Интеллектуальная система регистрации отказов, анализа и корректирующих действий с использованием метода анализа подобия и метода анализа общей причины для обеспечения надежности изделий авиационной техники в процессе жизненного цикла
Автор: Шишкин Вадим Викторинович, Романов Юрий Владимирович
Журнал: Известия Самарского научного центра Российской академии наук @izvestiya-ssc
Рубрика: Механика и машиностроение
Статья в выпуске: 4-2 т.14, 2012 года.
Бесплатный доступ
Рассматриваются основные принципы создания системы FRACAS, устанавливаются критерии результативности данной системы. Выделяются две группы критериев результативности, определяются основные влияющие факторы в каждой группе, описывается применение метода анализа подобия и метода анализа общей причины в процессе обеспечения надежности авиационной техники на всех этапах жизненного цикла.
Авиационная техника, жизненный цикл, надежность, корректирующие действия
Короткий адрес: https://sciup.org/148201264
IDR: 148201264
Текст научной статьи Интеллектуальная система регистрации отказов, анализа и корректирующих действий с использованием метода анализа подобия и метода анализа общей причины для обеспечения надежности изделий авиационной техники в процессе жизненного цикла
Для создания высококачественных изделий авиационной техники (АТ) в условиях растущей конкуренции на рынке жизненно важно эффективно обеспечивать надежность на протяжении всего жизненного цикла (ЖЦ).
Одним из важнейших средств обеспечения надежности является система FRACAS (Failure Reporting, Analysis and Corrective Action System — система регистрации отказов, анализа и корректирующих действий), позволяющая постоянно выявлять, отслеживать и устранять причины отказов и неисправностей, возникающих на этапах производства и эксплуатации.
Абсолютное большинство иностранных авиационных предприятий используют системы FRACAS. В России можно отметить проект создания Системы Сбора и Анализа Эксплуатационных Данных (ССиАЭД) воздушных судов, реализуемого ЗАО «Гражданские самолёты Сухого» в рамках создания глобальной системы послепродажного обслуживания (ППО) семейства ближнемагистральных пассажирских самолётов Sukhoi Superjet 100 [1].
Необходимость применения и преимущества таких систем являются очевидными. Однако реализовать эффективную и производительную систему, гарантирующую в результате требуемый уровень надежности и улучшение конструкции, довольно сложно.
Рассмотрим критерии результативности и основные принципы создания результативной системы FRACAS (рис. 1). Для определения критериев результативности системы FRACAS рассмотрим изменение уровня надежности АТ на постпроизводственных этапах. Учитывая
сложность современной АТ и ее жизненного цикла, в начальный период эксплуатации для АТ характерно наличие систематических отказов. Это приводит к снижению надежности АТ в начальный период эксплуатации на некоторое значение Δ Rн . Величина Δ Rн зависит от количества видов дефектов, приводящих к систематическим отказам и от количества экземпляров АТ, выпущенной с такими дефектами.
При выявлении несоответствия требованиям к надежности АТ в процессе эксплуатации проводятся корректирующие действия, направленные на изжитие причин систематических отказов. В результате, по мере устранения причин систематических отказов и доработки изделий, находящихся в эксплуатации, происходит повышение надежности и доведение уровня надежности до требуемого. Время доведения надежности до требуемого уровня Δ tн зависит от времени определения причин систематических отказов, времени разработки результативных корректирующих действий, времени определения объема коррекции и проведения доработок.
Часто в процессе эксплуатации АТ проводится ее модернизация, обусловленная расширением спектра функциональных задач. При проведении существенной модернизации также возможно появление систематических отказов и снижение уровня надежности на значение Δ Rм , на доведение которого до требуемого уровня необходимо время Δ tм .
Таким образом, повышение эффективности обеспечения надежности АТ можно охарактеризовать следующими критериями:
-
1. Δtн, Δtм → min ;
-
2. ΔRн, ΔRм → min .
На значения первой группы критериев основное влияние оказывает своевременность и результативность корректирующих действий. Значения второй группы критериев определяются наличи-
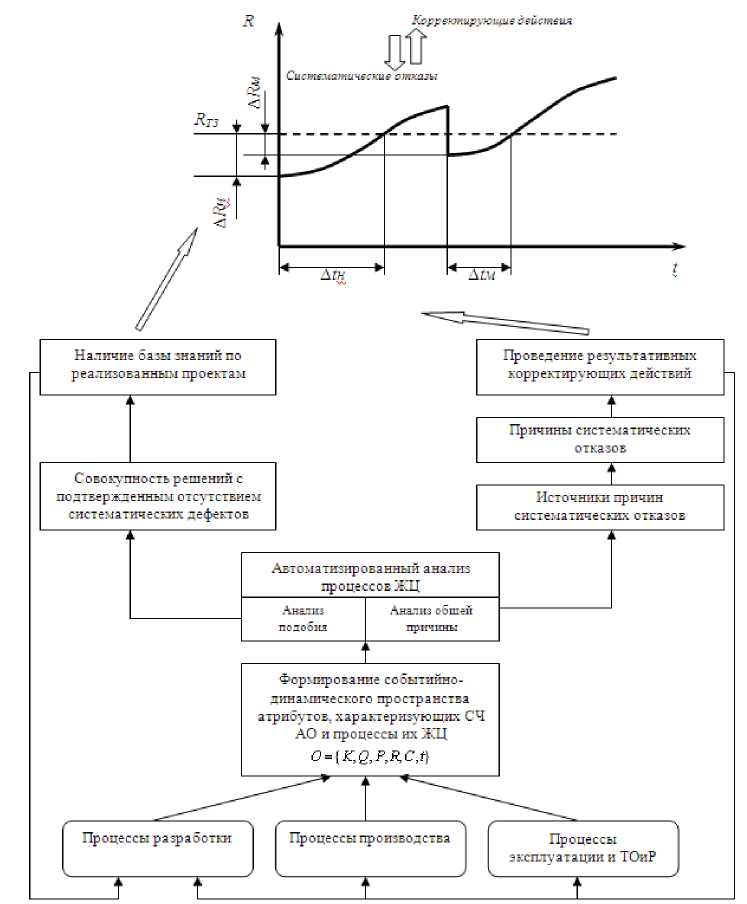
Рис. 1. Изменение уровня надежности на постпроизводственных этапах и последовательность действий, реализуемая системой FRACAS с автоматизированным анализом процессов ЖЦ
ем на предприятии, разрабатывающем АТ, базы знаний по реализованным проектам, что позволяет использовать проектные решения, проверенные по результатам реальной эксплуатации.
Для разработки результативных корректирующих действий необходимо определить причину систематических отказов. Причина отказа: обстоятельства в ходе разработки, производства или использования, которые привели к отказу[2]. Систематический отказ: отказ, однозначно вызванный одной причиной, которая может быть устранена только модификацией проекта или производственного процесса, правил эксплуатации и документации [2].
Из определений следует, что источниками отказов являются процессы разработки, производства и эксплуатации. Источниками общей причины отказов элементов при этом являются общие реализации процессов ЖЦ.
Для определения источника общей причины отказа может эффективно применяться анализ общего режима, применяемый для оценки безо- пасности систем и бортового оборудования воздушных судов гражданского назначения [3]. Анализ общего режима с точки зрения методологии FRACAS представляет собой анализ отказов АТ по результатам экспериментальной отработки на предмет выявления отказов и источников общего режима (то есть вызванных одной причиной). Для реализации такого метода необходимо составить перечень источников общей причины применительно к различным этапам жизненного цикла элементов АТ различного уровня разукрупнения и определить критерии принадлежности причин отказов к одному источнику.
Для создания базы знаний по реализованным проектам необходимо выделить проектные решения и оценить их по результатам реальной эксплуатации. Для этих целей можно эффективно применять анализ подобия. Анализ подобия – это структурированное сравнение элементов нового оборудования с подобными элементами ряда различных прототипов оборудования, для которых имеются данные надежности [4]. При этом необходимо определить сопоставляемые характеристики и обеспечить наличие и актуальность исходных данных на момент анализа.
При составлении перечней источников общей причины (анализ общего режима) и сопоставляемых характеристик (анализ подобия), как правило, выбирают:
-
- условия эксплуатации окружающей среды;
-
- процессы проектирования;
-
- процессы производства;
-
- процессы технического обслуживания и ремонта.
Учитывая, что источники общей причины и сопоставляемые характеристики можно представить как атрибуты элементов структуры для реализации системы FRACAS необходимо создание электронной структуры изделия, отвечающей потребностям методов анализа общего режима и анализа подобия.
Cструктуру АТ можно представить в виде формулы
O = { K , Q , t }, (1)
где K – множество элементов системы;
Q – множество связей между элементами;
t – момент времени, к которому относится описание АТ.
Среди всего множества элементов АТ можно выделить классы эквивалентности по уровню надежности (элементы одного типа). Из множества элементов, имеющих одинаковый уровень надежности, можно выделить подмножества элементов, имеющих одинаковые источники общей причины. Таким образом, формируются варианты применения однотипных элементов АТ относительно каждого источника систематических отказов.
При этом наличие систематических отказов по какому-либо источнику отказов вызывает резкое увеличение интенсивности отказа одного из вариантов применения и, как следствие, наличие неоднородности статистических оценок, что может являться критерием необходимости разработки корректирующих действий по данному процессу.
Таким образом, выражение (1) необходимо дополнить до вида
O = { K , Q , P , R , t }, (2)
где символ P означает параметры процессов, характеризующие элементы БО с точки зрения источников общей причины;
символ R - параметры, определяющие фактическую интенсивность отказа элемента или параметра потока отказов.
Оценка результативности корректирующих действий выполняется сравнением надежности элементов, изготовленных без учета корректирующих действий, с элементами, изготовленными с учетом корректирующих действий. Для идентификации внедренных корректирующих действий выражение (2) необходимо дополнить до вида
O = { K , Q , P , R , C , t }, (3)
где символ С – атрибут, определяющий признак внедренного корректирующего действия.
На рис. 1 показано изменение уровня надежности на постпроизводственных этапах и последовательность действий, реализуемая системой FRACAS с автоматизированным анализом процессов ЖЦ.
Таким образом, создание системы регистрации отказов, анализа и корректирующих действий с использованием методов анализа подобия и анализа общей причины позволяет в едином событийно-динамическим пространстве атрибутов эффективно решать задачи обеспечения надежности АТ в течение всего ЖЦ.
Список литературы Интеллектуальная система регистрации отказов, анализа и корректирующих действий с использованием метода анализа подобия и метода анализа общей причины для обеспечения надежности изделий авиационной техники в процессе жизненного цикла
- Стартует проект внедрения системы управления надёжностью воздушных судов (FRACAS) в ЗАО «Гражданские Самолёты Сухого». URL: http://www.pbaconsult.com/index.php?page=7&mode=event&sub=159 (дата обращения 4.09.2012).
- ГОСТ 27.002-2009 Надежность в технике. Термины и определения. М.: Стандартинформ, 2010.
- Руководство Р-4761. Руководство по методам оценки безопасности систем и бортового оборудования воздушных судов гражданской авиации. АР МАК, 2010.
- ГОСТ Р ИСО/ТО 10017-2005 Статистические методы. Руководство по применению в соответствии с ГОСТ Р ИСО 9001. М.: Стандартинформ, 2005.