Градиентные антифрикционные серебряно-алмазные покрытия
Автор: Ненашев М.В., Ибатуллин И.Д., Галлямов А.Р., Иванов А.Н.
Журнал: Известия Самарского научного центра Российской академии наук @izvestiya-ssc
Рубрика: Системные разработки трибологии машин и приборов
Статья в выпуске: 4-3 т.13, 2011 года.
Бесплатный доступ
В статье описаны физико-механические и триботехнические свойства антифрикционных градиентных серебряно-алмазных покрытий, осаждаемых из бесцианистых электролитов на асиметричном переменном токе.
Серебряно-алмазное покрытие, положительный градиент механических свойств, структура, физико-механические свойства, асимметричный переменный ток
Короткий адрес: https://sciup.org/148200216
IDR: 148200216
Текст научной статьи Градиентные антифрикционные серебряно-алмазные покрытия
Иванов Александр Николаевич, аспирант кафедры нанотехнологий в машиностроении без использования высоких температур и т. д. В триботехнике, как известно, находят применение как пластичные, так и твердые покрытия. Первые облегчают приработку, снижают трение, повышают нагрузочную способность и антизадирные свойства узла трения (баббиты, медь, серебро, золото и др.). Вторые упрочняют поверхность, снижают износ деталей (хром, нитрид титана и др.).
Одним из направлений, разрабатываемых в лаборатории наноструктурированных покрытий Сам-ГТУ, является создание высокоэффективной технологии нанесения антифрикционных серебряноалмазных покрытий. Ценность серебра как антифрикционного материала определяется его уникальными свойствами. Серебро обладает самой высокой электро- и теплопроводностью. Твердость электро-осажденного серебра 590-1370 МПа. Для повышения твердости, износостойкости и стойкости к потускнению серебряных покрытий используют легирование серебра другими металлами.
Коэффициент сухого трения серебряных покрытий по стали 0,14-0,19. Серебро проявляет хорошие антифрикционные свойства в атмосфере, вакууме, инертных средах, маслах, не содержащих значительных количеств серы, некоторых агрессивных средах. [5,6]. Серебро отличается высокой химической устойчивостью, растворяется только в концентрированной азотной кислоте и горячей серной (85 %-ной). По коррозионной стойкости серебро практически относится к благородным, т. е. не окисляющимся на воздухе, металлам.
Основными проблемами, связанными с нанесением серебряных покрытий в отечественном машиностроении, являются следующие. Для электрохимического серебрения чаще всего используют высокотоксичные цианистые электролиты, содержащие до 100 г/л цианистого калия. Известны и менее токсичные – дицианоаргентатные электролиты, но их применение затруднено из-за недостаточного качества осаждаемого серебра. Кроме того, опыт исследования различных покрытий показал явное превосходство качества зарубежных серебряных покрытий по сравнению с отечественными, что делает весьма актуальной задачу совершенствования технологии серебрения.
В целях повышения безопасности технологического процесса серебрения и обеспечения высоких эксплуатационных свойств получаемых покрытий использован ряд технических решений, включающий: 1) использование бесцианистых электролитов серебрения с добавкой водной суспензии ультра-дисперсных алмазов (УДА); 2) осаждение покрытий с применением асимметричного переменного тока и с меняющимся в процессе осаждения соотношением катодного и анодного токов, позволяющим получать покрытия с положительным градиентом механических свойств; 3) разработку технологии детонационной активации УДА; 4) создание новых методов контроля газонасыщения деталей с покрытиями.
Электронно-микроскопические исследования серебряно-алмазных покрытий показали (рис. 1), что получаемые осадки имеют равномерную сплошную (беспористую) структуру. Цвет покрытия белый полублестящий или матовый. Матовость покрытия обусловлена появлением на поверхности при осаждении кристаллов серебра, размерами несколько микрометров. Покрытие получается равномерным по толщине. Средняя толщина антифрикционных покрытий составляет 10…20 мкм.
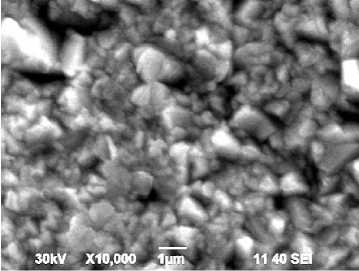
а
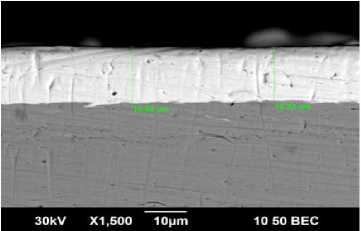
б
Рис. 1. Вид серебряно-алмазного покрытия. а) поверхность; б) поперечный срез.
Электронно-микроскопические исследования показали, что размеры зерен осадков серебра составляют в среднем 3…5 мкм (рис. 2 а). На субзеренном уровне выделяются блоки, размерами около 0,5 мкм. На поверхностях трения видны наночастицы УДА размерами 40…70 нм (рис. 2 б).
Одним из триботехнических принципов повышения стойкости поверхностей к задирам, разработанных И.В. Крагельским, является формирование положительного градиента механических свойств. Разработанная технология серебрения обеспечивает получение положительного градиента механических свойств осадка (повышения микротвердости по глубине) путем управления коэффициентом асимметрии переменного тока. Вблизи подложки наносится твердый мелкокристаллический осадок, вблизи поверхности зерна делаются крупнее и менее твердыми (рис. 3).
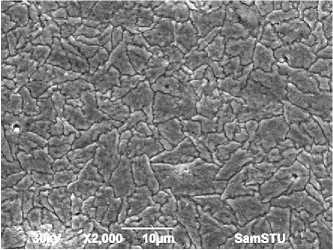
а
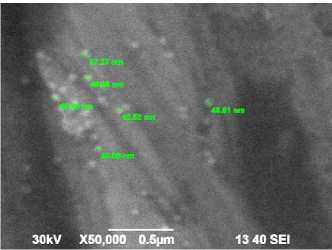
б
Рис. 2. Микро- и наноструктура серебряноалмазного покрытия.
а) микроструктура осажденного покрытия; б) наноалмазы (светлые точки) на приработанной поверхности серебряного покрытия.
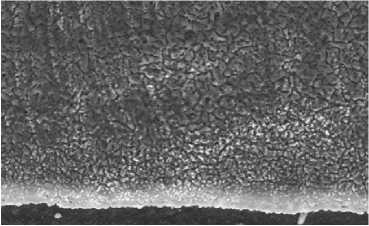
Рис. 3. Структура градиентного покрытия (×5000) на косом шлифе.
Структура серебряного покрытия, полученного из цианистого электролита с добавкой сурьмы в исходном состоянии близка к структуре серебряноалмазного покрытия, полученного из бесцианистого электролита, но в процессе трения проявляются заметные различия в свойствах и структуре данных покрытий. Покрытия с добавкой сурьмы в процессе трения проявляют склонность к охрупчиванию и развитию трещин (рис. 4 а), наблюдается измельчение зерен. Серебряно-алмазные покрытия (рис. 4 б) длительное время сохраняют пластичность и, соответственно, высокие защитные свойства.
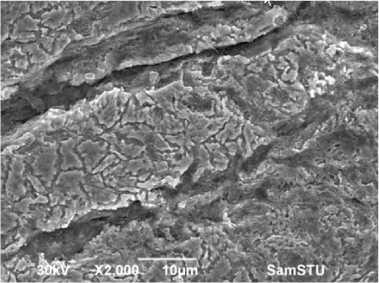
а
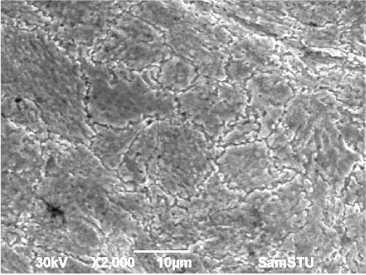
б
Рис. 4. Структура поверхностей трения серебряных покрытий:
а – с добавкой сурьмы; б – с добавкой УДА
Для электрохимического серебрения на ассимет-ричном переменном токе разработана автоматизированная гальваническая установка (рис. 5). Установка, разработанная на основе программируемого контроллера со встроенным микропроцессором, позволяет осуществлять автоматизированное управление электролизом по заданной программе с возможностью выбора тока произвольной формы (постоянный, переменный, импульсный, ассиметричный и др.), задания величины и длительности импульсов прямого и обратного токов, паузы между ними, положительного или отрицательного смещения постоянной составляющей тока, обеспечение стабилизации по току и по напряжению.
Отличительной особенностью установки является возможность формирования импульсов с различной крутизной фронта и различной частотой асимметричного переменного тока с регулируемым коэффициентом асимметрии. Основные технические характеристики: максимальный ток нагрузки 50А; точность задаваемого тока нагрузки 0,1А; длительность импульса тока 1-0,005 с; длительность одного цикла программы – не ограничено; количество возможных циклов в программе -10; питание от сети 50 Гц напряжением 220 В; габариты - 200X 500X250 мм.
Программирование гальванической установки возможно как с пульта управления, так и непосредственного с компьютера. Программа ведет учет, и запись формируемых эпюр текущих параметров электролиза (тока и напряжения на выходе источника, напряжения на электродах в гальванической ванне, температуры электролита, удельной проводимости электролита) на протяжении всего процесса нанесения покрытия.
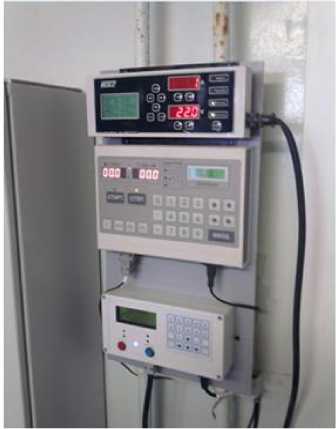
Рис. 5. Пульт гальванической установки для нанесения электрохимических покрытий на асимметричном переменном токе.
В процессе нанесения покрытия реализуется предварительно запрограммированная последовательность технологических режимов осаждения покрытий. При этом имеются достаточно широкие возможности по управлению технологическими режимами нанесения покрытий, включая выбор соотношения анодного и катодного токов (от 1/1,2 до 1/10), плотности тока и частоты (1…200 Гц).
Лабораторные исследования наноструктуриро-ванных серебряно-алмазных покрытий показали, что износостойкость серебряно-алмазного покрытия, осажденного в бесцианистом электролите до 2,5 раз превосходит износостойкость серебряного покрытия, полученного в цианистом электролите, при этом также улучшаются антифрикционные и противозадирные свойства (6,7).
Натурные испытания образцов с серебряноалмазными покрытиями на деталях опор буровых долот показало двукратное повышение ресурса. Исследование противоизносных свойств опытных стальных шайб с предлагаемым покрытием показало при осевой нагрузке 1500 кгс момент трения 1,5 кгс м и весовой износ 0,008г (при среднем износе штатной пары трения 0,017 г).
Промысловые испытания серийного долота, при изготовлении которого использована новая технология серебрения, проведенные в Сологаевском месторождении при наклонно-направленном бурении показали, что после отработки долота в течение 67 часов наблюдается значительный износ шарошек с частичным выпадением твердосплавного вооружения. При этом все три опоры сохранили работоспособность (люфтов и заеданий при повороте шарошек не наблюдается).
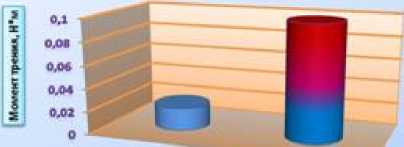
a
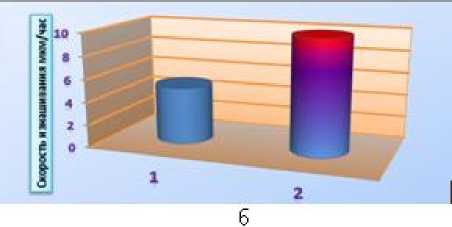
Рис. 6. Результаты сравнительной оценки серебряных покрытий: а) момент трения; б) скорость изнашивания; 1 - серебряно-алмазные покрытия, осажденные в бесцианистом электролите; 2 - серебряные покрытия, полученные в цианистом электролите.
Область применения антифрикционных наност-руктурированных серебряных покрытий: токонесущие детали радиоэлектронной и электротехнической аппаратуры (рис. 8 а), для защиты химических аппаратов и приборов, для покрытия трущихся поверхностей подшипников скольжения и качения в машиностроительной промышленности (рис. 8 б), для декоративных целей в ювелирной и легкой промышленности.
При использовании суспензий наночастиц ульт-радисперсных алмазов возникает необходимость их первоначальной подготовки и активирования перед использованием в технологическом процессе нанесения электрохимических покрытий. Суспензии представляют собой гетерогенные смеси частиц твердых материалов и чаще всего приготовлены на водной основе, иногда с добавками поверхностноактивных веществ (ПАВ). В них часто содержатся значительные количества таких примесей, как сажа, графит и др., что объясняется технологией их получения. Такие суспензии при их длительном хранении склонны к соосаждению и образованию довольно крупных конгломератов, состоящих из весьма значительного количества мелкодисперсных частиц. Размеры подобных конгломератов могут достигать 40 – 70 нм. (рис.9).
Механические способы их измельчения и диспергирования могут быть весьма трудоемкими и малоэффективными.
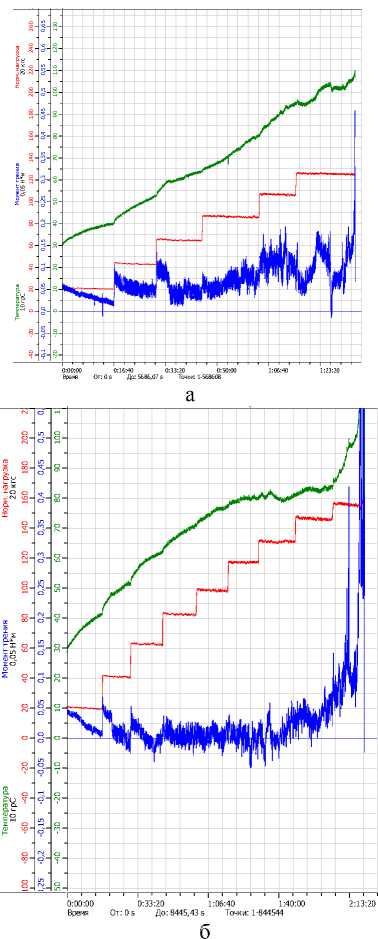
Рис 7 . Эпюры сравнительных триботехнических испытаний покрытий в режиме ступенчато возрастающей нагрузки: а) штатное серебряное покрытие из цианистых электролитов (нагрузка схватывания 110 кгс); б) наноструктурированное серебряноалмазное покрытие (нагрузка схватывания 160 кгс).
Разработанный способ диспергирования суспензий с УДА, заключающийся в том, что диспергирование жидкости и взрыв, происходят в смежных емкостях, разделенных друг от друга перегородкой (мембраной) не препятствующей прохождению ударной волны, но предотвращающей попадание продуктов взрыва в обрабатываемую жидкость. Причем для возможности широкого применения данного способа в качестве взрывчатых веществ предложено использовать не твердые ВВ, а газовые смеси, в частности пропан-бутановые, ацетиленкислородные и др.
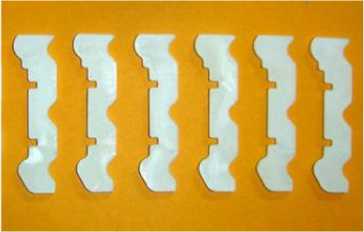
а
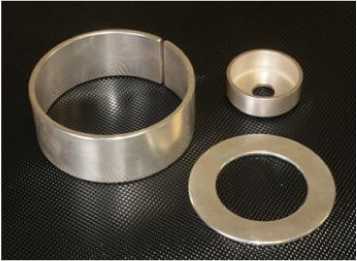
б
Рис. 8. Область применения серебряно-алмазных покрытий: а – ламели; б – плавающие элементы опор буровых долот (втулка, шайба, колпачек).
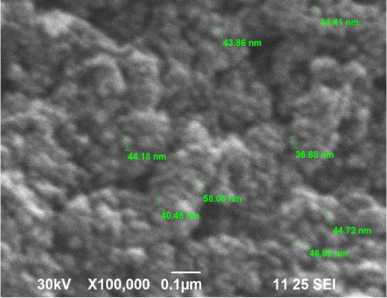
Рис. 9 . Конгломераты наночастиц ультрадис-персных алмазов.
Для реализации данного способа в УПБ «Роща» СамГТУ изготовлена экспериментальная установка (рис. 10), включающая два основных элемента: 1) промышленно выпускаемый автоматизированный детонационный комплекс (пушки моделей «Обь», «Дракон» и др.), с помощью которой создаются мощные ударные волны, формируемые при взрыве детонирующей газовой смеси (50% ацетилен + 50% кислород); 2) реактор, состоящий из двух камер – загрузочной и детонационной.
В загрузочную камеру заливают порцию обрабатываемой суспензии УДА. В отверстие детонацион- ной камеры вставляют срез пушки. При выстрелах пушки энергия ударной волны передается из детонационной в загрузочную камеру через мембрану с закрепленными на ней штыревыми резонаторами.
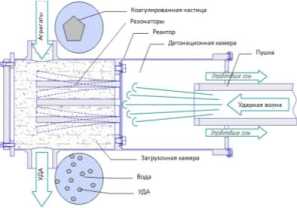
Рис. 10. Схема реактора экспериментальной установки для активации водной суспензии УДА.
Данная конструкция экспериментальной установки позволяет в широком диапазоне исследовать и оптимизировать технологические параметры детонационной обработки жидкости, включая коэффициент заполнения ствола газовой смесью, частоту и количество выстрелов, количество и форма резонаторов, расстояние от среза ствола до мембраны и др. Данная установка позволяет получать чистую суспензию с УДА, при этом технологичская операция является энергосберегающей (поскольку используется энергия химической реакции недефицитных газов).
Технические характеристики экспериментальной установки: габариты (механическая часть) – 90 X 1400X1800 мм; масса – 70 кг; объем загрузочной и детонационной камер – 5л; частота выстрелов 4 Гц, потребляемая мощность установки - до 0,6 Вт.
Заключение
-
1. Разработана технология и источник тока для нанесения градиентных антифрикционных серебряно-алмазных покрытий в бесцианистых электролитах на асимметричном переменном токе.
-
2. Показано, что серебряно-алмазные покрытия обладают повышенными триботехническими свойствами и могут найти широкое применение в промышленности.
-
3. Разработан детонационный метод диспергирования агрегатов УДА, позволяющий активировать частицы ультрадисперсных алмазов.
Список литературы Градиентные антифрикционные серебряно-алмазные покрытия
- Кайкарис В.А. Двухфакторная теория блескообразования//Электрохимия, 1967, Т.3, №10, с.1273-1279.
- Шлугер М.А. Гальванические покрытия в машиностроение. Справочник. Т.1. -М.: Машиностроение, 1985. -240с.
- Иванов А.Ф. Гальванотехника для мастеров. -М.: Металлургия, 1990. -208с.
- Зальцман Л. Г., Черная С. М. Спутник гальваника. -3-е изд. -К.: Тэхника, 1989.-191с.
- Гинберг А.М., Иванова А.Ф., Кравченко Л.Л. Гальванотехника. -М.: Металлургия, 1987.-с. 262-263.
- Журнал Всесоюзного химического общества им. Д. И. Менделеева. Т.25, №2, 1980. с. 120.
- Буркат Г.К., Долматов В.Ю. Ультрадисперсные алмазы в гальванотехнике//Физика твердого тела, Т.46, вып. 4, 2004.-с.685-692.