Исследование процесса формообразования поперечного гофра сильфона с минимальной разнотолщинностью
Автор: Антипов Д.В., Шаров А.А., Масленникова А.С.
Журнал: Известия Самарского научного центра Российской академии наук @izvestiya-ssc
Рубрика: Машиностроение и машиноведение
Статья в выпуске: 3 т.25, 2023 года.
Бесплатный доступ
В статье выполнены исследования по определению возможности подтверждения выдвинутой гипотезы о получении более равномерной стенки сильфона в области вершины гофра путем формообразования сильфона эластичной средой двухэтапным способом в разъемной секционной матрице с применением технологии стесненного изгиба. Дано описание областей применения сильфонов, их конструкций, определены наиболее прогрессивные методы изготовления сильфонов и их основной недостаток. Определена цель исследования и поставлены соответствующие задачи, которые необходимо решить. В исследовании применялись аналитические методы исследования и конечно-элементное моделирование. Предложен способ формообразования сильфона и геометрия формообразующей матрицы. Приведена методика расчета параметров технологического процесса для двух этапов формообразования сильфона. Представлены картины относительного изменения толщины гофра сильфона при формообразовании традиционным способом и при формообразовании предложенным способом. Представлены поля распределения эквивалентных напряжений по Мизесу на первом и на втором переходах при формообразовании предлагаемым способом. Проведено сравнение и дана оценка полученных результатов.
Сильфон, технология, формообразование, стесненный изгиб, утонение, конечно-элементное моделирование
Короткий адрес: https://sciup.org/148326926
IDR: 148326926 | DOI: 10.37313/1990-5378-2023-25-3-10-15
Текст научной статьи Исследование процесса формообразования поперечного гофра сильфона с минимальной разнотолщинностью
Металлические сильфоны применяются в промышленности при решении разнообразных технических задач, в том числе сильфоны нашли широкое применение в узлах летательных аппаратов, передающих газ и жидкости под давлением, для осевой компенсации тепловых расширений, а также рабочих и монтажных смещений. В процессе эксплуатации на сильфон действуют многоцикловые деформации сжатия, растяжения, изгиба и различные их комбинации под действием внутреннего или внешнего давления, температуры и механических напряжений, поэтому сильфон должен сохранять прочность и герметичность на протяжении заданного цикла.
По своей конструкции сильфоны могут быть мембранными, цилиндрическими однослойными, цилиндрическими многослойными,
коническими, фасонными, прямоугольными, армированными. Несмотря на все многообразие конструктивных исполнений, наиболее распространены цилиндрические однослойные сильфоны, изготавливаемые из цельнотянутой трубной заготовки.
Основной причиной разрушения сильфонов является износ материала в области вершины гофра, ввиду утонения материала в этой области на этапе изготовления изделия. Актуальность исследования, представленного в настоящей статье, заключается в том, что в связи с усложнением техники, возрастанием сложности решаемых задач, особыми условиями эксплуатации стоит проблема создания надежных изделий типа сильфон.
Существующие методы изготовления сильфонов имеют достаточно высокую производительность, однако на этапе изготовления изделия затруднительно получить равномерную толщину стенки в области вершины гофра. Методы формообразования эластичной и жидкой средой, считающиеся наиболее прогрессивными в области получения гофрированных оболочек с более равномерной толщиной стенки по всей поверхности изделия, способны обеспечить толщину стенки сильфона в области вершины гофра ниже исходной толщины заготовки на 10-30 % в зависимости от высоты гофра.
Учитывая, что известны технологические процессы формообразования листовых деталей, которые позволяют обеспечить набор материала в очаге деформации, где при обычных условиях формообразования образуется утонение материала, выдвинуто предположение, что применение таких технологий в процессе формообразования гофра сильфона способно снизить утонение стенки готового изделия в области вершины гофра.
С целью подтверждения выдвинутого предположения необходимо разработать способ формообразования сильфонов, который позволит снизить утонение в области вершины гофра и решить следующие задачи:
– разработать методику расчета параметров технологического процесса и математическую модель процесса формообразования сильфона с учетом воздействия эластомера;
– провести комплекс теоретических и экспериментальных исследований напряженно-деформированного состояния эластичного пуансона и заготовки методом конечных элементов;
– после реализации теоретических и экспериментальных исследований необходимо дать оценку характеру изменения толщины по всей поверхности изделия и подтвердить или опровергнуть гипотезу о возможности получения изделия с более равномерной толщиной стенки по всей его поверхности;
– в случае подтверждения выдвинутой гипотезы о возможности получения изделия с более равномерной толщиной стенки по всей его поверхности путем применения технологий стесненного изгиба рекомендуется провести натурный эксперимент.
МЕТОДЫ ИССЛЕДОВАНИЯ
Методической базой исследования послужили труды отечественных и зарубежных ученых: Андреева Л.Е., Арышенский Ю.М., Барвинок В.А.
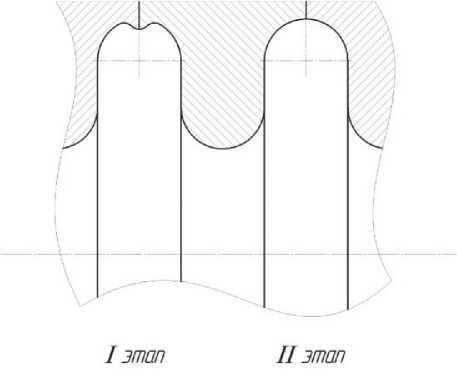
Рис. 1. Профиль разъемной секционной матрицы
[1], Белоусов В.П., Вилканс Д., Гречников Ф.В., Громова Е.Г. [2], Даммак Ф., Ершов В.И., Загай-ный В.К., Исаченков Е.И. [3], Калужский И.И., Катаев Ю.П., Кашелевский Г.И., Кирилин А.Н., Колганов И.М., Комаров А.Д. [4], Коневских В.А, Краковски М., Кузьмин В.А., Ломовской О.В. [5], Моисеев В.К. [6], Новиков А.Л., Плотников А.Н., Проскуряков Г.В., Пышкин В.А., Самохвалов В.П., Тенг Ф., Терехов В.М., Торимс Т., Федотов Ю.В., Феодосьев В.И., Филимонов В.И., Шаров А.А. и др. [7-8]
В рамках исследования применялись аналитические методы исследования и конечно-элементное моделирование.
РЕЗУЛЬТАТЫ И ИХ ОБСУЖДЕНИЯ
В настоящий момент предложен способ изготовления сильфонов методом последовательного формообразования в разъемной секционной матрице с применением технологии стесненного изгиба. Применение предложенного способа позволит уменьшить утонение материала в области вершины гофра за счет формирования гофра в два этапа: с избытком материала (I этап) и последующей его посадкой (II этап). Профиль матрицы представлен на рисунке 1.
Разработана методика расчета параметров технологического процесса для двух этапов формообразования сильфона. Методика расчета разрабатывалась с учетом основных положений, предложенных Е.И. Исаченковым. Приведен вывод формул для определения действительных толщин и требуемых давлений для формообразования гофра сильфона на каждом этапе формообразования:
SoRo(20i +^ + AhJ si ~ i \ . v
(R o + h)(2a + m i + /Г0 ф р)
где si – действительная толщина стенки волны сильфона на первом этапе, устанавливаемая из условия постоянства объема, s0 – толщина заготовки, R0 – радиус проходного сечения оболочки или исходной цилиндрической заготовки, r1 и r2 – радиусы профиля волны гофра на матрице, ∆ h – смещение заготовки в меридиональном направлении при формообразовании одной волны гофра, h – высота гофра после формообразования, a – прямолинейная часть гофра, l гофр – длина гофра сильфона.
2SoRoRl^Aea(2(rl + r2) + Ah)
CL = — ------------------;-------------г X
[ R2 - (R i - r2 ) 2] ( R o + h ) (2a + rni + / гофр )
2a + (к- 2)гг - 2r2 + /Го фр + Ah 2(r i + r2) + Ah
^2(

/
2h 2a + (к - 2)r l - 2r2 + ^ гофр + Ah
Ro + 2(rl + r2) + Ah где qп – давление, требуемое для формообразования гофра на первом этапе R1 – наружный радиус сильфона, после его формообразования, Аεα – параметр аппроксимации, β – коэффициент, учитывающий влияние среднего главного напряжения σ2.
г0а05г
S = ------,
T j a ,
где s – действительная толщина стенки волны сильфона после посадки избытка материала, r0 – радиус волны на конечном этапе посаживания, α 0– угол волны на конечном этапе посаживания, ri – радиус волны на начальном этапе посажи-вания, α i – угол волны на начальном этапе по-саживания.
q =
r o S j a o rtb
■ + n(—-1)1, v « 0 ^ 0
где q – давление, требуемое для формообразования гофра на втором этапе, b – ширина волны, П – модуль упрочнения, σ в – аппроксимированный предел текучести.
В настоящий момент реализован комплекс аналитических исследований и эксперимен- тальных исследований методом конечно-элементного моделирования в программном комплексе «ANSYS».
Экспериментальное исследование методом конечно-элементного моделирования было проведено как для процесса формообразования по предлагаемому способу, так и для традиционного способа. Экспериментальное исследование проводилось для 1/32, 1/8 и 1/4 частей оснастки и заготовки, разница значений толщин изделия для разработанных моделей составила порядка 0,4 %, что является фактом идентичного характера изменения толщин изделия и напряженно-деформированного состояния процесса формообразования. Поэтому для дальнейших исследований процесса формообразования допустимо равноценно использовать любую из ранее разработанных и предложенных моделей, вместо полной модели процесса формообразования гофра сильфона, с целью сокращения затрачиваемых временных ресурсов.
На рисунке 2 представлена картина относительного изменения толщины гофра сильфона при формообразовании традиционным
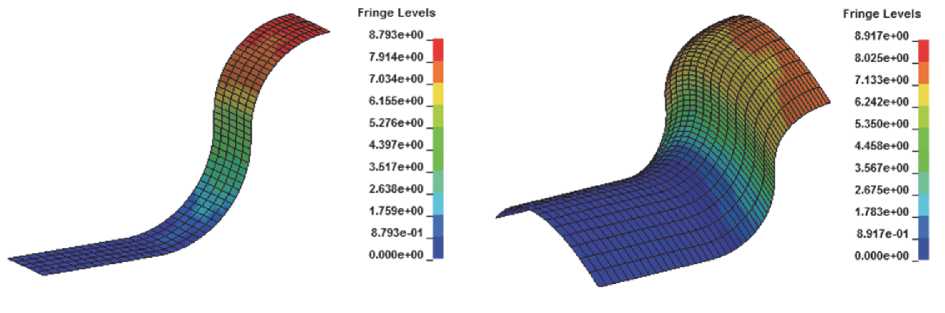
Рис. 2. Относительное изменение толщины гофра сильфона при формообразовании традиционным способом для 1/32 (1) и 1/8 (2) частей оснастки и заготовки
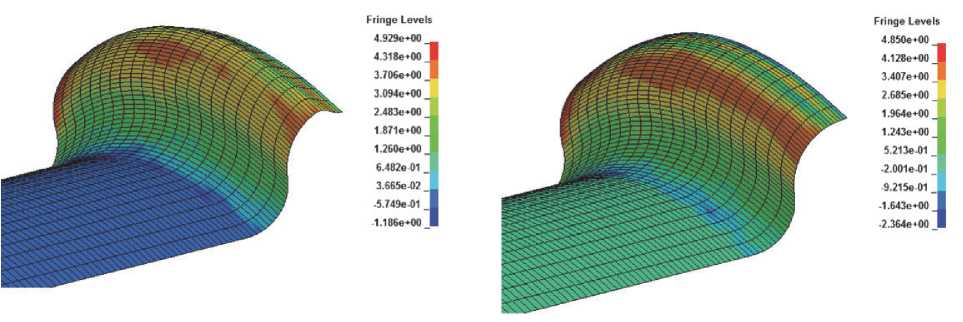
Рис. 3. Относительное изменение толщины гофра сильфона на первом (1) и на втором (2) переходах при формообразовании предлагаемым способом
способом для 1/32 и 1/8 частей оснастки и заготовки.
На рисунке 3 представлена картина относительного изменения толщины гофра сильфона на первом и на втором переходах, предлагаемого способа формообразования для 1/8 части оснастки и заготовки.
Абсолютное значение утонения в области вершины гофра составило порядка 10 % исходной толщины при формообразовании традиционным способом; 4 % исходной толщины при формообразовании предлагаемым способом на первом переходе; 1 % исходной толщины при формообразовании предлагаемым способом на втором переходе.
Наибольшее значение эквивалентных напряжений по Мизесу составило порядка 330 МПа на первом переходе при формообразовании предлагаемым способом и 340 МПа на втором переходе при формообразовании предлагаемым способом. Напряжения не превышают разрушающих напряжений для рассматриваемого материала. На рисунке 4 представлены поля распределения эквивалентных напряжений по Мизесу на первом и на втором переходах при формообразовании предлагаемым способом.
Расхождение полученных толщин и утонений в результате экспериментальных исследований методом конечно-элементного моделирования и аналитических расчетов при исследовании процесса формообразования предлагаемым способом составило порядка 2 %, что доказывает корректность полученных результатов. Приведенные результаты реализованных исследований также доказывают снижение утонения материала заготовки при формообразовании изделия предлагаемым способом, что позволит изготавливать и при- менять изделия, повышенного качества и надежности.
В общем случае, для определения параметров технологического процесса необходимо, исходя из заданных параметров заготовки (диаметр, толщина, материал трубы) и желаемой высоты гофра сильфона, осуществить подбор конкретной конфигурации матрицы для первого перехода, ориентируясь на полученные графические зависимости по результатам проведенных исследований и осуществить расчет необходимых для формообразования давлений.
На рисунке 5 представлены графические зависимости для осуществления подбора конфигурации матрицы для первого перехода. Зависимости представлены для материала заготовки 12Х18Н10Т. На рисунке 6 представлены основные геометрические параметры матрицы для первого перехода.
ВЫВОДЫ
В результате исследования разработана методика расчета параметров технологического процесса и математическая модель процесса формообразования сильфона с учетом воздействия эластомера, реализован комплекс теоретических и экспериментальных исследований, дана оценка полученных результатов и подтверждена гипотеза о возможности получения изделия с более равномерной толщиной стенки по всей его поверхности. В дальнейшем планируется проведение натурного эксперимента и последующего сравнения его результатов с аналитическими расчетами и результатами конечно-элементного моделирования для окончательной оценки выдвинутой гипотезы.
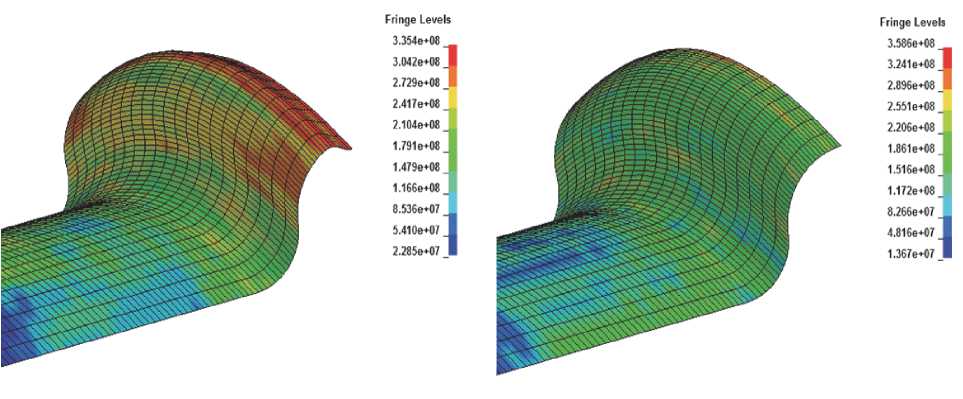
Рис. 4. Поля распределения эквивалентных напряжений по Мизесу на первом (1) и на втором (2) переходах при формообразовании предлагаемым способом
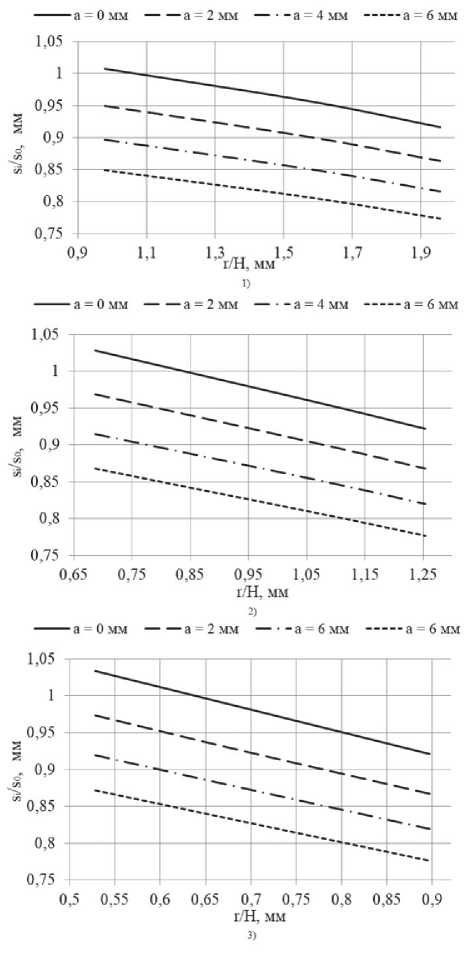
Рис. 5. Изменение относительной толщины в области вершины сформированного гофра сильфона в зависимости от отношения радиуса профиля матрицы r к высоте волны H для различных прямолинейных частей гофра сильфона a :
1) для H = 0,235 мм; 2) для H = 0,335 мм;
3) для H = 0,435 мм
Список литературы Исследование процесса формообразования поперечного гофра сильфона с минимальной разнотолщинностью
- Барвинок, В.А. Высокоэффективные технологические процессы изготовления элементов трубопроводных и топливных систем летательных аппаратов / В.А. Барвинок, А.Н. Кирилин, А.Д. Комаров [и др.]. - М.: Наука и технологии, 2002. - 394 с.
- Gromova E.G. Research of the parts pressing process using the elastic media pressure // Key Engineering Materials. 2016. V. 684. P. 273-277.
- Исаченков, Е.И. Штамповка резиной и жидкостью / Е.И. Исаченков. - М.: Машиностроение, 1967. 367 с.
- Кирилин, А.Н. Разработка и исследование технологии формовки рифтов эластичной средой на трубах большого диаметра / А.Н. Кирилин, А.Д. Комаров, В.К. Моисеев, Ю.В. Федотов // Проблемы машиностроения и автоматизации. - 2000. - №1-2. - С. 64-68.
- Material stress strain behaviour and elastomer pressure under constrained bending of sheet edges / O.V. Lomovskoi, V.K. Moiseev, A.N. Plotnikov, etc. // Russian Aeronautics. 2015. V. 58(1). P. 81-87.
- Results of the sheet parts curved edges constrained bending with elastomer / V.K. Moiseyev, A.A. Sharov, E.G. Gromova, etc. // Key Engineering Materials. 2017. V. 746. P. 285-289.
- Numerical simulation and experiment research on forming of two-step channel based on rubber pad pressing / HY. Wang, Z. Wei, F. Teng, PC. Zhang, JC. Sun, SJ. Ji // The International Journal of Advanced Manufacturing Technology. 2019. V. 101(5-8). P. 2175-2189.
- Experimental and numerical investigation of hole-flanging process with rubber punch / L. Belhassen, S. Koubaa, M. Wali, F. Dammak // Advances in mechanical engineering and mechanics II. 2021. P. 262-268.