Development and research of the innovative production technology of multifunctional invar alloys new generation
Автор: Chukin Mikhail V., Golubchik Eduard M., Koptseva Natalia V., Emova Yulia Yu., Chukin Dmitry M., Medvedeva Ekaterina M.
Журнал: Журнал Сибирского федерального университета. Серия: Техника и технологии @technologies-sfu
Статья в выпуске: 5 т.9, 2016 года.
Бесплатный доступ
Recently materials on the basis of multipurpose alloys with special mechanical and physical properties are widely adopted for creation of equipment of new generation. Such materials include Invar alloys with a minimum value of thermal expansion with high strength characteristics and hardness. Results of complex researches on influence of the modes of heat treatment on formation of structure are presented in article on the example of an alloy 32NUFM.
Multifunctional alloy, high-strength invar, heat treatment, hardness, microstructure
Короткий адрес: https://sciup.org/146115108
IDR: 146115108 | DOI: 10.17516/1999-494X-2016-9-5-744-749
Текст научной статьи Development and research of the innovative production technology of multifunctional invar alloys new generation
polished surface in a bath for identification of a microstructure. Microslices surfaces were investigated using an optical microscope at magnification of 50-1000 power with usage of the computer analysis system of images Thixomet PRO for detection of qualitative and quantitative structural features. The microstructure at magnification more than 1000X was investigated by the raster electronic microscopy (REM) in secondary and low-loss electrons by the scanning electronic microscope.
Microstructure of an alloy is presented in Fig. 1. It is an initial state before the heat treatment. Numerous nonmetallic inclusions were found on not etched metallographic section (Fig. 1 a ). Results of light microscopy of etched metallographic section showed that the alloy microstructure is the heterogeneous system consisting of grains of various size and particles of the second phase of various dispersion (Fig. 1 b ).
X-ray microanalysis was carried out for identification of the chemical elements which are a part of structural components of an alloy. Results are illustrated on the Fig. 2 and it shows that in the ranges received from a metal basis (matrix) of structure of an alloy 34NUFM peaks of Fe, Ni, and C, and also
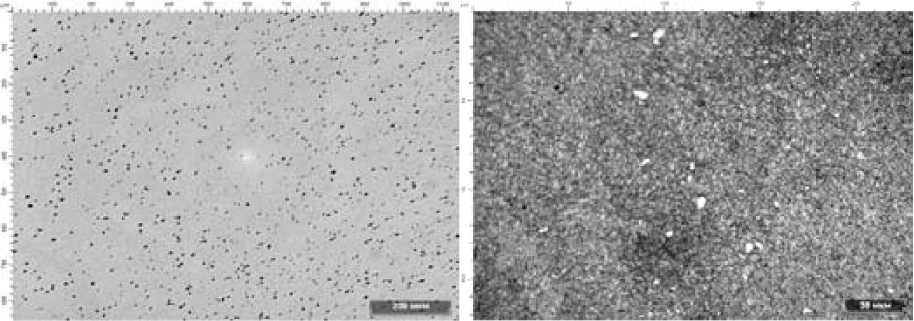
b
Fig. 1. Nonmetallic inclusions (a) and alloy microstructure (b) in an initial condition of an alloy 34NUFM: a – x 100; b – x 500
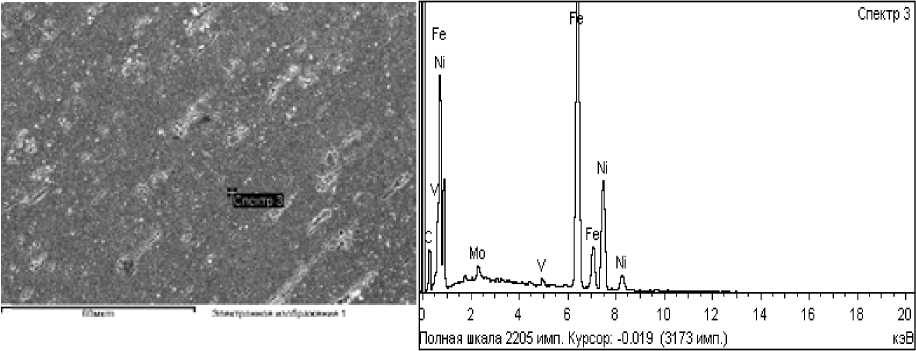
a b
Fig. 2. The electronic image of an alloy microstructure of 34NUFM (a) in an initial state and the characteristic range removed from a matrix (b)
Mo and V are found. It allows to identify an alloy matrix as the solid solution containing the specified elements.
Alloy 34NUFM was incurred to training from temperatures of 1200 and 1250 °C in water and oil. Distinctions in a microstructure of the tempered alloys were found. In case of training carried out from temperature of 1200 °C the structure is more uniform and the grain size is up to 30 microns (Fig. 3 a ) (during water cooling) and up to 40 microns (Fig. 3 b during oil cooling) that corresponds to grain No. 6-7. When training is carried out from temperature of 1250 °C the structure is non-uniform, distinction by the grain size is from 50 to 450 microns (Fig. 3 c ) (during water cooling) and from 40 to 450 microns (Fig. 3 d during oil cooling) that corresponds to grain from No. 6 to No. 1. The reason of such distinctions is growth of grain at increasing of heating temperature during training. Thus owing to fuller dissolution of carbide particles (which, as we know, curb grains growth) in separate microvolumes of structure more intensive growth of grain is observed. When training is carried out from 1200 °C carbides are dissolved to a lesser extent and they curb grains growth during heating before training, resulting in the grain is small. Samples of the studied alloy 34NUFM after training from temperatures of 1200 and 1250 °C in water and in oil were heated at temperatures: 300, 500, 600, 650, 700, and 800 °C, duration was 1 hour to provide disintegration of oversaturated γ-solid solution and to increase of strength characteristics.
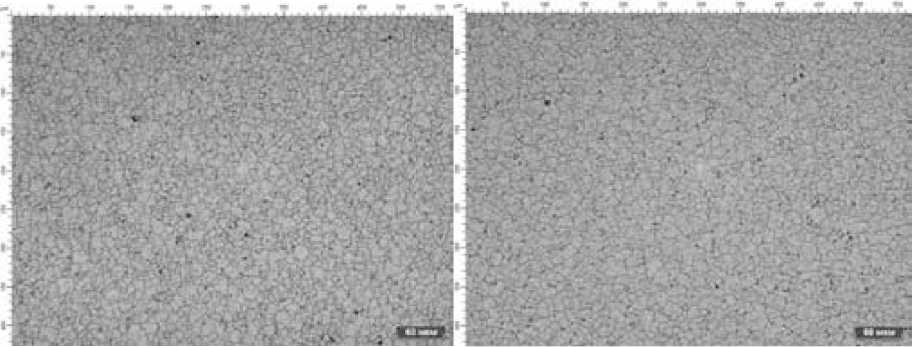
a b
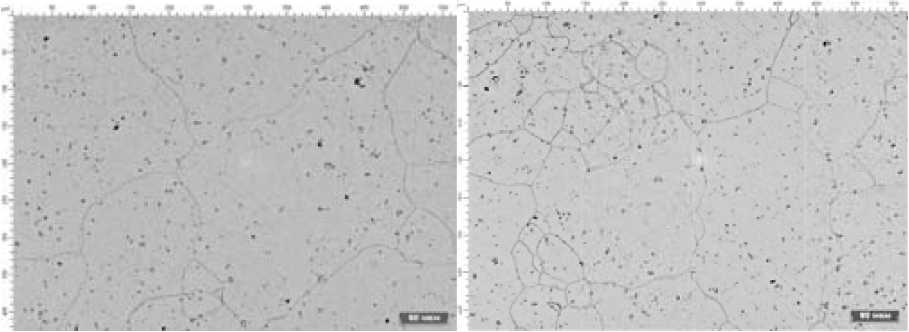
c d
Fig. 3. A general view of a microstructure of an alloy 34NUFM after training from 1200 °C (a, b) and 1250 °C (с, d) in water (a, c) and oil (b, d), x 200
The maximum of hardness is reached in the alloy tempered from temperature of 1200 °C in oil when heating were carried out in the range of temperatures of 600-700 °C. When training was carried out from the same temperature in water the maximum is reached when heating was up to 700 °C. Thus the maximum values of hardness are almost identical and these are 210-220 HV (21002200 MPa) (Fig. 4 a ).
When training is carried out from 1250 °C both in water and in oil hardness starts increasing already when heating temperature is 300 °C, and it increases most intensively when heating in the range of temperatures of 500 – 700 °C. Hardness reaches the maximum values when heating 700 °C and after training both in water and in oil. It should be noted that hardness of the alloy tempered in water after heating up to 700 °C is about 300 HV (~ 3000 MPa), and hardness of the alloy tempered in oil is only about 280 HV (~ 2800 MPa) (Fig. 4 b ).
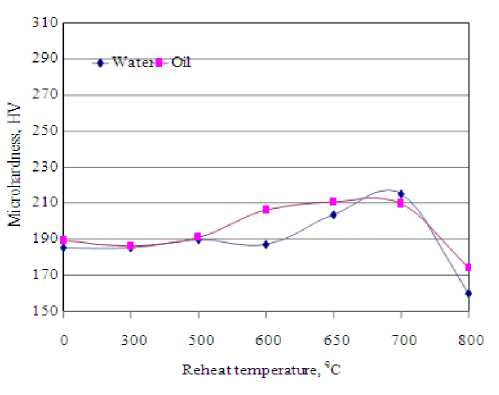
a
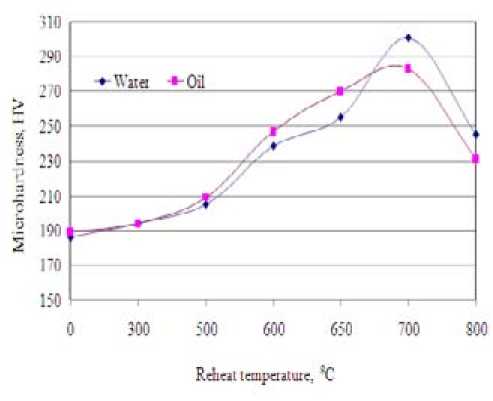
b
Fig. 4. Change of microhardness of the tempered alloy 34NUFM from temperature of the subsequent heating
Conclusions
-
1. The researches results showed that in case of heating an invar alloy of type 34NUFM before training the dissolution of part of carbide phases inclusions is provided and the solid solution is saturated with carbon and alloying elements. When heating temperature before training increases up to 1250° C, the fuller dissolution of carbides happens. During the training in oil the part of the dissolved carbides is precipitated, as a result the samples tempered in oil have higher hardness than alloys cooled in water.
-
2. During the increasing of the tempered alloys heating temperature the hardness at first increases, reaching a maximum that is connected with the strengthening particles precipitation. After achieved of the maximum value, hardness starts decreasing that can occur owing to the coagulation of precipitated particles. The maximum content of the strengthening phase in the tempered samples is observed after heating at 600-650 °C. The X-ray microanalysis showed that the precipitated strengthening phase includes the difficult carbides containing carbide-forming element: molybdenum and vanadium, and also may contains the titan used as a part of the deoxidating mixes during smelting an alloy of the specified structure.
Список литературы Development and research of the innovative production technology of multifunctional invar alloys new generation
- Чукин М.В., Голубчик Э.М., Кузнецова А.С. и др. Разработка композиций многофункциональных сплавов инварного класса с расширенными эксплуатационными характеристиками. Вестник Магнитогорского государственного технического университета им. Г.И. Носова, 2013, 3, 62-66
- Копцева Н.В., Голубчик Э.М., Ефимова Ю.Ю. и др. Особенности формирования комплекса физико-механических свойств в высокопрочных инварных сплавах. Сталь, 2014, 4, 97-99
- Чукин М.В., Голубчик Э.М., Гун Г.С. и др. Исследование физико-механических свойств и структуры высокопрочных многофункциональных сплавов инварного класса нового поколения. Вестник Магнитогорского государственного технического университета им. Г.И. Носова, 2014, 1, 43-47
- Чукин М.В., Копцева Н.В., Голубчик Э.М., Чукин Д.М., Медведева Е.М. Исследование режимов термической обработки при производстве высокопрочных инварных сплавов нового поколения. Металлург, 2014, 4, 97-101