Исследование возможности использования отходов огнеупорных и горнодобывающих производств для получения тяжелого магнезиального бетона
Автор: Аверина Галина Федоровна, Зимич Вита Васильевна, Владимиров Константин Дмитриевич, Лазаревич Егор Владимирович
Рубрика: Строительные материалы и изделия
Статья в выпуске: 2 т.18, 2018 года.
Бесплатный доступ
Исследуется возможность использования отходных отвалов комбината ОАО «Группа Магнезит» г. Сатка для производства тяжелого магнезиального бетона. Установлен фракционный и минералогический состав данного вида отходов, выделены и сгруппированы фракции, пригодные для использования в качестве крупного и мелкого заполнителя. Выявлена возможность использования фракций, не входящих в категорию заполнителей, в качестве сырьевого материала для получения магнезиального вяжущего методом комбинированного способа. Выдвинута гипотеза о принципе наилучшей совместной работы продуктов гидратации магнезиального вяжущего и магнийсодержащих заполнителей в составе бетонной смеси за счет сходной минералогии данных компонентов.
Магнезиальные вяжущие, магнезит, тяжелый бетон, фракционный состав, минералогический состав, заполнители
Короткий адрес: https://sciup.org/147232092
IDR: 147232092 | DOI: 10.14529/build180207
Текст научной статьи Исследование возможности использования отходов огнеупорных и горнодобывающих производств для получения тяжелого магнезиального бетона
Горнодобывающая промышленность Российской Федерации находится на втором месте по вредности среди всех прочих отраслей промышленности за счет распространения многотоннажных отходных отвалов на значительные территории. Одним из способов эффективной утилизации такого вида отходов с разным уровнем содержания соединений магния является использование их в качестве сырья для получения магнезиальных вяжущих строительного назначения методом низкотемпературного обжига [1–4].
Изделия на основе магнезиальных вяжущих обладают быстрым набором прочности без тепловой обработки и ее высокими показателями, высокой технологичностью, стойкостью к действию нефтепродуктов, грибков, бактерий, низкой истираемостью [5]. Однако в сравнении с наиболее потребляемым на данный момент вяжущим – портландцементом и различными его разновидностями – потребление магнезиальных вяжущих довольно невелико. Кроме низкой популярности магнезиального вяжущего в целом, это явление можно объяснить тем фактом, что наибольший объем ежегодно производимого цемента используется в качестве вяжущего для получения тяжелого бетона.
Тяжелый бетон – композиционный каменный материал, в состав которого входит матрица минерального или органического вяжущего, а также крупный и мелкий минеральный заполнитель. На данный момент композиционные смеси на основе магнезиального вяжущего представлены в основном строительными растворами и конст- рукционными блоками, дисперсно-армированными древесной шерстью и опилками [6–8].
Таким образом, технология производства классического тяжелого бетона на основе магнезиального вяжущего до сих пор не проработана. Разработка данной технологии производства позволит существенно расширить область применения магнезиальных вяжущих в строительстве, что в свою очередь приведет к росту его популярности в целом и значительно ускорит процесс переработки отвалов отходов магнезиальных производств.
Как правило, магнийсодержащие породы низких сортов, являющиеся отходными отвалами, представляют собой полиминеральную смесь фракции от 0 до 70 мм [9]. Следовательно, можно предположить, что из одного вида заданного сырья с помощью предварительного рассева фракций можно получить не только качественное магнезиальное вяжущее, но и заполнители для производства на его основе тяжелого бетона.
Для обоснования данного предположения целесообразно провести анализ фракционного и минералогического состава выбранного вида сырья, а также определить качественные характеристики полученных заполнителей согласно техническим регламентам.
Анализ фракционного состава необходим для выявления количественного содержания фракций, пригодных для использования в качестве крупного и мелкого заполнителя, а также количества остаточных фракций, предполагаемых в качестве сырья для производства магнезиального вяжущего.
Анализ минералогического состава необходим для выявления количественного содержания магнийсодержащих и примесных минералов в породе с целью назначения оптимального режима обжига [10–12].
Материалы и методы исследования
В качестве материала исследования принят магнезит Саткинского месторождения третьего и четвертого сортов ненормированного фракционного и минералогического состава.
Фракционный состав определяли рассевом проб на ситах, соответствующих техническому регламенту [13]. Сырьевые материалы подвергали комплексному исследованию с применением дериватографии, рентгенофазового анализа и стандартных методов. Термический анализ минералов проводили на дери-ватографе системы Luxx STA 409 немецкой фирмы Netsch. Скорость подъема температуры в печи – 10 °С/мин, максимальная температура нагрева – 1000 °С. Для испытания использовали платиновые тигли, нагревали в среде азота.
Рентгенофазовый анализ проводили на приборе ДРОН-3М, модернизированном приставкой PDWin, при напряжении 30 кВт, силе тока 10 мА и ширине выходной щели 1 мм. Съемки вели в интервале углов 6–70°.
Исследование свойств крупного и мелкого заполнителя проводили согласно стандартным методикам [14, 15].
Исследовательская часть
Для исследования фракционного состава шихты был произведен отбор 38 проб, которые в дальнейшем рассевали на ситах 40, 20, 10, 5, 2,5; 1,25; 0,63; 0,315; 0,16. Полученные остатки на ситах вычислялись в процентах от массы пробы (табл. 1).
Рентгенофазовый анализ проводили с целью выявления минералогического состава зерен фракций >40 и 0,16...0. По результатам рентгенофазового анализа установлено, что помимо основного минерала карбоната магния MgCO 3 (d|n = 2,7987; 2,1276; 1,6986 Å) в пробах, исследуемых фракций присутствуют примеси кальцита CaCO 3 (d|n = 3,0345; 1,8463; 1,8021 Å), доломита CaMg(CO 3 ) 2 (d|n= 2,8837; 2,1905; 1,7843 Å) и железистых включений Fe2O3 (d|n = 2,6671; 2,5365; 1,698 Å).
Для определения количественного содержания потенциально вредных примесей кальцита и доломита в различных фракциях сырьевой шихты использовали дериватографию. Отбор материала осуществляли из усредненных проб фракций 0…0,16 и ≥ 40 мм (рис. 1).
Из полученных дериватограмм следует, что фракция ≥ 40 мм состоит преимущественно из карбоната кальция (кальцита), имеет в своем составе примеси карбоната магния и доломита, что делает эту фракцию непригодной для получения магнезиального вяжущего. Во фракции 0…0,16 мм преобладает минерал доломит, а также присутствуют примеси магнезита, кальцита и оксида железа. Используя стехиометрические уравнения, установили процентное содержание минералов в зернах исследуемых фракций. Результаты количест-
Таблица 1
Среднее содержание фракций в пробах Саткинского магнезита 3 и 4 сортов
Фракции, мм |
||||||||||
> 40 |
20…40 |
10…20 |
5…10 |
2,5…5 |
1,25…2,5 |
0,63…1,25 |
0,315…0,63 |
0,16…0,315 |
0…0,16 |
|
Содержание, % |
0–10 |
2–38 |
2–22 |
8–26 |
6–20 |
0–16 |
1–16 |
2–18 |
0–15 |
15–45 |
Среднее распределение фракций в пробах, % |
5,49 |
14,13 |
9,71 |
8,82 |
6,99 |
5,31 |
4,82 |
3,86 |
2,94 |
37,76 |
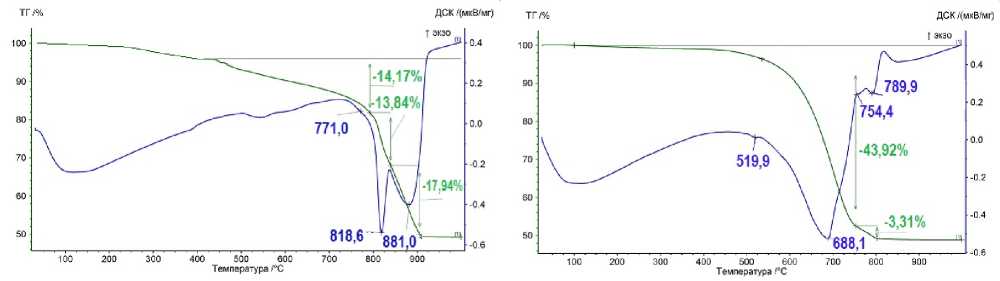
а) б)
Рис. 1. Дериватограммы усредненной пробы магнезита 3-го и 4-го сортов Саткинского месторождения фракции а) ≥ 40 мм, б) 0…0,16 мм
Исследование возможности использования отходов огнеупорных и горнодобывающих производств… венного анализа минералогического состава сырья различных фракций представлены в сводной таблице (табл. 2).
Из результатов, приведенных в таблице, следует, что минералогический состав сильно различается в зависимости от фракции исследуемого сырья. Фракция более 40 мм преимущественно состоит из доломита (до 52 %), магнезита (до 54 %) и кальцита (до 32 %). Фракция 0…0,16 мм в основном содержит магнезит (до 84 %) и доломит (до 20 %). Согласно высокому суммарному содержанию соединений магния в породе, рассматриваемые фракции пригодны для производства магнезиального вяжущего.
Таким образом, можно сделать вывод, что примерно 40 % от общего количества исследуемого материала представлено фракциями, не являющимися крупным или мелким заполнителем, но пригодными в качестве сырья для производства магнезиального вяжущего по комбинированному методу.
Вторая часть исследования состоит в предварительной оценке пригодности использования фракций 5…40 мм и 0,16…2,5 мм исследуемого материала в качестве крупного и мелкого заполнителя соответственно.
В качестве основной характеристики пригодности мелкого заполнителя был выбран показатель зернового состава, определяемый согласно ГОСТ 8735-88. «Песок для строительных работ. Методы испытаний». Результаты исследования зернового состава отсева исследуемой породы Саткинского месторождения фракции 0,16…2,5 приведены в табл. 3.
Кривая просеивания и область значений полных остатков на ситах, допустимых для применения в производстве тяжелого бетона согласно регламенту, представлена на рис. 2.
В качестве основной характеристики пригодности крупного заполнителя в данной работе принимали показатель дробимости согласно ГОСТ 8267–93 «Щебень и гравий из плотных горных пород для строительных работ. Технические условия». Методика определения данного показателя принималась согласно ГОСТ 8269.0-97 «Щебень и гравий из плотных горных пород и отходов промышленного производства для строительных работ. Методы физико-механических испытаний».
По результатам исследования было выявлено, что крупный заполнитель представлен фракцией 5–10 в количестве 22,4 % и 10–20 в количестве 70,6 %. Количество зерен, прошедших через контрольные сита 7,0 и 7,9 % соответственно. Суммарная дробимость крупного заполнителя с учетом количественного содержания фракций составил 7,7 %, что для осадочных пород соответствует
Таблица 2
Минералогический состав проб различных фракций
Фракция |
MgCO 3 , % |
CaCO 3 , % |
CaMg(CO 3 ) 2 , % |
Углисто-хлористое вещество, % |
|
>40 мм |
Разброс значений |
29…54 |
2,5…38 |
31,5…52 |
3…4 |
Среднее |
30 |
23 |
41 |
||
20…40 мм |
Разброс значений |
88…90 |
Следы |
8…13 |
3…4 |
Среднее |
89 |
11 |
|||
5…20 мм |
Разброс значений |
43…72 |
Следы |
21,5…51,5 |
< 1 |
Среднее |
53 |
42 |
|||
0,16…2,5 мм |
Разброс значений |
74…80 69 |
Следы |
5…17 11 |
< 1 |
0…0,16 мм |
Разброс значений |
75…84,5 |
Следы |
3,5…19,7 |
< 1 |
Среднее |
80 |
12 |
Таблица 3
Результаты исследования зернового состава мелкого заполнителя фракции 0,16…2,5 мм
Наименование остатка |
Размеры отверстий сит, мм |
||||
2,5 |
1,25 |
0,63 |
0,315 |
0,14 |
|
Остаток, г |
230 |
470 |
420 |
520 |
260 |
Частный остаток, % |
11,5 |
23.5 |
21 |
26 |
13 |
Полный остаток, % |
11,5 |
35 |
56 |
82 |
95 |
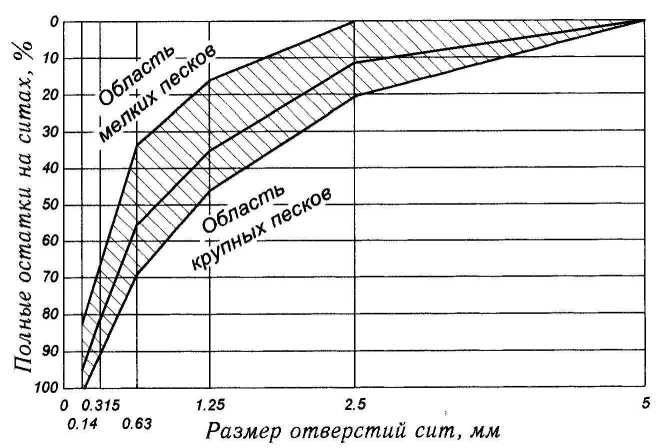
Рис. 2. Кривая просеивания для отсева исследуемой породы Саткинского месторождения
марке 1200. Следовательно, данный вид крупного заполнителя допускается применять для получения тяжелых бетонов любого класса прочности.
Таким образом, можно сделать вывод, что магнезит 3-го и 4-го сортов Саткинского месторождения пригоден для использования как в качестве сырья для производства магнезиального вяжущего, так и в качестве крупного и мелкого заполнителей. Для эффективной утилизации данного вида отходов целесообразно разделять общую массу сырья на фракции > 40 мм, 5…40 мм, 0,16…2,5 мм и < 0,16 мм. Фракцию более 40 мм дополнительно измельчать и совместно с зернами фракции менее 0,16 мм и использовать в качестве сырья для производства магнезиальных вяжущих комбинированным способом. На основе такого вяжущего можно получать тяжелые бетоны, используя отсев фракции 0,16…2,5 мм в качестве мелкого заполнителя и щебень фракции 10…40 мм в качестве крупного. Учитывая единую природу всех исходных компонентов такой бетонной смеси можно предположить, что в затвердевшем композите зерна заполнителя будут иметь высокие показатели сцепления с матрицей вяжущего.
Выводы
-
1. Магнезит третьего и четвертого сортов Саткинского месторождения разнороден по фракционному и химическому составу. Отдельные его фракции могут использоваться в качестве крупного и мелкого заполнителя. Крупный заполнитель имеет самую высокую марку по показателю дро-бимости, что предполагает его использование для получения тяжелых бетонов любого класса по прочности. Зерновой состав мелкого заполнителя находится в области допустимых значений для применения в производстве тяжелых бетонов.
-
2. Зерна фракции более 40 мм и менее 16 мм не пригодны для использования в качестве круп ного или мелкого заполнителя, но благодаря высо- 54
-
3. Использование крупного и мелкого заполнителя, полученного рассевом пород, являющихся сырьем для получения магнезиального вяжущего, позволит получать на его основе тяжелые бетоны высокой прочности за счет принципа наилучшей совместной работы компонентов за счет сходной минералогии.
-
4. Производство тяжелых магнезиальных бетонов позволит расширить область применения магнезиальных вяжущих и существенно ускорит темпы переработки отходных магнийсодержащих отвалов.
кому суммарному содержанию соединений магния могут использоваться в качестве сырья для получения магнезиальных вяжущих строительного назначения комбинированным методом.
Список литературы Исследование возможности использования отходов огнеупорных и горнодобывающих производств для получения тяжелого магнезиального бетона
- Яньшина, А.П. Особенности обжига гидроокиси магния из рапы / А.П. Яньшина // Огнеупоры. - 1960. - № 11. - С. 505-515.
- Воробьев, В.А. Производство минеральных вяжущих / В.А. Воробьев, В.С. Колокольников. - М.: Госстройиздат, 1960. - С. 304.
- Зырянова, В.Н. Магнезиальные вяжущие вещества из высокомагнезиальных отходов / В.Н. Зырянова, Г.И. Бердов // Известия высших учебных заведений. Строительство. - 2005. - № 10. - С. 46-53.
- Черных, Т.Н. Магнезиальные вяжущие из бруситовой породы Кульдурского месторождения: дис. … канд. техн. наук / Т.Н. Черных. - Челябинск, 2005.
- Минеральные вяжущие на основе высокомагнезиального природного сырья / Л.Я. Крамар, Т.Н. Черных, А.А. Орлов, Б.Я. Трофимов. - Челябинск: ООО «Искра-Профи», 2012. - 146 с.
- Иннокентьева, Л.С. Легкие бетоны на основе магнезиального вяжущего вещества / Л.С. Иннокентьева, А.Д. Егорова, А.Г. Гермогенова // Современные проблемы строительства и жизнеобеспечения: безопасность, качество, энерго- и ресурсосбережения: сборник статей IV Всероссийской научно-практической конференции, посвященной 60-летию Инженерно-технического института Северо-Восточного федерального университета им. М.К. Аммосова. Якутск, 27-28 окт.ября 2016 г. - 2016. - С. 186.
- Лыткина, Е.В. Ксилолитовые и костролитовые строительные материалы с использованием композиционного магнезиального вяжущего, содержащего диабаз / Е.В. Лыткина // Известия высших учебных заведений. Строительство. - 2010. - № 9. - С. 26-29.
- Соловьева, Т.В. Технология древесных композиционных материалов и изделий / Т.В. Соловьева, М.М. Ревяко, И.А. Хмызов. - Минск: БГТУ, 2008. - С. 177.
- Averina, G.F. Unified assessment technique for magnesium production waste to be applied in construction / G. Averina, T. Cherhyh, L. Kramar // AIP Conference Proceedings. - AIP Publishing, 2017. - Т. 1800, № 1. - С. 020003.
- Бирюлева, Д.К. Влияние продолжительности обжига доломита и структурных особенностей MgO и MgCl2•3Mg (OH)2•8H2O на прочность и водостойкость доломитового цемента / Д.К. Бирюлева, Н.С. Шелихов, Р.З. Рахимов // Изв. вузов. Строительство. - 2000. - № 4. - С. 32-37.
- Черных, Т.Н. Исследование влияния добавок-интенсификаторов на температуры обжига магнезиальных горных пород / Т.Н. Черных, Г.Ф. Аверина // Строительство и экология: теория, практика, инновации. - 2015. - С. 187-191.
- Августиник, А.И. Физико-химические процессы при обжиге доломит-серпентинитовой шихты для получения водоустойчивого доломитового клинкера / А.И. Августиник, П.Н. Бабин // Огнеупоры. - 1956. - № 7. - С. 322-326.
- ГОСТ 6613-86. Сетки проволочные тканые с квадратными ячейками. Технические условия (с Изменением № 1). - М.: Стандартинформ, 2006.
- ГОСТ 8269.0-97. Щебень и гравий из плотных горных пород и отходов промышленного производства для строительных работ. Методы физико-механических испытаний (с Изменениями № 1, 2). - М.: Госстрой России, ГУП ЦПП, 1998.
- ГОСТ 8735-88. Песок для строительных работ. Методы испытаний (с Изменениями № 1, 2). - М.: Стандартинформ, 2006.