Исследование фреттингостойкости прецизионных пар трения горных машин с использованием метода вибротриботестера
Автор: Трубицин Сергей Валентинович, Островский Михаил Сергеевич
Журнал: Горные науки и технологии @gornye-nauki-tekhnologii
Статья в выпуске: 3, 2010 года.
Бесплатный доступ
Изложены требования, предъявляемые к прецизионным парам трения, описан новый экспериментальный метод оценки и исследования защитных свойств поверхностного слоя деталей гидравлики с точки зрения фреттинг- процессов. Приведенная в докладе установка позволяет увеличить количество экспериментальных данных, что положительно скажется на разработке и уточнении модели фреттинг-коррозии, оценке ресурса прецизионных пар трения. The requirements, presented to the precision friction pairs, are presented, the new experimental method of estimation and study of the shielding properties of the surface layer of the components of hydraulics from the point of view of fretting- processes is described. The installation given in the report makes it possible to increase a quantity of experimental data, which positively will affect development and refinement of the model of fretting corrosion, estimation of the resource of precision friction pairs.
Гидропривод, прецизионные пары, золотниковые устройства, надежность, фреттинг hydrodrive
Короткий адрес: https://sciup.org/140215110
IDR: 140215110
Текст научной статьи Исследование фреттингостойкости прецизионных пар трения горных машин с использованием метода вибротриботестера
Современные экскаваторы и механизированные крепи, применяемые в горной отрасли, отличает высокая степень гидрофикации. Надежность гидравлических систем в значительной степени зависит от безотказной работы прецизионных пар трения, выполняющих функции чувствительных и вытеснительных элементов насосов, распределительных элементов следящих гидроприводов и других ответственных узлов.
Среди них наиболее широко распространенны золотниковые пары, представляющие собой чувствительные и регулировочные элементы, автоматически изменяющие или ограничивающие по заданной программе давление, его перепад в смежных областях или расход жидкости.
Детали прецизионных пар являются самыми сложными и дорогостоящими в производстве среди других деталей гидравлических агрегатов. Они обычно выполняются по 6 квалитету точности, с шероховатостью не выше Ra 0,16. Величина диаметрального зазора в зависимости от размера и назначения прецизионной пары может быть от 2-3 мкм до нескольких десятков. Детали прецизионных пар могут иметь различные типы перемещения, действующие на них усилия и условия работы. Они могут иметь конструктивные отличия и изготавливаться из различных материалов.
Однако, все прецизионные пары имеют общий признак, позволяющий объединить их в самостоятельный тип подвижных сопряжений машин с характерными для него видами и причинами отказов и неисправностей.
Основным конструктивно-функциональным признаком прецизионных пар является подвижное сопряжение двух деталей с зазором порядка 0,01 мм, обеспечивающие бесконтактное уплотнение, выполняющее функции чувствительного, регулирующего, распределительного или вытеснительного элемента в гидравлических и топливных агрегатах.
Принципиально, работающая золотниковая пара идентична колебательной системе пружинного маятника: обладающее массой тело совершает колебательные движения и подвергается воздействию упругой силы. В таких условиях в точках подвижного контакта происходит непрерывное разрушение поверхностного слоя деталей. Этот процесс является основной причиной отказов прецизионных пар, и получил название фреттинг-коррозии.
Разрушение поверхностного слоя золотниковых пар трения приводит к увеличению утечек, снижая объемный коэффициент полезного действия гидроагрегата. Дефекты поверхностного слоя, получаемые в результате фреттинга, вызывают увеличение трения между золотником и гильзой, снижая чувствительность и увеличивая статическую ошибку управляющей аппаратуры.
В данный момент наиболее распространенным методом защиты поверхностного слоя является химико-термическая обработка. Ее основными недостатками являются: высокая энергоемкость, большая длительность и коробление геометрической формы детали, вызываемое ее нагревом и охлаждением.
Сегодняшний этап научно-технического развития позволяет применять современные методы поверхностного упрочнения лишенные этих недостатков:
-
- лазерное, электронно-лучевое, плазменное и детонационное упрочнение;
-
- вакуумное ионно-плазменное упрочнение, ионное магнетронное распыление, ионное легирование;
-
- магнитное упрочнение;
-
- упрочнение наплавкой;
-
- нанесение защитных покрытий.
Проведенные практические испытания прецизионных пар трения, применяемых в авиации показали, что вакуумное ионно-плазменное нанесение покрытия TiN обеспечивает высокую микротвердость поверхности (1800-2500 кгс/мм2), низкую склонность к схватыванию и пониженный (в 2-3 раза) коэффициент трения по сравнению с металлическими парами. Эти характеристики обеспечивают повышение эрозионной стойкости поверхности детали до 50% при абразивном изнашивании. Покрытия нитрида титана имеют пониженный электрохимический потенциал, что уменьшает коррозионные явления.
Основной проблемой экспериментов такого рода является моделирование процессов фреттинга элементов пары трения с образцом из стали 45. Для более точной оценки долговечности возникает необходимость для экспериментального исследования реального контакта поверхностей в условиях фреттинг-взаимодействия.
Для экспериментального моделирования такого взаимодействия предлагается установка «Вибротриботестер».
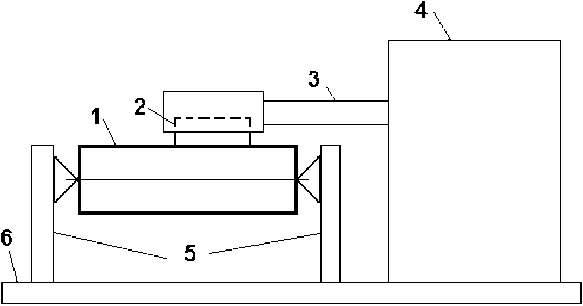
Рис. 1. Схема установка «Вибротриботестер» (1 - исследуемый образец; 2 – контробразец; 3 - штанга для крепления контробразца; 4 – вибростол; 5 - крепления образца; 6 – основание установки).
Колебания вибростола вызывают локальные повторяющиеся перемещения исследуемых поверхностей и приводят к появлению процесса фреттинг-коррозии и разрушению поверхностного слоя. Для испытаний в жидких смазочных материалах, возможна установка камеры, заполняемой рабочей жидкостью. Согласно действующему ГОСТ 23211-80 аналитический анализ результатов эксперимента начинается с исследования профиля исходной и отработанной поверхности. При этом строятся их профилограммы и проводятся средние линии профиля. Далее находится расстояние между ними h i .
Вычисляем средний износ j-го образца hj ,мкм, по формуле n hi
hj
р где р – число исследуемых пар, hi – расстояние между средними линиями исходного и отработанного профиля.
Данная установка позволяет проводить испытания пар трения с любым типом покрытий и термообработкой поверхности. Использование данной установки позволит проводить натурные эксперименты и расширить исследовательскую базу новыми данными. Это позволит уточнить модель процесса фреттинга, более точно прогнозировать ресурс прецизионных пар трения, выявить и применять более эффективные методы защиты поверхностного слоя деталей и в итоге увеличить надежность горных машин.
Список литературы Исследование фреттингостойкости прецизионных пар трения горных машин с использованием метода вибротриботестера
- Диагностика авиационных топливных гидравлических агрегатов./Лозовский В.Н. -М.: Транспорт, 1979. -295 c.
- Инженерия поверхности детали./Ред. Суслов А.Г. -М.: Машиностроение, 2008. -684 с.
- Методы упрочнения поверхностей деталей машин./Ред. Москвитин Г.В. -М.: Красанд, 2008. -400 с.