Интеллектуальное электронное документирование технологических объектов в системе PLM
Автор: Тугенгольд Андрей Кириллович, Тишин Александр Сергеевич, Лысенко Алексей Федорович, Цишкевич Захар Андреевич
Журнал: Вестник Донского государственного технического университета @vestnik-donstu
Рубрика: Технические науки
Статья в выпуске: 3 (54) т.11, 2011 года.
Бесплатный доступ
Представлен инновационный подход к документированию технологических объектов, даны рекомендации и методики создания интеллектуального паспорта технологического объекта в системе PLM, его базы знаний, организации, представления и обработки данных и знаний.
Интеллектуальный электронный паспорт, электронное документирование, технологические объекты, станки, база данных, база знаний, жизненный цикл изделия
Короткий адрес: https://sciup.org/14249554
IDR: 14249554
Текст научной статьи Интеллектуальное электронное документирование технологических объектов в системе PLM
Введение. Необходимость повышения качества выпускаемой продукции и возросшая конкуренция привели к заметному ужесточению требований, предъявляемых к технологическим машинам. Для того чтобы сохранить конкурентоспособность и вести эффективную экономическую деятельность, необходимо применять результативные системы контроля и управления этими машинами на всех этапах жизненного цикла. В статье предлагается инновационный подход к решению задач повышения эксплуатационных качеств технологических машин, в том числе металлорежущих станков. Подход основывается на следующих базовых концептуальных положениях.
-
1. Технологические машины как сложные мехатронные системы наделяются системой знаний (СЗ) о своих особенностях, в том числе преимуществах и недостатках, отличающих маши-ну-индивидуум1 от себе подобных. Этим обеспечивается информационная и интеллектуальная поддержка управления технологическим процессом обработки и сопровождения в жизненном цикле. Так СЗ в виде интеллектуального узла или блока УЧПУ станка используется для планирования и программирования процесса обработки конкретной детали. Планирование предполагает обеспечение экономически эффективной обработки при условии удовлетворения конструкторских требований к точности детали. Обеспечение точности обработки основывается на использовании технологии искусственного интеллекта в формировании предложенного в [1] обобщенного подхода – Generalized Knowledge Mining for Technological System (GKM TS) – «Обнаружение обобщенных знаний для технологической системы».
-
2. Подход предполагает реализацию указанных концептуальных положений путем создания для каждой единицы технологического оборудования интеллектуального электронного паспорта. Это дает возможность использования СЗ, формализуемой в разработанной документации, и возможность интеграции электронного паспорта в информационную инфраструктуру станка и технологической системы предприятия. Таким путем создается информационная и интеллектуальная поддержка управления процессом обработки на станке и, в целом, эксплуатации станка, включая обслуживание, ремонт и утилизацию.
Повышение эффективности функционирования в производственных условиях в течение жизненного цикла открывает новые возможности в соответствии с подходом PLM (Product Lifecycle Management – технология управления жизненным циклом изделий) и системой электронного документирования сложных технических объектов. Электронное представление информации о сложном техническом объекте стало нормой на мировом рынке высокотехнологичной продукции. Процессы в PLM в современных условиях немыслимы без применения интерактивных электронных технических руководств, технической и эксплуатационной документации, обучающих систем. Это особенно важно для станкостроительных предприятий, представляющих свои изделия на мировой рынок.
Постановка задачи. Стоит обратить внимание на следующие положения, ставшие отправными моментами в формировании предложенного инновационного подхода.
-
1. В проблеме повышения точности обработки деталей на металлорежущих станках внимание специалистов сосредоточено на двух аспектах [2]: анализ причин, вызывающих погрешности, и их устранение в процессе конструирования и изготовления станков; синтез методов учета составляющих погрешностей и методов управления процессом обработки, обеспечивающих заданную точность.
-
2. Документирование мехатронных технологических объектов. В сложившейся системе документального сопровождения технологического оборудования основную роль играет паспортизация. Паспорт – это технологический документ, содержащий сведения об основном назначении и особой применимости оборудования, которые определяют области его рационального использования. Например, в паспорте станка приводятся его кинематическая схема, перечень и характеристика применяемых инструментов и приспособлений, характеристика системы управления, электрическая схема привода и другие данные.
Несмотря на значительное количество исследований, выполненных по этой проблеме, актуальность продолжения разработок не ослабевает в связи с востребованностью и повышением значимости их результатов [3–5]. Однако геометрические погрешности получаемых поверхностей и особенно погрешности контурной обработки представляют собой нестационарные функции, в ряде случаев с негауссовскими законами распределения. В общем случае для такой сложной технологической системы, как станок, существенно затрудняется ее моделирование с помощью известных математических выражений. Велико число переменных и параметров, измерение отдельных переменных и определение их влияния на погрешности обработки поверхностей аналитическими методами сильно затруднено или недостижимо. Можно полагать, что создание полностью адекватной модели поведения такой системы в процессе обработки практически невозможно.
При традиционных системах управления станками стохастичность протекания самого технологического процесса, изменение внешних условий, погрешности исходных и текущих положений рабочих органов и инструмента, состояние заготовки и режущей части инструмента, отсутствие возможности получения достаточно точной информации о положении вершины инструмента относительно заготовки вносят неопределенность в формирование управлений рабочими органами станка. Применение методов интеллектуального управления станком позволяет сформировать оценки складывающейся ситуации, в том числе оценку состояния системы и оценку достигаемых параметров качества изготавливаемой детали, а также сделать правильный выбор из альтернативных вариантов управлений.
Использование алгоритмов искусственного интеллекта открывает возможности современного подхода к проблеме обеспечения точности обработки и основывается на принципе динамической самообучаемости и приспособляемости системы управления станка к реальным условиям.
К недостаткам существующей системы ведения паспортной и другой документальной информации многие станкостроительные предприятия относят:
-
- отсутствие возможности организованного документооборота технологических данных; несистемное хранение данных;
-
- практически полное отсутствие информационного обмена данными, содержащими результаты испытаний на геометрическую точность станков и точность обработки образцов изделий. Такие данные должны быть в сопроводительной документации в соответствии с существующими ГОСТами, устанавливающими показатели качества станков и методы испытаний (контроля) для их определения, в том числе ГОСТ 8-82, ГОСТ 27843-2006 и др.;
-
- невозможность оперативного поиска данных из-за отсутствия в электронном виде паспортной и другой документальной информации.
-
3. PLM-подход. PLM – это организационно-техническая система, обеспечивающая управление всей информацией об изделии и связанных с ним процессах на протяжении всего его жизненного цикла, начиная с проектирования и производства до снятия с эксплуатации. К таким изделиям относятся различные сложные технические объекты, например корабли и автомобили, самолёты и ракеты, различные машины и др. Информация об объекте, содержащаяся в системе PLM, является цифровым макетом этого объекта.
Специфические особенности, которыми обладает каждый станок, не учитываются при программировании обработки, практически паспорт станка и другая сопроводительная информация при этом не используются.
Для решения подобных задач при эксплуатации наукоемкого оборудования всё большее применение получают интерактивные электронные технические руководства, позволяющие осуществлять накопление и обмен информацией на всех стадиях жизненного цикла каждого конкретного технологического объекта.
Сам термин «управление жизненным циклом изделия» появился как результат почти двадцатилетней эволюции соответствующих рынков и технологий. В последние годы система сформировалась и постоянно расширяется как по степени охвата, так и по мощности предлагаемых решений. Система PLM ныне используется для решения задач:
-
- создание интеллектуальной базы знаний и информации, относящихся к изделию – техническому объекту;
-
- управление этими составляющими;
-
- адресное использование знаний и информации на протяжении всего жизненного цикла изделия.
Сочетание PLM с другими областями приносит новые возможности и открывает такие сферы, где потенциал связанного с объектом интеллектуального капитала реализуется внутри расширенной сферы.
Среди областей применения PLM важными для мехатронных технологических объектов и прежде всего для металлорежущих станков является управление интеграцией электронных устройств и программного обеспечения, управление техническими характеристиками, анализ и управление моделированием и пр. Подготовка информации в структурированной среде гарантирует ее доступность и управляемость на всем протяжении жизненного цикла [6]. Интерактивные электронные технические руководства для станков в системе PLM помогут решать задачи такого рода с большим эффектом.
Системная архитектура интеллектуального электронного паспорта технологического объекта. Для решения проблемы информационного обеспечения интеллектуального электронного документирования технологического оборудования, в том числе станков, предлагается создание для каждой единицы оборудования интеллектуального электронного паспорта (ИЭП) в системе PLM. Архитектура ИЭП состоит из двух частей: базовой, содержащей основную техническую информацию объекта, и интеллектуальной надстройки с СЗ и интерфейсами связей с УЧПУ и оператором (рисунок). Кратко остановимся на содержании каждой из частей.
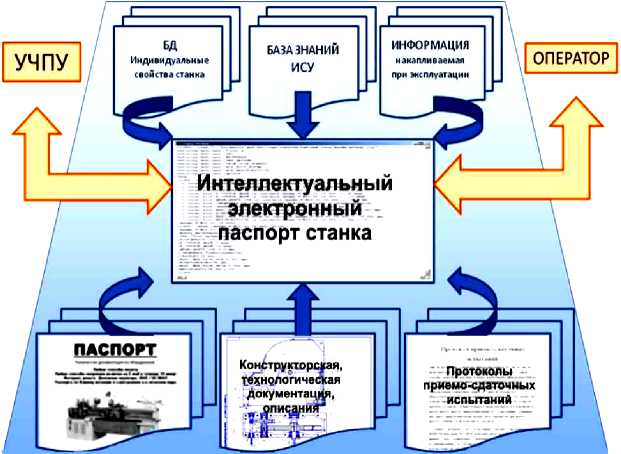
Источники информации в интеллектуальном электронном паспорте
ЧАСТЬ 1. БАЗОВАЯ ТЕХНИЧЕСКАЯ ИНФОРМАЦИЯ
-
1.1. Регистрационное документирование. В число обычно представляемых заказчику документов входит паспорт станка. Это документ с идентификационным номером и наименованием станка, содержащий сведения, удостоверяющие гарантии изготовителя, значения основных параметров и характеристик (свойств) изделия, а также сведения о сертификации и утилизации изделия. Прочие документы:
-
- гарантийное обслуживание производителем;
-
- сведения о капитальных ремонтах, техническом обслуживании и пр.;
-
- специальные эксплуатационные инструкции;
-
- другая необходимая информация по станку.
-
1.2. Информация по станку, включает следующие руководства:
-
- по транспортировке и установке станка,
-
- по эксплуатации станка,
-
- о стойке ЧПУ и программированию на станке,
-
- по сервисному обслуживанию.
Руководство по эксплуатации содержит сведения об особенностях конструкции, принципе действия, характеристиках (свойствах) станка, его составных частях и указания, необходимые для правильной и безопасной эксплуатации (использования по назначению, техническому обслуживанию, текущему ремонту, хранению и транспортированию).
-
1.3. Протоколы приемосдаточных испытаний станка. В электронном паспорте станка приводятся его кинематическая схема, перечень и характеристика применяемых инструментов и приспособлений, характеристика системы управления, электрическая схема привода и другие данные. Главный результат применения электронного отображения этой базовой части паспорта – организация легкого, оперативного, территориально-распределенного доступа к данным. С помощью него создается единая база данных, содержащая полную информацию об оборудовании. Для поиска и работы с информационной документацией не потребуется пользоваться сложно организованными бумажными архивами и постоянно возвращаться к ним во время выполнения плановопрофилактических работ. Поэтому эффективность работы эксплуатационного персонала возрастает как минимум на 20% (по зарубежным оценкам). Это важно в связи с тем, что мероприятия по совершенствованию технологии и интенсификации режимов обработки требуют систематического
пересмотра паспортных данных. Поэтому корректировка паспорта проводится частично на месте установки станка, данные уточняются после капитального ремонта и модернизации.
Первая базовая часть ИЭП станка функционально реализована как интегрированная база данных, представляющая собой совокупность графической, текстовой и табличной информации. Она содержит следующие данные: общие данные; заводские данные; сведения о техническом состоянии станка; результаты приемосдаточных испытаний; технико-экономические показатели; автоматический расчёт наработки станка; сведения об отказах и проводимых ремонтах; сведения об обследованиях станка и модернизации; результаты освидетельствования станка. Кроме того, предполагается наличие прогноза ремонтных работ.
Вторая часть представляет собой интеллектуальную надстройку с системой знаний и интерфейсами связей ИЭП с УЧПУ и операторами.
-
ЧАСТЬ 2. ИНТЕЛЛЕКТУАЛЬНАЯ ИНФОРМАЦИЯ
-
2.1. Индивидуальные свойства станка (наследуемые, оперативные).
-
2.2. Система знаний станка-индивидуума (собственная система знаний).
-
2.3. Связи ИЭП с УЧПУ и операторами.
Знания индивидуальных свойств станка служат информационной и интеллектуальной поддержкой управления процессом обработки на станке (а в целом, и эксплуатации станка, включая обслуживание, ремонт и утилизацию).
Основной информацией, характеризующей индивидуальные особенности станка, являются сведения по параметрам и свойствам, влияющим на точность обработки деталей и производительность.
Известно, что на погрешность обработки детали оказывает влияние значительное множество факторов [2]:
F = (f . , f . , f 3 , , fk ). (1)
Множество факторов (1), или входных воздействий, влияющих на общую погрешность F , в зависимости от возможности получения знаний о них может быть представлено в виде совокупности из «наследуемого» множества Н и «оперативного» множества О :
F =(F h , F o ), (2)
F h = ( f h 1 , f h 2 ,^, f hm );
F o = (f 1 , f o 2 ,^, j on ).
Под наследуемым множеством F h подразумевается совокупность m факторов, знания о которых получают при приемосдаточных или тестовых измерениях, а совокупность n факторов, измеряемых непосредственно в процессе обработки, отнесена к оперативному множеству F o . Одна из причин такого деления факторов заключается в ограниченной возможности получения оперативной информации от средств контроля непосредственно в процессе обработки детали [2]. Примерами наследуемых факторов являются отклонения от плоскостности столов, непараллельность перемещения суппортов относительно оси шпинделя, отклонения от взаимной перпендикулярности направлений перемещений рабочих органов и пр. К оперативным факторам относятся, например, ошибка датчика перемещений, погрешность наименьших номинальных перемещений рабочего органа при последовательных дискретных перемещениях, погрешности привода, изменяемые при рабочем ходе во время обработки и др.
В собственную СЗ станка кроме базы знаний по факторам погрешностей входят совокупности правил принятия решений по различным ситуациям в обработке, видам обработки (длина сверления, расточка, конусы, сферы, резьбы …) и требуемым параметрам точности (размерная точность, соосность и пр., шероховатость…). Оценка ситуации и принятие решений выполняется многоуровневой интеллектуальной системой управления (ИСУ) [2]. Программа синтеза решений по количеству и параметрам проходов определяется исходя из наследуемых и оперативных данных и знаний. В функции этой системы управления входят прогнозирование точности обработки, 323
принятие решений и программы действий, сопоставление прогнозов с результатами обработки деталей и накопление знаний.
Связи между ИЭП и УЧПУ станка предусматривают возможность использования принимаемых ИСУ решений для составления или коррекции управляющей программы, а также пополнения базы данных (БД) и базы знаний (БЗ) паспорта. Связь с операторами обеспечивает доступа к ИЭП через информационную сеть предприятия.
Кроме того, должны быть решены вопросы передачи устанавливаемой на компьютерную систему конечного пользователя управляющей системы и обеспечение удаленного доступа к данным ИЭП, скомплектованным разработчиком (по ГОСТ 2.601-2006 ЕСКД – эксплуатационные документы).
Формирование обобщенных знаний. Предлагаемый в статье подход предусматривает, что оценка ситуаций и принятие решений в ИСУ технологических систем производится на базе формируемых обобщенных знаний. Решения, соответствующие требованиям точности обработки, принимаются ИСУ станка при использовании обобщенных знаний, синтезируемых в БЗ на основе наследуемой информации из имеющейся совокупности F h и оперативной информации F o . Для синтеза обобщенных знаний используются возможности технологии Data Mining [1]. Инструментарий Data Mining, как указывалось, открывает средства для формирования нового обобщенного подхода GKM TS к построению ИСУ технологическими объектами - интерпретации практически полезных и доступных данных в производственных условиях о состоянии элементов технологической системы и формировании целостной системы знаний, необходимых для управления процессами.
В программу испытаний и обработки данных измерений включаются процедуры обнаружения знаний о влиянии совокупного многообразия факторов F на результирующие погрешности обработки детали с помощью технологии Data Mining и обучения ИСУ конкретного станка-индивидуума. Система обучения ИСУ (обучение с учителем) предусматривает, что входы – это дискретно регистрируемые изменения отклонения (от принятого значения для получения нужного размера детали) одной из составляющих погрешностей или их сочетания, а выходы – отклонения размера или формы, или взаиморасположения поверхностей. При этом выполняется последовательный перебор составляющих и их значений.
На основании совокупности примеров входных и выходных данных удается получить некоторую совокупность функций, которая аппроксимирует корреляцию между входными воздействиями и результирующей погрешностью, обеспечивая формирование БЗ в ИСУ станка. Кроме этого определяются (вероятностные и весовые) оценочные характеристики влияния каждого фактора множеств F h и F o .
При эксплуатации станка в процессе обработки детали информационная база ИСУ основывается на совокупности поступающей оперативной информации от тех датчиков, которые используются при работе станка, и знаний о влиянии наследуемых факторов. Cовокупный учет факторов, оказывающих влияние на результирующие погрешности обработки детали, с помощью системы нечетких отношений (установленных методом Data Mining) создает возможность отображения и прогнозирования поведения технологической системы в целом. Это позволяет решать вопросы повышения точности комплексно, а не частично или адресно, решая изолированно задачу учета влияния на точность обработки только износа инструмента, например, или только наследственности припуска. Но и в случае формирования обобщенных знаний для каждого станка определяется минимально необходимый состав информации о погрешностях, достаточный для достижения необходимой точности.
Как принято при нечетком прогнозировании, модель предсказания погрешности обработки поверхности представляется в виде множества правил. При заданных значениях входных переменных (факторов) f i оценку выходного значения погрешности обработки y* можно определить по следующей зависимости [7]:
y*= -"= - 2i < у. ;S=L 21, где n - число правил, yi - выходное значение, вычисленное по i - му правилу, gi - вес, представляющий значение истинности i - го правила.
При использовании для прогнозирования точности обработки нейронных сетей [2] в алгоритм вывода решений включаются процедуры:
-
- определение обучающей и валидационной выборок;
-
- подбор параметров нейросети;
-
- обучение нейросети;
-
- проверка работоспособности нейросети в реальных условиях.
Для полноценного эффективного функционирования интеллектуальных электронных паспортов технологического оборудования необходимо решение ряда вопросов, включая следующие:
-
- Накопление и обмен информацией на всех стадиях жизненного цикла каждого конкретного технологического объекта.
-
- Гармонизация терминологии, типов, видов документов, форматов их электронного представления, протоколов работы с ними, средств защиты от несанкционированного доступа.
-
- Информационная и интеллектуальная поддержка управления не только процессом обработки, но и в целом эксплуатации технологического объекта, включая обслуживание, ремонт и утилизацию и пр.
В состав работ по внедрению системы интеллектуальной электронной паспортизации целесообразно включить совокупность мероприятий, в том числе:
-
- проектирование форматов паспортов оборудования;
-
- организацию ввода паспортных данных с клиентских мест специалистов предприятия;
-
- создание БД моделей оборудования;
-
- организацию выборки и пополнения информации из БД И БЗ и пр.
Интеллектуальные электронные паспорта станков могут создаваться как на предприятиях-изготовителях станков, так и на эксплуатирующих предприятиях (продумать сокращенный вариант для последних) для экспорта.
Заключение. Интеллектуальное электронное документирование и паспортизация станков является важным этапом на пути создания единой среды эксплуатации, программирования и обслуживания станков и другого технологического оборудования на различных предприятиях и от различных производителей. Это средство построения информационной системы мониторинга эксплуатационных данных промышленного предприятия.
Кроме непосредственного повышения точности и производительности за счет возможности прогнозирования и реализации наиболее рационального использования технологического оборудования обеспечивается: обмен информацией; возможность выполнения вычислительных процедур для технологических нужд и для определения остаточного ресурса надежности оборудования; полная сохранность баз данных и знаний ИЭ паспортов на сервере за счет организации копирования и восстановления информации; возможность организации выборки данных по любым наборам параметров документальной информации и пр.
Список литературы Интеллектуальное электронное документирование технологических объектов в системе PLM
- Тугенгольд А.К. Оценка ситуации и принятие решений интеллектуальной системой управления технологическим объектом/А.К. Тугенгольд//Вестн. Донск. гос. техн. ун-та. -2010. -Т. 10, № 6. -С. 860-867.
- Тугенгольд А.К. Интеллектуальное управление мехатронными технологическими системами/А.К. Тугенгольд, Е.А. Лукьянов. -Ростов н/Д: Издательский центр ДГТУ, 2004. -117 с.
- Xu N. Systematic Investigation of Tool Wear Monitoring in Turning Operations/N. Xu, S.H. Huang, J. Snyder//ASME International Mechanical Engineering Congress and Exposition, November 5-11, Orlando, USA. -2005.
- Huang S.H. Tolerance-based Process Plan Evaluation Using Monte Carlo Simulation/S.H. Huang, Q. Liu, R. Musa//International Journal of Production Research. -2004. -Vol. 42. -No. 23. -Pp. 4871-4891.
- Laperriere L. Tolerance Analysis and Synthesis Using Jacobian Transforms/L. Laperriere, H. A. ElMaraghy//Annals of the CIRP. -2000. -Vol. 49. -No. 1. -Pp. 359-362.
- Weidenbrueck D. S1000D: A Standard for Technical Documentation/D. Weidenbrueck. [Электрон. ресурс]. -Режим доступа: http://tc.eserver.org/28083.html.
- Прикладные нечеткие системы/под ред. Т. Тэрано, К. Асаи, М. Сугено. -М.: Мир, 1993. -368 с.