Формирование конструктивно-технологических параметров сборочных и резьбообразующих операций на основе самоорганизующихся имитационных моделей
Автор: Березин С.Я., Кулеш И.М., Шигаева Е.В.
Журнал: Известия Самарского научного центра Российской академии наук @izvestiya-ssc
Рубрика: Машиностроение
Статья в выпуске: 1-2 т.12, 2010 года.
Бесплатный доступ
В статье рассмотрены проблемы разработки сложных технологических процессов, характеризующихся значительным объемом различных параметров. Для решения проблем предлагается система имитационного моделирования, которая позволяет автоматически устанавливать оптимальные значения параметров, обеспечивающих надежный ход самого технологического процесса, а также показатели конечного продукта, как результат его организации.
Имитационное моделирование, технологический процесс, оптимальные параметры
Короткий адрес: https://sciup.org/148198923
IDR: 148198923
Текст научной статьи Формирование конструктивно-технологических параметров сборочных и резьбообразующих операций на основе самоорганизующихся имитационных моделей
Кулеш Ирина Михайловна, аспирантка Шигаева Елена Вадимовна, аспирантка
Одна из первых попыток создания подобных моделей применительно к резьбообразующих и резьбосборочным операциям предпринята в работе [2]. В ней процесс рассматривается как система, на которую одновременно воздействует масса параметров, носящих детерминированный и случайный характер. Их проявление может непредсказуемым образом влиять на результаты технологического процесса, характеристики получаемых резьбовых поверхностей и соединений. Системное представление операции связанно с анализом большого количества информации, относящейся к различным структурным составляющим системы. Первым этапом разработки является параметрический анализ, основанный на детальном изучении производства технологической операции и ее материального обеспечения. Следующим этапом является имитационное моделирование, в результате которого формируется виртуальная вычислительная параметрическая модель, отражающая ход выполнения операции. Испытание данной модели позволяют установить такие условия, которые обеспечивают высокие качественные показатели, например, процесса сборки и получаемых соединений.
Структурная схема имитационной системы, разработанной для сборочно-резьбообразующих процессов представлена на рис. 1. Вначале производится ввод исходных данных D 1 , которые включают диаметры резьбы и допуски, шаг, глубина завинчивания, твердость корпусного материала и т.д. На их основе производится расчет промежуточных данных:
диаметр отверстия под резьбу, осевое усилие наживления, необходимую изгибную жесткость завинчивающей оснастки, предельный угол смещения крепежной детали, предельный крутящий момент и прочие ( D 2 ). На основе этих данных, а также на ранее полученных экспериментальных моделях рассчитываются данные сборочного процесса D 3
D з э I ( M кр , to, ® h , P u , A M , N , T , )
, где Mкр; ΔМ – крутящий момент сборки и амплитуда его колебаний соответственно; ω, ωН – угловая скорость завинчивания и наживле-ния соответственно; PU – изгибающее усилие в момент наживления; N – затраты мощности на сборку; Тз – время завинчивания.
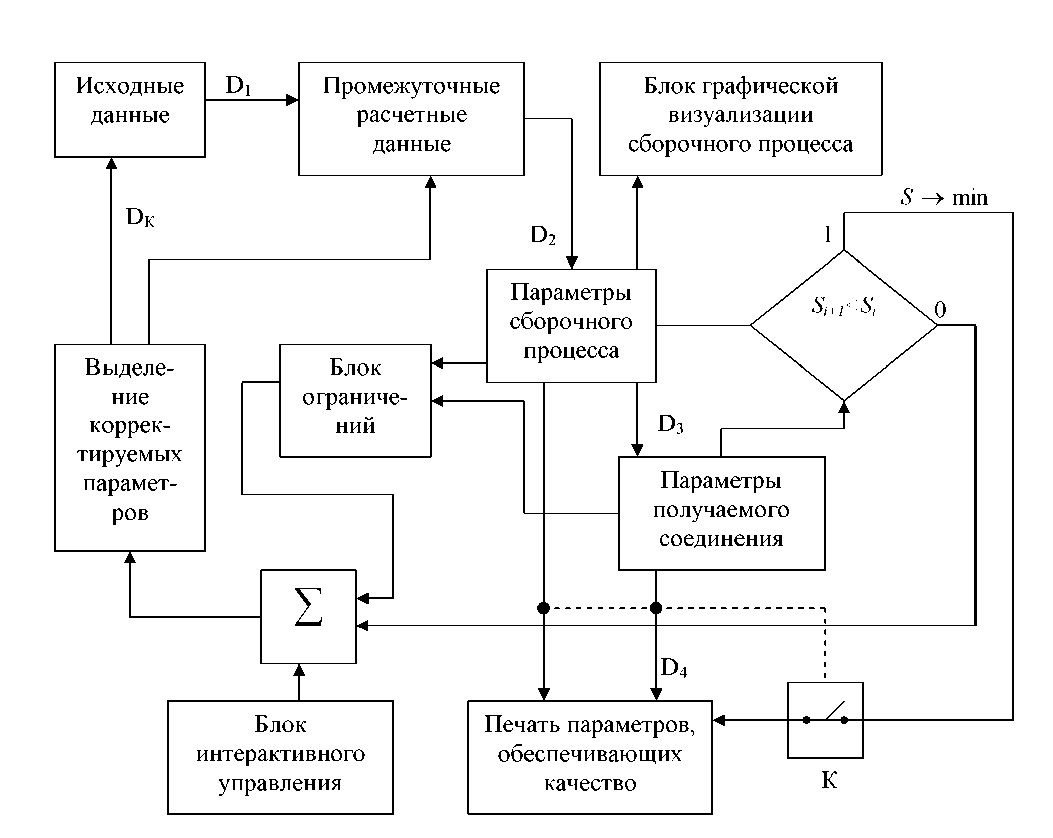
Рис. 1. Блок-схема имитационной модели сборочно-резьбообразующего процесса
Данные D 3 графически представляются в блоке визуализации во временном или пошаговом масштабе, например M кр = f (z) , где z – номер витка резьбы на глубине завинчивания. Далее рассчитываются параметры получаемого соединения D 4 , образующие следующую совокупность
D4 э I(Kc, Q, dik, Hупр, Уф ) , где Kс – коэффициент эффективности стопорения; Q – прочность витков резьбы; d1k – внутренний диаметр сформированной резьбы гнезда; Hупр – глубина упрочнения внутренней резьбы; γф – фактический угол перекоса оси установленной крепежной детали.
Оценка качества выполнения операции и получаемых соединений производится на основе комплексной целевой функции, в которую входят часть параметров D 3 и D 4
5 = a 1 Kc + a 2 K h + a 3 Kt + a 4 K A +
+ a5 KM + a6 Kg + a7 KN ^ min где a1…a7 – приоритетные оценочные коэффициенты; Kh – коэффициент полноты сформированного резьбового профиля; Kt – коэффициент производительности; KΔ – коэффициент стабильности протекания процесса завинчивания; KM – коэффициент силовой напряженности процесса; Kδ – коэффициент интенсивности радиальных давлений в резьбовом контакте; KN – коэффициент затрат мощности на процесс.
Расчетные формулы коэффициентов приведены в работе [3].
Перед вычислением целевой функции S данные D 3 и D 4 поступают в блок ограничений, где проверяется выполнение ряда условий:
W \ ^ тяV ;
max уф ^ y р;
' М к + АМ <[ М J
5 <5
С7< ^max ,
где ω max – предельное значение угловой скорости; γ р – расчетный угол перекоса крепежной детали; δ max - предельное значение припуска.
Если определенные условия не выполняются, то вначале выделяются, а затем корректируются те параметры, которые приводят к выполнению этих условий. После этого повторяется вся цепочка вычисления параметров D 1 , D 2 , D 3 , D 4 и функции S i . В состав корректируемых параметров входят следующая совокупность, которая относится ко всем четырем группам ( D 1 – D 4 )
D k Э 1 ( 7 ; , T 0 , l,Ф,d 0 , f 0 ,n,to,HB , P )
где Т d , Т 0 – допуски наружного диаметра охватываемой резьбы и диаметра отверстия гнезда соответственно; l – глубина завинчивания; φ – угол фаски на торце резьбообразующей детали;
d 0 – диаметр отверстия под резьбу; η – коэффициент полноты внутреннего резьбового профиля; НВ – твердость материала гнезда; Р – шаг резьбы.
Их изменения, как правило, не связанны с жесткими требованиями чертежа и технического задания. Однако, два последних (
НВ
,
Р
) не входят в это число, но, тем не менее, при невыполнении условий системы (1), приходиться корректировать и их. Например, при высоких значениях крутящих моментов, переходят к меньшим шагам или некоторому снижению твердости материала. После повторной коррекции и вычислений, рассчитывается значение
S
i+1
и т.д., до тех пор, пока не выполняется условие
S
i+1
i
и все условия в блоке ограничений. Тогда будет считаться, что
S
i+1
=S
min
и сформируется команда
К
, которая приведет к печати всех интересующих параметров сборки.
Сущность взаимосвязей между исходными, промежуточными и результирующими параметрами носит различный характер вероятностный, силовой, геометрический (конструктивный), физико-механический и т.д. Общая схема связей представлена на рис. 2.
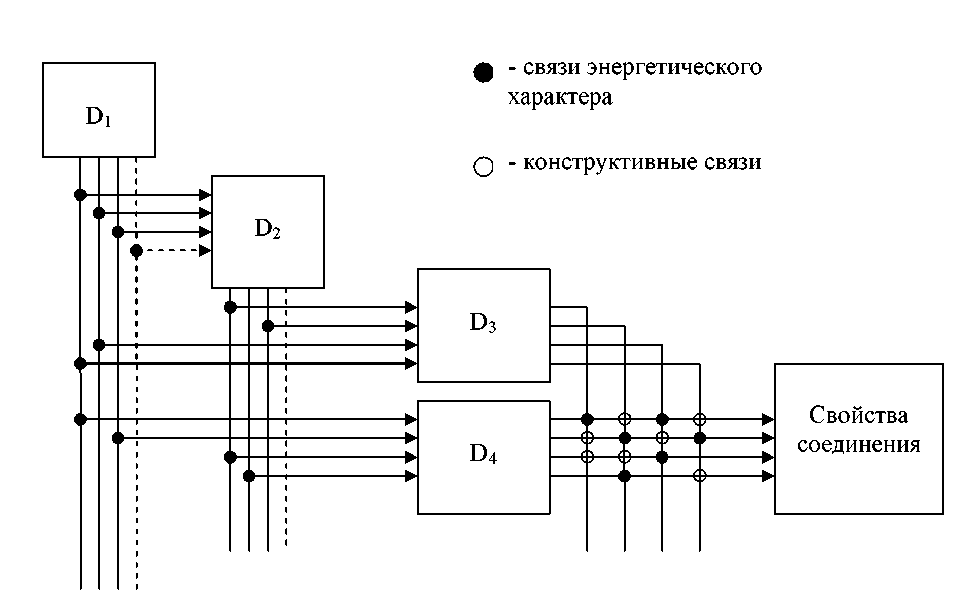
Рис. 2. Структура формирования взаимосвязей между расчетными параметрами имитационной системы
Указанная структура установлена на основе разработанного единого аналитического аппарата, включающего теоретические и экспериментальные формулы параметров групп D2, D3, D4, а также соотношения вероятностного характера, в которых параметры представлены в виде спектров распределения с величинами математических ожиданий, доверительных интервалов, коэффициентов асимметрии и т.д. В этом случае параметры, условия реализации процесса и значения целевой функции вычисляются по соответствующей методике обработки статистических данных. Временные показатели хода реализации процесса отображаются в блоке визуализации, фрагмент которого представлен на рис. 3. Графическое представление величин позволяет оперативно реализовать на создавшуюся ситуацию и вносить определенные коррекции параметров DK через блок интерактивного управления.
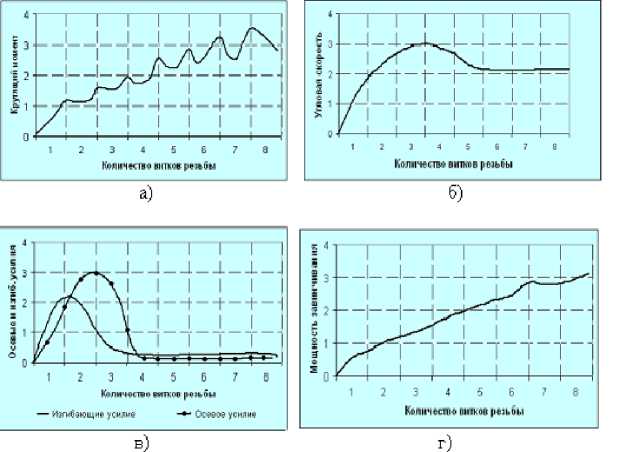
Рис. 3. Представление расчетных величин выполнения операций:
а) кривая крутящего момента; б) характер изменения угловой скорости;
в) кривая изменения осевых и изгибающих усилий; г) график мощности завинчивания
Выводы: применение подобных систем имитационного моделирования позволяет автоматизировать процесс получения оптимальных конструктивно-технологических параметров сборочной операции, а также готовить данные для разработки материальной части сборочных машин и их систем управления.
Список литературы Формирование конструктивно-технологических параметров сборочных и резьбообразующих операций на основе самоорганизующихся имитационных моделей
- Никиферов, А.Д. Современные проблемы в области технологии машиностроения: Учебное пособие/А.Д. Никиферов. -М.: Высшая школа, 2006. -392 с.
- Березин, С.Я. Имитационное моделирование условий автоматической сборки резьбовых соединений/С.Я. Березин, Е.В. Щербаков//Матер. VIII Всероссийская научно-практическая конференция «Кулагинские чтения». -Чита: ЧитГУ. -2007. -В. IV. -С. 21-23.
- Березин, С.Я. Моделирующие системы в среде технологического обеспечения сборочно-резьбообразующих операций. Монография/С.Я. Березин, Р.Е. Чумаков. -Чита: Поиск, 2004. -202 с.