Исследование поведения водорода в алюминиевом сплаве при производстве мелкой чушки на алюминиевом заводе ОК Русал
Автор: Куликов Б.П., Беляев С.В., Фролов В.Ф., Губанов И.Ю., Лесив Е.М., Юрьев П.О., Партыко Е.Г.
Журнал: Журнал Сибирского федерального университета. Серия: Техника и технологии @technologies-sfu
Статья в выпуске: 4 т.12, 2019 года.
Бесплатный доступ
В статье приведены результаты исследований динамики насыщения алюминия и его сплавов водородом в технологической схеме от алюминиевого электролизера до литейного конвейера в условиях Саяногорского алюминиевого завода ОК РУСАЛ. Показано, что одним из основных источников насыщения расплава алюминия водородом является его взаимодействие с влагой воздуха при открытых переливах металла в процессе его движения от электролизера до литейного конвейера. По результатам обследования предложены технические решения, направленные на снижение концентрации водорода в расплаве, которые составят предмет дальнейших исследований.
Насыщение водородом расплава алюминия, технология производства мелкой чушки, отбор проб металла, литейное оборудование и оснастка
Короткий адрес: https://sciup.org/146281203
IDR: 146281203 | DOI: 10.17516/1999-494X-0074
Текст научной статьи Исследование поведения водорода в алюминиевом сплаве при производстве мелкой чушки на алюминиевом заводе ОК Русал
В настоящее время одним из главных направлений развития алюминиевой отрасли стало увеличение в общей структуре производства металлопродукции высокого уровня обработки. В результате самой востребованной продукцией на мировом рынке потребления алюминия являются алюминиевые сплавы. Лидер российской алюминиевой отрасли ОК РУСАЛ активно развивает литейное производство и планирует довести долю сплавов в общем объеме производства до 75 %. Для дальнейшего повышения качества выпускаемой продукции необходимо снизить содержание водорода в ней до 0,1 см3/100 г Al. Достижение поставленных целей требует совершенствования действующего литейного производства на основе разработки и внедрения новых инновационных технических и технологических решений.
Водород является одной из наиболее значимых газовых примесей, оказывающей отрицательное влияние на технологические свойства продукции из алюминия и его сплавов [1]. Основные источники поступления водорода в алюминий - атмосферная влага, шихтовые материалы, флюсы, плавильные инструменты. Растворенный в затвердевшем металле водород способствует образованию газовой и газоусадочной пористости, которая возрастает с увеличением концентрации содержания водорода. Все это негативно влияет на физико-механические и эксплуатационные характеристики алюминия и его сплавов. Величина газовой пористости алюминиевых сплавов определяется степенью пересыщения твердого раствора водородом, пропорциональна разности концентраций водорода в жидком и твердом металле и возрастает с – 399 – увеличением скорости охлаждения при кристаллизации. Следует отметить, что чем больше соотношение растворимости водорода в жидком и твердом состоянии конкретного металла или сплава, тем больше будет у него пористость. У алюминия это соотношение составляет ~ 14, что на порядок больше, чем у других металлов.
Методика проведения исследований
Учитывая актуальность вопроса, связанного с минимизацией насыщения жидкого металла водородом, в настоящей работе провели количественную оценку изменения содержания водорода в жидком металле при его движении по технологической цепочке от алюминиевого электролизера до товарной продукции из алюминиево-кремниевых сплавов.
Работа выполнена на Саяногорском алюминиевом заводе ОК РУСАЛ. Аппаратурнотехнологическая схема транспортировки, подготовки и разливки литейного сплава АlSi7Mg при производстве из него мелкой чушки включает следующие основные операции:
-
1. Заливка алюминия-сырца из электролизеров в вакуум-транспортные ковши со съемной крышкой.
-
2. Транспортировка расплава в вакуум-транспортных ковшах из корпусов электролиза на участок удаления шлака с поверхности алюминия.
-
3. Удаление шлака с поверхности алюминия в ковшах, отбор пробы металла на спектральный анализ.
-
4. Транспортировка алюминия в литейный цех, отстой в вакуум-транспортных ковшах в течение 20÷40 мин перед заливкой в миксер.
-
5. Заливка металла из вакуум-транспортных ковшей в миксер до его заполнения.
-
6. Введение, плавление и растворение в жидком алюминии твердых промпродуктов производства, легирующих и модифицирующих добавок.
-
7. Обработка металла в миксере рафинирующими и покровными флюсами, удаление шлака с поверхности готового сплава.
-
8. Технологический отстой расплава в миксере, отбор пробы металла на экспресс-анализ, доведение температуры расплава в миксере до температуры разливки.
-
9. Разливка расплава из миксера в мелкую чушку с проведением дегазации и фильтрации жидкого металла.
С учетом используемого на металлургическом заводе литейного оборудования была разработана методика и схема отбора проб металла для определения содержания водорода. Принципиальная схема обследования приведена на рис. 1 и 2 с указанием точек отбора проб металла. Для маркировки проб использовали буквенное и цифровое обозначение: Э – электролизеры; К – ковши; М – миксеры; Т – металлотракты.
Пробы отливали в медную изложницу в соответствии с действующими на заводе инструкциями: в корпусах электролиза алюминия, на участке снятия шлака с ковшей и после отстоя металла в ковше в литейном цехе – по ГОСТ Р 50965. На рис. 3 показаны фотографии медной изложницы и отливаемых проб. При отборе проб металла фиксировали время, температуру расплава и воздуха, а также технологические параметры, касающиеся подготовки металла в миксерах, модифицирования и рафинирования сплавов при литье товарной продукции.
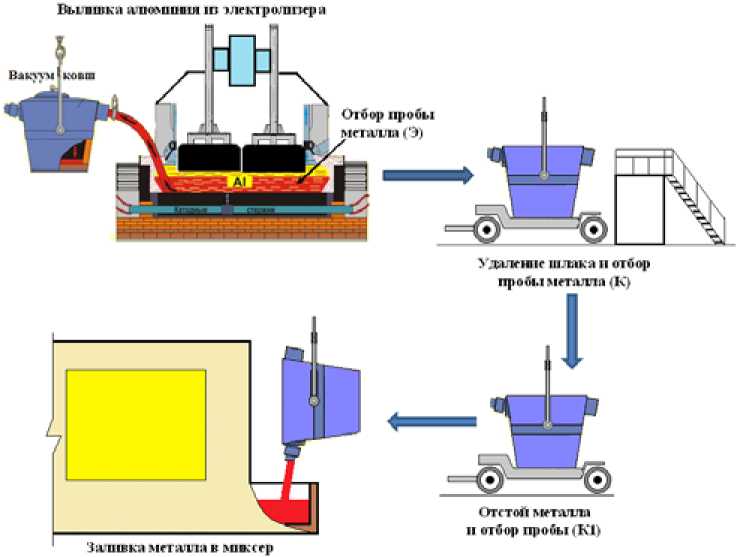
Рис. 1. Схема выливки, транспортировки, заливки расплава алюминия в миксер и отбора проб металла для анализа на содержание водорода
Fig. 1. Scheme of pouring out, transporting, pouring aluminum melt into a mixer and taking metal samples for hydrogen content analysis
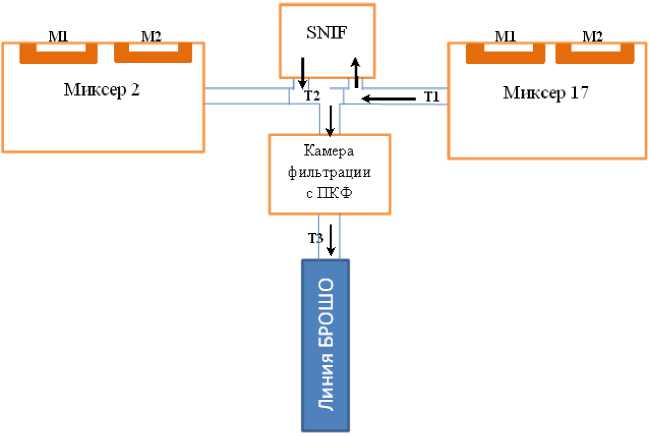
Рис. 2. Схема литейной установки производства мелкой чушки из литейного сплава АlSi7Mg с использованием литейной оснастки «Brochot»: буквами и цифрами на схеме указаны места отбора проб металла, стрелками – направление движения металла
Fig. 2. Scheme of the cast installation for production of small ingots from the AlSi7Mg casting alloy using the Brochot pattern equipment: letters and figures in the diagram indicate locations of metal sampling, and the arrows indicate direction of metal movement
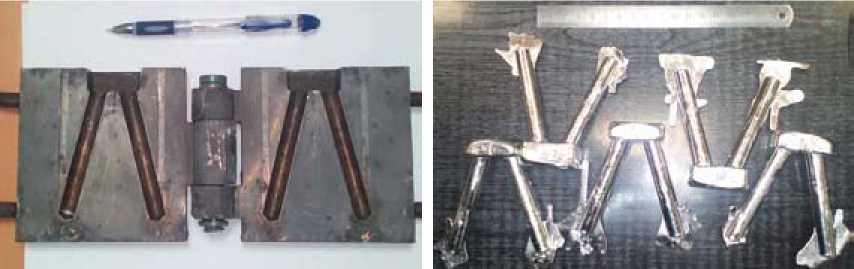
Рис. 3. Изложница и пробы металла для анализа на водород
Fig. 3. Mould and samples of metal for hydrogen analysis analysis
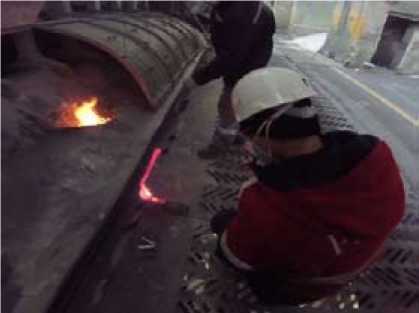
Рис. 4. Отбор проб алюминия из электролизеров
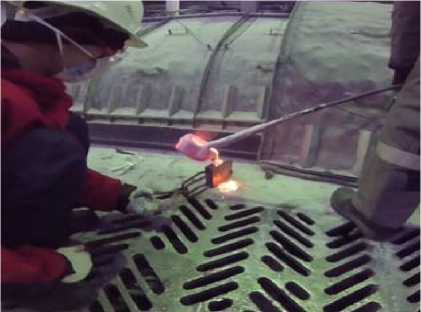
Fig. 4. Sampling of aluminum from electrolyzers
На рис. 4 приведены фотографии отбора проб алюминия из электролизеров в корпусах электролиза, на рис. 5 – отбор проб на участке удаления шлака с поверхности металла в соединительном коридоре между корпусами электролиза и литейным цехом.
Литейные алюминиево-кремниевые сплавы АlSi7Mg готовили и разливали из электрических отражательных миксеров емкостью по 30 т металла. Пробы сплава из миксеров отбирали из каждой форкамеры (рис. 1) сразу после заполнения миксера алюминием и после приготовления сплава перед началом его разливки.
Литейный сплав АlSi7Mg разливали в мелкую чушку на линии «Brochot» с предварительной очисткой сплава в две стадии: продувкой инертным газом-аргоном в двухроторной установке внепечного рафинирования SNIF P-140UHB и фильтрацией металла через пенокерамический фильтр (ПКФ) с пористостью 40 ppi.
Технические характеристики установки рафинирования SNIF P-140UHB и трубчатого ме-таллофильтра фирмы «Mitsui» приведены в табл. 1, 2.
По результатам обследования отобрано 73 пробы алюминия и его сплавов на различных участках аппаратурно-технологической схемы. Эти пробы готовили в соответствии – 402 –
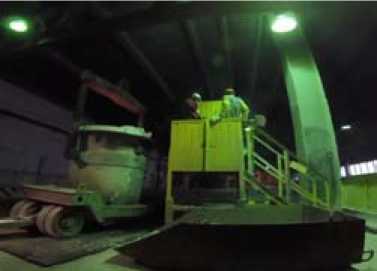
Рис. 5. Отбор проб алюминия на участке удаления шлака из ковшей
Fig. 5. Sampling of aluminum in the area of removal of slag from ladles
Таблица 1. Технические характеристики установки внепечного рафинирования SNIF P-140UHB
Table 1. Technical characteristics of the out-of-furnace refining plant SNIF P-140UHB
Наименование показателя, размерность |
Значение |
Вместимость камеры, т жидкого металла |
1,76 |
Номинальная мощность, кВт |
45 |
Электрическое напряжение, В |
380 |
Число нагревателей, шт. |
6 |
Максимальная температура воздуха в блоке с нагревателями, °C |
800 |
Максимальная температура жидкого металла, °C |
760 |
Производительность установки, т/ч |
63,5 |
Количество роторов, шт. |
2 |
Скорость вращения роторов: - режим холостого хода, об/мин, - рабочий режим, об/мин |
200±5 450÷500 |
Расход аргона на каждый ротор, нм3/ч |
2,2÷2,5 |
Таблица 2. Техническая характеристика металлофильтра «Mitsui»
Table 2. Technical characteristics of the Mitsui metal filter
В табл. 4 и на графике (рис. 7) приведены результаты анализов по содержанию водорода в расплаве на различных участках аппаратурно-технологической схемы выливки, транспортировки, подготовки и разливки металла на металлургическом заводе.
Анализ полученных результатов
Основные мероприятия по снижению содержания водорода и других неметаллических примесей в алюминии и его сплавах, предусмотренные действующими на заводе нормативными документами, включают:
-
1) отстаивание металла в вакуум-транспортных ковшах перед его заливкой в миксеры;
-
2) обработку металла в миксерах галогенидсодержащими флюсами с последующей выдержкой расплава;
Рис. 6. Анализатор газов «G8 Galileo»
-
Fig. 6. The gas analyzer "G8 Galileo"
Таблица 3. Техническая характеристика газоанализатора «G8 Galileo»
Table 3. Technical characteristics of the gas analyzer "G8 Galileo"
Показатели |
Значение, размерность |
Диапазон измерений содержания Н |
— 0,01-1000 ppm |
Время выполнения анализа |
От 50 с до 60 мин |
Разрешение |
0,01 ppm |
Погрешность |
±0,05 ppm или ±1 % отн. |
Электропитание |
Анализатор 400 В, периферийные устройства 230 В |
Газ-носитель |
Азот, аргон чистота 99,999 %, давление 2 бар |
Сжатый воздух |
Давление 5 бар |
Водяное охлаждение |
4 л/мин |
Габаритные размеры |
700×830×600 мм |
Таблица 4. Изменение концентрации водорода в жидком металле литейного сплава АlSi7Mg
Table 4. Change of the hydrogen concentration in molten metal (cast aluminum alloy AlSi7Mg)
Место отбора проб, количество проб |
Среднее содержание водорода, см3/100 г Al |
Электролизеры (Э) – 16 проб |
0,125 |
Ковши до отстоя (К) – 21 проба |
0,170 |
Ковши после отстоя (К1) – 13 проб |
0,139 |
Миксеры литейный сплав АlSi7Mg |
|
после заливки металла (М) – 4 пробы |
0,22 |
перед разливкой металла (М1) – 4 пробы |
0,173 |
Металлотракты, литейный сплав АlSi7Mg – 15 проб |
|
Т 1 |
0,173 |
Т 2 |
0,153 |
Т 3 |
0,157 |
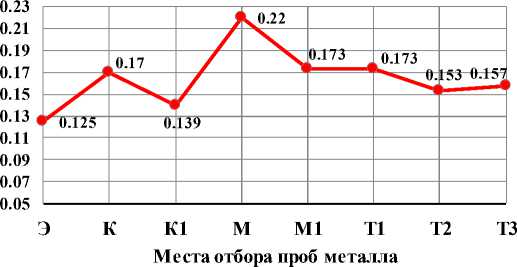
Рис. 7. Изменение концентрации водорода в жидком металле литейного сплава АlSi7Mg: Э – электролизеры; К – ковши до отстоя металла; К1 – ковши после отстоя металла; М – миксеры после заливки металла; М1 – миксеры перед разливкой металла; Т1 – Т3 – точки отбора проб из литейных желобов в соответствии с рис. 2
Fig. 7. Change of the hydrogen concentration in molten metal (cast aluminum alloy AlSi7Mg): Э – electrolyzers; К – ladlebefore metal sludge; K1 – ladle after metal sludge; M – mixers after pouring metal; M1 – mixers before pouring metal; Т1 – Т3 – sampling points from casting troughs in accordance with the Fig. 2
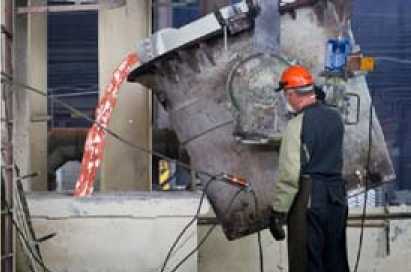
Рис. 8. Заливка алюминия в миксер
Fig. 8. Pouring aluminum into the mixer несмотря на снижение средней температуры металла примерно на 100 °C - до 860 °C. Насыщение алюминия-сырца водородом при наборе металла в ковш обусловлено взаимодействием открытой струи металла с влагой воздуха, а также эжекцией пузырьков влажного воздуха струей переливаемого металла в объем перелитого металла и является следствием открытого перелива алюминия при его выливке.
При последующей выдержке алюминия-сырца в ковшах перед заливкой в миксеры (точка К1, рис. 1) температура металла снижается с 860 до 790 °C, что сопровождается понижением концентрации водорода в металле с 0,17 до 0,139 см3/100 г Al.
Открытый перелив алюминия-сырца из вакуум-транспортных ковшей в миксеры (рис. 8) приводит к насыщению металла водородом вследствие эжекции пузырьков влажного воздуха в объем заливаемого металла.
После заливки алюминия в миксер и загрузки шихтовых материалов (кремния, магния и титана) содержание водорода в сплаве возросло с 0,139 до 0,22 см3/100 г Al. При этом температура металла в миксере снизилась до 740 °C. Известно [2-4], что кремний понижает, а титан и магний повышают растворимость водорода в жидком алюминии. В тройной системе алюминий-кремний-магний растворимость водорода увеличивается благодаря доминирующему влиянию магния. Именно поэтому в залитом в миксер металле после загрузки легирующих добавок скачкообразно увеличивается содержание водорода. В результате последующей обработки металла флюсом и технологической выдержки расплава в миксере концентрация водорода в сплаве на момент начала его разливки уменьшается с 0,22 до 0,173 см3/100 г Al. В пробах сплава, отобранных из металлотракта при отливке мелкой чушки на линии «Brochot» (точки Т1, Т2, Т3, рис. 2), концентрация водорода дополнительно снижается до 0,153^0,157 см3/100 г Al после рафинирования расплава аргоном в установке SNIF P-140UHB и фильтрации через пенокерамический фильтр.
Выводы
В результате проведенных исследований установлена зависимость изменения содержания водорода в расплаве при его движении от электролизера до литейного конвейера. Основная причина насыщения алюминия водородом в технологической цепи от алюминиевого – 406 – электролизера до литейного миксера заключается во взаимодействии жидкого металла с влагой воздуха при открытых переливах металла из электролизера в вакуум-транспортный ковш и из ковша в миксер. Анализ динамики насыщения алюминия и его сплавов водородом проведен при температуре атмосферного воздуха 2 - минус 3 °C. При такой температуре содержание водяного пара в воздухе равно 1^2 г/нм3. Поэтому прирост содержания водорода в металле при открытых переливах составил всего 0,011^0,045 см3/100 г Al. В теплый период года при температуре воздуха 25÷30 °C концентрация водяного пара в нем возрастает в 7-10 раз, что неминуемо приведет к дополнительному насыщению расплава водородом.
В качестве технических решений по снижению экспансии водорода в алюминий рекомендуется использовать закрытые переливы при выливке алюминия-сырца из электролизера вакуум-ковшом со съемным сифоном [5] и при заливке металла из ковша в миксер. Уменьшение содержания водорода в металле, залитом в миксер, сократит расход флюса на рафинирование расплава и время отстоя металла до разливки. Дополнительный эффект от применения закрытых переливов металла будет получен в результате снижения потерь алюминия за счет окисления [6].
Для рафинирования алюминия в вакуум-транспортном ковше рекомендуется совместить отстаивание металла с вакуумной обработкой. Во время отстаивания металла в ковшах последние накрывают крышкой и создают разрежение над поверхностью металла в ковше. Снижение общего давления над расплавом вызывает рост газовых пузырьков, обогащение их растворенным водородом и всплывание этих пузырьков к открытой поверхности расплава. Вместе с водородными пузырьками всплывают и инородные частицы нерастворимых примесей, поры и трещины в которых служили центрами выделения растворенного газа.
Для дополнительного рафинирования алюминия и его сплавов от водорода при разливке металла можно использовать пенокерамические фильтры, содержащие активные фтористые соли, например фториды кальция и магния.
В ходе обследования выявлены недостатки в существующей схеме отбора проб жидкого металла для определения содержания в нем водорода. Необходимо изменить методику отбора пробы: исключить перелив металла из пробоотборной ложки в изложницу и использовать изложницу непосредственно в качестве пробоотборника.
Список литературы Исследование поведения водорода в алюминиевом сплаве при производстве мелкой чушки на алюминиевом заводе ОК Русал
- Булах А.Г., Булах К.Г. Физико-химические свойства минералов и компонентов растворов. Л.: Недра, 1978. 167 с.
- Чернега, Д.Ф. Газы в цветных металлах и сплавах. М.: Металлургия, 1982. 176 с.
- Rundquist V., Manchiraju K., Han Q. Ultrasonic Degassing and processing of molten aluminum, Light Metals, 2015, 943-948 p.
- Добаткин В.И. Газы и окислы в алюминиевых деформируемых сплавах. М.: Металлургия, 1976, 264 с.
- Патент на полезную модель № 42970 U1 Российская Федерация, МПК B22D 41/00, С25С 3/06. -№ 2003129381/02. Вакуумный ковш для выливки жидкого металла, Куликов Б.П., Рагозин Л.В., Железняк В.Е.; заявл. 07.10.2003; опубл. 27.12.2004 Бюл. № 36.
- Куликов Б.П., Рагозин Л.В., Сироткин Д.Н. Балансовое обследование выливки алюминия-сырца, Цветные металлы, 2000, 8, 102-105.