Development calculation methods of technological parameters for receipt deformed semi-finished products of gold based alloys of probe 585
Автор: Sidelnikov Sergey B., Dovjhenko Nikolay N., Lebedeva Olga S., Belyaev Sergey V., Gailis Julia D., Feskov Evgeniy V.
Журнал: Журнал Сибирского федерального университета. Серия: Техника и технологии @technologies-sfu
Статья в выпуске: 6 т.5, 2012 года.
Бесплатный доступ
Developed algorithms, software, and calculation methods of deformation regimes and power parameters for cold bar rolling and drawing of rods and wires of gold alloys 585 standard. Obtain a formula for the calculation of the contact area during rolling in calibers similar in form to the rhombic. Presented the results of analysis factory regimes and proposed new routes of rolling and drawing, which have passed tested to obtain commercial pilot batches of jewelry chains.
Golden alloys, rolling, drawing, mechanical properties, deformation regimes, stress, contact area, tension
Короткий адрес: https://sciup.org/146114686
IDR: 146114686
Текст научной статьи Development calculation methods of technological parameters for receipt deformed semi-finished products of gold based alloys of probe 585
Development of technologies for implementation of new alloy compositions based on precious metals, alloyed with elements that improve their properties, on one side caused by expansion of the range of jewelry, associated with an increase in the color palette and the sophistication of the elements, that constitutes the entire finished product, on the other side - higher quality requirements. Actual also is the reduction of the harmful effects on human health of some metal-allergens included in the standard alloys. Perspective in this regard are alloys of gold 585 standard includes a small addition of ruthenium, rhodium, indium (as a modifier), provide a uniform fine-grained structure, increasing the level of mechanical properties and allowing to produce jewelry production by casting and metal forming [1].
Determining factors to get a quality finished jewelry products are technological regimes and power parameters for bar rolling mills type Famor TL12T and BILER mark INVIMEC [2] and technological parameters and kinematic characteristics of the process of drawing on the mill type 10NFS COMEVI [3]. In this case, great practical importance when designing technology of production the deformed semi-finished products have theoretical and experimental studies of
relationship of strength and plastic properties of the technological parameters of processing. This knowledge will make it possible not only to determine the power parameters of bar rolling and drawing of precious metals and alloys, but also carry out checks on allowable force used for this equipment. To identify technology and power parameters of production and analysis of factory modes production of deformed semi-finished products created algorithms and methods, including automated analysis of deformation modes and effort profiled cold bar rolling and drawing using rheological characteristics of the processed alloy.
In the process of industrial research new gold alloy 585 standard red color, held in Krasnoyarsk Facility of Non-Ferrous Metals named after Gulidov («Krastsvetmet» JSC.), provided data on the mechanical properties, based on which received the empirical relationships for determining the values of the ultimate tensile strength (σв) and yield strength (σ0,2) for these alloys, where the maximum amount of deformation reaches 95%.
σв = aε 2 + bε + c и σ0,2 = aε2 + bε + c, where a, b, c – dimensionless coefficients characterizing the properties of the new alloys (Table 1).
For prior calculations deformation regimes of bar rolling and drawing has been applied program «PROVOL», created in the programming environment Delphi, Borland Corporation product, which is designed for operating systems Windows, GNU/Linux, Mac OS X and Windows CE.
The general structure of the program represents the following sequence: unit selection calculation, input source data; presentation of calculations in the form of tables and graphs.
The algorithm of the program includes the initial data, calculation of the geometric dimensions of the processed metal, calculation mode of breakdowns by the aisles and definition power parameters, in this case uses the methodology for determining the technological regimes rolling and drawing given in refs [3,4].
As the initial information the program includes database for equipment and alloys (Fig. 1). The database is designed to store and retrieve data, presenting information in a convenient form and automate repetitive tasks. To create a database used program products Access that allows you to develop a simple and easy data entry form, and perform data processing and delivery of complex reports.
As the output data the program generates a table of results (Fig. 2) and diagrams of dependences calculated process parameters on the number of passes.
To solve the complex problem of determining power parameters for cold bar rolling of a new gold alloy 585 standard conducted research in the laboratory for profiled two-stand rolling mill type model AMBIFILO VELOCE ROSEN 180+200ר130 of Italian company Mario Di Maio. Technical characteristics of the equipment are shown in Table 2.
Table 1. Coefficient to determine the strength characteristics of gold alloys 585 standard red color
Mark of alloy |
Mechanical properties |
Dimensionless coefficients |
||
a |
b |
c |
||
Red gold |
σ в |
-0,001082 |
1,7356 |
446,8 |
σ 0,2 |
-0,0125 |
3,6301 |
217,29 |
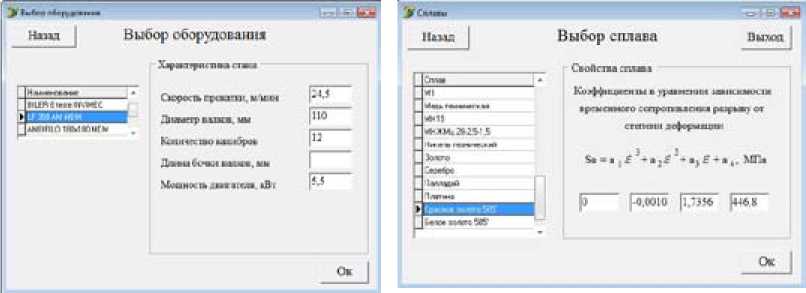
a
b
Fig. 1. Program window to calculate the parameters of bar rolling when selecting equipment (a) and alloy (b)
Table 2. Technical characteristics of section mill two-stand model
Name of the parameter |
The parameter value of the mill |
Engines power, kW |
4,8-7,5 and 0,25 |
The three-phase supply voltage, V |
380 |
The maximum torque rolling, kgm |
136 |
Rolling speed, m/min |
12,5+26 |
Length of barrel rolls, mm |
200+180 |
Roll diameter, mm |
130 |
Number of calibers |
50 |
Overall dimensions, mm |
1700×1320×1450 |
For obtain an accurate geometric model of the deformation zone in calibers close in shape to a rhomboid, rolled samples depicted in scale 1:1 using program AutoCAD, and then using vector graphics have led to specific form (Fig. 3). This allowed finding length of the metal contact and the contact area of the deformed metal with rolls with high accuracy (Fig. 4).
On the basis of these data was obtained empirical formula to determine the area of contact metal with rolls in calibers at cold bar rolling.
Fcont = 19,178 • e (0’2612'x), where х – size by the caliber, mm.
Using data obtained with the help of the developed software to performed calculations to determine the power parameters for the following factory processing. Rolling initial ingot diameter of 10 mm was carried out in three stages. In the first phase rolling led to the mill Famor TL 12T in calibers to the size of a square cross-section bars 3,7×3,7 mm. Then - on mills type BILER in two mills to size accordingly 2,1×2,1 mm и 1,1×1,1 mm. The calculated power parameters of rolling of a new alloy are presented in Table 3. Change efforts rolling through the aisles in Fig. 5.
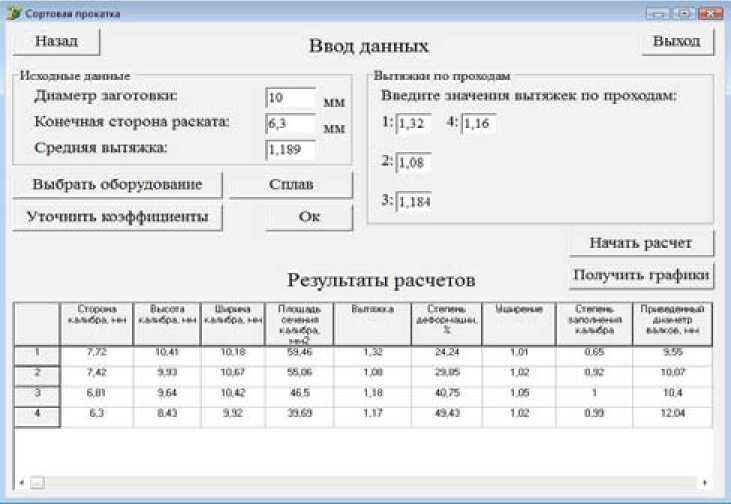
a
Jf Вопоменне лроеопсеи га1 в |
||||||||||
Назад |
Ввод данных ULno-’1 |
|||||||||
госяитг исиожыс _ Начальный диаметр К*4 мм Конечный диаметр 1^^ мм Средняя вытяжка Кэ® мм |
। [иГ 2 [иГ з- |ТлГ 4 [мГ 5- |иГ 6 |1J5 т |и$ 8 |1.Я 9 ||,31 Ifr |1Д5 |
|||||||||
Выбор оборудования Сплав | |
ьтаты расчетов |
Начать расчет |
||||||||
Ок Резул |
Получить графики |
|||||||||
Диаметр |
Выт<*>* |
Crew дефосмеиад * |
“Юр! eft* вопемем* ЧП. |
У Сиаде К1ХХНЛ «И |
Ди>-*-р >*Vt. !-' |
коросту прсеоож |
r_»OpOCTV иийбы м/с |
|||
1 |
1515 1 |
1.47 147 |
32.43 |
®Я |
102 |
356 99 |
00 |
ом |
||
2 |
0.837 |
54 34 |
430 1 9 |
102 |
241.46 |
09 99 |
0.08 |
0.97 |
||
1 |
0.630 |
143 |
6023 |
413j60 |
100 |
158.3 |
101.99 |
012 |
0.42 |
|
4 |
0.507 |
14 |
7751 |
395 47 |
1.13 |
107 33 |
116 |
018 |
040 |
|
5 |
0 490 |
IX |
взяе |
Х34 |
1.16 |
74 И |
IX |
025 |
054 |
|
6 |
0429 |
1.Х |
9601 |
3592 |
124 |
51 X |
146.Ю |
0.33 |
061 |
|
7 |
0 3G3 |
1Х |
91.12 |
35925 |
124 |
X4D |
IG6 |
0.45 |
069 |
|
9 |
0319 |
134 |
9337 |
35323 |
126 |
Х24 |
IX |
061 |
О.Х |
|
э |
02?Й |
1^1 |
ММ |
11507 |
,Л |
20 44 |
211.99 |
П.8 |
0W |
|
10 |
0.249 |
124 |
9593 |
2М78 |
1J# |
14 46 |
23999 |
1 |
1 |
|
b
Fig.2. Examples of calculation deformation regimes of rolling (a) and drawing (b)
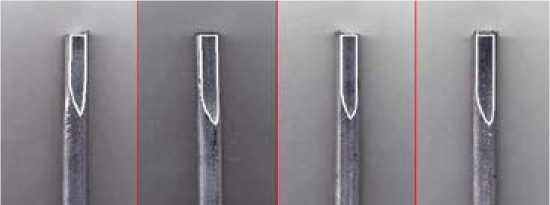
Fig. 3. Contact area of the deformed samples after rolling
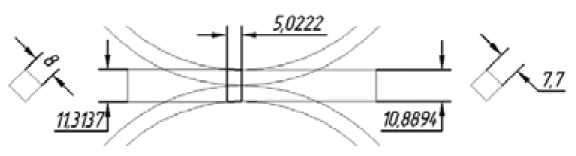
Fig. 4. Scheme to determine the length of the contact metal with rolls
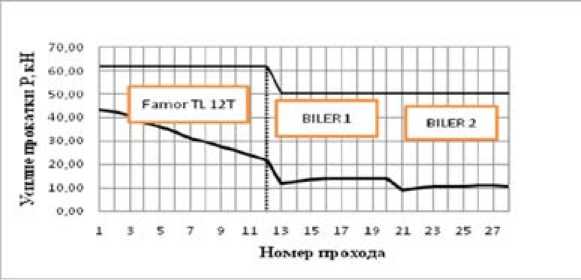
Fig. 5. Change efforts rolling through the aisles
The calculation showed that the values of effort does not exceed allowable (Fig. 5), as allowable force mill Famor TL 12T was 61.7 kN, and rolling mill type BILER – 50,3 kN.
The final stage to get the wire is drawing process on the mill type 10NFS COMEVI, which was carried out the following route: 1,1-1,00-0,90-0,80-0,70-0,60-0,50-0,45-0,35-0,30-0,25 mm. The calculation results are shown in Table 4.
To analyze the indicators of power parameters the process of drawing calculated voltage wire drawing and the safety factor. The analysis showed that for the new alloy to its mechanical properties, used in the factory route drawing is not rational. The reason is that in the first pass, the value of the safety factor below the permissible value γr =1,4, which suggests the possibility of wire breakage.
Graphical representation of stress changes drawing is shown in Fig. 6.
As seen from the above presented depending, distribution voltages wire drawing unevenly through the aisles, reaching peak levels at 1, 6 and 11 aisles, it can also lead to a wire breaks of thin sections.
Table 3. Bar rolling process parameters
№ of aisles |
F, mm2 |
ε sum, % |
F К, mm2 |
σ Т, MPa |
Р, kN |
rolling on the mill Famor |
|||||
1 |
62,41 |
20 |
150,99 |
286,44 |
43,25 |
2 |
57,76 |
26 |
139,61 |
304,47 |
42,51 |
3 |
51,84 |
34 |
125,76 |
326,16 |
41,02 |
4 |
43,56 |
45 |
107,52 |
354,10 |
38,07 |
5 |
38,44 |
51 |
96,85 |
369,99 |
35,83 |
6 |
34,81 |
56 |
89,55 |
380,61 |
34,08 |
7 |
29,16 |
63 |
78,59 |
396,07 |
31,13 |
8 |
26,01 |
67 |
72,67 |
404,13 |
29,37 |
9 |
23,04 |
71 |
67,19 |
411,36 |
27,64 |
10 |
20,25 |
74 |
62,13 |
417,83 |
25,96 |
11 |
16,81 |
79 |
55,96 |
425,37 |
23,80 |
12 |
13,69 |
83 |
50,41 |
431,79 |
21,77 |
rolling on the mill BILER №1 |
|||||
1 |
12,96 |
5 |
49,11 |
236,29 |
11,60 |
2 |
11,56 |
16 |
46,61 |
270,74 |
12,62 |
3 |
10,24 |
25 |
44,24 |
300,83 |
13,31 |
4 |
9,00 |
34 |
41,99 |
326,98 |
13,73 |
5 |
7,29 |
47 |
38,82 |
359,68 |
13,96 |
6 |
6,25 |
54 |
36,85 |
377,65 |
13,92 |
7 |
5,29 |
61 |
34,97 |
392,97 |
13,74 |
8 |
4,84 |
65 |
34,07 |
399,72 |
13,62 |
rolling on the mill BILER №2 |
|||||
1 |
4,00 |
17 |
32,34 |
276,53 |
11,60 |
2 |
3,24 |
33 |
30,69 |
323,63 |
12,62 |
3 |
2,56 |
47 |
29,13 |
360,56 |
13,31 |
4 |
2,25 |
54 |
28,38 |
375,75 |
13,73 |
5 |
1,96 |
60 |
27,64 |
389,04 |
13,96 |
6 |
1,69 |
65 |
26,93 |
400,60 |
13,92 |
7 |
1,44 |
70 |
26,24 |
410,61 |
13,74 |
8 |
1,21 |
75 |
25,56 |
419,24 |
13,62 |
To eliminate detected flaws designed new modes of drawing: using a wire drawing machine, used in factory conditions (Fig. 2), and tougher of drawing regime 1,1-0,82-0,67-0,55-0,45-0,37-0,30-0,25 mm, which provides smooth change of extracts coefficients through the aisles (Fig. 7) and lower stress values at the end of the process of drawing (Fig. 8).
Developed modes of drawing are characterized by a uniform distribution of the deformation characteristics, have high safety margins, which positively affected on the implementation of the drawing process.
Table 4. Drawing process parameters
№ of aisles |
d i , mm |
F, mm2 |
ε sum, % |
σ В, MPa |
Р В , N |
К В , MPa |
γ r |
1 |
1,00 |
0,7850 |
35 |
506,16 |
317,93 |
405,01 |
1,25 |
2 |
0,90 |
0,6359 |
47 |
526,51 |
114,62 |
180,27 |
2,92 |
3 |
0,80 |
0,5024 |
58 |
544,43 |
106,36 |
211,70 |
2,57 |
4 |
0,70 |
0,3847 |
68 |
560,03 |
96,78 |
251,61 |
2,23 |
5 |
0,60 |
0,2826 |
77 |
573,38 |
86,08 |
304,59 |
1,88 |
6 |
0,50 |
0,1963 |
84 |
584,55 |
74,41 |
379,16 |
1,54 |
7 |
0,45 |
0,1590 |
87 |
589,34 |
32,57 |
204,92 |
2,88 |
8 |
0,40 |
0,1256 |
90 |
593,61 |
29,37 |
233,85 |
2,54 |
9 |
0,35 |
0,0962 |
92 |
597,37 |
26,09 |
271,33 |
2,20 |
10 |
0,30 |
0,0707 |
94 |
600,61 |
22,75 |
321,94 |
1,87 |
11 |
0,25 |
0,0491 |
96 |
603,35 |
19,34 |
394,23 |
1,53 |
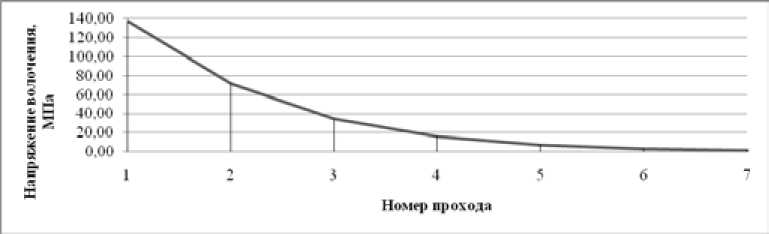
Fig. 8. Stress distribution of drawing through the aisles
On technology developed by «Krastsvetmet» JSC experimental batches of jewelry chains were manufactured, thus as a result of tests yield increased by 2-10%, depending on the diameter of the produced wire.
Thus, the results of research:
-
– the modeling process of bar rolling in calibers was carried out, which allowed to obtain the calculation depending to the area of contact metal with the rolls on the bar rolling mill and to calculate the power parameters of the process;
-
– proposed a method and created software, allows you to quickly calculate the deformation modes and power parameters of processing;
-
– analyzed deformation modes used for bar rolling and drawing in Krasnoyarsk Facility of NonFerrous Metals;
-
– proposed and verified regimes of rolling and drawing for new gold alloys 585 standard and obtained experimental batches of high quality products.