Диагностирование оборудования с использованием параметров технологического контроля
Автор: Минаков А.А., Федосеев Д.В.
Журнал: Известия Самарского научного центра Российской академии наук @izvestiya-ssc
Рубрика: Механика и промышленность
Статья в выпуске: 5-2 т.11, 2009 года.
Бесплатный доступ
В статье показана возможность определения технического состояния объекта на основе анализа информации о технологических режимах его работы. Рассмотрен метод диагностирования, включающий несколько этапов: формирование нормального состояния, формирование матрицы диагностических признаков, поиск неисправностей; и позволяющий предотвратить аварию или существенно уменьшить ее последствия. Описанная методика прошла успешную опытную эксплуатацию на установках БОР-60 и БН- 600 АЭС.
Диагностика, технологические параметры
Короткий адрес: https://sciup.org/148198730
IDR: 148198730
Текст научной статьи Диагностирование оборудования с использованием параметров технологического контроля
сбора и обработки информации сущест-венно расширяют как возможности оператора по определению неисправностей, так и позволяют автоматизировать сам процесс их определения, т.е. диагностирование. Для этого необходимо иметь методику и соответствующие ей алгоритмы диагностирования, использующие информацию от датчиков технологического контроля. Такого рода методики, алгоритмы и реализующие их программнотехнические комплексы (ПТК) разрабатываются уже несколько десятилетий [1-3]. Реализованные ПТК основывались на создании перечней (словарей) неисправностей (состояний) конкретного оборудования, в которых каждому состоянию ставились в соответствие определенные изменения наблюдаемых параметров или комплексных характеристик, получаемых (вычисляемых) из этих параметров [1]. Определяемые состояния вносились в перечень как исходя из опыта эксплуатации, так из анализа конструкции оборудования и протекающих в них процессов, как в нормальном, так и в аномальных состояниях.
Диагностирование – это выявление и анализ отклонений от нормального состояния. Основное состояние, которое вносится в перечень в явном или неявном виде – это нормальное состояние [1]. Даже если в словаре состояний только 2 состояния – нормальное и аномальное – это уже основа для системы диагностирования. Определение состояния в процессе функционирования объекта – функциональное диагностирование, осуществляемое пассивными методами, т.е. методами, не требующими дополнительного воздействия на объект [3].
Составление словаря состояния. В словаре состояний каждому состоянию D j
(j=0,...m , где m - количество состояний в словаре) поставлено в соответствие своя совокупность признаков диагностирования. В общем случае в этот словарь входит и нормальное состояние j=0 . Признак диагностирования - это факт выхода за уставку измеряемого параметра или наличие / отсутствие какого-либо дискретного параметра. В табл. 1 показан пример словаря состояний теплообменника, технологическая схема которого приведена на рис. 1. Приведенный словарь состояний абстрактного теплообменника в реальных условиях может иметь существенные отличия, определяемые конструкцией и технологией, тем не менее он показывает логику поиска неисправностей (определение состояния) при измерении всех технологических параметров, определяющих как режим работы теплообменника, так и характеризующие его состояния.
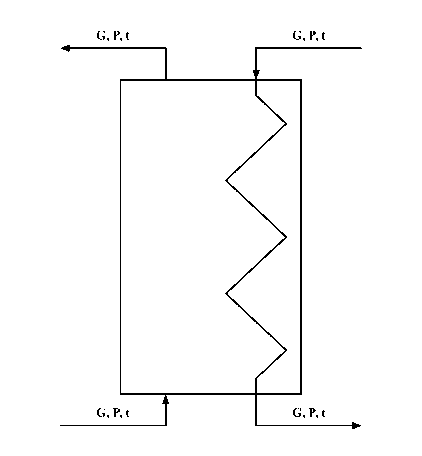
Р ис. 1. Схема теплообменника G ^iвых ) ,
Г) ВХ ( ВЫХ ) вХ ( ( ВЫХ )
P12 , 11,2 - расход, давление, температура теплоносителей соответственно на входе и выходе по каждой стороне поверхности теплообмена;
сторона 1 - греющая
Таблица 1. Словарь состояния теплообменника
Параметр |
Х 1 =G 1вх |
Х 2 =Р 1вх |
Х 3 =t 1вх |
вых Х 4 =G 1 |
Х =Р вых |
вых Х 6 =t 1 |
нормальное |
0 |
0 |
0 |
0 |
0 |
0 |
отложения на стороне 1 |
X 1 1 |
X 2 t |
0 |
X 4 1 |
X 5 1 |
X 6 1 |
отложения на стороне 2 |
0 |
0 |
0 |
0 |
0 |
Х б t |
течь через поверхность теплообмена со стороны 1 |
X 1 t |
X 2 I |
0 |
X 4 1 |
X 5 1 |
0 |
Параметр |
Х 7 =G 2вх |
Х 8 =Р 2вх |
Х 9 =t 2вх |
вых Х 10 =G 1 |
вых Х 11 =Р 2 |
вых Х 12 =t 2 |
нормальное |
0 |
0 |
0 |
0 |
0 |
0 |
отложения на стороне 1 |
0 |
0 |
0 |
0 |
0 |
X 12 1 |
отложения на стороне 2 |
X 7 1 |
X 8 t |
0 |
X 10 1 |
X 11 1 |
X 12 1 |
течь через поверхность теплообмена со стороны 1 |
0 |
0 |
0 |
X 10 t |
X 11 1 |
X 12 1 |
Примечание: 0 - параметр не вышел за границы нормального состояния; t1 - направление выхода за границу нормального состояния (вверх, вниз).
Современный уровень развития информационных технологий позволяет разработать универсальную методику диагностирования и реализовать ее алгоритмы и программы использования параметров технологического контроля для автоматического диагностирования промышленного оборудования различного типа.
Методика диагностирования с использованием параметров технологического контроля
Методика включает в себя несколько этапов:
-
- формирование нормального состояния;
-
- формирование матрицы диагностических признаков;
-
- поиск неисправностей (аномалий).
Основные допущения:
-
- рассматривается стационарное состояние объекта;
-
- перечень (словарь) состояний считается конечным и уже сформированным.
Формирование (подготовка) нормального состояния. Блок-схема подготовки нормального состояния показана на рис. 2. Работа любой автоматизированной системы контроля начинается с измерения параметров P i ,(i=1,…n). В общем случае измеряются не только технологические параметры, но и специальные (вибрация, концентрация вредных веществ, радиоактивность выбросов и т.п.). Каждый измеряемый параметр может рассматриваться как диагностический, но для более эффективного определения состояния объекта определяются также некоторые комплексные характеристики объекта, вычисляемые из измеряемых параметров X j (j=1,…m, где X j – функция от некоторого количества параметров P i ). Это может быть мощность, количество тепла, перепад давления, масса и т.п. Перечень определяется на начальной стадии работы по созданию ПТК в соответствии с технологической схемой, конструкцией, имеющимся опытом эксплуатации, анализом безопасности объекта [1].
Окончательный перечень диагностических параметров состоит из вычисленных характеристик и измеренных параметров d k {X j ,P i } ( k=1,...l , где l – количество диагностических параметров). В ряде частных случаев, множество вычисленных характеристик может быть и пустым, т.е. m=0 , тогда l=n . Таким образом, блок подготовки диагностических параметров может включать в себя подпрограмму вычисления комплексных характеристик, которая является специфической для каждого объекта диагностирования, но может и не иметь этой подпрограммы. Обязательной частью этого блока является выделение режимных параметров (характеристик), определяющих стационарное состояние. Чаще всего это один из измеряемых или вычисляемых параметров (мощность, расход, давление и (или) температура и т.п.), определяющие технологический режим работы объекта. Иногда это может быть и 2 или более параметров, но их число всегда очень ограничено.
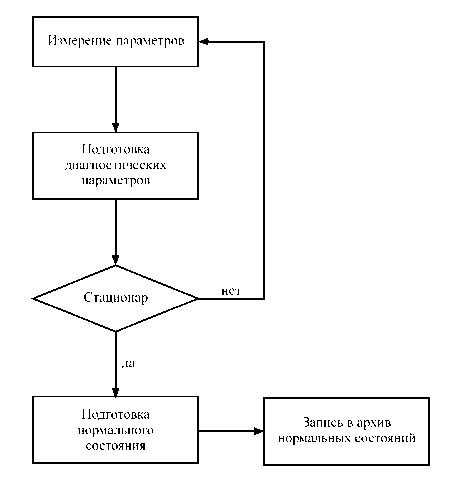
Рис. 2. Блок-схема подготовки нормального состояния
Критерием стационарности является отклонение режимного параметра d k0 за время t 0 на величину больше Δ d k0 . Если условие стационарности выполняется, то считается, что объект находится в нормальном состоянии и происходит подготовка (формальное определение) нормального состояния. Для всего массива d k определяются математические ожидания М к и среднеквадратические отклонения δ k . Количество точек измерения для определения M k и δ k выбирается с учетом времени опроса, исходя из критериев представительности выборки и общего времени определения (желательно не более 5 минут). Обычно это делается за время, близкое к t 0 . После определения выбираются границы нормального состояния Δ d k = a δ k , где a= (3-5). Величина a , в общем случае, выбирается из 2 противоречащих друг другу соображений: - исключение случайного выхода за границу нормального состояния;
-
- желание определить выход за границу нормального состояния как можно на более ранней стадии.
Если исходить из нормального (Гаусс-сового) распределения сигнала технологического параметра, при a= 3 вероятность случайного выхода за границу 3 δ≤ 0,04, если a= 5, то эта вероятность < 0,01. Опять же, в общем случае, нормальное состояние для каждого параметра d k определяется двумя границами, верхней и нижней M k ± a δ k . В еще более общем случае эти границы не симметричны, т.е. в нормальном состоянии:
Mk - a 1k ⋅ δk ≤ dk ≤ Mk+a2k ⋅ δk
Нормальное состояние характеризуется математическими ожиданиями М к , среднеквадратическими отклонениями δ k и верхними и нижними границами изменений параметров a 1k δ k и a 2k δ k . Эти характеристики нормального состояния записываются в архив нормальных состояний и используются в дальнейшем процессе диагностирования.
Формирование матрицы диагностических признаков. Диагностическим признаком является выход любого из диагностических параметров за границу нормального состояния. Определение этих признаков происходит в каждом цикле измерений после определения нормального состояния. При завершении цикла измерения и вычисления диагностических параметров производится сравнение полученных параметров d k с границами нормального состояния:
a 1k ⋅ δk ≤ dk ≤ a 2k ⋅ δk
Если неравенство выполняется во всем цикле, то фиксируется нормальное состояние. Если не выполняется, то заполняется матрица диагностических признаков для дальнейшего сравнения со словарем состояний с целью поиска причины выхода за границы нормального состояния, т.е. поиска неисправности.
Поиск неисправностей (аномалий). Поиск неисправностей, а точнее причин появления диагностических признаков (аномалий) производится на основе сравнения зафиксированного состояния (матрица признаков) с имеющимся в памяти словарем, в котором каждому состоянию поставлена в соответствие совокупность диагностических признаков, т.е. своя матрица. При этом необходимо, в первую очередь учитывать следующие факторы:
-
- неисправности измерительных каналов;
-
- изменение режима работы объекта.
Реальный опыт любого объекта показывает, что неисправности оборудования события более редкие, чем изменения режима работы или неисправность измерительных каналов. Поэтому измерение каждого параметра должно сопровождаться проверкой исправности измерительного канала:
12 pi 1 < pi< pi 2
Если неравенство выполняется, то канал исправен, а если нет, то канал считается неисправным, о чем выдается сообщение для устранения неисправности, а параметру присваивается предыдущее значение до момента устранения неисправности в канале измерения. Предельные значения pi1 и pi2 выбираются из соображений технической (технологической) разумности. Например, температура воды при атмосферном давлении не может быть меньше 0°С и больше 100°С.
В соответствии с условиями стационарности в словаре аномалий необходимо наличие состояния(ий) – изменение режима работы со своими диагностическими признаками. Выявление аномалии – «изменение режима» сопровождается сообщением, и программ-ма уходит на проверку стационарности до момента выхода на новый режим с определением нового нормального состояния и дальнейшим поиском аномалий. Подготовка словаря состояний заключается в анализе изменений диагностических параметров при возможных (предполагаемых) аномалиях. Этот анализ включает в себя изучение опыта эксплуатации объекта, а также расчетноэкспериментальные исследования объекта в условиях появления диагностируемых аномалий (состояний). В реальной ситуации для определения большинства аномалий достаточно качественного анализа изменения диагностических параметров, подобного описанному в табл. 1. Т.е. определяется знак изменения и признаком становится факт выхода за уставку нормального состояния (больше/меньше). В случае, когда речь идет об аномалиях в очень малой степени (сравнимой с естественными шумами параметров) влияющих на контролируемые параметры, необходимы более тщательные расчеты (расчетно-экспериментальные) исследования [4].
Метод сравнения наблюдаемого состояния со словарем более 5 лет применяется в стационарных автоматизированных системах контроля диагностирования и управления САДКО [5], в которых контролируются сигналы пьезоакселерометров и большого количества датчиков технологического контроля, и используется программа диагностирования ДИЭС [6] в качестве блока определения большого количества аномалий из словаря неисправностей вращающегося оборудования. Системы широко применяются на предприятиях металлургической, нефтеперерабатывающей промышленности и в жилищно-коммунальном хозяйстве [7-9]. Методика использования параметров технологического контроля для диагностирования значительного количества неисправностей оборудования АЭС с реакторами на быстрых нейтронах прошла успешную опытную эксплуатацию на установках БОР-60 и БН-600 [4].
Выводы: параметры технологического контроля промышленных объектов помимо информации о технологическом режиме работы содержат большое количество информации о техническом состоянии объекта. Для выявления и обработки этой информации разработаны методика и алгоритмы диагностирования, позволяющие на основе анализа конструкции и технологических режимов объекта составить перечни (словари) состояний (аномалия, неисправность, дефект), в которых каждому состоянию поставлены в соответствие изменения диагностических параметров (диагностические признаки). В рамках современных программно-технических комплексов возможна реализация разработанных методик и алгоритмов для функционального диагностирования (оперативное определение текущего состояния объекта). Методики и алгоритмы использования параметров технологического контроля для диагностирования объектов ядерных энергетических установок могут быть усовершенствованы и использованы в других отраслях.
Список литературы Диагностирование оборудования с использованием параметров технологического контроля
- Минаков, А.А. Ранняя диагностика аномалий БН-реакторов с использованием параметров технологического контроля/А.А. Минаков, В.А. Афанасьев, В.Н. Ефимов. Препринт-НИИАР -5 (65). ЦНИИ Атоминформ. -М., 1985.
- Afanas'ev, V.A. Die Vervendung von Parametern der technologischen Kontrolle für die Diagnostik von Anomalien schneller Brutreaktoren/V.A. Afanas'ev, V.N. Efimov, A.A. Minakov. -Kernenergie, 1984 (27) 3. -S. 97-101.
- Клюев, В.В. Технические средства диагностирования. Справочник. Под общ. ред. Клюева В.В./В.В. Клюев, П.А. Пархоменко, В.Е. Абрамчук и др. -М: Машиностроение, 1989.
- Минаков, А.А. Опыт разработки и использования систем диагностирования оборудования АЭС. В сб. «Контроль и диагностика процессов и оборудования энергоблоков с быстрыми натриевыми реакторами»/А.А. Минаков, В.Н. Ефимов, С.Н. Ещенко, А.А. Мынцов. -РАН. Уральское отделение. -1994. -С. 48-57.
- Комплекс программно-технический САДКО. Сертификат об утверждении типа средств измерений RU.C.34.004.AN 17813. Госреестр № 26914-04 от 04.06.2004 г.
- Мынцов А.А., Кочнев М.В., Мынцова О.В., Лещенко А.Ю. Программа диагностирования вращающегося оборудования «ДИЭС». Свидетельство об официальной регистрации программы для ЭВМ № 2003610125. г.Москва, 08.01.2003 г.
- Лаврухин, А.А. Стационарные системы автоматизированного контроля, диагностирования и управления на Новолипецком металлургическом комбинате/А.А. Лаврухин, А.П. Лякин//Сб. докладов X Междунар. науч.-практ. конф. «Энергосбережение. Диагностика-2008». -Димитровград, 22-24 апреля 2008. -С. 249-256.
- Федосеев, Д.В. Опыт применения стационарных систем контроля диагностирования и управления на нефтеперерабатывающих предприятиях/Д.В. Федосеев, В.А. Логинов, В.В. Дубровский//Сб. докладов X Междунар. науч.-практ. конф. «Энергосбережение. Диагностика-2008». -Димитровград, 22-24 апреля 2008. -С. 288-295.
- Минаков, А.А. Комплексное решение/А.А. Минаков, Э.Н. Абдуллов//Коммунальный комплекс России. -2008. -№ 8(50). -С. 40-42. -№9(51). -С. 24-26.