Исследование и моделирование процесса плазменной закалки стали 40Х
Автор: Жаткин С.С.
Журнал: Известия Самарского научного центра Российской академии наук @izvestiya-ssc
Рубрика: Машиностроение и машиноведение
Статья в выпуске: 4-2 т.25, 2023 года.
Бесплатный доступ
В работе представлены результаты экспериментальных исследований и моделирования процесса плазменного упрочнения образцов из стали 40Х. С использованием экспериментальных данных по размерам зон упрочнения в рамках теплофизического моделирования определены эффективный радиус и КПД плазменной дуги. Проведено моделирование плазменного поверхностного упрочнения в зависимости от скорости движения и тока плазменной дуги. На основе анализа предложены номограммы для определения глубины и ширины зоны упрочнения стали 40Х в зависимости от скорости и тока плазменной дуги. Построены термические циклы в зоне нагрева стали. Определены скорости охлаждения материала в зависимости от скорости движения и глубины упрочнения в сравнении с критической скоростью закалки стали.
Моделирование, плазменная обработка, скорость движения дуги, закалка, скорость охлаждения
Короткий адрес: https://sciup.org/148327530
IDR: 148327530 | DOI: 10.37313/1990-5378-2023-25-4(2)-249-257
Текст научной статьи Исследование и моделирование процесса плазменной закалки стали 40Х
Проблема продления эксплуатационного ресурса деталей и инструмента за счет поверхностного упрочнения остается актуальной, прежде всего, в ресурсосберегающем аспекте, поскольку их производство и утилизация сопровождаются потреблением сырьевых и энергетических ресурсов.
Среди известных технологий поверхностного упрочнения стальных деталей традиционными являются закалка токами высокой частоты, химико-термическая обработка, поверхностное пластическое деформирование. Вместе с тем большое внимание уделяется методам обработки концентрированными потоками энергии, поскольку при высокоскоростных температурных и силовых воздействиях формируются особые структуры с повышенными эксплуатационными характеристиками [1]. Критерием выбора рациональной технологии поверхностного упрочнения является компромисс между обеспечением высоких эксплуатационных свойств и стоимостью реализации технологии.
Процессы поверхностного упрочнения требуют применения концентрированного источника нагрева с плотностью теплового потока на поверхности материала 103-106 Вт/см2. Такими характеристиками обладают электрон-
ный и лазерный лучи, плазменная дуга, однако применение лазерного и электронного лучей сдерживается высокой стоимостью и низкой мобильностью оборудования, низкой производительностью процесса. Поэтому применение плазменной дуги, благодаря таким преимуществам как: высокий КПД нагрева, возможность регулирования погонной энергии сжатой дуги оправдано, как в экономическом, так и в технологическом плане [2].
В отличие от лазерного плазменное поверхностное упрочнение характеризуется более высокой производительностью, большими размерами упрочненной зоны (глубина – до 5 мм, ширина – до 15 мм) и более широкими оптимальными диапазонами режимов обработки, что позволяет выполнять упрочнение на значительную глубину по различным технологическим схемам – как с оплавлением, так и без оплавления поверхности.
Также отличительной особенностью метода плазменного поверхностного упрочнения является возможность получения скоростей нагрева и охлаждения материалов, на несколько порядков превышающих значения, характерные для традиционных методов упрочнения (печной закалки, закалки ТВЧ, газопламенной закалки и др.), что способствует получению упрочненных слоев с недостигаемым ранее уровнем эксплуатационных свойств.
Возможность регулирования концентрации энергии позволяет изменять как ширину и глубину обработки в широких пределах, так и управлять скоростью нагрева и охлаждения упрочняемого слоя [3 - 4]
Такие качества, как сравнительная простота и доступность оборудования, низкая стоимость, широкие технологические возможности, высокое качество обработки изделий из различных металлов позволяют плазменным технологиям на данном этапе успешно конкурировать с другими способами [5].
Образующиеся при скоростном нагреве и охлаждении структуры закалочного типа обладают высокой твердостью, износостойкостью, сопротивлением разрушению. Причем упрочнение целесообразно осуществлять как для новых деталей, так и для реставрированных, например, наплавкой и (или) механической обработкой рабочей поверхности, используя дешевые высокопроизводительные методы с низкой трудоемкостью, пригодные для применения в условиях действующего производства.
Плазменная обработка, в том числе и поверхностное упрочнение, зависит от таких факторов, как ток дуги, скорость ее движения относительно обрабатываемой заготовки, диаметр сопла, расстояние от сопла до заготовки, теплофизические характеристики материала. Однако для расчета режимов плазменной обработки на заданную глубину важно знать, в частности, радиус плазменной дуги, а также влияние скорости движения и тока плазменной дуги на размеры зон упрочнения обрабатываемых сталей. В работе исследуется влияние параметров плазменной дуги на размеры зоны упрочнения, а также моделирование процесса плазменной закалки стали 40Х.
МЕТОДИКА ИССЛЕДОВАНИЯ
Исследования проводились на образцах из стали 40Х размерами 75х75х17 мм. Плазменная поверхностная закалка была произведена на автоматической плазменной установке ARC-06В при токе плазменной дуги 80 А и диаметре сопла плазмотрона 2,4 мм. Расстояние от среза сопла до поверхности заготовки составляло 9 мм. При этом скорость движения плазменной горелки относительно обрабатываемой заготовки менялось от 150 мм/мин до 720 мм/мин. Напряжение дуги составляло 23 В.
Микротвердость измерялась на микротвердомере ПМТ-3, нагрузка на индентор составляла 200г. Измерения микротвердости проводились по сечению образца, от поверхности вглубь зоны обработки с шагом между «уколами» 0,12 мм при измерении по глубине и 0,3 мм при измерении по ширине.
Моделирование процесса плазменной закалки проводилось в пакете Mathcad 14 с использованием встроенных функций пакета.
РЕЗУЛЬТАТЫ И ИХ ОБСУЖДЕНИЕ
На рис. 1 приведены данные, полученные при измерении микротвердости по центру закаленной дорожки для стали 40Х на различных скоростях обработки. Микротвердость закаленного слоя принималась на уровне от H μ=400-460 кгс/мм2 (43-46 HRC) и выше, что соответствует критической твердости стали 40Х при количестве мартенсита 50% [6].
В верхних и средних слоях зоны обработки величина микротвердости незначительно ме-
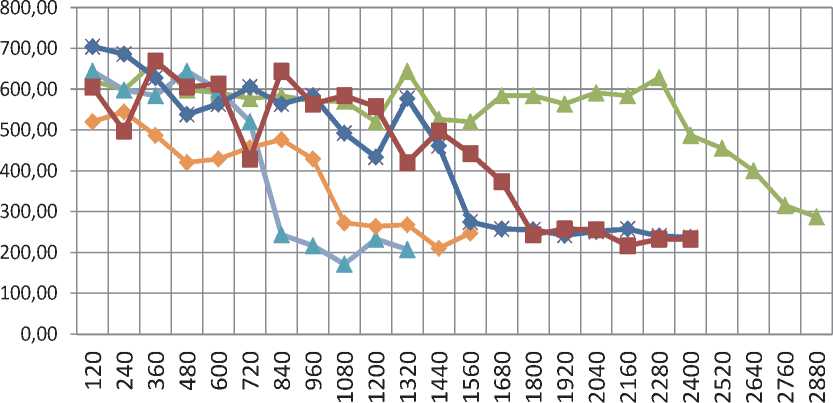
Шаг, мкм
-*-V=150 мм/мин ^ V=720 мм/мин -ф-V=540 мм/мин
^^V=420 мм/мин ^^V=300 мм/мин
Рис. 1. Распределение микротвердости по глубине зоны нагрева при различных скоростях обработки няется и находится в диапазоне 550-700 кгс/мм2 и ее падение по глубине обусловлено глубиной упрочнения, зависящей от глубины прогрева при различных скоростях движения плазменной дуги.
Распределение микротвердости по ширине зоны обработки строилось для каждой скорости движения на разной глубине прогрева – на глубине 150 мкм; 650 мкм и 1550 мкм. Например, на рис. 2 приведено распределение твердости по ширине при скорости обработки 150 мм/мин на указанных глубинах прогрева.
Из рис. 2 также хорошо видно, что на разной глубине величина микротвердости слабо меняется и составляет 550-700 кгс/мм2, что указывает на хорошую прокаливаемость стали 40Х.
Средние значения микротвердости на поверхности при различных скоростях обработки представлены ниже в таблице 1.
Влияние скорости движения плазменной дуги относительно заготовки существенно сказывается на глубине и ширине зоны закалки и связано с размерами зоны прогрева до температуры закалки.
Для примера на рис. 3 приведена макроструктура зоны обработки стали при скорости движения 720 мм/мин. Микроструктура сталей в различных зонах представлена на рис. 4.
Сталь 40Х в исходном состоянии имеет структуру пластинчатого перлита со слабо проявленной ферритной сеткой по границам зерен (рис. 6в). Зона закалки (рис. 6а) имеет выраженную структуру игольчатого мартенсита, которая переходит в мартенситотроостит, далее наблюдаются зерна перлита и ферритной сетки (рис. 6б).
По результатам металлографических исследований и измерений микротвердости были получены следующие данные по размерам зон закалки стали в зависимости от скорости движения заготовки относительно плазменной горелки (табл. 2).
В связи с трудностью контроля температур и скоростей нагрева, для выбора режимов упрочнения с использованием концентрированных потоков энергии (КПЭ) широкое распространение получило математическое моделирование температурных полей и структурно-фазовых превращений в материалах. При обработке с помощью КПЭ такой подход для определения режимов упрочнения является наиболее оптимальным, хотя результаты, представленные в литературных источниках, носят частный ха-
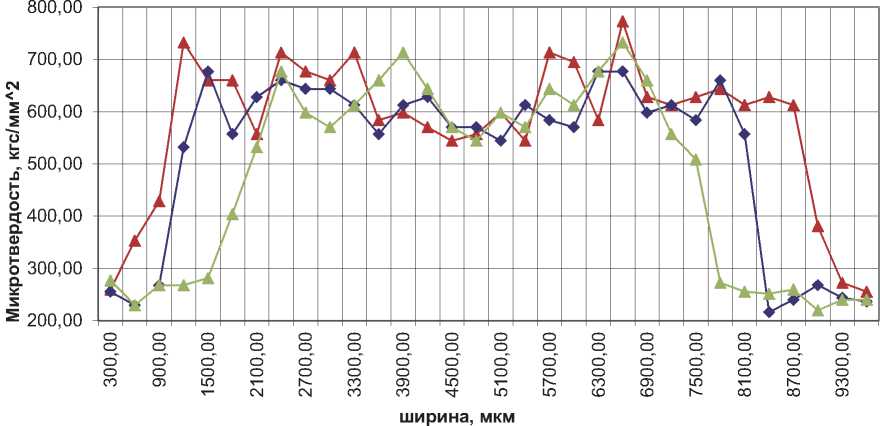
—*—150 —♦—850 —*- 1550
Рис. 2. Распределение микротвердости по ширине зоны нагрева при скорости обработки 150 мм/мин
Таблица 1. Средние значения микротвердости на поверхности зоны обработки в зависимости от скорости движения
Скорость обработки, мм/мин |
Микротвердость, кгс/мм2 |
150 |
700 |
300 |
680 |
420 |
650 |
540 |
550 |
720 |
650 |
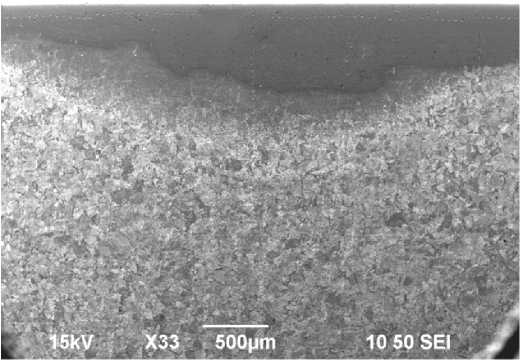
Рис. 3. Макроструктура стали 40Х после плазменной обработки: ток дуги 80 А, скорость движения 720 мм/мин
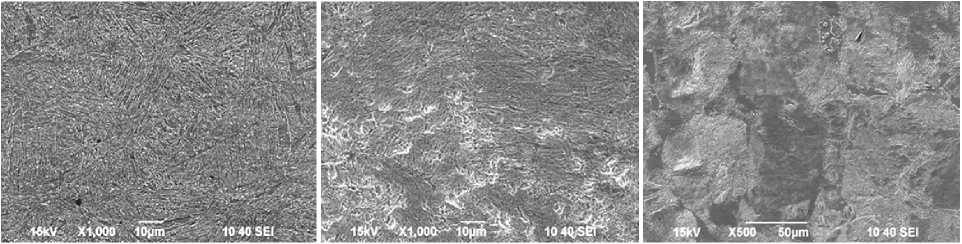
Рис. 4. Микроструктура зон плазменной обработки стали 40Х: а - зона закалки; б - переходная зона; в - исходная структура стали
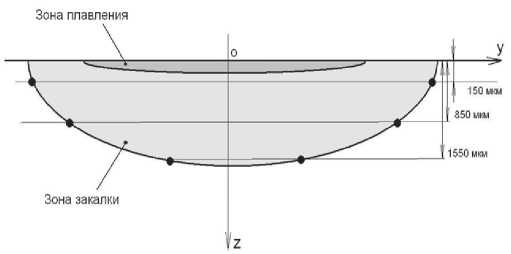
Рис. 5. К расчету эффективного радиуса и КПД плазменной дуги
Глуби
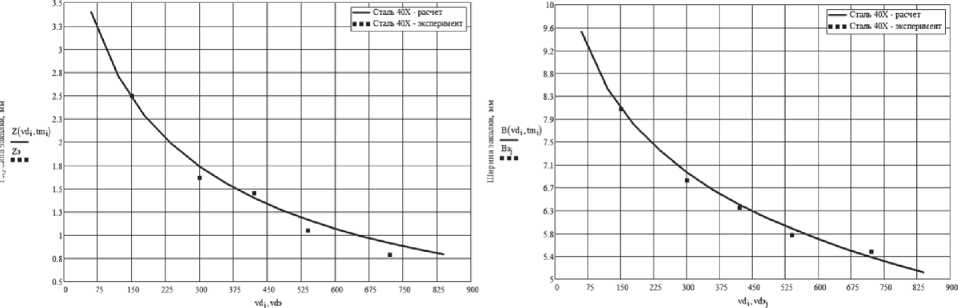
скорость движения, мм мим скорость движется, мм мин а б
Рис. 6. Зависимость глубины (а) и ширины (б) зоны закалки стали 40Х от скорости движения плазменной дуги
Таблица 2. Размеры зон закалки в зависимости от скорости движения
Скорость движения, мм/мин |
Глубина закалки, мм |
Ширина закалки, мм |
150 |
2.5 |
8.1 |
300 |
1.6 |
6,8 |
420 |
1.5 |
6,3 |
540 |
1.1 |
5,8 |
720 |
0.8 |
5,5 |
рактер и применимы для конкретных источников и обрабатываемых материалов [7]. Тем не менее, используя экспериментальные данные по поверхностной обработке (например, размеры зон, сварки, наплавки или упрочнения), можно определить параметры внешнего воздействия для последующего теоретического анализа и моделирования.
При моделировании плазменной обработки важным является правильное задание радиуса плазменной дуги, который в отличие от лазерного луча, однозначно не определяется. На радиус плазменной дуги оказывают влияние такие факторы, как ток дуги, расстояние от сопла плазмотрона до поверхности образца, тип плазмообразующего газа, напряжение дуги и диаметр выходного сопла плазмотрона. В данном случае на основе теплофизического моделирования определялся эффективный радиус и КПД плазменной дуги для данной установки.
Теплофизическое моделирование проводилось с использованием выражения для температурного поля плоского слоя [5]:
Кроме того, в отсутствии сканирования дуги относительно зоны обработки частота w и амплитуда сканирования А равны нулю. В этом случае выражение (1) упрощается и принимает вид:
Р э t B 1
T ( x , y , z , tB ) = —- ex p
4 nX H 0 t + 1 0
^
1 + 2 ■ — cos i=1
n iz
H
^^^^^^^
( x + v a« t ) 2 + У2 4 ■ a ■ ( t + 1 0 )
I 2.2 at
■ exp - n i —v
V h 2
dt + T о
T ( x , У , z , t B ) =
p 'B
1 з Г 1
—- exp
4ПШ J 0 t + 1 0
( x + va . t )2 + [ y - A ■ sin [ » • ( t B - 1 ) ]] 2 4 ■ a ■ ( t + t 0 )
E" (niz) ( _2.2 at ) 1 H n< cosl — I■ expl -n i ■ — I I q<)cos — d; dt + T, i=1 V H ) V H ) P- о H
(1) где PЭ=h×P – эффективная мощность плазменной дуги; h - эффективный КПД дуги. При этом мощность дуги определяется через ток и напряжение дуги P=IД×UД . H – толщина плоского слоя; t n - время нагрева, равное t B = 2 R зфф / v a„ ; Rэфф – эффективный радиус плазменной дуги; vдв – скорость движения заготовки; w - частота сканирования плазменной дуги относительно обрабатываемого образца; амплитуда сканирования A = D 2 ; D – размах колебаний дуги; t о = R ^ /4 ■ a ; T0 - начальная температура; q 1 (z) – функция интенсивности источника теплоты по толщине обрабатываемого материала. В большинстве задач сварки, наплавки и поверхностной термообработки плазменную дугу можно считать поверхностным нормально распределенным источником нагрева и согласно [5] для такого источника интеграл под суммой равен PЭ.
Температура плавления стали принималась равной 1760 К, а температура закалки – 1113 К (840 оС).
На основе экспериментальных данных по металлографическим данным и измерению микротвердости определялись размеры зоны плазменной закалки. Координаты зон плазменной закалки определялись по схеме, приведенной на рис. 5.
Расчет проводился в программе Mathcad 14 с использованием встроенных функций решения нелинейных уравнений. В процессе расчета выражение (2) записывалось дважды, при этом слева задавалась температура закалки, а справа – координаты выбранных точек на границе зон закалки. В результате для каждой скорости движения была составлена система двух уравнений, при решении которых для различных координат выводились значения эффективного радиуса и КПД плазменной дуги. После проведения данных расчетов были найдены средние значения эффективного радиуса и КПД плазменной дуги - Rэфф = 2,74 мм; h = 0,65. В дальнейших теплофизических расчетах использовались данные значения КПД и эффективного радиуса дуги.
Для скоростей обработки, принятых в эксперименте, построены графики зависимости глубины и ширины зоны закалки от скорости движения источника, приведенные на рисунке 6. Точками на графиках отмечены экспериментальные значения глубины и ширины зоны закалки для скоростей движения, указанных в таблице 2. Хорошо видна корреляция расчетных и экспериментальных данных, что подтверждает правильность вычисленных на основе экспериментальных данных эффективного радиуса и КПД плазменной дуги. Из рисунков видно, что
ширина зоны закалки численно изменяется слабее глубины закалки с ростом скорости движения источника.
Сводные значения экспериментальных и расчетных данных глубины и ширины зон плазменного упрочнения стали 40Х приведены в таблице 3. Хорошо видно, что при увеличении скорости обработки от 150 до 720 мм/мин глубина закалки уменьшается с 2,5 до 0,8-0,9 мм, т.е. в 2,8 - 3 раза. В процентном отношении снижение глубины закалки происходит на 64-68%. При этом ширина зоны закалки уменьшается в 1,4 -1,5 раза или на 32%.
Как отмечалось выше, на параметры плазменного упрочнения оказывают влияние различные факторы, в том числе ток дуги (рис. 7). С ростом тока дуги от 65 А до 92 А глубина и ширина зоны упрочнения увеличиваются практически линейно. При этом более выраженно изменяется глубина закалки, чем ширина. Так при скорости движения дуги 150 мм/мин в указанном диапазоне токов дуги глубина закалки изменяется на 27%, а ширина закаленной дорожки на 16%. При скорости 720 мм/мин изменение глубины составляет 36%, а ширины – 21%.
На основе анализа можно сделать вывод, что на глубину закалки оказывает существенное влияние как ток, так и скорость движения дуги, в то время как на ширину закаленной дорожки скорость движения оказывает меньшее влияние. Очевидно, что в большей степени ширина закаленной дорожки определяется диаметром сопла плазмотрона или эффективным радиусом плазменной дуги в зоне обработки.
На основе проведенного анализа в диапазоне токов плазменной дуги 65-92 А и скоростей движения 1-12 мм/с (60-720 мм/мин) для комплексной оценки совместного влияния данных параметров плазменной обработки на изменение размеров зон закалки были построены номограммы, представленные на рис. 8. Построенные номограммы зависимости глубины и ширины зон упрочнения стали 40Х от скорости движения и тока плазменной дуги позволяют определить ориентировочные режимы обработки для упрочнения на заданную глубину.
Сила тока и скорость движения дуги представляют собой два конкурирующих фактора по их влиянию на размеры зоны плазменной обработки, в том числе и при поверхностной закалке. Совместное их влияние на процесс обработки выражается погонной энергией, которая для плазменной обработки с учетом КПД дуги определяется как qnoz = I д ■ U д П vd6. (3)
Увеличение тепловложения с ростом погонной энергии дуги при плазменной закалке сталей способствует достижению более высоких температур нагрева поверхности и увеличению времени ее пребывания в области температур выше Ас1. Например, с увеличением погонной энергии плазменной закалки в заэвтектоид-ных сталях увеличивается степень растворения
Таблица 3. Сравнительные данные зон плазменного упрочнения стали 40Х в зависимости от скорости движения при токе дуги 80 А
V. мм/мин |
ширина, мм |
глубина, мм |
||
расчет |
эксперимент |
расчет |
эксперимент |
|
150 |
8,0 |
8.1 |
2,5 |
2.5 |
300 |
7,0 |
6,8 |
1,7 |
1.6 |
420 |
6,4 |
6,3 |
1,4 |
1.5 |
540 |
6 |
5,8 |
1,2 |
1.1 |
720 |
5,4 |
5,5 |
0,9 |
0.8 |
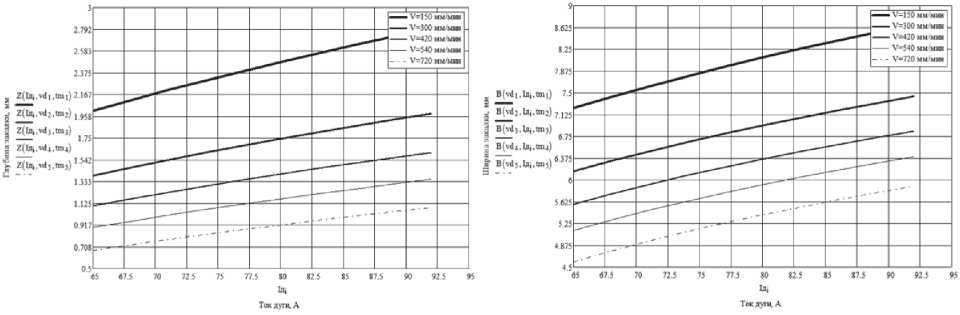
а
б
Рис. 7. Зависимость глубины (а) и ширины зоны закалки от тока плазменной дуги
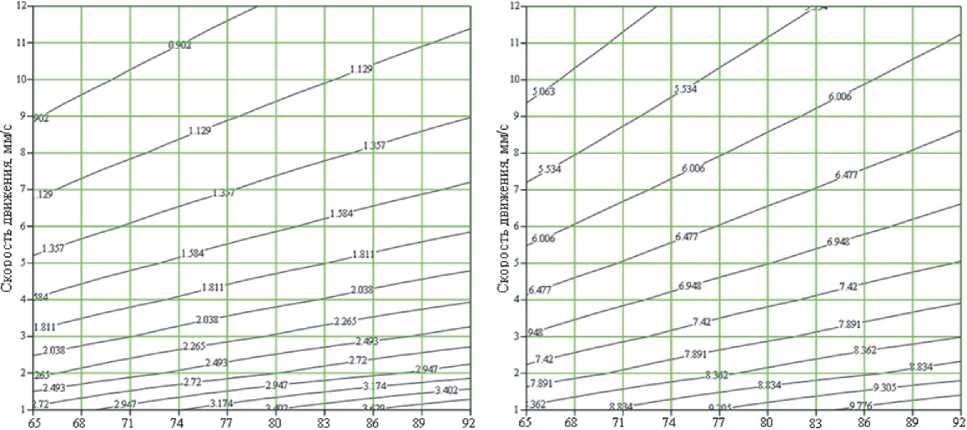
ТокдугнА Ток дуги. А а б
Рис. 8. Номограммы изменения глубины (а) и ширины (б) зоны плазменного упрочнения стали 40Х в зависимости от тока и скорости движения дуги
избыточного цементита, аустенит насыщается углеродом, что ведет к образованию значительной доли остаточного аустенита совместно с углеродистым тетрагональным мартенситом повышенной твердости при охлаждении. Поскольку карбиды обладают пониженной по сравнению со сталью теплопроводностью, чем больше содержание карбидной фазы, тем выше энергозатраты для формирования термообработанного слоя определенной глубины [8].
Используя приведенные выше номограммы (рис. 8), для заданных глубины и ширины зоны закалки можно определить необходимую погонную энергию. Ниже приведена таблица связи погонной энергии с шириной и глубиной упрочненного слоя для указанных выше скоростей движения и токов дуги.
Как и при любом другом методе упрочнения, связанном с термическим воздействием на металл, ряд показателей качества упрочненного слоя (глубина, твердость, знак и величина остаточных напряжений) будет определяться составом структур и характером их распределения по глубине материала. В свою очередь, тип формируемых структур зависит от параметров термических циклов, реализуемых в поверхностных слоях материала в процессе обработки: прежде всего скоростями нагрева и охлаждения в интер- вале температур фазовых переходов, максимальной температуры и времени нахождения материала при температурах фазовых переходов [7].
На рисунке 9 представлен термический цикл стали 40Х при V=420 мм/мин на поверхности и на глубине 1,4 мм. Также на рисунке приведены функции скоростей нагрева и охлаждения на поверхности образца и глубине 1,4 мм. Расчеты проводились с использованием формулы (2) в неподвижной системе координат. Для этого использовалось уравнение связи координаты х0 и х в неподвижной и подвижной системах координат:
x о = x + v de • t . (4)
За критическую скорость закалки для стали 40Х принималась 150 К/с.
Из рисунка видно, что на поверхности при температуре закалке скорость охлаждения составляет 1180 К/с, а на глубине 1,4 мм – 700 К/с, что выше критической скорости закалки для данной стали. Процесс идет с оплавлением поверхности, что согласуется с экспериментальными данными. Время существования жидкой фазы составляет 0,6 с, а время нахождения при температуре выше температуры закалки – 1,2 с. Для доэвтектоидных сталей температура закалки всего лишь на 30-50 оС выше точки Ас3 (815 оС для стали 40Х). Температура начала аустени-
Таблица 4. Связь глубины и ширины зоны закалки с погонной энергией
Погонная энергия, - 10 5 , Дж/м |
Глубина закалки, мм |
Ширина закаленной дорожки, мм |
1,2 - 1,5 |
1,1 - 1,2 |
5,4 - 6,2 |
1,7 - 1,9 |
1,4 - 1,5 |
5,7 - 6,5 |
2,6 - 3,3 |
1,8 -2 |
7,4 - 7,8 |
5,5 - 6,5 |
2,7 - 2,9 |
8,7 - 9,3 |
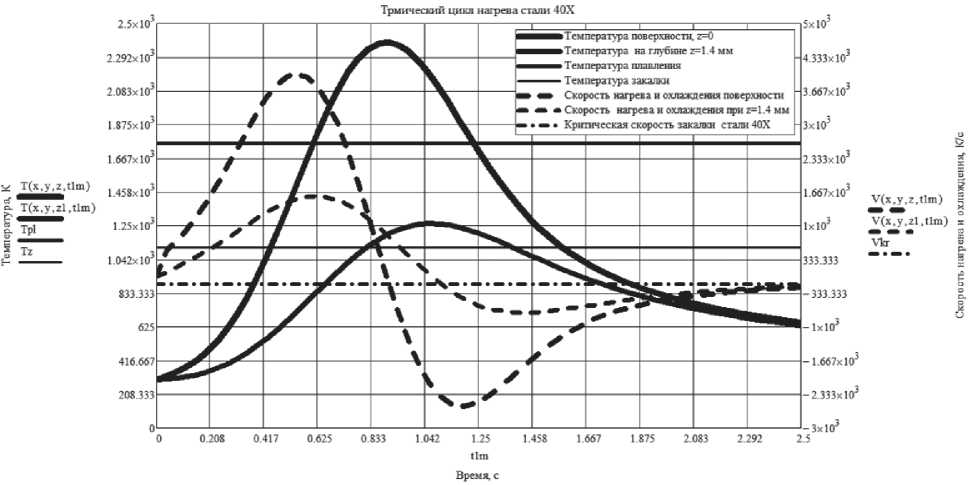
Рис. 9. Термический цикл стали 40Х при скорости движения 420 мм/мин
зации 1000 К (727 оС). Таким образом, процесс образования аустенита и растворения карбидов в данном случае будет протекать в течение 1,2 – 1,3 с. При этом максимальная температура на глубине 1,4 мм составляет 1200 К.
Из анализа термических циклов нагрева стали при различных скоростях движения дуги были определены скорости охлаждения на поверхности и глубине упрочнения при температуре закалки. Результаты расчетов представлены в таблице 5.
Таким образом, теплофизический анализ показал, что в заданном диапазоне скоростей движения при плазменной обработке стали 40Х с током дуги 80 А по расчетам на глубине упрочнения достигаются скорости охлаждения, превышающие критическую скорость закалки, что согласуется с экспериментальными данными измерения микротвердости и металлографического анализа. При этом с ростом скорости движения дуги происходит рост скоростей охлаждения как на поверхности, так и на глубине.
ВЫВОДЫ
В работе приведены результаты экспериментальных исследований и моделирование процесса поверхностной закалки стали 40Х плазменной дугой в диапазоне скоростей движения дуги 150 -720 мм/мин. По результатам экспериментальных данных измерений микротвердости и металлографического анализа определены размеры зон плазменного упрочнения в зависимости от скорости движения источника при токе плазменной дуги 80А.
С использованием массива экспериментальных данных по размерам зон упрочнения проведено моделирование процесса плазменной закалки и определены эффективный радиус и КПД плазменной дуги. На основе теплофизического анализа построены номограммы зависимости глубины и ширины зоны упрочнения стали 40Х от скорости движения и тока плазменной дуги, позволяющие определить ориентировочные режимы обработки для упрочнения на заданную глубину и величину погонной энергии.
В рамках рассматриваемой теплофизической модели проведен анализ термических циклов стали в указанном диапазоне скоростей движения плазменного источника и определены скорости охлаждения на поверхности и на глубине закалки, которые во всех случаях оказались выше критической скорости закалки.
Таблица 5. Скорость охлаждения в зависимости от скорости движения плазменной дуги
Скорость, мм/мин |
Время нахождения при температуре выше А с1 , с |
Скорость охлаждения, К/с |
Глубина закалки |
|
на поверхности |
на глубине |
|||
150 |
3,9 – 4,0 |
440 |
180 |
2,5 |
300 |
1,8 – 1,9 |
760 |
450 |
1,7 |
420 |
1,2 – 1,3 |
1180 |
700 |
1,4 |
540 |
0,9 - 1,0 |
1430 |
920 |
1,2 |
720 |
0,6 - 0,7 |
1830 |
1300 |
0,9 |
Список литературы Исследование и моделирование процесса плазменной закалки стали 40Х
- Евдокимов, В.Д. Технология упрочнения машиностроительных материалов. / В. Д. Евдокимов, Л. П. Клименко, А. Н. Евдокимова. - Киев: Профессионал, 2006. - 352 с.
- Белинин, Д.С. Особенности структурообразования при плазменной поверхностной закалке на большую глубину изделий из стали 40Х13 / Д.С. Белинин, Ю.Д. Щицын // Известия Самарского научного центра Российской академии наук. - 2012. - Т. 14. - № 4(5). - С. 1202-1205.
- Балановский, А.Е. Развитие плазменных технологий: сварка, наплавка, упрочнение, резка / А.Е. Балановский // Сварка в Сибири. - 2000. - № 2. - С. 8-19.
- Щицын, Ю. Д. Плазменные технологии в сварочном производстве. Ч. 1 / Ю. Д. Щицын. - Пермь: Пермский государственный технический университет, 2004. - 73 с.
- Соснин, Н.А. Плазменные технологии. Руководство для инженеров / Н. А. Соснин, С. А. Ермаков, П. А. Тополянский. - СПб: Изд-во Политехнического университета, 2013. - 406 с.
- Сорокин, В.Г. Марочник сталей и сплавов /В. Г. Сорокин, А. В. Волосникова, С.А. Вяткин и др. Под общ. ред. В.Г. Сорокина. - М.: Машиностроение, 1989.- 640 с.
- Иваницкий, В.В. Назначение режимов закалки с использованием концентрированных источников нагрева / В.В. Иваницкий, В.Ю. Скиба, Н.Л. Степанова // Обработка металлов. - 2005. - № 3 (26). - С. 22-24.
- Сафонов, Е.Н. Формирование структуры и свойств локальной зоны упрочнения при плазменной закалке заэвтектоидных сталей / Е.Н. Сафонов // Вестник Сибирского государственного индустриального университета. - 2017. - № 4 (22). - С. 31-35.