Energy-saving technology of preparing cotton fabrics for dyeing
Автор: Yasinskaya Natalia, Lenko Ksenia, Maruschak Yulia
Журнал: Вестник Витебского государственного технологического университета @vestnik-vstu
Рубрика: Химическая технология и экология
Статья в выпуске: 2 (43), 2022 года.
Бесплатный доступ
The purpose of the work is to develop a bioscouring technology, which results in the maximum purification of cotton fabric from impurities with minimal damage to the fiber - forming polymer. As a result of the research, it was found that in order to achieve the required degree of purification from impurities and maximum wettability, it is advisable to use combined biochemical methods of preparation, consisting of sequential treatment with enzyme preparations and a traditional alkaline scouring solution at low concentrations of its constituent components. Thanks to the use of non - toxic biodegradable enzymes in the technology of preparing cotton textile materials for dyeing, it is possible to reduce the concentration of traditional liquid reagents by further loosening the fiber structure and creating conditions for a deeper and more complete removal of impurities. Thus, there is a reduction in the concentration of NaOH by 2 times, a reduction in the duration of treatment in an alkaline solution, as well as exposure to high temperature by more than 2 times.
Короткий адрес: https://sciup.org/142235820
IDR: 142235820 | DOI: 10.24412/2079-7958-2022-2-126-134
Текст научной статьи Energy-saving technology of preparing cotton fabrics for dyeing
Витебский государственный технологический университет
As it is known, before coloring and final finishing, textile materials go through a preparation stage, which includes desizing, scouring and bleaching. As a result of scouring, 7–12 % of impurities of non-cellulose origin accompanying cellulose (waxy, pectin, ash, etc.) are removed, due to which there is an increase in capillary properties and a uniform sorption capacity of the textile material [1].
As a result of traditional alkaline scouring, pectin substances pass into soluble compounds and are completely removed from the fiber as a result of hydrolysis. Nitrogen-containing protein substances are hydrolyzed, forming amino acids, which with sodium hydroxide produces watersoluble salts. About 40 % of waxy substances (fatty acids) are saponified to form sodium salts of fatty acids. The remaining waxy substances are removed by emulsification with a surfactant [2]. For the successful flow of the emulsification process, it is necessary to transfer waxy substances to a molten state. The melting point of waxy substances is 80 °C , so the scouring temperature should be higher [2].
Under such conditions, nonselective oxidation of cellulose occurs: micro- and macroradicals are formed, pyran rings and glucosidic bonds are broken, and a mixture of hydroxy- and hydrocellulose is formed [3]. As a result of oxidation, the destruction of cellulose materials occurs, which is expressed in a decrease in the degree of polymerization, and, as a result, a deterioration in physical, mechanical and other consumer properties [4]. In addition, during alkaline scouring, a significant part of the reagents is removed during washing and enters wastewater and the atmosphere, causing enormous damage to the environment.
Currently, biotechnological methods for the preparation of textile materials from cellulose fibers are being developed and introduced into production more and more with the use of enzyme preparations that are active at low temperatures and in neutral environments [3, 5, 6]. Thus, the most commonly used preparation in scouring technologies is the cellulase enzyme, which causes the destruction of cellulose in the outer layers of the fiber in areas with the least ordered molecules [4]. Bioscouring involves carrying out the technological process at a temperature of 50-60 °C, while the removal of waxy impurities is carried out due to the partial hydrolysis of the cellulose of the primary wall and the destruction of the cuticle [5].
However, according to the studied literature sources [3], [7], not all accompanying impurities of cotton fiber can be removed in the process of bioscouring with a composition of enzyme preparations. In particular, the greatest difficulty is the removal by enzymes of the protein part of nitrogen-containing substances. They can be extracted only after their destruction under the action of hot alkali solutions or alkaline solutions of sodium hypochlorite, or in the presence of sodium silicate [2]. In this regard, the task of developing integrated technologies for the processing of cotton materials, including the stages of bioscouring and alkaline scouring (with a reduction in the concentration of NaOH in the solution), which minimizes the aggressive effect of chemicals on cellulose, and also improves the environmental friendliness of finishing technologies, is an urgent task.
The aim of the work is to develop a technology for scouring of cotton fabrics using new polyenzymatic compositions of Belarusian production, as a result of which the maximum cleaning of cotton fabric from accompanying impurities is achieved with minimal damage to the fiber-forming polymer. OBJECT AND SUBJECT OF RESEARCH
The object of study is a cotton fabric of plain weave ("Baranovichi Cotton Production Association", JSC) with a surface density of 120 g/m2 . This fabric was processed according to four technologies (Figure 1).
In the study the following preparations of a Belarusian manufacturer, Enzyme LLC company, were used: Enzitex СKO (Acidic cellulase, activity 10,000 units/g , optimal conditions for pH from 4.5 to 5.5, operating temperature 30– 70 °C ); Enzitex Bio-K (Acid pectinase, activity 6500 units/g . Optimal conditions for action pH from 3.0 to 4.5, operating temperature 40– 60 °C ); Enzitex ATS (Bacterial a -amylase, activity 10,000 units/g , optimal conditions for action pH from 5.5 to 6.5, operating temperature 40-90 °C ).
Scouring:
Bath module - 50;
Duration T- 30 min.;
Solution temperature t- 100’C.
Washing with hot and cold water
Figure 1 – Scheme of processing cotton fabrics
RESEARCH METHODS
To determine the effectiveness of scouring, the content of waxy and fatty substances, pectin substances, ash substances, and the degree of damage to cellulose were determined in the cotton fiber.
To determine the waxy and fatty substances of cotton fiber, the method of extracting them with an alcohol-benzene reagent (1:1) in a Soxhlet apparatus was used [4]. After drying the material to constant weight at t = 90 °C and cooling in a desiccator, it was weighed with an accuracy of 0.001 and the content of fat waxes ( % ) was calculated using the formula (1):
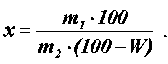
Pectins were extracted with 1 % ammonium citrate solution followed by spectrophotometric measurement on a PB 2201 spectrophotometer designed to measure spectral directional transmittances, optical density in transparent liquid solutions and solid samples and determine the concentration of substances in the spectral range of 190...1100 nm. The measurements were carried out at a wavelength of 360, 390, 530, and 630 nm, followed by the calculation of the quantitative content of polysaccharides included in the composition of pectin substances (hexosans, pentosans, polyuronides, furfural), as well as the calculation of the quantitative content of pectin substances [4].
The content of ash substances in the fiber was determined according to GOST 938.2-67. Leather. Ash content determination method [8].
The degree of damage to the cellulose of cotton fiber was determined by the relative viscosity ( η sp ) of 0.1 % copper-ammonia solutions of cellulose using a rotational viscometer Lamy Rheology RM100 PLUS [3].
EXPERIMENTAL STUDIES AND DISCUSSION OF RESULTS
The results of determining the chemical composition and the degree of damage to cotton materials are presented in Table 1.
Waxy impurities in cotton are localized in the peripheral part (cuticle and primary wall) of the fiber [3]. Waxes are based on hydrocarbons, fatty acids and their esters, as well as high molecular weight alcohols. One of the important conditions for the purification of cellulose fiber from waxy compounds is their transfer to a molten or softened state [9]. In an alkaline environment, up to 37% of waxy cotton is saponified, the rest can be removed only by emulsification or dissolution in nonpolar organic solvents [3].
When forming the technology for the preparation of textile materials from natural plant fibers, it should be taken into account that it is desirable to leave a certain part of waxy materials on the fiber, since they improve the elastic properties of the fibers and increase the consumer (physical and mechanical) properties of the textile material. It is known that a decrease in the content of waxy to 0.11 % and below leads to a loss of tear strength by 30 % [3]
Alkaline scouring removes 0.185 % of cotton extractives, while bioscouring releases about 0.546 % of waxy and fatty impurities. The smallest percentage of fat wax content is demonstrated by a sample that has undergone a combined biochemical treatment, which includes consecutive enzymatic and traditional alkaline scouring. This pattern is confirmed by the results of studies presented in [9], according to which the removal of waxes during enzymatic scouring is mainly carried out by introducing a surfactant into the working bath and introducing an additional hydrodynamic (mechanical) effect. Due to the partial destruction of the primary wall of the cotton fiber and the loosening of its structure by enzymes, there is a more complete surfactant sorption in the surface structures of the damaged fiber, which makes it possible to remove the largest amount of fatty substances by emulsification.
Pectic substances are one of the main satellites of cellulose. This is a group of complex carbons, consisting of polygalacturonic acid. In cotton, pectin substances are concentrated in the cuticle and in the primary wall (37 %). They can be complexed with waxy materials and with cellulose itself, which makes it difficult to remove them from the fiber [3].
Pectin can be extracted from cellulose fiber by various methods. Due to the hydrolytic destruction of glucosidic bonds, most of the pectin substances dissolve in solutions of alkalis and acids. When processing cotton fiber with peroxide solutions, depending on the concentration of hydrogen peroxide, from 11 to 29 % of pectin compounds can be removed. Pectic substances can be removed by boiling cotton with alkali under pressure, as well as using enzyme preparations [2]. Under the action of pectinases, the hydrolytic cleavage of pectin substances occurs in several stages: protopectinase acts on insoluble protopectin by
The use of enzyme scouring with pectinase as part of the composition causes hydrolytic cleavage of pectin substances, promotes their effective extraction from the fiber. With an increase in the concentration of pectinase in the cooking solution (Scheme 2, biochemical scouring), the proportion of removed pectin substances increases.
Photos of the residual ash content in a porcelain crucible after calcining cotton fiber in a muffle furnace are shown in Figure 2.
Purification of fiber from mineral substances, as a rule, is not difficult. The ash substances of cellulose are soluble in water and are removed from the fabric by washing with water or a weak acid solution. According to the results of the study, the largest percentage of ash impurities is removed during tissue bioscouring with polyenzymatic compositions. Biochemical scouring also removes 80% of minerals from cellulose fibers. Probably, this effect is achieved by additional loosening of the fiber structure and creating conditions for a deeper and more complete removal of impurities. The technology of enzymatic scouring of cotton textile material consists in the selective hydrolysis of the cellulose of the primary wall of cotton, as a result of which the cuticle is removed and the outer layer (primary wall) of the fiber is partially destroyed. It is believed that by destroying the primary wall, it is possible to remove the main part of the contaminants from this layer [2].
Thus, at this stage of research, it has been determined that the most effective is the combined biochemical scouring in terms of removing the
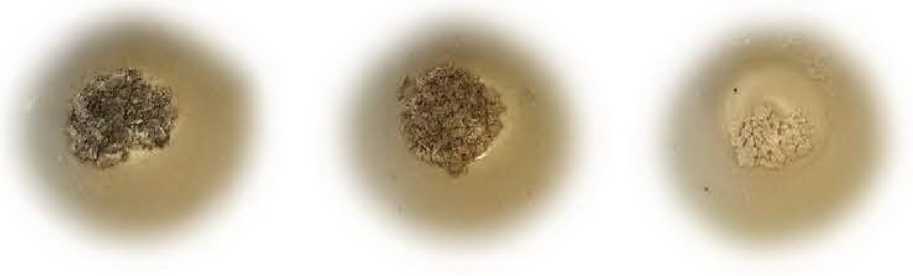
а
c
b
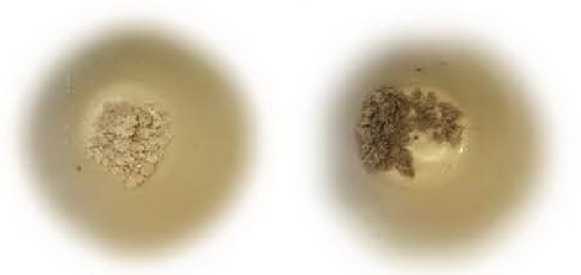
de
Figure 2 – Residual ash content in a porcelain crucible after calcining cotton fiber in a muffle furnace: a) severe;
b) alkaline scouring; c) bioscouring (scheme 1); d) bioscouring (scheme 2); e) biochemical scouring accompanying impurity compounds of cotton.
Cellulase is known to cause hydrolysis of the β-glucosidic bond in carbohydrates [3]. The result of such hydrolysis of cellulose is its destruction. Hydrocellulose is characterized by increased solubility in hot water, especially alkaline solutions. Thus, alkaline scouring increases the degree of degradation of the cotton biopolymer due to processing at high temperatures. Therefore, given the effect of scouring, whether alkaline or enzymatic, on cellulose, a decision was made to determine to what extent these technologies contribute to the destruction of cellulose.
The viscosity of the copper-ammonia solution of the tissue sample biotreated according to Mode 2 (with a lower concentration of the
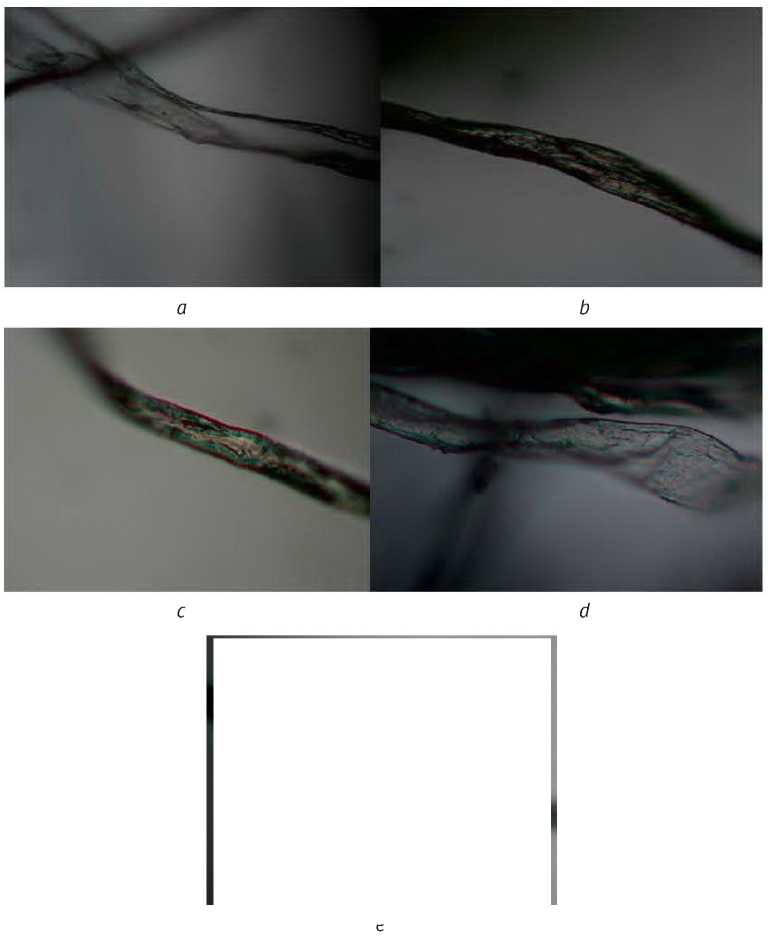
Figure 3 – Micrographs of the original and processed fibers: a) original fibre; b) alkaline scouring; c) bioscouring (scheme 1); d) bioscouring (scheme 2); e) biochemical scouring
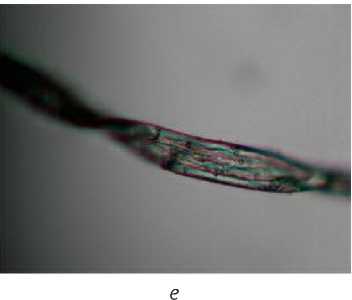
cellulase enzyme) decreased by 3.5 % compared to the solution of the original fabric, and exceeded the viscosity of the sample solution prepared according to Scheme 1. Introduction of bioscouring to alkaline scouring technology stage and a decrease in the concentration of alkali in the composition of the solution allows to reduce the degree of destruction of cellulose, i.e., the viscosity of the copper-ammonia solution increases by 10 % compared to the viscosity of the solution after alkaline scouring.
Using an optical microscope Altami Micromed, micrographs of the studied cotton fibers were taken (Figure 3).
Visual assessment of micrographs allows us to conclude that the outer layers of the fiber are destroyed after scouring in all modes. The most damaged fiber is noted after alkaline scouring, which is also confirmed by the results of a study of the viscosity of copper-ammonia solutions of cellulose.
CONCLUSIONS
Despite the fact that the use of enzyme scouring allows maximum preservation of cellulose, in order to achieve the required degree of purification from impurities and maximum wettability, it is advisable to use combined biochemical methods of preparation, consisting of sequential treatment with enzyme preparations and a traditional alkaline scouring solution at low concentrations of its constituent components.
Thanks to the use of non-toxic biodegradable enzymes in the technology of preparing cotton textile materials for dyeing, it is possible to reduce the concentration of NaOH by 2 times; reduce the duration of treatment in an alkaline solution; and also reduce exposure to high temperature by more than 2 times by additional loosening of the fiber structure and creating conditions for a deeper and complete removal of impurities. The result of a mild impact is the preservation of the fiberforming polymer, and, consequently, the strength of the fiber, as well as a decrease in the negative impact on the environmental situation.
The use of polyenzyme compositions in the scouring biotechnology makes it possible to comprehensively influence various types of impurities, contributing to the effective cleaning of the fiber and imparting increased hydrophilic properties to it.
The research was carried out within the framework of the research work "Biochemical modification of cellulose textile materials" № T22UZB-062" from the Belarusian Republican Foundation for Basic Research.
The article was prepared based on the materials of the report of the 'INTERNATIONAL CONFERENCE ON TEXTILE AND APPAREL INNOVATION (ICTAI-2022)', which took place on November 23–24, 2022 at the educational institution "Vitebsk State Technological University" (Republic of Belarus)
Список литературы Energy-saving technology of preparing cotton fabrics for dyeing
- Кричевский, Г. Е. (2001), Химическая технология текстильных материалов, Москва, 2001, 298 с.
- Барышева, Н. В. (2006), Разработка основ ферментативной технологии отварки хлопчатобумажных тканей: дисс.... канд. техн. наук, Москва, 2006, 179 с.
- Алеева, С. В. (2011), Химия и технология биокатализируемого наноконструирования льняных текстильных материалов, Российский химический журнал им. Д.И. Менделеева, 2011, No 3, С. 46-58.
- Алеева, С. В. (2014), Методологические основы совершенствования процессов биохимической модификации льняных текстильных материалов: дисс.... докт. техн. наук, Иваново, 2014, 396 с.
- Алеева, С. В. (2012), Исследование и описание изменения капиллярности льняной ткани в условиях ферментативной обработки, Изв. вузов. Химия и химическая технология, 2012, No 3, С. 91.
- Koksharov, S., Aleeva, S., Lepilova, O. (2015), Nanostructural biochemical modification of flax fiber in the processes of its preparation for spinning, AUTEX Research journal, 2015, V. 3, P. 215.
- Котко, К. А., Ясинская, Н. Н. (2019), Инновационная биотехнология подготовки целлюлозосодержащих текстильных материалов, Сборник научных работ студентов Республики Беларусь "НИРС 2018", Минск, 2019, С. 168-170.
- ГОСТ 938.2-67. Кожа. Метод определения содержания золы. Введ. 1967-30-06. Москва, ИПК Издательство стандартов, 2003, 4 с.
- Пряжникова, В. Г. (2003), Создание и применение препарата на базе ПАВ для интенсифицированной отварки хлопчатобумажных тканей: дисс.... канд. техн. наук, Москва, 2003, 134 с.
- Ясинская, Н. Н., Скобова, Н. В., Котко, К. А. (2018), Применение ферментных препаратов пектинолитического действия для подготовки льняных тканей к колорированию, Вестник Витебского государственного технологического университета, 2018, No 2, С. 104-111.