Finishing of cotton and polyester fabrics using chitosan-containing recipes
Автор: Hoque M., Klinkhammer K., Mahltig B.
Журнал: Вестник Витебского государственного технологического университета @vestnik-vstu
Рубрика: Химическая технология
Статья в выпуске: 3 (46), 2023 года.
Бесплатный доступ
With the increased stress in people’s daily lives, the secretion of sweat from the human body has steadily increased. Therefore, textile industries continue to introduce various products to meet consumers’ demands. Thus far, people use more cotton and polyester fabrics among other textile fabrics in their daily usage or total living period. Textile products, especially those made from cellulose fibers such as cotton, can promote the growth of microorganisms due to their high surface area and moisture retention. In contrast to cellulosic materials, polyester contains no chemically functional or hydrophilic groups. Therefore, it is necessary to ensure wearers’ protection as both cotton and polyester can create unwanted odors due to the decomposition of sweat by microorganisms. The application of chitosan on textile substrates is a useful approach for textile functionalization. Chitosan has been reported as a popular finishing agent due to its intrinsic properties, such as biocompatibility, biodegradability, non - toxicity, abundance in nature, antimicrobial, and antistatic ability, etc. In this study, the solution of chitosan was applied to 100 % cotton and polyester fabrics using a common pad - dry - cure technique. The resulting fabrics were characterized by drop - test, scanning electron microscopy (SEM), and color measurement. Thus, this study presents a small overview of the finishing using chitosan - containing recipes on both cotton and polyester fabrics.
Dyeing, chitosan, padding, scanning electron microscopy, sem, drop test
Короткий адрес: https://sciup.org/142240538
IDR: 142240538 | DOI: 10.24412/2079-7958-2023-3-84-91
Текст научной статьи Finishing of cotton and polyester fabrics using chitosan-containing recipes
Cotton and polyester fibers play a dominant role in the textile industry. Due to their properties and price, they are the most popular fibers in apparel, home textiles, and industrial textiles [1–4]. In our daily life, our bodies always secrete sweat, enhancing the bacterial growth within the fabric, which can cause unexpected odor and harm human health. It is important to protect the wearers against the escalation of bacteria and diseases [5]. With the increasing awareness of wearers‘ protection, numerous techniques for the surface modification of cotton and polyester fabrics have been performed to give additional functionalities [6]. Chitin is regarded as the second most abundant polysaccharide resource after cellulose [7]. Chitosan is gained from chitin through the deacetylation process. Figure 1 shows the chemical resemblance between cellulose, chitin, and chitosan with a 100 % degree of deacetylation. Chitosan contains different amounts of β-(1 → 4)-linked 2-amino-2-deoxy-β-D-glucopyranose and 2-acetamido-2-deoxy-β-D-glucopyranose residues [8, 9, 10, 11]. Chitosan is nontoxic, biodegradable, and biopolymer which offers antimicrobial function [12, 13, 14, 15, 16].
It has been reported that chitosan possesses excellent deodorizing, moisturizing, biocompatibility, and other attractive properties [17]. The presence of the amino groups in the structure make chitosan soluble at acidic pH. Further, a lower pH and degree of acetylation favors the antimicrobial function of chitosan [18 – 20]. The aim of this study is to evaluate
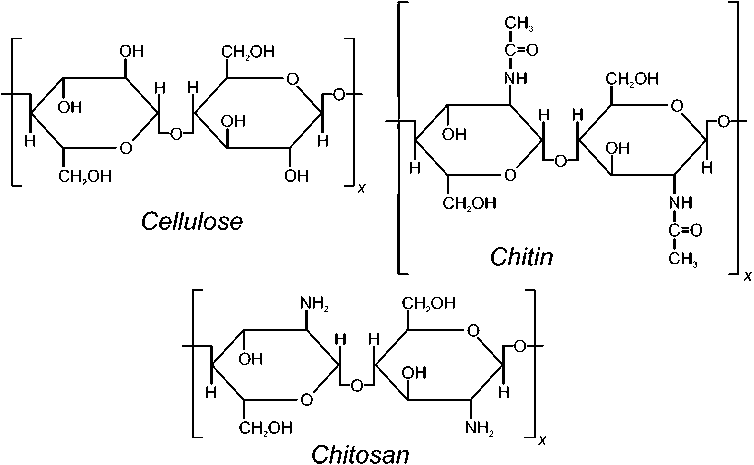
Figure 1 – Comparison of chemical structures of cellulose, chitin, and chitosan
characteristics after finish of cotton and polyester fabrics utilizing chitosan-containing recipes.
MATERIALS AND METHODS
Materials
In this research, different woven cotton and polyester fabrics from the company Technotex GmbH (Lauterbach, Germany) are used. Table 1 shows the description of the woven fabrics used for the experiments. Following chemicals were used: Chitosan with a deacetylation degree of 90 % was purchased from Biolog Heppe® GmbH (Landsberg, Germany), acetic acid from Bernd Kraft GmbH (Duisburg, Germany), and a dispersing agent Dispergator XHT-S from CHT Germany GmbH (Tübingen, Germany).
The padding is performed on a universal padding machine, DL-2500 HV from Feyen Maschinen GmbH (Krefeld, Germany), drying is done using Werner Mathis AG (Zurich, Switzerland)
dryer and a quick dyeing treatment is carried out on a Datacolor Ahiba Pro IR (Marl, Germany) device.
Treatment procedure
Chitosan solutions in 0.5 % concentration were prepared using 250 mL of soft water with 10 mL (w/v) of acetic acid (50 %). The pH value of the acidic solution without chitosan was 1.95. Chitosan powder of 1.30 g was carefully added into the acetic acid solution and stirred until complete dissolution. The pH of the chitosan-containing solution (w/v) was checked before applying between the padding rollers for finishing treatment, which is 2.23. During chitosan treatment on polyester fabrics, similar chitosan concentration was maintained but additionally 10 ml (w/v) of dispersing agent was mixed into the liquor bath. Both cotton and polyester fabrics were cut in size 21.5 cm × 30 cm and weighed to assess the weight gain (%) for before and after treatment.
Table 1 – Fabric description of woven fabrics used for current investigations
Fabric |
No. of warp threads/cm |
No. of weft threads/cm |
Weight per area (g/m 2 ) |
Cotton |
18 |
13 |
200 |
Polyester |
16.5 |
14.5 |
150 |
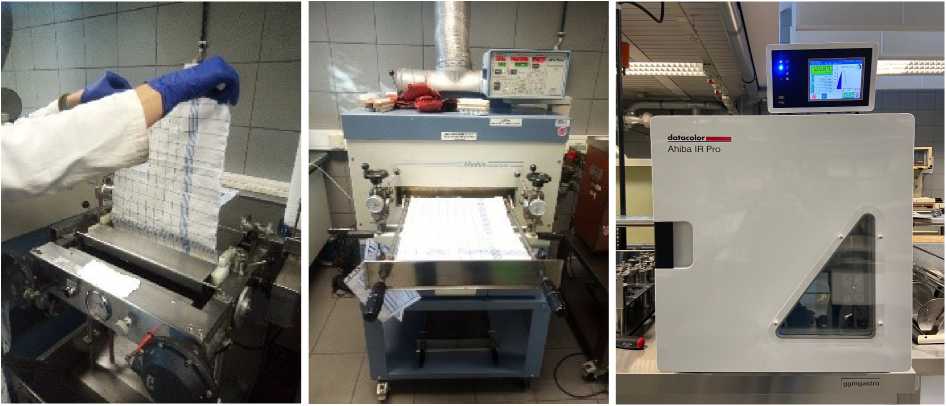
Figure 2 – Photographs of used devices – padding, drying, dyeing (from left to right)
Each sample was run through the rollers four times. The padding procedure was done at room temperature and after padding the fabrics were dried at 90 0C for 5 minutes.
For dyeing, a reactive dye, Remazol Brilliant Red F3B (2 %) from DyStar (Raunheim, Germany) was selected for both cotton and polyester samples including a surface active agent TritonX from Carl Roth GmbH + Co. KG (Karlsruhe, Germany). Treated and untreated samples were cut in size 7 cm × 15 cm and placed in the dye pots with solution of the dyeing machine (Figure 2), where the temperature was set to 40 0C for 5 minutes at 30 revolutions per minute. No extra wash cycle was performed after dyeing, but the dyed samples were rinsed with soft water.
Analytical methods
The fabric surface morphology is observed using a scanning electron microscope (SEM) (Tabletop Microscope TM4000, Hitachi, Japan). The hydrophilic properties of treated and untreated woven fabrics are determined by using TEGEWA-dropt-test with the Patent Blue V solution (0.2 %). On each fabric, three droplets of the dye solution were applied. For the detection of chitosan presence on the treated-dyed and untreated-dyed fabrics, color measurements are evaluated using a Datacolor 400 spectrophotometer from Datacolor Europe GmbH.
RESULTS AND DISCUSSION
In this study, same chitosan concentration (0.5 %) was implemented for both cotton and polyester fabrics by a universal padding machine. It is a simple process, but uneven distribution of the solution will always be a big issue as the samples are handled and run through the rollers completely manually. It is not easy to maintain the 100% precision of handwork and similarly liquor between the rollers stays in nonequilibrium state, as fluidity seemed not same for the left, right, and middle. However, the drop-test, color measurement will give small overview of chitosan presence on the fabric surface.
Wet gain assessment
The wet pick-up is determined to support information about the wetting properties of treated fabrics and is calculated using the following equation:
Список литературы Finishing of cotton and polyester fabrics using chitosan-containing recipes
- Liu, Z., Luo, Y., Zhao, X. Zheng, K., Wu, M. and Wang, L. (2022), A natural antibacterial agent based on modified chitosan by hinokitiol for antibacterial application on cotton fabric, Cellulose, 2022, 29(4), pp. 2731-2742. DOI: 10.1007/s10570-022-04456-2.
- Hoque, M.T. and Mahltig, B. (2020), Realisation of polyester fabrics with low transmission for ultraviolet light, Coloration Technology, 2020, 136(4), pp. 346-355. DOI: 10.1111/cote.12470.
- Hoque, M. T., Mazumder, N. U. S. and Islam, M. T. (2021), Enzymatic wet processing. In: Rather, L.J., Shabbir, M., Haji, A., Eds., Sustain. Pract. Text. Ind., Scrivener Publishing LLC, 2021, pp. 87-110. DOI: 10.1002/9781119818915.ch4.
- Mahltig, B., Rabe, M. and Muth, M. (2019), Textiles, Dyeing, and Finishing, In: Kirk-Othmer Encyclopedia of Chemical Technology, Wiley Blackwell, 2019, pp. 1-35. DOI: 10.1002/0471238961.0609140903011201. a01.pub2.
- Ye, W., Xin J.H., Li, P., Lee, Kam-Len D. and Kwong, T.-L. (2006), Durable antibacterial finish on cotton fabric by using chitosan based polymeric.pdf, J. Appl. Polym. Sci, 2006, 102(2), pp. 1787-1793. DOI: 10.1002/ app.24463.
- Xu, O. B., Xie L., Diao, H., Li, F., Zhang, Y. Y., Fu, F. Y. and Liu, X. D. (2017), Antibacterial cotton fabric with enhanced durability prepared using silver nanoparticles and carboxymethyl chitosan, Carbohydr. Polym., 2017, 177, pp. 187-193. DOI: 10.1016/j.carbpol.2017.08.129.
- Rahman Bhuiyan, M. A., Hossain, M. A., Zakaria, M., Islam, M. N. and Zulhash Uddin, M. (2017), Chitosan Coated Cotton Fiber: Physical and Antimicrobial Properties for Apparel Use, J. Polym. Environ., 2017, 25(2), 334-342. DOI: 10.1007/s10924-016-0815-2.
- Riaz, S. and Munir, A. (2020), Recent Advancemnets in Development of Antimicrobial Textiles. In: Shahid, M., Adivarekar, R., Eds., Advances in Functional Finishing of Textiles, Springer, 2020, pp. 129-168. DOI: 10.1007/978-981-15-3669-4_6.
- Grgac, S. F., Tarbuk, A., Dekanic, T., Sujka, W. and Draczynski Z. (2020), The chitosan implementation into cotton and polyester/cotton blend fabrics, Materials (Basel)., 2020, 13(7). DOI: 10.3390/ma13071616.
- Dutta, J., Tripathi, S. and Dutta, P. K. (2012), Progress in antimicrobial activities of chitin, chitosan and its oligosaccharides: a systematic study needs for food applications, Food Sci Technol Int, 2012, 18(1), pp. 3-34. DOI: 10.1177/1082013211399195.
- Rath, G., Hussain, T., Chauhan, G., Garg, T. and Goyal, A. (2015), Collagen nanofiber containing silver nanoparticles for improved wound-healing applications, J. Drug Target., 2015, 24(6), pp. 520-529, DOI: 10.3109/1061186X.2015.1095922.
- Zhang, Z., Ma, Z., Leng, O. and Wang, Y. (2019), Eco-friendly flame retardant coating deposited on cotton fabrics from bio-based chitosan, phytic acid and divalent metal ions, Int. J. Biol. Macromol., 2019, 140, pp. 303-310. DOI: 10.1016/j.ijbiomac.2019.08.049.
- Iheaturu, N. C., Aharanwa, B. C., Chike, K. O., Ezeamaku, U. L., Nnorom, O. O and Chima, C. C. (2019), Advancements in Textile Finishing, IOSR J. Polym. Text. Eng., 2019, 6(5), pp. 23-31. DOI: 10.9790/019X-06052331.
- Kamel, M. Y. and Hassabo, A. G. (2021), Anti-Microbial Finishing for Natural Textile Fabrics, J. Text. Color. Polym. Sci., 2021, 18(2), pp. 83-95. DOI: 10.21608/jtcps.2021.72333.1054.
- Choi, C., Nam, J.-P. and Nah, J.-W. (2016), Application of chitosan and chitosan derivatives as biomaterials, J. Ind. Eng. Chem, 2016, 33, pp. 1-10.
- Toskas G., Cherif, C., Hund, R.-D., Laourine, E., Mahltig, B., Fahmi, A., Heinemann, C., Hanke, T. (2013), Chitosan(PEO)/silica hybrid nanofibers as a potential biomaterial for bone regeneration, Carbohydr. Polym., 2013, 94(2), pp. 713-722. DOI: 10.1016/j.carbpol.2013.01.068.
- Tian, X., Hua, T., Poon, T., Yang, Y., Hu, H., Fu, J., Li, J. and Niu, B. (2022), Study on Effects of Blending Fiber Type and Ratio on Antibacterial Properties of Chitosan Blended Yarns and Fabrics, Fibers Polym., 2022, 23(9), pp. 2565-2576. DOI: 10.1007/s12221-022-0052-3.
- Hosseinnejad, M. and Jafari, S. M. (2016), Evaluation of different factors affecting antimicrobial properties of chitosan, Int. J. Biol. Macromol., 2016, 85, pp. 467-475. DOI: 10.1016/j.ijbiomac.2016.01.022.
- Hoque, M. T., Klinkhammer, K. and Mahltig, B. (2023), HT process for treatment of PET fabrics with chtiosan-containing recipes, CDATP, 2023, 4(2), pp. 222-230. DOI: 10.25367/cdatp.2023.4.p222-230.
- Hoque, M.T., Benrui, T., Grethe, T. and Mahltig, B. (2023), HT process for treatment of PET fabrics with chtiosan-containing recipes, CDATP, 2023, 4(2), pp. 187-200. DOI: 10.25367/cdatp.2023.4.p187-200.