Исследование процесса резания текстильных материалов
Автор: Зимина Е.Л., Коган А.Г.
Журнал: Вестник Витебского государственного технологического университета @vestnik-vstu
Рубрика: Технология и оборудование легкой промышленности и машиностроения
Статья в выпуске: 2 (33), 2017 года.
Бесплатный доступ
В работе представлен анализ основных закономерностей процесса резания текстильных отходов как упруго-пластичных материалов. Установлено, что варьируя технологическими параметрами режущего инструмента - количеством ножей, диаметром оправки ротора, толщиной тела ротора, высотой и длиной ножей, углом их наклона, а также размером ячеек сортировочного сита волокнистая масса достигает равномерной консистенции, а размеры частиц измельчаются до требуемой величины. Получены расчетные аналитические выражения и математические модели для определения показателей измельчения упруго-пластичных материалов с позиции размера частиц в общей волокнистой массе.
Процесс резания, текстильные отходы, волокнистая масса, процесс измельчения, упруго-пластичные материалы
Короткий адрес: https://sciup.org/142212338
IDR: 142212338
Текст научной статьи Исследование процесса резания текстильных материалов
ТЕКСТИЛЬНЫЕ ОТХОДЫ, УПРУГО-ПЛАСТИЧНЫЕ МАТЕРИАЛЫ, ПРОЦЕСС РЕЗАНИЯ, ВОЛОКНИСТАЯ МАССА, ПРОЦЕСС ИЗМЕЛЬЧЕНИЯ
В работе представлен анализ основных закономерностей процесса резания текстильных отходов как упруго-пластичных материалов. Установлено, что варьируя технологическими параметрами режущего инструмента - количеством ножей, диаметром оправки ротора, толщиной тела ротора, высотой и длиной ножей, углом их наклона, а также размером ячеек сортировочного сита волокнистая масса достигает равномерной консистенции, а размеры частиц измельчаются до требуемой величины. Получены расчетные аналитические выражения и математические модели для определения показателей измельчения упруго-пластичных материалов с позиции размера частиц в общей волокнистой массе.
TEXTILE WASTE, ELASTIC-PLASTIC MATERIALS, CUTTING PROCESS, FIBER MASS, MILLING PROCESS
The paper presents an analysis of the main regularities of the process of cutting textile waste as elastic-plastic materials. It is established that by varying the technological parameters of the cutting tool: the number of blades, the diameter of the rotor mandrel, the thickness of the rotor body, the height and length of the knives, the angle of their inclination, and the size of the cells of the screening screen, the pulp achieves a uniform consistency and the particle size is reduced to the required value. Calculated analytical expressions and mathematical models are obtained to determine the parameters of grinding elastoplastic materials from the position of particle size in the total fiber mass.
Эффективность и качество полученного волокнистого материала в процессе измельчения текстильных отходов зависят от рационального проведения процессов обработки их резанием, которое достигается в том случае, если:
-
- режущая часть инструмента имеет оптимальные геометрические параметры и качественную заточку лезвий;
-
- резание материалов осуществляется с технически и экономически обоснованными подачами материала и скоростями резания;
-
– максимально используются возможности механизмов оборудования для измельчения [1].
Современные тенденции развития машино строения, связанные с автоматизацией производственных процессов, созданием новых видов материалов с еще недостаточно изученными свойствами требуют поиска новых подходов к исследованию процесса резания, основанных на достижениях фундаментальных наук, разработки новых видов обработки резанием, режущих инструментов и станков [2].
На практике для определения режимов резания пользуются одним из методов расчета:
-
1) табличным (выбор параметров режима резания по специальным таблицам);
-
2) аналитическим (расчет по эмпирическим зависимостям);
-
3) графическим (построением графических зависимостей номограмм в логарифмической системе координат) [3].
Аналитическое описание процесса резания текстильных материалов возможно лишь при выявлении взаимосвязи между следующими группами факторов, влияющих на ход процесса и определяющих его результаты: технологическими требованиями к процессу, деформационно-прочностными свойствами материалов, типом и характеристиками режущего инструмента и оборудования, характером и параметрами де-формационно-разрушающего воздействия, особенностями силового взаимодействия лезвия с объектом обработки [4].
Целью работы является разработка аналитических выражений и математических моделей расчета технологических параметров оборудования для измельчения текстильных отходов.
Так как текстильные отходы в виде кромок, обрези, межлекальных выпадов имеют различные размеры, для их измельчения чаще всего используют ножевые дробилки и барабанные мельницы (роторные дробилки).
Основной характеристикой процесса измельчения является степень измельчения ( i ), которая определяется соотношением средневзвешенных размеров частиц материала до и после измельчения:

где dí – размер частиц до измельчения, мм; dê – размер частиц после измельчения, мм.
Степень измельчения отражает технологию и определяет параметры измельчителей. Требуемый размер частиц после измельчения зависит от области их дальнейшего применения.
Производительность роторных дробилок Q, м 3 /с определяют по формуле
0 = »^° d) -h-a '8
-
с-1; d – диаметр ротора у основания ножей, м; z – количество ножей.
Тогда производительность по массе равна
Q™ = Qp, кг/с(3)
где ρ – плотность материала, кг/м3.
Qm=w^^h-z.p.(4)
Большой диаметр ротора позволяет:
– установить большое количество ножей при постоянном шаге, благодаря чему минутная подача на нож возрастает, а следовательно повышается производительность;
– увеличить массу ротора и длину дуги контакта ротора с материалом, что улучшает теплоотвод, а следовательно, увеличивается стойкость ножей и самого ротора к износу;
– сделать большое посадочное отверстие, то есть применить более жесткую оправку, что позволит вращаться ротору на высоких скоростях без вибрации.
Однако увеличение диаметра ротора повышает крутящий момент, а следовательно и расход энергии, увеличивает расход стали для изготовления режущего инструмента.
Поэтому необходимо подбирать конструкцию ротора с наибольшим диаметром посадочного отверстия и возможно меньшим наружным диаметром.
Число ножей – важный параметр ротора в измельчителе, от которого зависит торцевой шаг и работоспособность ротора. Чем меньше количество ножей у ротора одного и того же диаметра, тем больше объем канавок для размещения волокнистого материала. Также чем больше ножей, тем меньше величина сил резания, приходящаяся на один нож. Поэтому число ножей должно быть оптимальным. Следовательно, расчет конструктивных элементов ротора сводится к определению его диаметра, числа ножей, диаметра оправки ротора, а также расчету элементов ножей – их высоты.
Особенности процесса резания с помощью роторного измельчителя:
– каждый нож работает с перерывами, периодически цепляя материал (рисунок 1). Отрицательным в данном случае является то, что врезание ножа в материал происходит с ударом;
– срезаемый материал должен свободно размещаться во впадине между ножами, а поэтому объем впадины должен быть больше объема срезаемого материала.
Для анализа толщины и площади сечения среза материала сначала определим значение угла контакта δ , то есть центрального угла, соответствующего дуге контакта ротора с материалом.
Из треугольника ОВС расстояние между двумя последовательными положениями траекторий двух смежных ножей, измеренное по нормали, то есть в радиальном направлении, t – толщина материала.
На рисунке 2 точка Â соответствует моменту выхода первого ножа из зоны контакта с материалом, точка Å – то же для второго ножа, δ – угол контакта.
Из треугольника ВСЕ имеем
ВС Gmax &ЫЙЙ . (6)
В общем случае
г
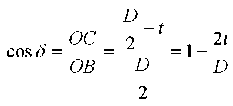
;
av= Sssm^ , (7)
V
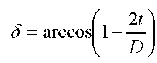
.
Толщина слоя срезаемого материала а – это
где ψ – мгновенный угол контакта, заключенный между вертикалью и радиусом, проведенным в точку контакта вершины ножа с материалом.
Зная ширину среза Â (ширина материала, попадающая под нож) и аmax , можно определить
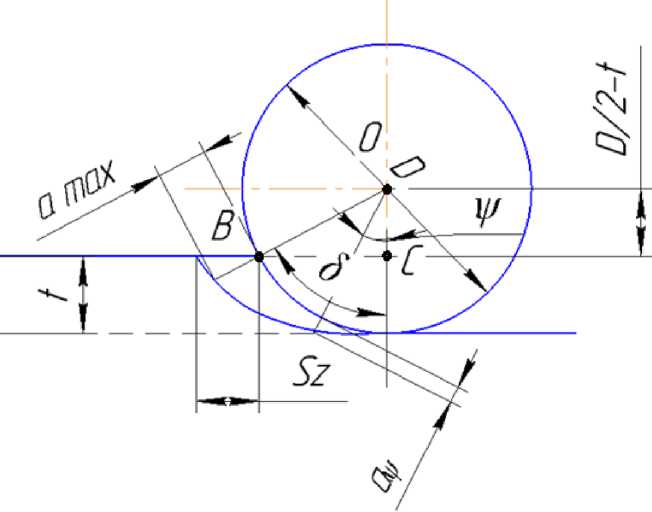
Рисунок 1 – Схема срезания материала одним ножом ротора
площадь поперечного сечения среза, снимаемого одним ножом f
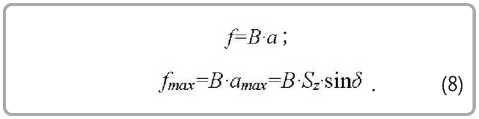
Так как
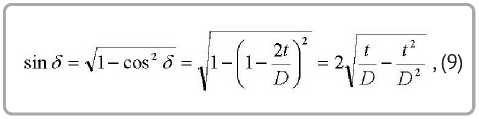
получаем
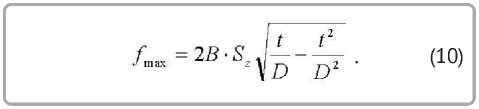
Учитывая, что при измельчении одновременно работают несколько ножей, вводится понятие суммарной площади поперечного сечения срезаемого слоя. Для ее определения необходимо знать, сколько ножей одновременно находится в работе и мгновенный угол контакта для каждого ножа.
Количество одновременно работающих ножей m будет равно

где η = 360 / z – центральный угол между двумя соседними ножами.
Учитывая формулу 11
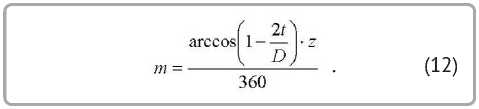
Следовательно, значение m будет тем больше, чем больше t , число ножей и чем меньше диаметр ротора по кромкам ножей.
Мгновенные углы контакта для ножей 1, 2, 3 (рисунок 3) соответственно равны: ψ1 = δ; ψ2 = δ - η; ψ3 = δ - 2η и так далее.
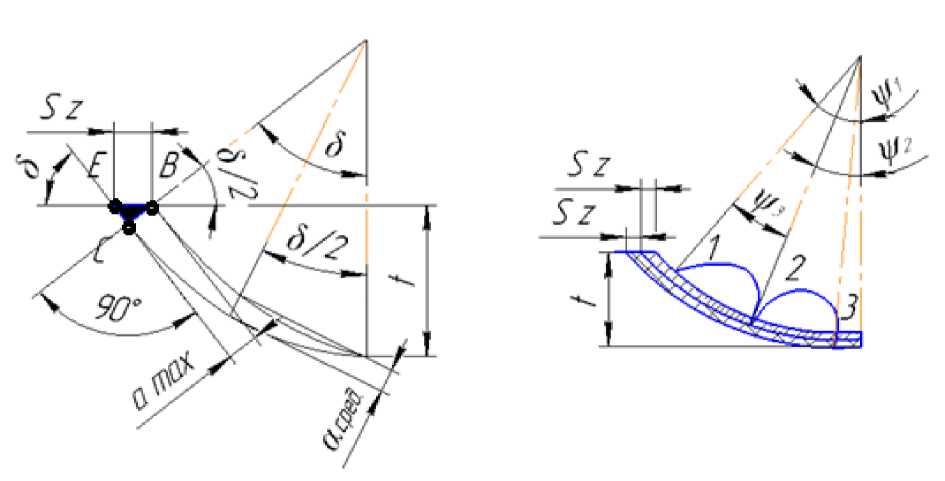
Рисунок 2 – Схема определения толщины среза и суммарной площади срезаемого слоя
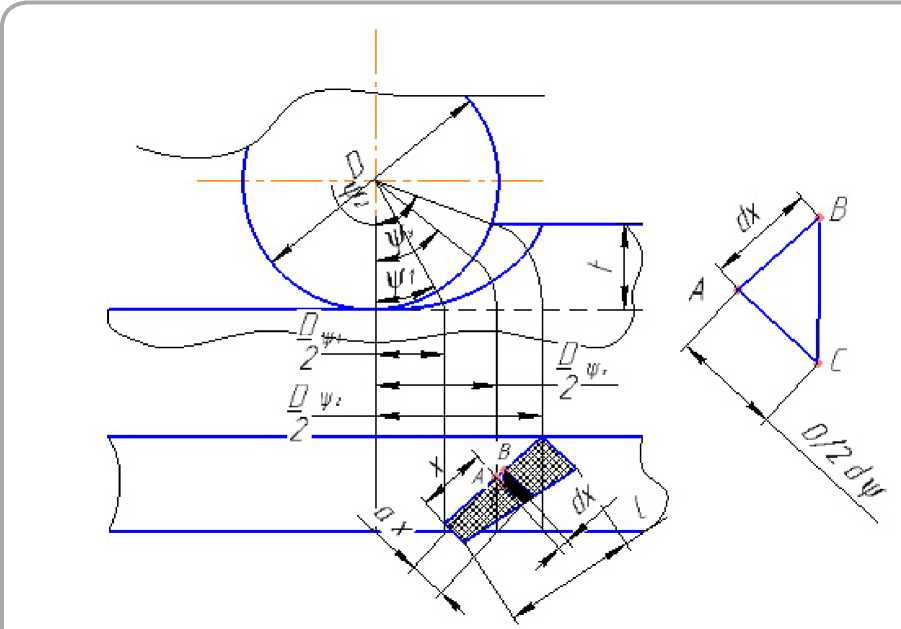
Рисунок 3 – Схема определения площади среза
Так как для каждого ножа площадь срезаемого слоя равна где γ – угол наклона ножей. Тогда
D diy _ . D dy dj = ax---;---= Ъг sm/---у2— . (17)
' 2 sin у ‘ 2 sin у суммарная площадь сечения среза
#= Е/ = B' Sglsmi^ +siny2 +.... + sinyfJ=S-^£sin^.(14)
Следовательно, площадь среза равна
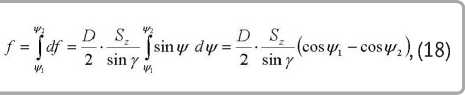
Так как f – это сечение среза, снимаемое од- ним ножом, а l – длина ножа, элементарный уча- а для количества ножей, равного m
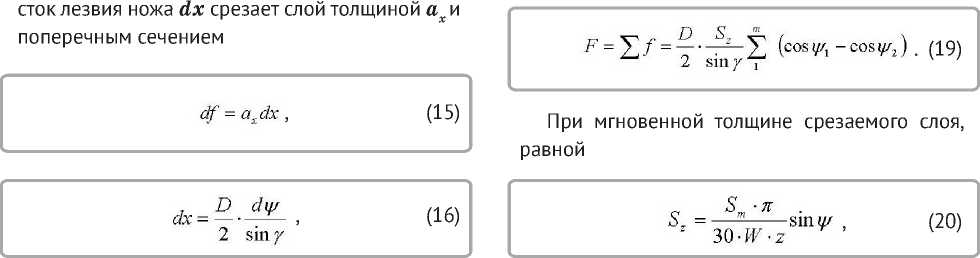
где Sm – подача материала в минуту, мм.
При условии, что материал подается под действием собственной силы тяжести
2 . pa№2 . т-л .
, (21) , где p* - поверхностная плотность материала, г/м2; а* - ширина подаваемого материала, м.
Тогда формула 19 примет вид
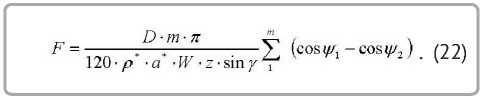
Для подтверждения расчетных значений был проведен эксперимент. Принятые при проведении эксперимента параметры работы измельчающего устройства представлены в таблице 1. Поверхностная плотность испытуемых образцов равна 200 г/м2.
Значения площади частиц, полученные экспериментальным и теоретическим путем, представлены на рисунке 4.
Из рисунка 4 видно, что значение площади частицы, полученной расчетным путем, 4,6 мм2 попадает в интервал 4,0 – 5,8 мм2 размеров частиц, полученных в результате проведенного эксперимента.
ВЫВОДЫ
В результате произведен анализ основных закономерностей процесса резания текстильных материалов. Установлено, что при варьировании технологическими параметрами режущего инструмента: количеством ножей, диаметром ротора, высотой, длиной ножей и углом их наклона – волокнистая масса достигается равномерной консистенции, а размеры частиц измельчаются до требуемой величины. Получена математическая модель для определения показателей измельчения материалов с позиции размера частиц в общей волокнистой массе.
Таблица 1 – Основные параметры устройства для измельчения при проведении испытаний |
|||
Показатель |
Единицы измерения |
Значение |
|
Диаметр ножевого ротора по кромкам ножей |
мм |
200 |
|
Рабочая длина ножей |
мм |
250 |
|
Частота вращения ротора |
мин-1 |
900 |
|
Число ножей |
шт |
3 |
|
Угол наклона ножей |
град |
45 |
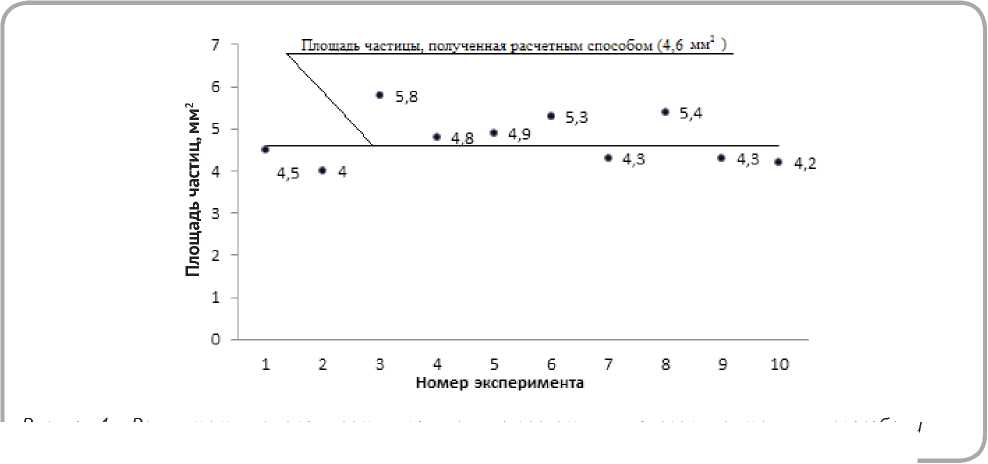
Рисунок 4 – Результаты замеров частиц, полученные расчетным и экспериментальным способами
Список литературы Исследование процесса резания текстильных материалов
- Зимина, Е. Л., Коган, А. Г., Ольшанский, В. И. Подготовка текстильных отходов при производстве нетканых материалов, полученных способом мокрого прессования, Вестник Витебского государственного технологического университета, 2016. - № 2 (31). - С. 47-54.
- Попок, Н. Н. (2006), Теория резания, Новополоцк, 228 с.
- Кулаженко, Е. Л. Исследование процесса резания упругопластичных материалов // Вестник Витебского государственного технологического университета. - 2009. - № 1 (16). - С. 57-61.