Исследование точности изготовления заготовок соплового аппарата турбины, изготовленных технологией селективного лазерного сплавления на основе краткосрочных контрольных карт качества
Автор: Алексеев В.П., Хаймович А.И., Смелов В.Г., Кокарева В.В.
Журнал: Известия Самарского научного центра Российской академии наук @izvestiya-ssc
Рубрика: Машиностроение и машиноведение
Статья в выпуске: 6 т.25, 2023 года.
Бесплатный доступ
В данной работе представлены результаты исследования точности изготовления секций соплового аппарата турбины, методом селективного лазерного сплавления, на основе краткосрочных контрольных карт качества. Изготовлены секции соплового аппарата турбины, из материала Inconel 738, методом селективного лазерного сплавления на установке SLM 280HL. Проведён контроль геометрических характеристик секций соплового аппарата турбины, изготовленной по аддитивной технологии, на координатно-измерительной машине. Представлена методика модификации номинальных/целевых карт, не увеличивающая длину контрольных карт вне зависимости от количества характеристик качества. Проведена процедура статистического анализа технологического процесса с использованием краткосрочных контрольных карт для количественных данных и оценка возможностей процесса, и его пригодности для выполнения заданных требований. В качестве характеристики качества изделия выбрана точность геометрии профиля пера лопаток секции соплового аппарат, так как она существенно влияет на эксплуатационные характеристики продукции. В результате проведенного статистического анализа установлено, что процесс находится в состоянии статистической управляемости в отношении внутренней изменчивости, процесс пригоден для обеспечения заданных требований и обладает достаточным запасом возможностей, необходимым для эффективного управления ходом процесса.
Селективное лазерное сплавление, металлический жаропрочный порошок, качество, сопловая секция, точность, контрольные карты качества
Короткий адрес: https://sciup.org/148328438
IDR: 148328438 | DOI: 10.37313/1990-5378-2023-25-6-5-11
Текст научной статьи Исследование точности изготовления заготовок соплового аппарата турбины, изготовленных технологией селективного лазерного сплавления на основе краткосрочных контрольных карт качества
В конструкцию современных и перспективных ГТД входит большое множество деталей, отличающихся высокими точностными параметрами, использованием специально профилированной конструкцией и часто наличием скрытых полостей, каналов малого размера.
Характерной особенностью подобных деталей является, в первую очередь, сложность технологического процесса их изготовления, а также механической обработки наружных и внутренних поверхностей.
Среди сложнопрофильных деталей особое внимание в производстве уделяется сопловым лопаткам турбины. Геометрические параметры этих деталей во многом определяют технико-экономические характеристики двигателя в целом.
Качество машиностроительных изделий и сложнопрофильных деталей индустриальных газотурбинных двигателей (ГТД) для газоперекачивающих и энергетических установок, в большей степени определяется используемыми технологическими процессами их изготовления. На сегодняшний день технология селективного лазерного сплавления (СЛС), как один из методов аддитивного производства, позволяет изготавливать сложные конструкции. Однако процесс СЛС обладает изменчивостью вследствие действия на него множества факторов, что приводит к непостоянству показателей качества изготавливаемого изделия.
На сегодняшний день в рамках комплексного проекта по созданию высокотехнологичного производства индустриальных ГТД в результате предварительных испытаний комплексной типовой технологии аддитивного производства деталей и узлов горячей части индустриальных газотурбинных двигателей (ГТД) были получены результаты контроля параметров качества опытных образцов - шероховатости, геометрической точности и параметров технологического процесса – скорость сканирования, мощность лазера, толщина слоя. Также была разработана цифровая модель физико-механических свойств материала для образцов, получаемых по технологии селективного лазерного сплавления металлического порошка жаропрочного сплава ВЖ159, с учетом образования анизотропии свойств при сплавлении, с помощью которой можно управлять параметрами технологического процесса для достижения множественных параметров качества изделий. На основании полученных данных для верификации полученных моделей технологического процесса селективного лазерного сплавления было проведено исследование точности изготовления секций соплового аппарата турбины методом селективного лазерного сплавления на основе краткосрочных контрольных карт качества.
Одним из методов управлением производственным или технологическим процессом, который обладает определенной изменчивостью, вследствие действия на него множества факторов, является статистическое управление процессами с использованием контрольных карт качества. Статистические методы управления качеством наукоемких изделий по сравнению с текущем контролем продукции позволяют выявить на этапе подготовки и планирования производства отклонения от технологического процесса, которые приведут к появлению брака, тем самым формируя прогнозные (предиктивные) модели управления качеством продукции. Статистический метод управления качеством производственного процесса, предложенный Ф. Шухартом, применяется и сегодня в виде контрольных карт, с помощью которых выявляются отклонения производственного процесса, устанавливаются причины их возникновения и возможно прогнозирование дальнейшего хода процесса [1].
Хотя диаграммы Шухарта просты и легки в реализации они предполагают присущую данным процесса нормальность и независимость. Это условие требует надежного набора исто- рических данных для установки допустимых контрольных пределов и оценки параметров процесса [1].
Технология аддитивного производства на сегодняшний день относится к мелкосерийному производству, ближе к единичному. Характерными чертами мелкосерийного производства являются небольшой размер партии, многокомпонентные типы, короткое время выполнения заказа, частые настройки/переналадки и ограниченные данные процесса. Частая на-стройка/переналадка усложняет обнаружение изменений, связанных со временем, и беговые вариации. Кроме того, ожидается, что данные для краткосрочных периодов будут автокорре-лированы.
Очевидно, что если стандартный контроль качества используется для управления технологическим процессом сложной детали с большим количеством характеристик качества, то количество контрольных карт и показателей возможностей становится очень большим. Эта ситуация распространена в аэрокосмической промышленности, где детали, как правило, очень сложные. Например, сопловые секции турбины имеет более 20 основных характеристик, каждая из которых имеет свой набор допусков. В таком случае количество контрольных карт, необходимых для мониторинга процесса, будет больше 50, а количество индексов возможностей будет больше 100, чтобы полностью охарактеризовать возможности процесса. В целях управления технологическим процессом и соответствия сложной детали трудно отслеживать такое количество контрольных карт и индексов возможностей.
Краткосрочный статистический контроль процессов – инструмент для управления процессами изготовления сложных деталей. Для переменных данных он может сократить количество контрольных карт до двух независимо от количества характеристик качества на деталь. Однако длина краткосрочных контрольных карт увеличивается на коэффициент, равный количеству характеристик качества. Если детали сложные со многими характеристиками качества, такие диаграммы быстро становятся загруженными и трудными для интерпретации. Кроме того, краткосрочные диаграммы подвержены неправильному толкованию, особенно если количество характеристик качества превышает семь. Чтобы оценить способность процесса характеристики качества соответствовать двусторонним допускам, требуется набор из четырех индексов способности. Сложная деталь со многими качественными характеристиками может иметь в четыре раза больше показателей возможностей. Отслеживание большого количества индексов возможностей обременительно.
Существует потребность в методологии для уменьшения количества диаграмм при сохранении хронологии процесса. Краткосрочный контроль процесса — это устоявшаяся методология, позволяющая сократить количество контрольных карт до одной диаграммы для атрибутивных данных или до одного набора из двух диаграмм для переменных данных независимо от количество качественных характеристик на деталь [2].
Целью данной работы является контроль качества изготовления деталей со сложной геометрией на малых сериях с использованием адаптированных карт.
МЕТОДИКА ИССЛЕДОВАНИЙ И ОБОРУДОВАНИЕ
Объектами исследования являются секции соплового аппарата турбины, изготовленные технологией СЛС металлического порошка жаропрочного сплава Inconel 738. Изготовление секций соплового аппарата турбины, выращенных из металлического порошка (средний диаметр частиц составляет 15…53 мкм) жаропрочного сплава Inconel 738 производилось на установке SLM 280HL. Установка имеет камеру построения размером 280×280×280 мм и оснащена иттербиевым волоконным лазером мощностью 400 Вт.
Контроль секций соплового аппарата турбины индустриального ГТД, изготовленной по аддитивной технологии производился на координатно-измерительной машине DEA Global Perfomance 07.10.07 при температуре 20 °С ± 2 °С и относительной влажности 80%. Результаты измерений представлены на рисунке 1.
Статистический анализ данных, полученных в результате экспериментов, выполняли в коммерческом программном продукте STATISTICA. Обработка контрольных измерений осуществлялась на основе краткосрочного контроля процесса.
Предлагаемая методика представляет собой модифицированную версию номинальных/ целевых карт. Следовательно, обычные ограничения номинальных/целевых диаграмм, заключающиеся в том, что дисперсия, связанная с каждой характеристикой качества, должна быть одинаковой, применимы и к модифицированной версии.
Алгоритм предлагаемого метода представлен на рисунке 2.
Модифицированная целевая/номинальные карты основаны на предположении, что нет необходимости поддерживать прослеживаемость каждой характеристики качества при формировании рациональной подгруппы [3]. Вместо этого все качественные характеристики каждой детали из подгруппы могут быть объединены в одну большую подгруппу. Это можно сделать
# l/fcxQfU**! TOW Ao 24 AV / \ V5 22z A \ 21 8 20 1 \ \X xA10 и 19// xXX' X2 18 \ X 16 \ 13 14 15 |
№ точки |
Значение отклонения, мм |
1 |
0,0712 |
|
2 |
0,0512 |
|
3 |
0,0514 |
|
4 |
0,0168 |
|
5 |
0,0167 |
|
6 |
-0,0626 |
|
7 |
-0,18838 |
|
8 |
-0,1964 |
|
9 |
-0,1521 |
|
10 |
-0,0785 |
|
11 |
0,104 |
|
12 |
0,1599 |
|
13 |
0,0103 |
|
14 |
-0,0839 |
|
15 |
-0,0742 |
|
16 |
0,1215 |
|
17 |
0,179 |
|
18 |
0,1828 |
|
19 |
0,1629 |
|
20 |
0,0309 |
|
21 |
-0,0191 |
|
22 |
-0,0478 |
|
23 |
-0,1044 |
|
24 |
-0,084 |
Рисунок 1 – Результаты измерения профиля пера лопатки в одном из сечений
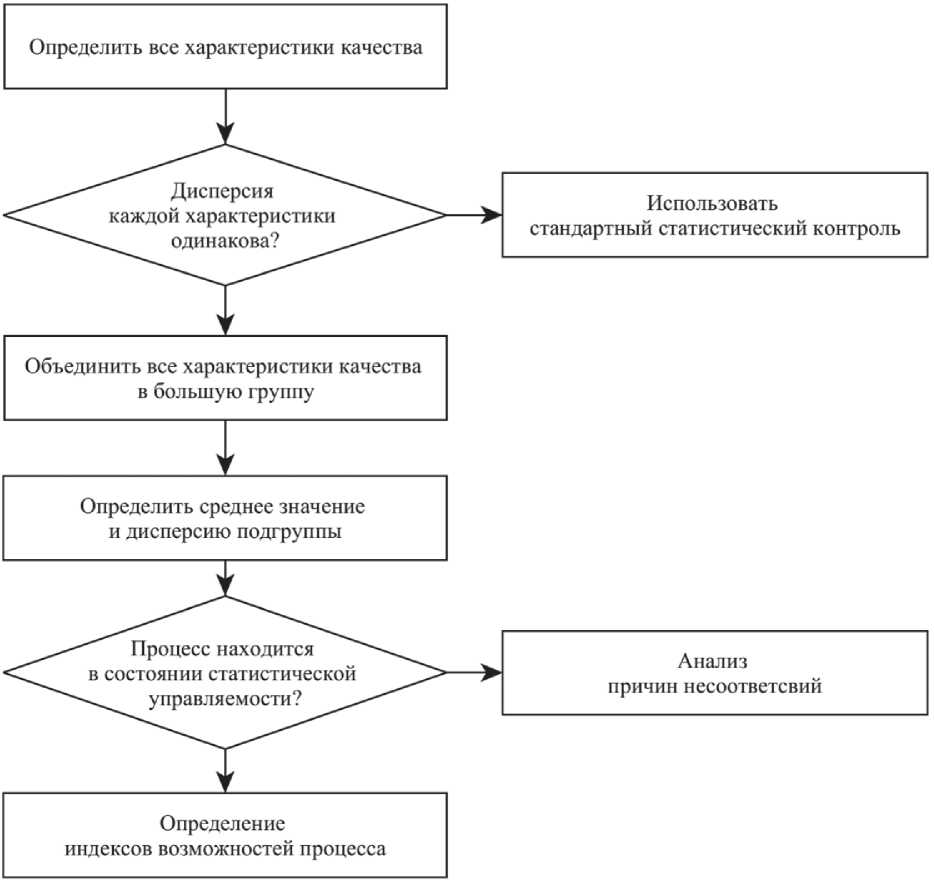
Рисунок 2 – Методика статистического анализа на основе краткосрочных контрольных карт
только в том случае, если дисперсия каждой характеристики качества одинакова. Размер подгруппы в модифицированной схеме является произведением количества показателей качества, приходящихся на одну деталь, и размера рациональной подгруппы, определяемой традиционными методами. Поскольку в новой схеме каждая подгруппа определяет единую характеристику качества для всех членов группы, количество баллов на модифицированной контрольной карте уменьшается на коэффициент, равный количеству характеристик качества по сравнению с контрольной картой.
Если бы на деталь приходилось m характеристик качества, то индексов пригодности для двусторонних допусков было бы в четыре раза больше. Если номинал каждой характеристики качества различен, но допуск один и тот же для каждой характеристики качества, то количество индексов возможностей может быть сокращено до одного набора из четырех, как описано ниже.
C p = ( ВГД - НГД ) /(6а ) = 2Т /(6а );
СР и = ( ВГД - X ) /(З а ) = (Т - X ) /(З а );
С pi = ( X - НГД ) /(З а ) = ( X + Т ) /(З а );
С pk = Min {Cpu; Cpi}, где ВГД – верхняя граница допуска; НГД – нижняя граница допуска; X – среднее значение; ст - среднеквадратичное отклонение.
Таким образом, с измененной схемой количество показателей возможностей было сокращено до одного набора из четырех, независимо от количества характеристик качества. Поскольку s оценивалось на основе всех характеристик качества, индексы возможностей, вычисляемые по новой схеме, представляют весь процесс, а не отдельные характеристики качества. Конечно, этот метод будет работать только в том случае, если допуск для каждой характеристики качества одинаков.
В разработанной методике все характеристики качества всех частей в подгруппе объединяются в большую подгруппу, что сводит к минимуму количество данных на графике и исключает риск неправильной интерпретации состояния процесса.
Вышеупомянутая схема имеет очевидные преимущества. Длина контрольной карты значительно уменьшена, фокус модифицированной диаграммы смещается на весь процесс, а не на отдельные характеристики качества. Кроме того, поскольку размер подгруппы увеличивается, уменьшается ошибка оценки параметров процесса, таких как среднее значение процесса и стандартное отклонение. Недостатком модифицированной схемы является потеря прослеживаемости отдельной характеристики качества.
Модифицированная схема была применена к анализу геометрической точности профиля пера сопловой секции турбины ГТД.
РЕЗУЛЬТАТЫ ИССЛЕДОВАНИЙ
В данной работе в качестве контролируемого геометрического параметра принято отклонение профиля пера от номинальной модели. Лопатка сопловой секции имеет сложный профиль (рисунок 1). Профиль пера измеряется в 24 указанных точках. Секция имеет три профиля пера, что увеличивает количество контрольных точек. В качестве номинального значения принято отклонение равное 0. Отклонение от номинальной модели профиля пера в каждом месте разное, но допуск одинаковый ±0,2 мм.
В целях управления технологическим процессом использовались диаграммы среднего
Хср и скользящего размаха MR. Их каждой толщины вычиталась номинальная, чтобы получить отклонение от номинального.
В модифицированной схеме были получены 34 значения отклонения профиля пера от номинального (1 лопатка, 2 сечения). 34 значения части рассматривались как одна подгруппа и использовались для расчета среднего значения подгруппы Хср и несмещенного стандартного отклонения, S. Конечно, чтобы эта схема работала, должны принадлежать одной и той же системе общей причины, то есть одному и тому же распределению вероятностей. Для проверки построим график нормального распределения (рисунок 3). Данные показывают, что распределение соответствует нормальному примерно со значением р = 0,2.
Графики среднего значения Хср и стандартного отклонения S показаны на рис. 4. Обратите внимание, что всего существует 12 подгрупп, т.е. 12 заготовок секций соплового аппарата турбины, каждая из которых представляет все 34 значения отклонения от номинального значения.
Следует отметить, что оценка возможностей разумна только в том случае, если процесс предсказуем, то есть находится под контролем. Точки выборочных размахов не нарушают границу UCLR = 0,0249 и LCLR = 0, т.е. отсутствует признак 1, а также нет присутствия особых структур точек [4]. Следовательно, процесс находится в состоянии статистической управляемости по скользящим размахам МR, т.е. в отношении внутренней изменчивости.
Индексы производимости можно рассчитать следующим образом:
Т = 0.2 мм – величина допуска;
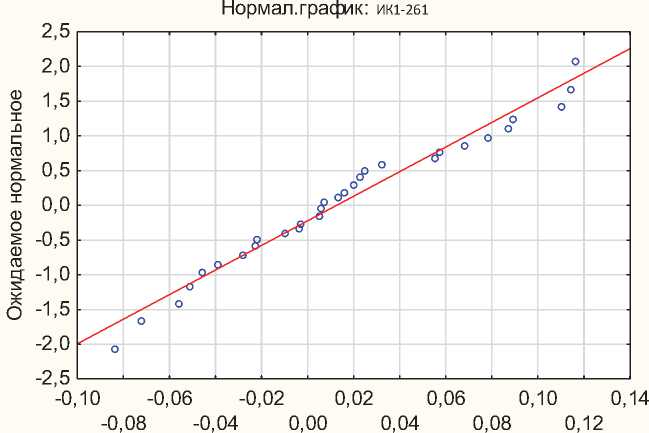
Значение
Рисунок 3 – График нормального распределения для СА ИК1-261 лопатка №1
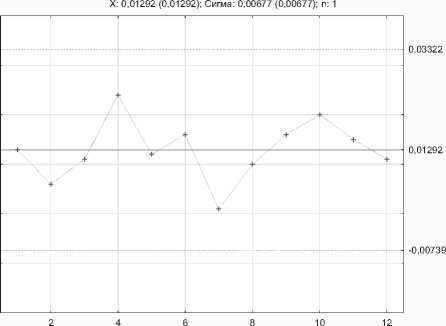
a
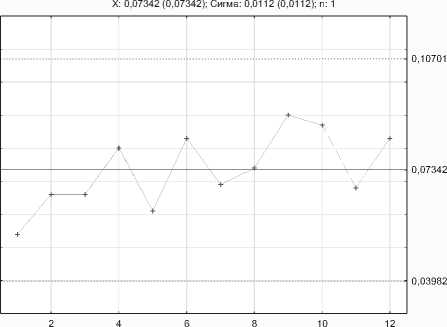
б
Рисунок 4 – График Хср (а) и S-диаграмма (б) для 1 лопатки СА
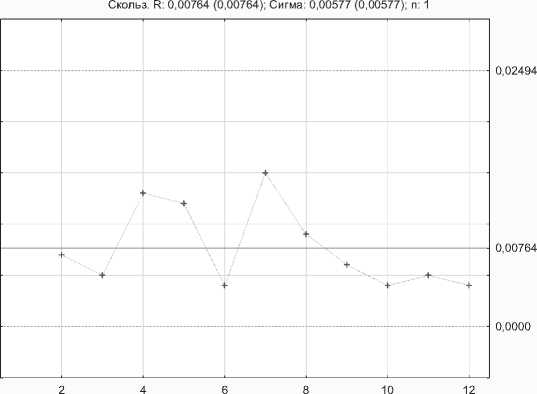
Рисунок 5 – График скользящих размахов MR для Хср
C p = ( ВГД - НГД ) /(6 ^ ) = 2 7 /(6 ^ ) = 4,92; С Р и = ( ВГД - X ) /(3 а ) = ( 7 - X ) /(3 а ) = 4,29; Сp l = ( X - НГД ) /(3 ^ ) = ( X + 7 ) /(3 ^ ) = 5,56;
С pk = Min {Cpu; Cpi }= 4,29, где, ВГД – верхняя граница допуска; НГД – нижняя граница допуска; X – среднее значение; σ – среднеквадратичное отклонение.
Знание величины стандартного отклонения внутренней изменчивости σ позволяет вычислить индекс пригодности (индекс возможностей) процесса. Если Cp >1, то процесс пригоден для выполнения заданных требований и имеется запас возможностей процесса. Для нашего примера Cp = 4,92>1, процесс пригоден для выполнения заданных требований и имеется запас возможностей, достаточный для управления ходом процесса по выполнению заданных требований. Процесс смещен относительно номинала в сторону НГД.
ВЫВОДЫ
Объединяя все характеристики качества в одну подгруппу, модифицированная схема ориентируется на процесс, а не на отдельные характеристики качества. Поскольку размер подгруппы намного больше по сравнению с размером подгруппы обычных краткосрочных диаграмм, ошибка в оценке среднего значения процесса и дисперсии уменьшается.
Независимо от количества характеристик качества модифицированная схема сокращает количество индексов возможностей до одного набора из четырех для двусторонних допусков при условии, что пределы спецификации имеют одинаковую величину.
Для сложных деталей с большим количеством контрольных характеристик очевидно, что при использовании модифицированной схемы достигается значительная экономия в отслеживания процесса.
Процесс селективного лазерного сплавления заготовок секций соплового аппарата пригоден для обеспечения заданных требований и обладает достаточным запасом возможностей, необходимым для эффективного управления ходом процесса: индекс пригодности Cp = 4,92.
Список литературы Исследование точности изготовления заготовок соплового аппарата турбины, изготовленных технологией селективного лазерного сплавления на основе краткосрочных контрольных карт качества
- Национальный стандарт Российской Федерации ГОСТ Р ИСО 7870 - 2 - 2015 Статистические методы Контрольные карты Шухарта (ISO 7870-2:2013, ЮТ) Ч2, Стандартинформ, Москва, 2016.
- Vermin S.K. Application of short-run SPC in manufacturing of complex parts // Proceedings of the 55th Annual Midwest Quality Conference. - 2000.
- Vermani S.K. Modified nominal/target control charts-A case study in supplier development // Quality Management Journal. - 2003. - Т. 10. - №. 4. - С. 8-17.
- Солонин, С.И. Метод контрольных карт: учебное пособие / С.И. Солонин. - 2014. - Екатеринбург: УФУ, 2014. EDN: VGSBSP