Исследование прочности и жесткости металлобетонов методом численного моделирования
Автор: Ерофеев П.С., Лаптев Г.А., Меркулов А.И., Ерофеев В.Т.
Журнал: Инженерные технологии и системы @vestnik-mrsu
Рубрика: Строительные материалы и технологии
Статья в выпуске: 4, 2008 года.
Бесплатный доступ
В статье выполнен анализ механических испытаний образцов металлобетона. В качестве средства анализа авторами использовалась методика оптимизации, в соответствии с которой разрабатывался план опытного эксперимента с учетом получения необходимых расчетных данных для целей использования программного комплекса. Программным комплексом предусматривалось варьирование следующих факторов: вид и свойства зернистых включений и матрицы, размеры фрагмента разрушения, критериев разрушения образцов и компонентов структуры.
Короткий адрес: https://sciup.org/14719159
IDR: 14719159
Текст научной статьи Исследование прочности и жесткости металлобетонов методом численного моделирования
В статье выполнен анализ механических испытаний образцов металлобетона. В качестве средства анализа авторами использовалась методика оптимизации, в соответствии с которой разрабатывался план опытного эксперимента с учетом получения необходимых расчетных данных для целей использования программного комплекса. Программным комплексом предусматривалось варьирование следующих факторов: вид и свойства зернистых включений и матрицы, размеры фрагмента разрушения, критериев разрушения образцов и компонентов структуры.
Выявление распределения напряжений и деформаций в композиционных материалах связано со значительными трудностями, обусловленными их специфической структурой и условиями нагружения. Поэтому в приближенных расчетах чаще используют упрощенные модели в сочетании с экспериментальными методами тестирования, например, метод конечных элементов. Развитие методов компьютерного моделирования структуры композиционных материалов повлекло за собой выполнение ряда задач, одна из которых — анализ напряжений и деформаций в зонах контакта структурных компонентов.
В данной работе выполнен анализ механических испытаний образцов металлобетона. Металлобетоном (метоном) называется материал, состоящий из минерального заполнителя (песок, щебень, гравий и г. д.) и металла, играющего роль вяжущего. В зависимости от металла метоны бывают алюминиевые, стальные, чугунные, титановые, медные, свинцовые, оловянные, цинковые и т. д. [3]. В качестве средства анализа использовалась методика оптимизации, приведенная в работе [2). В соответствии с этой методикой разрабатывался план опытного эксперимента с учетом получения необходимых расчетных данных для целей использования программного комплекса [I] Программным комплексом предусматривается варьирование следующих факторов: вид и свойства зернистых включений и матрицы, размеры фрагмента разрушения, критериев разрушения образцов и компонентов структуры. В процессе моделирования разрушения образцов методом итераций осуществляется подбор механических параметров компонен- тов. В процессе пошаговых итераций варьируются последовательно деформативные и прочностные параметры включений, зон матрицы когезии и адгезии. Условием итерации является равенство механических параметров объектов, найденных опытным путем и численным моделированием. Численные значения показателей компонентов в дальнейшем используются как параметры численного моделирования. Компоненты в структуре размещаются при помощи датчика случайных чисел согласно плану эксперимента. Интерфейсы (зоны взаимодействия) определяются соответствующими включениями: область кодгезии — внешняя оболочка включения, область адгезии — внешняя оболочка включения внутри матрицы. Для формирования расчетных моделей используется плоское на-пряженно-деформируемое состояние объекта.
Программа включает следующие функциональные блоки:
-
— формирования базы матриц жесткости исходной конечно-элементной модели, ее последующую поэтапную фрагментацию (степень фрагментации определяется минимальным размером элементарного фрагмента деформирования и разрушения);
-
— формирования структуры металлобетона (размещение включений с учетом их объемного удельного содержания и оболочек включений);
-
— формирования параметров состояния структуры на пути разрушения;
-
— циклического моделирования поэтапного деформирования и разрушения объектов (определение модуля обратимой деформации, прочности на сжатие компонентов (матрицы и
- заполнителей) методом итераций для каждого пункта плана экспериментальных работ);
-
— тестирования найденныхпараметровчис-ленным моделированием комплексных объектов, содержащих совокупность включений, и определения корректировочных коэффициентов, учитывающих структурные взаимодействия между ними;
-
— прогнозирования значения модуля деформации и прочности на сжатие оптимизируемого состава металлобетона;
-
— интерполяции и экстраполяции механических параметров модифицируемых составов металлобетонов;
-
— формирования и вывода файлов результатов численного моделирования.
При определении механических свойств составов металлобетонов нами определялись зависимости прочности и деформативности от вида матрицы, содержания и крупности зерен заполнителя. В процессе определения механических параметров компонентов одновременно проводится анализ структурных взаимодействий между ними. Системой численного моделирования определяется характер разру шения объекта и выявляется наиболее слабый структурный компонент.
Следует отметить, что термины параметров компонентов (матрица, включения, когезия и адгезия) имеют условное значение и действуют только применительно к рассмотрению структуры объекта моделирования при анализе структурных взаимодействий. Суть их заключается в математическом решении и проведении анализа системой численного моделирования состояния объекта и его изменения при приложении нагрузки и разрушении. Это состояние выражается интерпретированными значениями механических параметров. На основе проведенных вычислений аналитическими методами система переходит к определению параметров объекта моделирования модифицируемого материала, состав которого принят в соответствии с планом намеченных исследований.
В качестве исходных расчетных данных принимались результаты лабораторных испытаний образцов составов металлобетонов с матрицей из серого чугуна марки СЧ-20 (ГОСТ 1412-85) и конструкционного алюмини-
Таблица /
Исходные расчетные данные для моделирования структуры металлобетона на заполнителе из фарфоровых шариков
№ состава |
Е_. МПа |
К„.МПа |
МПа |
МПа |
Еф|Ш, МПа |
МПа |
Механические параметры объекта |
|
Е„, МПа |
R„, МПа |
|||||||
Составы на заполнителе из фарфоровых шариков диаметром 10 мм |
||||||||
1 |
115000 |
510 |
— |
— |
40 000 |
38 |
88 500 |
480 |
2 |
— |
— |
90 000 |
480 |
40 000 |
38 |
83 600 |
510 |
Составы на заполнителе из фарфоровых шариков диаметром 6 мм |
||||||||
3 |
115 000 |
510 |
— |
42 000 |
40 |
90 000 |
490 |
|
4 |
90 000 |
480 |
42 000 |
40 |
84 000 |
520 |
Таблица 2
Исходные расчетные данные для моделирования структуры металлобетонов на базальтовом и диабазовом щебне
В качестве заполнителя для двух групп испытаний на этих матрицах служили фарфоровые шарики диаметром 10 и 6 мм, а также диабазовый и базальтовый щебень. Исходные данные расчетов приведены в табл. 1 и 2.
В качестве объекта моделирования использовался куб с размером ребра 4 см, геометрически подобный опытному образцу при лабораторных испытаниях.
На рис. 1 и 2 приведены зависимости изменения прочности на сжатие и модуля деформации металлобетонов на сером и алюминиевом чугуне от степени наполнения фарфоровыми шариками, полученные при помощи численного моделирования.
С увеличением объемного содержания заполнителя модули деформации объектов на сером и алюминиевом чугуне несколько сбли жаются. При этом повышение содержания фарфоровых шариков приводит к значительному снижению жесткости металлобетона.
На рис. 3 и 4 приведены зависимости изменения прочности на сжатие и модуля деформации металлобетонов на сером и алюминиевом чугуне от степени наполнения диабазовым и базальтовым щебнем, также полученные при помощи численного моделирования.
Как видно из полученных результатов, при увеличении степени наполнения заполнителем происходит снижение прочности и дефор мативности металлобетона. В смеси с плавающим заполнителем без контактных зон (менее 50 % по объему) зерна заполнителя раздвинуты и не взаимодействуют между собой, оказывают влияние только на прилегающую зону металла. С увеличением степени наполнения (50—65 % по объему) создаются зоны взаимодействия оболочек адгезии (интерфейсы) отдельных зерен заполнителя, перекрывающих друг друга, а матрица в виде тонких металлических пленок обволакивает частицы, не
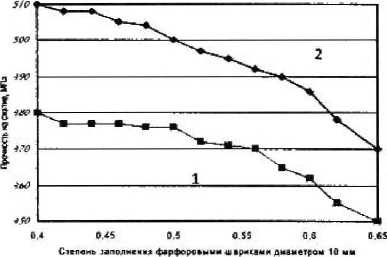
Рисунок 1
Зависимость прочности на сжатие (а) и модуля деформации (б) металлобетона на сером (1) и алюминиевом чугуне (2)
от степени наполнения фарфоровыми шариками диаметром 10 мм
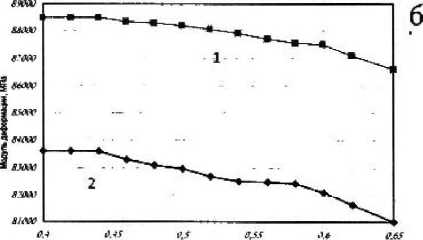
Сччн» де*ми*н** фас4ораоын* щармиями дне метре и 10 ■«
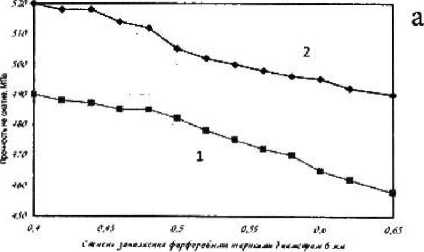
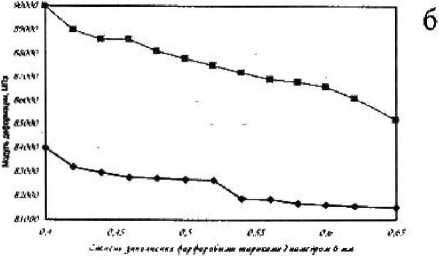
Рисунок 2
Зависимость прочности на сжатие (а) и модуля деформации (б) металлобетона на сером (1) и алюминиевом чугуне (2) от степени наполнения фарфоровыми шариками диаметром 6 мм
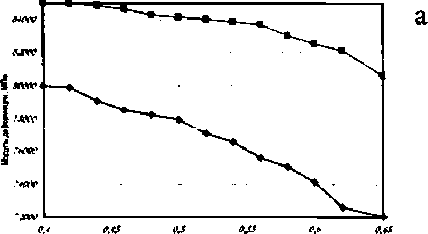
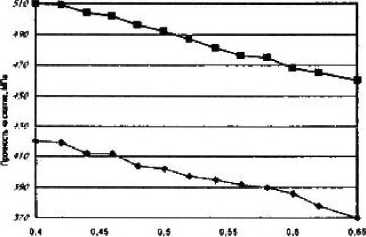
C"hem мповпмий ДееббМеме щебиве Ста ми к зяпапмиаи дилВлвовым щ«Ьаы
Рисунок 3
Зависимость прочности на сжатие (а) и модуля деформации (б) металлобетона на сером (I) и алюминиевом чугуне (2) от степени наполнения диабазовым щебнем
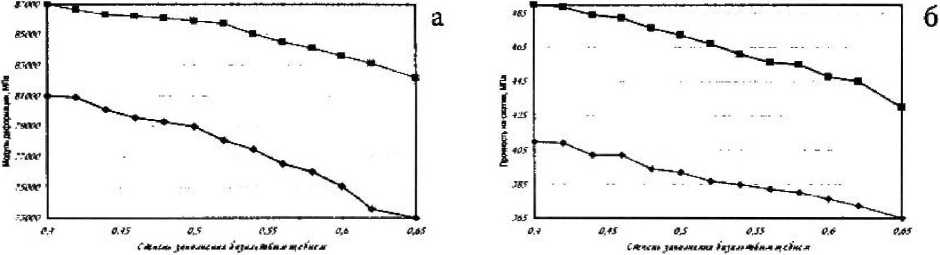
Рисунок 4
Зависимость прочности на сжатие (а) и модуля деформации (б) металлобетона на сером (1) и алюминиевом чугуне (2) от степени наполнения базальтовым щебнем
прерываясь. При степени наполнения до 50 % разрушению подвергается металлическая матрица. Критическая нагрузка, приложенная к образцу, ведет к разрушению металлической прослойки и объекта в целом. В данном случае разрушение начинается сколом материала в частной зоне. При дальнейшем увеличении содержания заполнителя нагрузка воспринимается и более слабым компонентом — фарфоровыми шариками или зернами щебня.
Таким образом, установленные численным моделированием данные повышения прочности при увеличении содержания металла и уменьшении прочности при увеличении содержания менее прочного заполнителя, а также разграничения напряжений в металлобетоне по зонам при поэтапном разрушении соответствует теории прочности бетонов на цементном связующем.
Нами проведены исследования механических свойств металлической матрицы из серого чугуна марки СЧ-20 с начальными данными Е = 115 000 МПа и R = 510 МПа. с.ч. сч.
Металлическая матрица из серого чугуна в моделировании представлена как сплошная среда с включениями в виде макропор. Проводились исследования характера разрушения структуры в зависимости от скорости нагружения и размеров макропор. С увеличением размеров макропор от начальных заданных значений размеров пор, рассматриваемых как включения, увеличивается и степень концентрации напряжений, а с увеличением скорости приложения нагрузки, превышающей скорость разрушения металлической матрицы, на каждом этапе разрушения увеличивается зона разрушения или обобщенный фрагмент разрушения. Он включает все одновременно разрушаемые области на каждом этапе разрушения (процесс разрушения рассматривается поэтапно).
В качестве объекта моделирования принят образец кубической формы размером 10 х Ю х Ю см. Численное моделирование структуры однородной металлической матрицы выполнялось также с использованием методики оптимизации композиционных материалов на основе метода конечных элементов. Раз-
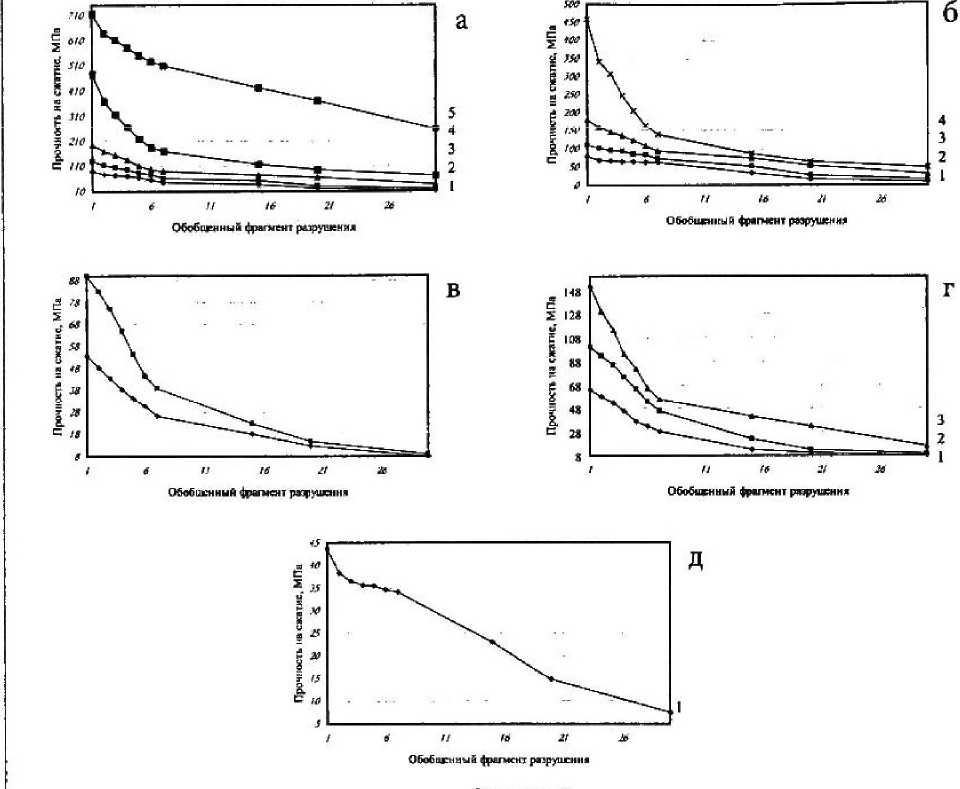
Рисунок 5
Диаграммы зависимости прочности металлической матрицы при числе циклов фрагментации конечно-элементной модели объекта: «а» — равном 8, «б» — 7, «в» — 6, «г» — 5, «д» — 4
мещение макропор при формировании структуры объекта моделирования реализуется на основе использования датчика случайных чисел. В качестве основы формирования структуры модели использовалась конечно-элементная модель, получаемая на основе поэтапной фрагментации треугольных конечных элементов. При выполнении исследований варьировалось число циклов фрагментации (при моделировании принимается 4-, 5-, 6-, 7-, 8-кратная разбивка каждого элементарного фрагмента разрушения), т. е. элементарный фрагмент разрушения определяется как конечный элемент последнего этапа фрагментации. Размер макропор определяется номером этапа фрагментации. Обобщенный фрагмент разрушения включает элементарные фрагменты разрушения, размещенные компактно или разрозненно в пределах всего объекта моделирования.
На рис. 5 приведены диаграммы зависимости прочности металлической матрицы при числе циклов фрагментации конечно-элементной модели объекта (для варианта «а» равном 8, «б» — 7, «в» — 6, «г» — 5, «д» — 4).
На всех диаграммах показаны графики зависимости для размеров пор, определенных конечным элементом — номером последнего этапа фрагментации. Таким образом, графикам 1, 2, 3, 4, 5 соответствуют номера этапов фрагментации конечных элементов — 4, 5, 6, 7, 8. При моделировании принято минимальное условное значение эффективного диаметра пор — 0,78 мм (при цикле фрагментации объекта моделирования — 8), максимальное условное значение — 12,5 мм (при цикле фрагментации объекта моделирования — 4).
На рис. 6 изображена структура металлической матрицы при формировании конечно-
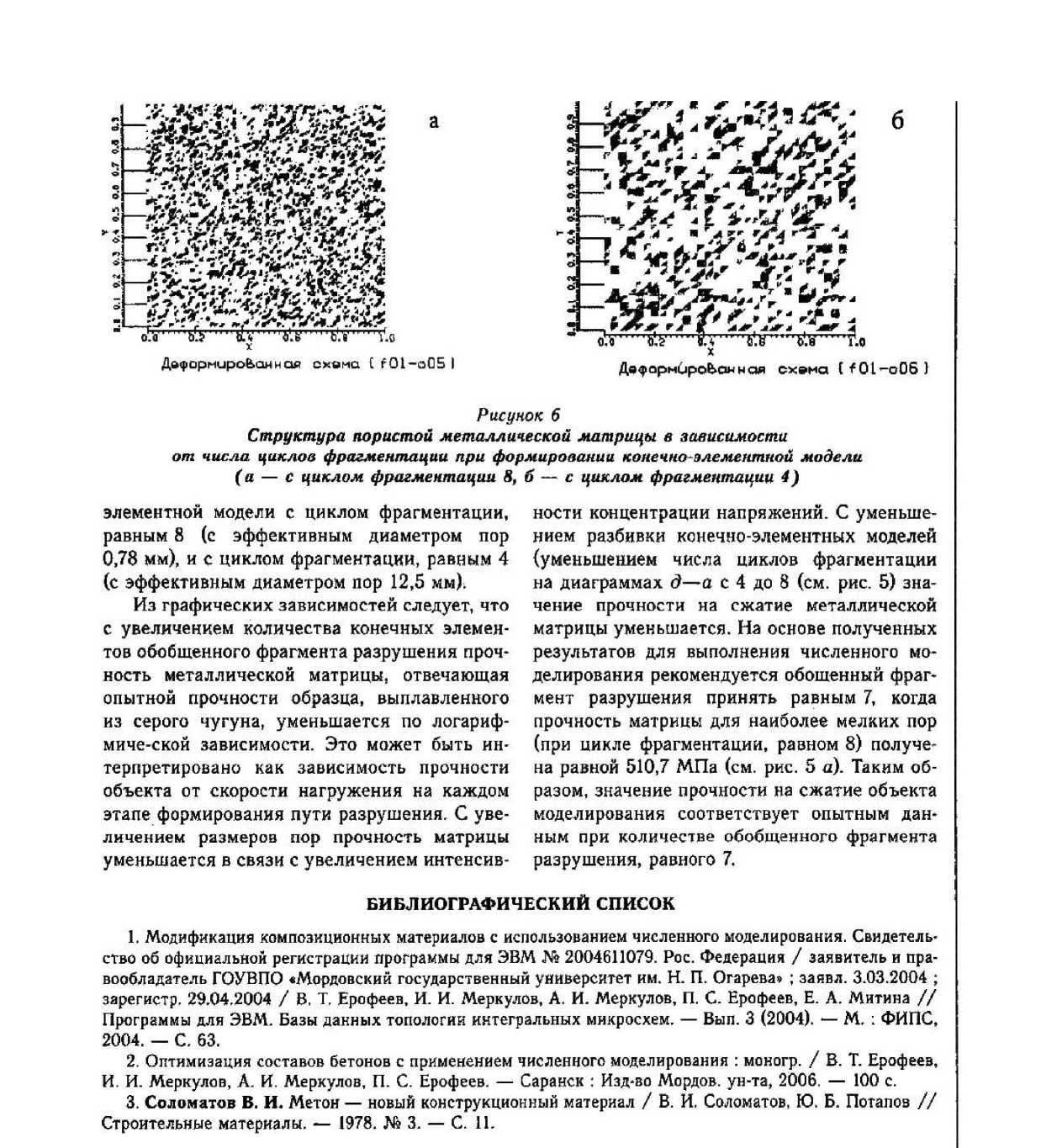
Рисунок б
Структура пористой металлической матрацы в зависимости от числа циклов фрагментации при формировании конечно-элементной модели (а — с циклом фрагментации 8, б — с циклом фрагментации 4)
элементной модели с циклом фрагментации, равным 8 (с эффективным диаметром пор 0,78 мм), и с циклом фрагментации, равным 4 (с эффективным диаметром пор 12,5 мм).
Из графических зависимостей следует, что с увеличением количества конечных элементов обобщенного фрагмента разрушения прочность металлической матрицы, отвечающая опытной прочности образца, выплавленного из серого чугуна, уменьшается по логариф-миче-ской зависимости. Это может быть интерпретировано как зависимость прочности объекта от скорости нагружения на каждом этапе формирования пути разрушения. С увеличением размеров пор прочность матрицы уменьшается в связи с увеличением интенсив ности концентрации напряжений. С уменьшением разбивки конечно-элементных моделей (уменьшением числа циклов фрагментации на диаграммах д—а с 4 до 8 (см. рис. 5) значение прочности на сжатие металлической матрицы уменьшается. На основе полученных результатов для выполнения численного моделирования рекомендуется обошенный фрагмент разрушения принять равным 7, когда прочность матрицы для наиболее мелких пор (при цикле фрагментации, равном 8) получена равной 510,7 МПа (см. рис. 5 а). Таким образом, значение прочности на сжатие объекта моделирования соответствует опытным данным при количестве обобщенного фрагмента разрушения, равного 7.
Деформированная схема [f01-o05 I
X '
До формированная схема (^01~о06 1
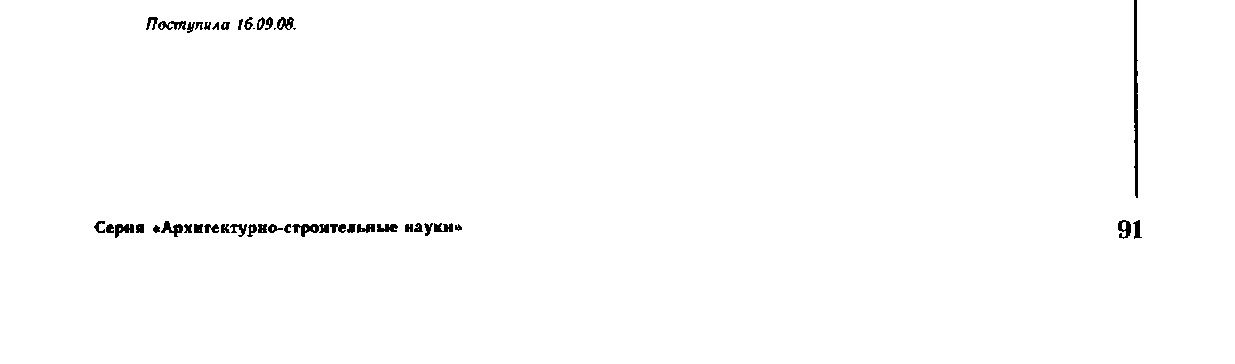
Список литературы Исследование прочности и жесткости металлобетонов методом численного моделирования
- Модификация композиционных материалов с использованием численного моделирования. Свидетельство об официальной регистрации программы для ЭВМ ¹ 2004611079. Рос. Федерация/заявитель и правообладатель ГОУВПО «Мордовский государственный университет им. Н. П. Огарева»; заявл. 3.03.2004; зарегистр. 29.04.2004/В. Т. Ерофеев, И. И. Меркулов, А. И. Меркулов, П. С. Ерофеев, Е. А. Митина//Программы для ЭВМ. Базы данных топологии интегральных микросхем. -Вып. 3 (2004). -М.: ФИПС, 2004. -С. 63.
- Оптимизация составов бетонов с применением численного моделирования: моногр./В. Т. Ерофеев, И. И. Меркулов, А. И. Меркулов, П. С. Ерофеев. -Саранск: Изд-во Мордов. ун-та, 2006. -100 с.
- Соломатов В. И. Метон -новый конструкционный материал/В. И. Соломатов, Ю. Б. Потапов//Строительные материалы. -1978. ¹ 3. -С. 11.