Инженерия поверхности деталей машин
Автор: Амельченко Николай Александрович, Анистратенко Николай Евгеньевич, Добрынина Лилия Сергеевна, Михайлов Сергей Викторович, Балашов Олег Евгеньевич
Журнал: Сибирский аэрокосмический журнал @vestnik-sibsau
Рубрика: Технологические процессы и материалы
Статья в выпуске: 1 (14), 2007 года.
Бесплатный доступ
Повышению износостойкости деталей машин и механизмов способствует инженерия их рабочих поверхностей с применением различных методов. Плазменная технология, являясь одним из методов инженерии поверхности, нуждается в совершенствовании процесса. Рассмотрены тепловые условия и механизм формирования покрытия при напылении. Показана возможность повышения эксплуатационных показателей покрытий из порошковых материалов нанометровых размеров.
Короткий адрес: https://sciup.org/148175447
IDR: 148175447
Текст научной статьи Инженерия поверхности деталей машин
Основными показателями качества машин являются надежность и ресурс, которые определяются свойствами поверхностных слоев деталей и соединений: пределом выносливости, коррозиестойкостью, износостойкостью, коэффициентом трения, контактной жесткостью, прочностью и герметичностью соединения. Снижение технических характеристик машин в процессе эксплуатации ниже допустимого уровня, как правило, влечет за собой значительные материальные расходы, связанные с восстановлением изношенных механизмов или их заменой. Достижение высокого качества и эксплуатационной надежности машин, а также их более низкой стоимости, являющихся условием обеспечения высокого и устойчивого уровня рыночной конкурентоспособности, возможно лишь на основе применения новых перспективных разработок и наукоемких технологий.
Как известно, причина низкого ресурса деталей и элементов конструкций связана преимущественно с износом и коррозионным повреждением их рабочих поверхностей [1]. В процессе эксплуатации рабочие механизмы подвергаются воздействию окружающей среды и технологических сред, применяемых в производственном процессе в качестве исходных или конечных при изготовлении сложных соединений и изделий, а также сред, используемых для осуществления рабочего цикла, например, в узлах трения - смазочные материалы. Актуальной проблемой в машиностроении является повышение износостойкости режущего инструмента, используемого в различных процессах при металлообработке.
Трибологические явления проявляются практически во всех сферах индустрии и в быту. Потери средств в машиностроении развитых государств, вследствие трения и износа, достигают~4...5 % национального дохода. Сопро- тивление трению поглощает во всем мире 30...40 % вырабатываемой энергии, которая при трении не просто теряется, а превращается в теплоту, вызывая нагрев механизмов и узлов машин. Во многих случаях последствия нагрева связаны с отказами и авариями. Примерно 80...90 % отказов машин происходит из-за износа узлов и деталей, а также рабочего инструмента. С целью снижения трения в мире за год расходуется более 108 т смазочных материалов. Отработавшие смазочные материалы, как правило, подлежат переработке или утилизации, иначе они представляют серьезную опасность для окружающей среды. За полный цикл использования машин эксплуатационные расходы, трудоемкость ремонта и затраты материалов на ремонт в несколько раз превышают затраты на изготовление новых машин [2].
Существует чрезвычайно высокая потребность в методах инженерии поверхности для защиты от коррозии и повышения износостойкости, улучшения качества машин, длительной эксплуатации различных объектов в космосе при высоких температурах и других условиях.
Инженерия поверхности охватывает комплекс научных дисциплин, среди которых особое место занимают технологии поверхностной обработки, нанесения покрытий и модифицирование поверхностных слоев.
Совершенствование вакуумных и плазменных технологий является одним из методов инженерии поверхности. В настоящее время доля износостойких газотермических покрытий, применяемых в промышленности, в общем объеме достигает 40 %. Считается, что конструкция сохраняет работоспособность в случае, если износ ее рабочей поверхности не превышает нескольких десятых миллиметра, и в этом случае восстановление конструкции напылением покрытия является экономически обоснованным [3].
Основная часть исследований, выполненных ранее [4], проводилась с использованием материалов для формирования газотермических покрытий с размерами частиц 20-60 мкм. На основе анализа результатов было выявлено, что формируемые покрытия обладают повышенной пористостью, низкими значениями адгезионной и когезионной прочности, значительно уступают по названным параметрам своим компактным аналогам. Это ограничивает их более широкое применение в промышленности.
С целью расширения технических возможностей и областей применения в настоящее время проводимые исследования в большей степени связаны с разработками технологии нанесения покрытий из нанопорошков. Достаточно эффективно совершенствуются методы высокоскоростного газоплазменного напыления (HVOF) и плазменного напыления на воздухе (APS) или в контролируемой атмосфере (VPS). Каждый из них имеет свои преимущества и ограничения.
Для напыления покрытий с наноструктурой используются материалы в следующем виде:
-
- суспензия с наночастицами или растворы;
-
- агломерированный композиционный сферический порошок диаметром 10-50 мкм, полученный распылительной сушкой суспензии, содержащей наночастицы (рис. 1);
-
- спеченные наночастицы с последующим дроблением до размера фракции 10-50 мкм;
-
- механически легированные порошки, содержащие наночастицы.
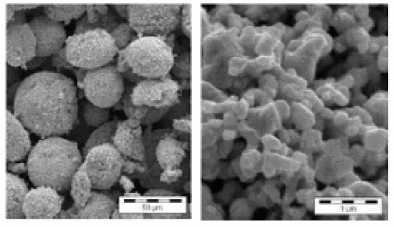
Рис. 1. Микрофотография агломерированных порошков WC + 15% Со (средний размер WC фазы - 40 нм [3])
При формировании прочного покрытия из материалов любой дисперсности значительную роль играет стадия деформации напыляемой частицы на подложке. Прочное соединение частиц покрытия с подложкой возможно при наличии физико-химического взаимодействия на всей площади их контакта. Вторичным признаком такого взаимодействия является процесс смачивания между подложкой и напыляемой частицей, а также частиц между собой. При этом большое значение имеет распределение температурных полей в объеме формируемого покрытия, постоянно изменяющихся во времени.
В настоящей работе приведены результаты исследования по оценке влияния температурного фактора на процесс формирования напыляемых покрытий.
Для расчета нестационарных температур в объеме покрытия (рис. 2) с учетом преобразований использовано уравнение теплопроводности (1), выведенное нами ранее для эквивалентного цилиндра [4], высота которого изменяется за счет осаждаемых частиц при напылении (рис. 2, а):
д T 1
--=---- х д t Cp -р
д д x

+ 2,5 а- 4k ( T - T ) - .
где q - удельный, эффективный тепловой поток; а - коэффициент теплоотдачи на границе «частица-покрытие»; % - коэффициент теплопроводности напыляемого материала; р - плотность материала покрытия; С р - удельная теплоемкость; к- коэффициент сосредоточенности частиц; Т - температура газа, омывающего фигуру напыления; Т0- начальная температура.
Задача решена в подвижной системе координат с началом отсчета (х = 0) в центральной части пятна (рис. 2, б) при граничных условиях:
-
а) в объеме покрытия на оси цилиндра
при х ^^ , Т( ^ , t) - т 0 —(-^ = 0; (2) д x
-
б) на поверхности центральной части
дT(0,t пятна прих - 0 -% —~---= q , дx
с начальными условиями t = 0, Т(х, 0) = Т0= 300 К.
В результате решения тепловой задачи получены за
висимости, которые позволяют имитировать температурное распределение в объеме покрытия (рис. 2, в). На основании результатов исследований установлено, что если х = x(t), то температура в точке с координатойх для момента времени t характеризуется зависимостью:
T ( x , t ) = — . q = х
2 VX- 2,5 a- 4k

, 1
- erfc —==
2 4F0
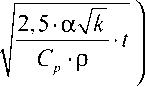

( - erfc
I
1 2,5 -a 4k
—;= + —----
2 4Fo \ Cp • P
2,5 a- 4k —
2,5 a- 4k • ---------------------------------- -
- 1
- T
- 1 + T o - e
Еслих = 0, то уравнение (4) преобразуется в следую
щее выражение и характеризует температуру на поверхности слоя покрытия:
T (0, t ) = —х 2V X- 2,5 a- 4k
erfc
2,5 -a 4k
erfc
-
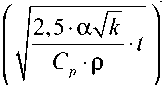
-
2,5 a- 4k
---— t
।
p
ченности к. Основным регулирующим параметром для g является коэффициент к, поскольку G и в взаимосвязаны и увеличение G компенсируется снижением в .
На основании анализа результатов экспериментов выявлено, что коэффициент сосредоточенности к, характеризующий закон распределения осаждаемого материала в пятне напыления, зависит от конструктивных особенностей распылителя. Для оценки величины к предложена методика расчета по расходным характеристикам процесса и массогабаритным характеристикам покрытия: массе напыленной фигуры т, ее высоте 8 т и плотности напыленного материала р и:
к = п • р п • 8 тах/т = п • pnT mm/G • в , (7) где v = 8 / т и т = G • в • т ; Т - время напыления фигуры, с.
Исследования микроструктуры напыленных покрытий (рис. 3) показали, что, осуществляя процесс напыления при обычных расходах вводимого в распылитель материала (производительность G = 0,5-1 кг/ч), за счет ком-пактирования струи в объеме покрытия можно обеспечить существование весьма высоких температур, способствующих возникновению на поверхности жидкофазного состояния. В этом случае возможно изменение механизма процесса кристаллизации частиц и, как следствие, уменьшение пористости, изменение структуры, фазового состава, повышения плотности и других эксплуатационных характеристик. Повышение износостойкости напыленного слоя следует ожидать за счет большей плотности и создания в нем аморфной структуры.
- 1 + T o - e
Для подвижной границы эквивалентного цилиндра с
учетом происходящего тепло- и массообмена удельный тепловой поток q определяется из граничного условия
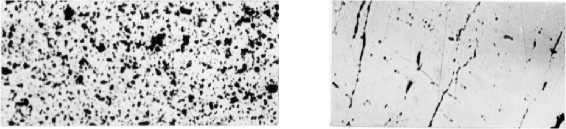
а б
Рис. 3. Изменение микроструктуры напыленных слоев керамики: а - на границе контакта с основой;
б - верхние слои покрытия
(3) по выражению
q = § 'С' Т Т о) + АЯ + qэкз]+ q a + q, (6)
В зависимости от теплофизических характеристик распыляемого материала и технологических условий напыления проведено моделирование теплового состояния покрытия. Результаты расчетов показывают, что характер взаимодействия осаждаемых частиц и распределение
температуры в покрытии существенно зависит от удельной производительности напыления g = G • в • к, определяемой расходом порошка G, коэффициентом использования материала (КИМ) в , и коэффициентом сосредото
Выявлено, что создание таких условий напыления лежит за пределами технологических возможностей существующего оборудования.
Недостаточная адгезионная и когезионная прочность покрытий во многих практических случаях связана с распределением контактных, межфазных и остаточных напряжений. Задача о полезном использовании или управ-

а б в
Рис. 2. Распределение нестационарных температур в объеме покрытия при напылении a-Al2O3: 1 - УПУ-8М (g = 0,32 г/с^см2, к = 2 см-2); 2 - плазмотрон ПКП (g = 0,87 г/с^см2, к = 5 см-2)
лении остаточными напряжениями в покрытиях с целью повышения качественных характеристик поверхностного слоя пока еще не решена.
Анализ микроструктуры напыленной керамики показывает, что в нижних слоях характерно образование пористой структуры (рис. 3, а). В данной зоне покрытия возможно появление аморфной фазы. Это связано с большим градиентом температуры на границе покрытие-подложка в результате резкого отвода тепла. По мере аккумуляции температуры с увеличением толщины покрытия механизм кристаллизации частиц изменяется, что приводит к образованию более плотной структуры в слое с меньшей пористостью (рис. 3, б).
Как показали исследования, одним из механизмов преобразования кристаллического строения в аморфную структуру на деталях из сплавов эвтектического состава является кратковременное воздействие на поверхность высококонцентрированных источников и последующее резкое охлаждение зоны нагрева. При этом скорость отвода теплоты в металл должна составлять не мене 105-108 К/с. Для деталей из других материалов перед обработкой следует нанести тонкий слой порошка этого металла с нужными для амор-физации присадками в количественном соотношении, близким к эвтектическому Данное направление является предметом дальнейших исследований.
В результате можно сделать выводы.
Для повышения эксплуатационных параметров деталей машин и механизмов на этапе их проектирования и изготовления следует проводить инженерию поверхности с применением различных методов и технологий.
Упрочнение поверхности с применением высокоэнергетических источников является одним из наиболее эффективных направлений. При этом повышение эксплуатационных характеристик материала существенно зависит от температурного фактора на поверхности.
В процессе восстановления геометрии изношенных поверхностей целесообразно использовать плазменную технологию, при этом более высоких показателей по износостойкости и прочности можно получить при формировании покрытий компактированной струей из материалов с дисперсией частиц на уровне наноразмеров.
Применение покрытий на основе нанопорошков открывает возможности создания композиционных материалов и покрытий с улучшенными эксплуатационными характеристиками или полностью новыми свойствами разного функционального назначения.