Исследование структуры сложных поверхностей деталей после дробеструйной обработки
Автор: Люшня Д.В., Носов Н.В.
Журнал: Известия Самарского научного центра Российской академии наук @izvestiya-ssc
Рубрика: Машиностроение и машиноведение
Статья в выпуске: 4-2 т.25, 2023 года.
Бесплатный доступ
В статье показано, что для определения параметров структуры поверхности необходимо применение оптических методов исследования. Разработан оптико-электронный комплекс , который позволяет определять амплитуду и средний шаг корреляционной поверхности в зависимости от режимов и условий дробеструйной обработки. Предложена методика измерения и программный комплекс по определению параметров структуры поверхности. Проведена идентификация структурных параметров с параметрами шероховатости сложных поверхностей.
Структура, микрорельеф, сложная поверхность, цифровое изображение, корреляционная обработка, идентификация, шероховатости сложных поверхностей
Короткий адрес: https://sciup.org/148327965
IDR: 148327965 | DOI: 10.37313/1990-5378-2023-25-4(2)-278-286
Текст научной статьи Исследование структуры сложных поверхностей деталей после дробеструйной обработки
EDN: ORUCBG
Структурный анализ поверхности занимает важное место в оценке качества поверхности деталей машин. Основой в оценке структуры лежит компьютерная обработка изображений различной природы. Широкое применение компьютерных методов структурного анализа нашли в материаловедении, медицине, криминалистике, при обработке изображений земной поверхности, полученных из космоса и аэрофотосъёмкой, а также в ряде других областей человеческой деятельности. К основным задачам структурного анализа относятся : выбор и формирование признаков, описывающих структурные различия; выделение и сегментация структур; классификация структур ; идентификация структур. Установлено, что в настоящее время не существует чёткого математического определения понятия структуры. В связи с этим методы описания структур и их различия, как правило, разрабатываются эвристически отдельно для каждого конкретного случая. В работах [1-3] и ряде зарубежных отечественных авторов представлены различные подходы к математическому описанию структур и методам их идентификации.
Для аналитического описания структур применяется ряд математических моделей. Среди них известны Time-series модель, ячеистая модель, синтаксические структурные модели, двумерная модель случайного марковского поля. Эти модели обычно применяются для воспроизводства внешнего вида структуры.
Для описания структуры изображения и её количественной оценки достаточно часто применяется метод, основанные на измерении пространственной частоты.
Системный анализ показал, что с точки зрения минимизации временных затрат при их реализации наиболее перспективным является использование метода измерения пространственных частот микрорельефа поверхностей. К группе частотных методов относится и метод цифровых преобразований, при котором в качестве характеристики структуры используется количество перепадов яркости на единицу площади изображения.
В нашей работе применен метод описание структуры с помощью автокорреляционной функции. Развитие данного метода связано с решением задач распознавания микрорельефов механически обработанных сложных поверхностей непосредственно в производственных условиях.
Многочисленными исследованиями установлено существенное, а в некоторых случаях и определяющее воздействие структуры рабочих поверхностей деталей взлетно-посадочных устройств на их надёжность и долговечность при эксплуатации [4-6].
В работе был применен оптико-электронный метод исследования, основанный на разработке теоретических основ реализации нового метода идентификации микронеровностей поверхности деталей. Сущность разработанного метода заключается в сравнении изображения структуры анализируемой поверхности с изображениями структур эталонных поверхностей, для которых заранее определены параметры шероховатости по стандартным методикам, например с помощью профилографа. В результате сравнения определяется (с заданной вероятностью) соответствие изображения структуры образцовой поверхности изображению структуры исследуемой поверхности. На основе этого ана- лиза было установлено, что поставленная задача может быть решена с использованием метода согласованной фильтрации. В работе было принято предположение, что входное изображение исследуемой поверхности x(n1, n2) обрабатывается линейной дискретной системой. В этом случае задача идентификации двумерного сигнала определённой формы решается с помощью согласованного с сигналом двумерного пространственного фильтра, отклик которого описывается выражением
∞∞
У ( n l ’ n 2) = ^ 2 u ( k l ’k 2) ^ k l — ( n l — n 01 ), k 2 — ( n 2 — n 02 )], k 1 =—^ k 2 =—^
(1) которое представляет собой двумерную свёртку сигнала u ( k ^ , k 2) и импульсной характеристики фильтра x [ k 1 — ( n — n 0l), k 2 — ( n 2— n 02)] . При этом импульсная характеристика фильтра получается из ожидаемого двумерного сигнала путём его зеркального отражения относительно координатных осей n и n 2 , и смещения отражённого сигнала в сторону исходного на П 01, П 02 отсчётов. Выходной сигнал y ( n1 , n 2) будет пропорционален автокорреляционной функции двумерного входного сигнала и будет достигнуто максимальное отношение сигнала к помехе на выходе фильтра. Разработан метод обработки изображения анализируемой поверхности для получения автокорреляционной функции, представленный на рисунке 1.
При каждом совмещении эталона U ( n , П 2 ) и текущего фрагмента полутонового изображения X ( n , n 2 ) подсчитывается коэффициент корреляции по известной формуле [6].
Л 1— 1 у н
ZZ ( m ( n l ’ n 2 ) — m u ) - ( xnn l — k l ’ n 2 — k 2 ) — m x ) r xy ( k l ’ k 2 ) = --------------------------------------------,
0 - ° 2
где ( n , n 2 ) индексы элементов эталонного окна, ( k 1 , k 2) - координаты эталона внутри зоны поиска K 1 х K 2, а < 7 1 и < 7 "2 - средние квадратические отклонения величин u ( n 1 , n 2 ) и X ( n 1 , n 2 ) от их математических ожиданий mu и mx соответственно. Закончив вычисление коэффициентов корреляции в первой полосе, задаётся следующая полоса того же формата, что и предыдущая, но смещённая вниз на один пиксель. В этой полосе по центру задаётся новый эталон с теми же размерами, что и предыдущий, и выполняются те же самые действия и.т.д. После обработки всего изображения в запоминающем устройстве будет сформирована матрица M 1 х M 2 коэффициентов корреляции или двумерная автокорреляционная функция. Анализируя выражение (2), можно отметить, что его числитель и знаменатель представляют из себя суммы произведений сигналов x ( n 1 , n 2) и u ( n 1 , n 2) . Следовательно, эти сигналы будут подвержены мультипликативному воздействию функции влияния f зл ( Д ф , д а ).
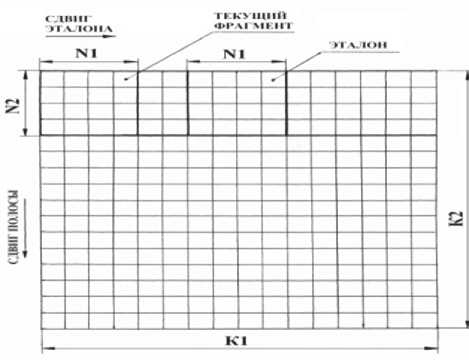
Рис. 1. Схема перемещения эталона
2 ^« п ^, П 2 ) — m, ) - f.„ ( Д Ф ,Д а ) - ( x ( ^— k l, П 2 — k J — m , ) - f ( Д ф ,д а ) r" (A’ k 2) = o l - f . ( Д Ф, Да ) О 2 - f , ( Д Ф .Д а ) '
Как видно из приведённого выражения, его структура соответствует структуре выражения (1) и функции влияния сокращаются. Следовательно, функцию (3) можно рассматривать как частный случай отношения (1) и утверждать, что она обладает искомым компенсационным свойством для устранения дополнительной погрешности, возникающей при оценке параметров микрорельефа непосредственно по видеосигналу, не требуя при этом введения дополнительной аппаратуры.
МЕТОДЫ ИССЛЕДОВАНИЯ
В исходном полутоновом кадре формата K 1 х K 2 пикселей, начиная с первой строки, выделяется полоса шириной в N 2 пикселей. По центру этой полосы задаётся эталон размером N 1 х N 2 пикселей. Затем эталон, начиная с крайней левой позиции, перемещается по выделенной полосе с шагом в 1 пиксель.
Для проведения исследований поверхности деталей взлетно-посадочных устройств был разработан переносной оптико-электронный комплекс для бесконтактного контроля геометрии, размеров и качества поверхности различных деталей в режиме 2D, представленный на рис.2. Комплекс обеспечен ноутбуком ( персональным компьютером), для которого в процес- се исследования разрабатывались специальные алгоритмы и программы. В качестве видеокамеры использовалась камера DIGITAL CAMERA Computar ZC-F11CH3, на выходе которой формировались чёрно-белые изображения заданного формата.
Мощность светового потока, падающего на исследуемую поверхность, в проведённых исследованиях изменялась варьированием напряжения питания лампы накаливания мощностью P = 60 Вт и U = 36 В . Питание подавалось от стабилизированного источника постоянного напряжения. Измерение освещённости исследуемой поверхности производилось люксметром марки 1016М, который располагался перпендикулярно падающему световому потоку . При этом площадь светового пятна на поверхности люксметра составляла S =0,00126 м2 . Мощность светового потока Ф (в люменах) определялась с помощью известного соотношения Ф = E·S , где E – освещённость, измеряемая в люксах.
Исследования структуры поверхности производилось после дробеструйной обработки деталей из титанового сплава ВТ8 на станках с ЧПУ. Деталь может не сниматься со станка или находиться рядом на столике, переносная видеокамера устанавливается на магнитной опоре над измеряемой поверхностью. Видеокамера передает цифровой сигнал в программный комплекс, который обрабатывает полученный сигнал определяя основные параметры структуры поверхности: среднюю амплитуду автокорреляционной функции Аср, средний шаг автокорреляционной функции Тср и их ошибки. Для сравнения результатов измерения структуры оптическим комплексом , изготавливались образцы –свидетели, которые обрабатывались на станке с ЧПУ с различными режимами дро- беструйной обработки. Затем на образцах-свидетелях определялись стандартные параметры шероховатости поверхности на профилографе модели SJ - 201P.. Найденные значения среднеарифметического отклонения профиля представляют собой средние значения, вычисленные по 10 измерениям для каждого образца. Затем определялись структурные параметры с помощью оптико-электронной системы. Анализируемая поверхность эталонных образцов имела размер 3 X 2,5мм, что соответствовало от 800 до 1000 профилей. Световой поток мощностью 600.10–3 лм падал на исследуемую поверхность под углом 45°. Формат видеокадра, записываемого в память компьютера, составлял 320 х 240 пикселей.
На рисунке 3 показана последовательность определения структурных параметров поверхности в следующим порядке: на реальной поверхности выделялся анализируемый участок (рис. 3а), затем, применяя разработанную методику, преобразуем реальную поверхность в бинарное изображение (рис. 3б) , применяя сканирующую методику движения эталона получаем реальную корреляционную поверхность (рис. 3в) и ее бинарное поле (рис. 3г). Производится статистический анализ полученных результатов, и определяются параметры структуры поверхности.
Программа построена таким образом, что можно построить корреляционный профиль (рис. 4), который чем-то напоминает профилограмму поверхности.
На структурные параметры поверхности оказывает большое влияние скорость дроби в факеле дробеструйной обработки. На рис. 5 показана методика определения структурных параметров поверхности при Vш =70 м/с
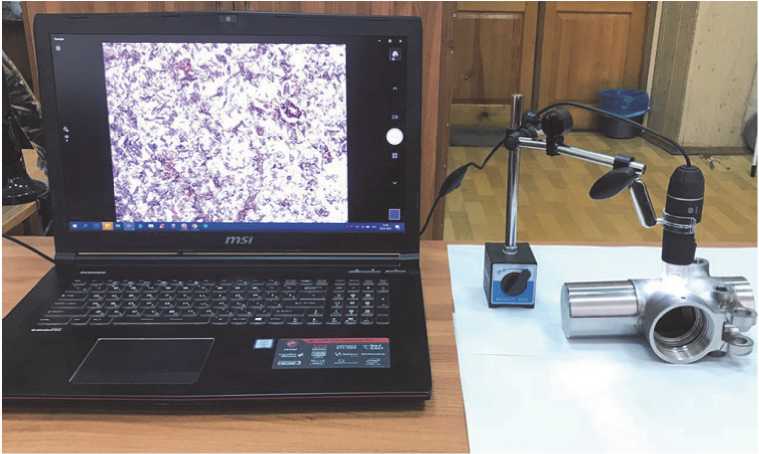
Рис. 2. Оптико-электронный комплекс для измерения параметров структуры сложных поверхностей деталей взлетно-посадочных устройств
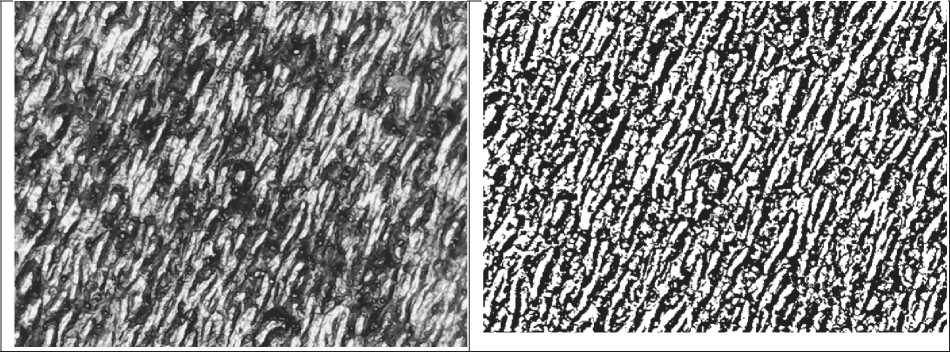
а б
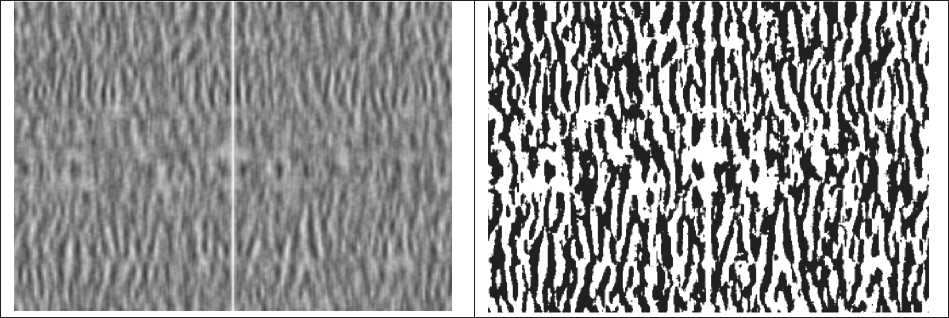
в
г
Рис. 3. Параметры структуры поверхности образца – свидетеля обработанного дробью диаметром 0,6 мм с режимами: скорость движения шариков в факеле Vш =60 м/с, время обработки т = 5- 20 мин, а –электронная фотография, б – бинарное изображение, в – корреляционное изображение, г – бинарное корреляционное изображение
На рис. 6 показаны корреляграммы поверхности образцовm обработанных дробью.
В этом случае можно предложить следующий общий алгоритм оценки микрогеометрии по параметрам структуры.
-
1. Для измеряемой шероховатости промышленного изделия изготавливаются по той же самой технологии образцы- свидетели поверхности с различной шероховатостью, определяемой стандартными, ГОСТовскими методами с помощью образцового средства измерения.
-
2. С помощью оптико-электронного измерительного средства формируются изображения образцовых поверхностей полученных поверхностей, по ним вычисляются корреляционные функции и строится аналитическая зависимость Ra = f ( Аср), Ra = f ( Тср)
-
4. Для заданной вероятности распознавания строится доверительный интервал I p = f (Аср), I p = f ( Тср), в который попадает случайная величина Аср и Тср.
-
5. Для анализируемой поверхности с неизвестной шероховатостью, сформированной по той же самой технологии, с помощью
-
6. Используя полученные зависимости Ra = f (А ср ) и I p = f (А ср ),
оптико-электронного измерительного средства формируется изображение поверхно- сти и определяется Аср и Тср корреляционной функции.
Ra = f (Тср) и I p = f (Тср) определяются Ra, Ramin, Ramax.
По результатам структурного анализа эта- лонов шероховатости поверхности после дробеструйной обработки получены зависимости по влиянию параметров структуры Аср и Тср на параметр Ra поверхности. Отмеченное обстоятельство объясняется возрастающим влиянием регулярной компоненты в формировании микрорельефа исследуемых поверхностей.
Полученные зависимости Ra = f(Аср) могут быть аналитически представлены выражениями вида Ra = К . Аср – В.
В частности, для проведенных исследований по дробеструйной обработке аналитическое выражение будет иметь вид:
Ra = 0,12 . Аср – 1,4 ,мкм; (4) Rz = Тср2 / 8 . rш мкм. (5)
Коррелярограммы поверхности |
Параметры структуры |
А 1.0 ■■ |о.75" 0.25 е го 0 ---------------1---------------1---------------1---------------1---------------1---------------1---------------1---------------1---------------1---------------1---------------1---------------1---------------> 0 40 80 120 160 200 240 280 320 360 400 440 480 пиксели |
А ср = 19,8 Т ср =14,3 ПК или Т ср =71,5мкм |
1 |
|
А гНМйЙйШ# Q --------------1-------------1-------------:-------------1-------------1-------------:-------------1-------------1-------------:-------------1-------------:-------------1-------------5 0 40 80 120 160 200 240 280 320 360 400 440 480 пиксели |
А ср = 20,5 Т ср =16,7 ПК или Т ср =83,5мкм |
2 Л ’r ANMVjw^ ° 0 40 80 120 160 200 240 280 320 360 400 440 480 пиксели |
А ср = 22 Т ср =20,8 ПК или Тср =104 мкм |
3 |
А ср = 23,2
ТС р =25,0 ПК или
Тср =125 мкм
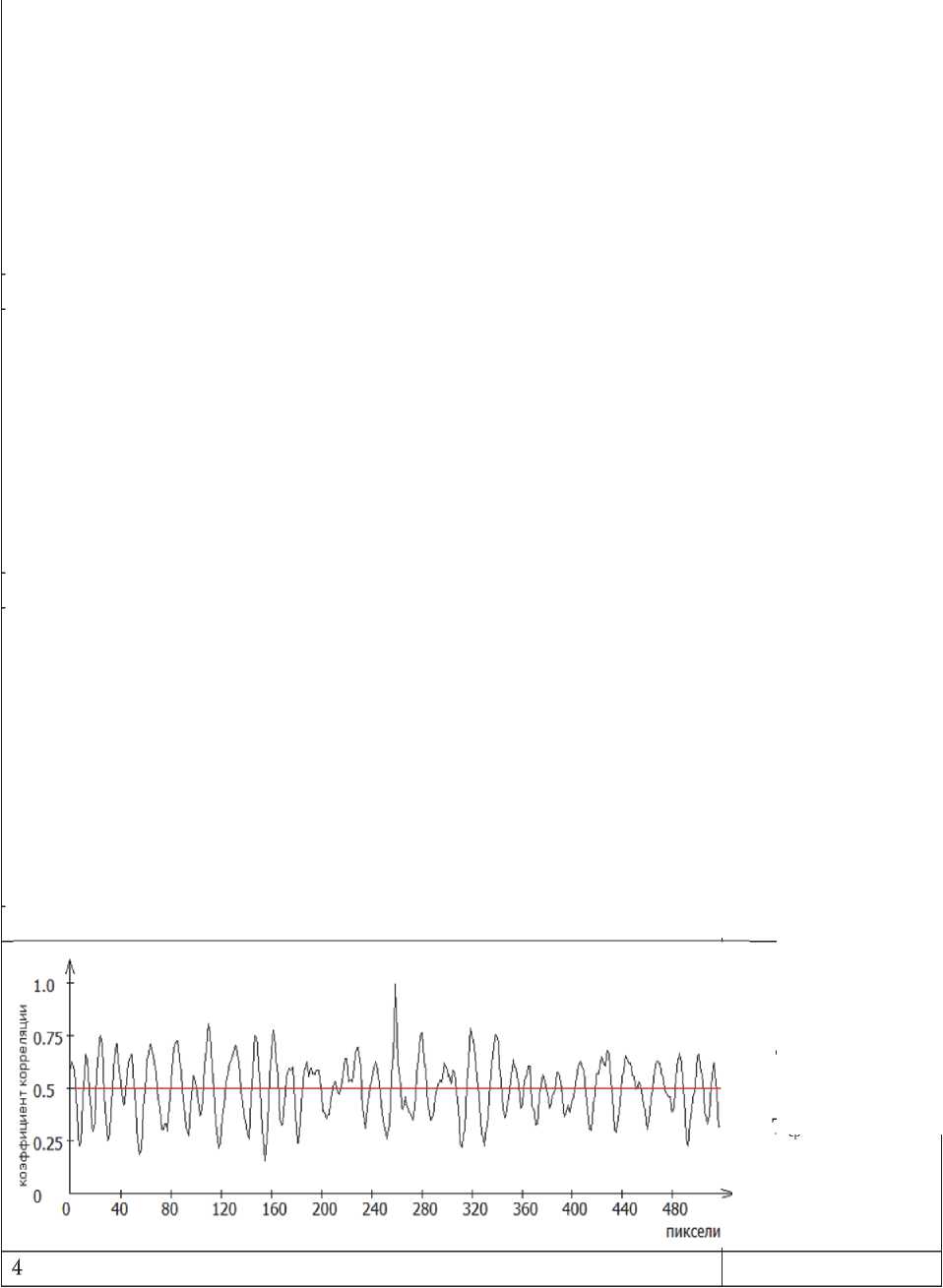
Рис. 4. Коррелялограммы поверхности образцов-свидетелей после дробеструйной обработки шариками d= 0,6 мм со скоростью движения шариков в факеле Vш =60 м/с с режимами τ = 20 мин (1), τ = 15 мин (2), τ = 10 мин (3), τ = 5 мин (4)
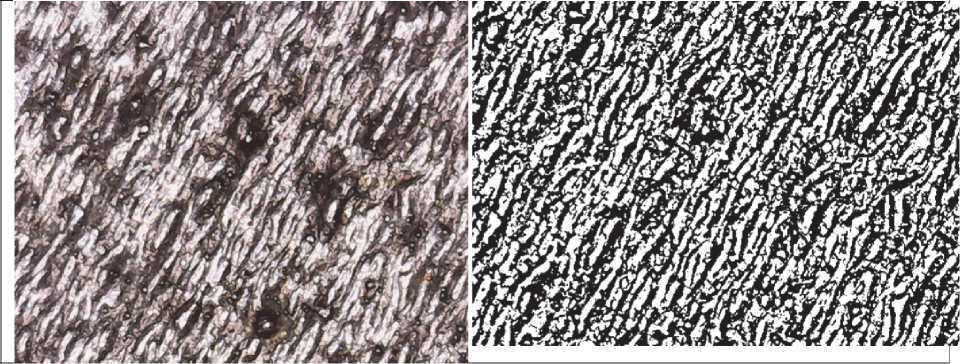
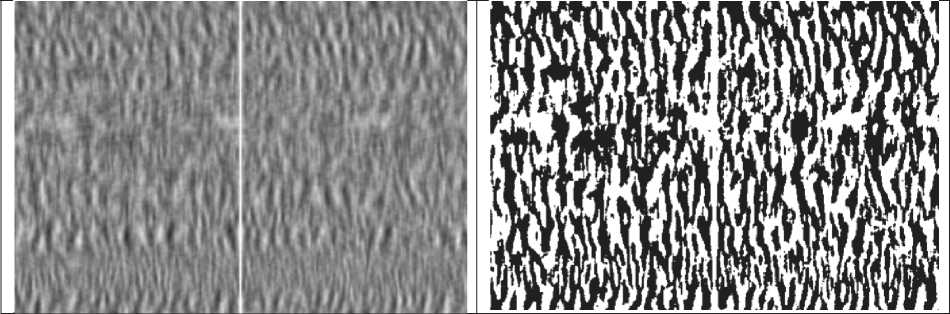
в г
Рис. 5. Параметры структуры поверхности образца – свидетеля обработанного дробью диаметром 0,6 мм с режимами: скорость движения шариков в факеле Vш =70 м/с , время обработки τ = 5- 20 мин, а – электронная фотография, б – бинарное изображение, в – корреляционное изображение, г – бинарное корреляционное изображение
Подставив экспериментальные значения в аналитические зависимости, получим значения Ra, приведенные в табл.1
Для сравнения результатов расчета по формулам 1 и 2 .нужно преобразовать параметр Rz
-
в Ra = Rz / 4 мкм
Анализ полученных зависимостей также показал, что для поверхностей с дробеструйной обработкой наблюдается повышение параметра Ra при увеличении скорости шариков с факеле
Таблица 1. Параметры обработки
Параметры структуры поверхности |
||||
А ср |
Ra, мкм |
Т ср , ПК |
Т ср , мкм |
Rz, мкм |
Скорость движения шариков в факеле Vш =60 м/с |
||||
19,8 |
0.96 |
14,3 |
71,5 |
4,16 |
22,5 |
1,3 |
16,7 |
83,5 |
5.68 |
26,0 |
1.72 |
20,8 |
94,0 |
7,2 |
28,2 |
1.98 |
22 |
110,0 |
9,6 |
Скорость движения шариков в факеле V ш =70 м/с |
||||
17,8 |
0,74 |
11,7 |
61,4 |
3,08 |
19,2 |
0,91 |
12,4 |
68,5 |
3,84 |
20,3 |
1,04 |
13,5 |
72,5 |
4,28 |
21,4 |
1,2 |
16,7 |
81,5 |
4,92 |
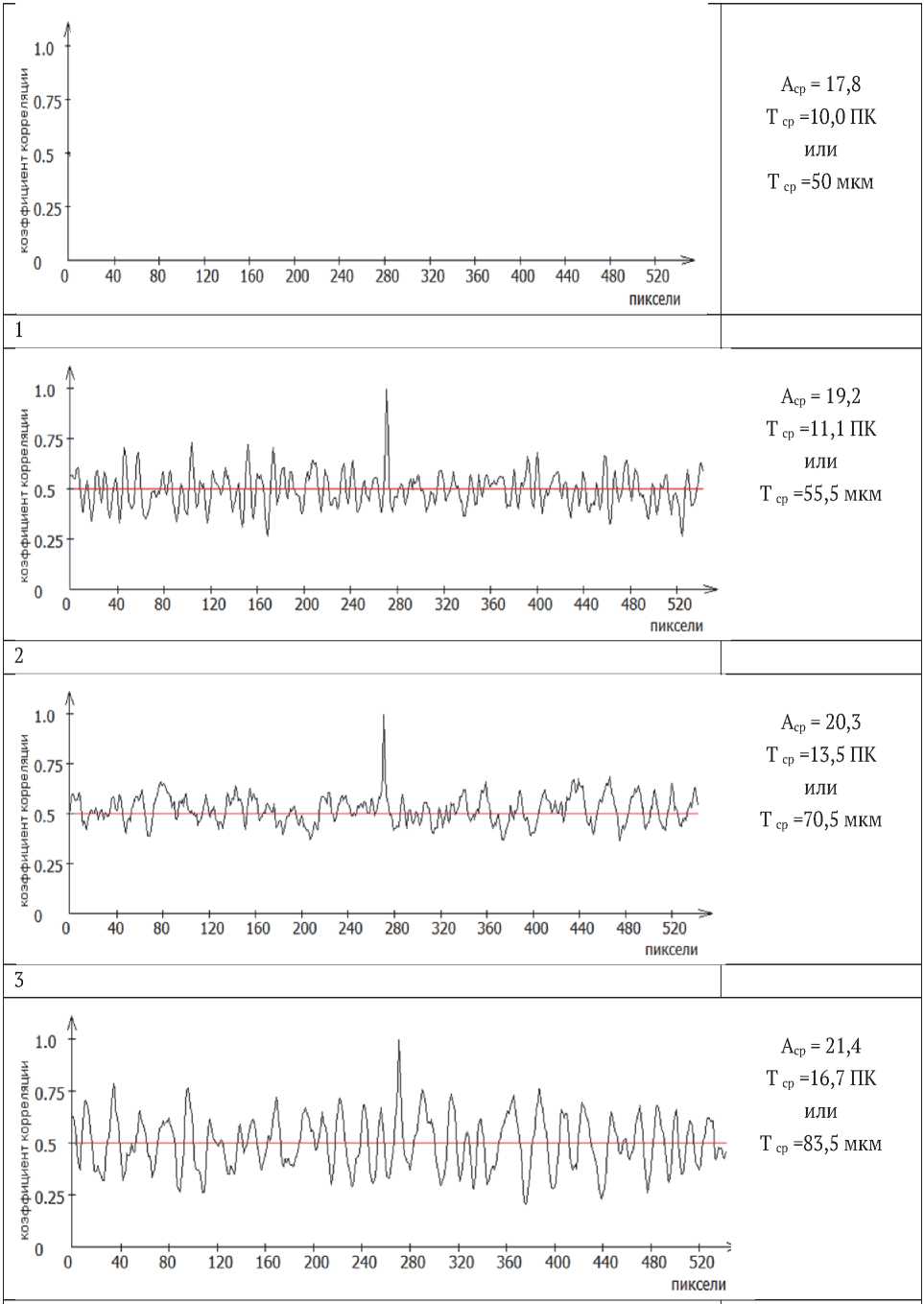
Рис. 6. Коррелялограммы поверхности образцов-свидетелей после дробеструйной обработки шариками d= 0,6 мм со скоростью движения шариков в факеле Vш =70 м/с с режимами τ = 20 мин (1), τ = 15 мин (2), τ = 10 мин (3), τ = 5 мин (4)
1 |
|
^WWV vyvywvvV |
дробеструйной установке и снижение параметров структуры А ср .и Т ср . при увеличении времени обработки. Отмеченное обстоятельство объясняется возрастающим влиянием регулярной компоненты в формировании микрорельефа исследуемых поверхностей.
Список литературы Исследование структуры сложных поверхностей деталей после дробеструйной обработки
- Сойфер, В.А. Анализ и распознавание наномасштабных изображенй: Традиционные подходы и новые постановки задач / В,А.Сойфер, А.В. Куприянов. – 2011. – Т. 35-2. – С. 136-134.
- Баврина, А.Е. Исследование фотограмитрических изображений с помощью матриц вероятномтного распределения яркости / А.Ю. Баврина, Н.Ю. Ильясова, А.В. Куприянов, А.Г. Храмов // Компьтерная оптика. – 2002. – № 23. – С. 62-65.
- Пластинин, А.И. Разработка методов формирования цветотекстурных признаков для анализа биомедицинских изображений / А.И. Пластинин, А.В. Куприянов, Н,Ю. Ильясова // Комьютерная оптика. – 2007.- – Т. 31-2. – С. 82-85.
- Yaйтхаус Д. Metrology of surfaces. Principles of industrial methods and devices, 2009, p 472.
- Garlock Bearings, Inc. (1987), «DU SelfLubricating Bearings», Catalog 781С, Thorofare, New Jersey.
- Constantinou M.C., Whittaker, A.S., Kalpakidis, Y. et al. (2007) ”Performance of Seismic Isolation Hardware under Service and Seismic Loading”, Report MCEER07, State of California Department of Transportation Project 65A0174
- Дунин-Барковский, И. В. Измерения и анализ шероховатости, волнистости и некруглости поверхности / И. В. Дунин-Барковский, А.Н. Карташова. – М.: Машиностроение, 1978. – 232 с.
- Суслов, А.Г. Назначение, обозначение и контроль параметров шероховатости поверхностей деталей машин / А.Г. Суслов, И.М. Корсакова. – М.: МГИУ, 2010. – 111с.
- Линник В.П. Прибор для интерференционного исследования микропрофиля поверхности “микро-профилометр” / В.П. Линник // Докл. АН СССР. – 1945. – Т. 49. – № 9. – С. 656-657.
- Абрамов, А.Д. Оценка параметров микрорельефа поверхностей деталей машин на основе квазиоптимальных корреляционных алгоритмов / А.Д. Абрамов, Н.В. Носов // Вестник компьютерных и информационных технологий. – 2016. – № 9. – С. 19-25.
- Патент 413179 РФ, МПК G01В 11/30 (2006/01), G01N 21/93(2006/01). Способ контроля шероховатости поверхности изделий / А.Д. Абрамов, А.И. Никонов, Н.В. Носов - № 2009109452; Заявл.16.03.2009; Опубл. 27.09.2010, бюл. № 6.