Exploring the sustainability of E-flow nanobubble technique in denim finishing with an analysis of product quality
Автор: Nahid-ull-islam Md., Md Maruf hasan Sh., Akter M., Kamrul Hassan chowdhury Md., Shahidul Islam sakib Md., Ahamed S., Abu Sayeed Md.
Журнал: Вестник Витебского государственного технологического университета @vestnik-vstu
Рубрика: Химическая технология
Статья в выпуске: 4 (50), 2024 года.
Бесплатный доступ
The apparel industry, specifically the denim washing sector, faces significant sustainability challenges due to its detrimental effects on water contamination and the production of enormous amounts of chemical waste. This study examines using e - flow treatments on denim fabric and evaluates its sustainability using Environment Impact Measuring (EIM) software. E - flow technologies are compelling alternatives to conventional denim finishing methods because they reduce water and chemical use in textile manufacturing. e - Flow Technology uses micronization and nebulization to replace traditional abrasion methods, utilizing air nanobubbles for improved performance chemistry. This technology allows for more flexible finishing operations, conserving water, reducing application costs, and ensuring the right amount of chemicals remain in the garment. The EIM technique assesses the ecological impact of clothes across four key domains: water, chemical, energy, and labor consumption in the production process. The EIM platform aims to evaluate the environmental impact of apparel finishing processes, thereby enhancing the production stage's environmental performance. It is a self accreditation tool for the clothing finishing industry, giving laundromats and garment finishers an advantage in creating greener operations. The study's findings provide valuable insights into the sustainability and comfort elements of e -flow nanobubble finishes in denim production, which can inform future advancements in the textile industry.
Denim, sustainability, e-flow, nanobubble
Короткий адрес: https://sciup.org/142244116
IDR: 142244116 | DOI: 10.24412/2079-7958-2024-4-93-102
Текст научной статьи Exploring the sustainability of E-flow nanobubble technique in denim finishing with an analysis of product quality
УДК 677.027:677.019:504.5 DOI:
-
1 Introduction
Denim has attained the status of a fashion icon due to various technological advancements, such as significant enhancements in spinning, weaving, and finishing processes. Washing is a crucial step in the production of exceptional denim jeans. Customers demand a variety of attributes in their jeans, which is why washing is so important in the denim industry. Denim is a durable 2/1 or 3/1 cotton twill fabric (sometimes called work-wear twill) with a coarse, raw white weft and a blue-dyed warp (Amutha, 2017). The e-flow wash is an environmentally friendly denim finishing technology that uses nanobubbles of air instead of water to transport chemicals onto clothing fabric. It is a mechanical process, no chemical is required. This process is characterized by zero discharge and offers substantial reductions in water consumption and energy usage. In comparison to conventional washing processes, it provides increased flexibility and allows for the production of a wide variety of finishes (Garcia, 2015a). This approach involves introducing atmospheric air into an e-flow reactor and subjecting it to an electromechanical shock, resulting in the generation of nanobubbles and a stream of humid air. The nanobubble mixture is subsequently introduced into a rotating tumbler that contains denim fabric (Figure 1). Nanobubbles disrupt the denim surface, resulting in a gentle tactile sensation and improved shrinkage control (Zouari, Manich, Marti, Gargoubi, & Boudokhane, 2023).
The nanobubble generated by e-flow reactor has an radius of around 1 nanometer and it’s skin is a uniform mix of water, chemicals, and air (Figure 2). This skin is responsible for transforming the properties of chemicals in the garment (Jeanologia, 2024b). The nanobubble carries the liquour on the surface of the fabric and ensures uniform effect after wash.
Air from atmosphere
e-flow reactor
Nanobubbie _ . + Denim (106 bubbles/ cm3)
Revolving tumbler ----------> Processed denim
Figure 1 – Schematic diagram of e-flow softening
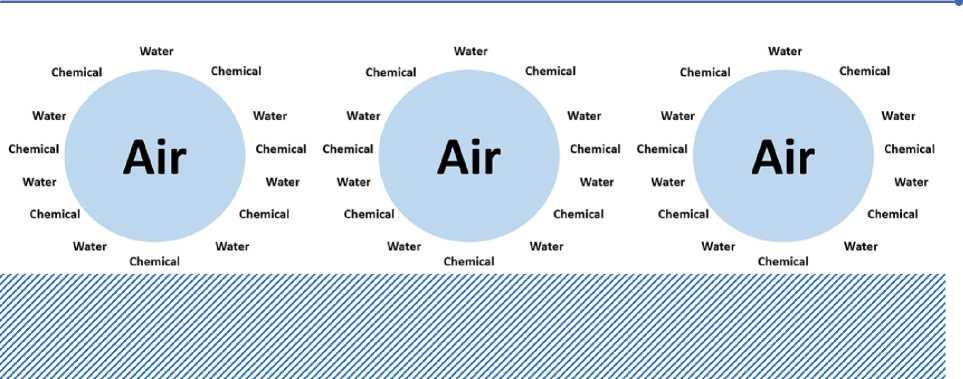
Figure 2 – Nanobubble skin
EIM (Environmental Impact Measuring) software stands out because it is the sole software capable of quantifying the ecological consequences of garment finishing techniques. Additionally, it serves as a powerful self-validation instrument that allows manufacturers, brands, and retailers to monitor the amount of energy, water, and chemicals utilized in the creation of their products, as well as any potential health hazards for personnel. Our objective is to enhance EIM by converting it into a user-friendly platform that integrates another venture. A working group comprising various EIM users integrates further industry initiatives into the tool management, enabling brands and garment finishers to upgrade EIM software according to their interests. The environmentally friendly features of EIM solve problems by reducing the need for energy, water, and less polluted chemicals for easier decision-making. The resolution of a moral dilemma is an additional factor. Removing potentially harmful chemicals and physical labour has a detrimental effect on the health of employees. Avoiding rising product manufacturing costs enables rapid adoption. We will introduce new technology, procedures, or services only when we can produce the ideal product at a cost-neutral rate. This disruptive approach paves the way for genuine progress (Jeanologia, 2024a). The study aims to explore the possibilities of implementing nanobubble technology to obtain eco-friendly denim softening with an analysis of product qualities after e-flow softening.
-
2 Materials and methods2.1 Materials
Six denim pants of large size are collected from a well-established factory in Bangladesh. Table 1 shows the specifications of the materials and methods used for the experiment. The e-flow machine was paired with an industrial washing machine to carry out dry and wet processes.
Denim finish with e-flow softening
Whether made of denim or another type of fabric, the use of a softener smooths and adds a pleasing touch to an article of clothing. The consumer can immediately see the increased value that this provides. Softeners not only enhance the fabric's properties but also prevent clothes from adhering to each other. Figure 3 shows the operation flow chart for e-flow softening. The laser recreates the whisker and the natural ageing process. The finishing was performed with e-flow softening at 50 % NBP (nanobubble percentage), a room temperature of 25 °C, a nanobubble flow of 120 litres per hour, and an 80 rpm centrifuge. Base OT concentrate (highly concentrated softener for natural and synthetic fibres) was used to soften denim. E-flow humidifies the residual ash from the laser. Still, the presence of high moisture levels and
Laser burning
Manual scrapping e-flow softening
Tumbler drying laser burning
Manual breaking localised pigment staining e-flow softening
Tumbler drying
G2 Ozone treatment
Figure 3 – Operation of the flow chart of denim with e-flow softening the surface wearing down can lead to back staining. The application of ozone treatment can effectively resolve this issue (Garcia, 2015a). The primary action of transferring nanobubble to the garment surface is carried out by the micronization method with an optional heating system for better performance.
-
2.2 MethodsEIM (Environmental Impact Measuring) Software
To evaluate the sustainability of e-flow processes, a comparative study was carried out using the EIM software. The impacts on workers, chemicals, water, and energy are divided into separate categories by the EIM score. The program pre-sets an environmental criterion against
Table 1 – Materials and methods with specification
Test Methods
Various testing procedures can be used to ascertain specific characteristics which must meet quality standards. Table 3 displays the various tests and accompanying instruments used in this research study to measure those characteristics. The reputed denim industry in Bangladesh conducted the tests at its inhouse laboratory. The spirality of denim was determined maintaining ISO 6330: 2021 standard. The tear force was measured according to ISO 13937-1: 2000 standard. Seam force and seam slippage were measured using ISO 13934-2: 2014 and ISO 13936-2: 2004 standards respectively. The study experiments were carried out on the instruments mentioned in the table.
-
3 Results and Discussion3.1 Sustainability of e-flow softening
E-flow significantly decreases water usage and allows for the efficient utilization of various resources, optimizing their consumption and making a substantial impact on cutting energy expenses. Table 4 provides a brief overview of the importance of nanobubble technology concerning the use of water, chemicals, and energy while using e-flow. The effectiveness of e-flow softening is evident in its ability to reduce water and chemicals per garment by 94.994 % and 84 %, respectively. Additionally, it indicates that each piece of clothing conserves 0.41 kilowatt-hours (kWh) of energy(Garcia, 2015b).
Table 5 shows the EIM score of water, energy, and chemical for e-flow softening. We can use the EIM score to measure sustainability throughout the production process. Nanobubble technology has a negligible environmental impact in terms of water, energy, chemicals, and worker effects. Water consumption has an EIM score of 23.2, indicating a low influence on water usage (Nahid-Ull-Islam et al., 2024). The energy consumption value also indicates a minimal effect on energy utilization. Chemicals and workers' impact values are low because of the reduced need for labor in e-flow softening, resulting in lower impact ranges.
Table 2 – EIM (Environmental Impact Measuring) software result display
EIM V2.0 |
|||||
Category |
EIM Score Range |
||||
Water |
Energy |
Chemical Impact |
Worker Impact |
||
0–45 |
0–2.5 |
0–33 |
0–13 |
Low impact |
0–33 |
45–90 |
2.5–3.6 |
33–66 |
13–29 |
Medium impact |
33–66 |
+ 90 |
+ 3.6 |
+ 66 |
+ 29 |
High impact |
+ 66 |
Table 3 – Test Methods
Test Name |
Standard |
Instrument |
Spirality |
ISO 6330:2021 |
Spirality tester |
Tear force (N) |
ISO 13937-1:2000 |
Elma tear testing machine |
Seam force (N) |
ISO 13934-2:2014 |
Constant Rate of Elongation machine |
Seam slippage (mm) |
ISO 13936-2:2004 |
Constant Rate of Elongation machine |
Table 4 – Significance of e-flow softening in terms of water, chemical, and energy consumption
Parameters |
Conventional (without nanobubble) |
With nanobubble |
Water (liter/garment) |
33.60 |
1.682 |
Chemical (gram/liter) |
2 |
0.32 |
Energy (kWh/garment) |
1.01 |
0.60 |
Table 5 – EIM score
Category |
EIM Score |
Standard |
Parameter (EIM Score) |
|||
Water |
Energy |
Chemical Impact |
Worker Impact |
|||
Water consumption |
23.2 |
Low impact |
0–45 |
0–2.5 |
0–33 |
0–13 |
Energy use |
2.3 |
Medium impact |
45–90 |
2.5–3.6 |
34–66 |
14–29 |
Chemical consumption |
4 |
High impact |
+ 90 |
+ 3.6 |
+ 66 |
+ 29 |
Workers’ impact |
5 |
-
3.2 Product quality after e-flow softening
Figure 4 shows the visual appearance of the sample before and after e-flow softening. Figures 4(a) and 4(c) depict the front and back of the denim sample before e-flow softening, while Figures 4(b) and 4(d) illustrate the front and back of the denim sample after e-flow softening, showing a modification in the sample's perspective. The degree to which a product meets customer expectations performs as intended, and complies with industry standards is referred to as its quality. This study looks at the way various washing techniques impact product quality and customer preferences.
Spirality is a frequent issue where yarn tends to twist in reverse direction on fabric due to fabric structure, yarn count and finishing of denim.Table 6 illustrates the evaluation of the spirality test after multiple wash cycles of denim after e-flow softening. It can be observed that the spirality percentage of denim after e-flow softening does not exceed the maximum requirement. Accordingly, after 1,2 and 3 wash cycles, the spirality is 1.0 %, 2.0 % and 3.0 % which lies with the requirement. Additionally maintaining spirality helps to prevent creases and wrinkles in the denim fabric, resulting in a smoother finish.
Table 7 demonstrates the tear force of denim after e-flow softening. Tearing force is the average force necessary to continue a tear that has already started in a fabric. Six samples are examined, and the minimum tear force in both the warp and weft directions is 30 and 24, respectively. The results showed that the samples' tear force was within the specified range. For example, in sample 5, the tear force in the warp and weft directions is 37 N and 26 N, respectively, which is within the standard value but greater than the minimal value since the higher the tear force, the better the material can survive the consequences of tearing (Nizam et al., 2023).
Table 8 shows the seam force(N) of denim after e-flow softening the case of an inseam and side seam, the seam force is within the standard range and exceeds the minimum of 260 N. In sample 1, the inseam and side seam values are 266.6 N and 295.4 N, respectively, which are greater than the minimal values. In addition to the inseam and side seam tear force of the seat, the back and front rises are measured. Seam force for the seat, back rise, and front rise are within the range and exceed the minimal amount. The higher the seam force of the sample, the greater the resistance to seam breaking at the inseam, side seam, seat, back rise, and front rise. A
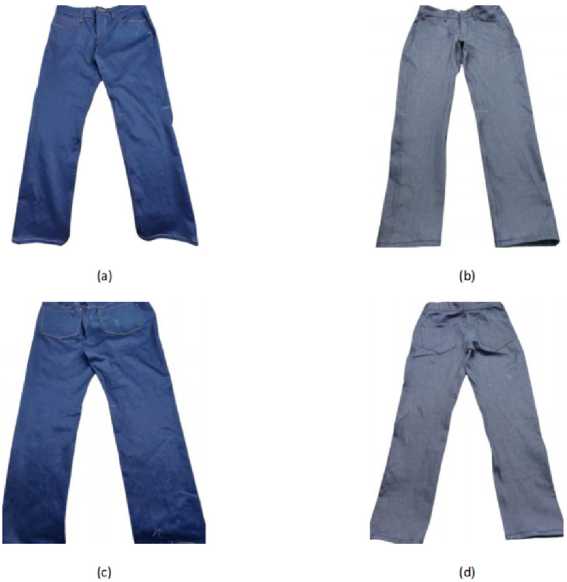
Figure 4 – The visual appearance of the sample before and after e-flow softening: (a) Before sample (front), (b) After sample (front), (c) Before sample (back), (d) After sample (back)
Table 6 – Spirality Test
Left side seam (cm) |
Left fold at the bottom hemmed (cm) |
Spirality (%) |
Requirement (%) |
|
After 1 wash |
49.0 |
0.5 |
1.0 |
3 |
After 3 washes |
48.8 |
1.0 |
2.0 |
|
After 5 washes |
48.8 |
1.2 |
2.5 |
Table 7 – Tear force(N) of denim after e-flow softening
Standard(N) |
Sample 1 |
Sample 2 |
Sample 3 |
Sample 4 |
Sample 5 |
Sample 6 |
|
Warp |
30 min |
40 |
33 |
43 |
32 |
37 |
34 |
Weft |
24 min |
26 |
26 |
32 |
25 |
26 |
26 |
Table 8 – Seam force (N) of denim after e-flow softening
Standard(N) |
Sample 1 |
Sample 2 |
Sample 3 |
Sample 4 |
Sample 5 |
Sample 6 |
|
Inseam |
260 min |
266.3 |
267.4 |
265.9 |
265.9 |
266.0 |
261.4 |
Side seam |
295.4 |
296.5 |
294.0 |
296.5 |
296.5 |
292.3 |
|
Seat |
459.5 |
460.9 |
454.3 |
455.4 |
468.3 |
464.0 |
|
Back Rise |
355.0 |
355.0 |
350.0 |
352.7 |
353.3 |
350.9 |
|
Front Rise |
276.9 |
277.7 |
273.4 |
275.3 |
275.9 |
274.0 |
Table 9 – Seam slippage(mm) of denim after e-flow softening
Standard(mm) |
S1 |
S2 |
S3 |
S4 |
S5 |
S6 |
|
Inseam |
6 max. |
0 |
0 |
0 |
0.5 |
0 |
0 |
Side Seam |
2 |
1.5 |
1.8 |
2.8 |
1.5 |
2.3 |