Химико-термическая обработка отвальных никелевых шлаков с целью извлечения никеля и железа
Автор: Веселовский Александр Александрович, Рощин Василий Ефимович, Лайхан Саламат Армангулы
Журнал: Вестник Южно-Уральского государственного университета. Серия: Металлургия @vestnik-susu-metallurgy
Рубрика: Металлургия чёрных, цветных и редких металлов
Статья в выпуске: 4 т.17, 2017 года.
Бесплатный доступ
Оценивается возможность и эффективность применения метода химико-термической обработки (ХТО) отвальных никелевых шлаков хлорсодержащими реагентами с осаждением никеля на железной подложке в шихте. Магнитная сепарация обработанных шлаков извлекает металлические образования после ХТО в концентрат, переплавка которого позволяет получить ферроникель. Немагнитный концентрат и шлак от переплава магнитного концентрата может быть использован в цементной промышленности и в строительстве в качестве щебня или наполнителя бетонов.
Шлак, никель, отвал, переработка шлака
Короткий адрес: https://sciup.org/147157110
IDR: 147157110 | DOI: 10.14529/met170402
Текст научной статьи Химико-термическая обработка отвальных никелевых шлаков с целью извлечения никеля и железа
Проблема переработки шлакоотвалов заводов черной и цветной металлургии является наиболее актуальной в настоящее время не только с точки зрения дополнительного сырья для извлечения цветных металлов и железа, но и с экологической. Утилизация такого сырья в последнее десятилетие стала национальной проблемой для многих государств мира в связи с интенсивным ростом производств и загрязнением окружающей среды.
Обеднение известных рудных месторождений и непрерывный рост производства цветных металлов вызвали научный и промышленный интерес к техногенным отходам металлургических предприятий, рассматривая эти отходы как фактор снижения себестоимости готовой металлопродукции при их вовлечении в процесс производства [1–3]. Вовлечение в производство низкосортных ломов и отходов при производстве никелевых сплавов увеличилось более чем в 1,5 раза [4]. В результате значительно выросли объемы техногенных отходов – шлаков, шламов, пыли и т. д., значительная часть которых до сих пор не используется, складируется в отвалах, хранилищах, отстойниках.
Отвальные никелевые шлаки в твердом состоянии частично перерабатываются чисто механическими методами с целью извлечения металлической фазы – корольков. Никель, кобальт и железо, находящиеся в этих шлаках в виде химических соединений (сульфидов и оксидов), не извлекаются, так как для этого необходимы сложные технологические операции, связанные с тонким помолом и переплавом отвальных шлаков.
Немагнитная фракция отвальных шлаков частично используется для изготовления абразивного порошка для абразивной обработки металлоизделий в качестве щебня для строительства дорог неответственного назначения, железнодорожных насыпей и т. п. При этом часть элементов теряется безвозвратно.
Поэтому, анализируя вышеизложенное, можно заключить, что экономия и резкое снижение уровня потерь цветных металлов при производстве готовой продукции – одна из приоритетных задач современного развития металлургического производства. Учитывая, что их решение должно удовлетворять требованиям экологии, актуальной представляется разработка и внедрение альтернативных технологий переработки техногенных отходов с получением готовой продукции.
Материалы, оборудование и методика проведения экспериментов
Исследованию подвергались складированные отвальные шлаки ЮУНК усредненного состава, находящиеся в отвалах на настоящий момент. Состав отвального шлака приведен в табл. 1.
Шлак измельчался в мельнице методом истирания до фракции 0,16 мм (основная часть на калиброванном сите) на машине истирания модели ИДА-175 Уфимского производства, фото которой представлено на рис. 1.
Для проведения восстановительного обжига использовался в качестве восстановителя хлористый аммоний, разлагающийся при температуре 350 °С на хлороводород и аммиак, при более высоких температурах роль восстановителя играет свободный хлор. Дополнительно в шихту вводился кокс.
Реакционная шихта для обжига состояла из 98 % масс. шлака и 2 % масс. NH 4 Cl. Обжиг проводился при температуре 1000 °С в течение 1–8 ч в спроектированной лабораторной установке на базе нагревательной трубной печи СУОЛ, схема которой представлена на рис. 2.
Работа установки происходит следующим образом. Камера нагрева с цилиндрическим муфелем, электронагревателем и датчиком температуры с помощью механизма поворота устанавливается в вертикальное положение (пунктирные линии на рис. 2). Реакционная шихта заполняет 90–95 % объема реторты для возможности перемешивания при вращении в период нагрева. Затем реторта закрывается задней крышкой, камера нагрева приводится в горизонтальное положение. Вал реторты приводится во вращение приводом с частотой 3–10 об/мин. Контроль температурного режима обработки проводится датчиками температуры, установленными на муфеле и дополнительными датчиками, размещенными в гильзе. Такой контроль температуры обеспечивает равномерный нагрев по длине и сечению реторты. При необходимости создания виброкипящего слоя на реторту накладываются высокочастотные колебания от вибратора. По окончании процесса реторта остывала вместе с печью до температуры ниже 100 °С, раскрывалась и проводились дальнейшие исследования.
Исследования строения шлака и его химический состав проводились электронномикроскопическим и рентгенофлуоресцентным анализом и анализом фазового состава.
Электронномикроскопический анализ проводился на сканирующем электронном микроскопе Jeol JSM-7001F. Поверхность исследовалась в режиме вторичных и отраженных электронов, были построены карты распределения элементов по поверхности.
Рентгенофлуоресцентный анализ осуществляли с помощью энергодисперсионного спектрометра Oxford INCA X-mai/80, который смонтирован на микроскопе Jeol JSM- 7001F.
Исследования фазового состава проведены с помощью рентгеновского дифрактометра Rigaku Ultima 4.
Таблица 1
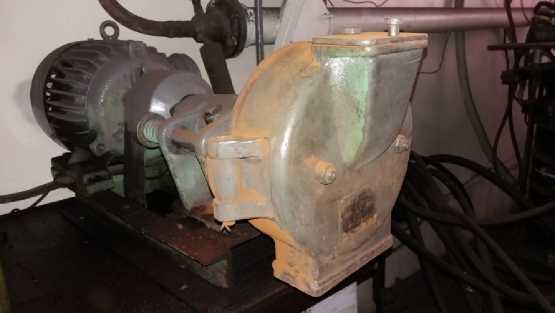
Рис. 1. Фотография истирающей машины ИДА-175
Химический состав отвального шлака ЮУНК
Состав отвальных шлаков, % масс. |
||||||||||
e общ |
Si |
Mg |
S |
Ca |
Al |
Cr |
Ni |
Co |
Mn |
Др. |
12–23 |
19,5–22 |
4,8–6,5 |
0,18–0,58 |
10,4–11 |
2,9–3,5 |
0,65–0,95 |
0,14–0,6 |
0,035–0,042 |
0,3 |
Ост. |
Металлургия чёрных, цветных и редких металлов
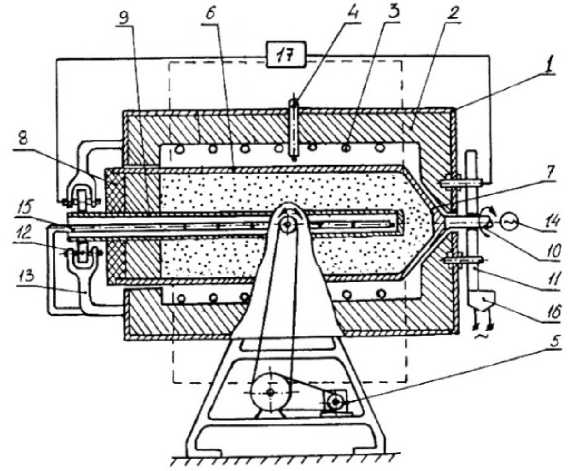
Рис. 2. Лабораторная установка для обжига отвального никелевого шлака: 1 – камера нагрева; 2 – цилиндрический муфель; 3 – электронагреватель; 4 – датчик температуры; 5 – механизм поворота; 6 – реторта; 7 и 8 – передняя и задняя крышки; 9 – глуходонная гильза; 10 – вал; 11 – передние катки; 12 – задние катки; 13 – изолятор; 14 – привод; 15 – дополнительные датчики температуры; 16 – вибратор; 17 – источник питания
Результаты проведенных экспериментов
Химический состав отвальных никелевых шлаков и карты распределения химических элементов представлены, соответственно, на рис. 3, 4 и в табл. 2, 3.
Результаты рентгеновского фазового анализа представлены на рис. 5 и 6.
Рентгенограмма на рис. 5 позволяет выделить три основные фазы: диопсида CaMgSi 2 O 6 (35 % масс.), частично замещенного магнием фаялита (Mg,Fe) 2 SiO 4 (12 % масс.), кварца SiO 2 (2,5 % масс.) и большого количества аморфного стекловидного шлака (50 % масс.).
Результаты фазового анализа согласуются с данными, полученными при картировании. Никель в шлаке находится в виде фазы (Fe,Ni)S, которая присутствует в малом количестве в виде отдельных включений, попавших в основной шлак механическим путем, и не может быть определена. Соотношение Fe :Ni в представленных на рис. 3 и 4 картах составляет от 1 : 1 до 1 : 5. Часть никеля находится в окисленной форме в виде ферритов (рис. 6). Опираясь на результаты рентгенограммы аморфного шлака (см. рис. 6), можно заключить, что кобальт преимущественно распределен в оксидной части шлака в виде ферритов и хромитов, хром присутствует в виде хромитов и оксидов.
На основании данных микрорентгеноспектрального и фазового анализов отвального никелевого шлака Южно-Уральского Никелевого комбината можно заключить, что основная часть никеля входит в состав сульфидных фаз с участием железа, типа (Fe,Ni)S, остальной никель замещает железо в фаялите или входит в состав ферритов. Сульфидные фазы являются мелкими каплевидными включениями. Размером от 10 до 100 мкм в массе стекловидного шлака на основе фаялита. Поэтому для полноты извлечения необходимо первоочередно тонко измельчать отвальный шлак.
Восстановление никеля из отвального никелевого шлака коксом путем расплавления позволило получить железоникелевый сплав с содержанием никеля 2,2–3,0 % масс., 0,57– 0,7 % серы, остальное – железо. Выход годного составил по металлической фазе 8–10 %, степень извлечения никеля – 49 %. Извлекать данным способом никель, даже применяя для этого сульфидирующие добавки или металл-коллектор, является экономически неэффективным и технологически трудным, приходится извлекать большие объемы шлака из печи
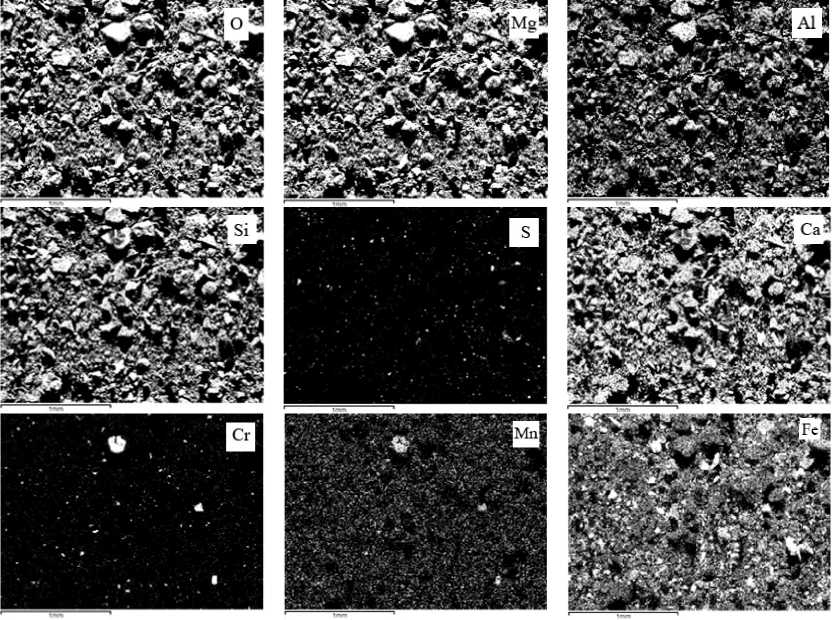
Рис. 3. Распределение элементов в шлаке на площади 2 × 3 мм
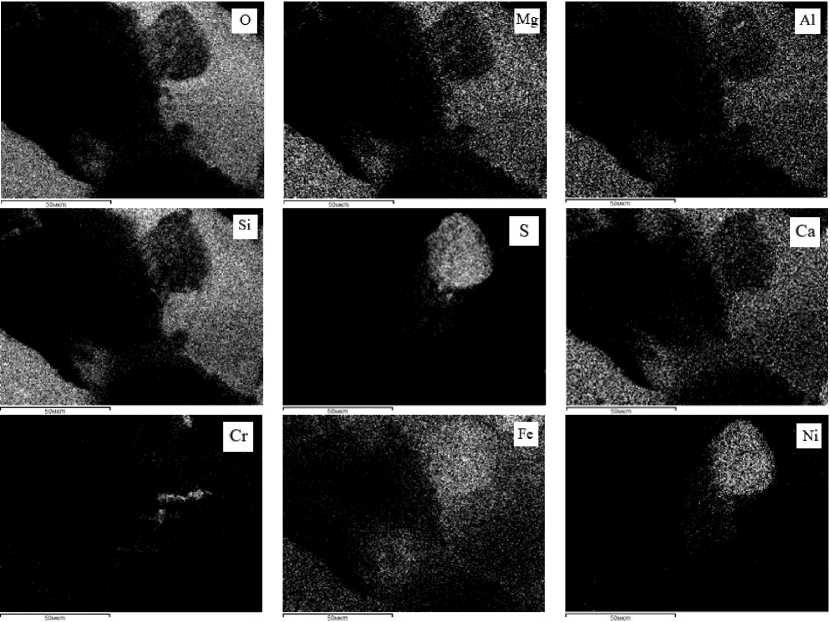
Рис. 4. Распределение элементов в шлаке на площади 100 × 200 мкм
Металлургия чёрных, цветных и редких металлов
Таблица 2
Состав размолотого и усредненного шлака, полученный от площади анализа 2 × 3 (рис. 3)
O |
Na |
Mg |
Al |
S i |
S |
Ca |
Ti |
Cr |
Mn |
Fe |
Co |
Ni |
Cu |
Zn |
Mo |
|
1 |
42,31 |
0,35 |
4,97 |
2,94 |
17 , 66 |
0,63 |
8,19 |
0,11 |
0,99 |
0,30 |
20,80 |
0,20 |
0,36 |
0,15 |
0,09 |
0,17 |
2 |
42,74 |
0,41 |
5,09 |
2,93 |
1 7, 93 |
0,61 |
8,29 |
0,11 |
0,75 |
0,30 |
20,09 |
0,19 |
0,29 |
0,19 |
0,12 |
0,16 |
3 |
42,14 |
0,32 |
4,95 |
2,90 |
1 7, 89 |
0,72 |
8,42 |
0,11 |
0,77 |
0,30 |
20,74 |
0,24 |
0,32 |
0,20 |
0,10 |
0,12 |
4 |
42,08 |
0,44 |
4,77 |
2,82 |
17 , 88 |
0,81 |
8,22 |
0,14 |
0,77 |
0,26 |
21,14 |
0,21 |
0,37 |
0,25 |
0,10 |
–0,03 |
5 |
41,37 |
0,38 |
4,74 |
2,87 |
17 , 56 |
1,01 |
8,26 |
0,13 |
0,72 |
0,30 |
21,59 |
0,21 |
0,48 |
0,23 |
0,19 |
0,19 |
Ср. |
42,13 |
0,38 |
4,90 |
2,89 |
17 , 78 |
0,76 |
8,28 |
0,12 |
0,80 |
0,29 |
20,87 |
0,21 |
0,36 |
0,20 |
0,12 |
0,12 |
Таблица 3
Состав никелевого включения (рис. 4)
O |
Na |
Mg |
Al |
Si |
S |
Ca |
Ti |
Cr |
Mn |
Fe |
Co |
Ni |
Cu |
Zn |
Mo |
Итог |
15,97 |
0,24 |
0,88 |
0,76 |
2,71 |
1 3, 13 |
0,78 |
0,06 |
0,14 |
–0,03 |
53,98 |
1,13 |
10,32 |
0,23 |
0,34 |
0,50 |
100,00 |
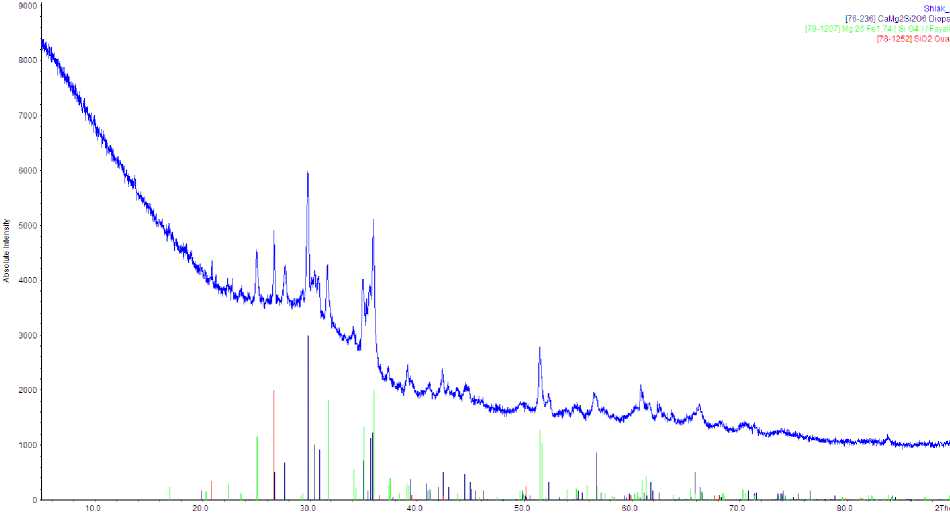
Рис. 5. Отнесение пиков рентгенограммы CaMgSi 2 O 6 диопсид (1), (Mg,Fe) 2 SiO 4 фаялит (2), SiO 2 кварц (3)
и и с п ол ьзовать ра з жи ж а ю щ и е фл ю сы. Д л я у в е л ичен ия э к он оми че с ких п ок а за те ле й п е реп л а в а н е обход и мо п р е д ва ри те льн о о б ог а ти ть о т в а л ьн ый н ик е ле вый шла к д о с од ержа н и я в н ем ни к еля, э к в и в а ле н тное ряд у ок и с ле н н ы х н и к еле в ы х руд р а зра ба тыв а е мых ме с то ро ждений [5].
Гораздо эффективнее из технологических и экономических соображений извлекать никель из отвальных шлаков в магнитный концентрат, используя хлористый аммоний и кокс. Хлористый аммоний, начиная с температуры 350 °С, разлагается с выделением хлороводорода, который при более высоких температурах диссоциирует с образованием свободного хлора. Кокс создает восстановительную атмосферу и участвует в процессах вос- становления никеля и железа. Процессы, протекающие в шихте, могут быть реализованы следующими химическими процессами [6–9]:
Ni 3 S 2 + Cl 2 = 2NiS + NiCl 2 ,
∆G = –265346 + 144,2Т;(1)
NiS + Cl 2 = NiCl 2 + S,
∆G = –157746 + 164,39Т;(2)
NiFe 2 O 4 + 3Cl 2 + 4C =
= 2FeCl 2 + NiCl 2 + 4CO,
∆G = –380623 – 97,8T;(3)
CoFe 2 O 4 + 3Cl 2 +4C =
= CoCl 2 + 2FeCl 2 + 4CO,
∆G = –399338 – 120,06T;(4)
FeCr 2 O 4 + 3Cl 2 + 4C =
= FeCl 2 + 2CrCl 2 + 4CO,
∆G = –520079 – 148,72T.(5)
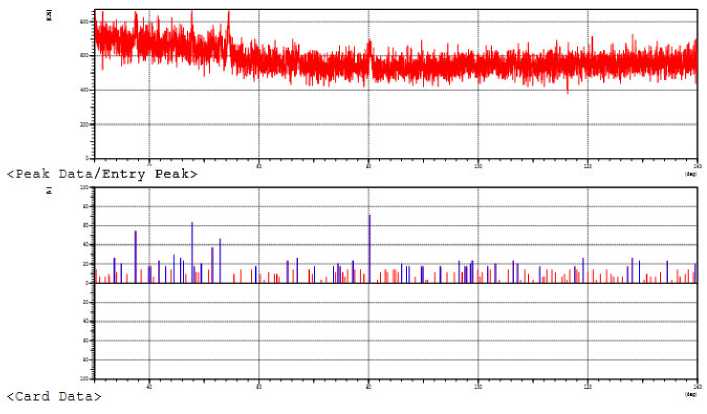
No. Card Chemical Formula Chemical Name (Mineral Name)
1 | 00-003-0864 CoFe2O4 Cobalt Iron Oxide
2 | 00-006-0532 Cz-O Chromium Oxide
3 | 00-035-1321 CdCz2O4 Cobalt Chromium Oxide
4 | 00-034-0140 Fet2Cr2O4
S L d I R
Dx WT% S.G. 0.676 0.909(10/13) 0.673 ----- 0.612
----- ----- Fd-3m 0.657 0.857 ( 6/ 9) 0.651 ----- 0.558
----- ----- F 0.488 0.750( 9/13) 0.668 ----- 0.501
Iron Chromium Oxide ( Chromite, syn
-
5 | 00-056-0285 NiO.3Fe2.104 Nickel Iron Oxide
-
6 | 00-034-0170 Fe2+2S1O4
Iron Silicate ( Fayalite, syn )
-
7 | 00-025-0411 Fe7SB
Iron Sulfide ( Pyrrhotite-3T, syn )
-
0 ] 00-012-0559 Cr3O4
0.770 O.B18( 9/27) 0.581 0.475
5.05 Fd-3m
0.842 0.750( 9/19) 0.544 0.408
4.55 Fd-3m
0.959 0.525(31/83) 0.773 0.406
4.40 Pmnb
0.503 0.545( 6/11) 0.538 0.294
4.53P31
0.464 0.6D0( 9/17) 0.479 0.287
5.13 ----- 141/amd
Chromium Oxide
Рис. 6. Рентгенограмма аморфной составляющей никелевого шлака
Образующийся хлорид никеля, начиная с температуры 978 °С, возгоняется и конденсируется на поверхности железных включений, которые, в свою очередь, образуются при восстановлении железа из оксидов в шлаке на границах коксовых включений (рис. 7, а). В результате реакции обмена железные частицы обогащаются никелем и увеличиваются в размерах (рис. 7, б и табл. 4).
Последующее измельчение спекшейся шихты и магнитная сепарация позволяют извлечь данные образования в магнитный концентрат. Результаты анализа магнитной части шлака с площади 2 × 3 мм представлены в табл. 5. Структура, места точечного спектрального анализа и результаты химического анализа с исследуемой площади поверхности немагнитной части шлака приведены на рис. 8 и в табл. 6.
Химический состав структурных составляющих немагнитной части шлака после хи- мико-термической обработки (рис. 8, а) представлен в табл. 7. Последующий переплав магнитной части шлака, составов, приведенных в табл. 8, позволяет получить ферроникель, химический состав которого приведен в табл. 9.
Анализируя данные табл. 7, можно заключить, что в большинстве структурных составляющих немагнитной части шлака отсутствует никель, так как он перешел в магнитный концентрат. Степень извлечения отвального никеля в магнитный концентрат составляет 80–85 %, а при последующем переплаве никель практически полностью переходит в расплав. Химический состав шлака, полученный от переплава магнитного концентрата, представлен в табл. 10.
Согласно данным табл. 10, шлак представляет собой очищенную от железа и никеля пустую породу в виде стекловидной фазы темно-блестящего цвета.
Металлургия чёрных, цветных и редких металлов
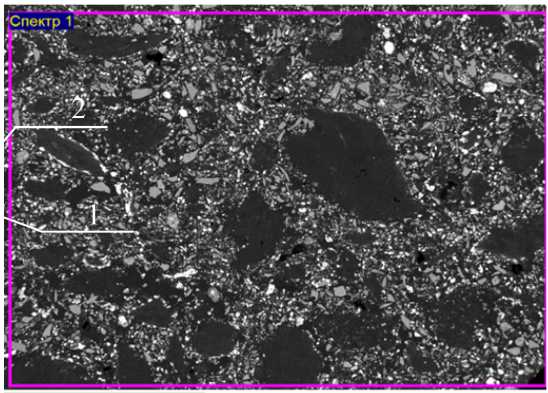
Электронное изображение 1
а)
Рис. 7. Морфология зарождения металлической фазы в шихте (а) и корольки ферроникеля (б) в шихте (2 % NH 4 Cl, 10 % кокс, остальное – шлак) после ее нагрева и выдержки при температуре 1000 °С в течение 1 ч: 1 – корольки ферроникеля; 2 – кокс
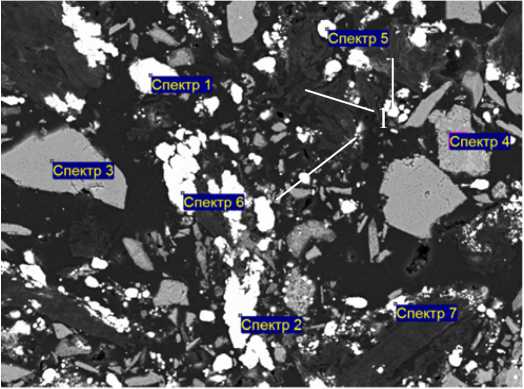
ЮОмкт 1 Электронное изображение 1
б)
Таблица 4
Номер спектра |
Химический состав, % масс. |
|||||||||
O |
Mg |
Al |
Si |
S |
Ca |
Cr |
Fe |
Co |
Ni |
|
1 |
1,3 |
0 |
0,1 |
0,2 |
0,2 |
0,1 |
0 |
76,7 |
2,0 |
19,8 |
2 |
1,6 |
0 |
0 |
0,2 |
0,3 |
0,1 |
0 |
95,8 |
0,8 |
1,9 |
3 |
42,7 |
7,0 |
3,3 |
21,0 |
0 |
13,9 |
0,5 |
11,4 |
0,1 |
0,1 |
4 |
40,2 |
4,7 |
3,4 |
20,9 |
0,4 |
11,7 |
1,2 |
17,2 |
0,1 |
0,1 |
5 |
1,0 |
0,1 |
0 |
0,1 |
0,3 |
0,1 |
0 |
96,5 |
0,9 |
1,5 |
6 |
1,3 |
0 |
0 |
0,2 |
0,2 |
0 |
0 |
96 |
1,0 |
1,7 |
7 |
2,6 |
0,4 |
0,1 |
0,3 |
0,3 |
0,1 |
0,1 |
94,4 |
0,8 |
1,7 |
Таблица 7
Номер спектра |
Химический состав, % масс. |
|||||||||
O |
Mg |
Al |
Si |
S |
Ca |
Cr |
Fe |
Co |
Ni |
|
1 |
42,4 |
5,3 |
2,6 |
22,6 |
0,1 |
14,4 |
0,8 |
11,7 |
0,1 |
0,0 |
2 |
41,1 |
6,3 |
2,6 |
23,9 |
0,0 |
9,9 |
0,7 |
15,4 |
0,2 |
0,0 |
3 |
36,0 |
7,4 |
0,3 |
27,1 |
0,0 |
11,9 |
1,0 |
16,5 |
0,0 |
0,0 |
4 |
40,5 |
0,1 |
0,4 |
46,6 |
0,3 |
0,2 |
0,1 |
12,1 |
0,1 |
0,3 |
Таблица 8
№ опыта |
Шихта для ХТО, % масс. |
Температура, °С |
Выдержка, ч |
Концентраты после сепарации, % масс. |
|||
Шлак |
NH 4 Cl |
Кокс |
Магн. |
Немагн. |
|||
1 |
88 |
2 |
10 |
1000 |
1 |
15 |
85 |
2 |
88 |
2 |
10 |
1000 |
2 |
69 |
31 |
3 |
88 |
2 |
10 |
1000 |
4 |
64 |
36 |
4 |
88 |
2 |
10 |
1000 |
6 |
54 |
46 |
5 |
88 |
2 |
10 |
1000 |
8 |
62 |
38 |
Таблица 9
№ опыта |
Шихта, % масс. |
Т , °С |
ВГ, % |
Химический состав ферроникеля, % масс. |
||||||
Конц. |
Кокс |
Cr |
Ni |
S |
Si |
Co |
Fe |
|||
1 |
99 |
1 |
1550 |
34 |
0,8 |
9,2 |
3,0 |
3,0 |
0,8 |
Ост. |
2 |
99 |
1 |
1550 |
28 |
1,0 |
6,1 |
1,7 |
4,3 |
0,7 |
Ост. |
3 |
99 |
1 |
1550 |
27 |
1,1 |
6,2 |
1,8 |
3,4 |
0,9 |
Ост. |
4 |
99 |
1 |
1550 |
32 |
1,9 |
6,2 |
4,5 |
6,0 |
0,8 |
Ост. |
5 |
99 |
1 |
1550 |
34 |
1,2 |
7,0 |
4,2 |
3,0 |
0,7 |
Ост. |
Таблица 10
№ опыта |
Химический состав, % масс. |
||||||
O |
Al |
Si |
Ca |
Mn |
Fe |
Ni |
|
1 |
54,12 |
15,44 |
20,82 |
7,93 |
0,28 |
0,08 |
0,09 |
2 |
53,96 |
18,29 |
19,38 |
8,05 |
0,16 |
0,1 |
0,08 |
3 |
53,75 |
15,21 |
21,62 |
8,95 |
0,26 |
0,11 |
0,10 |
4 |
53,51 |
20,18 |
18,20 |
7,86 |
0,28 |
0,00 |
0,00 |
5 |
52,89 |
20,70 |
17,16 |
8,99 |
0,15 |
0,08 |
0,03 |
Химический состав структурных составляющих шлака после прокалки (рис. 7, б)
Химический анализ магнитного концентрата (рис. 7, а)
Таблица 5
Номер |
O |
Mg |
Al |
Si |
S |
Ca |
Cr |
Fe |
Co |
Ni |
1 |
36,0 |
3,2 |
1 ,8 |
13,0 |
0,3 |
5,3 |
0,5 |
39,0 |
0,3 |
0,5 |
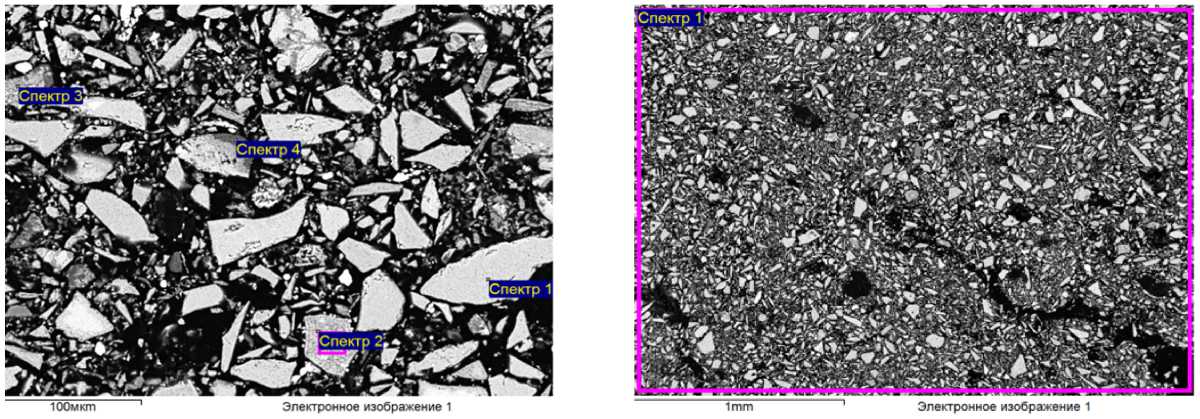
а)
б)
Рис. 8. Структура немагнитной фракции шлака с площади 500 × 400 мкм (а) и 3 × 2 мм (б), полученная от магнитной сепарации шихты (2 % NH 4 Cl, 10 % кокс, остальное – шлак), прокаленной в течение 1 ч при 1000 °С
Химический анализ немагнитной фракции (рис. 8, б)
Таблица 6
Номер |
O |
Mg |
Al |
Si |
S |
Ca |
Cr |
Fe |
Co |
Ni |
1 |
43,8 |
5,2 |
3 ,1 |
22,4 |
0,4 |
10,1 |
0,8 |
14 |
0,2 |
0,1 |
Химический состав структурных составляющих хвостов магнитной сепарации
Состав шихты и выход годного магнитного концентрата
Химический состав и выход годного ферроникеля, полученного от переплава магнитного концентрата (см. табл. 8)
Химический состав шлака, полученный после переплава магнитной фракции
Заключение
-
1. Проведенными анализами установлено, что в отвальном никелевом шлаке содержание никеля в среднем 0,36 % масс., основная часть которого входит в состав сульфидных фаз с участием железа, типа (Fe,Ni)S, остальной никель замещает железо в фаялите или входит в состав ферритов.
-
2. Кобальт преимущественно распределен в оксидной части шлака в виде ферритов и хромитов, основная часть железа сосредоточена в фаялите.
-
3. Переработка отвальных никелевых шла-
ков представленным способом позволяет извлекать до 80–85 % никеля и хрома, последний содержится в отвальных никелевых шлаках в качестве примеси, перешедшей из руды, и железа в количестве 55–65 % масс., которая переходит в магнитный концентрат после химико-термической обработки.
Список литературы Химико-термическая обработка отвальных никелевых шлаков с целью извлечения никеля и железа
- Куприянов, Ю.П. Шахтная плавка вторичного сырья цветных металлов/Ю.П. Куприянов. -М: ЦНИИцветмет экономики и информации, 1995. -164 с.
- Шохин, В.Н. Гравитационные методы обогащения/В.Н. Шохин, В.Н. Лопатин. -М.: Недра, 1993. -350 с.
- Стрельцов, Ф.Н. Повышение эффективности переработки шлаков на заводах ОЦМ/Ф.Н. Стрельцов, А.Н. Задиранов//Цветные металлы. -1993. -№ 1. -С. 61-64.
- Козырев, В.М. Основы современной экономики/В.М. Козырев. -М.: Финансы и статистика, 1998. -368 с.
- Диомидовский, Д.А. Металлургия ферроникеля/Д.А. Диомидовский, Б.П. Онищин. -М.: Металлургия, 1983. -183 с.
- Вайсбурд, С.Е. Физико-химические свойства и особенности строения сульфидных расплавов/С.Е. Вайсбурд. -М.: Металлургия, 1996. -304 с.
- Maurel C. Types de reactions d`oxidation observes au cours de analysethermiquedifferentielle, dans air mineral sulfures et arsenies de Fe, Co, Ni, Cu, Zn//Bull. Soc. Franc. Min. Crist. -1994. -T. 87, no. 3. -P. 377-385.
- Tanabe, T. Oxidation of mixed nickel-iron sulfide/T. Tanabe, M. Ogawa//J. Jap. Inst. Metals. -1996. -Vol. 50, no. 2. -P. 192-200.
- Мечев, В.В. Особенности сульфидирования ферритов цветных металлов/В.В. Мечев//Металлы. -1994. -№ 2. -С. 3-10.