Complex approach to the evaluation of the reactivity of solid organic fuels
Автор: Boiko Evgeny A., Pachkovsky Sergey V.
Журнал: Журнал Сибирского федерального университета. Серия: Техника и технологии @technologies-sfu
Статья в выпуске: 5 т.4, 2011 года.
Бесплатный доступ
A universal experiment-calculation approach for the evaluation of the kinetic characteristics of thermochemical transformation of solid organic fuels based on the application of the methods of complex thermal analysis and mathematical simulation has been proposed. The technique of the thermogravimetric experiment data processing and mathematical model description bases itself on a unifi ed calculation scheme of material balances and kinetic processes of natural coal burnout. Satisfactory qualitative and quantitative convergence of experimental and numerical results has been obtained.
Coal, kinetic processes of burning-out, complex thermal analysis, mathematical simulation
Короткий адрес: https://sciup.org/146114604
IDR: 146114604
Текст научной статьи Complex approach to the evaluation of the reactivity of solid organic fuels
The experience of using solid organic fuels in thermal power stations shows that till now there are no ways of their preparation and burning that would provide maximum efficiency, reliability and ecological safety of boiler unit operation [1, 2]. This problem is aggravated even greater when non-rated or inferior quality coals are burnt [3]. The most practical way of solving this problem can be provided by implementation of new technical processes, in particular, development of monitoring, engineering diagnostics and control systems of furnace processes as well as improvement of the methods, practices and devices of fuel utilization [4, 5].
To determine practical recommendations for the selection of optimum technical solutions of power utilization of solid organic fuels basing on the abovementioned principles it is urgent to establish a correct correlation of the initial quality characteristics of coal substance with the reaction characteristics of its thermochemical transformation basing on the kinetic parameters. The empirical relationships now in use in the majority of studies [6-8] are far from taking into account all basic stages, processes and factors of burning and, that is the most essential, are not always connected in an apparent form to the reaction parameters describing these processes which consequently raises doubts about reliability of these techniques and quality of suggested engineering solutions.
The purpose of the present study is to develop a complex method of evaluating the kinetic characteristics of the basic stages and phases of thermochemical transformation of a wide range of solid organic fuels as applied to the conditions of real furnace processes to provide qualitative and quantitative convergence of numerical and experimental data.
When studying the complex physicochemical process of solid organic fuel burnout in the furnaces of the steam boilers being a part of a more general gas-dynamic problem associated with description of heat-mass exchange and aerodynamics processes, there is arising a problem to construct an adequate kinetic mechanism and kinetic model describing behavior of chemically reacting system [9, 10]. The solution of this problem requires the following questions to be answered: what stages of the analyzed kinetic mechanism pre-determine kinetics of the system as a whole; what stages are redundant for the discussed kinetic scheme and may it be simplified; which of the kinetic mechanism alternatives is the most probable one [11, 12].
Assuming the reactivity to be adequate to the total time of the burnout of power-plant fuel [13], it can be stated that during pulverized burning this characteristic is determined by a set of parameters of the overlapping processes, in particular: rate of moisture evaporation, rate of emission and burning of volatile matters, rate of nonvolatile (coke) residue burning. At the same time the scheme of coal substance burnout at certain stages also becomes complicated by such processes as oxygen chemisorption, – 506 – gasification of non-volatile residue by carbon dioxide (CO2) and water vapors (H2O), transformation of the chemical components of the mineral fraction of fuel etc. [14, 15]. Consideration of these processes in the evaluation of the extent of the thermochemical transformations determining the burnout of pulverized solid fuel is necessitated by their essential mutual influence upon each other as well as significant contribution of the values of the thermal endo- and exoeffects inherent in the behavior of these processes [16]. The maximum correctness of such evaluation can be achieved by implementation of the complex approach based on experimental determination of the reaction characteristics of various stages and phases, which form the process of fuel burning, with subsequent calculated application of these data for computation of the kinetic parameters of coal thermochemical transformation [13].
The principal feature of the technique proposed is the unity of experimental-methodical ways and the analytical apparatus from the point of view of the structural scheme and the basic mathematical models employed in the description of individual processes and stages responsible for the burnout of solid organic fuel. This correlation, on the one hand, lays down strict requirements to the technique of conducting the kinetic experiment and processing its data and, on the other hand, provides, in the end, the appropriate quality of the mathematical simulation results of the processes of solid fuel thermochemical transformation kinetics in actual practice of processing plants. However, to implement such approach in practice it is necessary to overcome a series of procedural difficulties associated with the determination of the running rates of various stages of coal thermochemical transformation in a wide range of operating conditions (operating environment, temperature, heating rate, etc.), connected with overlapping of several processes and impossibility of their separate evaluation as applied to the conditions of real technical methods of solid organic fuel processing [17].
An effective instrument of solving the abovementioned problem is the use of the complex thermal analysis of solid fuel with continuous recording under non-isothermal conditions [18, 19] and the methods of mathematical simulation of kinetic processes [20, 21]. Here, a general structural physicochemical scheme with a set of basic models of individual processes and stages responsible for solid organic fuel burnout should be assumed as a basis of the method of thermogravimetric experiment data processing and mathematical model description.
Experiment
The plant for the complex thermal analysis of solid fuel (Fig. 1) integrates derivatograph (type Q -1500D) of Hungarian company MOM and chromatographic gas analyzer “Soyuz 3101” in the framework of the complete functional scheme that allows to derive the dynamics of gaseous products emission (CO, CO2, H2, CH4, etc.) under non-isothermal conditions alongside with the total characteristics of coal sample heating process (loss of weight, rate of weight loss, change of temperature, thermal effects) [22]. The derivatograph enables to work in quasi-isothermal mode with the heating rate adjustable from 0,2 to 5 mg min-1 in nine stages. The limit load of the scales is 10 g, the measurement accuracy at 20 mg sample is ± 1%. The instrument is equipped with a six-channel self-recorder with the measurement range from 50 µ V up to 5 mV 250-1 mm per each channel. Parameters of the derivatograph operating mode were selected and adjusted by evaluation calculations upon the results of repeated running of isothermal and quasi-static procedures in order to ensure running of the heat treatment processes of the investigated material in the kinetic area without any diffusion complications. The operating parameters of the derivatograph during fuel thermal decomposition met the following values: inert – 507 –
ШШШШ

Metering cock
Ascarite and anhydrone filters
Fig. 1. Schematic diagram of the plant for complex thermal analysis of solid fuel medium (He); weight of coal sample 500 mg; heating rate 5-20 K min-1; those during combustion of nonvolatile products of thermal decomposition and thermal-oxidative degradation of initial coal were: oxidizing medium (air); weight of coal sample 50 mg; heating rate 5–20 K min-1. For the investigated processes there was also a series of generalized adjustments employed: inert material Al2O3; platinum crucible; sensitivity of recording (цП) TG 500, DTA 1000, DTG 500; gas flow rate 200 cm3 min-1; size of coal particles: polyfraction (with sieve residue R90 = 45–50 %, R200 = 28–32 %, R1000 < 1 %).
The evaluation technique of the kinetics of the pulverized solid fuel burnout processes is based on the processing of the experimental data obtained in three experiments (Fig. 2) by means of the complex thermal analysis [23]: 1) in inert atmosphere (Fig. 2a) with gas analysis of the composition of emitted volatile matters (Fig. 2d) upon which results the characteristics of moisture evaporation process, the total output and composition of volatile matters are determined. The DTG-curve after subtraction of the differential curve of the total output of gas-vapor components (curve 5 in Fig. 2d) is transformed to the pitch formation curve; 2) in oxidizing medium the nonvolatile residue generated in the previous experiment (Fig. 2b) burns out; 3) in oxidizing medium: thermal-oxidative degradation of the initial coal substance characterized by overlapping of the processes of moisture evaporation, emission and burning of volatile matters as well as burning of nonvolatile base (Fig. 2c).
In consideration of synchronism of several processes running at thermal-oxidative degradation, which total rate is registered as DTG-curve, the process of volatile matters (the “synthetic” volatile ones [17]) emission was separated by subtracting the coke base oxidation rate from the DTG-curve of thermal-oxidative degradation process. The rate of the oxidation reaction of nonvolatile residue was determined upon the results of the second experiment and superimposed on the DTG-curve of the thermal-oxidative degradation process with appropriate correction of temperature intervals.
Then, the total curve of gas emission rate obtained in the first experiment and recalculated with respect to the rates of volatile matters emission in inert and oxidizing mediums on the assumption that – 508 –
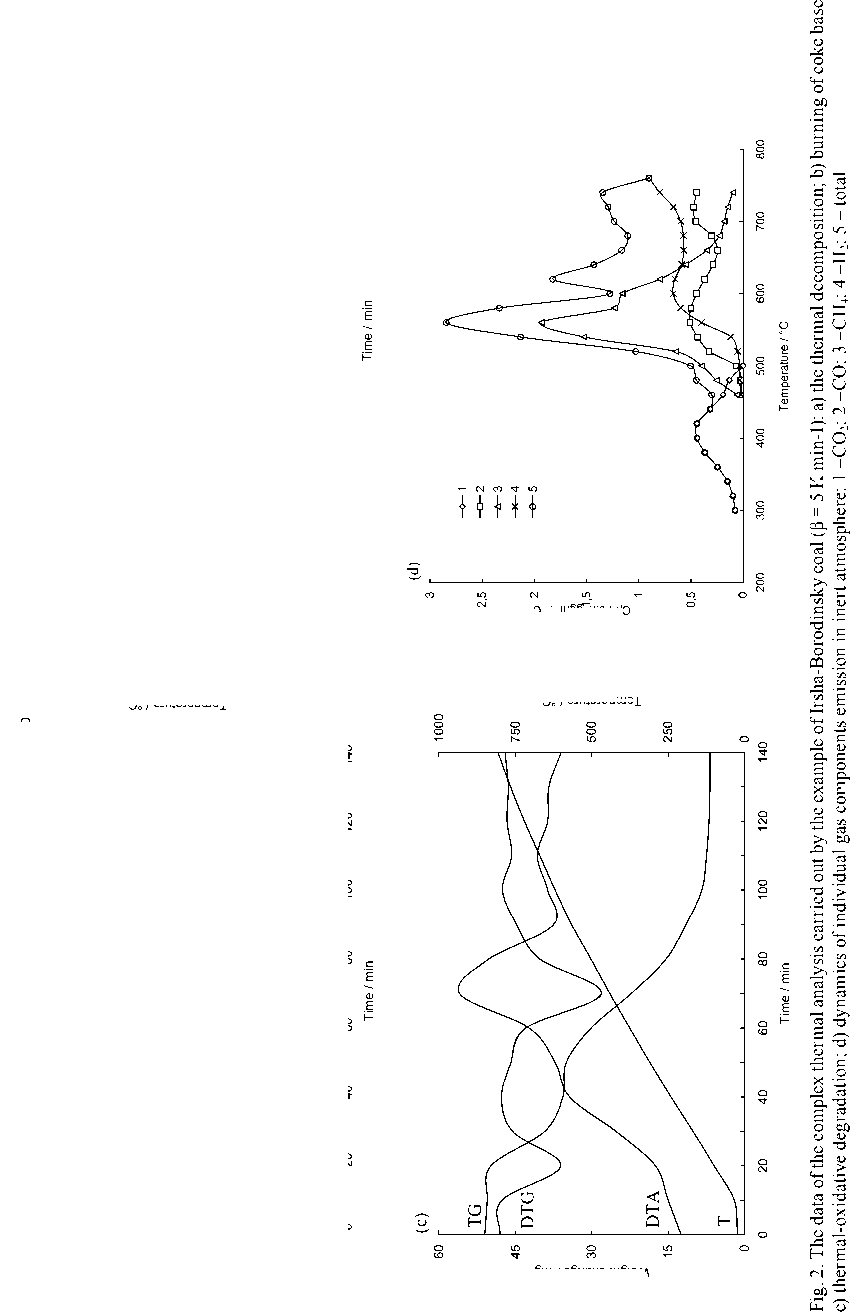
6ш / эбиецо 1цб1э/\д
Эо / ЭJn^вJэdшэl
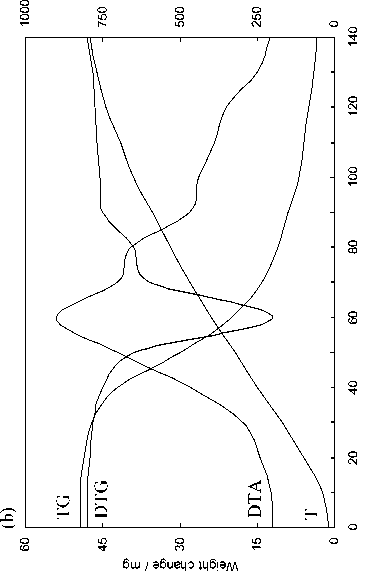
Эп / ЭJnleJэdшэ I
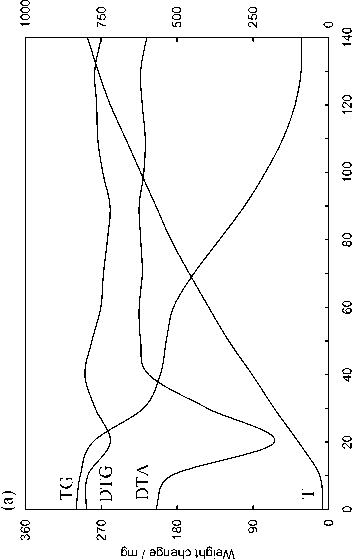
^Jo рШбб £шэи /
Э„ / ЭJnleJэdшэl
the total amount of gaseous components is constant was superimposed on the period of volatile matters emission derived during thermal-oxidative degradation. By subtracting the respective curve of gas emission from the differential curve of the process of volatile matters emission in oxidizing medium the differential curve of pitch formation in oxidizing medium (“synthetic” pitches) was produced.
For the kinetic evaluation of gasification processes of the coke base the nonvolatile coal residues generated during the thermal analysis in inert atmosphere with the final heating temperature of 1173 K were subjected to the treatment by carbon dioxide and steam under conditions of continuous temperature increasing in the complex thermal analysis plant. The heating rate in the experiments for determination of the reactivity of coke residues relative to CO 2 and H 2 O was 5 K min-1; concentration of CO 2 = 100 %, H 2 O = 100 % (at atmospheric pressure); weight mass 150 mg; the flow rate of CO 2 into the furnace of the derivatograph was 220–240 cm3min-1, the flow rate of H2O = 250–290 cm3min-1 [24]. The standard platinum plate-shaped crucibles of the derivatograph were used as object holder.
The above-stated technique of producing experimental data upon the results of experiments of the complex thermal analysis of solid fuels (thermal decomposition, burning of non-volatile residue and thermal-oxidative degradation, coke base gasification) enables to proceed to their processing in order to determine kinetic parameters (activation energy E and pre-exponential factor k 0 , numbers of individual stages of reaction, share of reacted substance, temperature interval of reaction running etc.) of multiphase overlapping processes of fuel thermochemical transformation [23].
Interpretation and discussion of research results
The kinetic analysis and evaluation of the complex experimental curves, representing the dynamics of thermochemical transformation of solid organic fuel, were carried out using a computational software package [25] built on the basis of generalized kinetic mathematical model on the assumption of multiphase process additivity that meets the following physicochemical (Fig. 3) and calculating schemes (Fig. 4).
According to the proposed schematization the process of coal burning is divided into several relatively independent overlapping multiphase stages (Fig. 3): drying and preheating of particle before
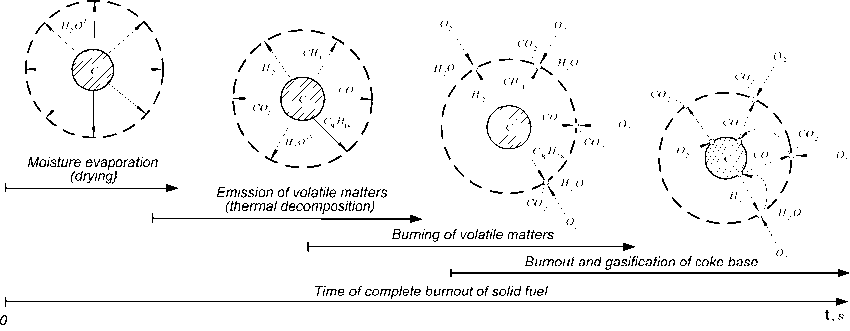
Fig. 3. Physicochemical model of thermal transformation of solid organic fuel
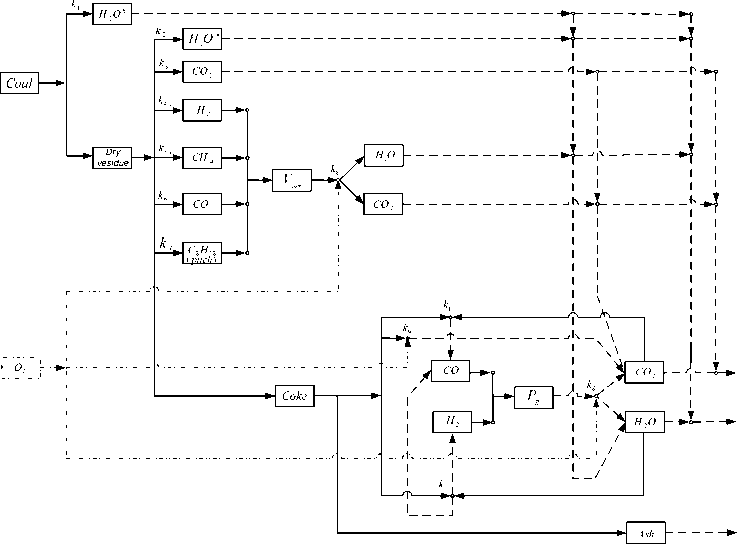
Fig. 4. The calculated scheme of the kinetic processes of the thermochemical transformation of solid fuel emission; emission and burning of volatile matters near the particle; burning of nonvolatile (coke) residue consisting of organic and mineral fractions.
The physicochemical model of thermal transformation of solid organic fuel in wide temperature range implies that the process of wet material drying is characterized by moisture evaporation from the volume of coal particle on the condition of movement of the evaporation surface, as a front of phase transition, inside of the particle and results from an increase of the dry layer surface temperature. Since moisture contained in fuel has bonds of different strength with coal substance it is appropriate to consider two independent evaporation fronts of hygroscopic and chemically bound moisture [26, 27], where the front of the chemically bound moisture evaporation remains behind the front of hygroscopic moisture evaporation.
As the temperature of the surface layer increases there is running the process of thermal destruction (pyrolysis) of organic mass accompanied by volatile matter emission. The up-to-date models of pyrolysis regard the organic mass of coal as an ensemble of condensed aromatic, hydroaromatic and heterocyclic structures (clusters) containing various functional groups as substituents [28]. During heating of fuel there are observed ruptures of the bonds, that attached functional groups to ring clusters, with formation of the volatile gas components (mainly CO2, H2, H2O, CO, CH4, HCN, aliphatic hydrocarbons). Together with the emission of light gas components there is a splitting of bridge-type structure of coal with release of large molecular fragments (pitches C 8 H 18 • 2H 2 O ) [29].
The emitted combustible gaseous volatile components reaching sufficient concentration of stoichiometric mixture react in gas phase with oxygen of air to generate final products CO2 and H2O [30].
During emission of volatile matters and their subsequent burning there is heating of coal particle accompanied by initialization of the process of its nonvolatile (coke) basis burning. The reaction runs on the coal particle surface and results in adsorption of air oxygen from gas space onto carbon surface. Here the atoms of oxygen enter a chemical reaction forming compound carbon-oxygen complexes C x O y . The latter then dissociates and forms products of complete burning ( CO 2 ).
Steams (H2O) and carbon dioxide (CO2 ) generated from the processes of drying, sublimation of the ballast volatile matters, burning of the combustible volatile matters and coke base of fuel as well as generated from the after-burning of incomplete products of combustion can react with the solid phase resulting in formation CO 2 and H 2 . These reactions run according to the chain-radical mechanism with direct participation of hydroxyls as intermediate compounds resulting in appearance of HCOH complex and also subsequent appearance of donor-acceptor-type valence bonds with monatomic carbon. Collision of atoms and molecules with lattice vacancies and presence of valence forces on active places of surface results in formation of intermediate complexes. The latter stimulates electron transfer, thus providing chemisorption of gaseous components on the surface of coke base with their subsequent oxidation to CO 2 and H 2 O [31].
The proposed calculation scheme enables to build a mathematical model that ensures control of material balance accomplishment of separate stages and phases of coal burning, and also the gross – process as a whole. When the mathematical model was build it was assumed that multiphase processes of thermochemical transformation of solid fuel were additive, the functional groups during thermal decomposition of fuel were emitted independently from each other, the ratio of functional groups in pitch were the same as in the initial coal, the volatile matters and nonvolatile coke residue, emitted during pyrolysis of coal dust, ideally mixed with oxidizing agent (air) and then entered chemical reaction.
The mathematical model of the kinetic processes of thermochemical transformation of solid organic fuel based on application of the commonly used stoichiometric equations [16, 17, 22, 26] with regard for the assumptions made in differential form looks as follows.
The equation of the kinetics of drying describes the kinetics of hygroscopic moisture evaporation from coal surface and complies the following stoichiometric equation H2O0 —kH2Oh > H2O :
where k h H2O0
d H 2 O 0 h dt
k H 2 O 0 h
H2O0 h ,
= k о h
H2O 0 h
exp
V
E H 2 O 0
RT (t) /
The equation of kinetics of volatile matter emission takes into consideration the contents of residual volatile matters in the fuel resulting from the multiphase mechanism of bond rupture being accompanied by emission of ballast (H2O and CO2 ) and combustible (H2, CH4, CO, pitches (C8H18 ∙2H2O) volatile vapor-gas components during thermal decomposition of organic coal mass [30] on the basis of zizjkV0 zizj stoichiometric scheme ZZ V0. j -^i^ zzVvoli j according to expression:
Evgeny A. Boiko and Sergey V. Pachkovsky. Complex Approach to the Evaluation of the Reactivity of Solid Organic Fuels ___________z______________________________________z_____________________________z____________z___________ ______________________________________________________________________________z________________________zz_____________________ dV0 dt
^^^^^^e
zi zj
■ 22 k . o. V >„• = 1 ■ • '
i = 1
where kv = kn
V 0 i , j 0 V 0 i ,
exp
,L EV 1
RT ( t ) , .
The kinetic equation of volatile matter burning describes homogeneous process of changing of combustible volatile matters concentration in the gas phase during their oxidation accompanied by formation of final products CO2 and H2O according to the following stoichiometric ratio v V + v O, ——com > v „ P . The first summand covers the dynamics of accumulation of the Vcom com O2 2 PVcom Vcom emitted combustible volatile matters in the volume near the particle, whereas the second one covers their burning:
dV com dt
z i j
= LL j
—
k com
v^
com
ν Vcom ν O2
com 2
/ 77 A where kv = k0
V com 0 Vcom
exp
EV =m |
I ■I RT(t)J
The equation of the kinetics of coke base burnout and gasification describes the consumption of carbon during reaction of fuel resulting in formation of CO2 according to stoichiometric ratio vCC + vO2O2 —C > vPC PC and recovery of complete combustion products (CO2, H2O) resulting in intermediate combustible products CO and H2 according to the scheme
zr
Д V er C + v P P r =1
CC V P g P ) .
The first summand represents the dynamics of coke base burnout, the second one describes gasification of combustion products [24]:
d C — dt
zr kCVCCVCQVO2 +У kC Vc c^rPVP-'
c c 2 r =1 C r c, r
/
E c,r )
RT ( t ) J .
where
kc = k
The kinetic equation of after-burning of the combustible products of gasification considers the process of changing of the concentrations of the combustible products resulted from the gasification of coke base with final products of the thermochemical transformation of solid organic fuel during their homogenous oxidation, which is accompanied by formation of final products CO2
kP
8 > Vp Pp . The first P P g P g
and H 2 O according to the following stoichiometric ratio v p P g + V o O2 g 2
summand covers the dynamics of accumulation of the emitted combustible volatile products of gasification, whereas the second one covers their burning:
dPL = T k V c cr p - P Ф - к v P - . O V O2
where k P g
= k 0,
Pg
exp
EP g
RT (t),
The equation of the dynamics of oxygen concentration shift in the gaseous phase describes the consumption rate of the oxidizing agent during homogeneous and heterogeneous combustion of gaseous components and coke base accordingly. The first and the second summands represent the process of O2 concentration loss as a result of burning of volatile matters and coke base, the third one represents the process of homogeneous oxidation of the gasification products formed:
d O 2 dt
ν V com k V com ν O 2 V com
OV 2 O2 + k C v Cv O ' + k P g v P g Pg O' .
The concentration of the products of thermochemical transformation of coal – dust particle is taken into consideration according to the equation describing the dynamics of moisture evaporation, emission of ballast volatile matters and volatile matters unreacted in oxidation, complete burning of volatile matters and coke base of fuel as well as gasification of nonvolatile products and after-burning of combustible products of gasification [28]. The first summand of this relationship represents the dynamics of product formation as a result of moisture evaporation, the second one represents that of ballast and unreacted volatile matters emission, the third one represents that of homogeneous burning of volatile matters, the fourth one represents that of heterogeneous burnout of coke base, the fifth one represents that of after-burning of combustible products of gasification, the sixth one describes the concentration loss of end products (CO 2 and H 2 O ) during ga sification with coke carbon base:
dP = k h H O h + zyjkkv V + kv v„ Vvvcom O^O2 ф + dt I2I0h 20 V0i,j 0i,j Vcom PVcom com 2
i 1 j 1
+ k c v p co ф рс + k p v p P g Pg O ф рр ^> C, r v p , r C C, r P vp , r ,
C C Pg r=1 ,,
The above-stated system of differential kinetic equations was meant for the following initial conditions: HO = H O , V , = V omM , C = CimM , O 2 = O 2 i n iti a l , H 2 O h = 0 , V = 0 , P = 0.
20 2 0initial 0 0initial initial 2 2initial2
In addition to the kinetic equations this system meets the law of conservation of mass dHOh
H2O0 + V0 + C + O2 + P = H2O0initial + V0initial ■ Cinitial ■ O2initial ,, since the ratio —2"^ ++ dt dt dC dO
+—+——- = 0 is met. dt dt
To describe the non-isothermal nature of the process of coal thermochemical transformation under conditions of the complex thermal analysis the mathematical model was supplemented with the dT
.
equation of the linear law of heating T = T o + e t , where e = — dt
The present mathematical model of independent overlapping reactions is assumed as a basis of the processing algorithm of the gross-process of thermochemical transformation of the solid organic fuel that enables determination of the whole aggregate of the reaction characteristics of the elementary stages of this process [25]. The implementation of the algorithm of sequential calculation and elimination of individual stages is associated with determination of isolated stage section on the accumulated kinetic – 514 – curve and based on the principle of sequential search and evaluation of the kinetic characteristics of elementary stages on the basis of using the correlation and multifactor regression analysis [32] of experimental points in Arrenius coordinates. In these coordinates the linearized kinetic equation of the marked out stage represents the equation of straight line. Sequential analysis of the correlation factor values of experimental points reveals the aggregate of points meeting the preset correlation value and taken as a stage interval.
In this case the rates of top chemical reactions (moisture evaporation and thermal decomposition) were calculated according to the following relationship:
W = ktch (C„о - C„)n.
The heterogeneous reactions (burnout of coke base and gasification of coke) were calculated, in consideration of particle size change, according to the expression [23]:
w khr ( C rs 0 — C rs )
di ’ where di = d0з
C —C rs 0 ^rs
C rs 0
Further, the sought kinetic parameters are determined by linear regression factors and the relationship of conversion degree at the i -th stage is build on the calculation basis according to the following ratio:
C . ( . ) = exp _ 1 b ( W
n i ,max
k 0 i ( 1 n ) F i ( t ) )
where F i ( t ) =
J exp tmax
E i
RT (t )J
dt
– integro-exponent function.
After subtraction of the calculated values from the initial experimental kinetic curves the process of searching and determination of the parameters of next stage begins and the direct kinetic problem subject to identification of the type of global stage of coal thermochemical transformation (drying, volatile matters emission, burning of coke base etc.) is solved according to the above-stated mathematical ratios.
On the basis of the technique stated above a cycle of researches on the kinetics of burning-out of Kansk-Achinsk coals, in particular those of Borodinsky, Berezovsky and Nazarovsky deposits, was carried out. The problem of power-producing utilization of these fuels in consideration of scale of their mining as well as immense role in the development of Siberia’s productive forces and the fuel and power base of Russia is of highest priority. The Kansk-Achinsk basin coals are humic, semi-glittering and semi-dull, lens-shaped streaky, belong to helytolitic type and consist of small fragments and fragmentary structure residues with distinctive microlamination. The main layer-forming coal types of heavy layers of the basin are attritic and fragmentary telohelits making up 70-95% of the overall capacity. Some distinctive features of the coal chemical composition, in particular, low hydrogen content, large amount of humic acids, relatively high humidity and emission of volatile matters, low and medium ash percentage, point out the low-reduction nature of the helified substance of the coals. The technical analysis and element percentage of Kansk-Achinsk coals are shown in Table 1.
Table 1. Characteristics of Kansk-Achinsk coals
Coal field |
Technical specification, % |
Element contents, % per working mass |
|||||||
W r |
A r |
V daf |
Q i r , (kJ kg -1 ) |
C r |
H r |
N r |
O r |
S r |
|
Borodinskoye |
33.0 |
9.95 |
48.2 |
15318 |
41.2 |
2.89 |
0.57 |
12.1 |
0.29 |
Berezovskoye |
35.5 |
4.0 |
49.5 |
15084 |
42.4 |
3.0 |
0.40 |
14.4 |
0.30 |
Nazarovskoye |
38.5 |
5.53 |
49.1 |
13157 |
38.8 |
2.86 |
0.41 |
13.5 |
0.40 |
Using the above-stated mathematical model and values of the kinetic characteristics found from the results of evaluation of the complex thermal analysis data the calculation analysis of the kinetic processes of thermal decomposition, coke base burnout and thermal-oxidative destruction of Kansk-Achinsk brown coals has been performed. In this article the results of the kinetic problem solution are given in comparison to the data of the complex thermoanalysis by an example of heat treatment of Kansk-Achinsk coals at heating rates of 5, 10 and 20 K min-1.
Type of the chemical reactions taken into consideration according to the calculation scheme presented in Fig. 4 and values of the respective kinetic parameters of various processes and stages of thermochemical transformation of Kansk-Achinsk coals revealed upon the results of the data processing of the complex thermal analysis are shown in Table 2. The calculation was carried out on PC Pentium 4 in programming environment Builder C ++ 6.0 . For the numerical solution of the system of differential equations the Runge-Kutt-Felberg method with automatic step selection and accuracy of 10-4 [32] was used. The calculation results in comparison to the data of the complex thermal analysis are given in Fig. 5. This figure shows the curves of thermochemical transformation degree changing under conditions of thermal decomposition ( ® d = m d/ m 0 td ), burning of coke base ( ® bc = m bc/ m 0 bc ) and thermal-oxidative destruction ( ® tod = m od/ m 0 d ) depending on process temperature, where mtd , mbc and mtod are the current fuel mass during thermal decomposition, burning of coke residue and thermal-oxidative destruction accordingly; m 0 td , m 0 bc and m 0 tod are the initial fuel mass before thermal decomposition, burning of coke base and thermal-oxidative destruction accordingly. At the same time, the calculation correctness was checked by control of ensuring the strict ratio of the material balance of thermochemical transformation process of fuel in terms of analytical mass m F - m w - m v - m e - m A = 0 , where m F is the mass of initial fuel, m w is the mass of hygroscopic moisture, mV is the mass of volatile matters, mC is the mass of coke base and m A is the mass of ash residue.
As evident from the obtained results the observed kinetics of moisture evaporation conforms to the competition mechanism of adsorption and desorption of water present in the coal in form of general phase and molecular clusters of coal structure pores. The curvilinear profile of changing of fuel sample mass in the temperature range of 293-453 K completely corresponds to the model of evaporation of moisture bound with material in the hygroscopic form according to Rebinder classification. The change of fuel mass in this section corresponds to evaporation of cellular moisture and moisture of monomolecular and multimolecular adsorption caused by hydrogen bonds of water molecules with active centers of fuel surface [26]. The maximum rate of moisture – 516 –
о о й Z |
С-1 О С-1 ,d г- ® 2 ч 2 м / оо vo сч со in со Xr-S) °У ЮрВ1 ^гйоооо2£ о о о ^ о - о со XiijiqBqoij ооооо°ЧНЧ? ° ° ° о S Д^-С-С-С^О-с! Ч Ч S S О o-l xh 1—< 1—< 1—< o-l ^ S ni 1—< I oi сч oi co oi |
|
(,-ТОШ и) 3 ЛЗтэиэ иоцвлцоу |
2 2 i Д^^^Д^дн! Д di 2^i^2^2^c3 x in । 5 2 rd x 5 |
|
^1 э8иы a.iniB.iaduiai |
Xh5y^X22ovX Ov co 2 I Ch co CO CO CO CO co co co co co co co co 1 S co co oi^tdw^S^r^ od ^ | ио Ф 0^ 2 S ^ ^ |
|
о о о 8 m |
G-S Ш) ‘( ,-S) °.y JOJOBJ Mqiqvqo.id |
j j j ■^°?8j:N°4h'/} ° "З”^”^”^ |
(рРШ я) у XSlQUQ иоцвлцоу |
||
^1 э8иы a.iniB.iaduiai |
5tn^^^^rC^ CO 1 co co co 1 1 1 S m co co |
|
О ,Й У О о m |
G~s Ш) X ,-s) Д iopBj Xjqiqvqoid |
^oScd^oCdr^ 2 0 0 co Й 0 co ° 4 2 Ъ У +122^222^ 2 2^2-h^o2-h |
(Г1ОШ H) g XSlQUQ иоцвлтру |
^^5^33^4? 3 5 2 Ч? hh 41 2 д p co Д g Д 2 2 di |
|
Ся)2 oSub.i a.iniB.iaduiai |
ДДДД^ДДД m м^^ДД^^Д |
0 04 |
о О О О 2 о' О + + " 4 Я щ У и О 4 Чч о и ф и t у и О X 4 4 Ф Т 4 । ^Т ^° S 2 S ® г; О ^ q >? -«е Й _= С *^ -'г О ГЛ >s >s X += О ° Ж + м ^ О ^--ч *П Ж X Й О О ОО | + + 4- Ьб |
'ojq иоцовэ^ |
m s х cd |
о 2 |
Й ? Й - ” о 3 -5 я „ о 8 1 1 -о ° — 00 У со Й й S у ,2 -й .2 2 о й о й ^ у 2 За щ 8 -о то тоох> |
I
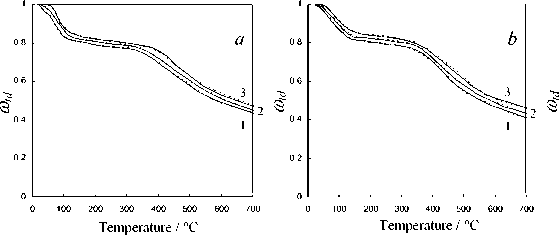
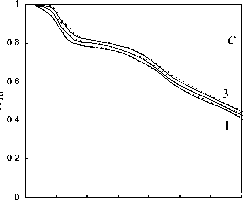
0 100 200 300 400 500 600 700
Temperature / ° C
II
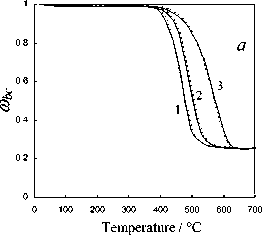
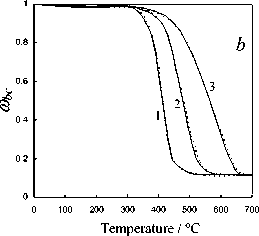
0.8
0.6
0.4
0.2
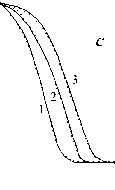
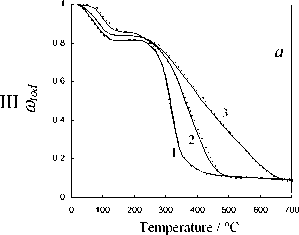
Fig. 5. Calculation results of the thermochemical transformation of Kansk-Achinsk coal (1 – β = 5 K min-1; 2 – β = 10 K min -1 ; 3 – β = 20 K min -1 ): I –thermal decomposition; II –coke base burnout; III –thermal-oxidative degradation; coal: a –Irsha-Borodinsky, b –Berеsovsky, c –Nasarovsky; solid line –the data of complex thermal analysis; dotted line –calculation
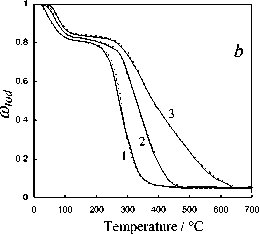
0 100 200 300 400 500 600 700
Temperature / ° C
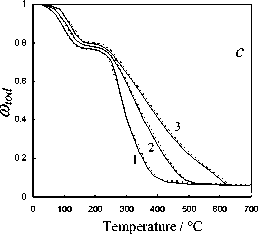
evaporation in the range of heating rate variations of 5–20 K min-1 during drying of Borodinsky coal is W max = 2.34–2.85 mg g-1,K-1; that of Berezovsky coal is W max = 2.2–2.75 mg g-1,K-1 and that of Nazarovsky coal is W max = 2.53–2.98 mg g-1,K-1 with general position of temperature maximum T max = 343–393 K.
The temperature corresponding to the maximum rate of thermal decomposition reaction ( T max) for all three types of Kansk-Achinsk coals has values of 713-733 K. The maximum rate of volatile matters emission is W max = 1.61–1.95 mg g-1,K-1 for Borodinsky coal; W max = 1.87–2.21 mg g-1,K-1 for Berezovsky coal and W max = 1.33–1.69 mg g-1,K-1 for Nazarovsky coal. The peak of the total gas emission during thermal decomposition occurs at the temperature of 833 K for Borodinsky coal ; 973 K for Berezovsky coal and 793 K for Nazarovsky coal. It is significant to note that the process of volatile matters emission of Borodinsky coal in oxidative atmosphere runs in a lower temperature range (513-633 K) and at a higher rate ( W max = 5.4–5.6 mg g-1,K-1) than the similar process in inert atmosphere (573-853 K and – 518 –
W max = 1.29–1.36 mg g-1, K-1). The same effect is observed during the volatile matters emission of Berezovsky and Nazarovsky coals.
Burnout of nonvolatile residues of Nazarovsky coal runs in two stages with the temperature maxima of reaction rate at T = 673-748 K and T = 763–818 K, at the rate values W = 0.44–0.56 max max mg g-1,K-1 and Wmax2 = 0.48–0.6 mg g-1, K-1 accordingly. Burnout of nonvolatile residues of Borodinsky and Berezovsky coals runs in one stage at the maximum reaction rate Wmax = 0.52–0.66 mg g-1,K-1 at Tmax = 703-823 K and Wmax = 0.65–0.79 mg g-1,K-1 at Tmax= 673-798 K accordingly.
The investigations performed and the comparison of calculation results of the kinetics of thermochemical transformation of various coals allows to establish that the proposed experimentcalculation method of evaluating the degree of solid fuel burnout provides satisfactory qualitative and quantitative convergence under the linear law of heating which simulates the conditions of the complex thermal analysis. The relative error of the experimental and calculated parameters of the investigated thermochemical reactions subject to 95% confidence interval of Student statistical test t was 3–5 %.
The comparative analysis of the obtained data on the kinetics of various processes of the thermochemical treatment of Kansk-Achinsk coals shows good conformity with the results of similar investigations of individual stages of burning of a wide range of coals presented by other authors [1, 6, 13, 24, 30, 31] with the maximum correlation of reaction parameters being observed in case of coincidence of the technical composition and the analysis of coals [6, 19, 27, 29, 31]. With that the conduction conditions of the thermogravimetric experiment and the method of processing its data allow to assert that the kinetic characteristics of fuel burnout determined with the help of the proposed approach can be used in calculations of high-speed and high-temperature processes peculiar to real power plants subject to proper consideration and superposition of the diffusion factors on the kinetic model [9]. Thus, the proposed method of determination of kinetic parameters of various burning stages of coal based on its complex thermal analysis can be recommended as a universal and scientifically substantiated approach for the evaluation of the mechanism of thermochemical transformation and the reactivity of solid organic fuel.
Summary and Conclusions
-
1. An experiment-calculation method of evaluation of the kinetic parameters of burning processes in the context of a unified approach for the conditions of a wide range of fuel utilization plants, particularly such processes as: moisture evaporation, volatile matters emission with separate evaluation of pitch and gas emission, burning and gasification of coke base of solid organic fuel, has been developed.
-
2. The complex application of both experimental and calculating methods of investigating the burning processes of Kansk-Achinsk coals implemented in the discussed technique enables evaluation and control of kinetics of various overlapping processes and stages of thermochemical transformation of solid fuel in a wide range of practices in consideration of changes of reactivity of coal in comparison with its initial quality.