Аппаратная реализация прибора для измерения геометрических параметров бандажей колесных пар
Автор: Буйносов А.П., Тихонов В.А.
Журнал: Журнал Сибирского федерального университета. Серия: Техника и технологии @technologies-sfu
Статья в выпуске: 2 т.6, 2013 года.
Бесплатный доступ
В статье представлен разработанный прибор для измерения геометрических параметров бандажей колесных пар без выкатки из-под локомотива непосредственно на подвижном составе. Даны рекомендации по аппаратной реализации и конструированию, обеспечению работы прибора с гарантированной точностью измерений.
Короткий адрес: https://sciup.org/146114733
IDR: 146114733
Текст научной статьи Аппаратная реализация прибора для измерения геометрических параметров бандажей колесных пар
В настоящее время для контроля за степенью износа бандажей колесных пар электровозов и тепловозов в локомотивных депо Российской Федерации применяются механические измерительные средства, такие как шаблоны, скобы и ряд других. Для обеспечения оперативного, высокоточного контроля элементов профиля катания колесных пар необходимо создание прибора, позволяющего выполнять эти задачи. Такой прибор был разработан в Уральском государственном университете путей сообщения (УрГУПС), он предназначен для измерения проката, толщины гребня и диаметра колесных пар локомотивов, проведения допускового контроля и разбраковки колес при техническом обслуживании локомотивов, освидетельствовании и ремонте [1]. Измерение этих параметров может производиться непосредственно на подвижном составе, без выкатки колесных пар, что обеспечивает оперативность контроля и экономическую эффективность.
Целью проведенного исследования является выработка обоснованных рекомендаций по конструированию, обеспечивающих работу прибора с гарантированной точностью измерений.
Измеритель параметров колесных пар предназначен для обеспечения оперативного, высокоточного измерения проката, толщины гребня колесных пар, проведения допускового контроля и разбраковки при их техническом обслуживании, освидетельствовании и ремонте и представляет собой переносное малогабаритное устройство, имеющее модульную конструкцию, общий вес которого не более 1,5 кг с габаритами 220 x 140 x 147 мм.
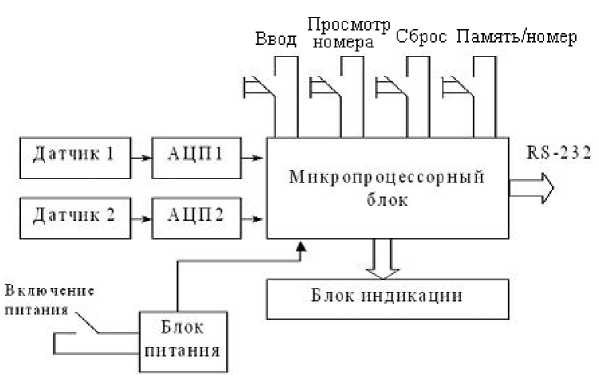
Рис. 1. Функциональная схема измерителя
Функциональная схема измерителя представлена на рис. 1, а алгоритм измерения – на рис. 2.
В состав прибора входят вычислитель и измерительная скоба с установленными на ней измерительными датчиками. Вычислитель для обоих вариантов выполнен на базе микропроцессора фирмы Intel 80С51, с помощью которого осуществляется измерение, обработка и индикация параметров непосредственно на месте проведения замеров. Все измеренные параметры хранятся в энергонезависимой памяти прибора в течение одной или нескольких рабочих смен, их можно оперативно просмотреть на блоке индикации. Объем оперативной памяти микропроцессорного блока 32 килобайта. Прибор имеет две модификаций: ИД и КИП (1-я – для измерения диаметра колесных пар, 2-я – для производства замеров величины проката и толщины гребня), которые отличаются измерительными датчиками [2].
Первый вариант (рис. 3) создан для измерения диаметра колеса и использует два резистивных датчика. Основной датчик устанавливается на гребень, и по нему измеряется величина диаметра; вторым датчиком производится измерение высоты гребня, и это значение вычитается из величины диаметра колеса. Это было сделано для уменьшения величины ошибки измерения, вносимой при измерениях диаметра бандажа по кругу катания из-за неоднородности рабочей поверхности колеса.
Во втором варианте (рис. 4), созданном для измерения проката и толщины гребня, в измерительной скобе используются три резистивных датчика. Напряжение, снимаемое с датчиков, преобразуется восьмиразрядными АЦП для каждого датчика отдельно и передается по шине данных в ответ на запрос центрального процессора.
Предусмотрена передача измеренных параметров в базу данных, установленную на компьютере, через стандартный последовательный порт. В базе данных осуществляется прогнозирование износа колес и формирование протоколов.
Интерфейс с компьютером через последовательный порт в стандарте RS-232 осуществляется через оптическую развязку и стандартный кабель. Блок питания представляет собой аккумулятор или обычную батарею типа «Крона», расположенную в корпусе вычислителя. Вклю-
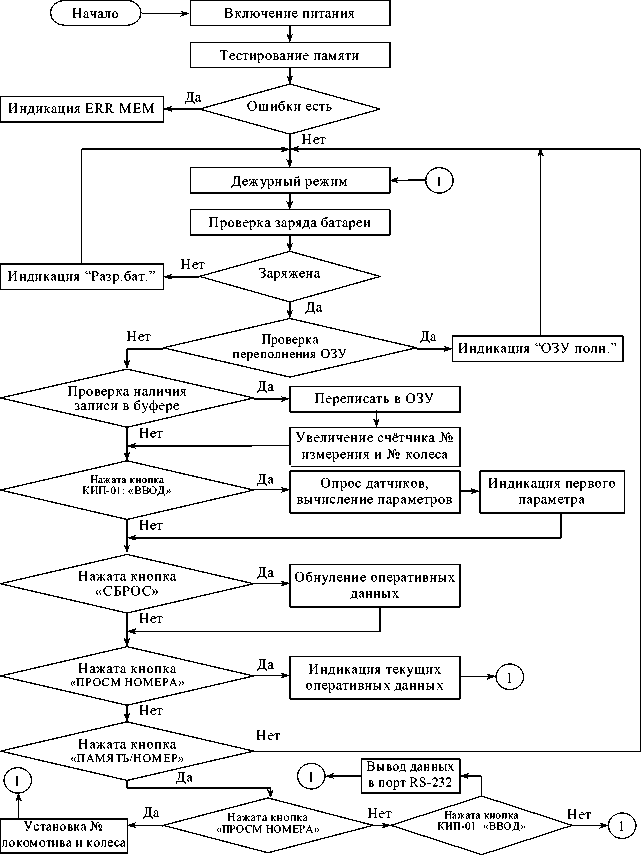
Рис. 2. Алгоритм измерения параметров
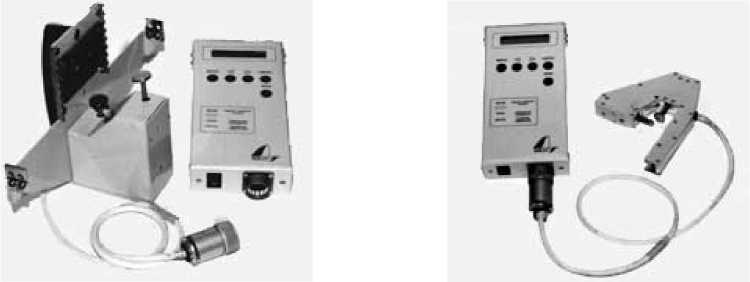
Рис. 3. Прибор для измерения диаметра колеса
Рис. 4. Прибор для измерения проката и толщины гребня чение питания производится выключателем, расположенным на корпусе вычислительного блока. В качестве функциональной клавиатуры использованы микрокнопки типа ПКН-159-3.
Конструкция прибора позволяет применять его в условиях загрязненной окружающей среды и при широком диапазоне температур.
Технические характеристики прибора для измерения диаметра:
– диапазон измерения диаметра колеса, мм – 910–1310;
– погрешность измерения диаметра колеса, не более, мм – ± 0,5;
– потребляемая мощность, Вт – 0,5;
– дискретность индикации параметров, мм – ± 0,01;
– время измерения, не более, с – 0,5.
Это было сделано для уменьшения величины ошибки измерения, вносимой при измерениях по кругу катания из-за неоднородности этой поверхности, минимизации влияния углового смещения измерительной скобы относительно торца колеса на результат измерения.
Принцип измерения диаметра колесных пар основан на определении величины стрелы сегмента, образуемого при установке измерительной скобы на колесо [3].
Технические характеристики прибора для измерения проката и толщины гребня:
– диапазон измерения проката, мм – 0–8;
– диапазон измерения толщины гребня, мм – 22–34;
– диапазон измерения параметра крутизны гребня, мм – 0–20;
– диапазон измерения диаметра колеса, мм – 910–1310;
-
– погрешность измерения проката и толщины гребня, мм – ± 0,2;
-
– погрешность измерения крутизны гребня, мм – ± 0,1;
-
– дискретность индикации параметров, мм – 0,01;
-
– время измерения, не более, с – 0,5.
Измерение параметров конфигурации профиля гребня выполняется с учетом номинального значения высоты гребня (30 мм). Величина проката определяется как разница между измеренной высотой гребня и ее номиналом. Толщина гребня определяется прямым измерением на уровне 20 мм от вершины гребня, при номинальной высоте гребня 30 мм и измерением на уровне 18 мм, при номинальной высоте гребня 28 мм. Датчик измерения высоты гребня и проката должен располагаться на расстоянии 70 мм от торца обода колеса (рис. 5).
Толщина гребня в этом варианте вычисляется следующим образом:
Х - у • sin a , (1)
где у - длина измерительного крюка.
При использовании для измерения толщины гребня датчика с измерительным крюком за базовые размеры можно принять следующие величины (рис. 6).
Величина проката вычисляется как
( l — l опор ) + h — 30. (2)
Для производства измерений с достаточной степенью точности необходимо оценить влияние перекоса при изготовлении опор прибора, прилегающих к торцу колеса, а также влияние смещения одной из опор относительно торца обода колеса на определение высоты гребня.
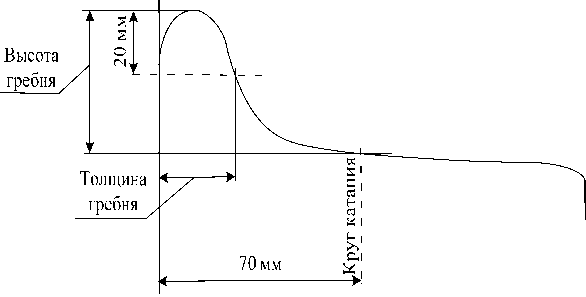
Рис. 5. Измерение параметров колесных пар
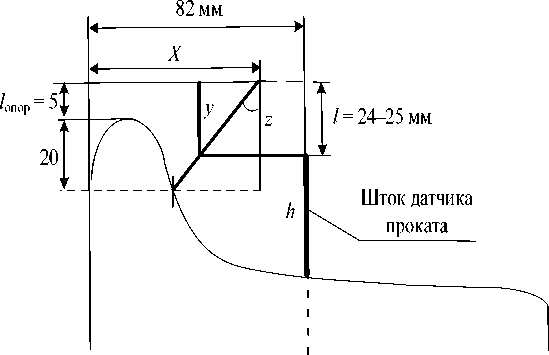
Рис. 6. Базовые размеры при производстве измерений
Выражение для оценки этой погрешности выглядит следующим образом:
A h гр - ( Х -2) № (3)
где в - угол наклона колеса (конусность по кругу катания) в точке измерения величины проката, в = 1°25 ‘ 56 ’’ (по ГОСТ 11018-2000); Х - смещение одной из опор относительно другой, в мм; у - смещение датчика относительно торца гребня, у = Х /2.
Результаты представлены в табл. 1, из которой следует, что поперечное смещение измерительной головки относительно торца обода незначительно влияет на точность измерения высоты гребня. Тем не менее необходимо выдерживать перекос в установке опор, которые прилегают к торцу обода не более 0,5 мм.
Выражение для оценки ошибки измерения толщины гребня из-за смещения одной из опор относительно торца обода на определение толщины гребня имеет вид
АТ = у • { X - ном.толщ . + ( x /2)}/ z - у ■ tg a ,
Таблица 1. Погрешность измерения толщины гребня от смещения опоры
Х , мм |
∆ h гр, мм |
0,25 |
0,0027 |
0,5 |
0,0055 |
1,0 |
0,0100 |
1,5 |
0,0160 |
2,0 |
0,0219 |
Таблица 2. Оценка ошибки измерения толщины гребня бандажа
Точка на гребне соответствует расстоянию 20 мм от вершины гребня. Задавшись размерами: z = 25 мм; номин. толщ. = 34 мм; X = 40 мм; Х = 45 мм; у = 25,7 мм; α = 13,495° и α = 23,7°, получаем следующие результаты, приведенные в табл. 2.
Таким образом, величина перекоса не должна превышать 0,25 мм, а размер расположения центра поворота измерительного крюка от торца обода должен быть минимально возможным.
Для оценки влияния наклона измерительной скобы относительно торца гребня исходя из неточности изготовления измерительной головки (плохо выдержаны углы в 90° на раме измерительной головки) на погрешность измерения параметров используется выражение
∆ Т = y [tg( α – ∆α ) – tg α ], (5)
где ∆α – угол наклона относительно торца; α – угол поворота измерительного крюка при номинальных размерах обода.
Полученные результаты свидетельствуют о том, что необходимо строго выдерживать углы и не превышать углы отклонения более 0,5°, при этом полный угол поворота измерительного крюка может быть до 25°, при базовой точке поворота крюка, расположенной на расстоянии 45 мм от торца обода колеса.
Полный поворот резистивного датчика составляет 300°. Для обеспечения точности измерения толщины обода и величины проката, равной ± 0,5 мм, необходимо использовать коэффициент передачи
K = 300°/25° = 12.
Таблица 3. Погрешность измерения толщины гребня от угла поворота датчика
∆α, ° |
А Т (ном. 34 мм а = 13,495°, Х = 40 мм) |
А Т (ном. 34 мм а = 23,749°, Х = 45 мм) |
0,5 |
0,2367 |
0,283 |
1,0 |
0,4724 |
0,565 |
1,0 |
0,7070 |
0,844 |
2,0 |
0,9410 |
1,121 |
Чувствительность резистивного датчика 16,6 Ом при полном сопротивлении 10 кОм, т.е. датчик чувствует поворот на 0,5° (табл. 3).
Из результатов проведенных исследований следуют рекомендации по конструкции измерителя параметров колесных пар:
-
- исходя из требований на погрешность измерения диаметра, равную 0,5 мм, можно принять расстояние между базовыми опорами измерительной скобы в 350 мм;
-
- для исключения сползания датчика при наклонах и измерении колес различных диаметров по гребню шток датчика должен иметь наконечник диаметром не менее 20 мм;
-
– нельзя использовать шестеренчатую передачу на резистивный датчик с коэффициентом передачи меньше чем K = 12;
-
– необходимо обеспечить плотное прилегание базовой поверхности измерительной скобы к торцу колеса с углом наклона в плоскости измерения не более 0,5°, отклонение опор, прижимаемых к торцу колеса, относительно друг друга на величину не более 0,25 мм;
-
- для обеспечения точности измерения высоты гребня необходимо делать опору для вершины гребня шириной не менее 25 мм от торца обода колеса;
-
– так как по инструкции МПС ЦТ/329 шероховатость обработки поверхности профиля колеса в точке измерения проката должна составлять RZ = 80 мм, нельзя делать шток датчика измерения проката с точечным наконечником. Торец штока должен быть обработан с закруглением 3°в плоскости измерения.
Таким образом, можно сделать вывод о том, что точность изготовления, сборки и настройки прибора существенным образом влияет на точность измерения толщины гребня и проката, диаметра колеса по кругу катания. Опоры прибора, прилегающие к торцу колеса, должны быть сделаны в виде двух реек, одна из которых больше по длине, а вторая длиной не более 10 мм. Это позволяет устанавливать прибор с плотным прилеганием к торцу колеса, тем самым уменьшая ошибку измерения как для головки измерения диаметра, так и для головки измерения толщины гребня, величины проката.
Для сравнения разработанного прибора и скобы КИ-124 у 58 колесных пар электровозов производили измерения диаметров бандажей и определяли их разность на одной колесной паре. Значения Di соответствуют результатам, полученным разработанным прибором, а Di ’ – cкобой КИ-124.
Ошибка измерений А ,- (i = 1, 2,..., n ) определена как разница в измерениях диаметров бандажей двумя приборами, т. е. А , = D , - D , ’. Полученный ряд ошибок является выборкой объема n .
Гистограммы распределения ошибок измерения F ( А ) диаметров бандажей и их разности представлены на рис. 7 и 8.
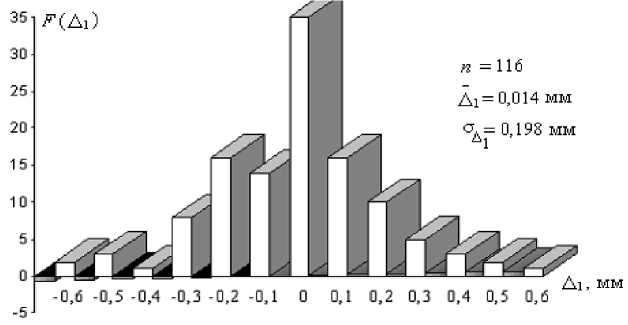
Рис. 7. Распределение ошибки в определении диаметров бандажей, измеренных двумя устройствами
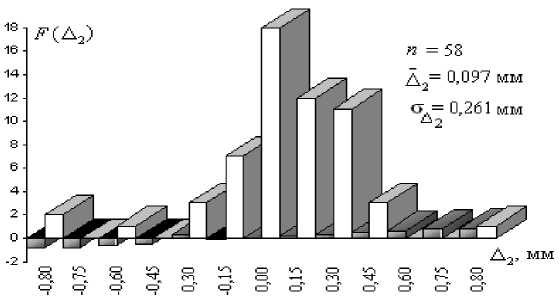
Рис. 8. Распределение ошибки в определении разности диаметров бандажей, измеренных двумя устройствами
Средние ошибки измерений составляют Δ 1 = 0,014 мм и Δ 2 = 0,097 мм, среднеквадратические отклонения σ Δ1 = 0,198 мм и σ Δ2 = 0,261 мм соответственно для измерения диаметра и разности диаметров бандажей. Максимальная ошибка в измерении, равная 3 σ∆ , не превышает 0,8 мм. Выборки являются зависимыми или связанными, так как диаметр каждого из n = 116 бандажей измерялся как первым, так и вторым прибором. Поэтому индивидуальные значения результатов измерений попарно взаимосвязаны.
Чтобы решить вопрос о том, согласуются ли измерительные свойства обоих приборов, измеренные значения D i ( i = 1, 2, …, n ) рассматриваем как выборку из нормально распределенной генеральной совокупности со средним значением m1 и дисперсией σ 12 , а значения Di ’ – как выборку из нормально распределенной генеральной совокупности с N ( m 2 ; σ 2 ). Проверяем гипотезу Н0 : m 1 – m 2 = m ∆ = 0. Если гипотеза верна, то ряд значений ∆ i ( i = 1, 2, …, n ) является выборкой объема n из нормально распределенной генеральной совокупности со средними зна- 2
чениями m ∆ и дисперсией σ Δ .
Для этого воспользуемся критерием Стьюдента с выборочной функцией [4, 5]:
Таблица 4. Сравнение точности измерительных приборов
Контролируемый параметр |
Значения факторных нагрузок d , |
А 1 , мм |
σ ∆ , мм |
t , мм |
Число степеней свободы, m |
t α, m , мм |
Диаметр бандажей |
0,148 |
0,014 |
0,198 |
2,601 |
115 |
2,62 |
Разность диаметров бандажей |
0,221 |
0,097 |
0,261 |
2,506 |
57 |
2,66 |
-
ˆ Δ-mΔ
.
σΔ
Расчетные значения t-критерия сравнивали с предельными tа,т (табл. IV в [6]) для критической области |f| > ta,m при уровне значимости а = 0,01 и m = n - 1 степенями свободы. Если |f| > ta,m, то гипотеза Н0 отвергается. И, наоборот, при |f| > ta,m нулевая гипотеза принимается. Результаты проверки гипотезы Н0: mд = 0 приведены в табл. 4, из которой видно, что гипотезы подтверждаются.
Для сопоставления точности результатов, полученных двумя приборами, использованы методы факторного анализа. Нагрузка общего (генерального) фактора а i между одинаковыми контролируемыми параметрами определялась по методу «наименьших квадратов»:
a i
R ⋅ σ
Δ i Δ
σ
i
где R А i - коэффициент корреляции между случайными величинами А и D i ; сА и c i - среднеквадратические отклонения тех же величин А и D i .
Характерность (точность) определяется по соотношению [4]
di 2 = 1 - ai 2 . (8)
Результаты расчета факторных нагрузок, проведенного двухфакторным методом, показывают, что отклонения a i от среднего значения (единицы), определяемое характерностью d i , вызвано главным образом ошибками измерения самих параметров (табл. 4).
Значения характерностей контролируемых параметров значительно меньше той точности измерительного инструмента, который применяется в эксплуатации. Так, при измерении толщины бандажа относительная точность толщиномера составляет ± 10 %, тогда как квадраты характерностей, полученные в результате расчетов для диаметров бандажей, составляют 2,190 %, а для разности диаметров – 4,884 %.
Использование разработанного прибора позволяет отбраковывать колесные пары, имеющие разность диаметров более установленной нормы согласно инструкции ЦТ/329, тем самым предотвращать интенсивный износ гребней бандажей, нарастание проката.
Гарантийный срок эксплуатации 12 месяцев исчисляется со дня ввода прибора в эксплуатацию. В течение гарантийного срока безвозмездно устраняются дефекты или производится замена вышедших из строя отдельных сборочных единиц прибора, если такая необходимость возникла не по вине пользователя.