Изменение структур и свойств быстрорежущих сталей в результате легирования и сложной термической обработки
Автор: Крукович В.В., Борисова Л.Г.
Журнал: Научный форум. Сибирь @forumsibir
Рубрика: Промпроизводство
Статья в выпуске: 1 т.2, 2016 года.
Бесплатный доступ
Короткий адрес: https://sciup.org/140220247
IDR: 140220247
Текст статьи Изменение структур и свойств быстрорежущих сталей в результате легирования и сложной термической обработки
Термическая обработка в технологическом процессе изготовления продукции занимает важнейшее место, так как с ее помощью можно коренным образом изменить структуру и свойства металлических изделий. Так, путем термической обработки можно существенно повысить показатели прочности, сопротивляемость хрупкому разрушению, улучшить режущие свойства инструмента, износостойкость различных узлов машин и механизмов, а так же можно получить заданные физические свойства.
Инструментальные стали являются основным материалом для изготовления металлорежущего инструмента. Качество продукции во многом зависит от качества инструмента [6].
Инструментальные стали – это большая группа сталей, которые в результате термической обработки получают высокую твердость, прочность и износостойкость, необходимые для обработки материалов резанием или давлением. Кроме того, многие инструментальные стали обладают теплоемкостью, т.е. способностью сохранять эти свойства при нагреве, возникающим в рабочей кромке инструментов при резании с повышенной скоростью, при деформировании в горячем состоянии и т.д. Основными свойствами инструментальных сталей являются: твердость, вязкость, износостойкость, теплоёмкость (красностойкость), про-каливаемость [3].
По твёрдости и вязкости инструментальные стали классифицируются на стали высокой твердости (HRC 58-65), но пониженной вязкости и стали с повышенной вязкостью, но пониженной твёрдости (HRC 40-55) [7].
Износостойкость инструментальной стали, т.е. способность ее сопротивляться различным видам изнашивания поверхности, является важнейшей характеристикой долговечности работы инструмента.
По теплостойкости стали разделяют на: не теплостойкие, полутеплостойкие и теплостойкие. Не теплостойкие стали сохраняют высокую твердость и другие свойства до температуры нагрева 200-300ºС, полутеп-лостойкие до 400-500ºС, а теплостойкие выше 550-
600ºС. Увеличение температуры теплостойкости существенно повышает срок службы инструмента. Так, повышение температуры теплостойкости быстрорежущей стали с 610ºС до 640ºС увеличивает срок службы режущего инструмента в 2-3 раза, а до 700ºС в 10-15 раз [3].
По назначению инструментальные стали делят на стали для режущих инструментов, штамповые стали для холодного деформирования, штамповые стали для горячего деформирования, стали для измерительного инструмента.
Применение быстрорежущих сталей для режущего инструмента позволяет повысить скорость резания в несколько раз, а стойкость инструмента в десятки раз. Главной оптимальной особенностью быстрорежущих сталей является высокая теплостойкость или красностойкость (600-700ºС) при наличии высокой твердости (HRC Э 63-70) и износостойкости инструмента. Уникальные свойства быстрорежущих сталей достигаются по средствам специального легирования и сложной термической обработки, обеспечивающих определенный фазовый состав.
Быстрорежущие стали имеют в своём составе сравнительно невысокое содержание углерода (0,70,95%) и весьма высокое содержание легирующих элементов (до 25%). Основными легирующими элементами являются: вольфрам (6-18%), хром (около 4%), ванадий (1-5%). Для повышения теплостойкости производятся стали, дополнительно легированные кобальтом (5-10%).
Карбидообразующие элементы образуют в стали специальные карбиды Ме 6 С на основе вольфрама и молибдена, МеС на основе ванадия и Ме 23 С 6 на основе хроме. Часть атомов Ме в указанных карбидах составляет железо и другие элементы [3]. Вертикальный (по-литермический) разрез диаграммы состояния Fe – Cr – W – V, характерный для быстрорежущих сталей приведен на рис. 1.
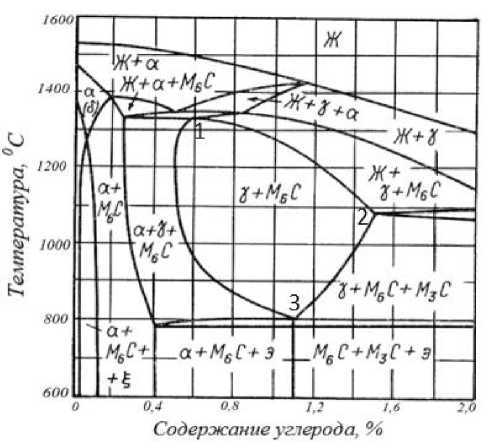
Рис. 1. Вертикальный разрез диаграммы состояния Fe - W - Cr - C - V (при 4%-Cr, 1%-V и 18%-W).
Аустенит в быстрорежущих сталях получается при нагреве выше 800 - 900ºС, однако при этих температурах аустенит не обогащен основными легирующими элементами и углеродом. Поэтому закалка стали от температуры выше Ас3 (линия 1 - 3 - 2) на 30 – 50ºС, как принято для обычных сталей, не может обеспечить главного свойства быстрорежущей стали – красностойкости [1]. Красностойкость достигается лишь после высокотемпературного нагрева под закалку до температур несколько ниже линии солидуса А4 (1-2), когда значительная часть легированных карбидов растворяется в аустените, обогащая его вольфрамом, молибденом, ванадием, хромом и углеродом [7].
Быстрорежущие стали различают: умеренной, повышенной и высокой теплостойкости. Теплостойкость умеренной стали составляет 600-615ºС, а наиболее характерными легирующими элементами являются вольфрам и молибден. Характерными представителями этой группы являются стали: Р18, Р12 и вольфрамомолибденовая сталь Р6М5 [5].
Стали повышенной теплостойкости имеют высокое содержание ванадия, углерода (азота), их дополнительно легируют кобальтом, что позволяет повысить теплостойкость до 650ºС. Наибольшее значение теплостойкости (700 - 730ºС) у сталей высокой теплостойкости с интерметаллидным упрочнением, например, у стали В11М7Л23.
В последнее время расширилось использование быстрорежущих сталей с повышенным содержанием углерода до 2%, при сравнительно низком содержании вольфрама и молибдена (11РЗАМЗФ2) и сталей, легированных азотом до 0,05-0,10% (Р6АМ5, Р6АМ5Ф3). Разработаны безвольфрамовые быстрорежущие стали типа 11М5ФЗ, имеющие свойства, близкие к стали Р6М5 [4].
Помимо процессов карбидообразования на свойства стали оказывает влияние превращения остаточного аустенита в мартенсит. Практически полное превращение остаточного аустенита в мартенсит возможно после нескольких циклов нагрева и охлаждения (2-х - 4-х кратный отпуск), продолжительностью более 1 часа, что приводит к небольшому снижению количества остаточного аустенита по сравнению с тем, что достигается при одночасовом отпуске [1].
При охлаждении до комнатных температур структура содержит 20-25% не распавшегося аустенита. После первого отпуска количество остаточного аустенита снижается до 10%. При этом мартенсит, полученный при закалке (около 65%) отпускается, но образуется новый не отпущенный мартенсит (около 15%) из остаточного аустенита. При втором отпуске количество остаточного аустенита снижается до 5%, отпускается мартенсит, полученный при первом отпуске, но опять появляется не отпущенный мартенсит (около 5%). После третьего отпуска количество остаточного аустенита составляет 1-2% и практически весь мартенсит является отпущенным (кроме 3-4%, полученных при третьем отпуске). Многократный отпуск приводит к росту твердости по сравнению с закаленным состоянием, т.е. явлению вторичной твердости [2].
Количество отпусков определяется содержанием остаточного аустенита после закалки и его стабильностью, зависящей от состава стали. Возможно применение сокращенного высокотемпературного отпуска или обработка холодом сразу после закалки до температуры – 80ºС. Такое охлаждение вызывает дополнительное превращение в мартенсит 10-20% остаточного аустенита [1].
Быстрорежущие стали являются хорошо изученными сталями из ряда инструментальных сталей и обладают свойствами, удовлетворяющими основным требованиям, предъявляемые к материалу рабочего слоя многих деталей машин и инструмента металлургического оборудования, таким, как высокая и равномерная твердость, теплостойкость, износостойкость, удовлетворительная вязкость и прочность. Термическая обработка включает в себя: отжиг, закалку и отпуск [6].
Перспективным способом получения быстрорежущих сталей является метод порошковой металлургии. Главной отличительной особенностью порошковых сталей является равномерное распределение карбидов по сечению, которое не превышает первого балла шкалы карбидной неоднородности по ГОСТ 19265– 73.
Список литературы Изменение структур и свойств быстрорежущих сталей в результате легирования и сложной термической обработки
- Геллер Ю.А. Инструментальные стали. -М.: Металлургия, 1986.
- Гуляев А.П. Металловедение. Учебник для вузов. 7-е изд., пере-раб. и доп. -М.: Альянс. -2012. -644 с.
- Жуковец И.И. Механические испытания металлов: учеб. пособие для вузов. -М.: Высш. шк., 2012.
- Зуев В.М. Термическая обработка в металловедении: учебник. -М.: Высш. шк., 1999.
- Звягин В.Б., Цуканов В.В., Сивенков А.В. Оборудование и автоматизация процессов тепловой обработки материалов и изделий. Основное оборудование: Учеб. пособие. -СПб.: Изд-во Национального минерально-сырьевого университета «Горный». -2012. -83 с.
- Солнцев Ю.П., Пряхин Е.И. Материаловедение: учебник для ВУЗов. -СПб.: Химиздат. -2015. -783 с
- Термическая обработка в машиностроении; под ред. Ю.М. Лахтина, А.Г. Рахштадта. -М.: Машиностроение, 1987.