Исследование механических свойств корундовой керамики при изменении пористости и размеров кристаллитов
Автор: Григорьев М.В., Кульков С.Н.
Журнал: Журнал Сибирского федерального университета. Серия: Техника и технологии @technologies-sfu
Статья в выпуске: 1 т.4, 2011 года.
Бесплатный доступ
Исследована прочность корундовой керамики на основе порошковых систем, получаемых методом термического разложения гидроксида алюминия и методом термического разложения водного раствора азотнокислой соли алюминия в плазме высокочастотного разряда. Показано, что при содержании 60 % плазмохимического порошка Al2O3 в смеси наблюдается резкое изменение прочностных характеристик, которые тем больше, чем меньше пористость, при этом пористости 55 % соответствует порог перколяции. Аппроксимация зависимости прочности от среднего размера пор на беспористое состояние показывает возможность получения керамики с почти теоретической прочностью. Обнаружена корреляция между микронапряжениями в кристаллитах и макропрочностью в спечённой керамике: при минимуме микронапряжений прочность соответствует 500 МПа, а микронапряжения 2,5 МПа соответствуют полностью макроразупрочненному материалу.
Прочность, пористость, наноструктуры, корунд
Короткий адрес: https://sciup.org/146114559
IDR: 146114559
Текст научной статьи Исследование механических свойств корундовой керамики при изменении пористости и размеров кристаллитов
В настоящее время исследователи уделяют внимание пористым проницаемым материалам, особенно керамическим. Это связано с широкими возможностями их применения в качестве биоимплантов, фильтров, носителей катализаторов и др. [1, 2].
Одним из перспективных материалов для изготовления пористых конструкций является оксид алюминия, характеризующийся высокой прочностью, коррозионной стойкостью, стойкостью к химически активным средам и биоинертностью [1-5].
Наличие пористости в корундовой керамике приводит, как правило, к заметному снижению механической прочности, вероятно, вследствие ограниченной возможности релаксации концентратов напряжений при нагружении [6]. Синтез пористых материалов на основе оксида алюминия с необходимым комплексом свойств требует детального исследования закономерностей формирования физико-механических характеристик в зависимости от особенностей структуры, таких как размеры структурных элементов, вид пор, их количество и распределение по размерам [7].
В связи с этим целью настоящей работы явилось изучение прочности корундовой керамики при изменении размеров структурных элементов и распределении пор по размерам в широком интервале пористости.
Материалы и методика
Исследована пористая керамика на основе порошков оксида алюминия различной дисперсности - технический глинозем, полученный методом термического разложения гидроксида алюминия (ГОСТ 30558-98), и плазмохимический порошок, полученный путём термического разложения водного раствора азотнокислой соли алюминия в плазме высокочастотного разряда (ТУ-2320-001-07622928-96) [8, 9]. В плазмохимическом порошке Al2O3 средний размер частиц равен 0,2 - 5 мкм, при этом частицы имеют пенообразное строение, также присутствуют сферические частицы, как полые, так и заполненные. Средний размер частиц в глиноземе равен 30 – 100 мкм, а морфология частиц имеет радиально-лучистый характер агрегирования первичных кристаллов, имеющих вид шестиугольных призм различной степени развития.
Для получения пористой керамики были приготовлены смеси порошков во всем концентрационном интервале от технического глинозема до плазмохимического Al2O3. Порошки смешивали в барабанной мельнице в течение 24 ч. Образцы цилиндрической формы прессовали на гидравлическом прессе с давлением 250 МПа.
Спекание осуществляли при температурах 1200 - 1650 °С с интервалом через 100 °С и продолжительностью изотермической выдержки в течение 1 ч.
Рентгеноструктурный анализ керамик на их основе осуществляли на дифрактометре типа ДРОН с фильтрованным CuK α -излучением. Средний размер кристаллитов рассчитывали по уширению рефлекса на малых углах дифракционной картины [10]. Величину микроискажений кристаллической решетки рассчитывали по уширению рефлекса на дальних углах дифракционной картины [10].
Испытания на сжатие образцов пористой керамики осуществляли на испытательной машине "Instron-1185” с постоянной скоростью нагружения 340-4 с-1. Испытания проводили на образцах цилиндрической формы, фиксировались осевая сжимающая нагрузка и деформация образцов. По полученным данным строили зависимость «напряжение σ (МПа) – относительная деформация ε (%)» с учётом жесткости испытательной машины.
Зависимости, полученные в данной работе, имели нелинейный характер, поэтому проводили их линеаризацию путем перестроения графиков в двойных логарифмических координатах.
Результаты и обсуждение
Широкий диапазон концентраций плазмохимического порошка Al2O3 в исходных смесях порошков и спекание в широком диапазоне температур позволили сформировать большой набор состояний корундовой керамики с различным объемом порового пространства и морфологией пор, величиной среднего размера кристаллитов и микроискажений кристаллической решетки.
На рис. 1 представлена зависимость предела прочности на сжатие от содержания в керамике плазмохимического порошка Al 2 O 3 для выделенных интервалов пористости. Из рисунка – 114 –
σ сж , 800
МПа
- пористость - пористость - пористость - пористость - пористость
50-55%
45-40%
37-32%
32-27%
25-20%
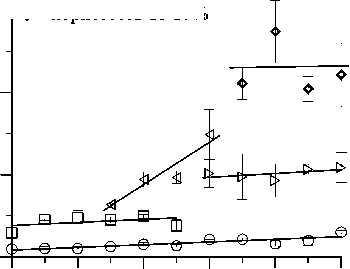
0 20 40 60 80 100
Содержание плазмохимического Al2O3, %
Рис. 1. Зависимость предела прочности на сжатие от концентрации плазмохимического порошка Al2O3 в керамике с различной пористостью
видно, что при пористости 50 % и ниже предел прочности, равный около 50 МПа, практически не зависит ни от морфологического строения исходных порошков, ни от соотношения плазмохимического порошка и глинозема. При изменении объема порового пространства от 40 до 32 % происходит разделение зависимости на две области: первая - концентрация плазмохимического порошка до 50 %, вторая – выше 50 %. Внутри этих областей зависимость прочности от содержания плазмохимического Al2O3 слабо выражена, однако в целом прочность в первой группе ниже в два раза, нежели во второй. Как видно из рисунка, объем порового пространства от 32 до 27 % получается только в образцах с концентрацией плазмохимического порошка оксида алюминия от 30 до 60 %; при этом необходимо отметить, что предел прочности значительно растет с ростом концентрации плазмохимического порошка в системе. При пористости менее 25 % и содержании плазмохимического порошка от 70 до 100 % образцы имеют максимальную прочность. Таким образом, показано, что на прочность корундовой керамики главным образом влияет объем порового пространства, а в образцах с одинаковой пористостью прочность тем выше, чем больше плазмохимического порошка в исходной смеси порошков.
На рис. 2 представлена зависимость предела прочности на сжатие от пористости. Видно, что она существенно уменьшается с ростом пористости (рис. 2, а), а линеаризация данной зависимости (рис. 2, б) свидетельствует о наличии области значений пористости около 55 %, при которой наклон заметно изменяется.
Прежде всего, это связано с тем, что при пористости до 50 % она имеет вид поровых кластеров различной формы, как обособленных, так и сообщающихся, а при пористости выше 50 % структура керамики имеет вид двух взаимопроникающих компонент – «вещество – пора». Таким образом, наблюдающийся излом на зависимости предела прочности на сжатие от пористости свидетельствует о том, что имеет место изменение характера поровой структуры, связанное, по-видимому, с известными в пористых материалах порогами перколяции [11].
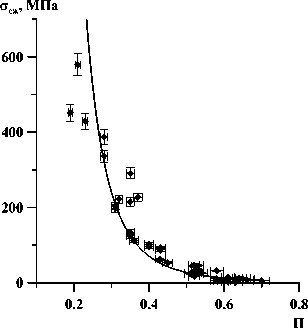
а
Рис. 2. Зависимость предела прочности
ln( σ )
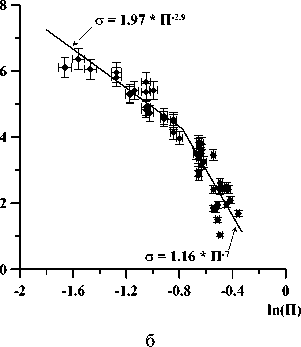
на сжатие от пористости корундовой керамики на основе
порошков различной дисперсности
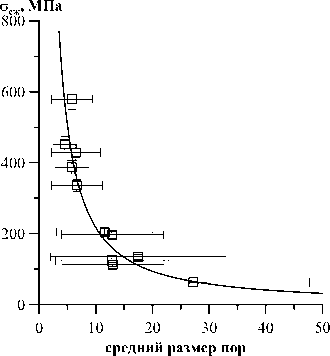
Рис. 3. Зависимость предела прочности на сжатие от среднего размера пор и его дисперсии в корундовой керамике
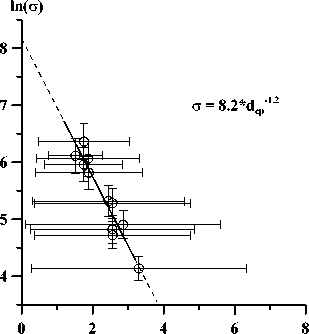
ln(d ср )
Вид порового пространства и размер пор также существенно влияют на прочность материала. На рис. 3 представлена зависимость предела прочности на сжатие от среднего размера пор (dср) в керамике и их дисперсии. Видно, что предел прочности тем больше, чем меньше средний размер пор и его дисперсия, а линеаризация данной зависимости и ее экстраполяция на нулевую пористость показала, что прочность исследуемой керамики составит около 3,5 ГПа, что соответствует оценкам в [12].
Известно, что в металлах связь между прочностью и размерами структурных элементов часто описывается соотношениями типа Холла-Петча [13], что связано, в первую очередь, с изменением дефектной структуры зерна и приграничной зоны, а во-вторых, с внутренними напряжениями.
Повышенная дефектность границ зерен на микроуровне способствует вовлечению их при комнатной температуре в пластическую деформацию путем проскальзывания по границам зерен и усилению диффузионных процессов вблизи них [14,15]. При этом прочность определяется соотношением «Холла-Петча»:
ст = С о + kD-n, (1)
где спт - предел текучести; с0 - сопротивление деформации монокристалла; D - средний размер зерна; k – коэффициент Холла-Петча [16, 17]; константа n имеет значение между ½ и 1, при этом n близко к единице, когда плотность дислокаций внутри зерна мала, и почти все дислокации сосредоточены в приграничной зоне [13].
В керамических материалах движение дислокаций и зернограничное проскальзывание при данных условиях проведения эксперимента сильно затруднены. Тем не менее, подобный анализ позволит оценить влияние размеров структурных элементов D, определенных из рентгенографических данных, на механические свойства материала.
Такая зависимость представлена на рис. 4, а, из которой видно, что она имеет экспоненциальный вид, а ее линеаризация показала, что зависимость описывается соотношением с = 15,2 • D5,
однако в отличие от металлов в керамике рост размера структурных элементов приводит к увеличению прочности. По-видимому, это обусловлено тем, что при минимальном размере структурных элементов прочность минимальна вследствие низкой температуры спекания, когда D не растет и пористость не уменьшается. С другой стороны, рост D (рост размеров структурных элементов) в исследуемых материалах происходит только при повышении температуры спекания, когда с уменьшением пористости идет их заметный рост, т.е. в зависимость типа «Холла-Петча» в данном случае входят два вклада - пористость и размер кристаллитов.
Зависимость между макро- и микронапряжениями в пористой керамике представлена на рис. 5. При высоком уровне микронапряжений предел прочности имеет минимальные значения, а при величине микронапряжений менее 1,5 МПа происходит резкий рост предела прочности. Линеаризация данной зависимости (рис. 5, б) описывается формулой
σ макро
6,3 Смикро ,
(3),
и ее экстраполяция показывает, что отсутствие микронапряжений позволяет получить максимальную «макропрочность» 0,5 ГПа, а при уровне микронапряжений после спекания выше 2,5 МПа образуется полностью разупрочненная керамика.
По-видимому, кроме пористости и размера структурных элементов, влияющих на ход зависимости, подобной закону Холла-Петча, изменение также обусловлено перемещением структурных элементов при их малом размере в случае малой прочности по границам зерен. Она определяется также высокой прочностью границ раздела в синтезированном каркасе - при повышении температуры спекания и, соответственно, при уменьшении порового пространства. Возможно также проявление микромеханической неустойчивости стержневых структур, приводящее к аномальному ходу кривых «σ-ε» [6].
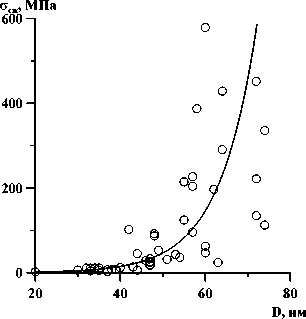
а
8ln( σ )
σ = 15.2 * D5
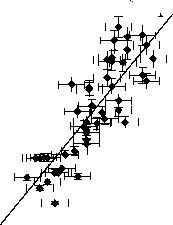
1—I—1I—1—I—1—I1—I
2.8 3.2 3.6 4 4.4 4.8
ln(D)
б
Рис. 4. Зависимость предела прочности на сжатие от среднего размера кристаллитов корундовой керамики на основе порошков различной дисперсности
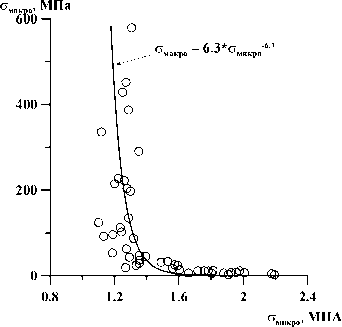
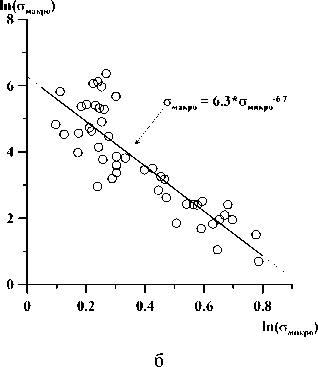
Рис. 5. Зависимость предела прочности на сжатие от микронапряжений кристаллической решетки корундовой керамики на основе порошков различной дисперсности
Выводы
Показано, что при содержании 60 % плазмохимического порошка Al2O3 в смеси наблюдается резкое изменение прочностных характеристик, которые тем больше, чем меньше пористость, при этом пористость 55 % соответствует порогу перколяции.
Аппроксимация зависимости прочности от среднего размера пор на беспористое состояние (с нулевым размером пор) показывает возможность получения керамики с почти теоретической прочностью.
Обнаружена корреляция между микронапряжениями в кристаллитах и макропрочностью в спечённой керамике – при минимуме микронапряжений прочность соответствует 500 МПа, а микронапряжения 2,5 МПа соответствуют полностью макроразупрочненному материалу.
Работа выполнена при частичной финансовой поддержке грантов ФАО №№ П-2115, П-254 и МК-5260.2010.8 Президента РФ.