуре 20 – 25 0С), что меньше, чем для преобразователей: ортофосфорная кислота – оксид цинка или ортофосфорная кислота – желтая кровяная соль. Независимо от количественного состава четырехкомпонентного преобразователя ржавчины после обработки образуется равномерный защитный слой как на стальной поверхности, не имеющей ржавчину, так и на поверхности, содержащей слой ржавчины. При этом образовавшийся слой во всех случаях имеет черный цвет, обусловленный наличием в составе преобразователя ржавчины графита. Однако, если в композиции преобразователя ржавчины содержание графита составляет менее 5 %, то на поверхности стального образца после обработки образуется неравномерный по структуре и цвету защитный слой даже при двукратном нанесении антикоррозионной композиции. Для получения равномерного защитного покрытия при двукратной обработке стального образца как по структуре, так и по цвету в составе композиции для преобразования ржавчины должно содержаться не менее 10 % графита.
Обработка образцов стали Ст3, не имеющей на поверхности продуктов коррозии, композиционным составом, содержащим ортофосфорную кислоту, оксид цинка, лигносульфанаты и графит, увеличивает время появления ржавчины в 3 % водном растворе NaCl и водном растворе штукатурки с 1,5 часа (необработанная сталь) до 10 – 15 суток, а в водопроводной воде до 20 – 30 суток. Образцы стали Ст3, содержащие на поверхности ржавчину (продукты коррозии), после обработки антикоррозионной композицией ортофосфорная кислота, оксид цинка, лигносульфанаты и графит при полном погружении в 3 % водный раствор NaCl и водный раствор штукатурки при температуре 25 0С устойчивы к коррозионному воздействию в течение 8 – 12 и 9 – 15 суток соответственно. В водопроводной воде защитные свойства образовавшегося после обработки четырехкомпонентным преобразователем ржавчины слоя выше, чем в 3 % водном растворе NaCl и водном растворе штукатурки, и составляют более 30 суток.
При частичном погружении стальных образцов в агрессивные среды независимо от состава антикоррозионной композиции, используемой для обработки, коррозия на границе электролит/воздух наступает во всех случаях приблизительно на 1 – 2 суток раньше, чем при полном погружении.
Структура и пористость антикоррозионных слоев, образовавшихся на поверхности образцов стали Ст3 с ржавчиной и не содержащей ее, изучена для составов антикоррозионных композиций ортофосфорная кислота, оксид цинка и ортофосфорная кислота, желтая кровяная соль. Эти композиции наиболее перспективны для защиты стальной арматуры и закладных деталей железобетона, поскольку состоят из минимального количества дешевых и доступных ингредиентов.
Для этого с применением электронного микроскопа Jeol (Япония) получены электронно-микроскопические снимки при увеличении в 50, 100, 200, 500 и 1000 раз. На рисунках 1 и 2 в качестве примера представлены микрофотографии поверхности образцов стали Ст3 и стали Ст3 с ржавчиной, обработанные антикоррозионным составом, содержащим небольшие количества ортофосфорной кислоты и оксида цинка при увеличении в 500 и 1000 раз.
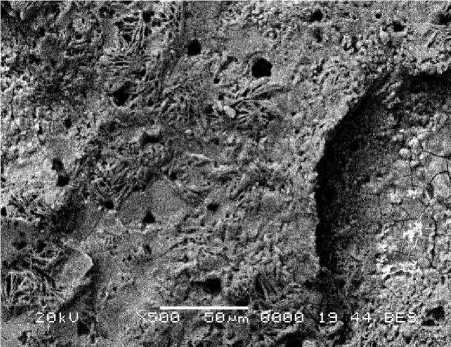
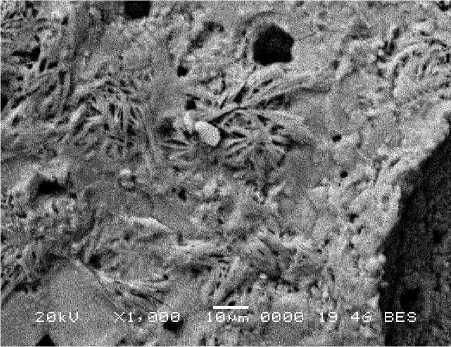
Рисунок 1 – Электронно-микроскопические фотографии поверхности стали Ст3, обработанной антикоррозионным составом, содержащим ортофосфорную кислоту и оксид цинка
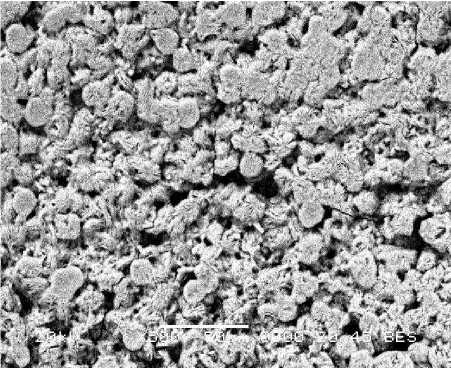
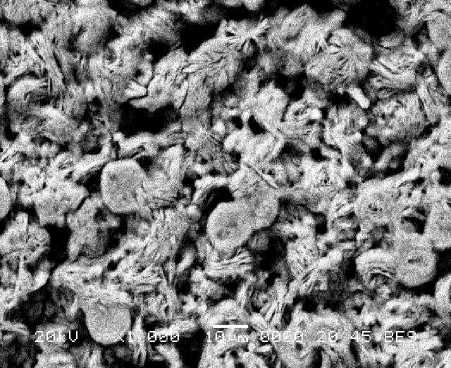
Рисунок 2 – Электронно-микроскопические фотографии поверхности стали Ст3 с ржавчиной, обработанной антикоррозионным составом, содержащим ортофосфорную кислоту и оксид цинка
Из рисунков видно, что микроструктура поверхности для изученных образцов стали существенно различается. На поверхности стали Ст3, не имеющей ржавчины, формируется сплошное покрытие с незначительным количеством пор размером не более 5 мкм. При нанесении антикоррозионного покрытия на сталь Ст3 с ржавчиной формируется защитный слой, имеющий кристаллическую структуру с размерами зерен 10 – 15 мкм. Структура защитного слоя на стали Ст3 без ржавчины мелкокристаллическая игольчатой формы с размерами кристаллов 10 – 20 мкм, в то время как структура защитного слоя на стали Ст3 с ржавчиной состоит преимущественно из кристаллов и кристаллитов сферической формы, размеры которых составляют 10 – 15 мкм. Причем в эту структуру сформированного антикоррозионного защитного поверхностного слоя на стали Ст3 с ржавчиной включены отдельные кристаллы и кристаллиты игольчатой формы.
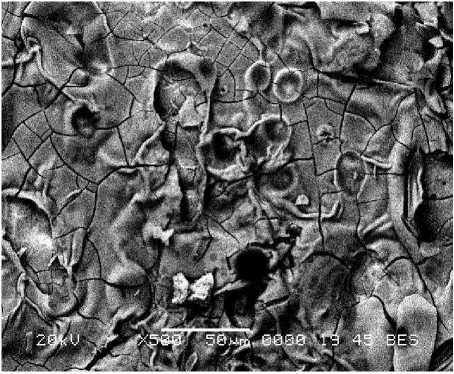
Рисунок 3 – Электронно-микроскопические фотографии поверхности стали Ст3, обработанной антикоррозионным составом, содержащим ортофосфорную кислоту и оксид цинка (с повышенным содержанием компонентов)
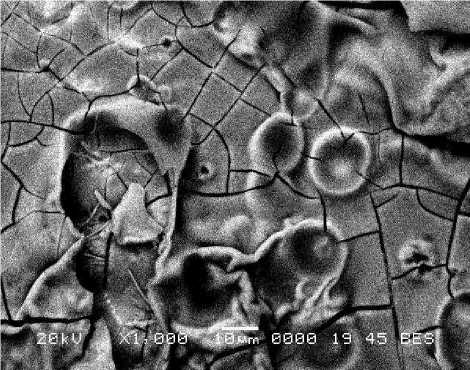
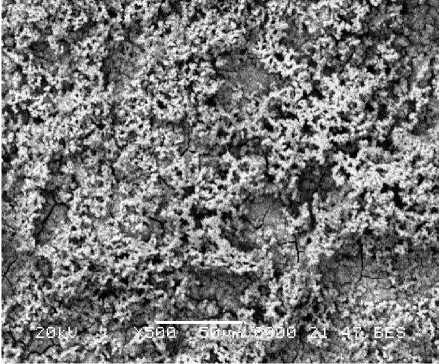
Рисунок 4 – Электронно-микроскопические фотографии поверхности стали Ст3 с ржавчиной, обработанной антикоррозионным составом, содержащим ортофосфорную кислоту и оксид цинка (с повышенным содержанием компонентов)
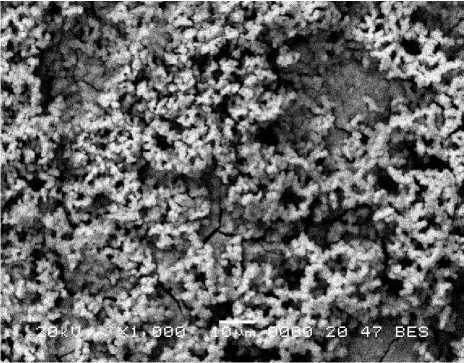
На рисунках 3 и 4 приведены микрофотографии поверхности образцов стали Ст3 и стали Ст3 с ржавчиной, обработанные антикоррозионным составом, включающим ортофосфорную кислоту и оксид цинка (с повышенным содержанием компонентов). Из рисунков видно, что микроструктура поверхности антикоррозионного защитного слоя и в этом случае также значительно различается. На поверхности стали Ст3 без ржавчины формируется сплошное покрытие, практически не имеющее пор. Структура поверхности представляет собой крупные кристаллиты с размерами 10 – 30 мкм, разделенные мелкими трещинами размером 0,5 мкм и менее. При нанесении антикоррозионного покрытия на сталь Ст3 с ржавчиной формируется сплошной равномерный достаточно однородный без разрывов защитный слой, имеющий кристаллическое строение, состоящее из мелких гранул размером 1 – 3 мкм.
Микрофотографии, представленные на рисунке 5, иллюстрируют структуру защитного поверхностного слоя, сформированного на стали Ст3 с ржавчиной с использованием преобразователя ржавчины: ортофосфорная кислота и желтая кровяная соль.
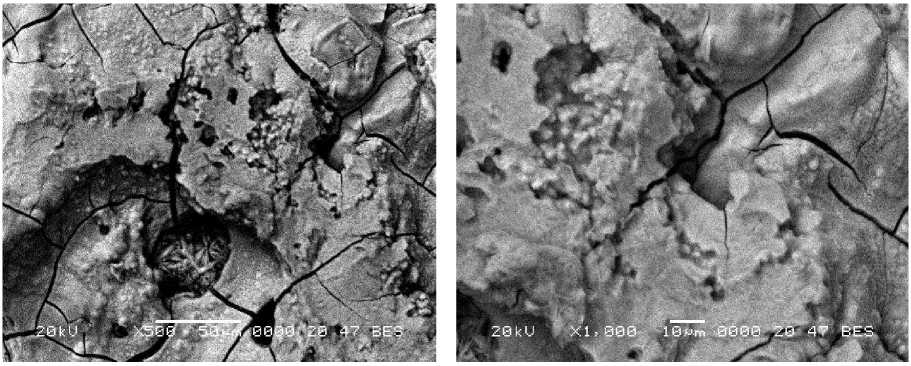
Рисунок 5 – Электронно-микроскопические фотографии поверхности стали Ст3 с ржавчиной, обработанной антикоррозионным составом, содержащим ортофосфорную кислоту и желтую кровяную соль
Видно, что микроструктура защитного слоя по внешнему виду очень близка к микроструктуре антикоррозионного защитного слоя, образующегося на поверхности стали Ст3 после ее обработки преобразователем ржавчины, содержащим ортофосфорную кислоту и оксид цинка (рис. 3). При этом формируется сплошное покрытие неравномерного рельефа без наличия пор. Этот защитный слой имеет крупнокристаллическое строение с размерами отдельных кристаллов, достигающими 1000 мкм, которые разделены между собой мелкими трещинами размером 0,5 мкм и менее.
На основании выполненных исследований определены оптимальные составы антикоррозионных композиций, позволяющие формировать защитный антикоррозионный слой, высыхающий в случае композиции оксида цинка с ортофосфорной кислотой в течение 45 минут, в случае композиции желтой кровяной соли с ортофосфорной кислотой – в течение 90 минут. Защитный антикоррозионный слой, сформированный с применением композиции ортофосфорная кислота; оксид цинка; лигносульфанаты; порошок графита, высыхает в течение 40 минут. Коррозионная устойчивость образцов стали Ст3, имеющих на поверхности ржавчину, после обработки оптимальным составом оксид цинка ортофосфорная кислота, составляет: 7; 8; 20 суток при полном погружении в 3 % водный раствор NaCl ; водный раствор штукатурки; водопроводную воду соответственно. При полном погружении образцов стали Ст3, имеющих ржавчину, после обработки оптимальным составом желтая кровяная соль ортофосфорная кислота коррозионная устойчивость составляет: 5; 6; 14 суток в 3 % водном растворе NaCl ; водном растворе штукатурки; водопроводной воде соответственно. Для образцов стали Ст3, имеющих на поверхности ржавчину, после обработки оптимальным составом ортофосфорная кислота, оксид цинка, лигносульфанаты, порошок графита коррозионная устойчивость составляет: 12, 15, 30 суток при полном погружении в 3 % водный раствор NaCl ; водный раствор штукатурки; водопроводную воду соответственно.
Список литературы Антикоррозионная композиция для защиты арматуры и закладных деталей железобетона
- Бусел, А. В. Коррозия и несиловые факторы разрушения дорожно-строительных материалов. Способы защиты/А. В. Бусел, Н. П. Матвейко. -Минск: БНТУ, 2009. -214 с.
- Торжество преобразователей ржавчины/[Электронный ресурс]. -2011. -Режим доступа http://www.uscars.lt/forumas/download/file.php?id=1814&sid. -Дата доступа 04.10. 2011