Цифровой анализ прочностных характеристик радиальных рабочих колес энергетических турбомашин для АПК с учетом упругости вала
Автор: Репецкий Олег Владимирович, Хоанг Динь Кыонг
Журнал: Агротехника и энергообеспечение @agrotech-orel
Рубрика: Физическое, математическое, компьютерное и электромоделирование
Статья в выпуске: 4 (33), 2021 года.
Бесплатный доступ
Радиальные рабочие колеса турбомашин - это сложные вращающиеся детали. Вычислительные модели вала с радиальным рабочим колесом и 10-ю лопатками были построены с использованием параметрических моделей уменьшенного порядка. Цифровые модели учитывают влияние различных вариантов для жестких закреплений по кольцу вала и скорость вращения для исследования изменения собственных частот и напряжений турбомашин. В дальнейшем можно с уверенностью предположить, что исследование изменения собственных частот и напряжения турбомашин от скорости вращения и различных вариантов закрепления по кольцу вала являются актуальными на стадиях проектирования и доводки. Эти расчеты позволяются существенно сократить объем дорогостоящих экспериментальных исследований, уменьшить сроки конструирования и значительно снизить требуемые компьютерные ресурсы при проектировании новых конструкций турбомашин для АПК.
Радиальная лопатка, метод конечных элементов, рабочее колесо, собственная частота, статическое напряжение, турбомашина, форма колебаний
Короткий адрес: https://sciup.org/147235500
IDR: 147235500
Текст научной статьи Цифровой анализ прочностных характеристик радиальных рабочих колес энергетических турбомашин для АПК с учетом упругости вала
Введение. Для модели вала с радиальным рабочим колесом и 10-ю лопатками (Рис. 1) возникает большой динамический отклик. Собственные частоты резко увеличиваются в эксплуатационном диапазоне вращения. Также отмечается, что в конструкции возникает большая деформация вала. В этой связи, в конструкции модели нужно рассматривать различные варианты для жестких закреплений по кольцу вала. По этому критерию, конструкция модели вала с радиальным рабочим колесом с 10-ю лопатками имела два варианта закрепления по диаметру вала в соответствующих узловых точках конечных элементов [1]. Первый вариант предусматривал что, в кольце 1 применялось жесткое закрепление, а в кольце 2 сохранена свобода перемещений в осевом направлении и оставлено закрепление в остальных осях. А второй вариант – в кольце 1 и 2 применялось жесткое закрепление [2]. Полученные результаты позволяют значительно снизить требуемые компьютерные ресурсы при проектировании новых турбомашин в АПК.
Материалы и методы исследования
Расчеты на прочность и компьютерное моделирование модели радиального рабочего колеса с валом и 10-ю лопатками энергетических турбомашин показана на Pис. 1. Основные механические характеристики имеют вид: материал рабочего колеса – сталь, модуль Юнга – 2,1.105 Мпа, плотность – 7850 кг/м3, коэффициент Пуассона – 0.3. Общий вид модели вала с радиальным рабочим колесом представлен на рисунке 1а. В качестве конечноэлементной модели применяется конечный элемент ТЕТ10 комплексной программы ANSYS
WORKBENCH с общим количеством конечных элементов – 72712 и
138379 узловыми
точками. Количество степеней свободы составляет - 415137 (Рис. 1б).
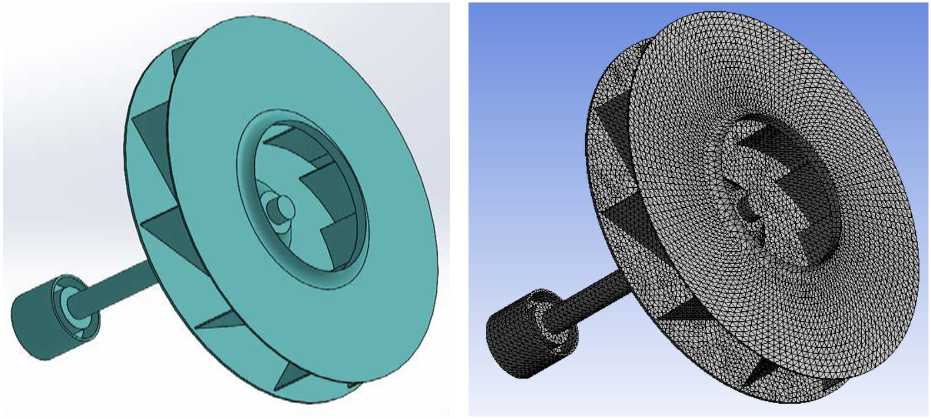
б
а
Рисунок 1 - Модель вала с радиальным рабочим колесом с 10-ю лопатками (а- общий вид; б - конечноэлементная модель)
Расчеты на прочность и компьютерное моделирование технических процессов являются актуальными на стадиях проектирования, доводки и эксплуатации. Метод конечных элементов (МКЭ) является актуальным методом, который обычно используется в технических областях в различных вычислительных программных комплексах, например коммерческих системах, таких как ANSYS WORKBENCH, SOLIDWORKS или инициативных пакетам программ, например BLADIS+ [2,3,4] для решения задач статики, колебаний и расчета ресурса различных технических систем. МКЭ имеет общий алгоритм, который позволяется быстро выполнить расчеты различных вариантов сложных конструкций [3,4,5].
Уравнения движения с использованием МКЭ для анализа прочностных характеристик имеют вид [6,7,8]:
( [ K e ] + [ K g ] + [ K r ] ) - ! » } = { F o) + { F t } + { F g } • (1)
и для проблемы свободной вибрации:
[ M №M C 1 5 M K E ] + [ K G H K R № = 0 • (2)
где { 5 } - вектор смещения, [ KE ] и [ M ] - матрицы упругой жесткости и массы, соответственно, [ K G ] - матрица геометрической жесткости, зависящая от скорости вращения и температуры, [ K R ] - дополнительная матрица жесткости (псевдомасс), возникающая в результате вращения, { F } • { F T } • { F G } - векторы, соответствующие силам создается вращением, температурой и давлением газа соответственно. [ C ] - матрица Кориолиса.
Результаты и обсуждение
Первый вариант представлен на Рис. 2. Конструкция модели вала с радиальным рабочим колесом с 10-ю лопатками была закреплена по диаметру вала в соответствующих узловых точках конечных элементов. В кольце 1 применялось жесткое закрепление, а в кольце 2 сохранена свобода перемещений в осевом направлении и оставлено закрепление в остальных осях.
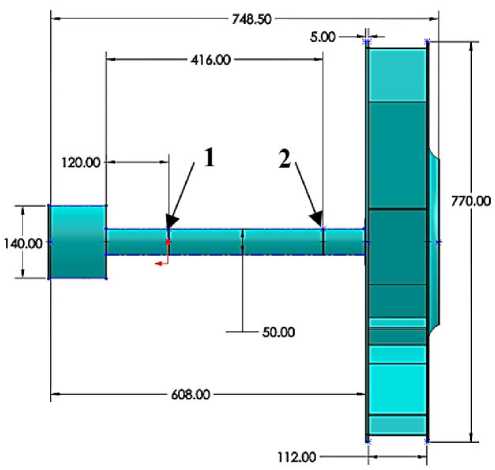
Рисунок 2 - Вид закрепления валы по ограниченным условиям
На Рис. 3 представлены шесть основных форм колебаний для модели вала с радиальным рабочим колесом. Каждая форма колебаний обладает характерной деформацией, по критерию количества узловых диаметров и числа узловых окружностей (n / m), определяющих форму 3 и 4 – 0/0, форму 1 – 1/0, форму 5 – 0/1,форму 18 – 1/1, форму 10 – 2/0.
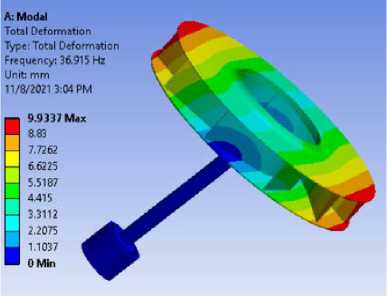
Форма 1
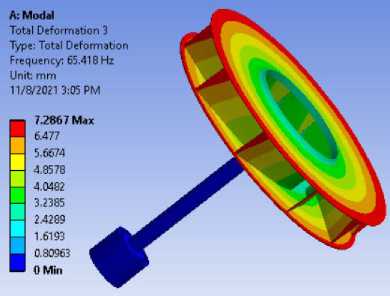
Форма 3
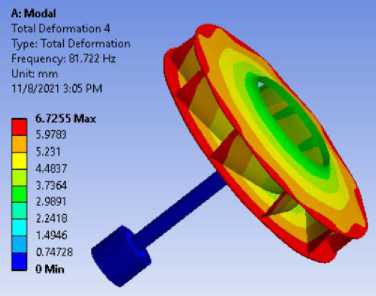
Форма 4
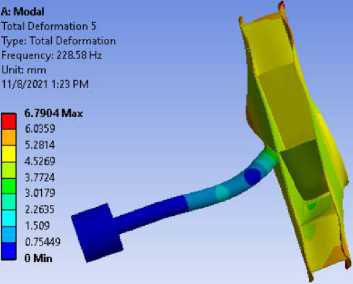
Форма 5
Таблица 1. Значения собственных частот колебаний для модели с учетом вала в комплексной программе ANSYS WORKBENCH.
Форма n / m |
Эксперимент, Гц |
Собственные частоты с учетом вала, Гц |
Отклонение Δf, % |
Максимальные значения деформаций, мм |
0/0 |
- |
65,418 |
- |
7,2867 |
- |
81,722 |
- |
6,7255 |
|
1/0 |
44 |
36,915 |
16,1 |
9,9337 |
0/1 |
- |
228,58 |
- |
6,7904 |
1/1 |
- |
438,7 |
- |
15,756 |
2/0 |
341 |
341,6 |
0,17 |
19,06 |
5/0 |
402,36 |
- |
33,694 |
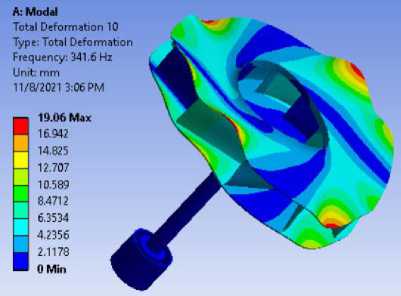
Форма 10
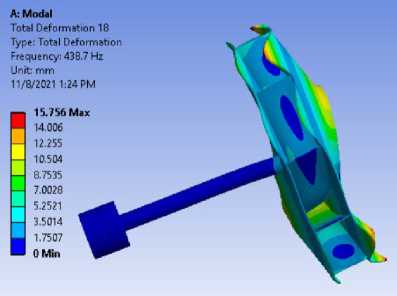
Форма 18
Рисунок 3 - Форма колебаний и собственные частоты модели с учетом вала с радиальным рабочим колесом 10-и лопаток энергетических турбомашин в программе ANSYS WORKBENCH.
Анализ таблицы 1 показал что, значения собственных частот колебаний от эксперимента для формы 1 отклоняется на величину около 16,1%, а для формы 10 на 0,17%.
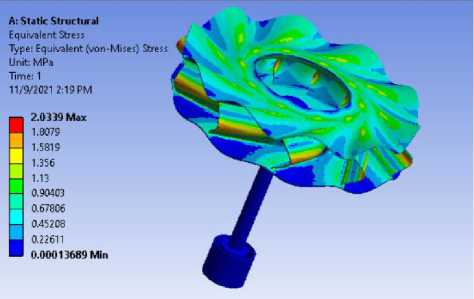
n = 5 (1/s)
Рисунок 4 - Расчеты статического напряжения с учетом вращения вала модели в комплексной программе ANSYS WORKBENCH.
Для анализа прочности и надежности радиальных рабочих колес от напряжений и
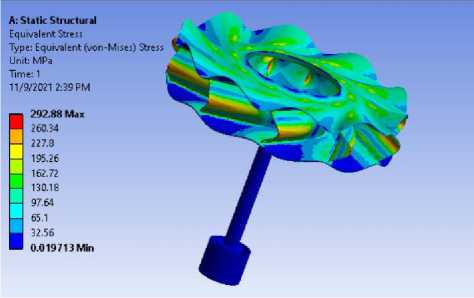
n = 60 (1/s)
собственных частот колебаний для этой модели с валом в проектировании компрессорного колеса, выполнены численные исследования статического напряженно-деформированного состояния (НДС) при оборотах 5 (1/s), 10 (1/s), 15 (1/s), 20 (1/s), 30 (1/s), 40 (1/s), 50 (1/s), 60 (1/s).
На Рис. 4 и в таблице 2 показываны расчеты статического напряжения σ э для этой модели с учетом вращения.
Таблица 2. Значение статического напряжения σ э для этой модели с учетом вращения, МПа
Скорость вращения колеса, 1/s |
Эксперимент, Мпа |
BLADIS+ (с валом), Мпа |
Максимальные статические напряжения модели, Мпа |
5 |
- |
- |
2,0339 |
10 |
- |
- |
8,1356 |
15 |
- |
- |
18,305 |
20 |
32 |
29,94 |
32,542 |
30 |
- |
- |
73,220 |
40 |
- |
- |
130,17 |
50 |
- |
- |
203,39 |
60 |
- |
- |
292,88 |
Расчеты значения собственных частот колебаний для этой модели с учетом вращения представлены в таблице 3.
Таблица 3. Расчеты значения собственных частот колебаний для этой модели с учетом вращения, Гц
Форма |
Собственные частоты колебаний, Гц |
||||||||
0 (1/s) |
5 (1/s) |
10 (1/s) |
15 (1/s) |
20 (1/s) |
30 (1/s) |
40 (1/s) |
50 (1/s) |
60 (1/s) |
|
1 |
36,915 |
37,162 |
37,887 |
39,061 |
40,641 |
44,809 |
49,969 |
55,76 |
61,901 |
2 |
36,924 |
37,168 |
37,893 |
39,068 |
40,648 |
44,815 |
49,975 |
55,766 |
61,906 |
3 |
65,418 |
65,432 |
65,444 |
65,462 |
65,487 |
65,551 |
65,625 |
65,702 |
65,777 |
4 |
81,722 |
81,789 |
81,99 |
82,324 |
82,79 |
84,112 |
85,935 |
88,229 |
90,959 |
5 |
228,58 |
228,58 |
228,6 |
228,62 |
228,66 |
228,77 |
228,92 |
229,1 |
229,33 |
6 |
228,62 |
228,61 |
228,63 |
228,66 |
228,7 |
228,81 |
228,96 |
229,14 |
229,37 |
7 |
289,09 |
288,7 |
288,59 |
288,4 |
288,13 |
287,37 |
286,29 |
284,91 |
283,21 |
8 |
289,38 |
288,97 |
288,85 |
288,66 |
288,4 |
287,63 |
286,56 |
285,18 |
283,48 |
9 |
339,82 |
339,98 |
340,45 |
341,23 |
342,31 |
345,38 |
349,62 |
354,98 |
361,38 |
10 |
341,6 |
341,79 |
342,39 |
343,39 |
344,79 |
348,71 |
354,06 |
360,74 |
368,63 |
11 |
341,64 |
341,84 |
342,44 |
343,44 |
344,84 |
348,76 |
354,12 |
360,8 |
368,69 |
12 |
402,36 |
402,77 |
404,11 |
406,34 |
409,43 |
418,13 |
429,99 |
444,73 |
461,04 |
Расчеты собственных частот колебаний для модели вала с радиальным рабочим колесом с 10-ю лопатками подобраны в таблице 4 по критерию числа узловых диаметров и узловых окружностей (n / m).
Таблица 4. Значения собственных частот колебаний для модели вала в комплексной программе ANSYS WORKBENCH по критерию числового узлового диаметра на числовой узловой окружности.
Форма n / m |
Значения собственных частот колебаний в ANSYS WORKBENCH, Гц |
||||||||
0 (1/s) |
5 (1/s) |
10 (1/s) |
15 (1/s) |
20 (1/s) |
30 (1/s) |
40 (1/s) |
50 (1/s) |
60 (1/s) |
|
0/0 |
81,72 |
81,78 |
81,99 |
82,32 |
82,79 |
84,11 |
85,93 |
88,22 |
90,95 |
1/0 |
36,91 |
37,16 |
37,88 |
39,06 |
40,64 |
44,80 |
49,96 |
55,76 |
61,90 |
0/1 |
228,5 |
228,5 |
228,6 |
228,6 |
228,6 |
228,7 |
228,9 |
229,1 |
229,3 |
2/0 |
341,6 |
341,7 |
342,3 |
343,3 |
344,7 |
348,7 |
354,0 |
360,7 |
368,6 |
5/0 |
402,3 |
402,7 |
404,1 |
406,3 |
409,4 |
418,1 |
429,9 |
444,7 |
461,0 |
Диаграмма Кэмпбелла показана на рисунке 5, где горизонтальная ось представляет скорость вращения ротора и вертикальная ось обозначает собственную частоту колебаний. Кривые динамические частоты указывают взаимосвязь между собственными частотами и скоростями вращения для каждой формы колебания [9]. В диаграмме анализируется 5-ть значений форм колебаний 1, 4, 5, 10, 12.
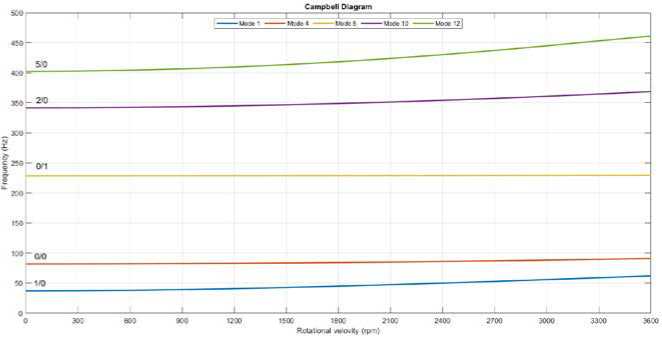
Рисунок 5 - Диаграмма Кэмпбелла для модели вала с радиальным рабочим колесом c 10-ю лопатками.
Второй вариант представлен на Рис. 2. Конструкция модели вала с радиальным рабочим колесом с 10-ю лопатками была закреплена по диаметру вала в соответствующих узловых точках конечных элементов. В зонах на кольцах 1 и 2 применялось жесткое закрепление.
На Рис. 7 представлены 6-ть основных форм колебаний для модели вала с радиальным рабочим колесом. Каждая форма обладает разнообразной характерной деформацией, по критерию количества узловых диаметров и числа узловых окружностей (n/m), определяющийся форму 4 – 0/0, форму 1 – 1/0, форму 7 – 0/1, форму 18 – 1/1, форму 10 – 2/0 и форму 12 – 5/0.
Таблица 5. Значения собственных частот колебаний для модели с учетом вала в комплексной программе ANSYS WORKBENCH.
Форма n / m |
Эксперимент, Гц |
Собственные частоты c учетом вала, Гц |
Отклонение Δf, % |
Максимальные значения деформацией, мм |
0/0 |
- |
81,991 |
- |
6,7344 |
1/0 |
44 |
39,581 |
10,04 |
9,9429 |
0/1 |
- |
319,62 |
- |
8,3027 |
1/1 |
- |
479,3 |
- |
24,791 |
2/0 |
341 |
341,61 |
0,18 |
19,963 |
5/0 |
- |
402,36 |
- |
33,702 |
Таблица 6. Расчеты значения собственных частот колебаний для этой модели с учетом вращения, Гц
Форма |
Собственные частоты колебаний, Гц |
||||||||
0 (1/s) |
5 (1/s) |
10 (1/s) |
15 (1/s) |
20 (1/s) |
30 (1/s) |
40 (1/s) |
50 (1/s) |
60 (1/s) |
|
1 |
39,581 |
39,838 |
40,574 |
41,769 |
43,384 |
47,678 |
53,068 |
59,217 |
65,779 |
2 |
39,596 |
39,845 |
40,58 |
41,775 |
43,39 |
47,684 |
53,073 |
59,223 |
65,871 |
3 |
65,424 |
65,438 |
65,449 |
65,467 |
65,492 |
65,555 |
65,628 |
65,705 |
65,877 |
4 |
81,991 |
82,06 |
82,263 |
82,601 |
83,073 |
84,41 |
86,254 |
88,577 |
91,342 |
5 |
289,03 |
288,64 |
288,52 |
288,33 |
288,06 |
287,3 |
286,22 |
284,83 |
283,12 |
6 |
289,32 |
288,91 |
288,79 |
288,6 |
288,34 |
287,57 |
286,49 |
285,11 |
283,4 |
7 |
319,62 |
319,98 |
320,13 |
320,39 |
320,74 |
321,73 |
323,04 |
324,64 |
326,44 |
8 |
320,06 |
320,09 |
320,24 |
320,5 |
320,85 |
321,84 |
323,17 |
324,77 |
326,58 |
9 |
341,0 |
341,16 |
341,64 |
342,42 |
343,52 |
346,63 |
350,91 |
356,32 |
362,79 |
10 |
341,61 |
341,8 |
342,4 |
343,4 |
344,79 |
348,71 |
354,06 |
360,74 |
368,63 |
11 |
341,64 |
341,84 |
342,44 |
343,45 |
344,84 |
348,76 |
354,12 |
360,8 |
368,69 |
12 |
402,36 |
402,77 |
404,11 |
406,34 |
409,43 |
418,13 |
429,99 |
444,73 |
462,05 |
Таблица 7. Общие значения собственных частот колебаний для каждого варианта модели в комплексной программе ANSYS WORKBENCH и BLADIS+ [1].
n / m |
Эксперимент, Гц |
BLADIS+ |
Собственные частоты модели без учета вала, Гц |
Собственные частоты модели с учетом вала (1й вариант), Гц |
Собственные частоты модели с учетом вала (2-й вариант), Гц |
0/0 |
– |
– |
80,263 |
65,418 |
– |
– |
– |
122,92 |
81,722 |
81,991 |
|
1/0 |
41 |
– |
41,513 |
36,915 |
39,581 |
– |
– |
47,963 |
– |
– |
|
0/1 |
– |
– |
356,11 |
228,58 |
319,62 |
1/1 |
– |
– |
365,33 |
– |
– |
– |
– |
425,99 |
438,7 |
479,3 |
|
2/0 |
341 |
349,0 |
341,62 |
341,6 |
341,61 |
5/0 |
– |
402,1 |
402,3 |
402,36 |
402,36 |
Вывод
Таким образом, в данной работе представлены основные формы колебаний и значения статических напряжений для модели вала радиального рабочего колеса c 10-ю лопатками энергетических турбомашин для перекачки воздуха в АПК. Также проводились экспериментальные исследования и сравнивались расчеты с данными эксперимента. Отмечается, что для двух вариантах модели с учетом вала собственные частоты уменьшаются по сравнению к моделью без учета вала для соотношения (n/m) и 0/0, 1/0, 0/1, 1/1. По каждому варианту наблюдаются уменьшение степени деформации вала в конструции и отсутствие значительного отклика собственных частот при вращении модели в диапазоне (45...50) 1/с. В этой связи можно предположить, что учет вала при численном анализе подобных конструкций не дает существенного эффекта и им можно пренебречь. Представленные кривые динамических частот показывают взаимосвязь между собственными частотами и скоростями вращения для каждой формы колебания в диаграмме Кэмпбелла и могут быть использованы в отстройке от резонансных режимов реальных конструкций радиальных рабочих колес в АПК.
Список литературы Цифровой анализ прочностных характеристик радиальных рабочих колес энергетических турбомашин для АПК с учетом упругости вала
- Irretier H., Repetskiy O. Analyse der Eigenschwingungen rotierender axialer und radialer Laufräder und Schaufelpakete von Turbomaschinen mittels Hyperelemente, Kondensation und der Methode zyklischer Symmetrie. Kassel: GH Kassel Universität, Institut für Mechanik, 121 S.
- Yan Y. J., Cui P. L. and Hao H. N. Vibration mechanism of a mistuned bladed disk // Journal of Sound and Vibration. 2008. Vol. 317.P. 294-307.
- Yang M. T. and Griffin J. H. A reduced-order model of mistuning using a subset of nominal system modes // J Eng Gas Turb Power. 2001. Vol. 123. P. 893-900.
- Repetckii O., Ryzhikov I. and Nguyen T. Q. Dynamics analysis in the design of turbomachinery using sensitivity coefficients // Journal of Physics: Conference Series. 2018. 012096.
- Repetckii O., Ryzhikov I. and Springer H. Numerical analysis of rotating flexible blade-disk-shaft systems // Proceedings of the ASME Turbo Expo. 1999.
- Whitehead D.S. Effect of mistuning on the vibration of turbomachine blades induced by wakes // Journal of mechanical engineering science. 1966. №. 1. Р. 15-21.
- Castanier M. P., Pierre C. Modeling and Analysis of Mistuned Bladed Disk Vibrations: Status and Engineering Directions // Journal of Propulsion and Powers. 2006. №. 2 (122). Р. 384-396.
- Ewins D. J. Vibration characteristics of Bladed disc assemblies // Journal of Mechanical Engineering Science. 1973. №. 5 (12). Р. 165-186.
- Campbell W. The protection of Steam Turbine Disk Wheels from Axial Vibrations // Trans. of the ASME 46. 1924. Р. 31-160.