Исследование структурно-фазового состояния металла как параметра качества обрабатываемых поверхностей деталей машин
Автор: Смирнов А.Н., Конева Н.А., Попова Н.А., Глинка А.С.
Журнал: Известия Самарского научного центра Российской академии наук @izvestiya-ssc
Рубрика: Машиностроение
Статья в выпуске: 1-2 т.12, 2010 года.
Бесплатный доступ
В настоящей работе проведено исследование одной из широко применяемых в машиностроении сталей - стали 35ХГС на различных этапах механической обработки. Основная задача исследования заключалась в определении параметров градиентной структуры стали. Структурные исследования проводились 3 основными методами: растровая электронная микроскопия, просвечивающая дифракционная электронная микроскопия на тонких фольгах и рентгеноструктурный анализ.
Структурно-фазовое состояние, сталь, обрабатываемая поверхность
Короткий адрес: https://sciup.org/148198979
IDR: 148198979
Текст научной статьи Исследование структурно-фазового состояния металла как параметра качества обрабатываемых поверхностей деталей машин
Для обеспечения надежности и долговечности деталей машин необходимо проводить всестороннее изучение путей улучшения качества поверхности с целью повышения ее эксплуатационных свойств. На характеристики обработанных поверхностей оказывают влияние все операции механической обработки, их следует рассматривать не изолированно, а во взаимосвязи, так как характеристики поверхностей формируются всем комплексом технологических воздействий и изменяются в процессе эксплуатации детали. Для изучения качества обработанных поверхностей необходимо знать структурно-фазовое состояние металла, как в процессе механической обработки, так и на стадии заготовительного производства.
В настоящей работе проведено исследование структурно-фазового состояния одной из широко применяемых в машиностроении сталей – стали 35ХГС. Были исследованы 3 образца. Образец № 1 – в исходном состоянии (в поверхностном слое и на глубине 1,0 и 1,5 мм от поверхности); образец № 2 – после
получистового точения при определенных режимах обработки; образец № 3 – после чистового точения (следующего за получистовым) при определенных режимах обработки. Характеристика изделий приведена в таблице 1.
Структурные исследования проводились тремя основными методами: растровая электронная микроскопия (РЭМ); просвечивающая дифракционная электронная микроскопия на тонких фольгах (ПЭМ) и рентгеноструктурный анализ (РСА).
Исследования, проведенные методом ПЭМ, показали, что структура исследуемой стали 35ХГС на поверхности изделия является полностью фрагментированной, на всех этапах изготовления изделия сталь 35ХГС в основном состоит из α -фазы. Морфологически α -фаза подразделяется на а) α -феррит и б) α -фазу, находящуюся в перлитной составляющей, т.е. сталь 35ХГС на поверхности изделия после каждого этапа изготовления обладает феррито-перлитной структурой. Средний размер фрагментов составляет величину ~0.4 мкм. Все микродифракционные картины, полученные с фрагментированной α -фазы, – кольцевые. В исходном состоянии на поверхности изделия имеет место микрозеренная феррито-перлитная смесь. На глубине 1,5 мм от поверхности структура состоит из 20% феррита и 80% несовершенного перлита (40% пластинчатый, 20% глобулярный и 20% смешанный). А на глубине 1,0 мм структура состоит из 30% феррита и 70% перлита, перлит становится несовершенным.
После проведения механической обработки во всех образцах присутствуютферрит-ные зерна в двух состояниях: нефрагментиро-ванном и фрагментированном состоянии (рис. 1). Микродифракционные картины, полученные с нефрагментированных ферритных зерен - идеальные, монокристаллические и карбидных рефлексов не обнаруживают. Микроди-фракционные картины, полученные с зерен фрагментированного феррита, также являются, как правило, монокристаллическими. Однако на рефлексах присутствуют тяжи из группы рефлексов. Величина тяжей может достигать значения ф ~ 20°. Часто на границах фрагментов присутствуют карбиды железа -цементит округлой формы и нанокристалли-ческого размера. Это подтверждается и мик-родифракционными картинами, полученными с таких участков структуры. Перлитные зерна присутствуют трех видов. Первый вид - пластинчатый перлит, представляющий собой конгломерат чередующихся пластин феррита и цементита. Пластины феррита в перлитных зернах могут быть нефрагментированными и фрагментированными.
Таблица 1. Характеристика исследуемых образцов
я я О |
Получистовой режим |
Чистовой режим |
||||
глубина снятого слоя, t (мм) |
число оборотов, n, об/мин |
ширина слоя снимаемой стружки, S, мм/об |
глубина снятого слоя, t (мм) |
число оборотов, n, об/мин |
ширина слоя снимаемой стружки, S, мм/об |
|
№1 |
- |
- |
- |
- |
- |
- |
№2 |
1 |
1000 |
0,25 |
- |
- |
- |
№3 |
1 |
1000 |
0,25 |
0,5 |
1200 |
0,15 |
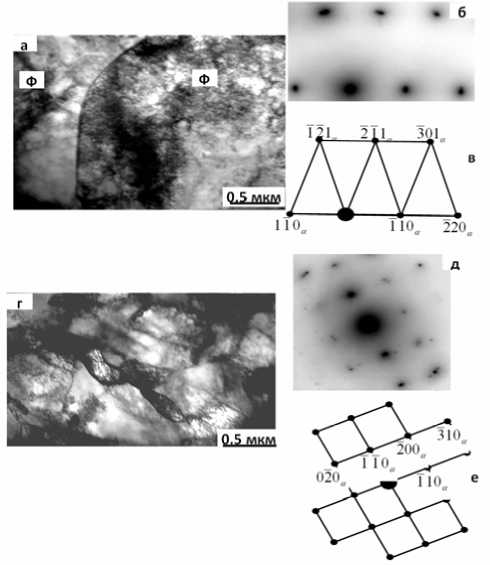
Рис. 1. Типичные электронномикроскопические изображения структуры стали 35ХГС
Зерна феррита: а-в - нефрагментированный феррит, обр. №3, стык двух ферритных (Ф) зерен (а - светлопольное изображение, б - микродифракцион-ная картина, в - её индицированная схема); г-е - фрагментированный феррит, обр. №2 (г - светлопольное изображение, д - микродифракционная картина, е - её индицированная схема)
Вторым видом перлитных зерен являются зерна с глобулярным перлитом - ферритная матрица с распределенными в ней цементит-ными выделениями глобулярной формы. Ферритная матрица в участках с глобулярным перлитом всегда нефрагментирована. Третьим видом перлитных зерен являются зерна со смешанным перлитом, когда в одном зерне присутствуют одновременно выделения цементита пластинчатой и глобулярной формы. Ферритная матрица в зернах со смешанным перлитом может быть нефрагментированной и фрагментированной. Весь перлит является дефектным. Объемные доли каждой структурной составляющей на разных этапах изготовления изделия различны.
В перлитных зернах термомеханическая обработка уже на первом этапе изготовления изделия (обр. №2) привела к изменению в структуре перлита. Эти изменения заключаются в изменении морфологии перлита и в разрушении цементита в перлите. Если в исходном состоянии (обр. № 1) преобладающим в структуре стали являлся пластинчатый перлит, то в обр. № 2 объемная доля пластинчатого перлита составляет лишь 30% от общего содержания перлита в стали.
По выполненным оценкам методом ПЭМ можно утверждать, что на поверхности изделия в исходном состоянии содержится небольшое количество цементита, а именно: объемная доля частиц цементита, расположенных на границах фрагментов и размер которых составляет ~10 нм, равна 0,6%, а объемная доля частиц цементита, расположенных в объеме материала случайным образом, размер которых на порядок выше (~0,1 мкм), -0,2%. В различных участках одного и того же образца (на первом этапе изготовления детали) присутствуют все стадии растворения цементита, встречаются также участки, в которых весь объем материала, занимаемый ранее цементитной пластиной, заполняется нано-размерными частицами.
Проведенные электронно-микроскопические дифракционные исследования эволюции пластин цементита перлитной колонии на первом этапе изготовления детали (обр. № 2), т.е. при термомеханической обработке, обнаружили фазовые превращения цементита. Цепочка фазовой трансформации цементита, исходя из результатов вышеизложенных исследований, выглядит следующим образом: Fe 3 C → Fe 3 C + Fe 20 C 9 → Fe 20 C 9 → Fe 20 C 9 + Fe 4 C → Fe 4 C.
Исследования, выполненные методом РЭМ, показали, что зерна перлита и феррита после различных этапов изготовления, как и в исходном образце, располагаются друг относительно друга случайным образом. При этом размеры зерен соизмеримы. На рис. 2 приведены изображения зеренной структуры стали 35ХГС, полученные методом РЭМ. Видно, что по контрасту зерна феррита и перлита, как и в исходном образце, практически не различимы. По размерам зеренная структура довольно однородна.
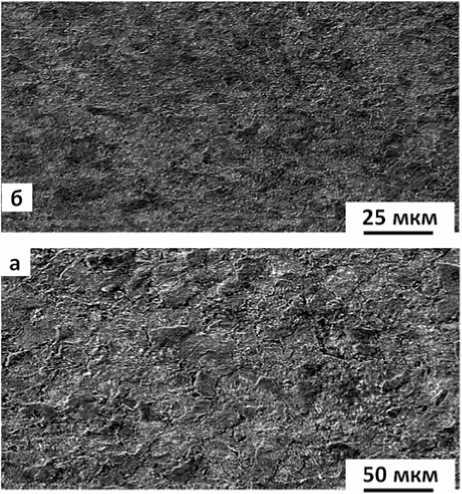
Рис. 2. Изображения зеренной структуры в стали 35ХГС, полученные методом РЭМ: а - обр. №2; б - обр. №3.
Данные РСА показали, что параметр кристаллической решетки α -фазы для всех образцов составляет величину, равную 0,286640 ± 0,00005 нм. Это означает, что α -фаза в основном состоит из железа, легирующих элементов в α -твердом растворе практически нет. Судя по величине параметра кристаллической решетки в α -твердом растворе углерод отсутствует.
Дальнодействующие поля напряжений (поля растяжения-сжатия) σ д измерялись методом РСА по размытию дифракционных линий, внутренние поля за счет дислокаций «леса» σ Л и локальные внутренние поля напряжений σ лок - методом ПЭМ: σ Л - из величины скалярной плотности дислокаций, σ лок - по величине кривизны-кручения кристаллической решетки. Внутренние напряжения во всех морфологических составляющих стали растут по мере изготовления изделия. Во-первых, всегда амплитуда выше, нежели σ лок , однако увеличение σ лок более значительно. Во-вторых, σ Л в феррите выше, чем в перлите, а σ лок – наоборот, ниже.
Выводы:
-
1. Исследовано структурно-фазовое состояние стали 35ХГС на стадии заготовительного производства (после механо-термической обработки) в поверхностном слое и на глубине 1,0 и 1,5 мм от поверхности; а также на этапе получистовой механической обработки (глубина снятого слоя составляет 1 мм) и чистовой механической обработки (суммарная глубина снятого слоя составляет 1,5 мм по сравнению с исходным образцом). Установлено, что поверхностный слой исследованной заготовки имеет полностью фрагментированную структуру, которая состоит из микрозе-ренной феррито-перлитной смеси. После проведения механической обработки во всех образцах присутствуют ферритные зерна в двух состояниях: нефрагментированном и фрагментированном состоянии. Перлитные зерна присутствуют трех видов. Весь перлит является дефектным. Объемные доли каждой структурной составляющей на разных этапах изготовления изделия различны.
-
2. В перлитных зернах термомеханическая обработка уже на первом этапе изготовления изделия (обр. № 2) привела к изменению в структуре перлита. Эти изменения заключаются в изменении морфологии перлита и разрушении цементита в перлите.
-
3. Исследования, выполненные методом РЭМ, показали, что зерна перлита и феррита после различных этапов изготовления, как и в исходном образце, располагаются друг относительно друга случайным образом. По размерам зеренная структура довольно однородна.
-
4. Параметр кристаллической решетки α -фазы для всех образцов составляет величину, равную 0.286640 ± 0.00005 нм. Это означает, что α -фаза в основном состоит из железа, легирующих элементов в α -твердом растворе практически нет.
-
5. Внутренние напряжения во всех морфологических составляющих стали растут по мере изготовления изделия.
Список литературы Исследование структурно-фазового состояния металла как параметра качества обрабатываемых поверхностей деталей машин
- Суслов, А.Г. Инженерия поверхности деталей -резерв в повышении конкурентоспособности машин//Инженерия поверхности. Приложение к журналу «Справочник. Инженерный журнал». -М.: Машиностроение. -2001. -№4. -С. 3-9.
- Качество машин: Справочник. В 2 т. Т1/А.Г. Суслов, Э.Д. Браун, Н.А. Виткевич и др. -М.: Машиностроение, 1995. -256 с.: ил.
- Качество машин: Справочник. В 2 т. Т2/А.Г. Суслов, Ю.В. Гуляев, А.М. Дальский и др. -М.: Машиностроение, 1995. -430 с.: ил.
- Гриднев, В.Н. Распад цементита при пластической деформации стали/В.Н. Гриднев, В.Г. Гаврилюк//Металлофизика. -1982. -Т.4, №3. -С. 74-87.
- Нестерова, Е.В. Кристаллографические особенности внутреннего строения колоний деформированного пластинчатого перлита/Е.В. Нестерова, В.В. Рыбин, Н.Ю. Золоторевский//ФММ. -2000. -Т.89, №1. -С. 47-53.
- Белоус, М.В. Состояние углерода в холоднодеформированной стали/М.В. Белоус, Г.М. Молчановская, В.Б. Новожилов, В.Т. Черепин//Металлофизика и новейшие технологии. -1994. -Т.16, №2. -С. 52-60.
- Счастливцев, В.М. Структурный и кинетический аспекты отжига тонкопластинчатого перлита/В.М. Счастливцев, Д.А. Мирзаев, И.Л. Яковлева//Изв. вузов. Черная металлургия. -1996. -№5. -С. 50-59.
- Козлов, Э.В. Влияние типа субструктуры на перераспределение углерода в стали мартенситного класса в ходе пластической деформации/Э.В. Козлов, Н.А. Попова, Л.Н. Игнатенко и др.//Изв. вузов. Физика. -2002. -№3. -С. 72-82.
- Козлов, Э.В. Эволюция фазового состава, дефектной структуры, внутренних напряжений и перераспределение углерода при отпуске литой конструкционной стали/Э.В. Козлов, Н.А. Попова, О.В. Кабанина и др. -Новокузнецк: Изд-во СибГИУ, 2007. -177 с.
- Козлов, Э.В. Градиентные структуры в перлитной стали/Козлов Э.В., Громов В.Е., Коваленко В.В. и др. -Новокузнецк: Изд-во СибГИУ, 2004. -224 с.
- Смирнов, А.Н. Субструктура, внутренние поля напряжений и проблема разрушений паропроводов из стали 12Х1МФ/А.Н. Смирнов, Э.В. Козлов. -Кемерово: Кузбассвузиздат, 2004. -163 с.