Исследование гидравлического контура управления адаптивного гидропривода подачи инструмента мобильной буровой машины
Автор: Сидоренко В.С., Грищенко В.И., Ракуленко С.В., Полешкин М.С., Дымочкин Д.Д.
Журнал: Вестник Донского государственного технического университета @vestnik-donstu
Рубрика: Машиностроение и машиноведение
Статья в выпуске: 1 т.19, 2019 года.
Бесплатный доступ
Введение. Статья посвящена исследованию адаптивного гидропривода подачи инструмента мобильной буровой машины на примере установки УРБ-2,5. Рассмотрен типовой технологический цикл мобильной буровой машины, определены критерии функционирования. По результатам анализа предложено оригинальное схемотехническое решение адаптивного гидропривода. Адаптации гидропривода подачи инструмента осуществляется при помощи регулируемого объемного гидродвигателя с контуром гидравлического управления при изменяющейся нагрузке на инструменте в процессе бурения.Материалы и методы. Предварительным вычислительным экспериментом в программе Matlab Simulink определены параметры устройств контура управления: гидромеханического датчика и гидроуправлямого клапана, на основе которых реализована экспериментальная установка. Выполненный многофакторный эксперимент позволил идентифицировать процессы в оригинальном гидравлическом контуре управления гидромотором при различных режимах нагружения инструмента.Результаты исследования...
Адаптивный гидропривод, мобильная буровая установка, технологический цикл бурения, контур гидравлического управления, гидромеханический датчик, кинематические и силовые характеристики
Короткий адрес: https://sciup.org/142219822
IDR: 142219822 | DOI: 10.23947/1992-5980-2019-19-1-13-23
Текст научной статьи Исследование гидравлического контура управления адаптивного гидропривода подачи инструмента мобильной буровой машины
Введение. Статья посвящена исследованию адаптивного гидропривода подачи инструмента мобильной буровой машины на примере установки УРБ-2,5. Рассмотрен типовой технологический цикл мобильной буровой машины, определены критерии функционирования. По результатам анализа предложено оригинальное схемотехническое решение адаптивного гидропривода. Адаптации гидропривода подачи инструмента осуществляется при помощи регулируемого объемного гидродвигателя с контуром гидравлического управления при изменяющейся нагрузке на инструменте в процессе бурения.
Материалы и методы. Предварительным вычислительным экспериментом в программе Matlab Simulink определены параметры устройств контура управления:
гидромеханического датчика и гидроуправлямого клапана, на основе которых реализована экспериментальная установка. Выполненный многофакторный эксперимент позволил идентифицировать процессы в оригинальном гидравлическом контуре управления гидромотором при различных режимах нагружения инструмента.
Результаты исследования. Получены и определены кинематические и силовые характеристики гидромеханической системы мобильной буровой установки, влияние гидравлического управления на параметры настройки устройств контура. Результаты позволили определить рациональные диапазоны функционирования гидромеханической системы для типового рабочего цикла. Обсуждение и заключения. Полученные результаты могут быть использованы при создании гидросистем новых буровых машин с различными характеристиками. Использование разработанных методик исследования и обработки их результатов позволит сократить затраты времени и средств при проектировании адаптивных гидросистем мобильных технологических машин, создании опытных образцов и проведении пуско-наладочных работ.
Introduction. An adaptive hydraulic drive of the tool advance in a mobile drilling machine is studied on the example of the URB-2.5 installation. A typical technological cycle of the mobile drilling machine is considered; the performance criteria are defined. An original design of the adaptive hydraulic drive is proposed on the basis of the analysis. Adaptation of the hydraulic drive of the tool advance is carried out using an adjustable volumetric hydraulic motor with a hydraulic control circuit under discontinuous loads on the tool during the drilling process.
Materials and Methods . Through a preliminary computational experiment in the Matlab Simulink program, the following parameters of the control loop devices were determined: a hydromechanical sensor and a hydraulically controlled valve, on the basis of which the experimental setup was implemented. The performed multifactor experiment allowed identifying the processes in the original hydraulic control circuit of the hydraulic motor under various modes of tool loading.
Research Results. The kinematic and power characteristics of the hydromechanical system of a mobile drilling rig, the hydraulic control effect on the settings of the hydraulic control circuit devices were obtained and determined. The results enabled to specify the rational ranges of the hydromechanical system operation for a typical work cycle. Discussion and Conclusions. The results obtained can be used to create hydraulic systems of new drilling machines with various characteristics. The application of the developed techniques of research and processing of their results will reduce the time and costs involved in designing adaptive hydraulic systems for mobile technological machines, creating prototypes and conducting commissioning procedures.
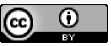
Машиностроение и машиноведение
∗ Работа выполнена в рамках инициативной НИР.
Образец для цитирования. Сидоренко, В. С. For citation: V.S. Sidorenko, et al. Study on oil pilot circuit Исследование гидравлического контура управления of adaptive hydraulic drive of tool advance in mobile drilling адаптивного гидропривода подачи инструмента machine. Vestnik of DSTU, 2019, vol. 19, no. 1, pp. 13–23.
мобильной буровой машины / В. С. Сидоренко [и др.] //
Вестник Донского гос. техн. ун-та. — 2019. — Т.19, №1.
Введение. Динамичное освоение природных ресурсов требует совершенствования действующих и создание новых автоматизированных комплексов технологического оборудования бурового производства с улучшенными механическими и энергетическими характеристиками. Анализ известных схемотехнических решений гидромеханических систем (ГМС) мобильных буровых машин (МБМ) выявил основную характерную особенность их построения — многодвигательная система, в которой важно учитывать влияние привода подачи инструмента и привода главного движения при технологическом цикле [1–4]. При этом качество, производительность и безопасность работы напрямую зависит от того, как согласуются кинематические и силовые параметры (V, M и др.) в процессе изменения нагрузок на инструменте [4, 5]. В связи с вышеизложенным, целью работы являлось повышение эффективности гидромеханической системы рабочих движений МБМ путем разработки и исследования ее контура гидравлического управления.
Критерии функционирования. В процессе бурения важным критерием является выполнение основного требования технологии — согласование работы привода главного движения и подачи, обеспечивая стабильную подачу на оборот инструмента [6].
Используя основные законы подобия различных технологических циклов, нетрудно применить приведенные рассуждения и к технологии бурения различных скважин [7, 8].
Производительность П О определяется:
ПО = 1/ТОЦ
ПСЦ = ПО ·kц kц = LСК / LОЦ
ТОЦ = ТМАШ + ТВС + ТПЗ + ТОБСЛ + ТРЕМ.(3)
ТМАШ = LОЦ / Vn; Vn = So·nИ nИ = 1000· VБУР / 3,14·DИ.(5)
Т ОЦ — время опорного цикла; Т ПЗ — время наладки следующего опорного рабочего цикла (наращивание длины инструмента); Т МАШ — машинное время, затрачиваемое на операцию резания (бурения) при перемещении инструмента на величину L ОЦ со скоростью V n ;
При выполнении условия S 0 = const, стойкость инструмента соответствует нормативной Т Н = [ТИН] при диаметре DИ и частоте вращения nИ инструмента. В этом случае сокращается количество смен инструмента на всей глубине бурения LСК = LО Ц · kц.
ТВС — время, затрачиваемое на установочные, наладочные операции, смену инструмента. Регламентируется типом оборудования [7];
Т ОБСЛ — время смены (замены) инструмента плановый после выработки его технологической стойкости Т Н ;
Т РЕМ — время на устранение отказов, при повышенной надежности сокращается; V БУР , S o — нормативы бурения грунтов различных категорий по σ i или из практики буровых работ в каждом регионе [5].
Долговечность инструмента и производительность напрямую зависят от стабильности величины S о (t) (рабочая технологическая подача на оборот) [7, 9]. Это достигается, если при уменьшении частоты вращения инструмента n(t), синхронно уменьшается скорость минутной подачи Sм(t), осуществляемой приводом зависимой подачи МБМ. В случае, если не учитываются упругие деформации в кинематической цепи подачи инструмента, величина подачи определяется:
^(О^ (6)
■ = ?
oU
Возможности жесткой стабилизации каждого из рабочих движений в условиях применения гидропривода, как известно, ограничены. В технологических машинах такого типа задача адаптации объемного гидропривода не решается в автоматическом режиме, а производится вручную оператором [3, 10].
Схемотехническое решение. На основе ранее предложенной структурной схемы [11], а также анализа типовых циклов работы МБМ, предлагается принципиальная комбинированная схема МБМ УРБ-2,5 (рис. 1), учитывающая особенности поведения и состав ее механической подсистемы.
Энергосиловая система машины состоит из гидравлических нерегулируемых аксиальнопоршневых насосов Н1, Н4, установленных на раздаточную коробку шасси через коробки отбора мощности (КОМ). Управление КОМ электропневматическое, осуществляется переключателями, установленными в кабине автошасси [10, 12].
Контур гидравлического управления (КГУ) установки получает гидравлическую энергию от тандем-насоса Н2, приводимого во вращение электродвигателем. Электродвигатель получает энергию от генератора автошасси. Первая секция Н2 направляет гидравлическую энергию к датчику ГМД1, вторая — к гидроуправляемому клапану (ГУК).
Машиностроение и машиноведение
Работа обоих контуров КГУ происходит без нагрузки, поэтому перегрев электродвигателя тандем-насоса Н2 исключен. Каждый насос тандема имеет предохранительно-переливной клапан с электрическим управлением КП2, КП3. Давление контролируется соответственно по манометрам МН3 и МН5. КГУ имеет собственный закрытый гидравлический бак Б2 [13]. Основным гидравлическим баком является бак Б1, оснащенный сливными фильтрами Ф1, Ф2, Ф3, теплообменными аппаратами ТО1 и ТО2.
Гидравлическая система (ГС) МБМ разделена на два больших контура. Во вспомогательный контур входит привод аутригеров (ГЦ1, ГЦ2), привод подъема-опускания мачты (ГЦ3), привод лебедки (ГМ3). В основной контур входит привод главного движения инструмента (роторный стол) и привод подачи (рис. 1).
Привод аутригеров п Привод подъема мачты Привод лебедки
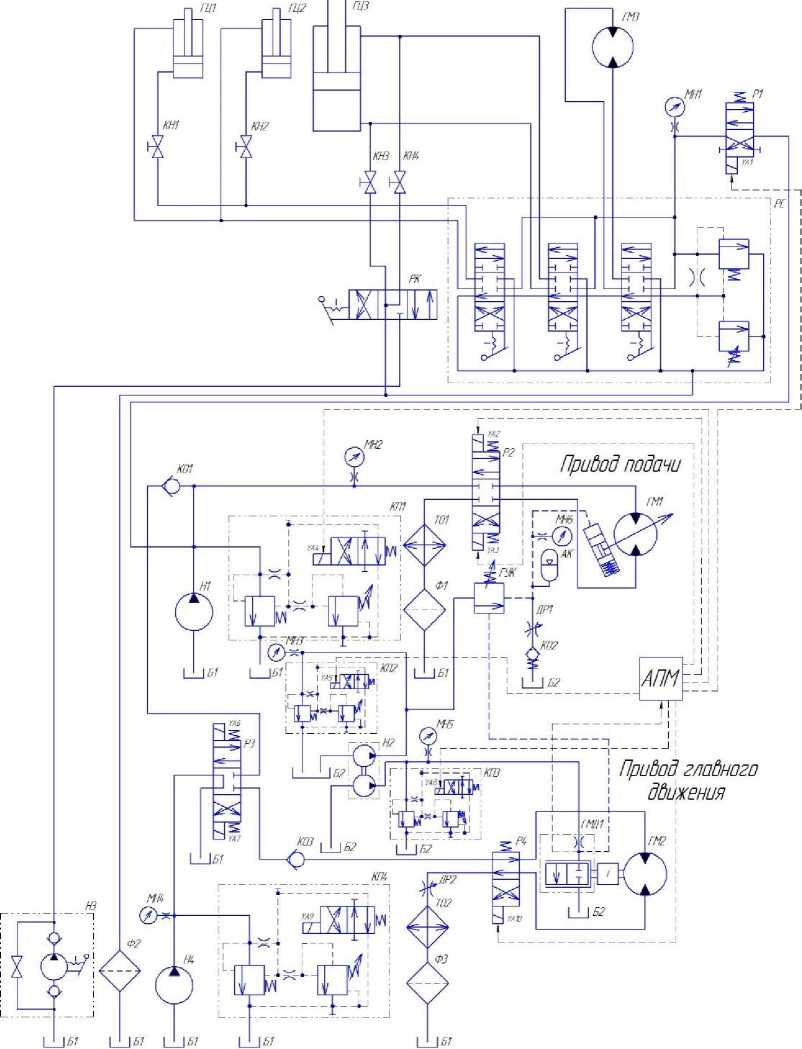
Рис. 1. Принципиальная гидравлическая схема МБМ УРБ-2,5
Входящий в основной контур привод подачи инструмента, получает гидравлическую энергию от гидронасоса Н1. Насос оснащен предохранительно-переливным клапаном КП1 с электрическим управлением. Рабочее давление контролируется по манометру МН2. Реверс движения, останов обеспечивает трехпозиционный распределитель Р2 с электрическим управлением с закрытым центром. Гидромотор ГМ1 привода подачи, регулируемый через механическую передачу, обеспечивает продольную подачу бурового инструмента. Теплообменный аппарат ТО1 и фильтр Ф1 обеспечивают фильтрацию и кондиционирование рабочей жидкости.
Насос Н4 приводится во вращение аналогично насосу Н1 (рис. 1). Распределитель Р3 обеспечивает пуск, останов привода главного движения или увеличение скорости подачи при ускоренных перемещениях работы привода подачи. В этом случае включается верхняя позиция распределителя и поток насоса Н4 через обратный клапан КО1 поступает в контур подачи привода, суммируется с потоком насоса Н1, обеспечивая быстрый спуск или подъем инструмента из скважины. При работе насоса Н4 на привод главного движения (Р3
в нижней позиции) обратный клапан КО1 препятствует сливу рабочей жидкости из контура подачи в бак Б1 [13].
Аналогичную функцию выполняет обратный клапан КО3 при работе насоса на привод подачи. Распределитель Р4 обеспечивает реверс привода главного движения. С помощью дросселя ДР2 настраивается скорость вращения инструмента (на холостом ходу).
Теплообменный аппарат ТО2 и сливной фильтр Ф3 обеспечивают фильтрацию и кондиционирование рабочей жидкости контура привода вращения.
Контур КГУ включает два оригинальных устройства — гидроуправляемый клапан ГУК (4) и гидравлический многопараметрический датчик ГМД (5) (рис. 2) [14]. При ускоренных перемещениях привода подачи, описанных ранее, насос Н2 (рис. 1) автоматически отключается системой управления (АПМ).
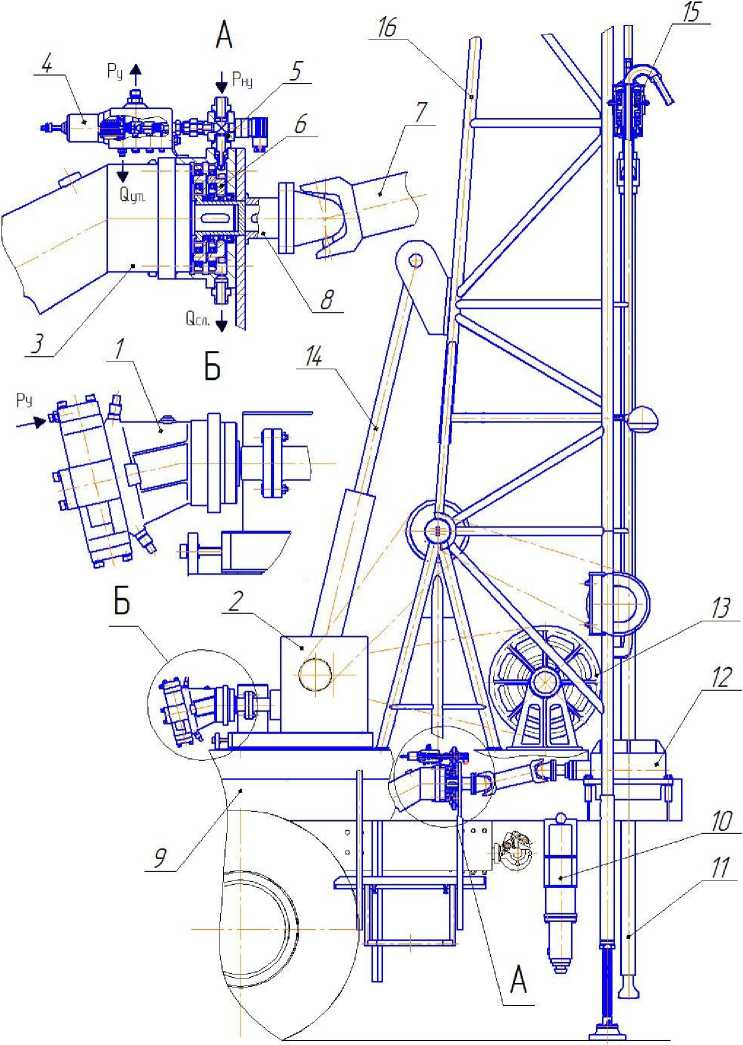
Рис. 2. Общий вид МБМ: 1 — гидромотор регулируемый; 2 — привод подачи инструмента; 3 — гидромотор нерегулируемый; 4 — клапан ГУК; 5 — датчик ГМД; 6 — редуктор; 7 — вал карданный; 8 — муфта; 9 — автошасси; 10 — система аутригеров; 11 — инструмент; 12 — привод главного движения; 13 — лебедка двухбарабанная;
14 — гидроцилиндр подъема (опускания) мачты; 15 — вертлюг; 16 - мачта
Машиностроение и машиноведение
Принцип работы КГУ (рис. 2) в составе гидросистемы МБМ заключается в следующем: вал ГМД (5) механически связан с валом ГМ2 через редуктор (6). Колебание давления на входе ГМД (5) передается на вход управления ГУК (4), который с помощью подбора пружин настраивается на такой режим работы, при котором на его выходе формируется среднедействующее давление, пропорциональное амплитуде колебаний, и, соответственно, скорости вращения вала гидромотора ГМ1.
При увеличении момента сопротивления на валу гидромотора ГМ2, скорость вращения вала и частота колебаний на входе ГМД уменьшается, а амплитуда давления увеличивается. При ее увеличении увеличивается среднее значение открытия клапана ГУК, который подает большее количество жидкости от Н2 к блоку регулятора ГМ1 привода подачи. Давление управления Ру на выходе ГУК возрастает, что обеспечивает увеличение рабочего объема гидромотора и снижает скорость движения подачи. Механизм функционирования контура КГУ в составе ГМС с зависимой подачей инструмента, а также принцип работы блока АПМ рассмотрен в работе [15].
Гидроаккумулятор АК сглаживает пульсацию давления управления Ру на входе управления гидромотора ГМ1. С помощью настройки дросселей ДР1, ДР2 и подбора клапана давления КО3 настраиваются предельные значения скоростей подачи и вращения инструмента и формируется требуемая функциональная зависимость между скоростями рабочих движений.
Оригинальный ГУК отличается функцией непрерывного регулирования сечения проточной части клапана. Следовательно, существует возможность регулирования производительности гидромотора во всем диапазоне изменения скорости.
Экспериментальное исследование. Для идентификации параметров ГМД, работающего в заданных условиях, разработано специальное стендовое оборудование и оснастка [13]. Расход гидромотора определялся при помощи турбинного датчика-расходомера, подключенного через плату преобразователь ЦАП-АЦП. Диапазоны регулирования параметров при исследовании приведены в таблице 1.
Таблица 1
Диапазоны параметров при исследовании ГМД
№ Параметр Обозначение Диапазон Ед. измерения Устройство контроля 1 Диаметр сопла dсп 0,5–1,2 мм Калибр-пробка 2 Дроссельной шайбы dдр 0,8–2 мм Калибр-пробка 3 Зазор между соплом и модулятором yз 0,2–1 мм Индикатор часового типа 4 Частота вращения nгмд 5–60 об/мин Датчик частоты вращения 5 Расход через ГМД Qгмд 0,5–20 л/мин Расходомер, мерный бак 6 Давление в ГМД pгмд 0,5–5 МПа Датчик давления 7 Характерный конструктивный параметр сечения проточной части ГМД xд 2–8 мм Штангенциркуль
Скорость перемещения и ускорение вала ГМ (привод подачи) определяли последовательным дифференцированием перемещения по времени по следующим формулам, реализуемым постобработкой данных в программе «PowerGraph» [8, 11, 16]:
“(^=^’ (9)
£(0 = ^, (10)
где w — угловая скорость ГМ, рад/с; £ — угловое ускорение ГМ, рад/с 2 .
Результаты обработки полученных экспериментальных данных по известным методикам [17, 18] представлены на рис. 3–9.
График на рис. 3 поясняет отклик по амплитуде колебаний давления ГМД при изменении скорости вращения гидромотора ГМ1 в диапазоне 45–125 рад/с. Данные получены при испытаниях сопел с диаметрами dсп=2,4,6 мм. В результате зависимость изменения давления имела практически линейный характер и падала по мере увеличения скорости, что связано с нестационарным режимом истечения рабочей жидкости через элемент сопло-заслонка.
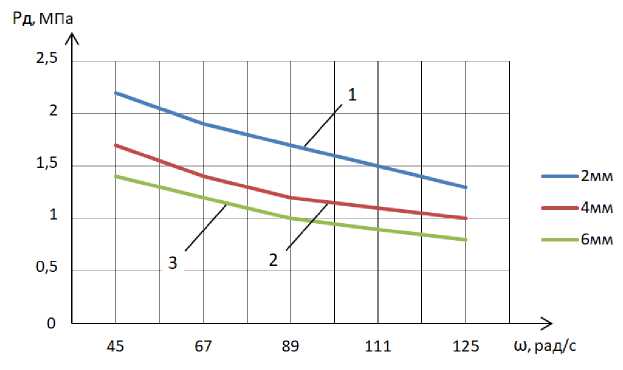
Рис. 3. Зависимость величины колебаний давления PД от скорости вращения ω гидромотора ГМ1, аппроксимации: 1 — P Д =0,14ω2-3ω+24,8; 2 — P Д =0,36ω2-3,84ω+20,4; 3 — P Д =0,21ω2-2,8ω+16,6
Результаты, представленные на рис. 4, показывают, что при увеличении характерного конструктивного параметра сечения проточной части ГМД Х Д с 2 до 8 мм, уровень давления управления изменяется с 1,9 до 1,4 МПа. Это позволяет сделать рекомендации по дальнейшей оптимизации проточной части ГМД [19]. В частности, по некоторому увеличению ХД. Однако дальнейшее ее увеличение нецелесообразно, поскольку увеличивает геометрические размеры диска модулятора.
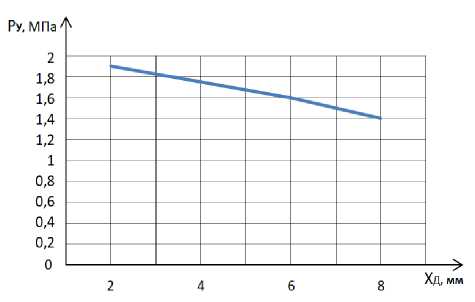
Рис. 4. Зависимость изменения давления управления Pу от влияния характерного конструктивного параметра сечения проточной части ГМД X Д , аппроксимация: PУ=1,65X Д +20,75
На рис. 5 представлено влияние конструктивных особенностей ХД на максимальную амплитуду давления Pдmax, используемую для контура гидравлического управления при подводе к ГУК.
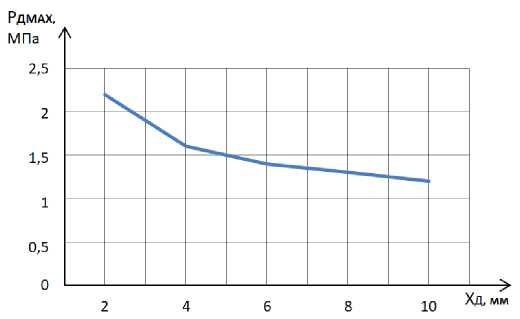
Рис. 5. Зависимость изменения максимальной амплитуды давления управления P Д . MAX от влияния характерного конструктивного параметра сечения проточной части ГМД X Д , аппроксимация: P Д MAX =21,46X Д -0,372
Машиностроение и машиноведение
При идентификации важным этапом было определение в цепи КГУ: ГМД — ГУК степень влияния параметров настройки каждого элемента управления. Так, параметром настройки ГУК, при функционировании контура управления, является жесткость его пружины Cпр, подбор которой существенно влияет на чувствительность подсистемы управления [20].
Построенная на рис. 6 характеристика, аппроксимированная по результатам эксперимента, носит линейный характер, и поясняет величину падения максимального давления управления с 1,7 до 1,4 МПа при изменении жесткости пружины ГУК.
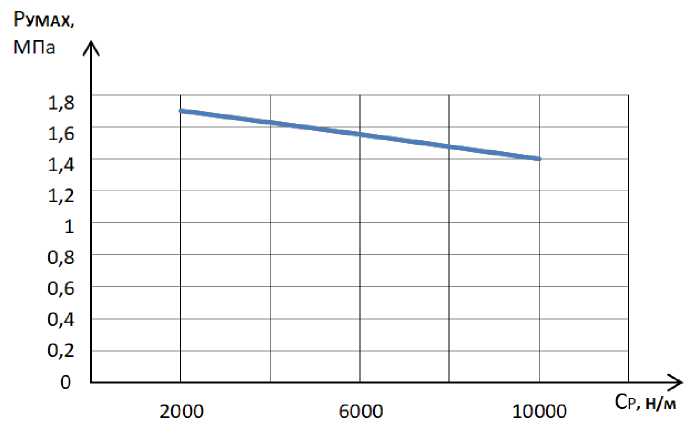
Рис. 6. Зависимость изменения максимального давления управления Pу. max от величины жесткости пружины ГУК, аппроксимация: PУMAX=1,5CP+18,5
Второй элемент настройки в контуре с ГУК — регулируемый дроссель в шунтирующей линии (рис. 1). Параметр его настройки — проходное сечение, регулировалось в диапазоне 2,5·10 -7 до 7,5·10 -7 м 2 , результаты эксперимента представлены на рис. 7.
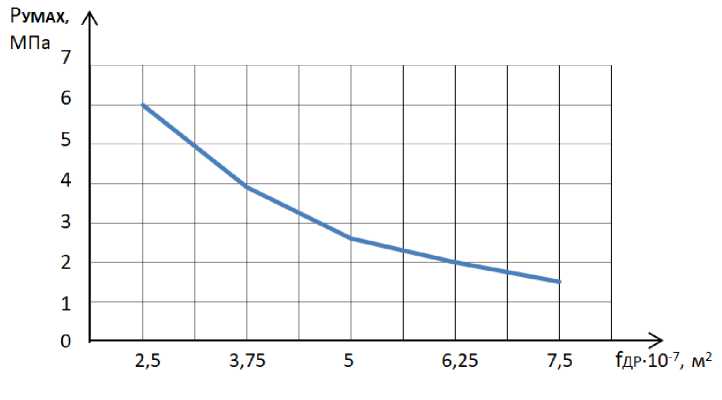
Рис. 7. Зависимость изменения максимального давления управления Pу. max от площади проходного сечения дросселя ДР1, аппроксимация: PУMAX=1,5f Д Р2-27,6·f Д Р+84,2
Исследовали четыре режима работы двигателя вращения инструмента (гидромотора ГМ1) при релейном нагружении и соответственно изменении угловой скорости ω на: 22 рад/с; 49 рад/с; 71 рад/с и 85 рад/с. Полученная по данным эксперимента зависимость представлена на рис. 8.
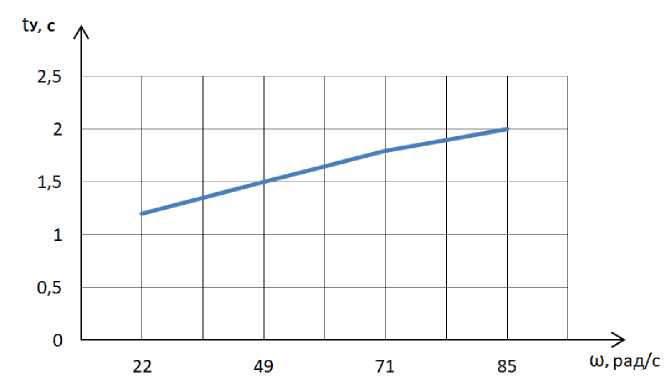
Рис. 8. Зависимость tу времени отклика КГУ от изменения угловой скорости вращения вала гидромотора ГМ1 ω, аппроксимация: t У =-0,002ω 2 -0,4ω+0,83
Поскольку КГУ входит в состав гидросистемы МБМ, его протяженность оказывает особое влияние на качество и время переходных процессов [16]. С целью определения степени влияния на вышеназванные параметры, произведены исследования времени изменения давления в линии управления при варьировании ее объема (рис. 9).
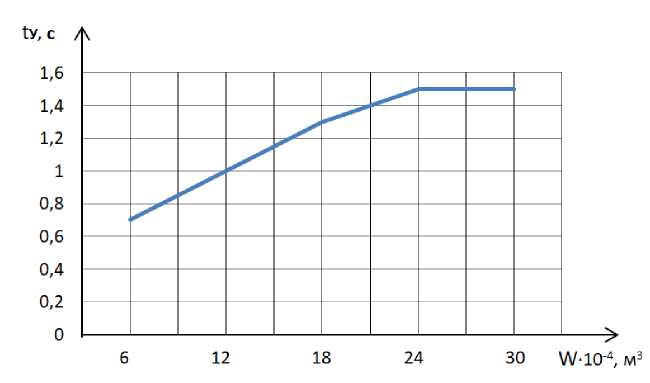
Рис. 9. Зависимость tу времени отклика КГУ от величины объема W в гидролинии управления, аппроксимация: t У =-0,02ω 3 +0,1ω 2 +0,12ω+0,5
Результаты позволяют определить критическое значение объема гидролинии W = 24·10 -4 м 3 , свыше которого время реакции КГУ не превышает 1,5 с, что обусловлено волновыми процессами, протекающими по трубопроводу, а также параметрами самих магистралей [20].
Выводы. В результате проведенных исследований были обоснованы требования и предложена обобщенная структура ГМС рабочих движений МБМ, позволившая повысить эффективность бурового производства за счет введения внутренней кинематической гидромеханической связи между главным и движением подачи инструмента.
Разработан и реализован контур гидравлического управления на основе многопараметрического датчика и гидроуправляемого клапана, обеспечивающий согласование рабочих движений при изменяющейся технологической нагрузке. Учитывая характерные особенности технологического процесса бурения, предложена конфигурация опорного рабочего цикла, позволившая разработать автоматизированную систему приводов рабочих движений.
Машиностроение и машиноведение
Список литературы Исследование гидравлического контура управления адаптивного гидропривода подачи инструмента мобильной буровой машины
- Озерский, А. И. Перспективные направления развития силового гидравлического привода/А. И. Озерский, Ю. И. Бабенков, М. Э. Шошиашвили//Известия высших учебных заведений. Сев-Кавк. регион. Техн. науки. -2008. -№6. -С. 55-61.
- Сысоев, Н. И. Обоснование структуры и рациональных режимных параметров мехатронной бурильной машины/Н. И. Сысоев, С. Г. Мирный, Д. А. Гринько//Горное оборудование и электромеханика. -2011. -№ 9. -С. 24-28.
- Муравенко, В. А. Буровые машины и механизмы. Т.1/В. А. Муравенко, А. Д. Муравенко. -Москва-Ижевск: Институт компьютерных исследований, 2002. -520 с.
- Мирный, С. Г. Обоснование и выбор рациональной частоты вращения штанги машин для сверления шпуров в породах повышенной крепости и абразивности: дис… канд. техн. наук/С. Г. Мирный. -Новочеркасск: НПИ, 2005. -142 с.
- Басарыгин Ю.М., Булатов А.И., Проселков Ю.М. Технология бурения нефтяных и газовых скважин. - М.: ООО "Недра-Бизнесцентр", 2001. - 679 с.
- Кудинов, В. А. Динамика станков/В. А. Кудинов. -Москва: Машиностроение, 1967. -359 с.
- Ящерицын, П. И. Теория резания/П. И. Ящерицын, Е. Э. Фельдштейн, М. А. Корниевич. -Москва: Новое знание, 2006. -512с.
- Ле Чунг Киен. Повышение эффективности гидропривода подачи технологического оборудования: дис…канд. техн. наук/Ле Чунг Киен. -Ростов-на-Дону, 2013. -165с.
- Гринько, Д. А. Метод расчета и поддержания рациональных режимных параметров бурильной машины мехатронного класса: дис… канд. техн. наук/Д. А. Гринько. -Новочеркасск, 2015. -158 с.
- Установка разведывательного бурения УРБ-2,5С-КАМАЗ. Руководство по эксплуатации УРБ-2,5С.00.00.000 РЭ. Ростов-на-Дону, ООО «Завод СтройНефтеМаш», 2012 г.
- Сидоренко, В. С. Адаптивный гидропривод с объемным регулированием подачи инструмента технологической машины/В. С. Сидоренко//Вестник Донского гос. техн. ун-та. -2017. -Т17, №2(89). -С. 88-99.
- Ракуленко, С. В. Адаптивный гидравлический привод подачи инструмента буровой установки/С. В. Ракуленко//Юбилейная конф. студ. и молодых ученых, посв. 85-летию ДГТУ: сб. докл. науч.-техн. конф. -Ростов-на-Дону, 2015 г. -С. 306-318.
- Сидоренко, В. С. Моделирование гидравлической системы с зависимой подачей инструмента мобильной буровой установки/В. С. Сидоренко//Гидравлические машины, гидроприводы и гидропневмоавтоматика. Современное состояние и перспективы развития -2016: сб. науч. тр. IХ междунар. науч.-техн. конф. -Санкт-Петербург: Издательство Политехнического университета, 2016. -С.365-375.
- Гидравлический датчик: патент 2538071 Рос. Федерация, МПК G01P3/32/В.С.Сидоренко, С.В. Ракуленко, Ле Чунг Киен. -№ 2013126107/28; заявл. 07.06.2013; опубл. 10.01.2015, Бюл. № 1. -8 с.
- Сидоренко, В. С. Динамика гидромеханической системы технологической машины с адаптивным приводом подачи инструмента/В. С. Сидоренко, С. В. Ракуленко, М. С. Полешкин//Вестник Самарского университета. Аэрокосмическая техника, технологии и машиностроение. -2017. -Т.16, №1. -С. 162-175.
- Попов, Д. Н. Динамика и регулирование гидро-и пневмосистем: учеб. для вузов. 2-е изд., перераб. и доп./Д. Н. Попов. -Москва: Машиностроение, 1987. -464 с.
- Мостеллер Фредерик. Анализ данных и регрессия/Фредерик Мостеллер, Джон. У Тьюки; пер. с англ. Ю. Н. Благовещенского; под ред. Ю. П. Адлера. -Москва: Финансы и статистика, 1982. -258с.
- Степнов, М. Н. Статистические методы обработки результатов механических испытаний/М. Н. Степнов. -Москва: Машиностроение, 1985. -220 с.
- Иванов, Г. М. Проектирование гидравлических систем машин/Г. М. Иванов. -Москва: Машиностроение, 1992. -224 с.
- Казмиренко, В. Ф. Электрогидравлические мехатронные модули движения. Основы теории и системное проектирование. Учебн. Пособие/В. Ф. Казмиренко. -Москва: Радио и связь, 2001. -432 с.