Инновационные совмещенные технологии при обработке металлов
Автор: Сидельников С.Б., Горохов Ю.В., Беляев С.В.
Журнал: Журнал Сибирского федерального университета. Серия: Техника и технологии @technologies-sfu
Статья в выпуске: 2 т.8, 2015 года.
Бесплатный доступ
Представлен обзор совмещённых технологий обработки металлов. Особое внимание уделено агрегатам, совмещающим литьё и непрерывное прессование. Экспериментально проверены теоретические зависимости между механическими свойствами пресс-изделий и параметрами процесса непрерывного литья-прессования. Спроектирована опытно промышленная установка совмещенного литья-прессования алюминиевых и медных сплавов. Разработаны и исследованы способы совмещенной прокатки-прессования и совмещенного литья-прокатки-прессования алюминиевых сплавов.
Совмещённые процессы, обработка металлов, литье, прессование
Короткий адрес: https://sciup.org/146114942
IDR: 146114942
Текст научной статьи Инновационные совмещенные технологии при обработке металлов
Во второй половине XIX столетия в результате технической революции наметился резкий рост потребления металлоконструкций, который стимулировал создание ряда способов полунепрерывного и непрерывного литья металлов [1, 2]. Полученные таким образом полуфабрикаты подвергались в основном последующей обработке давлением, в связи с чем возникла идея объединения этих операций в один непрерывный технологический процесс путем создания совмещенных технологий основных металлургических переделов в одном агрегате для производства требуемой продукции. В настоящее время созданы высокопроизводительные линии литейно-прокатных агрегатов (ЛПА) по производству сортового проката из черных и цветных металлов и сплавов. Однако использование ЛПА эффективно только в условиях массового производства, а при частых переходах с одного типоразмера профиля на другой при изготовлении небольших объемов применение ЛПА нерентабельно в связи с высокой стоимостью прокатного оборудования и затратами на его содержание и обслуживание. Особенно это относится к производству мелкосортной продукции, требующего наличия большого количества комплектов калиброванных валков. Здесь наиболее полно проявляются преимущества прессового производства. Так, последние достижения в области разработки процессов непрерывного прессования металлов и сплавов подтвердили эффективность замены в ЛПА прокатного стана на более универсальные установки непрерывного прессования или прокатки-прессования.
По этому принципу ведущими в этом направлении фирмами Babcock Wire Equipment и Holton Machinery LTD изготавливаются и тиражируются линии непрерывного прессования цветных металлов [3, 4] на базе установок Конформ. Высокое качество пресс-изделий и сравнительно низкая себестоимость их производства способствует повышенному спросу на линии Конформ, количество которых к настоящему времени перевалило за 1000. Дальнейшее совершенствование данного процесса связано прежде всего с проведением НИОКР, направленных на повышение его технико-экономических показателей. Ныне внимание не только зарубежных, но и отечественных металлургов направлено на совмещение операций литья и непрерывного прессования в одном агрегате, что позволит существенно снизить металлоемкость производственных линий, повысить их гибкость и степень автоматизации [5-7].
Первый такой агрегат был разработан с использованием машины Конформ, оснащенной элементами роторного кристаллизатора Д. Проперци. Производительность этих установок в основном зависит от скорости кристаллизации расплава и диаметра рабочего колеса установки. Так, при непрерывном литье-прессовании алюминиевых сплавов она составляет от 300 до 6000 кг/ч при диаметре колеса 300 и 1400 мм соответственно [8].
На рис. 1 приведена схема установки Кастэкс. Расплавленный металл с помощью устройства для регулирования расхода жидкого металла 4 поступает в канавку колеса 2, имеющего интенсивное внутреннее охлаждение. В результате интенсивного охлаждения инструмента происходит непрерывное затвердевание металла в нижней части установки. Твердый металл достигает пресс-матрицы 7 и отпрессовывается по способу Конформ.
Способ прессования Кастэкс, при котором жидкий металл заливается в установку, является самым экономичным способом получения стандартной проволоки или профилей из всех других способов изготовления аналогичных изделий из твердого металла путем деформации [9]. Однако технических данных об этой установке, практических результатах эксплуатации в технической литературе не приводится, что объясняется, по-видимому, нежеланием авторов
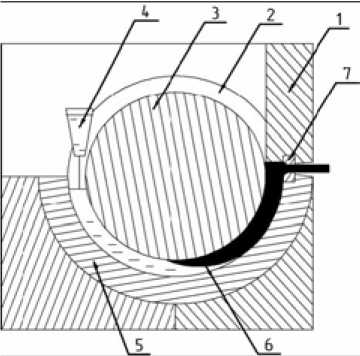
Рис. 1. Схема установки для непрерывного литья и прессования Кастэкс: 1 – разъемный корпус; 2 – кольцевая канавка; 3 – охлаждаемое колесо (ротор); 4 – устройство для регулирования расхода жидкого металла; 5 – кольцевая вставка; 6 – фронт кристаллизации; 7 – пресс-матрица раскрывать путь преодоления определенных трудностей в осуществлении и поддержании стабильного, устойчивого процесса непрерывной кристаллизации жидкого металла и его прессования, во многом зависящего от эффективной работы системы непрерывной подачи расплавленного металла в канавку рабочего колеса. Она должна отвечать следующим требованиям:
-
– расплавленный металл не затвердевает в начальной фазе процесса;
-
– скорость перемещения расплавленного металла постоянна и соответствует скорости его затвердевания, определяемой интенсивностью теплоотвода от прессового инструмента;
-
– в потоке расплавленного металла исключены завихрения.
Использование базовой установки Конформ для непрерывной заливки в канавку рабочего колеса жидкого металла, его кристаллизация и прессование вызывают затруднения в соблюдении этих требований, в частности в стабилизации подачи металла в инструмент, вследствие «намораживания» жидкой фазы расплава при затвердевании на входную частью неподвижной кольцевой вставки. Устранение этого недостатка возможно при совмещении непрерывного прессования с непрерывным литьем металла на установке Конформ с вертикальной осью вращения колеса-кристаллизатора карусельного типа [10-12]. В результате исследований, проведенных сотрудниками кафедры «Обработка металлов давлением» ФГАОУ ВПО «Сибирский федеральный университет» под руководством Ю.В. Горохова, предложено устройство для совмещенного литья-прессования цветных металлов с вертикальной осью вращения колеса-кристаллизатора карусельного типа. На рис. 2 приведена схема установки совмещения непрерывного литья-прессования металла с помощью установки Конформ, выполненной на базе карусельного кристаллизатора [12].
Расплавленный металл из питателя (на чертеже не показан) поступает в дозатор 1 и далее заливается в кольцевую канавку 3, выполненную на верхней части диска кристаллизатора 2. При этом скорость заливки расплавленного металла в кольцевую канавку 3 осуществляется в строгом соответствии с частотой вращения кристаллизатора 2. За время движения до промежуточной неподвижной сегментной вставки 8 расплавленный металл охлаждается, кристалли- – 187 –
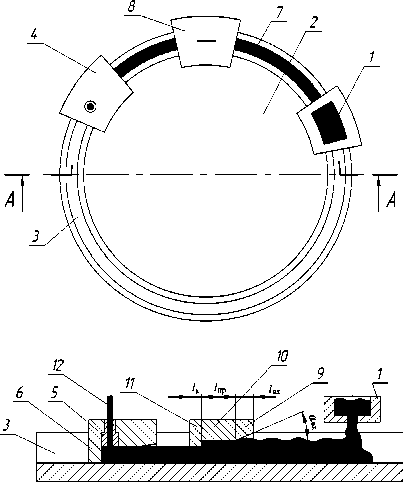
Рис. 2. Схема установки непрерывного литья и прессования методом Конформ: 1 – печь-миксер с дозатором; 2 – кристаллизатор; 3 – кольцевая канавка 3; 4 – основной неподвижный дугообразный сегмент; 5 – матрица; 6 – выступ; 7 – зона кристаллизации металла; 8 – промежуточная неподвижная сегментная вставка; 9, 10 – участки промежуточной неподвижной сегментной вставки; 11 – выступ, 12 – пресс-изделие зируется и принимает форму поперечного сечения канавки 3. В промежуточной неподвижной сегментной вставке 8 на поверхности закристаллизовавшегося металла прорабатывается его наружный слой с литейными дефектами и увеличивается интенсивность контакта закристаллизовавшегося металла со стенками кольцевой канавки 3. Далее закристаллизовавшийся металл в кольцевой канавке 3 по ходу вращения кристаллизатора 2 достигает выступа 6 в основном неподвижном дугообразном сегменте 4, где под действием сил контактного трения между стенками кольцевой канавки 3 и закристаллизовавшимся металлом происходит его выдавливание в пресс-изделие 12 через рабочий канал вертикальной матрицы 5.
Разработанное устройство было реализовано в лабораторной установке (рис. 3), в состав которой входят: электродвигатель переменного тока 1 мощностью 3,0 кВт; редуктор 2 с передаточным отношением 10; кристаллизатор 5, прикрепленный к корпусу 4 болтами; пресс-матрица 7; заливная воронка 8; соединительная муфта 3; дозатор 9. Все элементы прессового узла смонтированы на прочной сварной раме, обеспечивающей жесткость конструкции, предотвращая перекосы в соединительных муфтах и изгибы промежуточных валов в процессе литья – прессования металла.
На основе теории квазиравновесного двухфазного состояния были установлены температурные поля в переходной зоне твердожидкого расплава металла в канавке карусельного кристаллизатора для определения интенсивности и времени охлаждения слитка до заданной температуры прессования. Силовые параметры процесса определены методом баланса энергий, подводимых в деформационную зону и расходуемых в ней. Функциональная зависимость между механическими свойствами пресс-изделий и параметрами процесса непрерыв- – 188 –
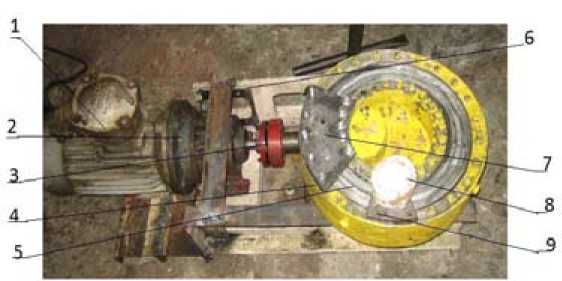
Рис. 3. Лабораторная установка непрерывного литья-прессования методом Конформ
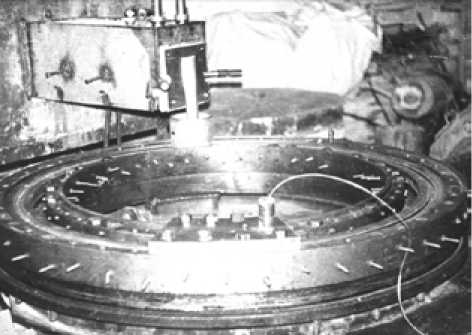
Рис. 4. Общий вид опытно-промышленной установки для совмещенного литья-прессования алюминиевых и медных сплавов ного литья-прессования получена с применением элементов математического планирования экспериментов. Все это позволило определить такие важные технологические и конструктивные параметры, как длину башмака (контейнера), достаточную для осуществления непрерывного прессования затвердевшей части слитка; время кристаллизации расплава металла, поступившего в канавку движущегося колеса, и протяженность этого участка; место подачи расплава в канавку колеса в зависимости от заданных значений температуры и скорости прессования, интенсивности охлаждения рабочего инструмента, а также энергосиловые параметры установки.
Результаты экспериментальной проверки на лабораторной установке теоретических зависимостей доказали их достаточную надежность и целесообразность для практического применения и были использованы для технического и технологического проектирования опытнопромышленной установки совмещенного литья-прессования алюминиевых и медных сплавов (рис. 4).
Привод опытно-промышленной установки включает электродвигатель постоянного тока мощностью 90 кВт с максимальной частотой вращения 1000 об/мин и редукторы с общим пере- даточным числом 320. Средний диаметр кольцевой канавки составляет 1200 мм, что при размере её поперечного сечения 40х40 мм обеспечивает производительность процесса непрерывного литья прессования латуни до 1,5 т в час. Для разливки расплавленного металла, поступающего из плавильной печи в литниковую коробку, применятся индукционный миксер ИЛКМ-2,5.
Опытно-промышленная установка совмещенного литья-прессования алюминиевых и медных сплавов, действующая по такой схеме, была нами спроектирована по заданию Каменск-Уральского завода ОЦМ и испытана в лаборатории кафедры ОМД Красноярского института цветных металлов и золота. Конструкция установки и принцип ее действия при изготовлении пресс-изделий из алюминиевых и медных сплавов описаны в монографии [5] и работе [6].
Таким образом, для отечественных металлургов создан инновационный комплекс технических и технологических решений в области непрерывного прессования методом Конформ и его совмещения с непрерывным литьем цветных металлов, внедрение которого позволит производить вполне конкурентоспособную продукцию на мировом рынке.
На этой же кафедре под руководством Н.Н. Довженко и С.Б. Сидельникова разработаны и исследованы способы совмещенной прокатки-прессования (СПП) и совмещенного литья-прокатки-прессования (СЛИПП) алюминиевых сплавов, которые по своим техникоэкономическим показателям могут составить конкуренцию способам Конформ и Кастэкс [13,14]. Экспериментальные исследования проводили на опытной установке СЛИПП, схема которой представлена рис. 5. В этом устройстве расплав заливается непосредственно в валки-кристаллизаторы, кристаллизируется в виде заготовки прямоугольной формы, которая подвергается деформации при помощи тех же валков, а затем выдавливается через калибрующее отверстие матрицы.
Устройство включает в себя: печь миксер 1 с расплавом, валок 3 с ручьем и валок 4 с выступом, имеющие водоохлаждаемые полости 5 и образующие закрытый калибр, перекрытый на выходе матрицей 6. Игла 7 расположена в обойме 8 соосно каналу с помощью винта 10 и державки 11. По периметру иглы 7 в обойме 8 выполнены каналы 12 для подачи смазки. Соот-
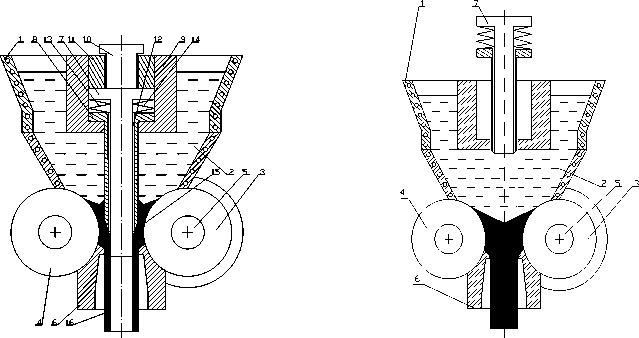
а) б)
Рис. 5. Устройство для бесслитковой прокатки-прессования полых (а) [15] и сплошных (б) пресс-изделий [16]
ношение критической рабочей длины иглы 7 и диаметра валка с ручьем 3 составляет 0,05-0,35. Механизм отвода иглы включает винт 10 и пружины 13, 14, а игла на части своей длины снабжена выступами 15, выполненными в поперечном сечении по форме каналов 12. Клиновидные полости 16 выполнены в матрице 6 с возможностью их охлаждения.
Отличительной чертой данного устройства является то, что оно снабжено установленной соосно матрице длинномерной иглой с механизмом ее отвода, жестко закрепленной фиксатором и расположенной в обойме с каналами для подачи смазки, размещенными по периметру иглы выступами для запирания каналов. При этом в валках выполнены водоохлаждаемые полости.