Добавка на основе олеата натрия и льняного масла для углепылеподавляющих растворов
Автор: Голубков В.А., Горенкова Г.А., Ворожцов Е.П., Беспалова М.А., Бортников С.В.
Журнал: Горные науки и технологии @gornye-nauki-tekhnologii
Рубрика: Технологическая безопасность в минерально-сырьевом комплексе и охрана окружающей среды
Статья в выпуске: 4 т.8, 2023 года.
Бесплатный доступ
Добыча угля, его транспортировка и переработка сопровождаются образованием и поступлением в воздушную среду значительных объемов твердых частиц, в том числе угольной пыли. Наиболее распространенной технологией борьбы с угольной пылью в воздухе является гидрообеспыливание. Эта технология основана на способности воды смачивать пылевые частицы и связывать их между собой и с поверхностями, на которые осаждается пыль. Существенное ограничение данной технологии заключается в гидрофобности поверхности угля, которая препятствует смачиванию водой частиц угольной пыли. Для увеличения смачиваемости гидрофобной поверхности угольных частиц в воду добавляют поверхностно-активные вещества. В настоящей работе нами предложен состав для пылеподавления на основе олеиновой кислоты, гидроксида натрия и льняного масла в воде, изучены его свойства и оценена способность улучшать смачиваемость угольной пыли. Найдена наиболее эффективная концентрация, которая позволяет рабочему раствору улучшить смачиваемость угольной пыли на 187 % относительно воды, что превышает смачивающую способность большинства известных реагентов. Предлагаемый состав содержит 140 мг/л олеиновой кислоты, 100 мг/л гидроксида натрия, 70 мг/л льняного масла в воде. Простота состава, отсутствие вредности для окружающей среды и человека, незначительное влияние на дальнейшую эксплуатацию угольного сырья делают предлагаемый состав смачивателя перспективным для применения в технологиях гидрообеспыливания в угольной промышленности.
Угольная пыль, пылеподавление, гидрообеспыливание, смачиваемость, поверхностно-активные вещества, олеат натрия, льняное масло
Короткий адрес: https://sciup.org/140303191
IDR: 140303191 | DOI: 10.17073/2500-0632-2023-02-79
Текст научной статьи Добавка на основе олеата натрия и льняного масла для углепылеподавляющих растворов
Разработка каменноугольных месторождений, транспортировка угля и его переработка сопровождаются образованием и поступлением в воздушную среду значительных объемов твердых взвешенных частиц горных пород, в том числе угольной пыли.
Длительное воздействие угольной пыли может привести к предотвратимым, но неизлечимым заболеваниям легких, таким как: пневмокониоз, хроническая обструктивная болезнь легких, туберкулез, хронический бронхит, эмфизема и другие, вплоть до летального исхода [1–4]. Этим болезням в наибольшей степени подвержены рабочие и инженеры угольных шахт и карьеров, станций перегрузки угля, цехов обогащения и занятые в его транспортировке. Кроме того, при высоких концентрациях каменноугольная пыль в смеси с кислородом воздуха является пожа-ро- и взрывоопасной [5]. Эти существенные проблемы указывают на необходимость применения эффективных технологий удаления угольной пыли из воздушной среды с минимизацией аэрологических рисков [6].
В целях предотвращения пылеобразования при разрушении, переработке и транспортировке пылящего материала и подавления образовавшейся пыли на добывающих и перерабатывающих горных предприятиях проводятся работы по увлажнению массивов горных пород и улавливанию летающей пыли. Эта группа методов, направленных на снижение содержания в атмосфере пыли и основанных на смачивании частиц водой, называется гидрообеспыливанием [7]. При гидрообеспыливании используется свойство воды смачивать пылевые частицы, связывать их и осаждать. Существенное ограничение данной технологии заключается в гидрофобности поверхности угля, которая препятствует смачиванию водой частиц угольной пыли. Для увеличения способности смачиваться необходимо модифицировать поверхность частиц – сделать её гидрофильной.
Значительные исследования были проведены в области разработки технологий борьбы с угольной пылью. Подавление пыли распылением воды с добавлением поверхностно-активных веществ (ПАВ) является одним из наиболее эффективных подходов [8]. Разработки данной технологии начались в первой половине XX в. и стали особенно востребованы после 1970-х годов из-за механизации и интенсификации добычи угля [9, 10].
Благодаря дифильной природе ПАВ эффективно адсорбируются на поверхности раздела вода–уголь и делают поверхность угольных частиц гидрофильной, этот процесс адсорбции уменьшает свободную поверхностную энергию угольной пыли и ускоряет процесс смачивания [11, 12].
Известные смачиватели для подавления угольной пыли, как правило, содержат в качестве основного компонента, улучшающего смачивание частиц пыли, различные ПАВ. Например, в работе [13] авторы предлагают использовать сочетание натриевой соли алкилбензосульфокислоты и оксиэтилированного алкилфенола (неонол), в работе [14] – натриевую соль карбоксиметилцеллюлозы. Кроме ПАВ, рассматриваемые смачиватели содержат другие компоненты в количествах 0,2–2,0 мас.% от общего состава: карбамид, неорганические соли, одноатомные и многоатомные спирты. Хотя известно много составов для пылепода-вления, поиск новых, более эффективных и экологичных, является актуальной задачей.
Целью настоящей работы явилось совершенствование процесса подавления угольной пыли методом гидрообеспыливания путем разработки нового состава смачивающего агента. Критериями отбора реагентов в настоящей работе стали:
-
– эффективность действия реагента в процессе пылеподавления, подтверждённая хотя бы косвенными методами;
-
– простота и экономичность предлагаемой технологии;
-
– экологичность применяемых реагентов.
В связи с этим представлялось целесообразным рассмотреть возможность использования вещества https://mst.misis.ru/
2023;8(4):341–349
природного происхождения, обладающего поверхностной активностью. В качестве подобного компонента использовали натриевую соль олеиновой кислоты.
Олеиновая кислота – анионогенное поверхностно-активное вещество, которое снижает адгезию неполярных веществ в системе поверхностей твердая неполярная поверхность : полярная жидкость. Также олеат натрия значительно снижает потенциал взрыва угольной пыли [15].
Гидроксид натрия – реагент, взаимодействующий с олеиновой кислотой с образованием водорастворимого олеата натрия.
Льняное масло – реагент, способный вызывать слипание частиц посредством сродства полярности масла и частиц угля, кроме того, жирные непредельные кислоты с длинными алкильными цепями способны полимеризоваться с образованием монослоя на поверхности [16].
Нами предложен состав [17] для применения в процессах гидрообеспыливания и определены оптимальные концентрации для улучшения эффективности пылеподавления рядом физико-химических методов.
Материалы и методы
Приготовление реагента
К 8 г (~28 ммоль) олеиновой кислоты прибавляли 30 мл воды и вносили 6 г (~150 ммоль) гидроксида натрия, после чего нагревали до 89–95 °С, после остывания доводили до 1 л водой. К полученному раствору при перемешивании добавляли навеску льняного масла для получения концентраций 1, 4, 8, 20 г/л.
Изучение смачиваемости угольной пыли проводили на образцах каменного угля Черногорского месторождения Минусинского угольного бассейна. Согласно данным С. И. Арбузова [18] по генетической классификации уголь Черногорского месторождения относится к каменным гумусовым углям, марки Д (длиннопламенные). Макрокомпонентный состав представлен витринитом (67–74 %), семивитринитом (1–4 %), фюзинитом (17–27 %), липтинитом (2–8 %) в разных процентных соотношениях по каждому отдельному пласту. Уголь месторождения среднезольный, содержание золы составляет 2,8–30 %. Выход летучих веществ в среднем 36–43 %, нижняя теплота сгорания – 4830 ккал/кг. Угольную пыль получали измельчением каменного угля Черногорского месторождения в фарфоровой ступке, усреднение проводили методом конверта, порошок просеивали через сито диаметром 0,5 мм. Согласно гранулометрическому анализу, проведённому на лазерном анализаторе размеров частиц Ласка ТД (Россия), доля частиц с размерами 0,5–5 мкм составляет менее 0,05%, 5–20 мкм – 56,0 %, 20–50 мкм – 43,5 %, 50–100 мкм – 0,5 %.
Метод капиллярного впитывания
Измерение смачивания поверхности угольных частиц водными растворами различного состава проводили по известному методу капиллярного впитывания [19], схема представлена на рис. 1. Навеску угольной пыли массой 1 г помещали в воронку Шотта (ПОР 100) с пористостью 0,04–0,1 мм, температура в помещении составляла 21 °С, максимальное время экспозиции 180 с. Смачиваемость, т.е. максимальное поглощение раствора, определена как отношение объема поглощенной жидкости к массе угля в %.
Исходный уровень жидкости
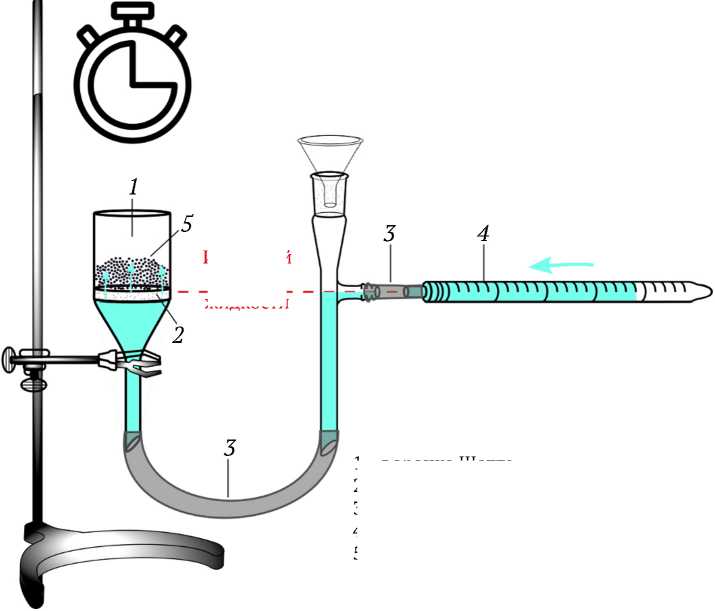
Рис. 1. Схема экспериментальной установки для определения смачиваемости
1 – воронка Шотта
2 – пористая прокладка воронки Шотта
3 – соединительные трубки
4 – градуированный капилляр
5 – навеска угольной пыли
2023;8(4):341–349
Метод плёночной флотации
Определение массы частиц угля, нанесенного на поверхность жидкости, оседающих во времени, проводили с использованием торсионных весов ВТ-500. Для этого 1 г угля наносили на поверхность воды или раствора реагента и измеряли массу осевших через 1 и 3 мин частиц.
Метод непрерывного взвешивания оседающих частиц
Седиментационные кривые (кривые зависимости массы оседающих частиц от времени оседания) для частиц угля в воде и в растворах реагента получали с использованием торсионных весов ВТ-500. Для этого 1 г угля диспергировали в 300 мл раствора и измеряли массу оседающих частиц во времени.
Измерение электрокинетического потенциала
Измерения распределения частиц по гидродинамическому диаметру методом динамического рассеяния света (DLS) и распределения частиц по электрокинетическому потенциалу методом электрофоретической подвижности проводили на приборе Zetasizer Nano ZS (Malvern Instruments, Великобритания): лазер – 633 нм; режим обратного рассеяния, угол 173°; поликарбонатная ячейка с Pd-электродами; температура измерений 25 °C. Все измерения коллоидов угля проводили при pH 11±0,1 и автогенной ионной силе. Измерения мицелл исходного реагента проводили при автогенных pH и ионной силе.
Коллоид каменного угля для измерения элек-трокинетического потенциала получали обработкой ультразвуком в воде с помощью ультразвукового гомогенизатора SONOPULS mini20 (Bandelin, Германия). 1 г угля заливали 50 мл деионизованной воды и обрабатывали в течение 15 мин (100 кДж). Суспензию отстаивали 24 ч при комнатной температуре и отбирали верхний слой, частички которого использовались в качестве модели пылевых частиц угля.
Результаты и обсуждение
Измерение смачиваемости и оптимизация состава
Смачиваемость угольной пыли различается в зависимости от используемого смачивающего состава. При обработке пыли дистиллированной водой показатель смачиваемости составляет 39 %. Для увеличения смачиваемости частиц пыли нами применялась натриевая соль олеиновой кислоты – олеат натрия. Добавление олеата натрия привело к повышению смачиваемости до 54 %. Более существенное повышение смачиваемости (до 64 %) наблюдается при использовании раствора олеата натрия с добавкой льняного масла. Внесение льняного масла в рабочий раствор производили в количестве 1, 4, 8, 20 г/л. Оптимальной концентрацией льняного масла в растворе является 4 г/л (рис. 2).
Синтез реагента оптимального состава для пылеподавления и его характеристики
На основании экспериментальных данных был подобран наиболее эффективный состав реагента: 8 г/л олеиновой кислоты, 6 г/л гидроксида натрия, 4 г/л льняного масла. Полученный реагент представляет собой прозрачную жидкость светло-жёлтого цвета; pH 12,85; электропроводность 22 мСм/см.
Поскольку концентрация ПАВ превышает критическую концентрацию мицеллообразования, реагент представляет собой дисперсную систему. Распределение дисперсной фазы по размеру имеет две моды: 1 – со средним размером 7,5 нм предположительно мицеллы; и 2 – со средним размером 150 нм (рис. 3). Более крупные частицы предположительно являются агрегатами мицелл ПАВ. При достаточно сильном разбавлении и те, и другие растворяются. Таким образом, данный состав подходит под большинство требований к смачивателям для пылеподавления в угольной и горнорудной промышленности [20].
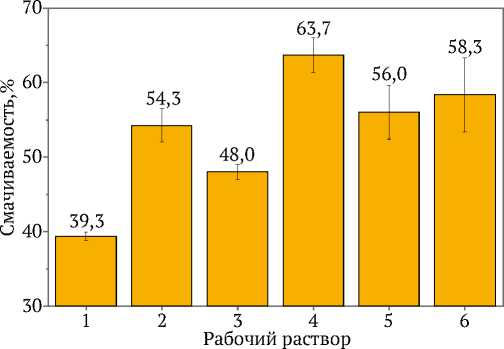
Рис. 2. Смачиваемость угольной пыли при использовании рабочих растворов: 1) дистиллированной воды; 2) олеата натрия (ОН); 3) ОН с льняным маслом CМ 1 г/л; 4) ОН с льняным маслом CМ 4 г/л; 5) ОН с льняным маслом CМ 8 г/л;
6) ОН с льняным маслом CМ 20 г/л
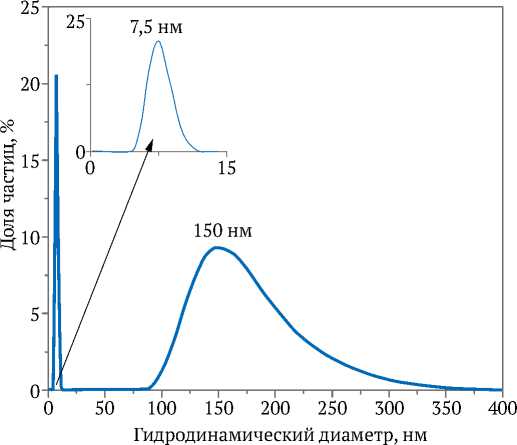
Рис. 3. Распределение мицелл и флоккул по размеру в исходном реагенте
2023;8(4):341–349
Подбор степени разбавления реагента
Поскольку использование в гидрообеспыливании реагента большой концентрации нецелесообразно по экономическому эффекту, чревато техническими и инженерными проблемами и даже негативным воздействием на окружающую среду, необходимо подобрать степень разбавления. Методом капиллярного впитывания было изучено влияние концентрации реагента на смачиваемость угольной пыли. Чистая вода показывает низкую эффективность смачивания (39 %), исходный реагент значительно более высокую – 64 %. Разбавление приводит к увеличению смачиваемости угля: 10 %-ный раствор – 68 %, 3,3 %-ный раствор – 69 %, 1,7 %-ный раствор – 73 % (рис. 4).
Приняв эффективность воды в смачивании угольной пыли за 100 %, можно оценить добавочную эффективность смачивания при использовании ПАВ, %:
EwPr Er= P , w где Er – эффективность смачивающего реагента, %; Ew – эффективность воды (100 %); Pr – показатели смачивающего агента в эксперименте, в данном случае смачиваемость, %; Pw – показатели воды в эксперименте.
В исследованиях разных добавок эта относительная эффективность колебалась от 100 % (равно эффекту чистой воды) до 193 % (превышает эффективность воды почти в 2 раза) [8]. Максимальную эффективность в смачивании угольной пыли предложенный нами состав имеет при разбавлении до 1,7 % (140 мг/л олеиновой кислоты, 100 мг/л гидроксида натрия, 70 мг/л льняного масла в воде). Его эффективность относительно чистой воды составила 187 %. Учитывая доступность и дешевизну компонентов, их малое потенциальное воздействие на окружающую среду, данный вариант реагента может быть рекомендован к дальнейшим исследованиям.
От используемого состава зависит не только смачиваемость, но и скорость смачивания. Показано, что вода имеет меньшую начальную скорость смачивания, а растворы реагента для гидрообеспыливания – значительно большую. Однако от концентрации ПАВ в системе начальная скорость оседания не зависит (рис. 5).
Тесты на погружение частиц в растворах ПАВ, такие как метод плёночной флотации и седиментационный анализ, являются традиционными способами оценки эффективности смачивания угольной пыли рабочими растворами [8, 21]. Скорость погружения частиц с поверхности раствора определяется в том числе эффективностью смачивания. При повышении концентрации до 3,3 % наблюдается увеличение массы осевших частиц. Это явным образом свидетельствует об улучшении смачивания частиц и, соответственно, более лёгком прохождении ими поверхности жидкости. При концентрации реагента более 5% масса осевших за время частиц значительно снижается, показатель даже ниже, чем для воды. В этих случаях процесс седиментации лимитируется не проникновением частицы с поверхности жидкости в объём раствора, а агрегативной устойчивостью частиц. Естественно, что в результате адсорбции анионогенного
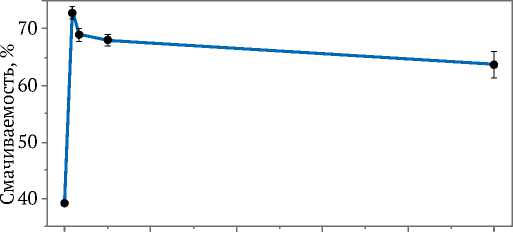
0 20 40 60 80 100
Концентрация реагента, %
Рис. 4. Смачиваемость угля растворами реагента разной концентрации
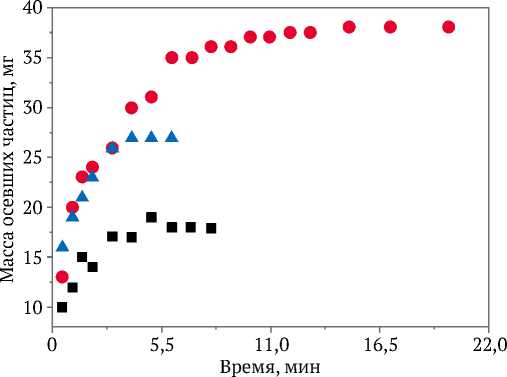
■ В дистиллированной воде
• В 1,7%-ном растворе реагента
▲ В 10%-ном растворе реагента
Рис. 5. Скорость седиментации частиц угольной пыли в водных растворах смачивающего реагента
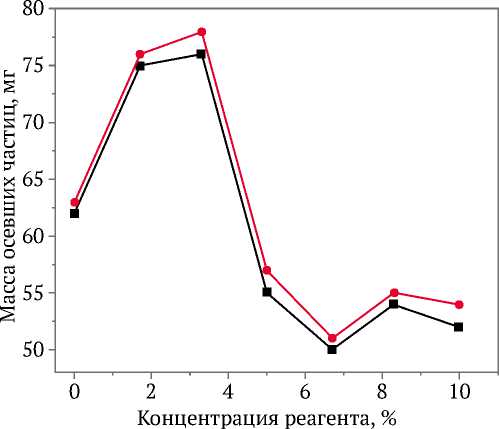
Время оседания -■- 1 мин —•— 3 мин
2023;8(4):341–349
ПАВ происходит усиление поверхностного заряда частиц и возникает большее электростатическое отталкивание между ними.
Для проверки установленных закономерностей были измерены распределения гидродинамических радиусов и электрокинетических потенциалов коллоидов угля (рис. 7).
Распределение частиц в воде мономодальное, средний размер 230 нм. Добавка ПАВ приводит к образованию 2 мод в распределении по размерам при всех концентрациях реагента. Значительная доля частиц уменьшила свой размер и образовалась мода со средним размером 100–110 нм, то есть происходит дезагрегация или дезагломерация частиц из-за электростатического отталкивания, что является хорошо известным явлением [22]. В том числе известно применение олеата натрия для диспергирования технического углерода с уменьшением размеров частиц [23].
Коллоид угля при pH 11 имеет очень выраженный отрицательный заряд, средний Z потенциал -46 мВ. Добавление ПАВ и его адсорбция на поверхности приводят к изменениям в распределении частиц по зарядам (рис. 7, б). При адсорбции ПАВ происходит сразу два процесса: подавление диссоциации поверхностных кислотных групп угля и появление новых центров ионизации – диссоциированных молекул адсорбата [24]. При более низких концентрациях ПАВ (0,9%-ный раствор реагента) оба фактора влияют слабо, а при максимальной концентрации ПАВ (5%-ный раствор реагента) распределение частиц по зарядам уже мало отличается от угля в воде, т.е. факторы компенсировали друг друга. Наиболее интересны результаты, полученные при концентрации реаген- та 1,7 и 3,3 %. В этих случаях наблюдается сужение распределения частиц по Z потенциалу и смещение в сторону меньших зарядов, в экспериментах по измерению смачиваемости и погружению частиц эти составы также показали лучшие результаты.
При контакте частиц угля и распылённых капель раствора ПАВ происходит эффективное смачивание частиц угля, в отличие от капель чистой воды. На рис. 8 представлено графическое объяснение действия добавок анионогенных ПАВ в процессе гидрообеспыливания. Сначала частицы пыли и капли сталкиваются (процессы I и II), эти стадии почти не зависят от свойств раствора. При взаимодействии гидрофобной частицы угольной пыли и чистой воды краевой угол смачивания 9 > 90°, что не позволяет каплям захватывать угольную пыль и осаждать её (процесс III). Адсорбция олеата натрия из капель раствора ПАВ делает поверхность угольных частиц более гидрофильной. В этом случае взаимодействие растворённых веществ, твёрдой частицы и воды позволяет воде растекаться по изначально гидрофобной поверхности, краевой угол смачивания 9 < 90° (процесс III). При таком характере взаимодействия жидкость – твёрдое тело агломерация происходит путём поглощения частиц каплями (процесс IV), которые разрастаются [12]. Однако при избыточной адсорбции и, соответственно, слишком большом поверхностном заряде частиц иммерсия частиц может замедляться или останавливаться из-за их электростатического отталкивания. Таким образом, объясняется обнаруженная экстремальная зависимость эффективности смачивания от концентрации ПАВ и обосновывается выбор концентрации реагента, необходимой для высокой эффективности смачивания угольной пыли.
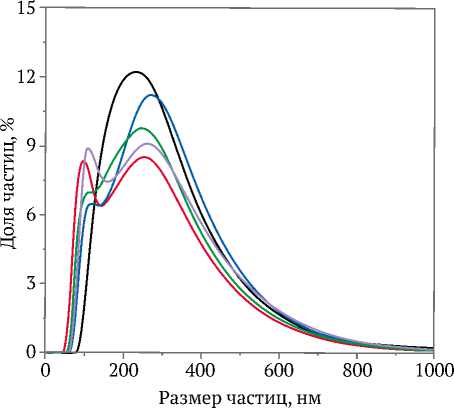
Дисперсная среда
Дистиллированная вода 0,9%-ный раствор реагента 1,7%-ный раствор реагента
а
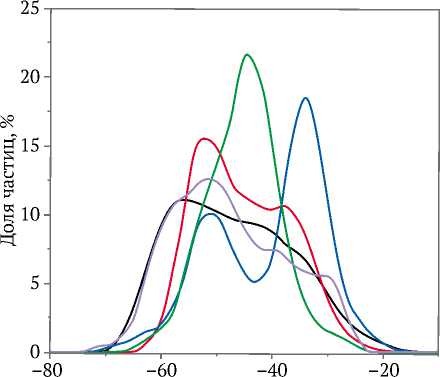
Электрокинетический потенциал, мВ
-
3,3%-ный раствор реагента
5,0%-ный раствор реагента
б
Рис. 7. Распределение коллоидных частиц по размеру – а и электрокинетическому потенциалу с добавками реагента для пылеподавления – б https://mst.misis.ru/
2023;8(4):341–349
Процесс I
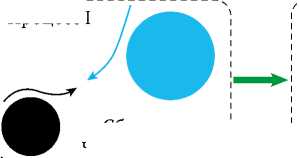
Сближение частиц и капель
Процесс II
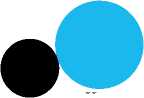
Процесс III – Смачивание
9 > 90°
Контакт частиц и капель ПАВ
Вода
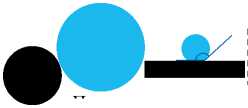
Процесс III – Смачивание
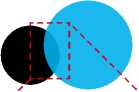
9 < 90°
Хорошее смачивание частиц угля
£ !
При невысокой адсорбции анионогенного ПАВ и умеренном заряде поверхности

Молекулы jfH7O ПАВ '
H2O
H 2 O

9 < 90°
Плохое смачивание частиц угля
Процесс IV – Агломерация
При большой адсорбции анионогенного ПАВ и избыточном заряде поверхности
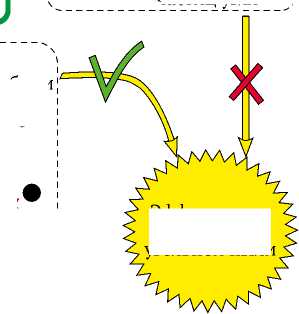
Эффективное оседание угольной пыли
Рис. 8. Схема действия добавок анионогенных ПАВ в процессе гидрообеспыливания
Заключение
Нами предложен состав смачивателя для подавления угольной пыли [17], изучены его свойства и оценена способность улучшать смачиваемость гидрофобной поверхности. С применением физико-химических методов определена наиболее эффективная концентрация состава для гидрообеспыливания – наиболее целесообразно применять 1,7%-ный раствор реагента (140 мг/л олеиновой кислоты, 100 мг/л гидроксида натрия, 70 мг/л льняного масла в воде). Эффективность в экспериментах по смачиванию угольной пыли составила 187 % по сравнению с чистой водой, что находится на уровне лучших составов для пылеподавления, известных в литературе. В результате показано, что исследуемые компоненты рабочих растворов оказывают положительное влияние на смачиваемость угля и её скорость. Преимуществом предложенного состава является безопасность применяемых ПАВ – олеиновой кислоты и льняного масла, которые получены из возобновляемого растительного сырья.
Список литературы Добавка на основе олеата натрия и льняного масла для углепылеподавляющих растворов
- Ayoglu F. N., Acikgoz B., Tutkun E., Gebedek S. Descriptive characteristics of coal workers’ pneumoconiosis cases in Turkey. Iranian Journal of Public Health. 2014;43(3):389. URL: https://ijph.tums.ac.ir/index.php/ijph/article/view/4162
- Pollock D., Potts J. D., Joy G. Investigation into dust exposures and mining practices in mines in the southern Appalachian Region. Mining Engineering. 2010;62:44.
- Ross M., Murray J. Occupational respiratory disease in mining. Occupational Medicine. 2004;54(5):304–310. https://doi.org/10.1093/occmed/kqh073
- Perret J. L., Plush B., Lachapelle P. et al. Coal mine dust lung disease in the modern era. Respirology. 2017;22(4):662–670. https://doi.org/10.1111/resp.13034
- Cao W., Gao W., Peng Y., Liang J., Pan F., Xu S. Experimental and numerical study on flame propagation behaviors in coal dust explosions. Powder Technology. 2014;266:456–462. https://doi.org/10.1016/j.powtec.2014.06.063
- Баловцев С. В. Аэрологические риски высших рангов в угольных шахтах. Горные науки и технологии. 2022;7(4):310–319. https://doi.org/10.17073/2500-0632-2022-08-18
- Летуев К., Ковшов С., Гридина Е. Технология гидрообеспыливания автомобильных дорог угольных разрезов с применением очищенных сточных и дренажных вод. Экология и промышленность России. 2020;24(1):30–33. https://doi.org/10.18412/1816-0395-2020-1-30-33
- Xu G., Chen Y., Eksteen J., Xu J. Surfactant-aided coal dust suppression: A review of evaluation methods and influencing factors. Science of The Total Environment. 2018;639:1060–1076. https://doi.org/10.1016/j.scitotenv.2018.05.182
- Hartmann I., Greenwald H. P. Use of wetting agents for allaying coal dust in mines. US Department of the Interior, Bureau of Mines; 1940.
- Harrold R. Surfactants vs. dust – do they work? Coal Age. 1979;84(6):102–105.
- Liu H., Sun D., Hao J. Colloid and interface chemistry. Chemical Industry Press, Peking, China; 2016.
- Li S., Zhao B., Lin H. et al. Review and prospects of surfactant-enhanced spray dust suppression: Mechanisms and effectiveness. Process Safety and Environmental Protection. 2021;154:410–424. https://doi.org/10.1016/j.psep.2021.08.037
- Глебов А. Ф. Смачиватель для подавления угольной пыли. RU2495250С1. Патент. 2013.
- Ковшов С. В., Ковшов В. П., Ерзин А. Х., Сафина А. М. Способ пылеподавления на открытых угольных складах. RU2532939. Патент. 2013.
- Huang Q., Honaker R. Q., Perry K. A., Lusk B. Surface chemistry modification of rock dust for improved dispersion and coal dust explosion prevention. In: Proceedings of the 2015 SME Annual Conference and Expo and CMA 117th National Western Mining Conference – Mining: Navigating the Global Waters. 2015. Pp. 245–251.
- Osman M. A., Suter U. W. Surface treatment of calcite with fatty acids: structure and properties of the organic monolayer. Chemistry of Materials. 2002;14(10):4408–4415. https://doi.org/10.1021/cm021222u
- Бортников С. В., Горенкова Г. А. Смачиватель для подавления угольной пыли. RU2689469 C1 Патент. 2019.
- Арбузов С. И., Ершов В. В. Геохимия редких элементов в углях Сибири. Томск; Д-Принт; 2007. 468 c.
- Коузов П. А., Скрябина Л. Я. Методы определения физико-химических свойств промышленных пылей. Л.: Химия; 1983.
- Поздняков Г., Третьяков А., Гаравин В., Новосельцев А. Требования к смачивателям для пылеподавления в угольной и горнорудной промышленности. Безопасность труда в промышленности. 2013(10):36–39.
- Walker P., Petersen E., Wright C. Surface active agent phenomena in dust abatement. Industrial & Engineering Chemistry. 1952;44(10):2389–2393. https://doi.org/10.1021/ie50514a032
- Knyazheva O., Baklanova O., Lavrenov A. et al. The effect of ultrasonic exfoliation and the introduction of a surfactant on particle size and aggregative stability water dispersions of carbon black. In: Oil and Gas Engineering (OGE-2018). 26 February – 2 March 2018, Omsk, Russia. 2018;2007(1):020016. https://doi.org/10.1063/1.5051855
- Sis H., Birinci M. Effect of nonionic and ionic surfactants on zeta potential and dispersion properties of carbon black powders. Colloids and Surfaces A: Physicochemical and Engineering Aspects. 2009;341(1–3):60–67. https://doi.org/10.1016/j.colsurfa.2009.03.039
- Maršálek R. The influence of surfactants on the zeta potential of coals. Energy Sources, Part A: Recovery, Utilization, and Environmental Effects. 2008;31(1):66–75. https://doi.org/10.1080/15567030701468142