Диагностирование как способ получения информации о техническом состоянии сельскохозяйственных машин и повышения их надёжности
Автор: Фомичв Е.В., Ревякин М.М.
Журнал: Агротехника и энергообеспечение @agrotech-orel
Рубрика: Технический сервис в агропромышленном комплексе
Статья в выпуске: 1 (1), 2014 года.
Бесплатный доступ
В статье исследован процесс диагностирования машин агропромышленного комплекса в сравнении с субъективными методами определения их технического состояния. Обосновано применение диагностирования в процессе определения технического состояния машинно-тракторного парка.
Диагностирование, контроль, информация, техническое состояние, параметр
Короткий адрес: https://sciup.org/14769931
IDR: 14769931
Текст научной статьи Диагностирование как способ получения информации о техническом состоянии сельскохозяйственных машин и повышения их надёжности
В статье исследован процесс диагностирования машин агропромышленного комплекса в сравнении с субъективными методами определения их технического состояния. Обосновано применение диагностирования в процессе определения технического состояния машинно-тракторного парка.
The article studied the process of diagnosing machines of agroindustrial complex in comparison with subjective methods to determine their technical condition. The application of the diagnosis in the process of defining the technical state of the machines and tractors.
Для формулировки эффективных решений по оперативному управлению производственными процессами технической эксплуатации машинно-тракторного парка (МТП) возникает необходимость использования достоверной информации о техническом состоянии каждого отдельно взятого объекта. Как известно, базовыми источниками информации такого рода являются технический контроль, включающий в себя осмотр и инструментальное диагностирование.
На начальном этапе развития специфика производственных процессов технической эксплуатации крайне неоднородных по своему составу объектов определила возможность применения в основном субъективных методов определения технического состояния. Однако, впоследствии, с усложнением процесса управления работоспособностью МТП, требования к индивидуальной информации значительно повысились, что послужило толчком для возникновения и развития технической диагностики, как отрасли, исследующей технические состояния объектов, их проявления, разрабатывающей методы их определения, а также принципы построения и организацию использования систем диагностирования. Перечень задач, решаемых с помощью диагностирования, также расширился: от элемента технологического процесса ТО и ремонта до одной из подсистем информационного обеспечения надежности.
Диагностирование представляет собой более совершенную форму проведения контрольных работ. Основными преимуществами процесса диагностирования является объективность и достоверность оценки технического состояния, что достигается применением инструментальных методов проверки; возможность определения выходных параметров
(параметры эффективности) агрегатов и систем сельскохозяйственных машин (мощность, топливная экономичность и др.); наличие условий для повышения надежности и организованности функционирования системы ТО и ремонта за счет более эффективного оперативного управления. [4]
Потребность наличия достоверной и объективной информации, получение которой возможно с применением инструментальных методов контроля, объясняется с точки зрения усложнения машин и стремления обеспечить поддержание ее работоспособности в условиях низкой обеспеченности квалифицированными кадрами. Современные комплектующие с одной стороны обеспечивают высокую эффективность применения ТС, а с другой – резко усложняют организацию ТО и ремонта и требуют создания прогрессивных методов их технической эксплуатации, в том числе и методов технического диагностирования.
Информация о техническом состоянии машин в АПК, формируемая механиками, на 76 % состоит из описаний внешних проявлений неисправностей. Данная информация имеет достаточно высокую (до 96 %) достоверность, но обладает низким качеством, так как содержит до 40 % неоднозначных сведений, когда одному внешнему проявлению может соответствовать несколько возможных неисправностей, требующих для их устранения проведение различных операций ТО и ремонта и, как следствие, разной подготовки производства. Применение диагностирования позволяет повысить надежность и эффективность работы технической службы путем уточнения и локализации неисправностей в случае неоднозначности информации и принятия на этой основе обоснованных решений, что значительно снижает простои на ТО и ремонт и повышает качество их проведения. Применение средств диагностики снижает затраты на ТО и текущий ремонт (ТР) на 5 %, расход запасных деталей и материалов – на 10 %, топлива и шин – на 20 %. Например, контроль момента зажигания повышает мощность двигателей автомобилей ГАЗ и ЗиЛ на 10 – 12 %. Срок окупаемости средств диагностики на предприятии с парком в 500 – 600 единиц техники составляет около года.
Получение достоверной и объективной информации о состоянии объектов различных моделей вполне реально, учитывая современный технический прогресс. Нельзя не отметить рост электронизации техники, появление простейших эле ментов 358
бортовой диагностики, а также пакетов программ типа Bosch [ESI]tronic, предоставляющий новейшую информацию о диагностике, поиске неисправностей, обслуживании и ремонте.
Для оценки технического состояния объекта необходимо определить текущее значение структурного параметра и сопоставить его значение с нормативным. Но без разборки агрегата или узла оценить значение структурного параметра в большинстве случаев невозможно. К тому же, проведение сборочно-разборочных работ приводит к нарушению взаимного положения приработавшихся деталей, что приводит к сокращению остаточного ресурса на 30 – 40 %. Поэтому при диагностировании о значениях структурных параметров судят по косвенным диагностическим признакам, качественной мерой которых являются диагностические параметры. Между структурными ( S ) и диагностическими ( D ) параметрами в зависимости от сложности машины могут иметь место различные взаимосвязи (рисунок 1). [1]

единич ная множест в енна я нео пред еленна я ком бинир ованн ая
Рисунок 1 – Взаимосвязь между структурными и диагностическими параметрами
При определении возможного набора диагностических параметров и выбора из множества наиболее удобных для использования часто применяют структурно-следственные схемы узла, которые представляют собой графическую модель, увязывающую в комплекс основные элементы механизма, характеризующие их структурные параметры, перечень характерных неисправностей, подлежащих выявлению, а также набор возможных для использования диагностических параметров. Список характерных неисправностей механизма определяется на основе статистических оценок показателей его надежности.
Характер изменения значения диагностического параметра обусловлен изменением значения структурного параметра. Аналогично структурным они имеют различную значимость и обычно определяют техническое состояние узла, агрегата, системы сельскохозяйственной машины комплексно. При фиксировании диагностических параметров, как правило, регистрируются помехи, что объясняется конструктивными особенностями диагностируемого объекта (комплексный фактор) и избирательными способностями и точностью диагностического оборудования (единичный фактор). Это значительно затрудняет постановку диагноза и снижает степень его достоверности. Поэтому важным моментом является отбор из выявленной базовой совокупности наиболее значимых и эффективных в использовании диагностических параметров.
Комплексный процесс технического диагностирования включает в себя следующие элементы: обеспечение функционирования объекта на заданных режимах или тестовое воздействие на объект; фиксация и преобразование сигналов, выражающих значение диагностического параметра, его измерение; постановка диагноза на основании логической обработки полученной информации и сопоставление ее с нормативными показателями. Структурная схема процесса диагностирования показана на рисунке 2.
У объекта диагностирования, выведенного на заданный режим, с помощью датчика первичной фиксации воспринимается сигнал, отражающий диагностический параметр D , характеризующий также значение структурного параметра. Далее сигнал в трансформированном виде D ' поступает на измерительное устройство, а затем количественное значение диагностического параметра D выдается устройством отображения данных.
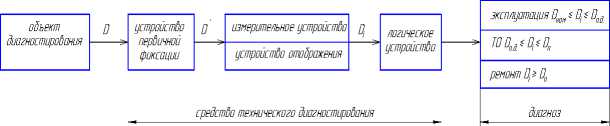
Рисунок 2 – Схема процесса технического диагностирования
В многокомпонентных автоматических средствах технического диагностирования с помощью специального логического устройства на базе процессора выполняется постановка диагноза, и выдаются конкретные рекомендации.
Учитывая задачи диагностирования, а также сложность современных машин, диагноз может отличаться по глубине. Для оценки работоспособности агрегата, системы или единицы техники в целом используются выходные параметры постановки диагноза уровня «годен», «не годен». Для определения потребности в ремонте необходим более глубокий диагноз, основанный на локализации конкретной неисправности. [2]
При постановке диагноза для сложной системы, когда при поиске неисправности используется несколько диагностических параметров, необходимо на основе данных о надежности объекта идентифицировать причинно-следственные связи между его наиболее вероятными неисправностями и используемыми диагностическими параметрами. Для этого при диагностировании целесообразно применение диагностических матриц – логических моделей, описывающих связи между диагностическими параметрами и возможными неисправностями объекта. [3]
Диагностические матрицы являются неотъемлемой составляющей автоматизированных логических устройств, применяемых в средствах технического диагностирования.
Список литературы Диагностирование как способ получения информации о техническом состоянии сельскохозяйственных машин и повышения их надёжности
- Глухов А. Д. Диагнозоспособность, функция связности и спектр графа /А. Д. Глухов//Электронное моделирование. -1995. -№2. -с. 92 -94.
- Ревякин М.М. Предпосылки формирования систем оперативной диагностики мобильных энергетических средств /М.М. Ревякин, А.А. Жосан//Инновационное развитие аграрного сектора экономики: взгляд молодых ученых: Сб. материалов Международной научно-практической конференции, декабрь 2009. -Курск: КГСХА, 2010. -278 с. -С. 267-271. -ISBN 978-5-7369-0685-7.
- Рейман А. Г. Интегрируемые системы. Теоретико-групповой подход /А. Г. Рейман, М. А. Семенов-Тян-Шанский. -М-Ижевск.: Институт компьютерных исследований. -2003. -352 с.
- Ульман И. Е. Техническое обслуживание и ремонт машин /И. Е. Ульман. -М.: Агропромиздат. -1990. -283 с.