Исследование динамики агрегата ротационного типа
Автор: Кацай Дмитрий Алексеевич
Статья в выпуске: 2 т.14, 2014 года.
Бесплатный доступ
Приводится математическая модель малогабаритного фрезерного агрегата с двухосным подвесом инструмента ротационного типа. Агрегат предназначен для выполнения поверхностной обработки асфальто-бетонных покрытий. Агрегат обеспечивает формирование поверхности с требуемым поперечным и продольным уклоном. Ротационный тип агрегата позволяет получить высокую производительность при малых усилиях взаимодействия режущих элементов с материалом. Математическая модель агрегата представлена в виде дифференциальных уравнений в форме Коши. Исследованы структурные свойства агрегата - как объекта управления. Произведен расчет коэффициентов регулятора по состоянию модальным методом.
Ротационный фрезерный агрегат, поверхностная обработка, структурные свойства, модальный метод
Короткий адрес: https://sciup.org/147154966
IDR: 147154966
Текст научной статьи Исследование динамики агрегата ротационного типа
Разрабатываемый фрезерный агрегат предназначен для поверхностной обработки дорожных покрытий. В процессе его испытаний были выполнены измерения сил резания следующих материалов: асфальт и лед. Схема для однокомпонентного измерения тензометрическим датчиком (далее тензодатчик) консольного типа силы резания материалов агрегатом в ручном режиме работы представлена на рис. 1. В представленной схеме производится измерение вертикальной составляющей силы резания. Две другие составляющие силы резания: в поперечном и продольном направлении относительно перемещения агрегата измерялись при других расположениях тензодатчика, получаемых путем разворота на 90 градусов.
Рис. 1. Схема измерения вертикальной составляющей силы резания в ручном режиме работы агрегата
В ходе эксперимента оператор вручную плавно приводил в касание барабан фрезерного агрегата с обрабатываемым материалом. Практически сразу начинается разрушение материала. Выявлено, что при малом давлении барабана на обрабатываемую поверхность получаются частицы разрушенного материала малого размера. С увеличением давления на материал увеличивается вертикальная составляющая усилия N в и размеры частиц.
Результаты проведенных экспериментальных исследований процесса ротационного фрезерования в ручном режиме работы мобильного агрегата близки к результатам, полученным в лабораторных условиях на стационарном фрезерном станке [1]. Принципиальное отличие рассматриваемой схемы ротационного фрезерования в кинематической схеме и типе режущих элементов. На рис. 2 показан вариант агрегата с осью вращения водила (барабана), расположенной параллельно обрабатываемой поверхности. В статье [1] ось вращения водила расположена перпендикулярно обрабатываемой поверхности и на водиле установлены режущие элементы чашечного типа.
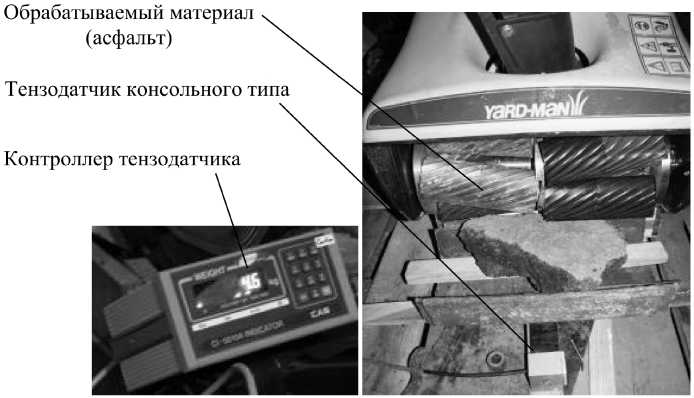
Рис. 2. Фото стенда для измерения вертикальной составляющей силы резания в ручном режиме работы агрегата
На основе фрезерного агрегата с ручным управлением разрабатывается механизированный агрегат с контуром управления положением фрезерного барабана относительно плоскости горизонта и подачи в направлении движения.
1. Постановка задачи
На рис. 3 показана кинематическая схема фрезерного агрегата, содержащего дополнительно введенную раму 1, образующую с платформой 2 карданов подвес для фрезерного барабана (ФБ) 3. Задача проводимого исследования состоит в анализе структурных свойств агрегата и синтезе обратной связи, обеспечивающей требуемые динамические свойства в процессе поверхностной обработки. Угловое положение ФБ контролируется датчиками углов ДУ 2 и ДУ 3 , а поступательное перемещение с помощью датчика угла ДУ 4 в предположении о качении опорного колеса агрегата без проскальзывания. На рис. 4 представлены системы координат, связанные с деталями агрегата, и реакции в опорах барабана ( R bl , R br ) и фрез ( R fl , R fr ), контактирующих с материалом.
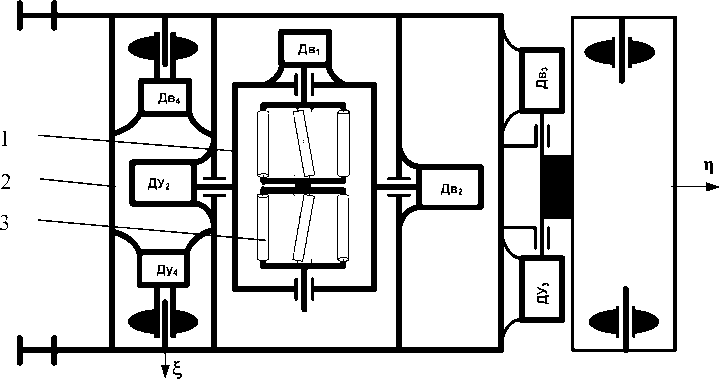
Рис. 3. Кинематическая схема агрегата
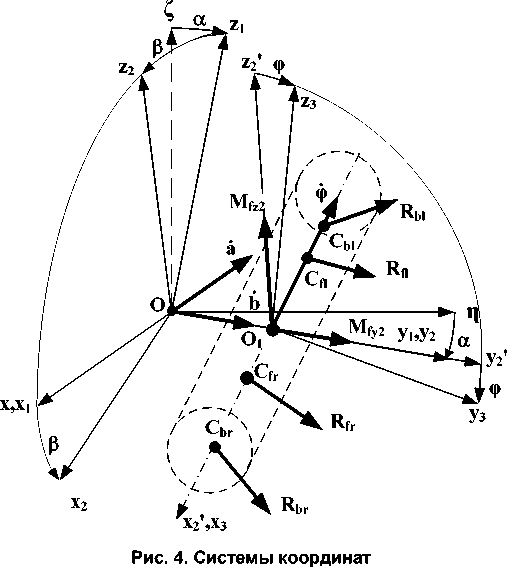
Математическая модель агрегата представлена в форме системы из дифференциальных уравнений второго порядка:
m пп-ii=Fn( t)-Rпn( t, ф, ф) ;
Jрп -a = Mдвз(t) + M(P)-Mo (ф,R,t);(2)
Jпп-в = Mдв2 (t)— mр(ф, R, t),(3)
где m пп – суммарная масса платформы и всех установленных на ней деталей и узлов, включая массу опорного узла агрегата; р - координата поступательного перемещения платформы; F n ( t ) - движущая сила, прикладываемая к платформе через двигатель Дв 4 ; R п п( t , ф , ф ) - реакция связей агрегата с обрабатываемой поверхностью, передаваемая через узлы агрегата, выражения для которой можно представить в виде стохастической функции; M ( P ) - момент от силы тяжести платформы с ФБ относительно оси вращения рамы; M a ( ф , R , t ) и M ^ ( ф , R , t ) - моменты от взаимодействия режущих элементов фрез с обрабатываемым материалом, выражения для которых можно представить в виде стохастической функции [2] R ( t , р ) = ( R 0 ( р ) + ^ ( t )- о (^ ( р ) ) ) - Rw ( t ) , где R 0 ( р ) - реакция связи режущего элемента фрезы с обрабатываемым материалом, которая при малой подаче фрезы может быть представлена линейной функцией R 0 ( р ) = b -р + с , b , с - коэффициенты, зависящие от свойств обрабатываемого материала; Rw ( t ) = {1, для t < t 1 и 0 для t 1 < t < T} - периодическая функция, модулирующая случайный процесс £ ( t ) , обусловленная вращением ФБ, несущего на себе п фрез-сателлитов; t 1 = у- п /ф , у - угловой размер фрезы-сателлита, Т = 2 л/ф - период одного оборота барабана, £ ( t ) -нормированный случайный процесс с нормальным законом распределения; дисперсия D ( A R ( х ) ) моделируемой реакции R ( t , х ) является функцией от подачи ФБ, задаваемой поступательным движением платформы в плоскости дорожного полотна: c ( A R ( х ) ) 2 = D ( A R ( х ) ) = ( kD - R 0 ( х ) ) 2 , где kD – коэффициент, зависящий от свойств обрабатываемого материала и вида фрезы; R = R ( R bi , R br , R fi , R fr ) .
Представим математическую модель агрегата в векторно-матричной форме Коши:
Особенность построения математической модели в линейной постановке состоит в распределении коэффициентов реакций взаимодействия ротационного инструмента с обрабатываемой поверхностью на две части. В вектор возмущения w (t) вошли постоянные составляющие реакций, а через коэффициенты cар, can, cpa, cpp, cpn, cna, cnp, cnn введены линейные составляющие реакций.
Управляемость агрегата по критерию Калмана должна соответствовать выполнению следующего критерия: rank ( Q u ) = 6, где Q u = ( B A • B ... A 5 • B ) - матрица управляемости.
Подстановка матриц состояния A и управления B в матрицу управляемости Qu позволяет сделать вывод о выполнении критерия управляемости независимо от параметров агрегата. Для подтверждения вывода приведем подматрицу, полученную из первых двух компонент матрицы управляемости:
Г 1 0 0 0 0 0 ^ |
||
0 1 0 0 0 0 |
||
0 0 1 0 0 0 |
||
Q U = ( B A • B ) = |
0 0 0 1 0 0 |
- (5) |
0 0 0 0 1 0 |
||
4 0 0 0 0 0 1 ; |
Находим выражение для главного определителя: |QU| = 1. Ненулевое значение главного оп- ределителя и отсутствие в его выражении параметров агрегата подтверждает структурную управляемость агрегата. Выполнение критерия управляемости дает основание сделать вывод о реализации с помощью управления u желаемых динамических свойств фрезерного агрегата.
Прямому измерению в агрегате доступны углы отклонения а и р рамы и платформы с по- мощью датчиков углов и поступательное перемещение агрегата с помощью датчика перемещения. Перечисленной совокупности датчиков соответствует следующее уравнение наблюдения:
' 0
0 10 0 ^
0 0 10
0 0 0 1 )
- матрица наблюдения; ^ ( t ) - вектор измерительного
y = Cx + § ( t ) , где C = 0 v 0
шума Гауссова типа.
Для формирования закона управления в форме линейной комбинации переменных состояния u = P • x необходим полный вектор состояния агрегата. С помощью критерия Калмана проверим наблюдаемость агрегата с помощью матрицы наблюдаемости:
Q c = f C T A T • C T ( A T ) 5 • C T j .
Анализ главных определителей, получаемых из матрицы наблюдаемости, позволил выбрать один, имеющий следующее численное значение:
= 1. (6)
Один из главных определителей матрицы наблюдаемости отличен от нуля, следовательно, rank ( Q c ) = 6 . Как и в случае с управляемостью ранг матрицы наблюдаемости не зависит от параметров агрегата, а определяется структурой его математической модели. Следовательно, можно в реальном времени восстанавливать недостающие компоненты вектора состояния агрегата и формировать управление фрезерным барабаном.
2. Синтез обратной связи
Для формирования вектора управления u необходимо ввести регулятор размерности 3 x 6: f Р 11 - Р 16 j
P =
V p 31 — p 36 J
Синтез коэффициентов регулятора выполним модальным методом. С этой целью запишем характеристическое уравнение агрегата, охваченного обратной связью:
| k • E - ( A - B • P )| = 0, (8)
где Е – единичная матрица шестого порядка.
Обозначим через V (P) вектор коэффициентов характеристического уравнения. Выражения для компонентов вектора содержат 18 неизвестных коэффициентов регулятора pij, где i = 3, j = 6 . Для нахождения численных значений коэффициентов регулятора сформируем желаемые численные значения коэффициентов характеристического уравнения. С этой целью представим передаточную функцию агрегата в виде произведения трех динамических звеньев второго порядка с различными постоянными времени Ti . Коэффициенты относительного демпфирования выберем одинаковыми со значением ^ ~ 0,7, при котором переходный процесс в агрегате будет происходить по апериодическому закону без перерегулирования. Такое требование к коэффициенту демпфирования обусловлено ожидаемым качеством результата фрезерования: исключить появление нежелательных углублений на обрабатываемой поверхности.
Обозначим через Vλ g вектор коэффициентов характеристического уравнения с желаемыми корнями. На основании вышеизложенного критерия назначения параметров динамических звеньев получим следующее выражение для формирования характеристического полинома с желаемыми коэффициентами:
f j mg W = A2 + A + 72- (9)
i = 1 V T i T i J
После раскрытия скобок и суммирования коэффициентов при различных степенях λ получим выражения для всех компонент вектора Vλ g .
Для нахождения коэффициентов регулятора приравняем сформированные вектора коэффициентов характеристического уравнения
Vx ( P ) = Vx g - (10)
Для решения системы алгебраических уравнений в программе Mathcad можно воспользоваться одной из стандартных процедур find или Minerr. В систему из шести алгебраических уравнений входит 18 коэффициентов регулятора. Избыточность количества параметров регулятора можно использовать для дальнейшего улучшения свойств динамической системы. С этой целью можно сформировать дополнительные ограничения в виде равенств или неравенств, используя, например, числители передаточных функций системы. В случае возникновения проблемы в решении можно обратиться к поиску стартовой точки путем аналитического конструирования регулятора с применением матричного уравнения Риккати с матричной переменной. Решение уравнения Риккати позволяет получить регулятор, обеспечивающий устойчивость замкнутой системы. Получающиеся при этом численные значения корней могут оказаться неоптимальными по требованиям быстродействия или перерегулирования и настраиваются на следующем шаге модальным методом.
В качестве численного примера выберем следующие частоты собственных колебаний агрегата: f 1 = 3 Гц, f 2 = 10 Гц, f 3 = 18 Гц, которым будут соответствовать постоянные времени: T 1 = 0,053 с, T 2 = 0,016 с, T 3 = 0,009 с.
Пусть матрица состояния А имеет следующие численные значения: l ′ = 1; c αβ = c αη = c βα = = c ββ = c βη = 0; c ηα = c ηβ = c ηη = - 1 . Зададим начальные значения всех коэффициентов регулятора нулевыми p ij = 0 , где i = 3, j = 6 . После обращения к процедуре Minerr в программе Mathcad получим значения коэффициентов регулятора (см. таблицу).
Численные значения коэффициентов регулятора
P |
91,20 |
26,65 |
208,93 |
1170,23 |
–1573,16 |
–19014,58 |
–246,91 |
–146,76 |
–2161,64 |
–1404,78 |
936,51 |
–16311,23 |
|
15,31 |
27,86 |
328,25 |
264,05 |
222,27 |
3420,57 |
Подстановка коэффициентов регулятора в выражение для характеристического уравнения замкнутой системы дает следующие значения корней:
λ 1,2 = - 79,168 ± 80, 768 i ; λ 3,4 =- 43,982 ± 44,871 i ; λ 5,6 = - 13,195 ± 13,461 i .
Округление коэффициентов регулятора до целых значений с помощью функции ceil в программе Mathcad приводит к изменениям в значениях корней на величины не более 4 %, что свидетельствует о низкой чувствительности динамических свойств агрегата к изменению коэффициентов не только регулятора, но и параметров его матрицы состояния.
Реализация обратной связи в агрегате потребует восстановления всего вектора его состояния. Поскольку на агрегат поступает случайное возмущение от взаимодействия ротационного инструмента с обрабатываемым материалом, сопровождающееся измерительным шумом, то целесообразно в качестве наблюдающего устройства использовать фильтр Калмана.
Выводы
Проверка структурных свойств агрегата показывает, что на его основе можно построить дорожную фрезерную машину с требуемыми динамическими характеристиками. В качестве управляющего устройства целесообразно использовать регулятор по состоянию, коэффициенты которого можно настраивать модальным методом.
Список литературы Исследование динамики агрегата ротационного типа
- Кацай, Д.А. Ротационное фрезерование асфальта. Процессы и оборудование металлургического производства: межрегион. сб. науч. тр./Д.А. Кацай, П.Г. Мазеин, С.Д. Сметанин; под ред. С.И. Платова. -Магнитогорск: ГОУ ВПО «МГТУ», 2009. -Вып. № 8. -С. 61-66.
- Кацай, Д.А. Математическая модель автоматизированной системы управления мобильным агрегатом повышенной энергоэффективности/Д.А. Кацай//Труды научно-практической конференции «Актуальные проблемы автоматизации и управления». -Челябинск: Издат. центр ЮУрГУ, 2013. -С. 35-39.