Исследование структуры поверхности Fe-Cr-Ni катализатора, полученного из стали 12Х18Н10
Автор: Мельников Алексей Александрович, Филипченко Сергей Владимирович, Мазницына Елена Александровна, Еменева Анастасия Юрьевна
Журнал: Известия Самарского научного центра Российской академии наук @izvestiya-ssc
Рубрика: Механика и машиностроение
Статья в выпуске: 6-2 т.17, 2015 года.
Бесплатный доступ
В данной статье рассмотрено формирование структуры поверхности металлического гетерогенного катализатора из проволоки стали 12Х18Н10.
Катализатор, оксиды металлов, удельная поверхность, наночастицы
Короткий адрес: https://sciup.org/148204268
IDR: 148204268
Текст научной статьи Исследование структуры поверхности Fe-Cr-Ni катализатора, полученного из стали 12Х18Н10
Катализаторы, используемые в промышленности, должны обладать постоянной высокой каталитической активностью, селективностью, механическойпрочностью, термостойкостью. устойчивостью к действию каталитических ядов, большой длительностью работы, легкой регенерируемостью, малой стоимостью. Эти требования относятся, в первую очередь, к катализаторам для гетерогенного катализа [1].
В гетерогенном катализе активность катализатора, как правило, пропорциональна его удельной поверхности. Большой удельной поверхностью обладают пористые высокодисперсные катализаторы или катализаторы, полученные нанесением активных компонентов на пористые носители. Чем выше пористость катализатора и чем меньше диаметр пор, тем больше внутренняя поверхность. Современные катализаторы характеризуются большими значениями удельной поверхности (до 10–100 м2/г) [2].
Важным свойством катализатора является механическая прочность катализатора, которая обеспечивает его длительную эксплуатацию. Прочность определяется количеством контактов между зернами катализатора и при увеличении пористости уменьшается. Поэтому в некоторых случаях подбирают оптимальную пористость катализатора для сохранения его прочности при необходимом значении внутренней поверхности.
Металлические (реже оксидные) катализаторы готовят обычно нанесением активного компонента на носитель. Выбранный носитель
(Al2О3, силикагель и т.д.) пропитывают раствором, содержащим необходимые компоненты катализатора, подвергают сушке и нагреванию. Окончательно металлические катализаторы требуемой дисперсности формируются при нагревании, восстановлении оксидов восстановителями (Н2, СО) перед катализом или непосредственно во время катализа. Однако механическая прочность таких катализаторов недостаточна. Давление лежащих выше слоев, механические воздействия при загрузке и выгрузке, изменение температуры, эрозия потоками жидкости или газа приводит к истиранию частиц при ударах друг о друга и о стенки реакторов. В связи с этим перспективными являются катализаторы на термостойких носителях, которые можно получить, используя в качестве основы железо-никель-хромовую проволоку. Они могут быть использованы при процессах с большим тепловым эффектом, например, катализаторы глубокого окисления углеводородов.
МЕТОДИКА ЭКСПЕРИМЕНТА
В качестве основы для получения железо-никель-хромового катализатора была выбрана проволока марки 12Х18Н10. Спрессованные из проволоки брикеты помещались в реактор, в котором проходил многократный процесс окисления восстановления.
Изменения структуры и химического состава поверхности на различных стадиях процесса наблюдались на модельных образцах с помощью электронного микроскопа. Изучение микроструктуры проводилось на электронном растровом сканирующем микроскопе TESCAN Vega SB. Определение элементного состава фаз осуществлялось с помощью энергодисперсионного детектора микрорентгеноспектрального анализа INCAx-act.
Общий вид исходного образца катализатора из стали 12Х18Н10 показан на рис. 1. Толщина исходной проволоки составляла 0,2 мм.
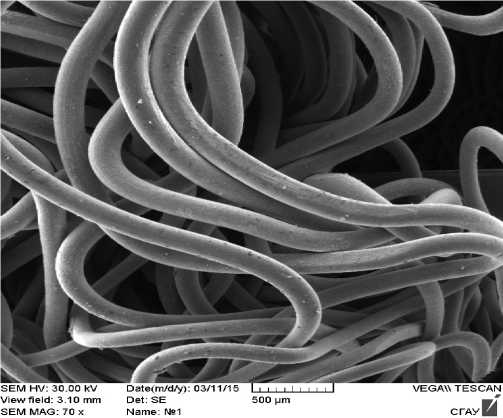
железо-никелевый катализатор
После окисления
Рис. 1. Заготовка катализатора
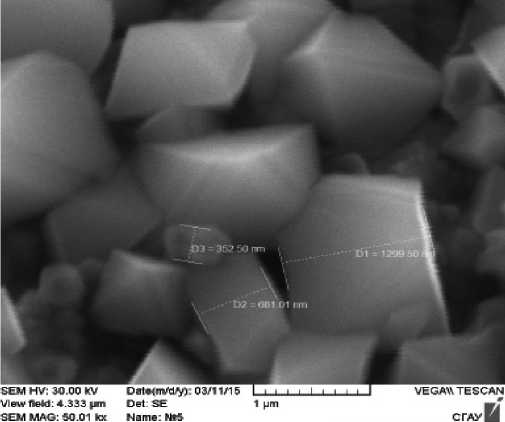
железо-лмелевьы катагеемтор После оеэесленмя
Рис. 3. Кристаллы оксидов на поверхности металла
в исходном состоянии
АНАЛИЗ РЕЗУЛЬТАТОВ
Согласно определению, катализатор остается химически неизменным после завершения реакции. Однако при гетерогенном катализе, обычно протекающем при высоких температурах, неизбежно изменяется физическое состояние катализатора, прежде всего микроструктура его поверхности. Это связано с процессами окисления – восстановления, а также с механическими воздействиями на поверхность гранул.
Нагрев до температуры 950 оС приводит к окислению металла. В начальный момент на поверхности появляются сферические зародыши оксидов (рис. 2).
При следовании на электронном микроскопе можно увидеть оксиды в виде правильно ограненных кристаллов размером от 300 до 1300 нм (рис. 3).
В процессе работы в реакторе происходит многократное изменение температуры в диапазоне 600-9500С, что приводит к окислению металла. Подача углеводородов вместе с водой приводит к их диссоциации с образованием водорода и оксида углерода СО. Это вызывает восстановление образовавшихся оксидов. В результате металл проволоки превращается в прочную твердую пористую губку (рис. 4).Исследования показали, что зерна свежеприготовленного катализатора имеют сильно развитую поверхность с большим числом мелких пор.
На поверхности катализатора хорошо видны кристаллы оксидов, покрытые мелкими светлыми округлыми частицами (рис. 5). Размер кристаллов оксидов составляет 7-15 мкм.
Элементный состав катализатора приведен в табл. 1.
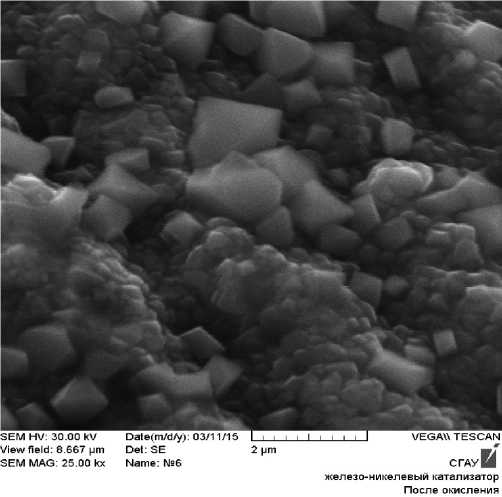
Рис. 2. Поверхность металла после начальной стадии окисления
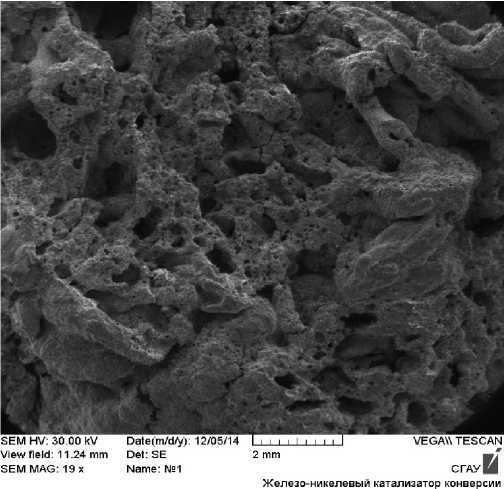
Рис. 4. Поверхность сформировавшегося катализатора
Таблица 1. Элементный состав катализатора
Элемент |
Весовой % |
Атомный % |
C |
11.32 |
23.62 |
O |
32.23 |
50.49 |
Si |
0.98 |
0.88 |
Cr |
7.98 |
3.85 |
Mn |
0.94 |
0.43 |
Fe |
39.48 |
17.72 |
Ni |
7.08 |
3.02 |
Итого |
100.00 |
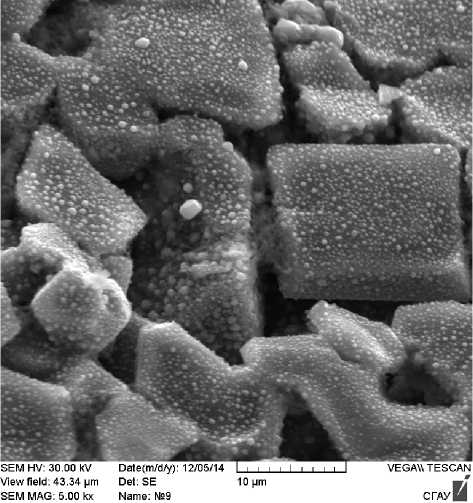
Железо-никелевый катализатор конверсии
Рис. 5. Кристаллы оксидов на поверхности готового катализатора
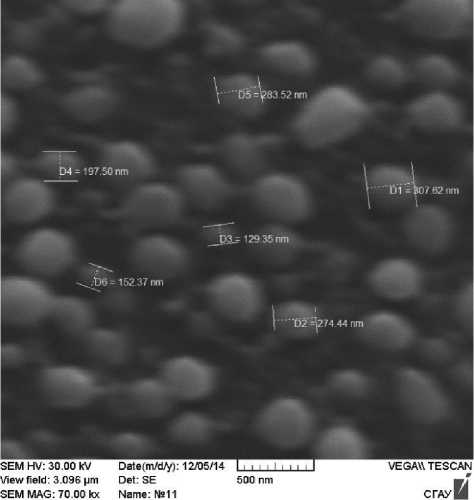
Железо-никелевый катализатор конверсии
Рис. 6. Светлые выделения на поверхности
кристаллов оксидов катализатора
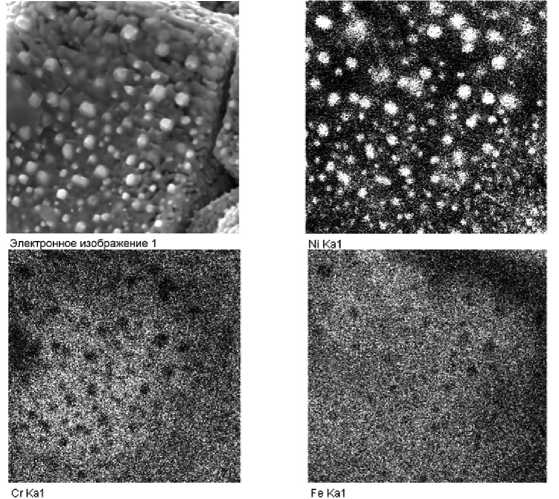
Рис. 7. Карты распределения элементов
Детальное исследование светлых выделений на поверхности кристаллов позволило определить их размер, который составляет от 100 до 300 нм (рис.6).
Анализ карт распределения элементов по площади исследуемой поверхности позволил определить, что мелкие округлые выделения соответствуют максимально высокому содержанию никеля (рис. 7).
Таким образом, исследования показали, что использование проволоки из стали 12Х18Н10 в качестве основы катализатора в процессе многократного нагревания и охлаждения в интервале температур 620-950 оС в среде углеводородов сопровождается процессами окисления-вос- становления. Это позволяет создать на ее базе металлический гетерогенный катализатор. Поверхность катализатора состоит из кристаллов оксидов железа и хрома с выделениями наночастиц никеля. Опытная эксплуатация показала высокую эффективность и достаточную прочность полученного катализатора.
Список литературы Исследование структуры поверхности Fe-Cr-Ni катализатора, полученного из стали 12Х18Н10
- Жуховицкий А.А., Шварцман Л.А. Физическая химия: учеб.для вузов. 4-е изд. М.: Металлургия, 1987. 686 с.
- Грег С., Синг К. Адсорбция, удельная поверхность, пористость: Пер. с англ. 2-е изд. М.: Мир, 1984. 306 с.