Баротермическая обработка ингредиентов комбикормов
Автор: Сыроватка Владимир Иванович, Жданова Наталья Владимировна, Рассказов Александр Николаевич, Торопов Дмитрий Иванович
Журнал: Инженерные технологии и системы @vestnik-mrsu
Рубрика: Технологии и средства механизации сельского хозяйства
Статья в выпуске: 3, 2019 года.
Бесплатный доступ
Введение. В статье обоснована необходимость высокотемпературной обработки ингредиентов комбикормов. Рассмотрены принципы работы и конструктивные особенности применяемых способов и оборудования для кормопроизводства. Проанализированы фазовые переходы, достоинства и выделены ключевые энергетические, технологические и технические недостатки. Целью исследования является обоснование возможности создания поточной линии тепловой обработки комбикормов путем применения тепловых затворов, обеспечивающих непрерывную загрузку сырья в реактор и выгрузку обработанных кормов при высоком давлении и температуре. Материалы и методы. Предложено перевести процесс баротермической обработки в более высокую зону фазовой диаграммы системы р, t (давление и температура). Это участок зоны перегретого пара с параметрами температуры 300-374 °С, давления 12-21 МПа и экспозицией обработки 30-60 секунд, что заменяет высокозатратные процессы нормализации, экспандирования, экструдирования и гранулирования. Показано изменение энтальпии Н в диапазоне Р от 0 до 21 МПа и t от 0 до 600 °С. Тепловые режимы представлены в аналитических зависимостях (формулах), которые являются базовыми условиями применения цифровых технологий. Результаты исследования. Предложено конструктивное исполнение реактора с тепловым затвором на загрузке и выгрузке, который является базовым агрегатом поточной линии тепловой обработки комбикормов. Результаты исследования являются основополагающими для разработки проекта и образца поточной малоемкостной линии. Обсуждение и заключение. Переход процесса баротермической обработки комбикормов в зону перегретого пара позволяет осуществить перевод плохо усвояемых элементов зерновых и бобовых в легкоусвояемые, очистить корма от патогенных бактерий. К преимуществам реактора и линии относятся простота конструкции, экономия энергии и возможность реализации перспективных цифровых технологий.
Баротермическая обработка комбикормов, фазовые переходы, реактор, поточная линия
Короткий адрес: https://sciup.org/147220629
IDR: 147220629 | DOI: 10.15507/2658-4123.029.201903.428-442
Текст научной статьи Баротермическая обработка ингредиентов комбикормов
Актуальность данной работы состоит в том, что объем производства и качество продуктов питания – зеркальное отражение этих показателей в комби-кормах1 [1; 2]. Известно, что мировое производство комбикормов в 2017 году составило 1,07 млрд т2, в том числе для свиней – 289 млн т или 28 % мирового производства; для птиц – 300 млн т, для молочных коров – 118 млн т. В Китае на 6000 заводах произведено 187 млн т комбикормов, в США – 173 млн т, в Бразилии – 70 млн т, в Индии – 34 млн т. В России произведено 27,3 млн т на комбикормовых заводах и в хозяйствах – 10,7 млн т. Общее производство комбикормов составило 38 млн т. Заводские корма использованы: для свиней – 10 млн т, для птиц – 15,2 млн т и для КРС – 2,1 млн т3. Кроме того, в животноводческих и птицеводческих хозяйствах ежегодно используется 40– 50 млн т фуражного зерна в виде кормовых смесей. Мировое производство масличных культур (соя, рапс, арахис и подсолнечник) в сезоне 2016–17 года составило 509 млн т4, а с учетом семян хлопка, кокосовых орехов, масличной пальмы производство составит 571 млн т. В США произведено сои 114,3 млн т, при урожае 34 ц/га, в Бразилии – 101 млн т, в Аргентине – 57 млн т, в России – 3,5 млн т, а рапса – 1,5 млн т5.
Обзор литературы
Решение задачи вытекает из потребности в тепловой обработке ингредиентов комбикормов.
В зависимости от вида фуражного зерна, сорта растения, условий его произрастания и других факторов в нем содержится 56…70 % безазотистых экстрактивных веществ6, которые плохо усваиваются животными и птицей. При тепловой обработке крахмал переходит в усвояемые декстрины и полисахариды.
Том 29, № 3. 2019
Нейтрализация антипитательных веществ в сое и рапсе. Соя и рапс – важные белковые и энергетические компоненты. Соевая мука является основным источником белка при производстве комбикормов, однако содержит 5…10 % антипитательных веществ-ингибиторов, которые подавляют и задерживают ферменты, вырабатываемые поджелудочной железой. В результате поджелудочная железа вынуждена продуцировать их более интенсивно, что вызывает ее гипертрофию [3–5].
Эффективным путем устранения ингибиторов является высокотемпературная обработка в сочетании с повышенным давлением. Увеличивает эффективность термообработки также предварительное пропаривание сои в течение 20–30 мин. Наибольшую энергетическую ценность в комбикормах составляют семена рапса, поскольку содержат 40–48 % жира и 21–33 % сырого протеина при коэффициенте переваримости 84,4–93,4 % (табл.1)7.
Однако семена рапса содержат эруковую кислоту, которая не утилизируется ферментативной системой млекопитающих и птиц и имеет тенденцию накапливаться в их организме. Эруковая кислота вызывает нарушения сердечно-сосудистой системы, инфильтрации скелетной мускулатуры и миокарда, цирроз печени. Доля эруковой кислоты в составе растительных масел: рапсовое масло 56–65 %, горчичное – 50 %, сурепное масло – 47 %. Семена рапса подлежат глубокой термообработке.
Т а б л и ц а 1
T a b l e 1
Химический состав масличных культур The chemical composition of oilseeds
Вид зерна / Type of grain |
Вода, % / Water, % |
Белок, % / Protein, % |
Жир, % / Fat, % |
Углеводы усвояемые, % / Digestible carbohydrates, % |
Пищевые волокна, % / Alimentary fiber, % |
Зола, % / Ash, % |
Горох / Peas |
14,0 |
20,5 |
2,0 |
49,5 |
11,2 |
2,8 |
Соя / Soy |
12,0 |
34,9 |
17,3 |
17,3 |
13,5 |
5,0 |
Подсолнечник / Sunflower |
8,0 |
20,7 |
42,9 |
10,5 |
5,0 |
2,9 |
Рапс / Rape |
8,1 |
30,8 |
43,6 |
7,2 |
5,8 |
4,5 |
Фасоль / Beans |
14,0 |
21,0 |
2,0 |
47,0 |
12,4 |
3,6 |
Чечевица / Lentils |
14,0 |
24,0 |
1,5 |
46,3 |
11,5 |
2,7 |
Горчица / Mustard |
6,4 |
25,8 |
30,8 |
23,4 |
8,8 |
4,8 |
Температура разложения эруковой кислоты – 380 °C, а плавления – 33,8 °C 8.
Зерновое сырье и другие компоненты, используемые для производства комбикормов, нередко обсеменены микроорганизмами, где присутствуют токсичные для человека и животных продукты метаболизма этих грибков. Обеззараживание всех компонентов улучшает качество комбикормов.
Использование в комбикормах рыбной, мясокостной муки, мелассы, жиров и других незерновых компонентов невозможно без глубокой тепловой обработки [6].
Достижение температуры обрабатываемого комбикорма 170–180 °C в настоящее время [7; 8] осуществляется в несколько этапов с применением сложных технологических схем и дорогостоящего оборудования: первый этап – нормализация смеси, то есть рассыпной комбикорм паром прогревается до 100 °C; второй – смесь пропускается через экспандер, где подогревается до 130 °C, затем – в экструдер, где температура смеси достигает 150 °C и в заключение корма подаются в гранулятор, где температура гранул достигает 180 °C [9; 10]. Этой температуры недостаточно для более глубокой декстринизации (только 60 %). На всех трех этапах повышение температуры корма достигается трением при высоком давлении, что энергоемко. Все это ведет к увеличению удельного расхода электроэнергии. Технологическую схему тепловой обработки ингредиентов комбикормов следует упростить, что значительно снизит удельную энергоемкость, металлоемкость и капиталоемкость; это возможно при выполнении процесса тепловой обработки в области сухого пара9 [11; 12].
Материалы и методы
Исходя из мировых тенденций развития энергетики, необходимо переводить процесс баротермической обработки в более высокую область фазовой диаграммы системы p, t (давление, температура). В p,t-диаграм-ме фазового состояния воды рабочий процесс тепловой обработки комбикормов смещен от нулевой к критической точке (374 °С)10 [13]. Это участок зоны перегретого пара с параметрами температуры 300–374 °С, давления 12–21 МПа и экспозицией обработки 30–60 с (рис. 1)11, что позволяет исключить высокозатратные несовершенные процессы (экспандирование, экструди-рование, гранулирование), упростить структурную схему поточных линий по производству гранулированных кормов, в несколько раз снизить энергоемкость и металлоемкость, использовать отработанный пар (120–150 °С) на предварительную тепловую обработку сои, рапса, зернового сырья, а также мелассы, жира и других добавок, применить цифровые технологии и малоемкостные поточные автоматизированные линии по производству обезвреженных, экологически чистых рассыпных, гра-
Том 29, № 3. 2019 нулированных, лечебных кормов, а также вспученного фуражного зерна.
Энтальпия системы теплового процесса
Известно, что в результате подвода теплоты к телу ее температура повышается и вследствие увеличения объема тела производится внешняя работа; подведенная к телу теплота расходуется на увеличение внутренней энергии тела U и на совершение работы L 12 [14].
Это выражается уравнением:
Q 1 - 2 = b U 1 - 2 + L 1 - 2 , (1)
где Q 1‒2 – теплота, сообщенная телу при нагревании от состояния 1 до состояния 2; Δ U 1‒2 ‒ изменение внутренней энергии тела в том же процессе, равное разности внутренних энергий системы в точках 2 и 1; L 1‒2 – работа, совершенная телом в процессе перехода системы
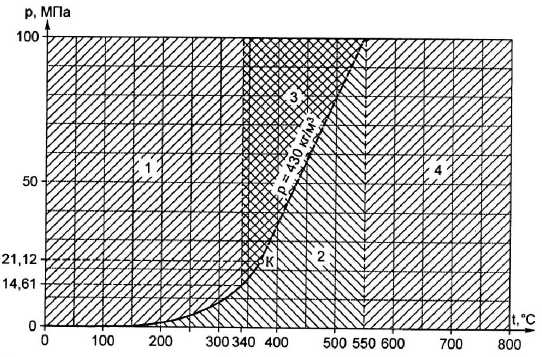
Р и с. 1. Области применения уравнений состояния Международной системы в p,t -диаграмме: K – критическая точка
F i g. 1. Fields of application of equations of state International system in p,t -diagram: K – critical point
из точки 1 в точку 2 (повышение давления в котле).
Уравнение (1) выражает первый закон термодинамики или частный случай общего закона сохранения энергии: для любой изолированной системы количество энергии, заключенное в этой системе, сохраняется неизменным.
Это же соотношение, записанное в дифференциальной форме, имеет вид:
dQ = dU + dL . (2)
Принято, что теплота, подводимая к системе, считается положительной, а теплота, отводимая от системы – отрицательной. Соответственно, работу, производимую системой, считать положительной, а работу, совершаемую над системой – отрицательной.
Так как работа расширения является функцией процесса p,V -диаграммы, то уравнение (2) можно записать:
dQ = dU + pdV . (3)
Сумма внутренней энергии системы U и произведения давления системы p на величину объема системы V называется энтальпией (теплосодержанием) и обозначается через H :
H = U + pV . (4)
Энтальпия – это та энергия, которая доступна для преобразования в теплоту или работу при определенной температуре и давлении. Энтальпия измеряется в тех же единицах, что и теплота, работа, внутренняя энергия.
Первый закон термодинамики характеризует процессы превращения энергии теплоты или работы с количественной стороны13.
Второй закон термодинамики характеризует качественную сторону этих процессов. Так же как и первый закон, он сформулирован на основании опытов: любой реальный самопроизвольный процесс является необратимым. Теплота не может сама собой переходить от более холодного тела к более нагретому, поэтому идею о существовании вечного двигателя второго рода осуществить невозможно (Планк)14.
Термическим коэффициентом полезного действия (КПД) цикла η B называется отношение работы цикла ( Q 1 ‒ Q 2) к количеству теплоты Q 1, подведенного к рабочему телу в цикле:
П т

где Q 2– количество полезно использованной теплоты.
П т
T - T 2 = Q i - Q 2
T 1 Q 1
где T 1 и T 1 ‒ начальная и конечная температура цикла.
Энтропия (от греческого «поворот») – степень неполноты, неопределенности знаний, впервые был введен Клаузисом в термодинамике в 1865 году для определения меры необратимого рассеивания энергии, меры отклонения реального процесса от идеального:
5Q dS = T ’ '7)
где dS – приращение энергии; δQ – минимальная теплота, подведенная к системе; Т – абсолютная температура процесса.
Дифференциал энтальпии, выраженный в собственных переменных, через энтропию S и давление p :
dH = d (U + pV), dH = 8Q + Vdp, (8) dH = TdS + Vdp.
Энтальпией системы удобно пользоваться в тех случаях, когда в качестве независимых переменных, определяющих состояние системы, выбирают давление p и температуру T, H ( p,T ) .
По таблице 315 рассчитаны и показаны изменения энтальпии (рис. 2) в диапазоне t от 0 до 600 °С и p от 0 до 21,0 МПа.
Из графика (рис. 2) видно, что энтальпия системы при температуре 300–400 °С в пять раз выше, чем при температуре на участке 100 °С, а коэффициент теплопередачи резко возрастает. Этот тепловой поток при высоком давлении и коэффициенте теплопередачи ускоряет прогрев комбикормов и многократно сокращает время обработки (от 60–70 минут до 50–60 секунд). При этом достигается экономия удельных затрат энергии и металлоемкости.
Удельный расход комбикормов при использовании измельченных смесей фуражного зерна, но не подверженных тепловой обработке, возрастает в 1,2…1,3 раза. В таком случае выгодно применять, в особенности для свиней, вспучивание отдельных видов фуражного зерна или их смесей.
Задача заключается в обеспечении заданных режимов баротермической обработки концентрированных кормов в непрерывном потоке за счет создания устройств загрузки и выгрузки в виде тепловых затворов, обеспечивающих непрерывную загрузку сырья и выгрузку обработанных кормов (при высоком давлении и температуре), что позволяет исключить простои реактора при загрузке и выгрузке, повысить КПД реактора и его производительность, при этом снизить потери энергии [14].
Реактор баротермической обработки концентрированных кормов16 [29] включает горизонтально расположенную емкость (далее корпус) 1 (рис. 3)
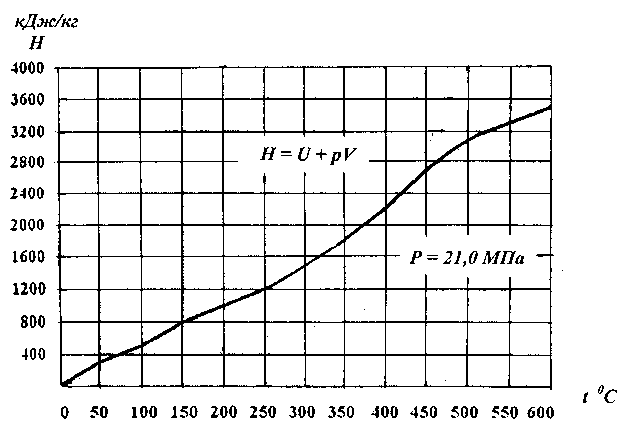
Р и с. 2. Изменения энтальпии Н при увеличении p от 0 до 21,0 МПа и t от 0 до 600 °С
F i g. 2. Changes in the enthalpy H with increasing p from 0 to 21,0 MPa and t from 0 to 600 °C
с загрузочной горловиной 2, выгрузным люком 3 и рабочим органом 4. На загрузочной горловине 2 установлен тепловой затвор загрузки, состоящий из цилиндрического корпуса 5, внутри которого на валу 6 последовательно расположены: двухступенчатый шнек, прецезионно сопряженный с корпусом затвора (рис. 4), ленточная навивка и лопасти квадратной формы 9, установленные под углом α = 30° к оси вала, имеющие рабочие кромки, заточенные под углом 15–20°. К выгрузному люку 3 присоединен тепловой затвор выгрузки, состоящий из цилиндрического корпуса 10, внутри которого на валу 11 последовательно расположены: двухступенчатый шнек с ленточной навивкой (12 и 13) и лопасти квадратной фор- мы 14, установленные под углом 30° к оси вала, имеющие рабочие кромки, заточенные под углом 15–20°.
Конструктивное выполнение тепловых затворов загрузки и выгрузки в виде последовательно установленных на валу двухступенчатого шнека и лопастей позволяет за счет исполнения шнека, имеющего ленточную навивку (шаг навивки S первой ступени больше шага навивки второй ступени S1 в 2 раза), принимать рассыпной концентрированный корм (сырье) первой ступенью, перемещать его вдоль оси вала ко второй ступени, в которой происходит уплотнение и продавливание за счет изменения шага навивки и дальнейшее продвижение до встречи с лопастями, которые в свою очередь измельчают
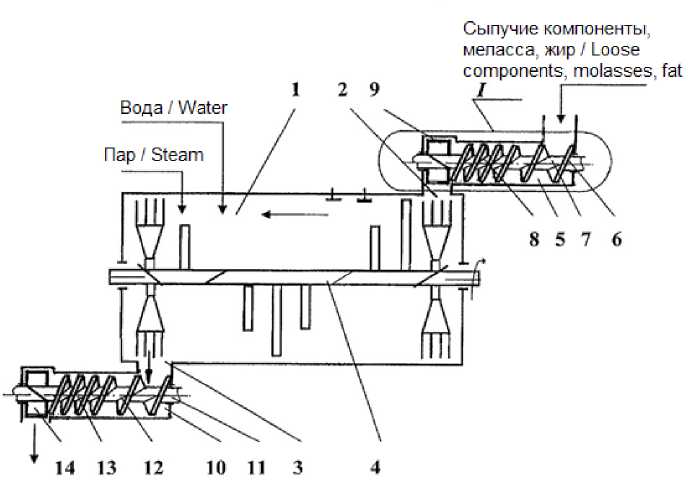
Р и с. 3. Реактор баротермической обработки концентрированных кормов:
1– корпус реактора; 2 – загрузочная горловина реактора; 3 – выгрузной люк; 4 – рабочий орган реактора; 5 – корпус теплового затвора загрузки; 6 – вал; 7 – двухступенчатый шнек;
8 – одноступенчатый шнек; 9 – лопасти; 10 – корпус теплового затвора выгрузки;
11 – вал теплового затвора; 12 – первая ступень двухступенчатого шнека;
13 – вторая ступень шнека; 14 – лопасти
F i g. 3. Reactor for barothermal processing of concentrated feed:
1 – reactor vessel; 2 – reactor loading neck; 3 – unloading hatch; 4 – reactor operating unit; 5 – heat load valve case; 6 – shaft; 7 – two-stage auger; 8 – one-stage auger; 9 – blades; 10 – body of the thermal discharge valve; 11 – shaft of the thermal shutter; 12 – first stage of the two-stage auger;
13 – second stage of the auger; 14 – blades
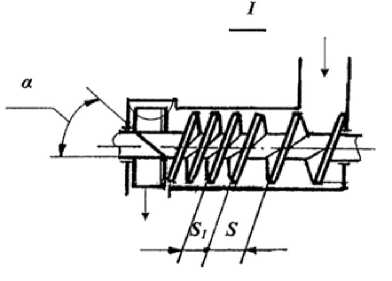
Р и с. 4. Тепловой затвор F i g. 4. Thermal shutter
уплотненную массу. Так как одним из основных условий работы реактора при баротермической обработке кормов является поддержание постоянного давления и температуры, то уплотненный во второй ступени шнека корм не дает возможности выхода, находящегося под давлением пара и соответственно потери теплоты, причем достигается это за счет прецезионного сопряжения между шнеком и корпусом. Измельчение уплотненной массы необходимо для равномерной дальнейшей баротермической обработки корма.
За счет наличия двух затворов одинаковой конструкции упрощается строение самого реактора и его обслуживание, так как он работает в непрерывном режиме.
Реактор баротермической обработки концентрированных кормов (рис. 3) работает следующим образом: концентрированный рассыпной корм (комбикорм или его компоненты) непрерывным потоком поступает в корпус 5 теплового затвора загрузки, непосредственно на первую ступень 7 двухступенчатого шнека, расположенного на валу 6 , которая перемещает его вдоль оси вала ко второй ступени 8 , при этом сыпучий корм уплотняется, частично разрушается, далее в спрессованном виде он передается к лопастям 9 , имеющим заточенные рабочие кромки, которыми измельчается и принудительно самими 436
лопастями передается в загрузочную горловину 2 корпуса 1 реактора, в котором под воздействием высокой температуры и давления происходит баротермическая обработка корма, при этом рабочий орган 4 реактора производит рыхление, смешивание и перемещение его вдоль корпуса 1 к выгрузному люку 3 , под которым расположен тепловой затвор выгрузки. Выгрузка из реактора происходит принудительно рабочим органом 4 реактора в корпус 10 теплового затвора выгрузки непосредственно на первую ступень 12 двухступенчатого шнека, расположенного на валу 11 теплового затвора, которая перемещает его вдоль оси вала ко второй ступени 13 , при этом на второй ступени сыпучий корм уплотняется и в спрессованном виде передается к лопастям 14, которыми измельчается и принудительно выталкивается наружу.
Использование данного реактора при баротермической обработке рассыпных концентрированных кормов позволяет исключить остановку реактора на загрузку и выгрузку, за счет надежной конструкции тепловых затворов загрузки и выгрузки (рис. 4), что дает возможность обеспечить непрерывную (поточную) работу реактора под рабочим давлением пара, ускорить время обработки, повысить производительность, сократить потери теплоты, а следовательно и энергии, при гаран-
Технологии и средства механизации сельского хозяйства
тированном выполнении процесса декстринизации крахмала и санитарной обработки концентрированных кормов.
Линия тепловой обработки комбикормов (рис. 5)17 включает приемный бункер для сои 1 (soy receiving bin 1) и приемный бункер для рапса 2 (rapeseed receiving bin 2) с установленными в их нижней части теплообменниками 3 (heat exchangers 3), бункер для наполнителей 4 (filler bin 4), для зерновых 5 (grain bin 5), для жира 6 (fat bin 6), для мелассы 7 (molasses hopper 7), для БМВД 8 (protein-vitamin mineral supplements bin 8), дозаторы непрерывного действия 9 (continuous dispensers 9) или краны 10 (cranes 10); под приемными бункерами для сои 1 (soy receiving bin 1), рапса 2 (rapeseed receiving bin 2) и наполнителей 4 (filler bin 4) размещен смеситель 11 (mixer 11), последовательно сообщенный с винтовой зерноплющилкой 12 (grain crusher 12), внутри цилиндрического корпуса которой 13 (cylindrical housing 13) расположены цилиндрический шнек 14 (cylindrical auger 14) с однозаходным винтовым элементом и радиальные кольца 15 (radial rings 15), установленные на внутренней стороне цилиндрического корпуса 13 (cylindrical housing 13) на расстоянии друг от друга равном шагу S-ленточной резьбы шнека с зазором к виткам шнека 0,5 мм и имеющие высоту 3–4 мм, и шнековым транспортером 16 (screw conveyor 16), соединенным с тепловым затвором загрузки 17 (thermal shutter boot 17) реактора баротермической обработки 18 (barothermal processing reactor 18), имеющего тепловой затвор выгрузки 19 (thermal shutter discharge 19), встроенный в газгольдер 20 (gazgolder 20), который нижней частью, посредством барабанного шлюза 21 (drum gateway 21) соединен с охладителем 22 (chiller 22), снабженным механизмом дозированной подачи атмосферного воздуха 23 (atmospheric dosing mechanism 23), перфоратором 24 (perforator 24) и механизмом регулирования количества отбора теплоносителя 25 (mechanism for regulating the amount of coolant selection 25), а верхней частью посредством паропровода 26 (steam lines 26), имеющего кран 27 (crane 27), сообщен с теплообменниками 3 (heat exchangers 3) приемных бункеров 1 и 2 (receiving hopper 1 and 2), при этом охладитель 22 (chiller 22) через тепловую магистраль 28 (heat line 28) сообщен с приемными бункерами 5–7 (receiving bins 5–7). Над приемным бункером для зерновых 5 (receiving bin for grain 5) установлен циклон 29 (cyclone 29) с вентилятором 30 (fan 30), над приемными бункерами для сои 1 и рапса 2 (receiving bins for soybean 1 and rapeseed 2) установлены предохранительные клапаны 31 (safety valve 31), а на входе пара в приемные бункера для зерновых 5 (receiving bin for grain 5), жира 6 (fat bin 6), мелассы 7 (molasses hopper 7) установлены паровые краны 32 (steam taps 32). Паропровод 26 (steam lines 26) и тепловая магистраль 28 (heat line 28) снабжены устройством для сбора и слива конденсата 33 (device for collecting and draining condensate 33).
Работа линии тепловой обработки комбикормов (рис. 5) осуществляется следующим образом. Исходное сырье (ингредиенты) засыпают в приемные бункеры: 1 – для сои, 2 – для рапса, 4 – для наполнителя, 5 – для зерновых, 6 – для жира, 7 – для мелассы, 8 – для БМВД. При работающем реакторе баротермической обработки 18 через тепловой затвор выгрузки 19 и газгольдер 20 по паропроводу 26 и при открытом кране 27 пар под давлением поступает в теплообменники 3 приемных бункеров для сои 1 и для рапса 2 , где происходит предварительное запаривание сои и рапса. Далее установленную дозу каждого из перечисленных компонентов подают в смеситель 11 дозаторами
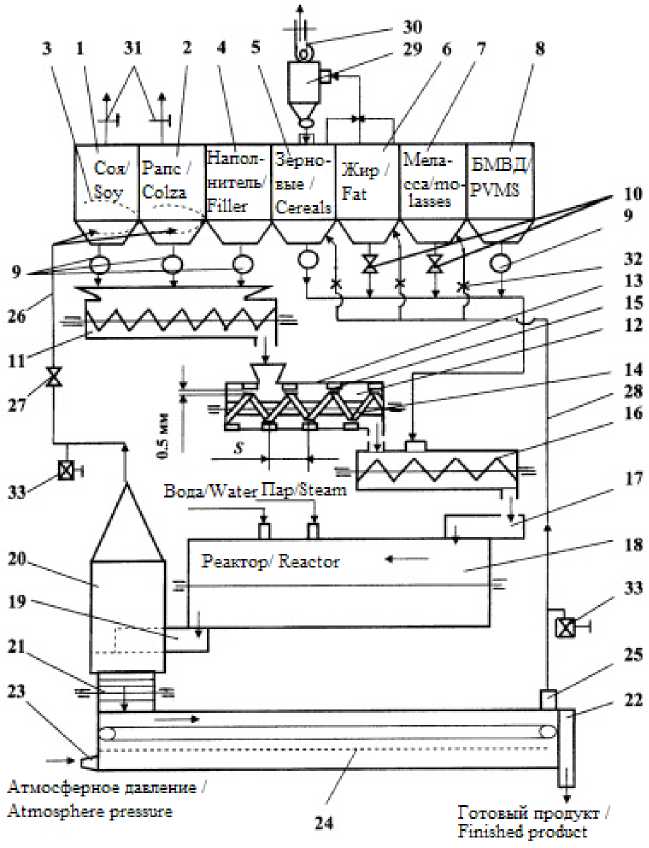
Р и с. 5. Линия тепловой обработки комбикормов F i g. 5. Heat treatment line of mixed feeds
непрерывного действия 9 из приемных бункеров 1, 2, 4 . Смесь равномерным потоком высыпается в винтовую зерноплющилку 12 , в которой за счет шнека 14 , расположенного в цилиндрическом корпусе 13 и имеющего однозаход-ный винтовой элемент, продавливается вдоль зерноплющилки и в процессе продавливания через зазор, равный
0,5 мм между кольцами 15, установленными на внутренней стороне цилиндрического корпуса 13 на расстоянии друг от друга, равном шагу S-ленточной резьбы шнека, и имеющих высоту 3–4 мм, и витками шнека 14, происходит плющение и измельчение частиц до размеров толщиной менее 0,5 мм, чем обеспечивается хороший доступ пара при дальнейшей обработке в баротермическом реакторе 18. Обработанная смесь сои, рапса и наполнителя поступает в шнековый транспортер 16, в который также посредством дозаторов непрерывного действия 9 и кранов 10 подаются ингредиенты из приемных бункеров 5–8, все составляющие смешиваются и перемещаются через тепловой затвор загрузки 17 в реактор баротермической обработки 18, где при заданных температуре, давлении и экспозиции происходит кондиционирование, гомогенизация кормов с одновременным перемещением обрабатываемой массы в сторону теплового затвора выгрузки 19, который также встроен в газгольдер 20, и далее обработанный комбикорм посредством барабанного шлюза 21 выгружается в охладитель 22, в который подается атмосферный воздух, регулируемый механизмом дозированной подачи 23 и, равномерно распределяясь по всей длине охладителя, снабженного перфоратором 24, охлаждается и выпускается в тару. При включенном вентиляторе 30 циклона 29 и посредством механизма регулирования количества отбора теплоносителя 25 по тепловой магистрали 28 тепло из охладителя подается к приемным бункерам 5–7 для подогрева зерновых, жира и мелассы и регулируется паровыми кранами 32. Небольшая часть ингредиентов (зерновых) засасывается пневмосистемой и, оседая в циклоне 29, ссыпается в приемный бункер 5 для дальнейшей переработки. Образовавшийся конденсат с устройства для сбора и слива 33 на паровой системе 26 и тепловой магистрали 28 удаляют при неработающей линии. Избыток давления (пара), поступающего в теплообменники приемных бункеров 1 и 2, стравливают через предохранительные клапаны 31. Линия тепловой обработки работает в непрерывном поточном режиме: содержит реактор с регулируемыми загрузочным и выгрузным затворами, узлы подготовки и подачи всех ингредиентов, пульт с интеллектуальной системой управления, исполняющий заданный технологический алгоритм работы, составленный на основе цифровой технолгии и конструктивных параметров, представленных в статье.
Обсуждение и заключение
Перевод процесса баротермической обработки ингредиентов комбикормов в зону 300–374 °С и давления 12–21 МПа p,t -диаграммы обеспечивает стерильность, интенсификацию и надежность процесса перевода вредных и плохо усвояемых составляющих элементов зерновых и бобовых в полезные, легко усвояемые корма [15].
Применение реактора баротермической обработки кормов с тепловыми затворами взамен автоклавам и запарникам обеспечивает непрерывную поточную работу линии, экономию времени обработки и тепловой энергии18.
Линия тепловой обработки комбикормов с реактором совмещает энергоемкие процессы нормализации, экспандирования, экструдирования и гранулирования, при этом повышается качество обработки, снижается удельная энергоемкость и металло-емкость19. Комбикорма очищаются от сальмонеллы, патогенных бактерий, грибков и плесени. Время обработки 60–120 секунд. Представленный режим баротермической обработки и конструктивные решения линии могут быть полезными при разработке проектов на базе цифровых технологий комбикормовых предприятий и цехов животноводческих и птицеводческих ферм.
Поступила 07.12.2019; принята к публикации 10.04.2019; опубликована онлайн 30.09.2019
Об авторах:
Все авторы прочитали и одобрили окончательный вариант рукописи.
Список литературы Баротермическая обработка ингредиентов комбикормов
- Измайлов А. Ю. Интеллектуальные технологии и роботизированные средства в сельскохозяйственном производстве // Вестник российской академии наук. 2019. Т. 89, № 5. С. 536-538. DOI: 10.31857/S0869-5873895536-538
- Голикова Т. А. Научное обеспечение реализации приоритетов научно-технологического развития Российской Федерации. Выступление заместителя председателя Правительства РФ // Вестник Российской академии наук. 2019, Т. 89, № 4. С. 311-314. DOI: 10.31857/S0869-5873894311-314
- Madau F. A., Furesi R., Pulina P. Technical Efficiency and Total Factor Productivity Changes in European Dairy Farm Sectors // Agricultural and Food Economics. 2017. Vol. 5, Issue 17. Pp. 1-14. DOI: 10.1186/s40100-017-0085-x
- Kostlivy V, Fuksova Z. Technical Efficiency and Its Determinants for Czech Livestock Farms // Agricultural Economics. 2019. Vol. 65, Issue 4. Pp. 175-184. -AGRICECON DOI: 10.17221/162/2018
- Subsidies and Technical Efficiency in Agriculture: Evidence from European Dairy Farms / L. La-truffe [et al.] // American Journal of Agricultural Economics. 2017. Vol. 99, Issue 3. Pp. 783-799. DOI: 10.1093/ajae/aaw077
- Kharmanda G. The Safest Point Method as an Efficient Tool for Reliability-Based Design Optimization Applied to Free Vibrated Composite Structures // Вестник Донского государственного технического университета. 2017. Т. 17, № 2 (89). С. 46-55.
- DOI: 10.23947/1992-5980-2017-17-2-46-55
- Ferket P. R. Technological Advances Could Make Extrusion an Economically Alternative to Pel-ling // Feedstuffs. 1991. Vol. 63, Issue 9. Pp. 19-21. URL: http://edepot.wur.nl/121964 (дата обращения: 15.05.2019).
- Krolczyk J. B. Homogeneity Assessment of Multi-Element Heterogeneous Granular Mixtures by Using Multivariate Analysis of Variance // Tehnicki Vjesnik. 2016. Vol. 23, Issue 2. Pp. 383-388.
- DOI: 10.17559/TV-20151031183255
- Best P. Extruder Opereting Costs. Comparisons with Double Pelleting in a Dutch Feedmill // Feed International. 1993. Vol. 14, no. 6. Pp. 32-34. URL: http://www.dissercat.com/content/tekhnologiya-proizvodstva-polu-i-polnozhirnykh-produktov-soi-i-rapsa-dlya-kombikormov-na-eks (дата обращения: 15.05.2019).
- Wasserstein R. L., Lazar N. A. The Asa's Statement on P-Values: Context, Process and Purpose // The American Statistician. 2016. Vol. 70, no. 2. Pp. 129-133.
- DOI: 10.1080/00031305.2016.1154108
- Krolczyk J. B. The Effect of Mixing Time on the Homogeneity of Multi-Component Granular Systems // Transactions of Famena. 2016. Vol. 40, Issue 1. Pp. 45-56. URL: https://hrcak.srce.hr/file/229037 (дата обращения: 15.05.2019).
- Strielkowski W., Lisin E. Economic Aspects of Innovations in Energy Storage // International Journal Of Energy Economics And Policy. 2017. Vol. 7, no. 1. Pp. 62-66. URL: https:// www.econjournals.com/index.php/ijeep/article/view/3528 (дата обращения: 15.05.2019).
- Khoshbin-e-Khoshnazar M. R. Ice Phase Transition as a Sample of Finite System Phase Transition // Physics Education. 2016. Vol. 32, Issue 2. URL: https://www.physedu.in/uploads/ publication/23/371/4.-Ice-Phase-transition-as-a-sample-of-finite-system-phase-transition.pdf (дата обращения: 15.05.2019).
- Ковальчук М. В., Нарайкин О. С., Яцишина Е. Б. Природоподобные технологии: новые возможности и новые вызовы // Вестник Российской академии наук. 2019. Т. 89, № 5. С. 455-465.
- DOI: 10.31857/S0869-5873895455-465
- Лухт Х., Долуд М., Зябрев В. Гидротермическая обработка соевых бобов // Комбикорма. 2019. № 1. С. 31-34. URL: http://kombi-korma.ru/arkhiv/no-01-19 (дата обращения: 15.05.2019).