Исследование роли извести при шлакообразовании и внепечной обработке стали инертными газами
Автор: Бахаев Денис Анатольевич, Кочетов Александр Иванович, Кем Александр Юрьевич, Ансимов Алексей Александрович
Журнал: Вестник Донского государственного технического университета @vestnik-donstu
Рубрика: Технические науки
Статья в выпуске: 7-8 (75) т.13, 2013 года.
Бесплатный доступ
Показано, что создание таких технологий обусловлено необходимостью получения стали стандартно высокого качества по составу и температуре. Внепечная обработка стали обеспечивает эти условия и, следовательно, эффективную работу установок непрерывной разливки стали. Представлены апробированные в промышленных условиях экспериментальные данные о влиянии расхода извести на процессы шлакообразования в дуговых электросталеплавильных печах и на последующую внепечную обработку в агрегатах ковш-печь. Предложена технологическая схема комплексной обработки «Дуговая сталеплавильная печь → Внепечная обработка → Установка непрерывной разливки стали». Она исключает повышение окисленности шлака при донной продувке, угар алюминия в ковше и увеличение концентрации кислорода в жидкой стали. Предложенные технологические решения по оптимизации расхода извести, наводке шлака и регламентации режима продувки стали в ковше позволили повысить основные технико-экономические показатели производства стали в условиях Оскольского электрометаллургического комбината (ОЭМК).
Известь, шлак, плавка стали, дуговая сталеплавильная печь, ковш, внепечная обработка, продувка, аргон, азот, кислород, установка непрерывной разливки стали
Короткий адрес: https://sciup.org/14250025
IDR: 14250025 | DOI: 10.12737/2018
Текст научной статьи Исследование роли извести при шлакообразовании и внепечной обработке стали инертными газами
Введение. Возможности регулирования физико-химических условий протекания процессов плавки в традиционных сталеплавильных агрегатах ограничены. Это привело к созданию новых комплексных сталеплавильных технологий. Они предполагают внепечную обработку (ВО) жидкой стали, наличие дуговой печи (ДСП) и установку непрерывной разливки стали (УНРС). Практика показала, что эффективная работа установок непрерывной разливки стали возможна при использовании стали стандартно высокого качества по составу и температуре от плавки к плавке. Вне-печная обработка стали обеспечивает эти условия [1]. Однако остаётся актуальной проблема получения современных марок сталей с ультранизким содержанием нежелательных элементов (S + P ˂ 0,005 %) и растворённых газов ( IF -сталь).
Следует отметить, что интенсивность процессов шлакообразования в значительной мере зависит от межфазной активности кальцийсодержащих соединений (например, извести), вводимых в ДСП, и режимов последующей внепечной обработки [2—4]. Таким образом, при шлакообразовании можно определить, насколько сталь очищена от нежелательных примесей и газов.
Цель настоящей работы — исследовать влияние расхода извести как наиболее распространённого кальцийсодержащего материала на процессы шлакообразования в дуговой сталеплавильной печи, режимы и результаты внепечной обработки промышленных марок сталей.
Результаты и их обсуждение. Обработка экспериментальных данных по результатам шлакообразования в ДСП-150 при плавке с использованием металлизованных окатышей позволила
Работа выполнена в рамках инициативной НИР.
установить влияние удельного расхода извести (кг/т) на изменение содержания фосфора [P, %] в стали (рис. 1). Увеличение расхода извести в интервале 10…50 кг/т сопровождается снижением величины [P, %], однако при дальнейшем увеличении удельного расхода извести её влияние на показатель [P, %] падает. Установлено, что перед выпуском в ковш наименьшие значения содержания фосфора в стали (▲ ~ 0,005 % Р — рис. 1, а) соответствуют удельному расходу извести около 50 кг/т. Это связано со снижением величины адаптационного коэффициента до значения aPO * 0,01, характеризующего условия, в которых содержание фосфора приближается к равно- весному.
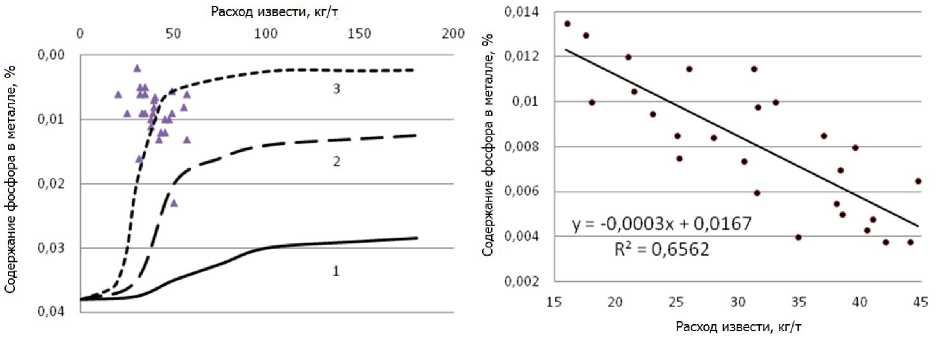
а )
Рис. 1. Выплавка стали 09Г2С (•; ▲ — фактические данные): а — влияние расхода извести на [P, %] при различных значениях адаптационного коэффициента aPO : кривая 1 — aPO = 1; кривая 2 — aPO = 0,1; кривая 3 — aPO = 0,01;
б — зависимость содержания фосфора перед выпуском от удельного расхода извести
При транспортировке сталеразливочного ковша после выпуска металла из дуговой печи в ходе внепечной обработки стали (продувка расплава аргоном) меняется состояние шлака (рис. 2). Установлено, что температура поверхности шлака T п.ш. (рис. 2, а ) в процессе продувки металла аргоном ( V Ar = 0,2—0,4 м3/т) снижается адекватно снижению удельных тепловых потоков Q пот от шлака в окружающую среду (рис. 2, в ) при среднем расходе аргона V Ar ≈ 0,3 м3/т [3, 4]. При этом толщина корки шлака зависит от толщины шлакового покрова в ковше и заметно изменяется только после 30-минутной выдержки (рис. 2, б ). Сравнение характера изменения температуры поверхности корковой зоны шлака (рис. 2, а ) и динамики теплопотерь металла (рис. 2, в ) показывает, что теплопроводность твёрдого шлака на поверхности ниже теплопроводности жидкого шлака. Этим обусловлено увеличение (прирост) толщины корки за счёт слоёв шлака, прилегающих к жидкой стали. В конечном итоге тепловые потери металла в ковше заметно уменьшаются.
При донной продувке жидкой стали в ковше азотом (рис. 3) происходит, во-первых, насыщение металла азотом (Δ[N], %), зависящее от расхода дутья ( Q N , м3).
Во-вторых, наблюдается угар алюминия (ΔAl, %). Он зависит от окисленности шлака, характеризуемой суммарным содержанием оксидов железа и марганца (∑ (FeO + MnO), %) (рис. 4) и количеством шлакообразующей массы в ковше. С увеличением количества шлака в ковше угар алюминия возрастает. Это указывает на необходимость оптимизации как количества, так и степени окисленности шлака.
Ранее выполненные исследования [1, 5] доказывают тесную взаимосвязь окисленности шлака (рис. 5, а ) и активности (концентрации) кислорода в стали ( а [o] ).
Температура поверхности шлака, °C
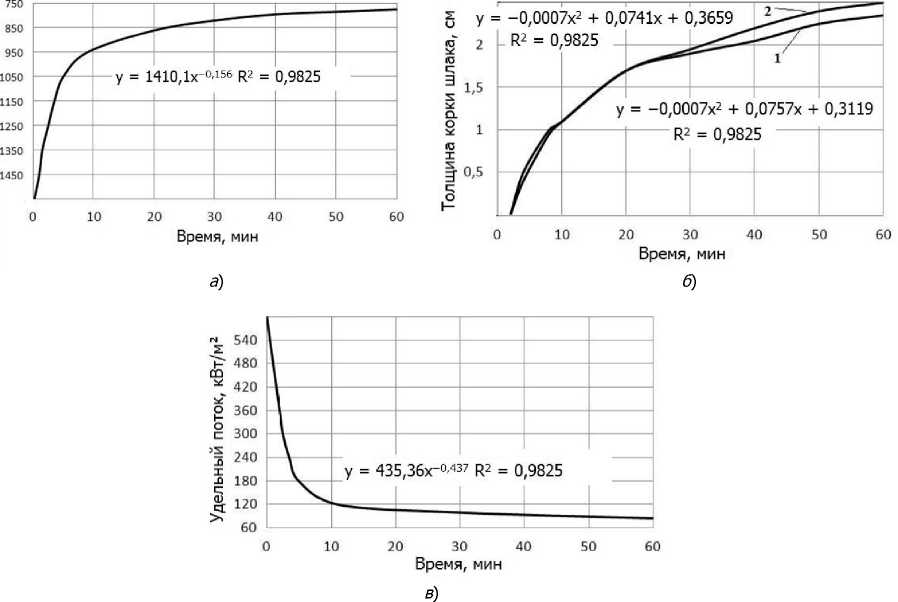
Рис. 2. Изменение во времени температуры поверхности шлака ( а ), толщины корки шлака ( б ), удельных тепловых потоков от шлака к окружающей среде ( в ): кривые 1, 2 — толщина слоя шлака 0,2 и 0,25 м соответственно
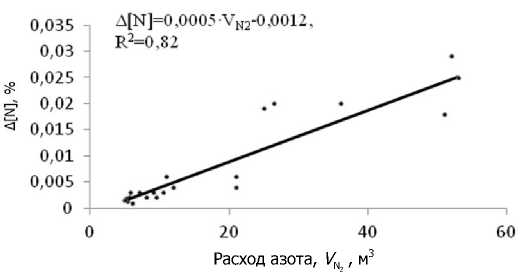
Рис. 3. Зависимость между приростом содержания азота в стали и общим количеством введённого газообразного азота (донная продувка)
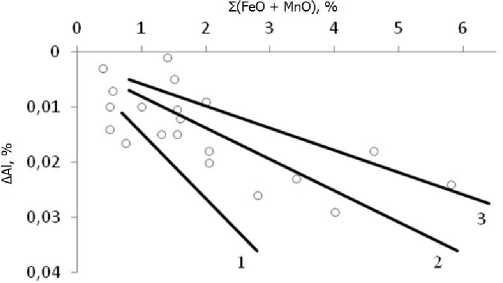
Рис. 4. Угар алюминия в зависимости от суммарной концентрации оксидов железа и марганца в шлаке:
кривая 1 — 2 т; кривая 2 — 3 т; кривая 3 — от 3 до 5 т
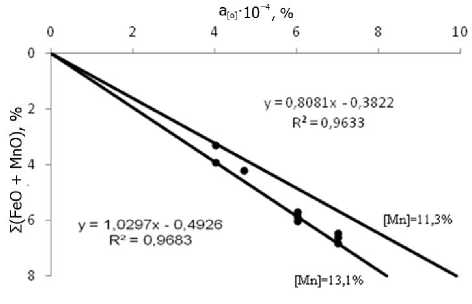
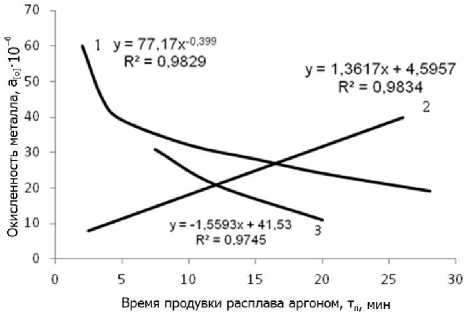
а ) б )
Рис. 5. Зависимость Σ(FeO + MnO) в шлаке от активности кислорода а [o] в стали ( а ) и изменение окисленности стали в зависимости от продолжительности продувки аргоном ( б )
Это подтверждают результаты измерения указанных величин в ковше (табл. 1). Снизить окисленность в ковше перед обработкой стали в агрегате ковш-печь можно путём диффузионного раскисления шлака перед выпуском стали.
Таблица 1
Результаты измерения активности (концентрации) кислорода в жидкой стали а [o] и окисленности шлака Σ(FeO + MnO)
№ плавки |
Результаты измерения а [o] , % |
Результаты анализа |
Σ(FeO + MnO) расч , % |
Невязка значений Σ(FeO + MnO),% |
|
[Mn], % |
Σ(FeO + MnO) эксп , % |
||||
217 |
0,0004 |
11,5 |
3,44 |
3,34 |
2,91 |
123 |
0,0004 |
11,9 |
3,71 |
3,44 |
7,28 |
141 |
0,0004 |
12,0 |
3,71 |
3,50 |
5,66 |
206 |
0,0004 |
12,4 |
3,83 |
3,58 |
6,53 |
228 |
0,0005 |
11,3 |
4,44 |
4,11 |
7,43 |
197 |
0,0006 |
12,1 |
5,44 |
5,19 |
4,60 |
142 |
0,0006 |
12,5 |
5,65 |
5,39 |
4,60 |
128 |
0,0006 |
13,1 |
5,85 |
5,63 |
3,76 |
225 |
0,0007 |
11,8 |
6,05 |
5,88 |
2,81 |
116 |
0,0007 |
12,1 |
6,26 |
6,14 |
1,92 |
196 |
0,0007 |
12,7 |
6,54 |
6,35 |
2,91 |
Проведённые исследования позволили установить, что степень окисленности стали ( а [o] ), а следовательно, и содержание в ней [O] и [N] можно регулировать следующим образом: — заменой азота аргоном;
-
— изменением расхода аргона (рис. 5, б ) на продувку;
-
— расходом вводимого в расплав раскислителя — алюминиевой проволоки (см. рис. 5, б , кривая 2).
В практике термодинамических расчётов широко используется зависимость ∑(FeO + MnO) = а [o] (180,3 + 706,8[Mn]). В процессе продувки аргоном марганец оказывает существенное влияние на окисленность шлака и металла в ковше. Об этом свидетельствуют приведённые на рис. 5, а экспериментальные точки на расчётных линиях. При введении алюминиевой проволоки (см. рис. 5, б ) в металл в процессе внепечной обработки его аргоном значение а [o] существенно падает. Следовательно, уменьшается и окисленность шлака, что способствует улучшению качественных показателей перед разливкой стали на УНРС [6, 7].
Установлено, что характер изменения скорости охлаждения жидкой стали в ковше зависит от массы металла в нём и расхода аргона на продувку (это соответствует данным [3]). Большое значение имеет и технология продувки, в частности наличие крышки ковша. Так, если ковш накрывать крышкой, уменьшая таким образом нагрев металла на 20—30 °C в течение одной плавки, то в год сокращение энергозатрат может составить около 50 кВт·ч на 1 тонну стали. Таким образом можно существенно снизить энергоёмкость производства [1, 4].
В агрегате ковш-печь [1, 3] прогрев шлака и металла электрическими дугами способствует интенсификации процессов внепечной обработки стали. При использовании полых электродов в агрегате (табл. 2) существенно улучшаются технологические показатели. Например, степень десульфурации повышается при меньшем расходе извести (с 3,4 до 3,25 кг/т), ферросплавов (с 0,4 до 0,22 кг/т). При этом удельный расход электроэнергии снижается с 10,2 до 9,8 кВт·ч/т [6].
Таблица 2
Технологические показатели обработки плавок стали 08 на АКП в базовом режиме работы и при работе с полыми электродами (ковш ёмкостью 350 т)
Наименование параметра |
Базовый режим: min–max/среднее |
Работа с полыми электродами: min–max/среднее |
Обработано на АКП, плавок |
8 |
10 |
Температура всего металла по приходу на АКП, оС Температура отдачи металла на разливку, оС |
1532–1610/1570,9 1555–1607/1584,3 |
1529–1606/1568,0 1567–1605/1581,1 |
Продолжительность обработки, мин Продолжительность нагрева на плавке, мин |
4,2–235/50,8 0,3–29,2/10,8 |
14,3–128,5/50,6 1,05–31/10,93 |
Удельный расход электроэнергии, кВт·ч/т |
0,9–11,4/10,2 |
0,85–11,1/9,8 |
Удельный расхода аргона, л/т |
55–222/125 |
54–228/129 |
Удельный расход извести, кг/т Удельный расход флюорита, кг/т Удельный расход алюминия, кг/т |
0,61–6/3,4 0,28–3,6/1,14 0,005–2,6/0,63 |
0,56–6/3,25 0,3–3,47/1,12 0,004–2,5/0,57 |
Удельный расход ферромарганца, кг/т |
0,15–0,93/0,4 |
0,1–0,65/0,22 |
Обобщённый анализ работы агрегатов ковш-печь [1, 3, 4] позволяет утверждать следующее. Каждые 10 °С перегрева металла требует около 4 кВт·ч/т электроэнергии. На 1 кВт·ч/т расходуется 0,0073 кг электродов, а расход огнеупорных материалов при таком перегреве увеличивается на 0,3 % (табл. 3).
Таблица 3
Сравнительные технико-экономические показатели внепечной обработки стали 45 (числитель) и ШХ15 (знаменатель) в АКП по типовой технологии ОЭМК (Б) и по рекомендуемому энергосберегающему режиму (А)
Группа плавок |
Период обработки расплава |
Показатели |
||||
Удельный расход эл. энергии, Q уд , кВт·ч/т |
Время работы под током, τ т , мин |
Расход электродов, ∆ R э , кг/т |
Энергетический КПД, η э , % |
Кол-во плавок |
||
А |
I |
12,81/15,7 |
7,1/8,96 |
0,083/0,105 |
50/60,3 |
14/13 |
II |
7,92/7,15 |
4,11/3,91 |
0,06/0,054 |
38,6/53 |
||
III |
3,81/3,4 |
1,77/1,7 |
0,029/0,026 |
39,9/36,6 |
||
Суммарные (группа А) |
24,54/26,25 |
12,98/14,57 |
0,172/0,185 |
42,8/50 |
||
Б |
I |
13,47/16,99 |
7,2/9,55 |
0,088/0,12 |
48/47 |
15/12 |
II |
8,68/7,22 |
4,76/3,9 |
0,066/0,055 |
36/52 |
||
III |
4,44/3,87 |
2,32/2,14 |
0,034/0,029 |
37/34,15 |
||
Суммарные (группа Б) |
26,59/28,08 |
14,28/15,59 |
0,188/0,2 |
40,3/44,4 |
Из анализа данных работы агрегата ковш-печь на Оскольском электрометаллургическом комбинате (см. табл. 3) следует, что значение энергетического КПД (η э ) для группы А повышается на 4—6 %. Кроме того, достигается меньшее время работы агрегата под током. Это способствует сокращению расхода как электроэнергии (на 5—7 %), так и электродов в процессе внепечной обработки стали.
Рекомендуемый на основании проведённых исследований энергосберегающий режим вне-печной обработки демонстрирует существенно более высокие основные технологические характеристики по сравнению с комплексным технологическим процессом «ДСП → ВО → УНРС» по типовой технологии ОЭМК (табл. 2, 3).
Заключение. Установлено, что расход подаваемой на шлак в ДСП извести влияет на результаты процесса шлакообразования в дуговой печи, а также на технологические показатели при внепеч-ной обработке жидкой стали в ковшах инертными газами. Показано, что с увеличением расхода извести с 15 до 45 кг на тонну жидкой стали содержание фосфора в металле снижается более чем в 2 раза.
Предложена технологическая схема комплексной обработки «ДСП → ВО → УНРС», исключающая повышение окисленности шлака при донной продувке, угар алюминия в ковше и увеличение концентрации кислорода в жидкой стали.
Рекомендованы технологические решения по оптимизации расхода извести, наводке шлака и регламентации режима продувки стали в ковше, позволившие повысить основные техникоэкономические показатели производства стали в условиях ОЭМК.
Список литературы Исследование роли извести при шлакообразовании и внепечной обработке стали инертными газами
- Харламов, Д. А. Исследование процессов нагрева металла при внепечной обработке стали в агрегате ковш-печь/Д. А. Харламов, Э. Э. Меркер, А. И. Булгаков//Известия вузов. Чёрная металлургия. -2002. -№ 3. -С. 26-28.
- Федина, В. В. Шлаковый режим при электроплавке и внепечной обработке стали/В. В. Федина, Э. Э. Меркер, А. И. Булгаков//Известия вузов. Чёрная металлургия. -2003. -№ 11. -С. 24-26.
- Кабаков, З. С. Сокращение потерь тепла от металла в сталеразливочном ковше/З. С. Кабаков, М. А. Пахолкова//Металлург. -2012. -№ 9. -С. 51-52.
- Гизатулин, Р. А. Разработка технологии внепечной обработки стали в агрегате ковш-печь/Р. А. Гизатулин, Л. А. Годик//Электрометаллургия. -2008. -№ 2. -С. 11-13.
- Тен, Э. Б. Повышение качества отливок из стали 110Г13Л обработкой в ковше/Э. Б. Тен, Е. Ю. Лихолобов//Литейщик России. -2010. -№ 10. -С. 18-21.
- Агапитов, Е. Б. Развитие системы управления электродуговой установкой ковш-печь с полыми электродами/Е. Б. Агапитов, Г. П. Корнилов, М. М. Ерофеев//Известия вузов. Электротехника. -2006. -№ 4. -С. 81-84.
- Харламов, Д. А. Энергосберегающая технология внепечной обработки стали в агрегате ковш-печь/Д. А. Харламов, Э. Э. Меркер, А. И. Кочетов. -Старый Оскол: ТНТ, 2006. -232 с.