Control of convective flows in liquid metal influenced by electromagnetic forces
Автор: Timofeev Viktor N., Korchagin Аlexander I., Pavlov Evgeniy A., Timofeev Nikolay V.
Журнал: Журнал Сибирского федерального университета. Серия: Техника и технологии @technologies-sfu
Статья в выпуске: 1 т.5, 2012 года.
Бесплатный доступ
During preparation of metal alloys stirring of the melt plays an important role in order to even its chemical composition and temperature in the whole bath volume. It is necessary to create specific convectional streams of metal in the bath for effective stirring. Based on the known analysis of selforganization of convectional streams in the liquid heated from beneath (Rayleigh-Bernard effect), the present article describes a MHD-stirrer which allows receive a similar pattern of streams in the molten melt by using electromagnetic force. We have considered stirring processes in the rectangular bath and a MHD-stirrer which allows increase efficiency and reduce energy costs on the alloy preparation process.
Structure flows, liquid metal, mhd-stirrer, self-organization, control of flows
Короткий адрес: https://sciup.org/146114627
IDR: 146114627
Текст научной статьи Control of convective flows in liquid metal influenced by electromagnetic forces
The end of the 20th century saw great development of high-intensive technologies, based on self-organizing processes of dissipative structures. A system is called self-organizing if it develops a special, temporary or functional structure without a specific outer influence. We understand outer influence as some influence which is followed by the corresponding modifications of the system. For example, when feeding energy to the system reaches some critical value and instability occurs, the system develops a new state.
A laser has become a paradigm for self-organizing coherent processes because accordingly interacting atoms in a laser lead to appearance of a coherent laser wave.
There is another example of appearance of a macroscopic structure as a result of self-organization known in the hydrodynamics. When a layer of liquid is heated from the bottom, characteristic, spacetime structures – Bernard’s cells occur. When liquid heating is more intensive, new space-time structures can occur – oscillations /1/.
The present article attempts to observe application of self-organizing effect in technological processes of alloy preparation with usage of MHD-technology.
As it is known, MHD-technology is based on the influence from an electromagnetic field on melts with a special purpose. For example, in the baths of melting furnaces and out-of-furnace metal treatment devices with liquid metal, forced stirring of the melt can be carried out in order to intensify the heat-mass exchange by influencing the melt with certainly distributed and directed electromagnetic forces.
Under certain heating conditions of the liquid system, actuation of self-consistent dissipative structures occurs with an over-critical value of the leading parameter which leads to drastic increase of the heat-mass exchange intensity. It is possible to design casting-melting devices with MHD-stirrers so that to take into account possibilities of self-organization in a liquid metal in order to reach the end result with minimal energy demands and automation of the technological process.
Stirring of a melt in casting-melting devices
One of the main ways to improve melting processes and refining of casting alloys is intensification of heat-mass exchange in a liquid bath of melting furnaces and out-of-furnace metal treatment devices with the help of forced melt stirring. Stirring provides maximum temperature gradient and concentration on the border of the molten metal with the interacting phases (metal, alloying and refining hard and liquid reagents, atmosphere and vacuum). The gradient occurs thanks to supply of new portions of nonreacting metal to those borders and to decrease of the laminar border layer thickness, mass transfer, which is determined by the coefficients of diffusion and heat conductivity, the values lower than the corresponding coefficients with convectional heat transfer. In a number of cases the metal movement induces stirring of the reagent and speed of the heat transfer which can become limiting on a certain stage. Intensification of the process can also happen due to increase of the phase contact surface when stirring by creating waves, shredding metal or reagent for drops e.t.c.
Possibilities to use mechanical stirring are quite limited by high melt temperatures and their large chemical activity. Therefore in the last decades non-contact MHD-devices for force influence on molten metal have been widely spread.
The staff of the chair “Electrotechnics and electrical engineering” of Siberian Federal University (Krasnoyarsk) have designed and implemented different MHD-devices of metallurgical purposes in industrial enterprises: MHD-stirrers in furnaces and mixers; MHD-stirrer in crucibles; MHD-stirrers of a liquid centre of crystallizing ingots; Device for casting billets with a MHD-mould; MHD-rotators of liquid metal in channels of induction channel furnaces /2/.
In all the devices force impact of pulsing, running or rotating magnetic field is used on molten metal in order to receive certain technological effects. In the process of alloy preparation it is necessary to reach evenness both in chemical composition and temperature in the whole melt volume.
In order to carry out the technological process of alloy preparation the energy is needed, both to provide the necessary temperature rate and to provide stirring. A way and values of the heat and electromagnetic energies imposed on the melt define the behavior of the system, enable it to find its structure which corresponds to the distribution of heat, gravitation and electromagnetic fields as well as to the geometry of melt bath.
Casting-melting equipment on metallurgical plants
At the present time metallurgical plants employ different furnaces and mixers for preparation of alloys.
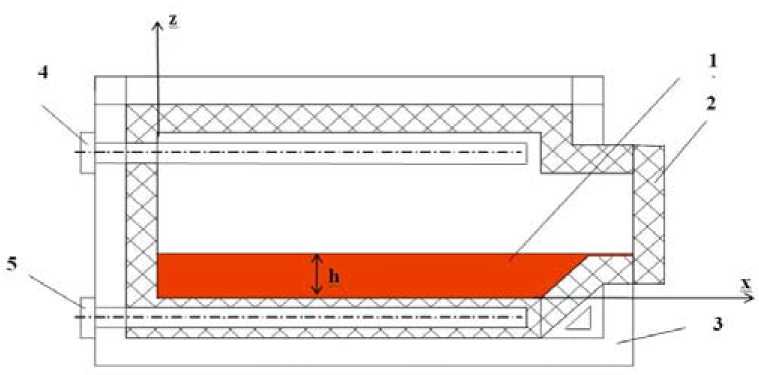
Fig. 1 Electrical resistance furnace for preparation of aluminum alloys with a rectangular bath
The most popular ones are resistance furnaces, induction crucible and channel furnaces /7/. Fig. 1 shows a schematic of a rectangular resistance furnace for preparation of aluminum alloys. Here 1 – molten metal, 2 – lining, 3 – steelframe, 4 –electric heaters installed under the furnace roof, 5 – electric hetaers installed in the furnace hearth.
When electric heaters 4 are installed only under the furnace roof, the heat stream coming from them reaches the melt mainly due to radiation and thus the upper melt layer has a larger temperature than the lower layer. With the melt height h about 1 m the temperature difference ∆Т between the upper and the lower melt layers can reach 1400С. The heat inside of the melt goes from the upper layer to the lower one mainly due to heat conductivity. In order to even the temperature in the whole melt volume, it is necessary to carry out its forced stirring. If electric heaters 5 are installed only in the furnace hearth/8/, the heat will be delivered to the lower melt layer due to heat conductivity. With a certain temperature difference ∆Т a convectional stream occurs and the heat goes to that bath both due to heat conductivity and convection.
When electric heaters are installed both under the furnace roof and in the furnace hearth, heating will be combined and we can control electric heating both from the bottom and from the upper melt surface.
An example of a more wide spread casting-melting equipment with the melt heated from the lower surface are induction crucible furnaces (ICF).
Fig. 2 shows a ICF with a cylindrical bath. Here 1 – melt; 2- refractory; 3 – steelworks; 4 – inductor winding; 5- inductor core; 6 – channel part with molten metal. When the inductor winding is connected to the varying voltage net, electric current occurs which heats the melt and the heat from the bath lower part is emitted to its upper layers with heat conductivity and convection.
When using MHD-stirring both in rectangular furnaces and cylindrical ones electromagnetic forces which significantly influence heat-mass transfer and convectional stream structure will occur.
A convectional stream has a certain structure and depends on the temperature drop between the upper and lower layers, liquid characteristics and bath geometry.
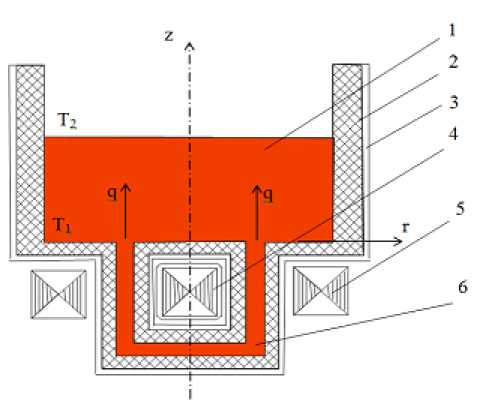
Fig. 2 Induction channel furnace with a cylindrical bath
Analysis of self-organization in a layer of liquid when heated from the bottom
All the liquids can be divided into liquids characterized by Prandtl number based on their influence on heat exchange conditions /4/.
Prandtl number is the ratio
P r = 7 , (1)
k where ν – cinematic viscosity; k- thermal conductivity.
In liquids with a big value Pr (all those are non-metallic dropping liquids) processes of movement quantity transfer prove to be more significant that heat transfer processes.
In liquids where Pr << 1 (all molten metals) heat transfer processes are more intensive that processes of movement quantity transfer.
The convection in horizontal liquid layers heated from the bottom has been studied since 1900. In the following years many experiments were carried out which were named experiments of Rayleigh-Bernard with a high and low Prandtl number.
An example of self-organization in a drain ditch with liquid with P r > 1, heated from the bottom and cooled from a free surface is shown in Fig. /4/. Because of heating and cooling between the lower and upper liquid surface, there is a certain temperature difference ∆Т = Т 1 - Т 2 which occurs. As the experiment shows, this temperature difference surprisingly influences the liquid behavior. If the temperature difference ∆Т between the lower and upper surfaces lower than a critical value ∆Т крит , liquid is in a state of peace and heat is transferred only with heat conductivity. When the temperature difference is larger than critical (Т 1 - Т 2 )› ∆Т крит macroscopic liquid movement suddenly becomes visible. For example, in the form of bowls, as in Fig.3, if the form of a drain ditch is rectangular or in a form of regular hexagonal cells, such cells have received the name of Bernard’s cells. We can say that the parameter ∆Т governs a macroscopic system behavior; therefore ∆Т is called a governing parameter.
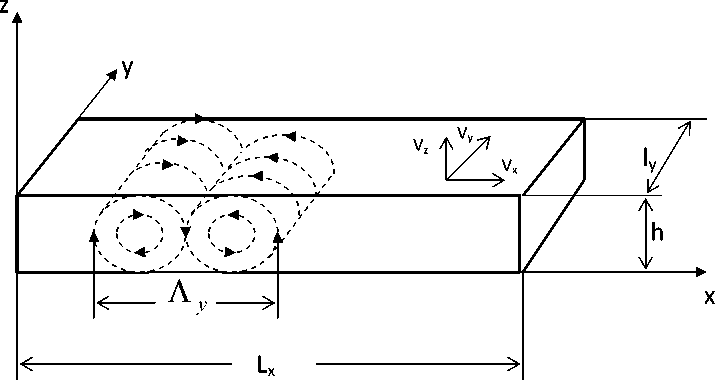
Fig. 3 Convectional streams in a rectangular bath
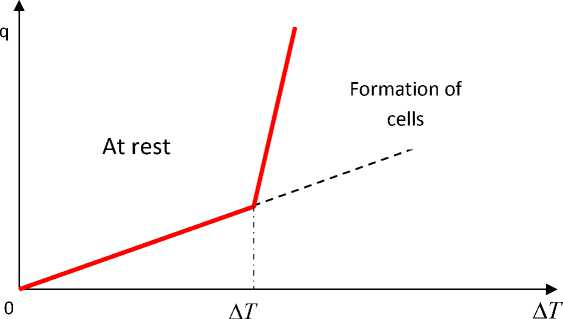
Fig. 4 Dependence of heat stream on the lower surface to the upper one of the temperature difference Δ T
Dependence of the heat flow q per a period of time from the lower surface to the upper one depending on ∆Т is presented in Fig. 4.
When the value of the temperature difference is critical, the mode of motionless liquid is unstable (dashed line) and it is replaced with a stable mode characterized with presence of convectional cells.
With a large value of ∆Т fluid at rest is not able to handle transfer of the corresponding large amount of heat and therefore a convectional mode is steadied which is more favorable for heat transfer. In comparison with an even balanced distribution, the convection cells are a more high-organized structure occurring as a result of cooperative movement of liquid molecules.
Physical explanations of the process are as follows. Because the liquid near the lower surface has a lower density that the liquid near the upper surface due to thermal expansion, due to gravity force and consequently buoyant Archimedean force, “light lower layer” and “ heavy” upper layer tend to replace each other. As a result of the liquid viscosity there is no movement even with minor ∆Т.
When the temperature gradient reaches a critical value, a convectional stream occurs which has a special structure in the shape of cylinders or hexagonal cells.
A non-dimensional criteria which is proportional to the ratio of buoyant force to viscosity force is a Rayleigh number
= a ⋅ g ⋅ h 3 Δ T ν k
where α – coefficient of bulk expansion, g – acceleration of gravity.
Following that we can say that when a critical value of Rayleigh number is reached, there occurs an organized structure in the heated liquid as a result of cooperative movement of the liquid molecules.
The results of Rayleigh-Bernard convection (silicon oil) with a high Prandtl number in a rectangular bath are presented in /5/. A layer of the observed liquid was placed between a lower polished copper plate and an upper mono-crystal sapphire plate with high heat conductivity. The convectional structure was visualized on the horizontal display with a shadow method.
If Rayleigh’s number Ra (proportionally applied to the temperature difference layer in a vertical direction) exceeds critical value of Raс , there is a convectional movement in the liquid in the shape of rotating cylinders. In the layer limited by the planes of a rectangular frame of axes (at that in a horizontal plane L x > L y , and the width L y is not too big in comparison with the depth h of the layer), the convectional structure consists of straight cylinders with the axes perpendicular to a larger side Lx . This periodic structure has a certain wave length Λ x , which is close to 2h neat the threshold R aс . The measures showed that with Ra > Rac (but near Rac ) when we neglect edge effects, the speed changes in space as in Fourier component
V = V m cos2 π x , (6)
where х – a coordinate in the direction perpendicular the axes of cylinders.
Thus for a rectangular vessel with liquid, an orderly system of cylinders is the most preferable convectional structure.
When Ra is increased to a certain value, the convectional stream stays a bidimensional one ( V x , V z , V y = 0), however higher special harmonics V 2 with a period Λ x /2 and V 3 period Λ x /3 are added to the main harmonics V with a period Λ x .
New bifurcation is higher than a certain threshold R a when a third speed component V y appears, the convectional structure become a three-dimensional one.
The results of experimental study of the convection in the mercury-liquid with a low Prandtl number ( Pr = 0,031 при 273 K ) are presented in /6/. The convection was investigated both in a cylindrical vessel and in a parallelepiped with the dimensions:
D = 1,7 cm, h = 0,85 cm, Lx =1,6 cm, Ly =0,8 cm, h = 0,8 cm; here D – diameter, h – vessel height, L x – large horizontal size, L y – smaller horizontal size.
Temperature difference on the layer thickness was created by heating on the lower copper block with constant current.
When analyzing the breaks of the dependence of Nusselt number on Ra the following conclusions are made. The first break with Ra ≈ Rac is connected with occurrence of convection. For liquids with – 33 – low Prandtl number the main instability of the cylinder bidimensional system is oscillatory instability which increases buoyant force. The second break is observed with Ra ≈ 2,5 Rac. It can be connected with occurrence of the second frequency in a spectrum of temperature. In the marginal case of low Prandtl numbers a mode occurs instead of balance between buoyant force and viscous dissipation where buoyant force is balanced with inertial members. It happens with Ra ≈ 4 Rac.
Summing up the results of the described experiments we can make a conclusion that with certain influences on molten metal self-organizing convectional streams can occur in it. Their structure depends on the melt characteristics, bath geometry and temperature gradient value. Knowing the structure of convectional streams we can design MHD-devices in such a way that the created electromagnetic fields will intensify processes of heat-mass transfer or provided energy efficient stirring when there is no temperature drop.
The convectional movement of molten metal in the shape of cylindrical bowls in a rectangular bath can also be obtained with the help of electromagnetic forces.
Mathematical and experiment Results
Fig. 5 shows a rectangular bath 1 with molten metal 2. If, for example, a large side L x ≈5 h where h – metal height, it is possible to install 3 coils. Three consequently connected coils inclined to the right present one phase A and three consequently connected coils inclined to the left present another phase B. When the phases A and B are connected to a two-phase power supply with a phase shift of 900, alternating currents appear in the coils i A =I m sinωt ; i В =I m sin(ωt+900); where I m and ω – is an amplitude and angle current frequency. We know from the electrotechnics that two coils space-shifted and fed by the phase-shifted currents create magnetic fields.
As a result of the influence of rotator magnetic fields on the melt convectional streams in the form of rotating cylinders occur.
A system of three pairs of coils can be replaced with an inductor containing a magnetic wire 3 and six coils wound on the magnetic wire frame. Here each phase consists of three consequently connected
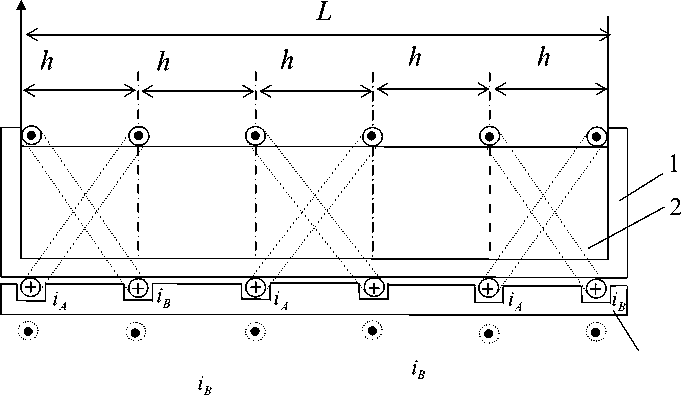
Fig. 5 Convectional MHD – movement in the rectangular bath
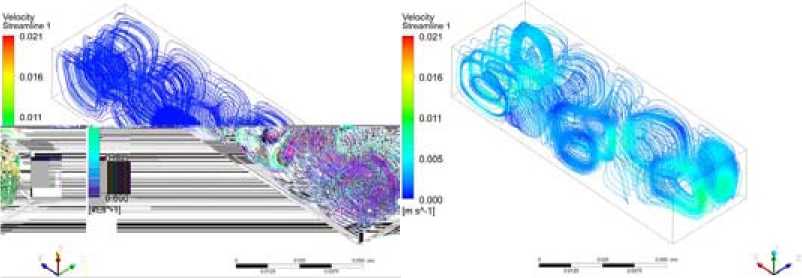
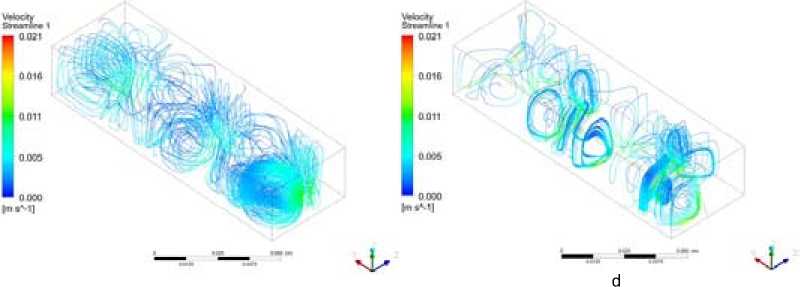
Fig. 6. Pathway with a different frequency: а) f=50 Hz; b) f=800 Hz; c) f=1500 Г=Hz; d) f=10000 Гц coils. The inductor can be installed under the bath with a melt. Such a construction has an advantage as it does not include the coils located in the bath with a larger temperature.
A mathematic and phys c models have been built to investigate a pattern of flows in a rectangular bath when an inductor electromagnetic field influences the melt, installed under the bath.
Bath manufactured from s ainless steel has the following dimensions (mm): Lx = 125; Ly = 40; h = 25.
As liquid metal gallium was us d with heat conductivity γ Ga ≈3, 106 Om-1∙m-1 and the melting temperature 38 °С.
Mutual solution of electrodynamical and hydrodynamical solutions was carried out with a program package ANSYS Academic Research.
Fig. 6а, 6b, 6с and 6d show the results of numerical simulation for the molten metal convectional streams with a different inductor current frequency. As it follows from Fig. 6а with f = 50 Hz metal movement is presented by rotating cylinders. With an increase of frequency Fig. 6b (f = 800); Fig. 6с (f = 2000) the cylinders begin to deteriorate, slowly the movement of distinct eddies becomes a complex turbulent movement (Fig. 6d, f =10 000).
This conclusion is also confirmed by Fig. 7, which shows the graphs of distribution for the velocity component Vx along the bath length у of the melt bottom ( z ≈0). When with frequency f<1000Hz velocity curves are close to the sinusoid , with a period Т≈2h, then with the frequency f>1000Hz higher – 35 –
0,0070 -| nЛЛАЛ - |
Dependence of Velocity u-comp in point x= |
0,0375 m |
|||||
0,0050 - 0,0040 - ПЛЛЯЛ - |
|||||||
0,0020 - 0,0010 ’ |
|||||||
и,ииии ■ -0,0010 - -0,0020 - |
2( |
00 4> |
qo вс |
00 8( |
00 10 |
)00 12 |
)00 |
и |
|||||||
Fig 7. A graph of distribution of the velocity compound V on the bath length у of the melt bottom
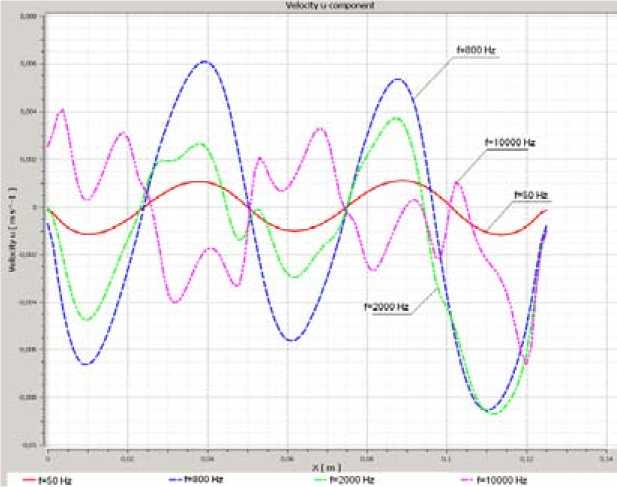
Fig.8 Dependence of the velocity V on the frequency f harmonic appears. Fig. 8 shows dependence Vx on the frequency, in the point: х =3/2h ; z≈0. Maximal value of the velocity is reached with the frequency f≈900 Hz, with a further increase of the frequency, the velocity first decreases and after changes a sign.
All the calculation have been carried out with a constant current value in the coils I = 5А. As it follows from the above calculations, the current frequency governs the pattern of the convectional streams and thus it can be called a governing parameter. Obviously we can govern the pattern of the convectional streams with the current value I on the inductor coils with constant frequency.
By an experimental investigation it was possible to prove existence of bowls at the inductor winding feeding with the currents of 50Hz to 800Hz frequency. At that a propeller with flat planes of stainless steel was inserted into the melt area, the propeller diameter is a few centimeters lower than h. A fine wire was welded to one of the vanes. The propeller was lowered under the oxide film of the molten gallium and the angle velocity was defined by the wire movement. The measurements of the velocity were approximate as the wire passing the oxide film experiences large resistance.
Together with that we registered change of the rotation direction for bowls and increase of the rotational speed with increase of frequency.
Thus by changing the current frequency of the inductor coil (governing the parameters) we can obtain a different structure of the convectional streams in the melt leading to effective stirring.
Conclusions
-
1. One of the main directions in updating the technology of alloy preparation is intensification of convectional heat-mass exchange in a melt. The most effective dynamics should embrace maximally possible set of hydrodynamic structures for the corresponding macroscopic and microscopic stirring along the whole bath volume.
-
2. Taking into account the melt characteristics, thermal strains, bath geometry we can design MHD-devices which will strengthen the effect of self-organization of dissipative structures by the influence of electromagnetic fields on the melt and will enable us to create energy-efficient castingmelting equipment.