Исследование эффективности электроплавки окатышей в дуговой печи при дожигании оксида углерода топливно-кислородными горелками
Автор: Степанов Виктор Александрович, Крахт Людмила Николаевна, Меркер Эдуард Эдгарович, Кем Александр Юрьевич, Харламов Денис Александрович
Журнал: Вестник Донского государственного технического университета @vestnik-donstu
Рубрика: Машиностроение и машиноведение
Статья в выпуске: 2 (85) т.16, 2016 года.
Бесплатный доступ
Рассмотрены особенности нагрева и плавления железорудных металлизованных окатышей (ЖМО) с применением способа подачи окатышей через осевые каналы электродов. При использовании данной системы подачи железорудного сырья через отверстия в электродах сыпучие окатыши попадают в зону влияния электрических дуг на расплав, что обеспечивает высокую скорость их плавления. При этом улучшаются технико-экономические показатели электроплавки в дуговой сталеплавильной печи (ДСП). Применение топливно-кислородных горелок с подачей кислорода позволяет оптимизировать процесс плавления железорудных металлизованных окатышей, улучшая условия шлакообразования, нагрева, обезуглероживания металла с дожиганием отходящих горючих газов (СО, Н2, и др.) в дуговой печи.
Металлизованные окатыши, электроплавка, электрод, дуговая печь, дожигание газов, электрическая дуга, горелка
Короткий адрес: https://sciup.org/14250215
IDR: 14250215 | DOI: 10.12737/19700
Текст научной статьи Исследование эффективности электроплавки окатышей в дуговой печи при дожигании оксида углерода топливно-кислородными горелками
Введение. Производство стали в дуговых сталеплавильных печах — современная технология плавки высокого уровня [1–2]. Эффективность технологии электроплавки железорудных металлизованных окатышей (ЖМО) в дуговой сталеплавильной печи (ДСП) зависит от теплового состояния ванны жидкого металла, метода загрузки и скорости плавления ЖМО в ней, окисленности шлака и металла, степени обезуглероживания расплава [3–5]. Известно применение в реальных производственных условиях плавки ЖМО в ДСП топливно-кислородных горелок (ТКГ) для подачи кислорода, газа и угольной пыли с целью интенсификации процессов шлакообразования, нагрева и обезуглероживания в рабочем пространстве печи [6–8].
Машиностроение и машиноведение
Цель настоящей работы — исследование особенностей дожигании оксида углерода в ДСП топливнокислородными горелками и установление их влияния на эффективность электроплавки ЖМО.
Результаты и их обсуждение . Исследования, выполненные в лабораторных и производственных условиях, показали, что подача ЖМО в расплав ванны дуговой печи, в зону воздействия электрических дуг, интенсифицирует технологические процессы электроплавки стали за счет повышения скорости нагрева и плавления окатышей в расплаве [9-10]. При этом установлено, что быстрый и экономичный нагрев ЖМО в значительной мере определяется скоростью загрузки окатышей в ванну жидкого металла.
Выбор скорости загрузки ЖМО ( Vок , кг/с) осуществляется с учётом текущего теплового состояния ванны, которое зависит от тепловой мощности печи и скорости плавления порций окатышей ( Vпл , кг/с) в агрегате. При этом общая продолжительность нагрева и плавления окатышей (т К , , с) зависит от общей тепловоспринимающей поверхности слоя ЖМО ( F0K , м2) и его массы (2 т ок , кг).
В работе использовалось следующее обобщающее выражение для расчетов:
Т OK = ( F ok • П -Р ок " Г к )Ф^), (1)
где F ок = 4 п - г о ,; гок — радиус окатыша; 2 ток = n • ток ; n — количество окатышей; т ок = (4 / 3) п - г ок • р ок ; р ок — плотность материала окатыша, кг/м 3 .
Учитывая, что поверхность порций ЖМО за некоторое время достигает температуры плавления (Тпл(пов), оС), а внутри каждого окатыша сохраняется пониженная температура (Ток(в), оС), то суммарное время нагрева и плавления окатыша то, будет равно ок τ∑
р ок " [ С ок ( Тпл ( пов ) Т ок ( в ) ) + ^ Н пл ] ‘ r ок
ср qок где №пл — удельная теплота плавления окатыша, Дж/кг; Сок — удельная теплоёмкость окатыша, Дж/ (кг К); qссрк — усреднённый тепловой поток на поверхность слоя ЖМО при нагреве его от Ток(в) до Тпл(пов), который равен пл ( пов )
Ч ср = J а эф • ( Тр - Т ок ( в ) ) d Т
Т ок ( в )
где а э ф — эффективный коэффициент теплоотдачи, Вт / (м2 К); Т р — температура расплава в печи, К .
Анализ приведённых выражений показывает, что при постоянстве физических свойств ( рок , Сок , ^Нпл ) и массы окатышей (ток), суммарное время ток и скорость их загрузки (Vок ) в ДСП зависит от факторов теплового состояния ванны (Тр ,оС) и эффективности теплообмена (аэф ) в системе «окатыш — расплав». На рис. 1 представле ны результаты расчётов значений т^к в зависимости от Тр и аэф для разных данных по r ок при условиях подачи ЖМО в зону высоких температур под электроды в печи и вне этих электродов.
ок т s ,c
3100 2900 2700 3100 23 00 2100 1900 T p , K
* ■ ■ ■ ■ ■ ■ 0
40-
30-
20-
10-1
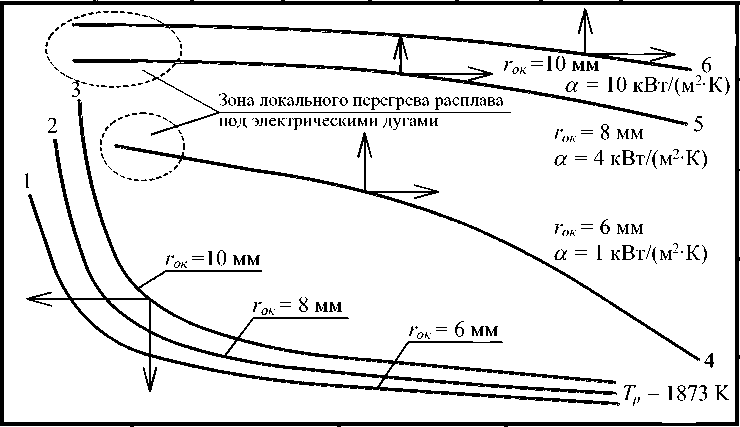
ь io ток, c
5,5
a , кВт/(м2К)
Рис. 1. Зависимость суммарной продолжительности плавления единичного окатыша т ок от эффективного коэффициента теплоотдачи а эф (кривые 1-3) и температуры расплава Т (кривые 4-6): 1, 2, 3 — т ОК ЖМО радиусом 6, 8, 10 мм при Tp =1873 K , соответственно; 4, 5, 6 — т ОК ЖМО радиусом 6, 8, 10 мм и коэффициентом теплоотдачи 1, 4 и 10 кВт/(м2 • К)
Из полученных данных следует, что продолжительность плавления окатыша снижается (т ОК ^ min) при увеличении α эф и уменьшении r , причём при подаче ЖМО под электрические дуги (кривые 4, 5 и 6) общее время τ ок в 2-3 раза ниже (кривые 1, 2 и 3), чем при условии подачи окатышей вне зоны непосредственного влияния дуг.
В лабораторных условиях для оценки влияния степени обезуглероживания ванны на скорость плавления ЖМО, металлизованные окатыши расплавляли в тигле с жидким металлом, при этом перемешивание осуществляли продувкой азотом. Оценивали зависимость скорости плавления ЖМО ( Vпл , кг /с) от степени перемешивания расплава ( VN , м3 /с) и содержания углерода в окатышах. Из полученных данных (рис. 2) можно сделать вывод о заметном влиянии на скорость плавления окатышей в металло-шлаковой ванне содержания в них углерода и интенсивности продувки расплава газообразным азотом, что можно соотнести со скоростью обезуглероживания ванны.
В производственных условиях при подаче потока ЖМО через полые электроды в подэлектродное пространство совместно с сыпучими добавочными материалами (известь, коксик) наблюдается повышение вспениваемости шлака, что позволяет повысить эффективность работы ДСП. При этом снижение расхода электроэнергии составило 8,878 ГДж или 16,4 кВт ч/т стали, что согласуется с данными [10]. При подаче кислорода через сопла ТКГ на шлак и металл часть О2 расходуется на дожигание СО , а остальная часть — на окисление углерода в металле, т.е. Vc = К1 • q0 = f (А[O]), где К1 — стехиометрический коэффициент; q0 — скорость поступления О2 в расплав, с-1 . При этом окисленность металла А[O] = [O]ф - [O]р , где [O]ф и [O]р — фактическое и равновесное содержание О2 в объёме металла соответственно. Равновесное с углеродом содержание кислорода в металле равно [O]р = рсо / (КС •[C] • fC • f0), где рсо — давление выделения пузырей СО , H/м2; КС — константа равновесия реак ции окисления углерода; [C] — содержание углерода в расплаве, % ; fC и f} — коэффициент активности углерода и
Машиностроение и машиноведение
кислорода.
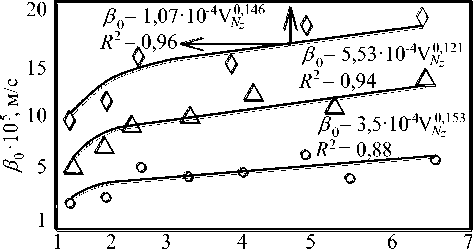
О 1, T = 1300 °C К 2, T = 1400 °C 0 3, T = 1475 °C
Расход азота на перемешивание расплава V n z '10 6 м3/с
а)
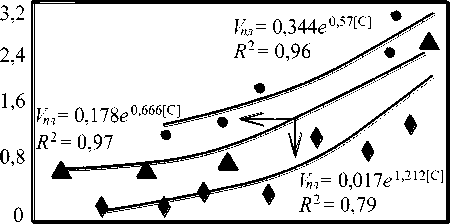
• 4, V nz = 6,2^106 м3/с ▲ 5, V nz = 3,5^10 " 6м3/с ф 6, V nz = 0 м3/с
1,5 2,0 2,5 3,0 3,5 4,0
Содержание углерода в расплаве [C], %
б)
Рис. 2. Зависимость коэффициента массоотдачи от расхода азота при различных температурах его нагрева (а) и влияние содержания углерода в расплаве на скорость плавления окатышей при различных расходах азота (б)
Из анализа приведённых выражений следует, что чем выше содержание [ C ], тем меньше значение [ O ] , а следовательно выше перепад А [ O ], что приводит к повышению скорости обезуглероживания металла, т.е. Ус ^ max . Это обстоятельство показывает, что вспенивание шлака и погружение электрических дуг в шлак интенсифицирует процессы нагрева и плавления окатышей в ванне дуговой печи [5, 7-9, 10].
Эффективность энергосберегающих условий электроплавки ЖМО в ДСП определяется взаимосвязью уровня теплопитания ванны ( А qe , Вт ) и фактическим расходом окатышей ( Уок , кг/с в соответствии с выражением:
Аqe = GT- Cm (dT) = ( Go + Vok - t) - Cm - V (4) d t где Gt = G0 + Vok - t — текущая масса металла в печи по ходу загрузки ЖМО в ванну, кг; G0 — начальная масса в пе чи от расплавления скрапа, кг; Cm — средняя теплоёмкость металла в печи, Дж/(кг^оС); т — время загрузки ЖМО в печь, с; Vt — скорость нагрева металла в ДСП, оС/с.
После преобразования выражения (4) формула расчёта расхода окатышей по ходу электроплавки имеет вид:
V ok = (/ q ; - G o )/ t . (5)
С т + V t
Эффективность электроплавки ЖМО в ДСП определяется необходимостью соблюдения оптимального соотношения между показателями расхода окатышей ( Уок , кг / с) и скоростью их плавления (Упл , кг /с) в ванне агрегата, т.е. Уок < Упл = ток - n / т , где ток — масса окатышей, кг; n — количество одновременно плавящихся окатышей на поверхности металла под дугами; т — время плавления окатыша, с. При попадании порций ЖМО в расплав на поверхность испарения металла (менисков под дугами) значение n = 0,9069 - (3 - Sмен)/ Sok , где 0,9069 — коэффициент размещения окатышей в слое при их наилучшем заполнении поверхности менисков (3 - Sмен, м2 ); SMeH = 2п(Lg + гэ) - h , где Ld — длина дуги, м; r — радиус электрода в печи, м; SOK = п-r2К — поверхность, которую занимает один окатыш, м2; r0K — средний радиус окатышей, м.
С учётом вышеизложенного оптимальное соотношение для электроплавки окатышей в печи имеет вид:
Уок / Vпл = К0(хэ), где К0(хэ) — критерий оптимального хода плавки стали в ванне ДСП. С учётом преобразований и при т = п- r -р значение К имеет вид:
ок з ок ок ( А . Э .)
К 0( х . э .) = ( =q- - ^ о )/( 4 п- d - n ). (6) С т - V t 3
Из анализа выражения (6) следует, что если критерий оптимальности больше единицы, то снижается скорость плавления ( У л ^ min), а если К 0( х э ) < 1, то скорость загрузки окатышей повышается ( Уок ^ max ), но при этом падает значение Упл по ходу процесса плавки. По ходу электроплавки ЖМО теплоусвоение ванны A qe = О в - т / G T , а загрузку окатышей в дуговую печь осуществляют в зависимости от теплового состояния ванны ( QB ,Вт • ч/т) с учётом погружения тепла от электрических дуг ( Q g ,Вт • ч/т) и дожигания ( Qc0 , Вт • ч/т) оксида углерода ( СО ) струями кислорода ТКГ во вспененном шлаке агрегата, то есть
Q e = ( б д + Q Ж ) - ( Q Ифзл + О Ш ), (7) где Q g — тепловая мощность всех электрических дуг в печи, Вт - ч / т ; О ф, и О ШЛ — потери тепла через футеровку и шлаком, Вт^ч/т.
Струи кислорода из сопел ТКГ по ходу движения до поверхности шлака и в объёме шлака взаимодействуют с потоком СО , выделяющегося из ванны, с последующим его дожиганием по реакции СО + 0,5 - О 2 ^ СО 2 с выделением тепла около 12,5 МДж/м3. Объём выделяющегося СО из ванны печи определяется по формуле:
У СО = 28/12( Ус - G т + У ок - [ C ]) /( G о - 100 - р со ), (8) где V c — скорость обезуглероживания металла в ванне ДСП, %[ C ]/ c ; р co — плотность газа пузырей, кг/м3 . Значение О ДО = V co - Q co -т / G T , где Qco — тепловой эффект реакции дожигания 1 м 3 СО до СО 2 , равный ® 12500 кДж / м 3 .
Эффективность режима дожигания СО струями ТКГ во вспененном шлаке оценивается двумя параметрами: КПД дожигания СО , равным п со = СО2 / ( СО2 + СО ) и эффективностью теплопередачи Кэф = A ц С / О ДО. , где A ^ СО — доля энергии дожигания СО , переданная шлаковой ванне.
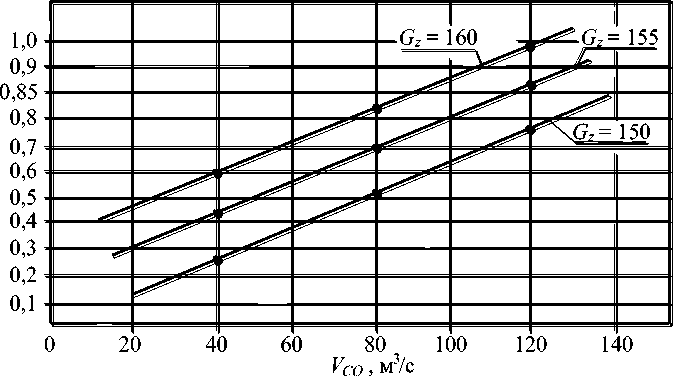
а)
Машиностроение и машиноведение
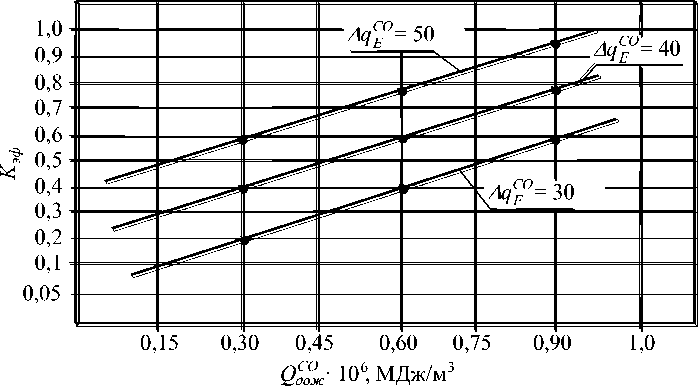
Рис. 3. Зависимость количества выделяемой энергии ( а ) при дожигании СО ( О СО , МДж/м 3 ) от скорости его выделения из ванны ( Vc о , м 3 /с) при различных значениях массы металла в печи по ходу загрузки ЖМО в расплав ( GT , кг); влияние Q ^ 0 ( б ) на коэффициент эффективности теплопередачи от газов к шлаку ( K эф ) при различных долях энергии дожигания СО , передаваемой шлаковой ванне ( A q EO , % ) в ДСП
Из полученных данных следует, что с увеличением объёма выделяемого из ванны СО ( VC0 ^ max ), количество образуемой энергии ( О СО ,МДж/м3) в печи возрастает по мере увеличения массы металла ( G т ^ max ) в ванне. При этом по мере возрастания величины теплоты дожигания О СО коэффициент эффективности теплопередачи ( К эф ) от потока дожигаемого газа к ванне в печи возрастает при создании условий увеличения Δ q ECO . Установлено, что эти условия выполняются при, например, вращении топливно-кислородного факела от ТКГ, повышении скорости его истечения из горелки или увеличении угла её наклона к поверхности ванны.
При организации дожигания СО струями О 2 от ТКГ в условиях заглубления факелов дожигания во вспененный шлак механизм теплопередачи соответствует условиям при погружном горении, которое отличается высокой эффективностью теплообмена ( К эф ^ 1). Шлаковая ванна нагревается со скоростью 5-10 ° С / мин и за счёт интенсивной её циркуляции от обезуглероживания и плавления ЖМО тепло передаётся металлу. Теплообмен между шлаком и ванной металла ускоряется за счёт VC ^ max и выбрасывания капель металла в шлак с последующим их оседанием в металл с более высокой температурой. Поскольку скорость поступления в шлак тепла от дожигания СО составляет О ш = Vt ' G ш ' с ш , где Vt — скорость нагрева шлака; Сш и с ш — масса шлака и его удельная теплоёмкость соответственно. При массовой скорости поступления капель (брызг) металла в шлак V k их массовая доля в шлаке будет К , тогда масса металлических капель в шлаке составит G k = С ш • К . При этом продолжительность пребывания капель металла в шлаке будет т к = G k / Vk , а уровень нагрева их за это время равно A tk = Vk -т k , °С Перенос тепла при оседании капель в ванну металла составит Qk = Vk ■ т k ■ c m , где c m — удельная теплоёмкость капель металла, Дж/(кг • ОС).
На основе совместного рассмотрения равенств для Ош и Qk получим соотношение:
О ш / Q k = ( c k - к )/( c m. к + (1 - к ) . c m ). (9)
Экспериментально установлено, что с увеличением расхода О 2 , идущего на дожигание СО значения О ССОж , Qk и VC возрастают, что интенсифицирует теплопередачу в системе «шлак — металл» за счёт стремления К эф и A q 1 ° ^ max. При этом коэффициент полезного теплоиспользования в дуговой печи равен:
П КПТ = 1 - [( Ог ух + Ч пот -т пл )/( О^ кз + О О + О к )], (10) где О у — потери тепла с уходящими газами и пылью; qnom — удельные потери тепла через футеровку агрегата; О Рз — тепловой эффект реакции окисления углерода и других составляющих химсостава ЖМО.
Анализ выражений (5), (7)–(10) показывает, что при использовании режима дожигания СО в шлаке струями О2 от ТКГ параметры Vt , QСдоОж , Qk и ηКПТ существенно возрастают, что в целом интенсифицирует теплообмен между шлаком и металлом, а это способствует улучшению показателей процесса ∆qCO , Кэф и τ , что приводит к повышению производительности печи и снижению удельного расхода электроэнергии на процессы плавки ЖМО в агрегате.
Расходы кислорода от ТКГ на сжигание топлива и дожигание СО не только интенсифицируют нагрев шлака в печи, но и влияют на окисленность шлака ( ∑ FeO , % ), режимы обезуглероживания и нагрева металла в ДСП при различных расходах окатышей в агрегате.
Выводы . Теплоэнергетические условия электроплавки ЖМО в ДСП при подаче их через трубчатые (полые) электроды с применением ТКГ и дожиганием СО в шлаке являются более выгодными по сравнению с типовым режимом плавления окатышей, когда используются сплошные графитизированные электроды, т.е. при непрерывной подаче металлизованных окатышей в печь вне зоны воздействия на окатыш электрических дуг, так как температура шлакового расплава в этой зоне существенно ниже, чем в расплаве под дугами. При использовании топливнокислородных горелок в дуговой печи необходим избыток О 2 на дожигание СО в шлаке и вне его, что интенсифицирует нагрев и плавление окатышей в системе «шлак — металл», а это обстоятельство, в свою очередь, способствует улучшению технико-экономических показателей процесса электроплавки стали.
Список литературы Исследование эффективности электроплавки окатышей в дуговой печи при дожигании оксида углерода топливно-кислородными горелками
- Henrion, R. Perfect electric melting/R. Henrion, F. Schleimer//Iron and Steelmaker. -1982. -V.9. -№ 11. -P. 48-51.
- Kohiani, T. Features and trend in electric steelmaking for new market mills/T. Kohiani, K.Kudo, S. Murokami//Transactions of the Iron and Steel Institute of Japan. -1981. -№ 10. -P. 431-436.
- Способ электроплавки стали: патент 236009 Рос. Федерация/Э. Э. Меркер, А. А. Гришин, А. И. Кочетов. -опубл. 27.06.2009, Бюл. № 18. -27 с.
- Сазонов, А. В. Интенсификация плавления окатышей при их загрузке в зону воздействия электрической дуги на шлаковый расплав/А. В. Сазонов, Э. Э. Меркер, Е. А. Черменёв//Бюллетень «Чёрная металлургия». -2011. -№ 8. -С. 62-64.
- Черменёв, Е. А. Об эффективности электроплавки стали при загрузке металлизованного сырья через трубчатые электроды в ванну дуговой печи/Е. А. Черменёв, Э. Э. Меркер, О. П. Коберник//Бюллетень «Чёрная металлургия». -2013. -№ 5. -C. 48-51.
- Меркер, Э. Э. Особенности технологии электроплавки окатышей в дуговой печи/Э. Э. Меркер, А. В. Сазонов, А. А. Гришин//Известия ВУЗов. Чёрная металлургия. -2008. -№ 2. -C. 31-33.
- Меркер, Э. Э. Энергосберегающий режим плавки окатышей в 150-т ДСП/Э. Э. Меркер, В. В. Федина, А. И. Кочетов//Электрометаллургия. -2003. -№ 9. -C. 43-44.
- Меркер, Э. Э. Электроплавка окатышей в дуговой печи/Э. Э. Меркер, В. В. Федина, Д. А. Харламов//Бюллетень «Чёрная металлургия». -2004. -№ 7. -C. 16-19.
- Меркер, Э. Э. Повышение энергоэффективности электроплавки стали при подаче окатышей в ДСП через каналы в электродах/Э. Э. Меркер, В. А. Степанов//Бюллетень «Чёрная металлургия». -2014. -№ 1. -C. 41-47.
- Меркер, Э. Э. Энергосберегающие условия плавления металлизованных окатышей при их подаче через трубчатые электроды в ванну дуговой печи/Э. Э. Меркер, Е. А. Черменёв//Сталь. -2015. -№ 1. -C. 23-28.