Improvement of technology and jar mills for preparation of coal-water fuel from waste coal
Автор: Murko V.I., Volkov M.A., Grinyuk D.P., Baranova M.P., Holboev G.O.
Журнал: Горные науки и технологии @gornye-nauki-tekhnologii
Рубрика: Обогащение и переработка минерального и техногенного сырья
Статья в выпуске: 1 т.5, 2020 года.
Бесплатный доступ
The process and equipment have been developed for preparation and burning (at small and medium capacity boiler plants) of slurry coal-water fuel, produced from finely dispersed coal preparation waste (filter cakes) from coal preparation plants of Komsomolets Mine and Named after S. M. Kirov Mine. It was shown that, based on these wastes, it is possible to produce slurry coal-water fuel with solids content of 56-60 %, the required structural and rheological characteristics, and lower heating value of up to 13 MJ/kg. Based on the research findings, detail design was developed for creation of the pilot process complex for processing of waste coal to produce slurry coal-water fuel for burning at boiler plant. Assessment of using the whole volume of the SUEK Kuzbass coal preparation plants waste coal at the nearby Belovskaya SDPP was performed, which showed high economic and environmental efficiency of the proposed project.
Waste coal, slurry coal, coal-water fuel, jar mill, vibration testing machine
Короткий адрес: https://sciup.org/140250757
IDR: 140250757 | DOI: 10.17073/2500-0632-2020-1-4-11
Текст научной статьи Improvement of technology and jar mills for preparation of coal-water fuel from waste coal
In recent years, industrial application of so-called jar mills for fine grinding has begun. The mills allow both dry and wet grinding to high degree of material dispersity. High-frequency jars and diverse nature of the impacts of grinding bodies on the material create the processed material fatigue breaking mode. This is the main feature of the jar grinding process and explains why jar mill is especially effective in producing highly dispersed products. As a result of the combined mechanical effects of high frequency and periodically arising stress states in the material being milled, weak points always present in the solid material structure are further weakened and breakage of particles occurs in these points.
Coal preparation process at modern coal preparation plants in Russia is characterized by the use of closed water-slurry circuits to produce coal concentrate with required moisture content without thermal drying of fine-grain coal. At the same time, finely dispersed waste coal of 0–0.5 mm grain size, commonly represented by filter press cake, is sent to waste dump together with waste rock. The filter cake yield is up to 7 % of being prepared coal mass [1–12]. Dispatching this product to waste dump with waste rock is caused by the fact that its use is complicated by high ash content, up to 50 %, and moisture content up to 45 %. Similar situation takes place at the Tugnuisky Coal Preparation Plant LLC of the SUEK OJSC. The annual output of the filter cake at the Plant is 800 kt.
To solve the problem of reducing the yield of waste coal and increasing the yield of commercial products at the Tugnuisky Coal Preparation Plant, it is proposed to use the technology for the production and burning of coal–water slurry fuel (CWF), produced on the basis of the filter cake. Studies have been conducted on the CWF preparation with its following combustion at a semicommercial installation.
2020;5(1):4-11
МИСиС
One of the main stages of coal–water slurry (CWS) preparation process is grinding, since it is the stage which allows regulating particle size distribution of the final product. CWS particle size distribution controls CWS’s rheological parameters, determines flow properties (flow pattern) of the structured system. It is known that improvement of CWF characteristics is achieved by using a certain amount of fine fraction (0–50 μm) of solid material. There is evidence [12] that, for improving CWS combustion characteristics and stability, the coal fine fraction should amount to up to 50 %, at total solid content of about 70 %. In this case, it is proposed to use waste coal of sufficiently high rank as initial material.
A feature of PFS of modern coal preparation plants (CPP) in Russia is the use of closed water-slurry cycle, which eliminates the slurry discharge outside CPP to external settling sumps and slurry dumps, and no use of thermal drying of fine coal due to their more efficient mechanical dewatering. As a result, the process generates significant amount (up to 10–12 % of CPP raw coal preparation volume) of toxic finely-dispersed waste coal (TFWC) of fineness below 0.5 mm, moisture 30–45 %, and ash content 25–65 %. This product is not in demand at the market, it is refractory (hardly dressable) and, as a rule, is disposed with waste rocks in waste dumps. Given high toxicity of TFWC due to the presence of flocculants and coagulants (applied at CPP) with carcinogenic and mutagenic effects on the particle surface, storage of such dangerous waste creates significant environmental problems in the region.
To solve the problem of TFWC utilization, a technology and a set of equipment have been developed for obtaining slurry coal-water fuel based on TFWC and its efficient burning with capturing and reclamation of the resulting ash-and-slag waste (ASW). The paper discusses the proposed technology and describes operation of the equipment used (reactor-mixers, vertical bi-chamber jar mill, activator pump, boiler with vortex adiabatic combustion chamber, and two-stage flue gas cleaning system). The results of operation of the created experimental process system for processing TFWC from several Kuzbass CPPs are presented.
To solve the fine waste coal utilization problem, SUEK-Kuzbass JSC adopted a decision to create pilot process system for processing of finely-dispersed waste coal by preparing and burning slurry coal fuel based on filter cake of the SUEK-Kuzbass coal preparation plants.
This decision was based on the studies on preparation and burning of slurry coal fuel, produced on the basis of finely-dispersed waste coal, performed at the pilot-plant stand of Kuzbass State Technical University [13–20]. This paper presents the performed study findings and shows the prospects of solving the existing problem. Thus, the work aim was to prepare the initial data for creating the pilot process system.
Characteristics of the feedstock
To study the opportunity of preparing slurry coal-water fuel based on finely-dispersed waste coal, filter cake samples weighting 2000 kg each were delivered from the CPPs of Komsomolets Mine and Named after S. M. Kirov Mine (S. M. Kirov Mine). The delivered samples were analyzed in coal chemical laboratory. Qualitative characteristics of the studied samples are given in Table 1.
Table 1 data show that moisture of the filter cake samples taken for the research was steadily high: W t r = 35.2–40.8 %. Unlike moisture, the filter cake ash content depends on quality of the feedstock and can vary both in narrow range ( A d = 30.7 %; 26.8 %) and in wide range, up to 15.6 % ( A d = 32.8 %; 48.4 %) for the filter cake from the CPP of the Named after S. M. Kirov Mine. Particle size distribution of the filter cake from the CPPs of the Komsomolets Mine and Named after S. M. Kirov Mine included fineness range up to 3.0 mm [6–9].

ГОРНЫЕ НАУКИ И
2020;5(1):4-11
МИСиС^
Национальный исследовательский технологический университет
Table 1
Qualitative Characteristic of the Tested Samples
Indicator |
Coal-preparation plant of Komsomolets Mine |
Coal-preparation plant of S.M. Kirov Mine |
||
Sample No. 1 |
Sample No. 2 |
Sample No. 3 |
Sample No. 4 |
|
Moisture, weight % |
35.2 |
34.8 |
40.3 |
40.8 |
Ash content (on dry basis), % |
30.7 |
26.8 |
32.8 |
48.4 |
Volatile-matter yield (on dry ash-free basis), % |
43.0 |
43.1 |
42.4 |
41.4 |
Sulfur total (on dry basis), % |
0.52 |
0.48 |
0.15 |
0.13 |
Higher heating value (on dry basis), МJ/kg |
33.70 |
33.04 |
33.08 |
33.00 |
Lower heating value of combustible mass, МJ/kg |
13.75 |
14.3 |
11.8 |
8.7 |
Grain size, mm 0.250–3.000 |
5.7 |
8.4 |
4.5 |
6.3 |
0.071–0.250 |
15.1 |
18.7 |
26.8 |
17.3 |
< 0.071 |
79.2 |
72.9 |
68.7 |
76.4 |
Total |
100.0 |
100.0 |
100.0 |
100.0 |
Research technique for preparation of slurry coal fuel
The filter cake is actually semi-finished product for producing coal-water fuel with characteristics allowing it to be efficiently burned in boiler swirling-type furnace or co-fired with traditional fuel in coal-fired boiler units.
Evaluation of the possibility of preparing CWF from coal waste (filter cakes of the Komsomolets mine and the S.M. Kirov mine) and selection of the optimal plasticizing additive were carried out under laboratory conditions using universal vibration testing machine.
In the process of the research, laboratory samples of slurry coal fuel were prepared by mixing the filter cake and aqueous solution of plasticizing agent. Considering the initial fineness of the filter cake, for the CWF samples preparation, mixing or grinding chamber of periodic action at the universal vibration testing machine was used. Dosing of the initial components was performed manually. The purpose of the laboratory studies was to select the optimal plasticizing additive option based on the analysis of the prepared CWF main structural and rheological characteristics.
The CWF samples were analyzed for solid phase weight fraction, particle size distribution, and viscosity. Static stability was determined by the presence of sediment and water gain during storage of the sample in static conditions. The solid phase mass fraction was determined by standard drying method according to GOST 27314–91, or according to GOST 11014–2001; the particle size distribution, by wet sieving on 0.355 mm, 0.250 mm, and 0.071 mm sieves according to GOST 2093–82; and the ash content, according to GOST 11022–95. The lower calorific value was calculated using the measured values of the weight fraction and ash content of the solid phase. Recalculation of the analysis results for various fuel states was carried out according to GOST 27313–95.
Viscosity measurements were carried out using RHEOTEST rotational viscometer in the range of shear rate from 1.0 to 437.4 s –1 with standard cylinder system S2. The measurement temperature was 20 ± 5 o С [6–12].
Further, at the pilot-plant stand (in semi-industrial conditions), the processes of CWF pilot batch preparation and combustion in the boiler unit of the pilot-plant stand were developed and optimized. At the same time, the composition and amount of harmful emissions originated during the combustion were determined at the stand.
Based on findings of the studies on the CWF preparation at the universal vibration testing machine in two ways (mixing and grinding), optimal type of the plasticizing additive (high molec-
2020;5(1):4-11
МИСиС
ular weight inorganic compound), its consumption (0.3 %) and the solid phase mass fraction in the prepared fuel (57.0 %) were determined.
Then, on the basis of the results obtained, experimental CWF batches were prepared at the experimental stand using the process flow sheet (PFS) shown in Fig. 1.
Technical water
Filter cake
Plasticizing agent
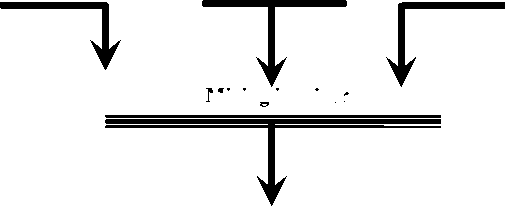
Mixing in mixer
Sizing to grain size of 1(3) mm
Evaporated moisture to storage +1 (3) mm
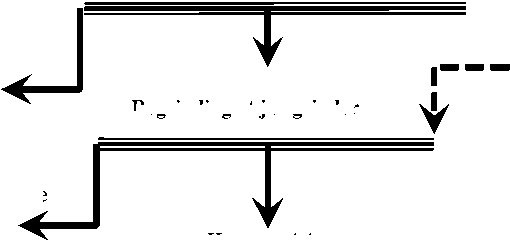
Regrinding at jar grinder
Feeding middlings (screenings)
of 0-10 mm grain size
Homogenizing
Storage
Fig. 1. Process Flow Sheet of the CWF Preparation from Filter Cake
According to the PFS, the initial filter cake and aqueous solution of the plasticizing agent were fed to the batch mixer, and then the produced water-coal slurry (in metered amounts) was fed to the universal vibration-testing machine, where regrinding and further mixing of the produced CWF was carried out. The universal vibration-testing machine is a bicameral jar mill, consisting of concentrically located cylindrical chambers, filled with grinding balls and interconnected by channels. The initial slurry enters the inner (central) chamber of the jar mill, moves down and through the channels enters the peripheral chamber. In the peripheral chamber, the slurry moves upward. Discharge of the milled material is carried out through the external threshold of the peripheral chamber. This principle of the jar mill operation allows for low energy consumption for grinding particles in the mixture at the required size of large particles in the finished CWF. The prepared CWF was pumped into storage tanks [12].
In order to stabilize the CWF quality in terms of ash content, the option of supplying screenings or crushed middlings of grain size of 0 to 10 mm to the jar mill was provided.
The influence of mechanical activation on the structural and rheological characteristics of finely dispersed coal slurries, produced on the basis of filter cakes in the specially created experimental activator pump, was determined. In the activator pump, the CWF was processed under conditions of shear strain in the gap of 0.2–0.3 mm
2020;5(1):4-11
МИСиС
between two disks at relative angular frequency of revolution of the movable disk of 2900 rpm. As a result, at the peripheral part of the disk, the shear rate reached 2100–3160 s–1, i.e. the conditions corresponding to the ultimate failure of the structure were obviously implemented. Passing the produced CWF through the activator pump reduced viscosity of the slurry by 30 % and increased static stability of the CWF.
Table 2 shows structural-rheological and thermophysical indicators of the CWF pilot batches.
Table 2
Characteristics of the Prepared CWF Pilot Batches
Ash content A d , % |
Yield of >0.25 mm grain size, % |
Solid phase weight fraction, С s , % |
Effective viscosity at shear rate of 81 s -1 , η, MPa·s |
Stability, days |
Lower heating value, Q i r , МJ/kg |
Filter Cake of Coal-Preparation Plant of Komsomolets Mine |
|||||
26.8 |
1.9 |
56.9 |
178 |
15 |
12.22 |
Filter Cake of Coal-Preparation Plant of S.M. Kirov Mine |
|||||
48.4 |
1.4 |
56.6 |
148 |
15 |
8.24 |
It was experimentally determined that the performance of the universal vibration-testing machine on the initial slurry ranges 0.155–0.217 tph depending on particle size of the initial slurry. At this operation mode of the machine, the yield of class +0.250 mm to the finished slurry did not exceed the limiting value, required under the burning conditions (R 250 ≤ 5 %) and amounted to 1.4–1.9 %.
Considering that the content of micron classes of fineness in the initial product — filter cake — is usually more than 70 % (see Table 1), it is advisable to install a rod mill for re-grinding operation in the pilot process system. The use of the rod mill makes it possible to obtain solid phase particles of more uniform size, and the presence of micron-size particles in the initial product further contributes to this. Thus, it becomes possible to provide the solid phase particle size distribution in the finished milled product to be close to bi-modal. As a result, the solid phase content in the finished fuel increases by 2–3 % while maintaining favorable structural rheological characteristics, that, in turn, leads to increasing the fuel heating value. To implement this condition, the rod jar mill design was developed (Fig. 2); the operation concept of the mill is similar to that of the bicameral ball jar mill at the demonstration stand.
The jar mill consists of housing ( 1 ), divided by inserts ( 2 ) into central ( 3 ) and peripheral ( 4 ) voids, which are hydraulically interconnected by slots ( 5 ) formed between the lower edges of the inserts and the bottom ( 6 ) of the housing. Feeding funnel ( 8 ) is installed on the upper cover ( 7 ) of the housing. The voids are filled with grinding bodies ( 9 ) (rods, balls). The voids are of rectangular shape that allows using rods as grinding media. Outside of the peripheral voids on their outer side walls ( 10 ), outlet gutters ( 11 ) are fixed, connected to the drain pipes ( 12 ). The housing is mounted on frame ( 13 ) with springs ( 14 ). Vibration exciter ( 15 ) is fixed on the housing bottom.
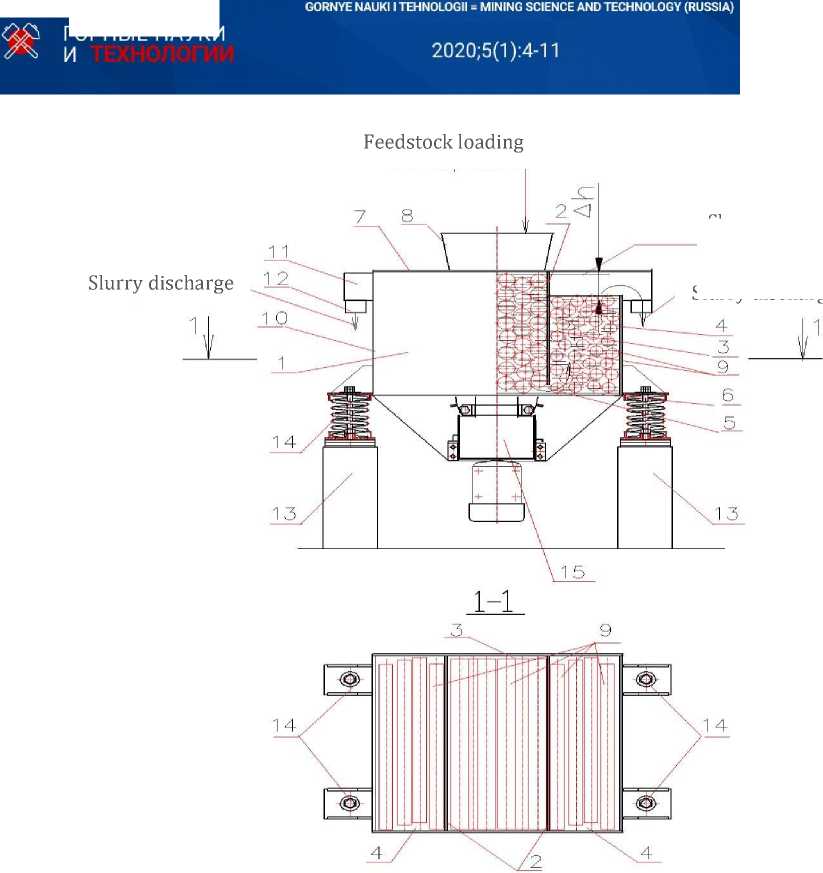
Fig. 2. Design of the Developed Jar Mill
МИСиС^
Slurry level
Slurry discharge
The jar mill operates as follows. The source material and liquid phase (water) through the feeding funnel 8 are fed into the central void 3 of the jar mill chamber, filled with grinding medium (rods or balls). Due to the impact of the vibrating grinding medium provided by vibration exciter 15, mixing of the incoming products and preliminary wet grinding of the solid material particles are carried out. The resulting slurry through the slots in inserts 2, enters the outer peripheral voids 4 of the chamber, also filled with grinding medium (rods or balls), under the shaking action of which wet grinding of the solid particles continues. In this case, grinding medium moves upward at speed being substantially lower than in the central void that ensures high grinding efficiency at lower energy consumption. In this case, the slurry movement speed in the void is controlled by changing the difference in level of the slurry in the central and peripheral voids due to change in the height of the outer side walls of the peripheral voids. Since the material solid particle fineness in the central and peripheral voids is different, the size of the grinding bodies in the peripheral voids is smaller than that in the central one. The milled product from the peripheral voids is discharged through the inner wall of the outlet gutters 11 and tubes 12 into receiving tank (not shown in Fig. 2). Thus, special design of the camera in compliance with the proposed option enables using both balls and rods as grinding bodies. This ensures implementation of more efficient wet grinding of material in the jar mill to provide particle size distribution close to bimodal when processing mixture of materials of different fineness [12–14].
CWF Burning at Pilot-Plant Stand
The pilot batches of CWF were burned in the boiler unit consisting of a boiler with thermal output of 0.63 MW, fuel supply system, ash collection system, blower heater for heat removal,
2020;5(1):4-11
МИСиС
and draft equipment [13]. The created boiler consists of a firebox – a vortex combustion chamber located in water-cooled case, and an economizer for removing heat from hot flue gases generated in the firebox. CWF is tangentially fed to the vortex furnace through a burner with pneumomechanical nozzle. Blasting air is also tangentially fed to the combustion chamber. The fuel is sprayed by compressed air fed to the nozzle. The fuel feeding is controlled by changing the fuel pump motor speed. The combustion chamber is equipped with water-cooled throat, which allows to hold burning coal particles and sprayed CWF droplets during the time required for their complete burning. The two-stage dust collection system consists of multicyclone collector and fabric filter providing high efficiency of dust collection from the exhaust gases. Table 3 presents the results of the tests on the CWF pilot batch burning.
Table 3
Results of the Tests on Combustion of the Coal-Water Fuel Pilot Batches
Indicator |
Value for Coal-Preparation Plant of: |
|
S.M. Kirov Mine |
Komsomolets Mine |
|
Boiler thermal output, MW |
0.47–0.57 |
0.52–0.66 |
Temperature conditions in firebox, o С |
980–1050 |
980–1050 |
CWF consumption, kg/hr |
220–250 |
170–210 |
CWF pressure, MPa |
0.20 |
0.19 |
Compressed air pressure, MPa |
0.21 |
0.20 |
Furnace off-gases temperature, o С |
250–260 |
250–260 |
Energy efficiency ratio, % |
0.83 |
0.85 |
Conclusions
-
1. The process and equipment have been developed for preparation and burning (at small and medium capacity boiler plants) of slurry coalwater fuel, produced from finely dispersed coal preparation waste (filter cakes) from coal preparation plants of Komsomolets Mine and Named after S. M. Kirov Mine. It was shown that, based on these wastes, it is possible to produce slurry coal-water fuel with solids content of 56‒60 %, the required structural and rheological characteristics, and lower heating value of up to 13 MJ/kg.
-
2. The boiler of thermal output of 0.63 MW with vortex combustion system, efficiently operating using coal waste fuel, was developed, manufactured and tested. The boiler operation tests on
the CWF showed its high efficiency (83–86 %), with the level of harmful emissions in the flue gases being significantly below the permissible values. High performance was achieved in terms of the CWF carbon in fly ash and incomplete combustion (below 5 % and 80 mg/m3, respectively, much below corresponding permissible values).
Based on the research findings, detail design was developed for creation of the pilot process system for processing of waste coal to produce slurry coal-water fuel for burning at boiler plants. Assessment of using the whole volume of the SUEK Kuzbass coal preparation plants waste coal at the nearby Belovskaya SDPP was performed, which showed high economic and environmental efficiency of the proposed project.
<2Й ГОРНЫЕ НАУКИ МИСиС м 2020'5(1 У 4-11 1
" И I । у. Национальный исследовательский технологический университет
DOI: 10.1051/e3sconf/20172102001.
Список литературы Improvement of technology and jar mills for preparation of coal-water fuel from waste coal
- Kaplunov D. R., Radchenko D. N. Design principles and selection of subsurface use technologies ensuring sustainable development of underground mines (Printsipy proektirovaniya i vybor tekhnologiĭ osvoeniya nedr, obespechivayushchikh ustoychivoe razvitie podzemnykh rudnikov) // Mining Journal, 2017, No. 11, pp. 52-59(in Russ.).
- Wan E. I., Fraser M. D., Logan C. N. Low sulphur coal-water fuel to retrofit coal-fired to comply with US clean air act amendments of 1990 // Proceedings of the IEA-CLM. Clearwater, FL, USA - Paris, France, International Energy, 1993, p. 22.
- Ashworth R. A., Melick T. A., Morrison D. K., Battista J. J. Electric utility CWS firing options to re-duce NOx emissions, Twenty Third International Technical Conference on Coal Utilization & Fuel Systems, Coal & Slurry Technology Association and ASME-FACT, Clearwater, Florida. 1998, pp. 719-730.
- Morrison J. D., Scaroni A. W., Battista J. J. The use of coal slurries for production of coal-water fuel. XIII International Coal Preparation Congress. Brisbane, Australia, 1998, pp. 643-645.
- Alaa M. Musalam and Abdel Fattah A. Qaraman. The thermal behavior of the coal-water fuel (CWF) // International Journal of Energy and Environmental Research. 2016, Vol. 4, No. 3, pp. 27-36.
- Murko V. I., Karpenok V. I., Senchurova Yu. А., Khyamyalyainen V. A., Tailakov O. V. Study of sul-fur oxide reduction during combustion of coal-water slurry // Coal in the 21st Century: Mining, Processing and Safety. 2016, pp. 297-300.
- Murko V., Hamalainen V., Baranova M. Р. IIIrd International Innovative Mining Symposium E3S Web of Conferences 41. 2018, pp. 01042.
- DOI: 10.1051/e3sconf/20184101042
- Baranova M. Energy and Resource-Saving Sources of Energy in Small Power Engineering of Siberia // Founder Of The Second International Innovative Mining Symposium. 2017, pp. 02001.
- DOI: 10.1051/e3sconf/20172102001
- Murko V. I., Fedyaev V. I., Karpenok V.I., Zasypkin I. M., Senchurova Y. A., Riesterer A. Investigation of the spraying mechanism and combustion of the suspended coal fuel // Thermal Science. 2015, v. 19, No. 1,pp. 243-251.
- Murko V. I., Puzyryov E. M., Karpenok V. I., Fedyaev V. I., Baranova M. P. The Usage of Boilers with a Furnace for Burning Enrichment Products and Deballasting Coal // XVIII Internation Coal Preparation Congress. 2016, pp. 345-350.
- DOI: 10.1007/978-3-319-40943-6_51
- Murko V. I., Fedyaev V. I., Aynetdinov H. L., Baranova M. P. Enviromentally clean techology of fine waste coal utilization // The 17th International Coal Preparation Congress. Turkey. 2013, pp. 679-682.
- Patent No. 2145038. M.cl. F 23 Q 5/00. Method of Combustion and Combustion Stabilization of the Water-Coal Fuel in the Settling Chamber (in Russ.), V. I. Murko, M. P. Fomicheva, A. N. Timoshevskiy, I. M. Zasypkin, et al. - No. 97120914/06. Appl. 03.12.97. Published on 27.01.2000, Bulletin No. 3
- Biletskyy V., Sergeyev P. and Krut O. Fundamentals of highly loaded coal-water slurries. Mining of Mineral Deposits. Taylor & Francis Group, London, 2013, pp. 105-113.
- Kijo-Kleczkowska A. Analysis of cyclic combustion of the coal-water slurry // Archives of Thermodynamics. 2011, 32(1), pp. 45-75.
- Kijo-Kleczkowska A. Combustion of coal-water slurrys // Fuel. 2011, 90 (2), pp. 865-868.
- Suetina T. A., Kochetkov A. V., Tolmachev A. G., Li Zhoy, Peng Lin. Features of automatic control of primary crushers (Osobennosti avtomaticheskogo upravleniya drobilkami pervichnogo drobleniya) // Internet journal "Science Studies". 2015, v. 7, No. 5, pp. 2-11 (in Russ.).
- Lagunov Yu. A. Substantiation of crushing-and-grinding facility parameters (Obosnovanie parametrov drobil'no-izmel'chitel'nykh agregatov) // Mining Information and Analytical Bulletin. 2000, No. 4, pp. 79-82(in Russ.).
- Zelin Zhang, Jianguo Yang, Dongyang Dou. A surface probability model for estimation of size distribution on a conveyor belt // Physicochem. Probl. Miner. Process. 2014, No. 50(2), pp. 591-605.
- Golik V., Komashchenko V., Morkun V. Geomechanical terms of use of the mill tailings for prepara-tion // Metallurgical and Mining Industry. 2015, No. 4, pp. 321-324.
- "Proenergomash" [Electronic resource] URL: www.pem-energo.ru (address date 18.10.2017).