Efficiency improvement for platinum concentrates production from electrolytic slimes at polar division of OAO MMC Norilsk Nickel
Автор: Lapshin Dmitry A., Grabchak Eduard F., Kuzmina Irina S., Goryacheva Yuliya A., Kozhanov Aleksandr L.
Журнал: Журнал Сибирского федерального университета. Серия: Техника и технологии @technologies-sfu
Статья в выпуске: 7 т.6, 2013 года.
Бесплатный доступ
Slime processing at PD OAO MMC Norilsk Nickel involves oxidizing-sulphatizing roasting, calcine leaching with sulphate solution, calcine cake smelting into anodes followed by electrolytic dissolution, and a number of processes designed for accompanying elements recovery. Resulting final products are platinum-palladium (60-65 % Σ Pt+Pd) and rhodium-ruthenium (2.0-3.5 % Rh) concentrates (KP-1 and KP-2, respectively), refined silver, selenium of technical grade and tellurium. Process cycle duration, considerable work-in-process amount, a great number of operations and low efficiency of individual operations are considered to be disadvantages of the slimes processing method. We determined optimal process conditions for copper slimes calcine cake repulping with sulphate (reagents, consumption and sodium hypochlorite feed rate) offering 6-7 fold increase of Pt recovery into solution and 1,5-2,0 fold that of Pd. PGMs precipitation from resulting solutions was fount to yield precipitate with Pt and Pd content amounting up to 55 %; this makes it possible to produce it as final product. The product is then sent to a final product (KP-1 concentrate) packaging section bypassing smelting and electrolysis stages with inherent high PGMs losses, resource intensity and long duration time.
Slime, concentrates, pgm
Короткий адрес: https://sciup.org/146114793
IDR: 146114793
Текст научной статьи Efficiency improvement for platinum concentrates production from electrolytic slimes at polar division of OAO MMC Norilsk Nickel
Polar Division (PD) of OAO MMC Norilsk Nickel is the major Russian producer of PGM concentrates. Copper-nickel ore processing technology currently applied by Polar Division implies platinum group metal concentration in slimes from copper and nickel electrorefining.
Slime processing at PD OAO MMC Norilsk Nickel involves oxidizing-sulphatizing roasting, calcine leaching with sulphate solution, calcine cake smelting into anodes followed by electrolytic dissolution, and a number of processes designed for accompanying elements recovery. Resulting final products are platinum-palladium (60-65 % Σ Pt+Pd) and rhodium-ruthenium (2.0-3.5 % Rh) concentrates (KP-1 and KP-2, respectively), refined silver, selenium of technical grade and tellurium.
Process cycle duration, considerable work-in-process amount, a great number of operations and low efficiency of individual operations are considered to be disadvantages of the slimes processing method.
One operation of copper slime processing flow sheet includes calcine repulping with sulphate solution (250-280 g/dm3 of CH2SO4) to extract tellurium. Part of platinum metals (PGM) passes into solution along with tellurium. To recover PGMs from solutions after copper slime calcine cake repulping a method of precipitation thereof with hydrazine hydrate and thiourea was implemented at Polar Division. Resulting PGMs residue contains up to 60 % of Pt and Pd sum. The product is then sent to a final product (KP-1 concentrate) packaging section bypassing smelting and electrolysis stages with inherent high PGMs losses, resource intensity and long duration time [1]. This “shortcut” method produces no more than 10 % of initial platinum metals content of copper slime, whereas annual economic benefit amounts at least 7 mln Rub. Therefore, development of a method offering higher PGMs recovery into residue is topical challenge.
Results and discussion
Precipitation rate of PGMs from solution after copper slime calcine cake repulping is 95-99 %, therefore for PGM recovery into residue to increase, the amount of PGMs passed into repulp solution should be higher.
Oxidants addition at the repupling stage is the simplest technical solution offering higher PGMs recovery into solution. For the experiment the most available reagents not introducing foreign impurities (hydrogen peroxide and sodium hypochlorite) were chosen. Present study addresses dependence of PGMs passing into solution on amount of sodium hypochlorite (5-100 % of initial volume) and hydrogen peroxide (5-50 % of initial volume) as well as reagent addition time (from 15-20 minutes to 2 hours) at the acid repulping stage.
Test results are shown in Fig. 1-3.
As can be seen from the results, 10 % addition of initial NaClO volume resulted in Pt recovery growth from 6 to 50-55 % and from 35 to 60-65 % for Pd. Further increase in sodium hypochlorite flow rate produced modest growth of platinum and palladium recovery rate (up to 70 % and 80 %, respectively).
In contrast to PGMs recovery, Rh, Ru and Ir extraction curves are comparatively flat with a maximum growth observed at 25 % of sodium hypochlorite addition, where Ir recovery rate changed from 45 to 90-95 %, from 28 to 40-45 % for Rh and from 20 to 30-35 % in case with ruthenium.
Along with PGMs recovery we investigated selenium and tellurium extraction into solution since they pass into residue in downstream PGMs precipitation resulting in lower platinum and palladium content thereof.
Selenium and tellurium recoveries reached their peaks at 5 % of sodium hypochlorite initial volume.
Sodium hypochlorite feed rate produced little effect on metal recovery results. However, on addition of sodium hypochlorite within 20 minutes chlorine gas release was observed at 25 % of oxidizer initial volume which may entail extra costs for commercial process realization. On the other hand for 120 minutes of sodium hypochlorite addition the chlorine gas release was not observed everywhere over the flow-rate range being studied.
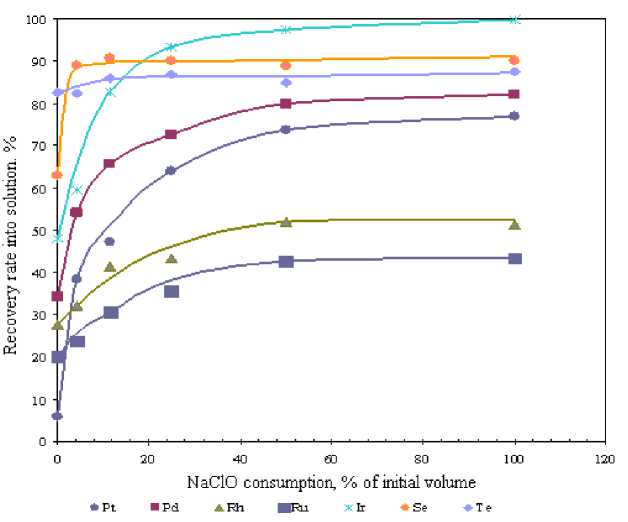
Fig. 1. Relationship between metals recovery rate into solution and NaClO amount (NaClO addition time – 20 min.)
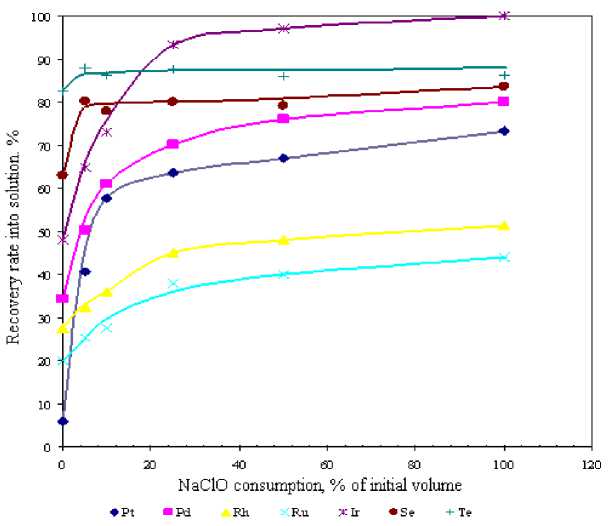
Fig. 2. Relationship between metals recovery rate into solution and NaClO amount (NaClO addition time – 120 min.)
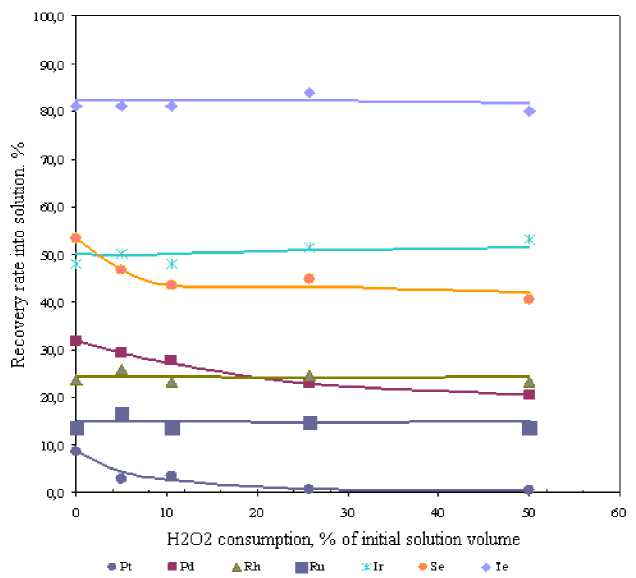
Fig. 3. Relationship between metals recovery rate into solution and H 2 O 2 amount (H 2 O 2 addition time – 20 min.)
H2O2 addition in the amount of 5-50 % of initial volume resulted in lower Pt, Pd and Se recovery into solution. It is known from the literature [2] that hydrogen peroxide, under certain conditions, exhibits reducing properties. Identical behavior of Pt, Pd and Se recovery curves suggests selenium reduction by hydrogen peroxide and precipitation thereof as platinum and palladium selenides. The same mechanism of selenium precipitation for its recovery from platinum-bearing solution has been mentioned in other works [3].
Hydrogen peroxide addition did not produce any effect on Rh, Ru, Ir and Te recovery everywhere over the flow-rate range being studied.
It is known that rare platinum-group metals extraction from sulphate solutions, unlike Pt and Pd, is a very complicated technological challenge through the ability of these metals to form multicharge poly-nuclear complexes. Therefore, 5-10 % of sodium hypochlorite addition for two hours is required to maximize Pt and Pd transfer into solution together with minimum rare platinum-group metals passing into solution and to lower chlorine gas release. In this case Pt recovery increased from 6 to 50 %, Pd – from 35 to 65 %, Rh – from 28 to 39 %, Ru – from 20 to 30 % and Ir – from 45 to 80 %.
Resulting solutions were tested on PGM precipitation therefrom under conditions close to commercial. Platinum and palladium content of obtained precipitates amounted up to 55 %.
Conclusions
In order to increase PGMs pass into solution the addition of sodium hypochlorite and hydrogen peroxide at the stage of copper slimes calcine cake repulping with sulphate was tested.
-
1. Relationships between PGMs recovery and sodium hypochlorite and hydrogen peroxide flowrates were established.
-
2. We determined optimal process conditions for copper slimes calcine cake repulping with sulphate (reagents, consumption and sodium hypochlorite feed rate) offering 6-7 fold increase of Pt recovery into solution and 1,5-2,0 fold that of Pd.
-
3. PGMs precipitation from resulting solutions was fount to yield precipitate with Pt and Pd content amounting up to 55 %; this makes it possible to produce it as final product.