Изготовление фольги из сплавов свинца и олова в условиях ЮУрГУ и ООО НПО «Р.О.С.Антикор»
Автор: Пелленен А.П., Пашкеев К.Ю., Мясоедов В.А., Сарафанов А.Е., Китав П.С.
Журнал: Вестник Южно-Уральского государственного университета. Серия: Металлургия @vestnik-susu-metallurgy
Рубрика: Обработка металлов давлением. Технологии и машины обработки давлением
Статья в выпуске: 1 т.24, 2024 года.
Бесплатный доступ
Свинцовая, оловянная и свинцовая фольга, плакированная оловом, используется в различных отраслях техники, медицине и пищевой индустрии. Согласно ГОСТ 18394-2016 толщина фольги находится в диапазоне 0,015-0,21 мм, а ширина фольги - 70-450 мм. Технология изготовления фольги на основе свинца, олова и их сплавов разработана достаточно давно, в 20-30-х гг. прошлого столетия. В СССР и за рубежом в те годы в силу специфических физико-механических свойств прокатываемых металлов использовалась холодная прокатка, реализующая рулонный и карточный методы прокатки. Применение в то время рулонного или карточного метода прокатки обусловливалось прежде всего наличием соответствующего оборудования. Прокатка фольги осуществлялась как на реверсивных, так и на нереверсивных двухвалковых прокатных станах, имеющих диаметры рабочих валков 230-700 мм. Анализ состояния технологии и применяемого оборудования для прокатки фольги из свинца, олова и свинцовой фольги, плакированной оловом, в настоящее время мало отличается от технологий, используемых в СССР. По нашему мнению, это объясняется малотоннажностью заказов, малым выходом годного (60-70 % от ленточной заготовки толщиной 0,9 мм), низкой рентабельностью и незаинтересованностью производителей в совершенствовании технологии. По имеющимся сведениям, время исполнения заказов на некоторых предприятиях доходит до 6 месяцев. Эти недостатки в удовлетворении спроса на малотоннажные партии отмечались в Распоряжении Правительства РФ № 4260-Р от 28 декабря 2022 г. В настоящей работе представлен опыт изготовления малотоннажных партий на основе свинца и олова в условиях ООО НПО «Р.О.С.Антикор» и ЮУрГУ. Проведенная исследовательская работа по разработке технологии и ее отработке для условий упомянутых организаций позволила разработать технологический регламент изготовления фольги и технические условия на свинцовую, оловянную и свинцовую фольгу, плакированную оловом.
Фольга оловянная, свинцовая и свинцовая фольга, плакированная оловом, малотоннажные партии, толщина фольги 0, 03-0, 3 мм, технологии изготовления
Короткий адрес: https://sciup.org/147243230
IDR: 147243230 | DOI: 10.14529/met240107
Текст научной статьи Изготовление фольги из сплавов свинца и олова в условиях ЮУрГУ и ООО НПО «Р.О.С.Антикор»
Original article
PRODUCTION OF FOIL FROM LEAD AND TIN ALLOYSIN THE CONDITIONS OF SUSU AND RPA “R.O.S.Anticor“ LLC
Свинцовая, оловянная и свинцовая фольга, плакированная оловом, используется в различных отраслях техники, медицине и пищевой индустрии. Согласно ГОСТ 18394–2016 [1] толщина фольги находится в диапазоне 0,015– 0,21 мм, а ширина фольги – 70–450 мм. В ряде случаев используют и фольгу толщиной 0,007 мм, как правило, для электронной промышленности.
Технология изготовления фольги на основе свинца, олова и их сплавов разработана достаточно давно, в 20–30-х гг. прошлого столетия [2–4]. В СССР и за рубежом в те годы в силу специфических физико-механических свойств прокатываемых металлов, а именно низкой температуры рекристаллизации (ниже комнатной) и низких прочностных свойств (предел прочности σв = 15…30 МПа) [5], использовалась холодная прокатка, реализующая рулонный и карточный методы прокатки. При этом термообработка (отжиг) в технологии не использовался.
Применение в то время рулонного или карточного метода прокатки обусловливалось прежде всего наличием соответствующего оборудования. Прокатка фольги осуществлялась как на реверсивных, так и на нереверсивных двухвалковых прокатных станах, имеющих диаметры рабочих валков 230–700 мм.
В СССР оловянную фольгу до толщины 0,01 мм, а также фольгу на основе свинца до толщины 0,02 мм получали карточным методом. При достижении толщины 1,0 мм лист перегибался пополам и пакет прокатывался так, что каждый лист его получал толщину 0,5 мм. Затем пакет снова перегибался, и прокатка велась в 4, 8, 16 и т. д. до 64 слоев [2]. Для предупреждения листов от сваривания друг с другом применяли смазку, большей частью являющуюся раствором мыла. Практически такая технология использовалась до 50-х гг. прошлого века. Выход годного из-за проколов, непланшетности, больших отходов при порезке для получения требуемых размеров фольги составлял около 20 %.
В этот период за рубежом уже использовалась реверсивная рулонная прокатка с намоткой фольги шириной до 650 мм на моталки [4]. Рабочие валки диаметром 260 мм и длиной бочки 750 мм и фрикционные моталки с возможностью регулирования натяжений фольги приводились от одного двигателя.
К началу 1960-х гг. в СССР [6, 7] фольгу из свинца и олова стали получать в основном рулонным способом на специализированных фольгопрокатных двухвалковых станах с диаметром рабочих валков 230 и 350 мм и длиной бочки до 600 мм. При этом требуемые натяжения фольги на моталках обеспечивались электродвигателями с применением систем автоматического регулирования натяжений.
Анализ состояния технологии и применяемого оборудования для прокатки фольги из свинца, олова и свинцовой фольги, плакированной оловом, в настоящее время мало отличается от технологий, используемых в
СССР. По нашему мнению, это объясняется малотоннажностью заказов, малым выходом годного (60–70 % от ленточной заготовки толщиной 0,9 мм), низкой рентабельностью и незаинтересованностью производителей в совершенствовании технологии. По имеющимся сведениям, время исполнения заказов на некоторых предприятиях доходит до 6 месяцев. Эти недостатки в удовлетворении спроса на малотоннажные партии отмечались в Распоряжении Правительства РФ № 4260-Р от 28 декабря 2022 г. [8].
В настоящей работе представлен опыт изготовления малотоннажных партий на основе свинца и олова в условиях ООО НПО «Р.О.С.Антикор» и ЮУрГУ. Проведенная исследовательская работа по разработке технологии и ее отработке для условий упомянутых организаций позволила разработать технические условия на свинцовую, оловянную и свинцовую фольгу, плакированную оловом [9]. Поскольку свинец и олово имеют достаточно близкие механические свойства [5], то режимы деформаций при прокатке этих сплавов практически одинаковы. Некоторые технологические особенности имеет свинцовая фольга, плакированная оловом.
В соответствии с технологическим регламентом биметаллическую заготовку олово– свинец–олово для последующего изготовления из нее фольги получают на двухвалковом реверсивном стане ООО НПО «Р.О.С.Антикор» (рис. 1), имеющем следующую техническую характеристику:
диаметр рабочих валков – 710 мм;
длина бочки валков – 1400 мм;
скорость прокатки – 1 м/с;
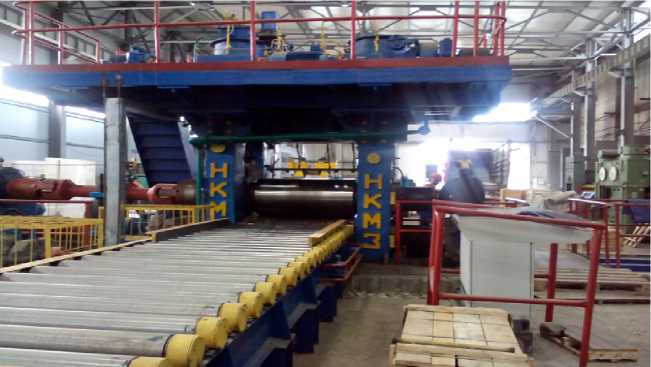
Рис. 1. Стан двухвалковый 710 х 1400 мм ООО НПО «Р.О.С.Антикор»
Fig. 1. Twin-roll mill 710 х 1400 mm RPA “R.O.S.Anticor” LLC
максимальное усилие прокатки – 6 МН;
максимальный крутящий момент – 1,5 МН·м;
длина рольгангов – 12 м;
стан оснащен гильотинными ножницами с шириной реза 1400 мм, установленными в конце рольганга.
Предварительно из литого свинцового сляба марки С3 по ГОСТ 3778–98 с присадкой сурьмы Су2 по ГОСТ 1089–82 в количестве 1,9–3,1 % и олова О2 по ГОСТ 860–75 [10–12] в количестве 1,0–3,0 %, имеющего исходные размеры 100 х 700 х 1100 мм, получают за пять пропусков свинцовые пластины толщиной 20 мм, шириной 650 мм и длиной 500 мм. Обрезка прокатанной заготовки осуществляется на гильотинных ножницах стана. Оловянные полосы размерами 0,6 х 500 х 1400 мм получают из литой заготовки толщиной 30 мм, шириной 600 мм и длиной 550 мм.
Такое соотношение толщин свинцовой пластины и оловянной полосы обусловлено требованиями ГОСТ 18394–2016 и ТУ 1835007-61252951-2016 [1, 9]. Согласно техническим требованиям суммарная толщина обоих плакирующих слоев должна составлять от 5 до 8 % суммарной толщины биметаллической фольги. В исходном пакете суммарная толщина слоев олова (1,2 мм) составляет 5,55 % от общей толщины пакета (21,2 мм). Однако при плакировании и последующей прокатке наблюдается значительная неравномерность деформации слоев. Степень деформации свинца практически в 1,3 раза выше, чем оловянной полосы. При этом суммарная толщина плакирующих слоев олова доходит до 7–7,5 % от толщины фольги 0,05 мм.
Перед плакированием (сваркой) свинцовой пластины и оловянной полосы их обезжиривают и зачищают металлическими проволочными щетками диаметром 300 мм. Диаметр проволок, изготовленных из стали У8, составляет 0,5 мм. Свинцовую пластину зачищают с двух сторон, а оловянную – с одной стороны. При подготовке исходных компонентов к плакированию предъявляются соответствующие требования к качеству поверхности. Незначительные раковины, царапины, вдавливания на поверхности при последующем плакировании и прокатке приводят к местной неравномерности деформации и разрывам плакирующего слоя.
После подготовки поверхностей свинцовая пластина оборачивается оловянной поло- сой. При этом не зачищенная сторона оловянной полосы находится снаружи.
Следует отметить, что в практике производства слоистых металлических композиций плакирующий слой используют по ширине на 10–20 мм больше ширины основного слоя [13–15]. Этот прием предотвращает попадание смазки между слоями, которая может привести к неприварке слоев. Кроме того, если ширина плакирующего слоя больше ширины основы, в этом случае происходит обрезка кромок плакирующей полосы.
При плакировании свинцовой пластины оловянной полосой, если ее ширина больше ширины основы, не происходит обрезка кромок. Это приводит к разрывам оловянной полосы, а в ряде случаев и свинцовой пластины по кромкам, увеличению расходного коэффициента и невозможности получения качественной продукции. В связи с этим используется оловянная полоса шириной на 50 мм меньше ширины свинцовой пластины. При этом не появляются разрывы по кромкам слоев.
Перед прокаткой исходного биметаллического пакета производят обезжиривание валков растворителем уайт-спиритом для обеспечения стабильного захвата металла валками. Первые 2–3 прохода выполняют реверсивно при небольших обжатиях, практически по 1–2 мм с тем, чтобы плакирующая оловянная полоса ровно и без складок прилегала к свинцовой пластине. После достижения суммарной толщины пакета 13–14 мм для обеспечения сварки слоев осуществляют прокатку в один проход с деформацией не менее 55–60 % до толщины 6 мм, а затем прокатку биметаллической полосы до толщины 4 мм за один проход. При этом длина полосы составляет 2,7 м. При прокатке после толщины 14 мм используется смазка, содержащая 50 % керосина и 50 % индустриального масла И-20.
Таким образом, прокатка биметаллической полосы олово – свинец – олово с толщины 21,2 мм до толщины 4 мм в условиях ООО НПО «Р.О.С.Антикор» осуществляется по режиму 21,2 → 19 → 17 → 14 → 6 → 4 мм. После достижения толщины полосы 4 мм для получения фольги толщиной 0,03–0,2 мм в рулоне полосы режутся на ширину 140 мм и передаются в ЮУрГУ для последующей обработки.
Для получения фольги в условиях ООО НПО «Р.О.С.Антикор» толщиной 0,1 мм в виде карточек размерами 450 х 500 мм полосы прокатываются по режиму 4,0 → 2,7 → 1,6 → → 0,65 → 0,4 мм. Затем полоса складывается вдвое и далее деформируется до толщины 0,2 мм за 2 прохода, т. е. 0,8 → 0,4 → 0,2 мм. Для предотвращения возможного сваривания слоев полосы при прокатке они смазываются ламповым маслом (ТУ 0253-06-529-4011842008, смесь жидких парафинов).
Прокатанные полосы складываются в пакеты из слоев, и производится резка на требуемые размеры по шаблону. Затем карточки раздираются и в толщине 0,1 мм, после контроля ОТК, отгружаются заказчикам.
В условиях ООО НПО «Р.О.С.Антикор» свинцовые и оловянные полосы до толщины 4 мм прокатываются практически по тем же режимам деформации, что и свинцовые полосы, плакированные оловом. При этом в толщине 4 мм полосы разрезаются на гильотинных ножницах на ширину 140 мм и длину 2–3 м. Полученные заготовки, как и биметаллические полосы олово – свинец – олово, далее прокатываются в условиях ЮУрГУ на универсальном стане холодной прокатки ХПЛ-200 (рис. 2).
Техническая характеристика стана ХПЛ-200 следующая.
В двухвалковом варианте:
диаметр рабочих валков – 180 мм;
длина бочки валков – 200 мм.
В четырехвалковом варианте: диаметр рабочих валков – 60 мм; длина бочки валков – 200 мм.
Максимальная исходная толщина полосы – 10 мм;
минимальная толщина фольги – 0,03 мм;
скорость прокатки – до 1 м/с;
максимальное усилие прокатки – 400 кН;
максимальный крутящий момент – 500 кН·м;
диапазон натяжений ленты (фольги) – 0,06–5 кН;
охлаждение валков – эмульсионное.
На схеме стана ХПЛ-200 (см. рис. 2) фрикционные моталки приводятся во вращение с помощью ременной передачи от основных моталок 2 и 8 через дисковые фрикционы, которые в процессе прокатки позволяют регулировать натяжения фольги при значительном изменении диаметра рулона на барабане моталки. На основных моталках натяжения ленты поддерживаются системой автоматического регулирования с помощью лазерных датчиков, фиксирующих изменение диаметра рулона на моталках.
Поставляемые с ООО НПО «Р.О.С.Анти-кор» свинцовые и оловянные полосы в толщине 4 мм по 3–4 штуки свариваются в рулон весом 40–60 кг. Сварка полос производится встык с использованием роботизированного комплекса лазерной наплавки FL-Clad-R4. Комплекс оснащен пятиосевым промышленным роботом KUKA R-120 грузоподъемностью до 120 кг (рис. 3), волоконным иттербиевым лазером LS-4 (IPG Photonics) мощностью 4 кВт, головой оптической для сварки FLW D50L (IPG Photonics) [16].
Сварка полос толщиной 4 мм включает несколько операций: позиционирование пары полос относительно друг друга в горизонтальной плоскости на специализированном столе, сварка с одной стороны, переворот полос, сварка с другой стороны. Сварка осуществляется путем прямого движения лазерного луча по стыку полос со скоростью 10 мм/с. Диаметр луча при этом составляет 4 мм, мощность лазерного излучения – 500 Вт. При таком режиме сварки глубина проплавления с одной стороны составляет 2,5–2,7 мм без значительного растекания свинца или олова
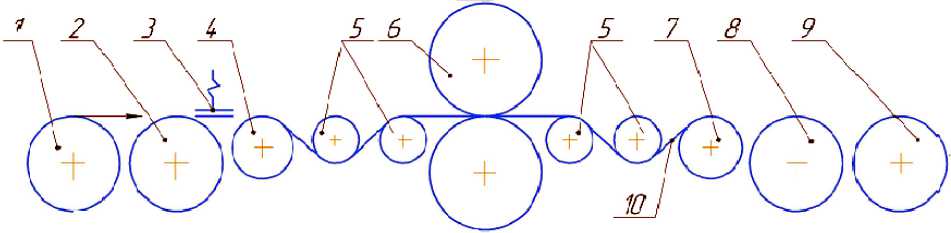
Рис. 2. Схема универсального стана ХПЛ-200: 1 – разматыватель; 2 – моталка; 3 – прижим; 4 – фрикционная моталка, 5 – обводные ролики; 6 – рабочие валки; 7 – фрикционная моталка; 8 – моталка; 9 – концевая моталка; 10 – фольга
Fig. 2. Scheme of the universal mill KhPL-200: 1 – unwinder; 2 – winder; 3 – clamp; 4 – friction winder; 5 – deflector rollers; 6 – work rolls; 7 – friction winder; 8 – winder; 9 – end winder; 10 – foil
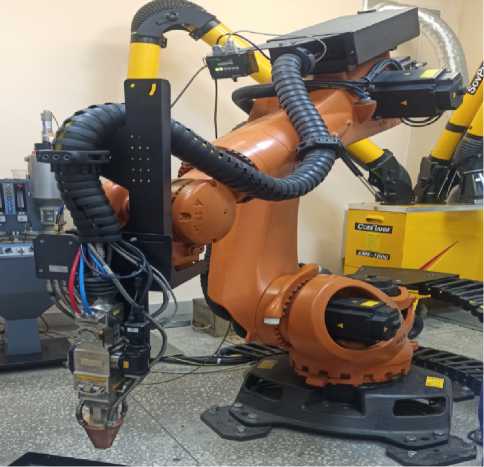
Рис. 3. Робот KUKA R-120
Fig. 3. Robot KUKA R-120
из зоны сварки. Таким образом, при сварке с двух сторон происходит проплавление на всю толщину полосы. Толщина сварного шва составляет 5–5,5 мм.
Свинцовые, оловянные и плакированные полосы олово–свинец–олово прокатываются на стане ХПЛ-200 в двухвалковом варианте до толщины 0,3 мм реверсивно по режиму: 4,0 → 2,0 → 1,0 → 0,5 → 0,3 мм. При этом первый проход осуществляется с разматыва-теля, заднее натяжение полос обеспечивается прижимом (см. рис. 2). В первом проходе при прохождении сварного шва через валки для исключения обрывов скорость прокатки полос снижается до 0,1 м/с. Натяжения концов полосы при прокатке обеспечиваются моталками 2 и 8. При этом полоса не охватывает обводные ролики 5 (см. рис. 2).
После достижения толщины полосы 0,3 мм она сматывается на стальную шпулю диаметром 220 мм на концевую моталку. Затем шпуля с полосой вновь устанавливается на разма-тыватель и в первом проходе полоса деформируется до толщины 0,15 мм (это уже согласно ГОСТ 18394–2016 – фольга [1]). При этом передний конец фольги охватывает обводные ролики 5 (см. рис. 2) и заправляется на моталку 7, вращение которой осуществляется через фрикцион, обеспечивающий требуемое натяжение. Заднее натяжение в данном проходе обеспечивается прижимом 3. После схода заднего конца полосы и выхода его из прижима он закрепляется на фрикционной моталке 4, огибая обводные ролики, как показано на схеме рис. 2. В дальнейшем прокатка фольги осуществляется реверсивно с использованием фрикционных моталок 4, 7 (см. рис. 2) по режиму 0,15 → 0,08 → 0,05 → 0,03 мм. Смотка фольги при прокатке производится на установленные на барабаны моталок полихлорвиниловые шпули диаметром 160 мм.
Необходимость использования обводных роликов 5 (см. рис. 2) при прокатке фольги объясняется тем, что при их отсутствии под действием натяжений возникает продольная волнистость, что приводит, как правило, к образованию складок между рабочими валками и моталками и при прокатке образуются гофры или порезы фольги, приводящие к ее обрывам. При использовании обводных роликов фольга на них разглаживается и обеспечивается прокатка без образования складок фольги перед рабочими валками и на моталках.
Резка фольги на требуемую ширину осуществляется на дисковых ножницах с диаметром ножей 80 мм. Между ножами устанавливаются резиновые втулки (рис. 4), изготовленные из мягкой пористой резины [17]. Использование такой резины не приводит к прокалыванию фольги, если на ее поверхности присутствуют твердые частицы. Наличие проколов фольги, как правило, не допускается, или их количество оговаривается заказчиком.
Технологические операции и приведенные режимы обжатий изготовления фольги являются базовыми. При необходимости по
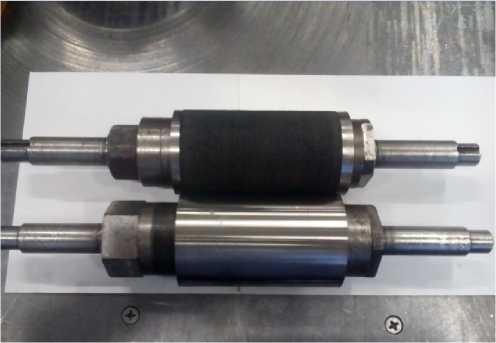
Рис. 4. Дисковые ножи в сборе Fig. 4. Disk knives assembled
требованиям заказчиков режимы деформации корректируются для получения требуемых размеров по толщине и ширине фольги.
За период 2022–2023 гг. в условиях ЮУрГУ и ООО НПО «Р.О.С.Антикор» было изготовлено более 15 т свинцовой, оловянной и свинцовой фольги, плакированной оловом, толщиной 0,04–0,3 мм для предприятий электротехнической, химической промышленности и предприятий ВПК. Минимальный вес заказываемой продукции – 5 кг. Время изготовления заказов, как показал опыт, не превышало трех недель.
Заключение
Представлены технологические режимы и опыт изготовления малотоннажных партий фольги из сплавов свинца и олова толщиной 0,04–0,3 мм в условиях ЮУрГУ и НПО «Р.О.С.Антикор». Имеющееся технологическое оборудование в НПО «Р.О.С.Антикор» позволяет, используя карточный метод холодной прокатки, изготавливать фольгу толщиной 0,1 мм и шириной до 600 мм. В ЮУрГУ имеется возможность производить фольгу толщиной 0,04 мм и шириной до 130 мм рулонным методом.
Фольга поставляется в соответствии с ТУ 1835-007-61252951-2016. В период 2022–2023 гг. было изготовлено более 15 т фольги. Причем основное количество фольги (14,5 т) было произведено на оборудовании ЮУрГУ.
Список литературы Изготовление фольги из сплавов свинца и олова в условиях ЮУрГУ и ООО НПО «Р.О.С.Антикор»
- ГОСТ 18394–2016. Фольга свинцовая, плакированная оловом, и оловянная. Технические условия. М.: Стандартинформ, 2017. 7 с.
- Прокатка цветных металлов. В 3 ч. Ч. 1: Производство листов и лент из тяжелых и легких металлов и их сплавов / под ред. П.С. Истомина. М.; Л.; Свердловск: Госметаллургиздат, 1934. 534 с.
- Прокатка цветных металлов. В 3 ч. Ч. 3: 1. Теория прокатки. 2. Расчеты оборудования прокатных цехов. 3. Калибровка прокатных валков / под ред. П.С. Истомина. М.; Л.; Свердловск: Госметаллургиздат, 1933–1934. 488 с.
- Davis E. Metal foil rolling // Metallurgy. Manchester, 1933. P. 141–143.
- Смирягин А.П., Смирягина Н.А., Белова А.В. Промышленные цветные металлы и сплавы. М.: Металлургия, 1974. 488 с.
- Черняк С.Н., Карасевич В.И. Производство фольги. М.: Металлургиздат, 1957. 272 с.
- Черняк С.Н., Карасевич В.И., Коваленко П.А. Производство фольги. М.: Металлургия, 1968. 386 с.
- Распоряжение Правительства РФ от 28 декабря 2022 г. № 4260-Р.
- ТУ 1835-007-61252951-2016. Фольга свинцовая, свинцовая, плакированная оловом, и оловянная. Челябинск: ООО НПО «Р.О.С.Антикор», 2016. 8 с.
- ГОСТ 3778–98. Свинец. Технические условия. М.: ИПК Издательство стандартов, 2003. 11 с.
- ГОСТ 1089–82. Сурьма. Технические условия. М.: ИПК Издательство стандартов, 2002. 6 с.
- ГОСТ 860–75. Олово. Технические условия. М.: Стандартинформ, 2008. 12 с.
- Биметаллы / Л.Н. Дмитров, Е.В. Кузнецов, А.Г. Кобелев и др. Пермь: Перм. кн. изд-во, 1991. 415 с.
- Слоистые металлические композиции / И.Н. Потапов, В.Н. Лебедев, А.Г. Кобелев и др. М.: Металлургия, 1986. 216 с.
- Пелленен А.П., Хабибуллин А.А. Экспериментальное исследование качества обрезки кромки плакирующей ленты при плакировании лент холодной прокаткой // Вестник ЮУрГУ. Серия «Металлургия». 2015. Т. 15, № 4. С. 147–150. DOI: 10.14529/met150420
- Роботизированный комплекс лазерной наплавки IRE-POLUS. URL: https://www.ipgphotonics.com/ru/products/laser-systems/naplavka-termouprochnenie/sistemy-dlya-naplavki/yacheykilazernoy-naplavki.
- ТУ 38 105867-90. Пластина пористая техническая с двумя пленками. М.: ВНИИЭМИ, 1990. 18 с.