Исследование перспективных составов для отливки медных анодов
Автор: Озеров С.С., Богатырев Д.М., Бородин А.Д., Султанов Н.Н.
Журнал: Вестник Южно-Уральского государственного университета. Серия: Металлургия @vestnik-susu-metallurgy
Рубрика: Литейное производство
Статья в выпуске: 3 т.23, 2023 года.
Бесплатный доступ
Розлив меди в аноды является завершающей стадией огневого рафинирования меди. В настоящее время на медном заводе ПАО «ГМК «Норильский Никель» для предохранения изложниц от быстрого изнашивания и предотвращения приваривания к ней анодов при розливе изложницы поливают раствором термостойкой обмазки на основе диоксида кремния. Слой обмазки, оставшийся на аноде, приводит к увеличению выхода шлама на стадии электролиза, а также к усложнению дальнейшего процесса переработки шлама. В связи с этим целью данной работы являлся подбор обмазки, предотвращающей возможность заражения анодов диоксидом кремния. Таким образом, в работе в качестве огнеупорного наполнителя обмазки использовался материал, не содержащий в своем составе шлакообразующих компонентов, - графит. Поскольку графит плохо смачивается водой, возникает проблема создания суспензии с равномерно распределенным по всему объему графитом. В качестве связующего в данной работе использовались водные растворы поливинилового спирта, лигносульфоната, а также мездрового клея. По результатам исследований отмечается образование газовой пористости и неровностей получаемых анодов при использовании в роли связующего водного раствора лигносульфоната и мездрового клея. Кроме того, по результатам исследований отмечается накопление минеральной составляющей в составе огнеупорного наполнителя при использовании водного раствора лигносульфоната. При использовании в качестве связующего мездрового клея отмечается наличие зловонного запаха, а также повышенный расход данного типа связующего. Таким образом, установлено, что оптимальными свойствами для использования в качестве огнеупорной краски обладает комбинация «поливиниловый спирт - графит». В целях оптимизации технологических параметров использования связующего и огнеупорного наполнителя проведены исследования седиментационной устойчивости, а также кроющей способности рекомендуемой антипригарной краски.
Анод, антипригарная краска, графит, изложница, литье, медь, огнеупорный наполнитель, поливиниловый спирт, пригар, противопригарное покрытие, розлив, связующее
Короткий адрес: https://sciup.org/147241796
IDR: 147241796 | DOI: 10.14529/met230302
Текст научной статьи Исследование перспективных составов для отливки медных анодов
В настоящее время при розливе медных анодов МЗ используется обмазка на основе SiO2. Материал обмазки частично сохраняется на анодах и впоследствии переходит в шлам электролитных ванн. Диоксид кремния не только увеличивает объем шлама, но и существенно осложняет технологию его переработки. Целью данной работы является поиск антипригарной обмазки, не коллектирующей-ся впоследствии в шламе электролизных ванн ЦЭМ МЗ либо удаляемой из шлама при промывке или на головных операциях (обжиг – выщелачивание) при переработке в МЦ МЗ, и разработка технологии розлива медных анодов МЗ, исключающей вероятность заражения отливок SiO 2 и CaO.
Перед стартом экспериментальных исследований был проведен анализ научно-тех- нической литературы по опыту использования различных противопригарных покрытий при литье медных изделий. Согласно промышленному опыту медеплавильных производств для предотвращения пригара при отливке медных анодов наибольшее распространение получило использование сульфата бария. Сульфат бария ранее использовался в качестве противопригарного покрытия, но по различным причинам от его использования отказались. Сведений о применении каких-либо других противопригарных покрытий при отливке медных анодов в открытых источниках не обнаружено, поэтому для поиска перспективных вариантов проанализированы публикации, посвященные технологиям литья медных сплавов. На основании анализа научнотехнической литературы установлено, что основными компонентами любого противопри- гарного покрытия являются: огнеупорный наполнитель, предотвращающий пригар отливки к изложнице; связующее, обеспечивающее сплошность покрытия и способность его прочно удерживаться на поверхности изложницы; дисперсионная среда, являющаяся носителем двух первых компонентов. В наибольшей степени задачам исследований удовлетворяют противопригарные покрытия и краски, в которых роль огнеупорного наполнителя выполняют углеродистые материалы [1–10].
Материалы, используемые в исследовании, и методика проведения эксперимента
Для проведения исследований была изготовлена изложница из анодной меди (рис. 1). Габариты изложницы были приняты на основании коэффициентов подобия в сравнении с промышленной изложницей для отливки 2 кг лабораторного анода прямоугольной формы: высота 10 мм, ширина 150 мм, длина 180 мм.
В качестве объекта исследований использовалась черновая медь, По данным химиче- ского анализа содержание примесей в черновой меди следующее, % масс.: 0,325–0,354 Ni; 0,007–0,088 S.
В качестве контрольного образца огнеупорного наполнителя обмазки, используемой в данный момент при отливке анодов МЗ, использовался мертель огнеупорный алюмосиликатный. Химический состав пробы контрольного образца приведен в табл. 1. В качестве углеродистого огнеупорного наполнителя использовался графитовый порошок, полученный при измельчении графитированных электродов производства ОАО «Энергопром – Челябинский электродный завод», выпускаемых согласно ТУ 1911-109 -52-2010.
В качестве связующих веществ использовались водные растворы поливинилового спирта (ПВС) PVA 088-50 производства Sinopec Sichuan Vinylon Works (Китай), лигносульфоната технического марки (ЛСТ) А ОАО «Кондопога», мездровый клей (табл. 2). Водные растворы данных материалов одновременно выполняли роль связующих веществ и дисперсионной среды. Выбор данных
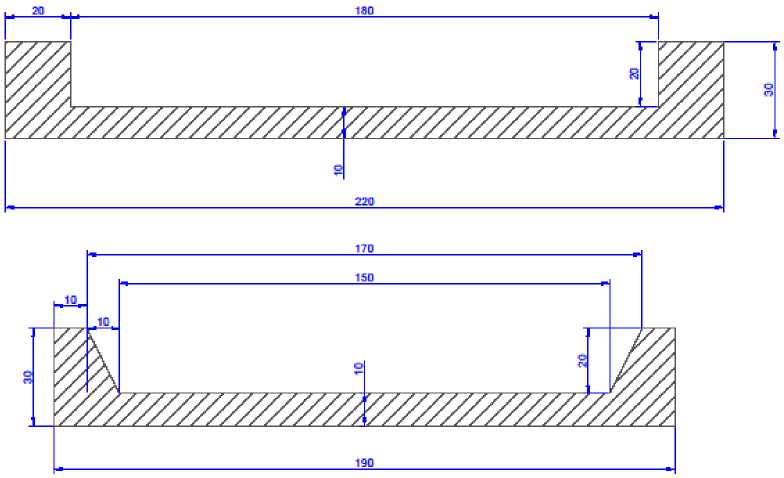
Рис. 1. Схема лабораторной изложницы
Fig. 1. Laboratory mold diagram
Таблица 1
Table 1
Содержание основных компонентов в огнеупорных наполнителях
Content of main components in refractory fillers
Наполнитель |
Содержание, % масс. |
||||||||
Fe |
SiO 2 |
CaO |
Al2O3 |
MgO |
Na 2 O |
C |
S |
п.п.п. |
|
Мертель |
1,28–1,34 |
43,4–46,3 |
0,245–0,262 |
35,0–35,6 |
0,39–0,41 |
0,31–0,34 |
0,250 |
2,65–2,69 |
|
Графит |
0,35 |
0,077 |
0,26 |
0,036 |
< 0,1 |
95,3 |
0,38 |
Таблица 2
Содержание основных компонентов в связующих материалах в твердом виде
Table 2
Content of main components in binding materials in solid form
Исследования проводились на базе индукционной печи – ТГИЛ 6.799. С целью предотвращения окисления меди кислородом воздуха плавку проводили в графитовых тиглях, а медь загружали порционно при достижении в реакционном пространстве температуры ~ 1100 °С. Загрузка очередной порции меди производилась только после полного проплавления ранее загруженной. Одновременно с началом плавления подготовленной навески меди изложница помещалась на нагревательную плитку, после чего включался разогрев плитки. Предварительно положение изложницы выравнивалось по уровню. При достижении температуры изложницы в диапазоне 100–200 °С на ее поверхность наносилась противопригарная обмазка. Использовались различные способы нанесения противопригарного покрытия: полив, распыление, обмазка кистью, копчение. После нанесения краски изложница разогревалась до температуры ~ 400 °С, что имитировало состояние изложницы при непрерывной работе карусельной машины. Температура расплава меди во время розлива составляла 1100–1130 °С. С целью поддержания на постоянном уровне расстояния между краем тигля, из которого производился розлив расплава меди, и поверхностью изложницы была изготовлена специальная упорная конструкция для металлургических щипцов. Расстояние между краем тигля и поверхностью изложницы во всех проведенных экспериментах составляло 20–21 см.
Результаты исследований и их обсуждение
Изначально оценивалась эффективность использования в качестве противопригарной обмазки контрольного образца мертеля огнеупорного, использованного в виде водной суспензии. Использовалось два способа нане- сения обмазки на основе мертеля на изложницу – полив и окрашивание кистью. Установлено, что возникновение пригара лимитируется расходом мертеля. При повышенных расходах мертеля – более 0,4 кг/м2 – удается получить аноды без пригара к изложнице. При этом получаемые аноды характеризуются низким качеством, присутствует значительное количество следов газовой пористости и наличие включений огнеупорного наполнителя (области, выделенные красным) (рис. 2).
При снижении расхода мертеля 0,4 кг/м2 происходит пригар анода к изложнице, при этом способ нанесения огнеупорного покрытия не влияет (рис. 3).
Основной причиной возникновения пригара является размытие струей расплава меди противопригарного покрытия и тела изложницы вследствие низкой степени адгезии противопригарного покрытия к изложнице. Размытие тела изложницы сопровождается образованием каверн на ее поверхности и последующим совместным затвердеванием размытой области и анода. Образующий пригар следует отнести к термическому типу.
Далее выполнена сравнительная оценка использования противопригарных красок, полученных путем смешения водных растворов различных типов связующих веществ в комбинации с графитом.
Необходимо отметить, что чаще всего товарной формой технического лигносульфоната является 50%-ный водный раствор. Растворы ПВС и мездрового клея необходимо предварительно готовить. При этом приготовление мездрового клея имеет определенные сложности. Для получения концентрированного раствора, обладающего достаточными клеящими свойствами, необходимо предварительно замочить мездровый клей и оставить набухать на 12–24 ч, после чего разваривать его при температуре 60–70 °С на «водяной бане». Характеристики используемых связующих веществ приведены в табл. 3. Отношение между раствором связующего
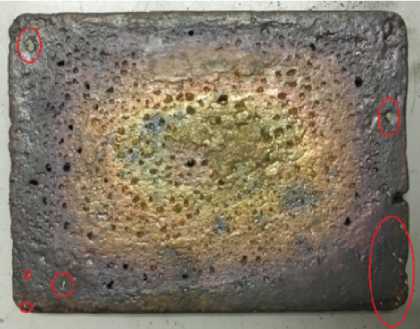
Рис. 2. Лабораторный анод, полученный при нанесении мертеля окрашиванием кистью
Fig. 2. Laboratory anode obtained by applying mortar with a brush
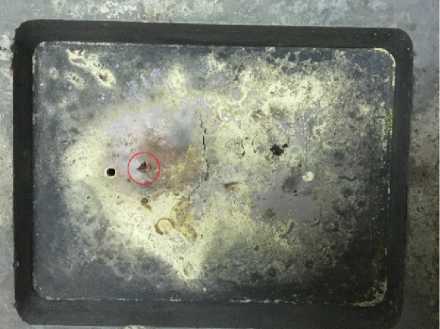
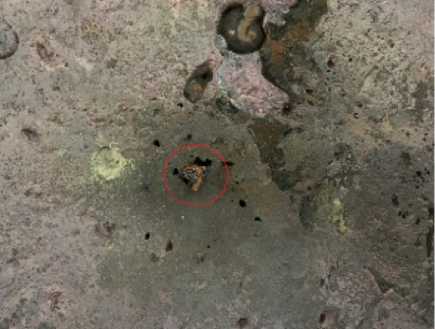
а) b)
Рис. 3. Общий вид изложницы (а) и анода (b)
Fig. 3. General view of the mold (a) and anode (b)
Таблица 3
Технологические свойства растворов связующих веществ
Table 3
Technological properties of binder solutions
Полученные противопригарные краски наносились на поверхность изложницы путем окрашивания кистью. При использовании в качестве связующего вещества противопригарной краски мездрового клея и огнеупорного наполнителя графита не происходит пригара анода к изложнице. Удельный расход графита в проведенных опытах составлял 0,242–0,311 кг/м2, мездрового клея – 0,073–0,093 кг/м2. При этом на поверхности анодов диагностируется наличие газовой пористости (рис. 4а) и неровностей поверхности (рис. 4b).
Также необходимо отметить любопытную особенность. Через 5 сут после изготовления противопригарная краска на основе мездрового клея покрылась плесенью, что несомненно оказывает влияние на ее эксплуатационные качества.
Применение противопригарной краски «лигносульфонат – графит» не приводит к пригару отливки к изложнице. Удельный расход графита в проведенных опытах составлял 0,213–0,220 кг/м2, лигносульфоната – 0,213–0,220 кг/м2. На донной поверхности анода фиксируется наличие газовой пористости и неровностей, кроме того, образуются наплывы в результате вскипания расплава при розливе и охлаждении анода (рис. 5). Вскипание расплава связано с деструкцией и удалением летучих органических соединений, входящих в состав лигносульфоната. Так, по результатам исследований образца лигносульфоната методами ДТА и ТГА с использованием комплексной установки для проведения дифференциально-термического и термогра- виметрического анализов SETSYS evolution TG-DSC/DTA 1750 установлено, что удаление летучих соединений протекает в два этапа: 249–555 °С – последовательное протекание реакций начального и основного температурного разложения, в том числе удаление кристаллической связанной влаги, и 570–848 °С – деструкция с образованием углеродсодержащего остатка.
Также необходимо отметить, что на поверхности анода после его извлечения из изложницы остаются следы огнеупорного наполнителя, которые не удаляются при закалке анода в воду и будут оказывать влияние негативное влияние на операционную эффективность последующих переделов. Для удаления следов огнеупорного наполнителя
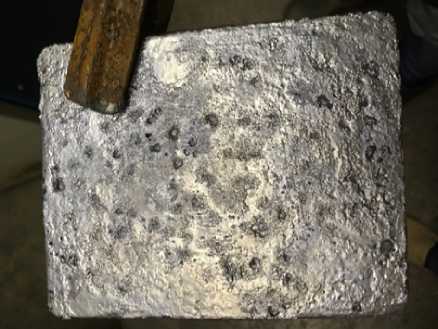
а)
Рис. 4. Общий вид анодов, отлитых при использовании огнеупорного покрытия «мездровый клей – графит»
Fig. 4. General view of anodes cast using a fire-resistant coating of hide glue – graphite
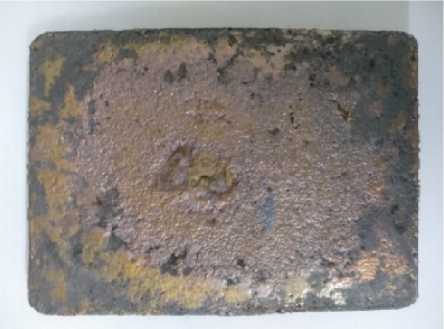
b)
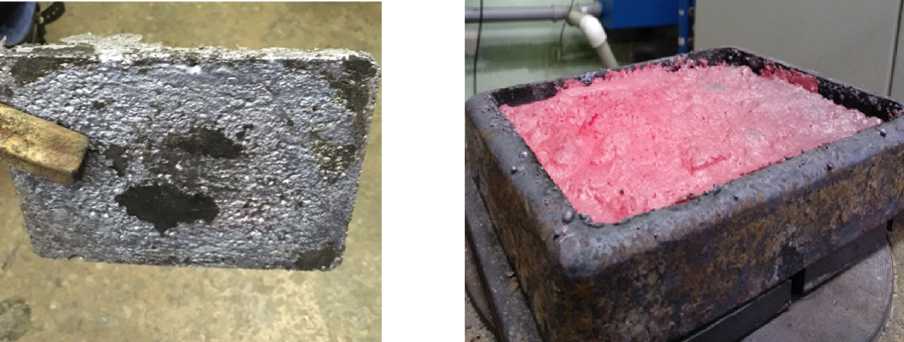
а)
b)
Рис. 5. Вид анода (а) и изложницы (b) при застывании отливки при использовании огнеупорного покрытия «лигносульфонат – графит»
Fig. 5. View of the anode (a) and mold when the casting solidifies, using a refractory coating of lignosulfonate – graphite
треб у е тс я п ри ме н е н и е ме ха н и че ск и х способов очистки.
Испол ьзован ие п ротив оп ри га рн ой к р а с ки «поливиниловый спирт – г ра фи т» п озв оляе т доб и в а тьс я на и б ол е е ро в н ой и гла дк ой поверхности без значительных д е фект о в (рис. 6). На п оверхн ос ти а н ода на б люд а е т с я н е зн а ч ительн ое н али п а н и е гр а фита . У д е льный расход г ра фи т а в п ров е д е н н ы х оп ыта х с о с та в лял 0,174–0,267 кг/м2, поли в ин и л ового с п ирт а – 0,034–0,054 кг/м2.
После п ров ед е н и я и сс л е д ов а н и й были о т обра н ы п ро б ы огне у п орн ого н а п олн и теля, о с та ющ е г ос я н а п ов е рхн ос ти и зложн и ц ы п осле розли в а п ри и с п ол ьзов а н и и различных св я зу ю щ и х вещ е с тв . Р е зу льта ты п ри в е д е н ы в таб л. 4, д ля с р а в н е н и я в н е й п ри в е д е н с ос тав и сход н ого графи та , и с п о льзу е мого в к а че с тв е огнеупорного наполнителя.
Первое, что обращает на себя внимание, – это состав огнеупорного наполнителя после проведения опытов при использовании ЛСТ. Проба была отобрана после проведения единичного опыта. В составе огнеупорного наполнителя в несколько раз увеличивается со- держание минеральной составляющей: диоксида кремния и оксида магния – в 2 раза, оксида кальция – более чем 3 раза, а оксида натрия – более чем в 46 раз. Содержание серы увеличивается в 5 раз, а содержание углерода снижается на ~ 20 %. Учитывая, что данная проба была отобрана после проведения одного опыта, то становится очевидным, что в условиях непрерывного производства будет происходить накопление золы лигносульфоната, которое будет носить негативный характер на следующих стадиях производства: электролиз, переработка медных шламов.
Проба огнеупорного наполнителя при использовании ПВС была отобрана после проведения 2 опытов. Отмечается незначительный рост всех примесных составляющих и незначительное снижение содержания углерода – ~ 5,5 %. Полученные данные объясняются низкой зольностью поливинилового спирта, которая не превышает 0,5 %.
Проба огнеупорного наполнителя при использовании мездрового клея отобрана после проведения единичного опыта. Установлено,
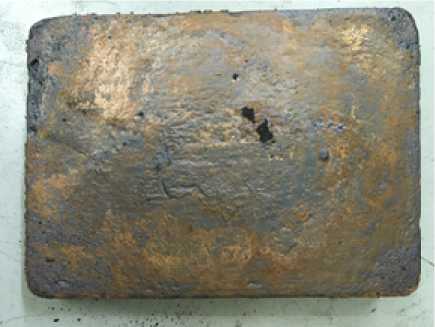
а)
Рис. 6. Общий вид анодов, отлитых при использовании огнеупорного покрытия «ПВС – графит» Fig. 6. General view of anodes cast using a refractory PVA – graphite coating
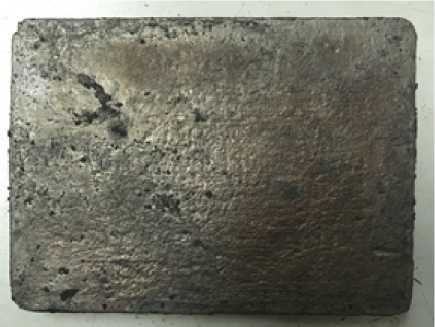
b)
Таблица 4
Состав огнеупорного наполнителя, остающегося после розлива на поверхности изложницы
Table 4
Composition of the refractory filler remaining on the surface of the mold after filling
Окончательное решение по выбору наиболее эффективного состава антипригарной краски принимали на основании оценки адгезионных свойств покрытия (табл. 5). Адгезионные свойства красок определяли способом определения устойчивости к истиранию краски. Исследование устойчивости к истиранию красок проводили по методике, приведенной в ГОСТ 10772–78.
Установлено, что краски, приготовленные с использованием в качестве связующего компонента ЛСТ и мездрового клея, обладают более низкими адгезионными свойствами, чем краска, полученная при использовании в качестве связующего 10%-ного водного раствора ПВС.
Таким образом, на основании сравнительного анализа наибольшей эффективностью обладает противопригарное покрытие на основе водного раствора поливинилового спирта и графита. Дальнейшие исследования были направлены на рационализацию технологических параметров использования краски: состав, способ нанесения, минимальный расход, предотвращающий пригар.
Выбор рационального состава краски проводили на основании исследования сиде-ментационной устойчивости, кроющей способности и сопротивления истиранию. При этом варьировали крупность графита и концентрацию раствора поливинилового спирта.
Определение седиментационной устойчивости производили по методике, приведенной в ГОСТ 10772–78, с использованием 10%-ного раствора ПВС. Результаты исследований седиментационной устойчивости представлены в табл. 6.
Как видно из приведенных в табл. 6 данных, наивысшая седиментационная устойчивость наблюдается при использовании наиболее тонкоизмельченного графита, крупность менее 40 мкм. Седиментационная устойчивость ухудшается при увеличении крупности графита, что связано с увеличением скорости оседания частиц в связи с ростом массы единичной частицы. Следует отметить, что в литературных источниках [1, 14, 15] отмечается, что поливиниловый спирт может быть использован в качестве стабилизатора для повышения седиментационной устойчивости краски.
Исследование кроющей способности антипригарной краски проводили двумя способами. Целью первого способа было определение влияния крупности частиц графита на кроющую способность краски. Исследования
Таблица 5
Таблица 6
Результаты исследования устойчивости к истиранию антипригарных красок
Table 5
Results of a study of abrasion resistance of non-stick paints
Тип связующего |
Толщина пластины, мм |
Толщина пластины после нанесения краски, мм |
Масса материала, пошедшего на истирание, кг |
Устойчивость к истиранию, кг/мм |
ПВС |
2,94 |
3,09 |
1,26150 |
8,410 |
ЛСТ |
2,94 |
3,11 |
0,79475 |
4,675 |
Мездровый клей |
2,94 |
3,05 |
1,19673 |
5,984 |
Седиментационная устойчивость суспензий поливинилового спирта и графита
Table 6
Sedimentation stability of suspensions of polyvinyl alcohol and graphite
Целью второго способа был подбор рационального соотношения между компонентами краски и концентрации раствора поливинилового спирта. При проведении данного этапа исследовании использовалась фракция графита крупностью менее 180 мкм. Краска различного состава наносилась на медную пластину (рис. 8а). Оценивалось количество краски и ее компонентов, необходимое для создания равномерного покрытия на поверхности пластины (рис. 8b). Площадь пластины составляет 0,034 м2. Кроме того, на качественном уровне оценивалось агрегатное состояние краски. Результаты приведены в табл. 7.
Как видно из данных табл. 7, при снижении концетрации поливинилового спирта расход краски, необходимый для создания равномерного покрытия на поверхности пластины, снижается. В первую очередь это связано со снижением вязкости раствора ПВС по мере его разбавления. Расход графита снижается при увеличении соотношения Ж к Т, что также
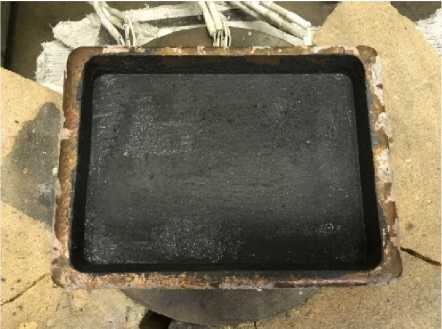
а)
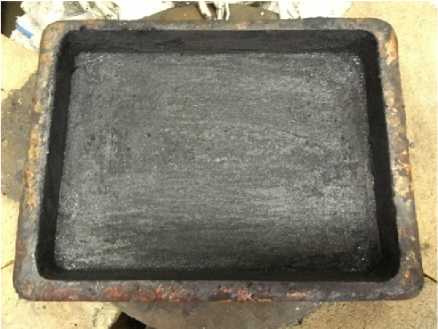
b)
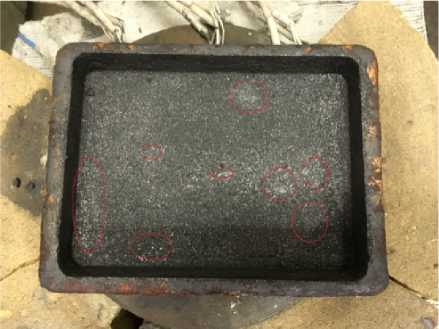
c)
Рис. 7. Изложница, покрытая противопригарной краской «ПВС – графит» с различной крупностью графита, мкм: а) –40; b) –180+40; c) –250+180; d) –450+315 Fig. 7. Mold coated with non-stick PVA – graphite paint, with different graphite sizes, µ m: а) –40; b) –180+40; c) –250+180; d) –450+315
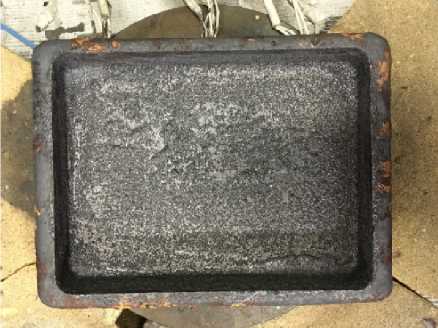
d)
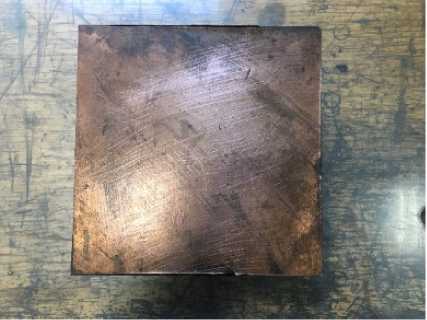
а)
Рис. 8. Внешний вид медной пластины, на которую наносилась краска различных составов Fig. 8. External copper plate on which paint of various compositions was applied
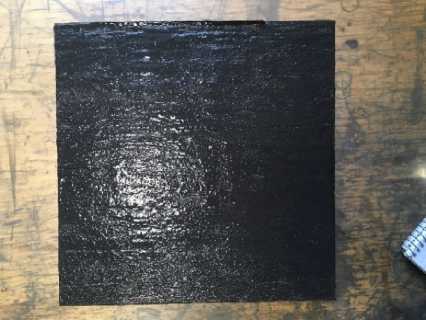
b)
Таблица 7
Результаты оценки кроющей способности краски «ПВС – графит» разной консистенции
Table 7
Results of assessing the covering power of PVA – graphite paints of different consistencies
Минимальный расход краски, обеспечивающий равномерное покрытие поверхности пластины, наблюдается при использовании 5%-ного водного раствора ПВС при соотношении Ж:Т = 2 : 1.
Результаты исследования устойчивости к истиранию антипригарной краски на основе поливинилового спирта и графита приведены в табл. 8.
Как видно из полученных результатов, устойчивость к истиранию возрастает при увеличении концентрации поливинилового спирта в антипригарной краске. Это связано с тем, что, чем выше концентрация поливинилового спирта, тем толще слой краски, наносимой на пластину. Вместе с тем при увеличении концентрации поливинилового спирта в краске возрастает его роль в качестве связующего. Дополнительно в целях понимания адгезионных свойств краски на основе ПВС и выбора рациональной концентрации ПВС аналогичные исследования были проведены с антипригарным покрытием текущего производства. Устойчивость к истиранию краски текущего производства не превышает 0,55 кг/мм,
Таблица 8
Результаты исследования устойчивости к истиранию антипригарной краски на основе поливинилового спирта и графита
Table 8
Results of a study of abrasion resistance of non-stick paint based on polyvinyl alcohol and graphite
Концентрация раствора ПВС, % |
Толщина пластины, мм |
Толщина пластины после нанесения краски, мм |
Масса материала, пошедшего на истирание, кг |
Устойчивость к истиранию, кг/мм |
10 |
2,94 |
3,09 |
1,2615 |
8,410 |
7,5 |
2,94 |
3,06 |
0,87847 |
7,320 |
5 |
2,94 |
3,05 |
0,70087 |
6,372 |
Таблица 9
Результаты исследований
Table 9
Research results
На следующем этапе исследований производили отработку способа нанесения противопригарного покрытия на поверхность изложницы и определение минимального расхода краски, не приводящего к пригару. Нанесение краски осуществлялось различными способами. Сводные результаты исследований приведены в табл. 9.
Установлено, что наиболее технологичным способом нанесения противопригарной краски при розливе медных анодов является распыление. Нанесение краски с помощью квача и кистей различных размеров в условиях непрерывного производства является трудоемкой работой и требует значительного количества ручного труда. Нанесение краски поливом может привести к образованию на поверхности анодов приплывов, что приведет к их выбраковке. В это же время растушевка слоя противопригарной краски, нанесенной поливом, позволяет создать гладкий равномерной слой покрытия на поверхности изложницы, без существенных неровностей, которые наблюдаются без растушевки. Данный комбинированный способ может быть использован при розливе медных анодов, однако в сравнении с нанесением краски распылением характеризуется большими затратами ручного труда.
Для предотвращения пригара анода к изложнице расход противопригарной краски при первичном нанесении должен обеспечивать расход графита не менее 0,174 кг/м2. Повторное нанесение противопригарной краски должно обеспечивать поддержание данного параметра не ниже установленного значения.
Заключение
Проведены исследования по поиску перспективных составов противопригарных красок, предотвращающих вероятность заражения анодов SiO2 и CaO, и оценке их технологических свойств. По результатам исследований установлено:
– использование технического лигносульфоната в качестве связующего компонента противопригарной краски не приемлемо ввиду возможности накопления минеральной составляющей в составе огнеупорного наполнителя, заражения ею анодов с последующим переходом в шлам электролиза нежелательных компонентов и возникновения газовой пористости на поверхности анода, что является одним из видов дефекта;
– использование в качестве связующего компонента противопригарной краски мездрового клея имеет определенные недостатки: непереносимый зловонный тошнотворный запах, сложности в приготовлении концентрированного раствора, обладающего достаточными клеящими свойствами, повышенный расход огнеупорного наполнителя, связанный с потерей мездровым клеем клеящих свойств при нанесении на горячую изложницу, возможность образования газовой пористости в отливках, что является одним из видов дефекта. По совокупности этих причин мездровый клей не рекомендуется использовать в качестве связующего компонента противопригарной краски;
– использование в качестве связующего компонента противопригарной краски поливинилового спирта обеспечивает наименьшей расход огнеупорного наполнителя, не приводит к образованию газовой пористости анодов и накоплению минеральной составляющей в составе огнеупорного наполнителя, обеспечивает наибольшую силу адгезии краски к поверхности изложницы, характеризуется наименьшим расходом связующего вещества в пересчете на активный компонент.
Таким образом, наиболее целесообразно использовать в качестве связующего вещества при приготовлении противопригарной краски поливиниловый спирт. Рекомендуемый состав противопригарной краски:
-
– концентрация раствора поливиниловго спирта – 5 %;
-
– крупность огнеупорного наполнителя графита – не более 180 мкм;
-
– отношение Ж:Т – 2 : 1.
Основные технологические свойства краски:
-
– вязкость – 98 сПз;
-
– плотность – 1,28 г/см3.
Для предотвращения пригара анода к изложнице расход противопригарной краски при первичном нанесении должен обеспечивать расход графита не менее 0,174 кг/м2. Повторное нанесение противопригарной краски должно обеспечивать поддержание данного параметра не ниже установленного значения.
Список литературы Исследование перспективных составов для отливки медных анодов
- Голотенков О.Н. Формовочные материалы: учеб. пособие. Пенза: Изд-во Пенз. гос. ун-та, 2004. 164 с.
- Голотенков О.Н. Формовочные материалы: учеб. пособие. Пенза: Изд-во Пенз. гос. ун-та, 2009. 166 с.
- Кукуй Д.М., Андрианов Н.В. Теория и технология литейного производства. Формовочные материалы и смеси. Минск: БНТУ, 2005. 361 с.
- Боровский Ю.Ф., Шацких М.И. Формовочные и стержневые смеси. Л.: Машиностроение, 1980. 86 с.
- Кузнецов Р.В., Мартынов К.В. Водные противопригарные покрытия с мелкодисперсными наполнителями // Литейное производство. 2015. № 2. С. 25–28.
- Черкасов Л.М., Павленко И.И. Пригар на изложницах из доменного чугуна // Литейное производство. 1967. № 2. С. 37–38.
- Производство отливок из сплавов цветных металлов / А.В. Курдюмов, В.Д. Белов, М.В. Пискунов и др. М.: Изд. Дом МИСиС, 2011. 615 с.
- Производство отливок из сплавов цветных металлов / А.В. Курдюмов, М.В. Пискунов, В.М. Чурсин, Е.Л. Бибиков. М.: Металлургия, 1986. 416 с.
- Липницкий А.М., Морозов И.В., Яценко А.А. Технология цветного литья. Л.: Машино-строение, 1986. 224 с.
- Производство литых заготовок из деформируемых алюминиевых и медных сплавов / Р.К. Мысик, Ю.Н. Логинов, А.В. Сулицин, С.В. Брусницын. Екатеринбург: УрФУ, 2011. 414 с.
- Озеров С.С. Разработка технологий брикетирования сульфидного медно-никелевого концентрата и силикатного флюса: дис. … канд. техн. наук: 05.16.02. СПб., 2017. 232 с.
- Оценка эффективности использования поливиниловых спиртов в качестве связующего при брикетировании флотационного медно-никелевого концентрата / С.С. Озеров, А.Б. Портов, Л.Б. Цымбулов, А.К. Машьянов // Цветные металлы. 2016. № 8. С. 39–45.
- Оценка эффективности использования технических лигносульфонатов различных марок в качестве связующего при брикетировании флотационного медно-никелевого концентрата / С.С. Озеров, А.Б. Портов, Л.Б. Цымбулов, А.К. Машьянов // Цветные металлы. 2017. № 3. С. 33–39. DOI: 10.17580/tsm.2016.08.05
- Буров А.В. Литье слитков меди и медных сплавов. М.: Металлургия, 1972. 176 с.
- Королев С.П., Шешко А.Г., Михайловская Т.В. Кокильные краски для литья цветных и черных сплавов // Литейное производство. 2008. № 11. С. 30–31.