Borogypsum: mineral composition, processing technology
Автор: Khatkova A.N., Nikitina L.G., Pateyuk S.A., Cherkasov V.G.
Журнал: Вестник геонаук @vestnik-geo
Рубрика: Научные статьи
Статья в выпуске: 3 (303), 2020 года.
Бесплатный доступ
We have chosen borogypsum for our study, which contains gypsum and silicon dioxide used in various industries. Present methods of borogypsum processing were considered. A new flotation reagent was proposed to separate the silicon concentrate from boric acid production waste. With the help of methods of mathematical planning, a multifactor experiment was carried out to reveal the optimal mode of flotation. We chose the following factors: temperature, pH, concentration of the main flotation reagent, agitation time, and also the time of flotation. The results of an experimental study of the raw material and obtained samples were presented with the help of modern physicochemical methods (spectrophotometry, IR spectroscopy, scanning electron microscopy, X-ray phase analysis), which allowed studying the chemical and mineral compositions and the structure of the samples. The new flotation concentration technology from boric acid wastes was developed.
Waste, secondary raw materials, borogypsum, silicon dioxide, gypsum, perlastane on-60, flotation, flotation reagent, multifactor experiment, перластан on-60
Короткий адрес: https://sciup.org/149129420
IDR: 149129420 | DOI: 10.19110/geov.2020.3.3
Текст научной статьи Borogypsum: mineral composition, processing technology
In many countries, most of the industrial wastes are not processed, but simply stored in certain areas [5, 8]. The weakness of the Russian industry is a high resource intensity [17]. The rates of wastes generation are significantly ahead of their processing and natural deactivation [2, 6, 15]. Therefore, the wastes dumping and processing should be approached very carefully to minimize contamination of the environment [2, 7, 9, 10]. It is necessary to introduce new effective methods of waste disposal, which will entail measurable economic and environmental consequences [3, 16].
The Russian Far East possesses high reserves of unique mineral raw materials, but present processing technologies do not allow using them efficiently. Over the years of operation of mining and chemical industries in the Far East, millions of tons of technogenic wastes have been accumulated, which are not being processed at present. Thus, the total amount of boric acid waste products — borogypsum — in the Far East region is more than 25 million tons. Raw recycling is an alternative method of production of gypsum and silica-containing products.
Borogypsum includes a well-floated component — gypsum [1, 4]. The processing plant of Dalnegorsky mining-pro-
cessing complex already has all the necessary equipment for flotation. Some flotation machines are not used and may be involved in other processes. Gypsum, released into a foam product, is used for production of gypsum binder, and the silicon concentrate, remaining in the chamber, is used for the production of «white soot». Thus, flotation seems to be the most suitable method of gypsum processing.
To subsequently convert silicon concentrate into «white soot», which meets the technical specifications GOST 18307-78 [11], it is necessary to provide silicon dioxide content from 50 to 65 %, with output 15 % and higher, using flotation. In this case, gypsum concentrate, as a dump product, must comply with the technical conditions GOST 4013-82 [12].
The aim of this work is to identify the material composition of borogypsum and to develop a new technology of enrichment of waste products of boric acid production, providing valuable commodity concentrates (gypsum and silicon).
Objects and research methods
A sample of wastes from the production of boric acid — borogypsum — from Dalnegorsky mining and processing complex was chosen as the object of study.
Table 1. Levels of the studied factors
Табёица 1. Уровни изучаемых факторов
Factor / Ôàêòîð |
Levels / Óðîâíè |
||||
1 |
2 |
3 |
4 |
5 |
|
Õ1 — Flotation temperature, °Ñ / Õ1 — Òåìïåðàòóðà ôëîòàöèè, °Ñ |
10 |
15 |
20 |
25 |
30 |
Õ2 —Flotation pH / Õ2 — pH ôëîòàöèè |
5.5 |
6.5 |
7.5 |
8.5 |
9.0 |
Õ3 — Perlastan consumption ON-60, g/t / Õ3 — Ðàñõîä ïåðëàñòàíà ON-60, ã/ò |
200 |
250 |
300 |
350 |
400 |
Õ4 — Agitation time, s / Õ4 — Âðåìÿ àãèòàöèè, ñ |
60 |
90 |
120 |
150 |
180 |
Õ5 — Flotation time, min / Õ5 — Âðåìÿ ôëîòàöèè, ìèí |
4.0 |
4.5 |
5.0 |
5.5 |
6.0 |
Table 2. Results of reverse flotation of amorphous silica under optimal conditions of a multifactor experiment Табёица 2. Результаты обратной флотации аморфного кремнезема в оптимальных условиях многофакторного эксперимента
Flotation Mode / Ðåæèì ôëîòàöèè |
Results / Ðåçóëüòàòû |
||
Parameter / Ïàðàìåòð |
Value Çíà÷åíèå |
Parameter / Ïàðàìåòð |
Value Çíà÷åíèå |
Temperature, ° Ñ / Òåìïåðàòóðà, °Ñ pH |
30 7.91 |
SiO2 yield in chamber product,% Âûõîä SiO2 â êàìåðíûé ïðîäóêò, % |
36.77 |
C bas. flotation, g/t / Ñ îñí. ôëîòàöèè, ã/ò C control flotation, g/t / Ñ êîíòð. ôëîòàöèè, ã/ò Agitation time, s / Âðåìÿ àãèòàöèè, ñ |
400 200 180 |
SiO2 content in chamber product,% Ñîäåðæàíèå SiO2 â êàìåðíîì ïðîäóêòå, % |
46.27 |
Time of main flotation, min / Âðåìÿ îñí. ôëîòàöèè, ìèí Time of control flotation, min / Âðåìÿ êîíòð. ôëîòàöèè, ìèí |
4.5 4.5 |
SiO2 extraction in chamber product,% Èçâëå÷åíèå SiO2 â êàìåðíûé ïðîäóêò, % |
65.15 |
Table 3. SEM results of the obtained products
Табёица 3. Результаты РЭМ полученных продуктов
Product / Продукт |
Si, % |
S, % |
Ca, % |
O, % |
Other elements, % / Другие элементы, % |
Original / Исходный |
12.72 |
9.63 |
13.53 |
61.23 |
2.89 |
Foamy No. 1 / Пенный № 1 |
9.13 |
13.55 |
19.26 |
56.25 |
1.81 |
Foamy No. 2 / Пенный № 2 |
4.61 |
13.18 |
22.04 |
58.49 |
1.68 |
Chamber / Камерный |
18.12 |
7.78 |
11.90 |
56.80 |
5.40 |
For flotation separation of silicon concentrate from borogypsum, we proposed perlastan ON 60 flotation reagent, which was proven during flotation of nonmetallic fluorite ores [13, 20].
Perlastan — a trade name for anion-active surface substances of N-acyl-sarcosine group [18]. Perlastan ON 60 is one of several modifications available. Its chemical composition — sodium oleylsarcosinate C17H33CON(CH3) CH2COONa. At room temperature it looks like a yellow viscous liquid.
Perlastans are chemically and by reactivity similar to fatty acid flotation reagents. Acid perlastans dissolve in most organic solvents, for example, alcohols, glycols, ethers. Perlastan ON-60 is soluble in water. Perlastans are not sensitive to electrolyte solutions and hard water, their good foaming and wetting properties are their important features. Perlastans are resistant to oxidation by such strong oxidizing agents as hypochlorite, hydrogen peroxide and benzoyl peroxide. Perlastan salts have interesting properties due to the hydrophobic tail of the molecule. In water perlastans are many times less toxic than other anionic surfactants. A mild physiological effect and non-toxicity result in the widespread application of per-lastans in such areas as cosmetics, perfumes and household chemicals.
The samples were studied by the photometric method using KFK-3-1 ZOMZ instrument for the content of silicon dioxide.
IR spectra were recorded by SHIMADZU FTIR-8400S infrared Fourier spectrometer in the region of 4000–400 cm–1 on KBr tablets.
The morphology and chemical composition of the samples were examined by scanning electron microscope (SEM) JSM-6510LV JEOL (Japan), with microanalysis system — energy disperse X-ray spectrometer INCA Energy 350, Oxford Instruments (United Kingdom) at 500X and 1000X. The samples were prepared by applying a powdered sample on a double-sided electrically conductive carbon with subsequent spraying a platinum film on the base.
The X-ray phase analysis was used to determine the mineral composition. The samples were grinded in agate pounder with alcohol and studied by powder diffraction method using X-ray diffractometer DRON-3.0, radiation — ÑuÊ α , Ni — filter, V=25 kV, I=20 mA, in the range 5-65°2 θ , scan step — 0.05°. Diffraction patterns were deciphered by the phase search software (DiffracPlus, PDF-2, 2007).
To determine optimal conditions of flotation, we used the method of rational planning of multifactor experiment [14] based on the non-linear multiple correlation and also the well-known formula by M. M. Protodyakonov proposed to process statistics. A new form of the equation with limitations by the theoretical maximum, shows its applicability for the description of kinetic dependences. Statistical criteria are used, which allow evaluating partial and master dependencies. The method recommended accelerated methods of algebraic description of partial dependencies.
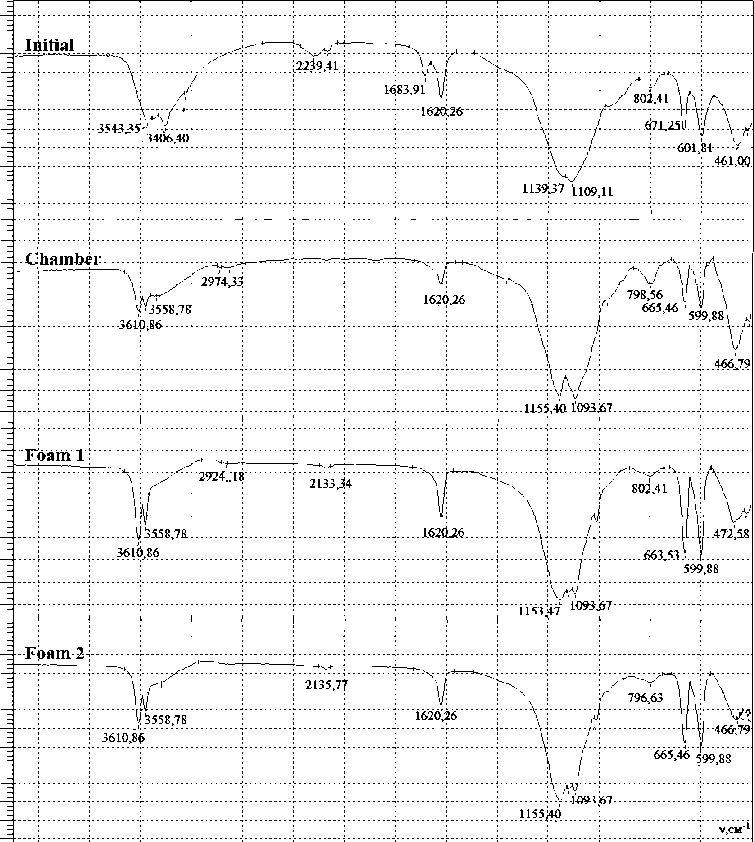
1400 ' 1000 ' 3600 3200 ' 2800 2400 ' 2000 ' 1800 1600 1100 ' 1200 LDOO 800 600 400
Fig. 1. IR spectra of studied samples
Ðèñ. 1. ÈÊ-ñïåêòðû èññëåäóåìûõ îáðàçöîâ
Results and discussion
During the multifactor experiment (Table 1) we determined an optimal flotation mode. Table 2 presents results of reverse flotation of amorphous silica in optimal conditions of the multifactor experiment.
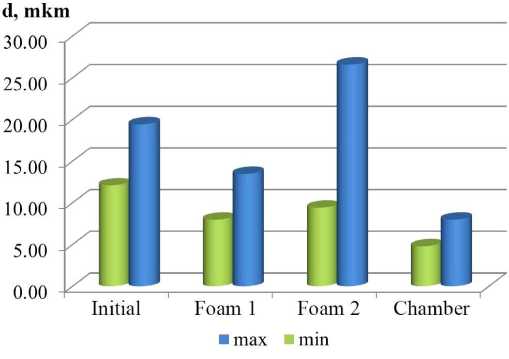
Fig. 2. Minimum and maximum diameter of the enzyme of particle aggregates in SEM micrographs
Ðèñ. 2. Ìèíèìàëüíûé è ìàêñèìàëüíûé äèàìåòð Ôåðåòà àãðåãàòîâ ÷àñòèö íà ìèêðîôîòîãðàôèÿõ ÐÝÌ
IR spectroscopy. In the IR spectra (Fig. 1), stretching vibrations of Si-O-Si groups (regions 1094 cm–1, 466 cm–1) refer to the content of silicon dioxide, and vibrations of SO4 groups (regions 1153 cm–1 , 665 cm–1 , 600 cm–1 ) — to the content of gypsum and anhydride in the samples. The change in the relative intensity of the absorption bands belonging to stretching vibrations of silicon dioxide and gypsum was measured with respect to the intensity of the absorption band belonging to stretching vibrations of Si-O-Si groups in the region 1094 cm–1 [19]. The relative intensity of the absorption bands of the stretching vibrations of SO4 groups increas-
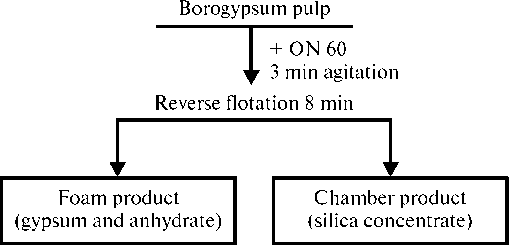
Fig. 3. Flotation scheme of borogypsum
Ðèñ. 3. Ñõåìà ôëîòàöèè áîðîãèïñà
Table 4. The chemical composition of the studied products Таблица 4. Химический состав исследуемых продуктов
Indicator / Показатель |
Designation Обозначение |
Content wt. % / Содержание, масс. доля, % |
|||
Product / Продукт |
|||||
Original Исходный |
Chamber Камерный |
Foamy No. 1 Пенный № 1 |
Foamy No. 2 Пенный № 2 |
||
Silicon (oxide) / Кремний (оксид) |
SiO 2 |
23.12 |
45.27 |
11.90 |
15.69 |
Calcium (oxide) / Кальций (оксид) |
CaO |
25.20 |
19.57 |
31.76 |
31.70 |
Sulfur (oxide) / Сера (оксид) |
SO3 общ. |
31.53 |
18.59 |
45.71 |
41.14 |
Boron (oxide) / Бор (оксид) |
B 2 O 3 |
1.06 |
1.46 |
0.67 |
0.88 |
Iron (oxide) / Железо (оксид) |
Fe 2 O 3 общ. |
3.08 |
5.21 |
1.83 |
3.49 |
Aluminum (oxide) / Алюминий (оксид) |
А^з |
0.65 |
1.07 |
0.31 |
0.56 |
Magnesium (oxide) / Магний (оксид) |
MgO |
0.28 |
0.60 |
0.14 |
0.17 |
Manganese (oxide) / Марганец (оксид) |
MnO |
0.25 |
0.49 |
0.12 |
0.18 |
Sodium (oxide) / Натрий (оксид) |
Na2O |
0.23 |
0.33 |
0.19 |
0.18 |
Potassium (oxide) / Калий (оксид) |
K 2 O |
0.090 |
0.15 |
0.040 |
0.060 |
Titanium (oxide) / Титан (оксид) |
TA |
0.040 |
0.080 |
0.020 |
0.030 |
Hygroscopic water / Вода гигроскопическая |
H 2 O + |
13.79 |
6.16 |
6.62 |
5.48 |
Table 5. Mineralogical composition of the samples
Таблица 5. Минеральный состав исследуемых образцов
Mineral / Минерал |
Theoretical formula Теоретическая формула |
Mass fraction,% / Массовая доля, % |
|||
Product / Продукт |
|||||
Original Исходный |
Chamber Камерный |
Foamy No. 1 Пенный № 1 |
Foamy No. 2 Пенный № 2 |
||
Gypsum / Гипс |
CaSO4 x 2H2O |
48 |
28 |
63 |
50 |
Anhydrite / Ангидрит |
CaSO4 |
16 |
8.5 |
17 |
24 |
Quartz / Кварц |
SiO2 |
2 |
4 |
1 |
1 |
Hedenbergite / Геденбергит |
CaFeSi2O6 |
1 |
6 |
||
Wollastonite / Волластонит |
CaSiO3 |
4 |
6 |
||
Garnet / Гранат |
Ca3Al2(SiO4)2(OH)4 |
3 |
4 |
1 |
3 |
Sum of the crystalline phases / Сумма кристаллических фаз |
74 |
56.5 |
82 |
78 |
|
Amorphous silica dioxide / Аморфный диоксид кремния |
22.12 |
41.27 |
10.90 |
14.69 |
|
Undecomposed minerals / Аморфный диоксид кремния |
3.88 |
2.23 |
7.1 |
7.31 |
Table 6. Comparative characteristics
Таблица 6. Сравнительная характеристика
Characteristic Показатель |
Scheme proposed by Dalnegorsky Processing plant Схема ООО «Дальнегорский ГОК» |
Our scheme Разработанная нами схема |
Flotation reagent Флотационный реагент |
Liquid soap Жидкое мыло |
Perlastan Перластан ON-60 |
Reagent consumption g/t of borogypsum sludge Расход реагента, г/т шламов борогипса |
1500 |
1000 |
Medium regulator Регулятор среды |
Soda Сода |
Not required Не требуется |
Consumption of a medium regulator, kg/t of borogypsum sludge Расход регулятора среды, кг/т шламов борогипса |
7-10 |
- |
Temperature, °С Температура, °С |
40 |
30 |
pH |
8.5-9.0 |
7.5 |
Time of main flotation, min Время основной флотации, мин |
9 |
8 |
Control flotation time Время контрольной флотации |
5 |
нет |
Extraction of SiO 2 , % Извлечение SiO 2 , % |
33.57 |
64.02 |
Output of SiO2, % Выход SiO2, % |
15.11 |
32.50 |
SiO2 yield,% Содержание SiO 2 , % |
60.24 |
53.56 |
Table 7. Technical and economic indicators
Таблица 7. Технико-экономические показатели
Scanning electron microscopy. The samples have a complicated microsurface relief; fine material is formed by crystals and aggregates. Minimum and maximum Feret diameter is presented in Fig. 2. The chemical composition of the samples is given in Table 3. The greater part of Ca and S after flotation passed into foam products, taking a minor amount of Si. This allows significantly increasing Si content in the chamber product.
Based on SEM images, it can be noted that the chamber product has a more finely dispersed structure (Fig. 2). The flotation results in aggregation of particles as evidenced by increasing maximum Feret diameter of the particles in foam product No. 2, in comparison with the original sample.
Comparative studies of chemical and mineral composition of initial product and the samples obtained are shown in Table 4 and Table 5 respectively. We determined that the 26
content of silicon dioxide after flotation significantly increases in the chamber product and decreases in the foam product, and the content of sulfur and calcium increases on the contrary.
Experiments showed that the fractional reagent feed is not effective, it is necessary to increase Perlastan flow only in primary flotation. We determined the most efficient flotation mode of borogypsum with collecting reagent ON-60.
Analyzing the obtained data, the authors proposed the most effective mode of flotation of borogypsum with collecting reagent perlastan ON-60 according to the scheme in Fig. 3, with the following flotation parameters: temperature — 30° C; pH 7.5; perlastan ON-60 consumption — 1000 g/t; agitation time — 180 s; main flotation time, min — 8. This technological scheme allows obtaining a high-quality product with a silicon dioxide content 53.56 %, at a high silicon dioxide recovery 64.02 %. Comparing the scheme offered at Dalnegorsky processing plant, with the scheme developed by the authors, the latter has a number of advantages (Table 6).
Table 7 presents the feasibility study [20] of the work performed. The proposed scheme of boric acid production recycling increases net profit of enterprises to 55.36 mln rub. This is resulted from addition of two commodity concentrates — silicon and gypsum. Despite increasing costs of fixed and current assets, the income from the production of additional concentrates exceeds these costs. The proposed scheme for the processing of wastes using Perlastan ON-60 collecting reagent is more efficient than the liquid soap scheme, since the latter entails additional costs for equipment, personnel and consumables. The environmental effect of the introduction of this technology into production is also important. Because of the wastes processing, not only the cost of waste storage is reduced by 1.77 million rubles, but also the environmental situation in the region is significantly improved, both due to a significant reduction in the intensity of waste accumulation and the release of land from stored wastes.
Conclusions
The work has solved an urgent scientific and technical problem of increasing technical and economic indicators of flotation of waste products of boric acid production based on the development of new reagent modes using perlastan ON-60 collecting reagent, which is selective for minerals of borogypsum.
On the basis of the studies we made the following conclusions:
-
1. Technological features of the datolithic ores waste processing parameters are determined by the content of main minerals (gypsum, anhydrite, amorphous silica), which predetermine use of flotation methods for the enrichment of industrial raw.
-
2. It was confirmed that perlastan ON-60 collecting reagent is an effective reagent for separation of borogypsum minerals. Extraction of silicon dioxide, when it is applied, increases by 30.45 % compared with the known mode.
-
3. We developed a new technology for redistribution of waste products of boric acid production, which allowed producing two types of commercial concentrates (gypsum and silicon), as well as reducing rate of waste formation, which could result in a significant improvement of the ecological situation in the areas of waste burial.
Список литературы Borogypsum: mineral composition, processing technology
- Bulut G., Atak S., Tuncer E. Celestite-gypsum separation by flotation. The Canadian Journal of Metallurgy and Materials Science, 2008, issue 2, vol. 47, pp. 119-126.
- European commission, available at: http://ec.europa.eu/environment/waste/mining/index.htm, 2019.
- Kudelko J. Effectiveness of mineral waste management. International Journal of Mining, Reclamation and Environment, 2018, No. 1-9, pp. 440-448 DOI: 1080/17480930.2018.1438036.
- Matsuno T., Kadota M., Ishiguro Y. Separation of Gypsum by the Flotation Process. Bulletin of the Society of Salt Science, 1958, vol. 12, issue 2, pp. 73-78.
- Negm A. M., N. Shareef N. Waste Management in MENA Regions - Switzerland: Springer, 2019, pp. 1-11.